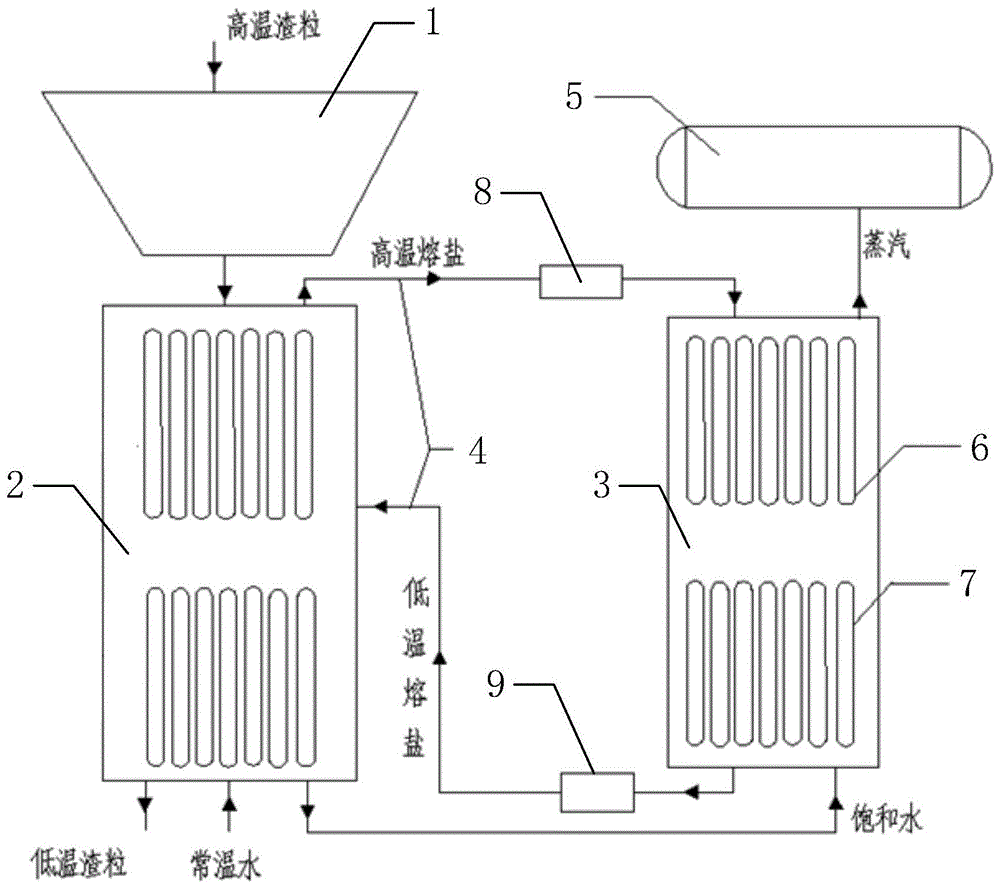
本发明属于炉渣回收领域,涉及一种高温渣粒余热回收系统及回收方法。
背景技术:
在我国的工业领域分布着丰富的余热余能资源,随着节能技术的不断发展,越来越多的余热资源得到了应用,但是蕴含有高温余热的高温熔渣的显热一直没有得到有效利用。炉渣存量庞大、温度高,含有丰富的余热余能资源,如何有效的余热回收一直是困扰钢铁企业的大难题。国内外普遍对高温炉渣采用水淬的方式,余热利用率低。目前国内外开始采用炉渣粒化并移动床传热的方式进行余热回收,但该技术存在压力管道磨损严重存在爆管的危险,同时,由于排渣是间歇的,且排渣量瞬时变化,波动很大,如何把间歇、瞬变的余热资源变为稳定的连续能源供给能源用户,是一个急需解决的问题。
技术实现要素:
有鉴于此,本发明的目的在于提供一种高温渣粒余热回收系统及回收方法。
为达到上述目的,本发明提供如下技术方案:
一种高温渣粒余热回收系统,包括依次连通的渣粒储存包、自流床固体粒子余热锅炉、熔盐余热锅炉;所述自流床固体粒子余热锅炉与熔盐余热锅炉之间设有用于储存及交换热量的熔盐储热系统。
可选的,所述熔盐储热系统采用熔盐进行热量交换,与自流床固体粒子余热锅炉的高温颗粒换热后升温至高温熔盐,与饱和水换热后,饱和水升温产生蒸汽,换热后高温熔盐降温至低温熔盐,并循环至自流床固体粒子余热锅炉的高温侧循环换热。
可选的,自流床固体粒子余热锅炉与渣粒储存包连通的一侧为熔盐换热区,另一侧为水换热区;水换热区换热产生的饱和水连通至熔盐余热锅炉。
可选的,所述自流床固体粒子余热锅炉内熔盐换热区的换热管叉逆流布置,水换热区的换热管叉逆流布置。
可选的,所述熔盐余热锅炉沿内部水流动方向依次设有蒸发器、过热器、汽包;所述蒸发器、过热器均为套管式换热管,液态熔盐在套管式换热管内侧流通,水或蒸汽在套管式换热管外侧流通。
可选的,所述蒸发器、过热器内的套管逆流布置。
可选的,所述熔盐储热系统内设有用于暂时存储高温熔盐的高温熔盐罐、以及用于暂时存储低温熔盐的低温熔盐罐。
一种高温渣粒余热回收方法,包括以下步骤:高温渣粒与低温熔盐及常温水依次换热,产生高温熔盐及饱和水;高温熔盐与饱和水进行换热,产生低温熔盐及蒸汽。
可选的,所述高温熔盐及低温熔盐均为液态熔盐。
可选的,熔盐是由几种熔盐组成的混合盐。
本发明的有益效果在于:
本发明将熔盐储热系统和自流床余热锅炉紧密结合,实现了间歇、瞬变的余热资源的稳定供应,同时该技术采用熔盐系统跟高温颗粒进行换热,管内的熔盐处于常压状态,避免了高温锅炉管束处于高压状态,有效解决了蒸汽爆管的危险。
本发明的其他优点、目标和特征在某种程度上将在随后的说明书中进行阐述,并且在某种程度上,基于对下文的考察研究对本领域技术人员而言将是显而易见的,或者可以从本发明的实践中得到教导。本发明的目标和其他优点可以通过下面的说明书来实现和获得。
附图说明
为了使本发明的目的、技术方案和优点更加清楚,下面将结合附图对本发明作优选的详细描述,其中:
图1为本发明的整体结构示意图。
附图标记:渣粒储存包1、自流床固体粒子余热锅炉2、熔盐余热锅炉3、熔盐储热系统4、汽包5、过热器6、蒸发器7、高温熔盐罐8、低温熔盐罐9。
具体实施方式
以下通过特定的具体实例说明本发明的实施方式,本领域技术人员可由本说明书所揭露的内容轻易地了解本发明的其他优点与功效。本发明还可以通过另外不同的具体实施方式加以实施或应用,本说明书中的各项细节也可以基于不同观点与应用,在没有背离本发明的精神下进行各种修饰或改变。需要说明的是,以下实施例中所提供的图示仅以示意方式说明本发明的基本构想,在不冲突的情况下,以下实施例及实施例中的特征可以相互组合。
其中,附图仅用于示例性说明,表示的仅是示意图,而非实物图,不能理解为对本发明的限制;为了更好地说明本发明的实施例,附图某些部件会有省略、放大或缩小,并不代表实际产品的尺寸;对本领域技术人员来说,附图中某些公知结构及其说明可能省略是可以理解的。
本发明实施例的附图中相同或相似的标号对应相同或相似的部件;在本发明的描述中,需要理解的是,若有术语“上”、“下”、“左”、“右”、“前”、“后”等指示的方位或位置关系为基于附图所示的方位或位置关系,仅是为了便于描述本发明和简化描述,而不是指示或暗示所指的装置或元件必须具有特定的方位、以特定的方位构造和操作,因此附图中描述位置关系的用语仅用于示例性说明,不能理解为对本发明的限制,对于本领域的普通技术人员而言,可以根据具体情况理解上述术语的具体含义。
请参阅图1,为一种高温渣粒余热回收系统,包括渣粒储存包1、自流床固体粒子余热锅炉2、熔盐余热锅炉3、熔盐储热系统4。自流床固体粒子余热锅炉2,交换热装置上部分为高温渣粒与熔盐直接接触换热,换热管叉排逆流布置,交换热装置下部分是低温渣粒与常温水进行热交换,套管换热管逆流布置。熔盐余热锅炉3,包含蒸发器7、过热器6、汽包5等组成,蒸发器7、过热器6均为套管式换热管,外部走水或者饱和蒸汽,内部走液态熔盐。熔盐储热系统4,包含高温熔盐罐8、低温熔盐罐9、连接管等。
高温渣粒首先进入渣粒储存包1,而后经渣粒储存包1的出料机进入自流床固体粒子余热锅炉2进行换热,先与上部的液态熔盐进行热交换,换热管与高温固体渣粒直接接触换热,进口处换热管叉排逆流布置,再与下部的常温水进行热交换,套管换热管逆流布置,渣粒冷却到200℃以下后由下端的出料口排出。自流床固体粒子余热锅炉2上部的高温熔盐经过高温熔盐罐8存储后,进入到熔盐余热锅炉3,与饱和水进行换热,冷却后的低温熔盐再经过设置的低温熔盐罐9返回至自流床固体粒子余热锅炉2。
自流床固体粒子余热锅炉2系统下部的常温水换热后形成饱和水,进入到熔盐余热锅炉3,依次经过蒸发器7、过热器6与高温熔盐换热后生产350-500℃的蒸汽,蒸汽可以并入厂区蒸汽管网,也可用于发电。熔盐余热锅炉3的蒸发器7、过热器6均为套管式换热管,熔盐与水或蒸汽主要是逆流换热。该单元中的渣粒储存包1的设立是为了保证熔盐余热锅炉3的稳定连续运行,其容积大小根据熔渣出炉时序及产量决定。在自流床固体粒子余热锅炉2和熔盐余热锅炉3中间连接处设置的高温熔盐罐8和低温熔盐罐9,用于存储液态熔盐,保持稳定供给。高温熔盐处于常压状态,避免了高温锅炉管束磨损后发生爆管现象,有效提高了锅炉的安全系数。
最后说明的是,以上实施例仅用以说明本发明的技术方案而非限制,尽管参照较佳实施例对本发明进行了详细说明,本领域的普通技术人员应当理解,可以对本发明的技术方案进行修改或者等同替换,而不脱离本技术方案的宗旨和范围,其均应涵盖在本发明的权利要求范围当中。
技术特征:
1.一种高温渣粒余热回收系统,其特征在于:包括依次连通的渣粒储存包、自流床固体粒子余热锅炉、熔盐余热锅炉;所述自流床固体粒子余热锅炉与熔盐余热锅炉之间设有用于储存及交换热量的熔盐储热系统。
2.根据权利要求1所述的一种高温渣粒余热回收系统,其特征在于:所述熔盐储热系统采用熔盐进行热量交换,与自流床固体粒子余热锅炉的高温颗粒换热后升温至高温熔盐,与饱和水换热后,饱和水升温产生蒸汽,换热后高温熔盐降温至低温熔盐,并循环至自流床固体粒子余热锅炉的高温侧循环换热。
3.根据权利要求1所述的一种高温渣粒余热回收系统,其特征在于:自流床固体粒子余热锅炉与渣粒储存包连通的一侧为熔盐换热区,另一侧为水换热区;水换热区换热产生的饱和水连通至熔盐余热锅炉。
4.根据权利要求3所述的一种高温渣粒余热回收系统,其特征在于:所述自流床固体粒子余热锅炉内熔盐换热区的换热管叉逆流布置,水换热区的换热管叉逆流布置。
5.根据权利要求1所述的一种高温渣粒余热回收系统,其特征在于:所述熔盐余热锅炉沿内部水流动方向依次设有蒸发器、过热器、汽包;所述蒸发器、过热器均为套管式换热管,液态熔盐在套管式换热管内侧流通,水或蒸汽在套管式换热管外侧流通。
6.根据权利要求5所述的一种高温渣粒余热回收系统,其特征在于:所述蒸发器、过热器内的套管逆流布置。
7.根据权利要求2所述的一种高温渣粒余热回收系统,其特征在于:所述熔盐储热系统内设有用于暂时存储高温熔盐的高温熔盐罐、以及用于暂时存储低温熔盐的低温熔盐罐。
8.一种高温渣粒余热回收方法,其特征在于,包括以下步骤:
高温渣粒与低温熔盐及常温水依次换热,产生高温熔盐及饱和水;
高温熔盐与饱和水进行换热,产生低温熔盐及蒸汽。
9.根据权利要求8所述的一种高温渣粒余热回收方法,其特征在于,所述高温熔盐及低温熔盐均为液态熔盐。
10.根据权利要求8或9所述的一种高温渣粒余热回收方法,其特征在于,熔盐是由几种熔盐组成的混合盐。
技术总结
本发明属于炉渣回收领域,涉及一种高温渣粒余热回收系统及回收方法。包括依次连通的渣粒储存包、自流床固体粒子余热锅炉、熔盐余热锅炉;所述自流床固体粒子余热锅炉与熔盐余热锅炉之间设有用于储存及交换热量的熔盐储热系统。高温渣粒经过渣粒储存包,保证渣粒连续性进入到自流床固体粒子余热锅炉中,上部与液态熔盐进行热交换后,与下部的水进行热交换,将高温渣粒冷却至200℃以下,由下端的出料口排出。高温熔盐进入到熔盐余热锅炉,先后经过蒸发器、过热器与饱和水进行换热,形成350‑500℃的蒸汽。本发明利用熔盐储热系统回收高温渣粒的显热,并利用高温熔盐处于常压状态避免了高温锅炉管束磨损后发生爆管现象,有效提高了锅炉的安全系数。
技术研发人员:李朋;郭英;李志;雍海泉
受保护的技术使用者:重庆赛迪热工环保工程技术有限公司;中冶赛迪技术研究中心有限公司
技术研发日:2021.04.12
技术公布日:2021.06.22
本文用于企业家、创业者技术爱好者查询,结果仅供参考。