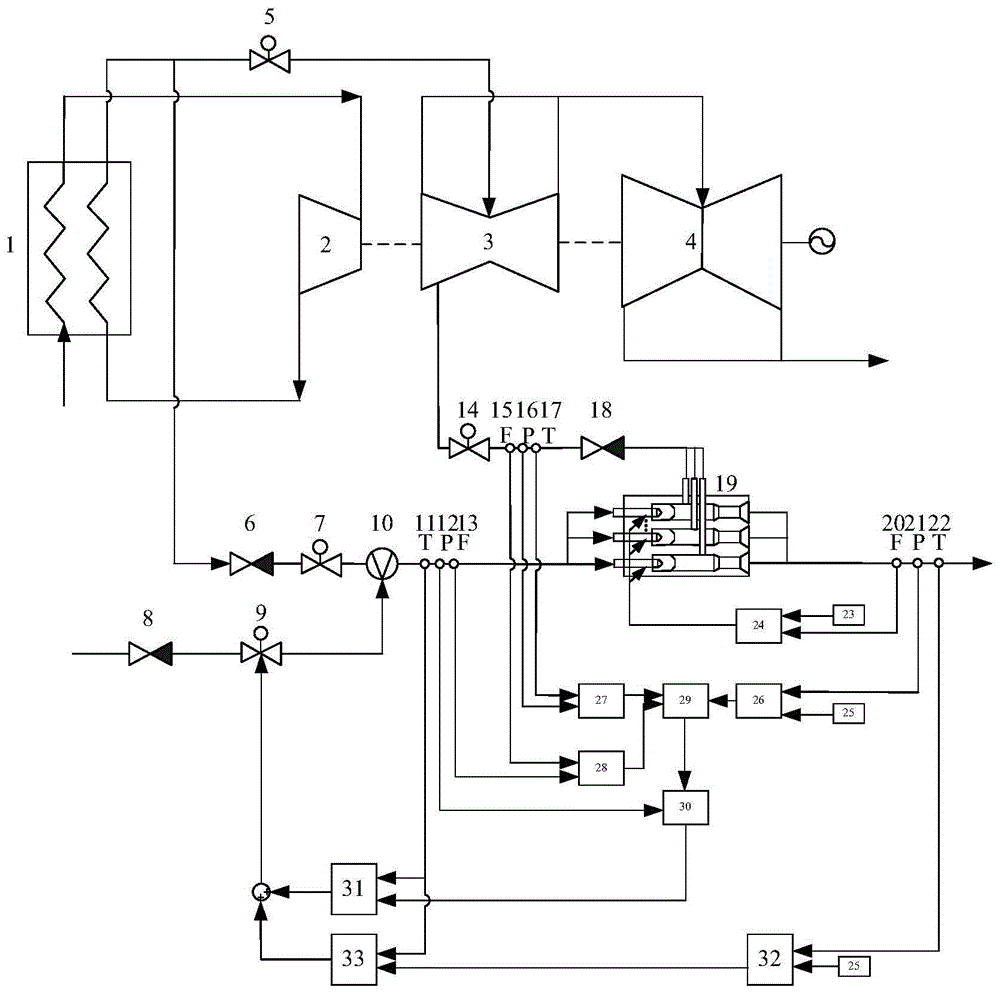
本发明涉及火电机组抽汽供热系统的自动控制领域,具体涉及一种耦合压力匹配器的热再抽汽供热控制系统及方法。
背景技术:
随着我国经济、工业的快速发展,工业用汽和居民用汽量也随之增加,燃煤机组热电联产仍是满足当前的用汽负荷的重要途径之一。同时,随着我国电力体制改革和节能减排政策的深入和完善,发电企业在市场开放和竞价上网的竞争中,既要保证安全生产,同时对机组运行经济性的要求更加迫切,因此如何有效地降低热电联产供热热耗、实现热电解耦是当前供热技术的研究重点。
目前汽轮机的再热器热段、再热器冷段蒸汽、中压缸排汽等都可以选作供热蒸汽。可以根据不同用户用汽参数需求,选择合理的蒸汽供热方式实现蒸汽的梯级利用。以较高参数的工业用汽为研究对象,多选用热再和冷再抽汽进行供热,经分析,由于热段抽汽温度高,在满足同样供热量的前提下,则抽汽量少,凝汽量增加(在同样进汽量的条件下),则机组发电量增加。当然热段抽汽的焓值耗用的锅炉热量多,但考虑到锅炉的运行方式,在蒸发量不变时,锅炉燃煤量不变。因此,相比在冷段抽汽,减少过热蒸汽量只会排烟温度升高。因此单从热经济上分析,利用热段抽汽比冷段抽汽更合适合适。同时冷段抽汽的抽汽量受再热器超温的限制,一般锅炉厂给出的数据是锅炉蒸发量的5%左右。由于冷段抽汽量受限制,在要求供汽量较大,温度较高时一般采用热段抽汽。
目前常规的供汽手段及控制方法主要有以下几种:
1.汽轮机抽汽调压方式供汽,如旋转隔板,调节蝶阀,座缸阀等都是利用阀门节流的方式调节蒸汽压力,或者直接通过高压蒸汽减温减压降低到热用户所需参数。这种供热方式都有很大的节流作用,造成非供热蒸汽的节流损失,尤其是在供热量占总流量的份额较小时,节流损失更大,使其牺牲了蒸汽的作功能力,浪费了大量的高压蒸汽作功能力。
2.通过单喷嘴压力匹配器进行供热,采用高压蒸汽抽吸低压蒸汽,混合后达到所需蒸汽参数,由于负荷发生变化,蒸汽参数随之改变,相同的压力匹配器结构会造成抽吸比例不同,使得可控效果不好。虽然热利用效率较高,但受机组负荷变化和蒸汽参数影响较大,可调范围较窄,流量无法调节,不适合机组变工况运行。目前可调式多喷嘴压力匹配器是在单喷嘴的基础上发展起来的新型压力匹配器,内设有多个喷射器,每个喷射器有独立的制动装置,可以统一控制匹配器的压力和流量,在较大的蒸汽流量范围内调节,从而给热电厂热电解耦调节控制提供了有利的手段,但是目前采用压力匹配器出口温度、压力控制通过传统pid控制针阀开度和减温器减温水量,控制效果一般,具有较大的惯性和延时性。
技术实现要素:
为了解决上述现有技术存在的问题,本发明提出了一种耦合压力匹配器的热再抽汽供热控制系统及方法,本发明采用多喷嘴针阀控制压力匹配器的出口压力和流量,可以使得蒸汽流量在较大的范围内实现自动控制,解决了压力匹配器流量不能调节的矛盾;采用串级控制方法进行压力匹配器出口汽温的控制,由两个串接工作的控制器构成的双闭环控制系统,使用副控制器对减温水干扰进行超前控制,减少干扰对出口汽温的影响,解决压力匹配器出口汽温的滞后和时间常数很大、减温水干扰作用强而频繁、难以控制精确的难题。
为了达到上述目的,本发明采用如下技术方案:
一种耦合压力匹配器的热再抽汽供热控制系统,锅炉1内换热器出口与汽轮机的高压缸2入口相连,高压缸2出口与锅炉1内再热器入口相连,锅炉1内再热器出口分别与中调门5和热再抽汽止回阀6相连,中调门5与中压缸3相连,随后与低压缸4相连;热再抽汽止回阀6与热再抽汽调节阀7相连,减温水止回阀8与减温水调节阀9相连,随后热再抽汽调节阀7和减温水调节阀9与减温器10相连,随后减温器10依次与驱动蒸汽温度传感器11、驱动蒸汽压力传感器12和驱动蒸汽流量传感器13相连,中压缸3与吸入蒸汽调节阀14连接,随后吸入蒸汽调节阀14依次与吸入蒸汽流量传感器15、吸入蒸汽压力传感器16和吸入蒸汽温度传感器17相连,随后与吸入蒸汽止回阀18相连,驱动蒸汽流量传感器13和吸入蒸汽止回阀18与可调式多喷嘴压力匹配器19相连,随后可调式多喷嘴压力匹配器19依次与供汽母管蒸汽流量传感器20、供汽母管蒸汽压力传感器21和供汽母管蒸汽温度传感器22相连;用户侧实际需求供热流量23和供汽母管蒸汽流量传感器20与压力匹配器针阀控制模块24相连,随后压力匹配器针阀控制器24与可调式多喷嘴压力匹配器19相连;供汽母管蒸汽压力传感器21和机组供汽出口温度设定值25与供热母管理论焓值计算模块26连接,吸入蒸汽压力传感器16和吸入蒸汽温度传感器17与吸入蒸汽焓值计算模块27相连,驱动蒸汽流量传感器13和吸入蒸汽流量传感器15和当前工况引射系数计算模块28相连,随后供热母管理论焓值计算模块26、吸入蒸汽焓值计算模块27和当前工况引射系数计算模块28与驱动蒸汽理论焓值计算模块29相连,驱动蒸汽压力传感器12和驱动蒸汽理论焓值计算模块29与驱动蒸汽理论温度计算模块30相连,驱动蒸汽温度传感器11和驱动蒸汽理论温度计算模块30与减温水调节阀超前控制器31相连,机组供汽出口温度设定值25和供汽母管蒸汽温度传感器22与减温水调节阀主控制器32相连,驱动蒸汽温度传感器11和减温水调节阀主控制器32与减温水调节阀副控制器33相连,随后减温水调节阀超前控制器31和减温水调节阀副控制器33与减温水调节阀9相连。
所述可调式多喷嘴压力匹配器19内设有多个喷射器,每个喷射器有独立的制动装置,能够统一控制压力和流量在较大的蒸汽流量范围内调节。
所述压力匹配器针阀控制器24、减温水调节阀超前控制器31、减温水调节阀主控制器32和减温水调节阀副控制器33均采用pid控制器。
所述的一种耦合压力匹配器的热再抽汽供热控制系统的控制方法为:锅炉1通过其内换热器将热量传递给锅炉给水,使得锅炉给水变为高温高压的蒸汽,随后驱动高压缸2作功发电,高压缸2排汽进入锅炉1内再热器中进行换热,然后高温蒸汽通过中调阀5驱动中压缸3、低压缸4进行作功发电;在中调阀5前和锅炉1再热器后引出部分高温蒸汽,通过热再抽汽止回阀6、热再抽汽调节阀7送入减温器10,通过减温水调节阀9喷淋的减温水调节进入可调式多喷嘴压力匹配器19的驱动蒸汽温度,从而驱动中压缸3的低温抽汽,经过吸入蒸汽调节阀14和吸入蒸汽止回阀18进入可调式多喷嘴压力匹配器19进行混合至所需的蒸汽参数供热用户使用;
将供汽母管蒸汽流量传感器20测量的实际供汽母管蒸汽流量和用户侧实际需求供热流量23送入压力匹配器针阀控制模块24进行计算产生针阀控制指令,从而控制多喷嘴压力匹配器19的开度满足出口流量和压力需求;将供汽母管蒸汽压力传感器21测量的母管蒸汽压力和机组供汽出口温度设定值25送入供热母管理论焓值计算模块26计算获得供热母管理论焓值;将吸入蒸汽压力传感器16测量的吸入蒸汽压力和吸入蒸汽温度传感器17测量的吸入蒸汽温度送入吸入蒸汽焓值计算模块27计算获得吸入蒸汽焓值;将驱动蒸汽流量传感器13和吸入蒸汽流量传感器15测量的蒸汽流量送入当前工况引射系数计算模块28计算获得引射系数,然后将供热母管理论焓值计算模块26、吸入蒸汽焓值计算模块27、当前工况引射系数计算模块28计算的结果送入驱动蒸汽理论焓值计算模块29进行能量平衡计算获得驱动蒸汽理论焓值,随后将计算的驱动蒸汽理论焓值和驱动蒸汽压力传感器12测量的驱动蒸汽压力送入驱动蒸汽理论温度计算模块30计算获得驱动蒸汽理论温度,随后将驱动蒸汽温度传感器11测量的蒸汽温度和驱动理论温度同时送入减温水调节阀超前控制器31获得减温水调阀指令一;另一方面通过机组供汽出口温度设定值25和供汽母管蒸汽温度传感器22测得的供汽母管蒸汽温度送入减温水调节阀主控制器32,随后将计算结果与驱动蒸汽温度传感器11测得的驱动蒸汽温度一起送入减温水调节阀副控制器33中计算获得减温水调阀指令二;将减温水调阀指令一和减温水调阀指令二叠加作用从而控制减温水调节阀9的开度,实现压力匹配器供汽出口温度的精确控制。
下面对现有技术的缺点与本发明技术方案的优点论述如下:
(1)目前供热机组多采用减温减压阀进行供热控制,其中的控制方法多以供热出口压力为调节目的,并不能实现对流量的精确控制。由于供热管道较长,惯性较大,供热压力的变化具有较大的滞后性,以此来控制供热流量满足热用户需求,较为粗放;同时减温减压势必会造成较大的节流作用,浪费了大量的高温蒸汽能量。
(2)通过单喷嘴压力匹配器进行供热,采用高压蒸汽抽吸低压蒸汽,混合后达到所需蒸汽参数,避免了高温蒸汽的节流损失。但由于机组负荷发生变化,抽汽参数随之改变,相同的压力匹配器结构会造成抽吸比例不同,使得可控效果不好。虽然热利用效率较高,但受机组负荷变化和蒸汽参数影响较大,可调范围较窄,流量无法调节,不适合机组变工况运行。
(3)本发明的控制系统及方法是基于可调式多喷嘴压力匹配器来进行控制,内设有多个喷射器,每个喷射器有独立的制动装置,可以统一控制匹配器的压力和流量,在较大的蒸汽流量范围内调节,从而给热电厂热电解耦调节控制提供了有利的手段,但是目前采用常规pid单回路控制方法,通过控制针阀开度和减温器减温水量,直接控制压力匹配器出口温度、压力,控制效果一般,具有较大的惯性和延时性。
(4)本发明采用调节针阀开启来实现压力匹配器出口流量和压力的调节,同时选取串级控制系统对压力匹配器汽温进行调节,通过引入驱动蒸汽温度这一直接反应减温水扰动的变量组成副控制器回路,完成出口汽温的粗调控制,同时使用主控制器回路完成出口汽温的细调,通过这两条回路的配合控制完成普通单回路控制系统很难达到的控制效果,削弱减温水对出口汽温的扰动影响;除此之外,在机组变负荷工况下,驱动蒸汽和吸入蒸汽的参数实时变化,在通过压力匹配器的混合后,反映到出口汽温势必会有一定的滞后,本发明可以超前获得驱动蒸汽的温度前馈,可以削弱机组工况变化造成驱动蒸汽和吸入蒸汽参数变化带来的扰动影响,控制更为精确。
附图说明
图1为本发明耦合压力匹配器的热再抽汽供热控制系统连接示意图。
具体实施方式
下面结合附图和具体实施方式对本发明作进一步详细说明。
如图1所示,本发明一种耦合压力匹配器的热再抽汽供热控制系统,锅炉1内换热器出口与汽轮机的高压缸2入口相连,高压缸2出口与锅炉1内再热器入口相连,锅炉1内再热器出口分别与中调门5和热再抽汽止回阀6相连,中调门5与中压缸3相连,随后与低压缸4相连;热再抽汽止回阀6与热再抽汽调节阀7相连,减温水止回阀8与减温水调节阀9相连,随后热再抽汽调节阀7和减温水调节阀9与减温器10相连,随后减温器10依次与驱动蒸汽温度传感器11、驱动蒸汽压力传感器12和驱动蒸汽流量传感器13相连,中压缸3与吸入蒸汽调节阀14连接,随后吸入蒸汽调节阀14依次与吸入蒸汽流量传感器15、吸入蒸汽压力传感器16和吸入蒸汽温度传感器17相连,随后与吸入蒸汽止回阀18相连,驱动蒸汽流量传感器13和吸入蒸汽止回阀18与可调式多喷嘴压力匹配器19相连,随后可调式多喷嘴压力匹配器19依次与供汽母管蒸汽流量传感器20、供汽母管蒸汽压力传感器21和供汽母管蒸汽温度传感器22相连;用户侧实际需求供热流量23和供汽母管蒸汽流量传感器20与压力匹配器针阀控制模块24相连,随后压力匹配器针阀控制器24与可调式多喷嘴压力匹配器19相连;供汽母管蒸汽压力传感器21和机组供汽出口温度设定值25与供热母管理论焓值计算模块26连接,吸入蒸汽压力传感器16和吸入蒸汽温度传感器17与吸入蒸汽焓值计算模块27相连,驱动蒸汽流量传感器13和吸入蒸汽流量传感器15和当前工况引射系数计算模块28相连,随后供热母管理论焓值计算模块26、吸入蒸汽焓值计算模块27和当前工况引射系数计算模块28与驱动蒸汽理论焓值计算模块29相连,驱动蒸汽压力传感器12和驱动蒸汽理论焓值计算模块29与驱动蒸汽理论温度计算模块30相连,驱动蒸汽温度传感器11和驱动蒸汽理论温度计算模块30与减温水调节阀超前控制器31相连,机组供汽出口温度设定值25和供汽母管蒸汽温度传感器22与减温水调节阀主控制器32相连,驱动蒸汽温度传感器11和减温水调节阀主控制器32与减温水调节阀副控制器33相连,随后减温水调节阀超前控制器31和减温水调节阀副控制器33与减温水调节阀9相连。
作为本发明的优选实施方式,所述可调式多喷嘴压力匹配器19内设有多个喷射器,每个喷射器有独立的制动装置,能够统一控制压力和流量在较大的蒸汽流量范围内调节。
作为本发明的优选实施方式,所述压力匹配器针阀控制器24、减温水调节阀超前控制器31、减温水调节阀主控制器32和减温水调节阀副控制器33均采用pid控制器。pid控制器基本原理如下:
其中,p(t)为控制器输出控制指令;k为设定的参数增益;e(t)为t时刻,控制器实际输入值与该控制器模块理论设定值之间的偏差;ti表示积分时间,td表示微分时间。
作为本发明的优选实施方式,所述当前工况引射系数计算模块28可以通过驱动蒸汽流量传感器13和吸入蒸汽流量传感器15所测得的实际蒸汽流量计算获得压力匹配器的引射系数。计算公式如下:
μ=gh/gp
其中:gh为吸入蒸汽流量;gp为驱动蒸汽流量。
作为本发明的优选实施方式,所述供热母管理论焓值计算模块26、吸入蒸汽焓值计算模块27、驱动蒸汽理论焓值计算模块29与驱动蒸汽理论温度计算模块30采用水和水蒸气热力学性质计算公式进行求解,获得蒸汽焓值和温度值。计算公式如下:
其中:p、t、h分别为压力、温度、焓值,p*、t*、h*为定值,ni、ii、ji、ni1、ji1、ni2、ii2、ji2为一组常数组,r为气体常数。
如图1所示,本发明所述的一种耦合压力匹配器的热再抽汽供热控制系统的控制方法为:锅炉1通过其内换热器将热量传递给锅炉给水,使得锅炉给水变为高温高压的蒸汽,随后驱动高压缸2作功发电,高压缸2排汽进入锅炉1内再热器中进行换热,然后高温蒸汽通过中调阀5驱动中压缸3、低压缸4进行作功发电;在中调阀5前和锅炉1再热器后引出部分高温蒸汽,通过热再抽汽止回阀6、热再抽汽调节阀7送入减温器10,通过减温水调节阀9喷淋的减温水调节进入可调式多喷嘴压力匹配器19的驱动蒸汽温度,从而驱动中压缸3的低温抽汽,经过吸入蒸汽调节阀14和吸入蒸汽止回阀18进入可调式多喷嘴压力匹配器19进行混合至所需的蒸汽参数供热用户使用;
将供汽母管蒸汽流量传感器20测量的实际供汽母管蒸汽流量和用户侧实际需求供热流量23送入压力匹配器针阀控制模块24进行计算产生针阀控制指令,从而控制多喷嘴压力匹配器19的开度满足出口流量和压力需求;将供汽母管蒸汽压力传感器21测量的母管蒸汽压力和机组供汽出口温度设定值25送入供热母管理论焓值计算模块26计算获得供热母管理论焓值;将吸入蒸汽压力传感器16测量的吸入蒸汽压力和吸入蒸汽温度传感器17测量的吸入蒸汽温度送入吸入蒸汽焓值计算模块27计算获得吸入蒸汽焓值;将驱动蒸汽流量传感器13和吸入蒸汽流量传感器15测量的蒸汽流量送入当前工况引射系数计算模块28计算获得引射系数,然后将供热母管理论焓值计算模块26、吸入蒸汽焓值计算模块27、当前工况引射系数计算模块28计算的结果送入驱动蒸汽理论焓值计算模块29进行能量平衡计算获得驱动蒸汽理论焓值,随后将计算的驱动蒸汽理论焓值和驱动蒸汽压力传感器12测量的驱动蒸汽压力送入驱动蒸汽理论温度计算模块30计算获得驱动蒸汽理论温度,随后将驱动蒸汽温度传感器11测量的蒸汽温度和驱动理论温度同时送入减温水调节阀超前控制器31获得减温水调阀指令一;另一方面通过机组供汽出口温度设定值25和供汽母管蒸汽温度传感器22测得的供汽母管蒸汽温度送入减温水调节阀主控制器32,随后将计算结果与驱动蒸汽温度传感器11测得的驱动蒸汽温度一起送入减温水调节阀副控制器33中计算获得减温水调阀指令二;将减温水调阀指令一和减温水调阀指令二叠加作用从而控制减温水调节阀9的开度,实现压力匹配器供汽出口温度的精确控制。
本文用于企业家、创业者技术爱好者查询,结果仅供参考。