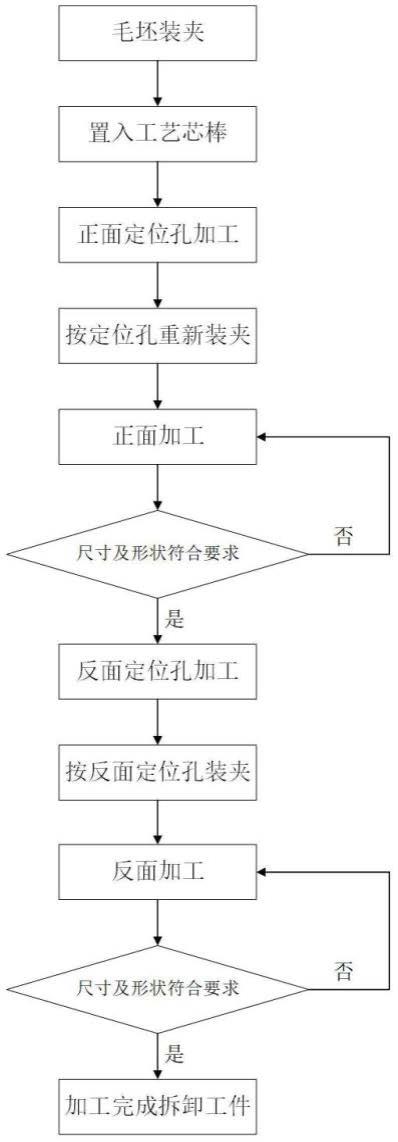
1.本发明涉及机械加工技术领域,尤其涉及一种阵列复材管夹层正反面高精度加工方法。
背景技术:
2.阵列复材管是一种蜂窝结构,由单个复合材料管二维密排制成,如附图2所示。阵列复材管具有低密度、高轴向刚度、良好的热稳定性、抗冲击性和耐腐蚀等优点,可应用于航空航天、交通汽车等领域。在服役过程中,阵列复材管作为夹层,其正反面与上下蒙皮胶接装配形成“三明治”结构,同时其刚度较强,无法通过弯折与蒙皮贴合,需机械加工其正反面获得所需的尺寸和精度。在分别加工阵列复材管夹层正反表面时,存在定位基准的转化,但在阵列复材管夹层的制备过程中,其复材管单元的圆柱度较差,导致在成型阵列过程中单元之间的相对位置精度较差,直接使用复材管单元定位将导致夹层正反面的相对位置和相对姿态存在误差,影响整个夹层在厚度方向上的均匀性,一方面厚度的偏差影响夹层结构法向热膨胀量均匀性,另一方面姿态的偏差使得夹层与蒙皮的面形无法准确配合,导致在二者胶结装配过程中产生过大的结构内应力,制造的“三明治”构件不能满足服役要求。
3.专利cn202110362500.x提出一种使用同一阵列复材管单元作为定位基准实现二次加工的装夹方法,其定位精度受到单元制备误差的影响,且定位误差不可控制;专利cn202110844261.1提出在工件和工装夹具上钻孔的方法以提高装夹成功率的加工方法,但其操作复杂,且不适用于双面加工。
技术实现要素:
4.针对上述问题,本发明提出一种阵列复材管夹层正反面高精度加工方法,在加工夹层结构正面之前,在阵列复材管单元内部加工正面定位基准,当正面加工完成后,基于当前坐标系,加工反面所需的定位基准,有效避免了阵列复材管单元制备误差和定位基准偏移导致的正反面相对位置误差。使用该方法加工的阵列复材管夹层正反面相对位置精度较高,有利于提升夹层结构产品合格率,降低返修率,具有显著的经济效益,同时该方法可推广至具有双面加工需求的蜂窝构件加工,有利于提升行业整体的加工水平。本发明采用的技术手段如下:
5.一种阵列复材管夹层正反面高精度加工方法,包括如下步骤:
6.正面加工:s1、将正面加工夹具安装在机床操作台上,把阵列复材管夹层结构毛坯装夹至正面加工夹具;
7.s2、根据加工定位需求,在阵列复材管毛坯四个单元内分别置入辅助垫圈,使其底端与正面加工夹具接触,再将四根工艺芯轴分别放置在四个辅助垫圈上,最后将工艺芯轴与阵列复材管毛坯固连;
8.s3、将定位孔加工刀具安装至数控机床上,开启数控机床,按正面加工夹具上的预留位置在两个正面定位孔用工艺芯轴上加工出正面定位孔;
9.s4、按加工出的正面定位孔重新将阵列复材管毛坯可靠装夹至正面加工夹具上,将刀具安装至数控机床上,按尺寸要求进行加工,获得符合要求的工件正面;
10.反面加工:s5、按反面加工夹具上的预留位置,在两根反面定位孔用工艺芯轴上加工出反面定位孔,拆卸工件,取下两根已加工正面定位孔的工艺芯轴,取下两根正面定位孔的辅助垫圈;
11.s6、将反面加工夹具安装在机床操作台上,按加工出的反面定位孔将已完成正面加工的阵列复材管毛坯装夹至反面加工夹具上,开启数控机床,按尺寸要求进行加工,获得符合要求的工件反面。
12.进一步地,所述辅助垫圈尺寸小于阵列复材管单元尺寸,使其能便利置入阵列复材管单元中,且其中心有大于定位孔的通孔。
13.进一步地,所述的步骤s2中,四个单元,两个用于正面加工装夹,两个用于反面加工装夹,其位置与夹具上设置的与定位销相连的孔位置相符。
14.进一步地,所述的步骤s2中,工艺芯轴与阵列复材管毛坯通过胶结的方式固连,所用的胶可通过相应方法去除,无残留。
15.进一步地,所述工艺芯轴和辅助垫圈均存在预设尺寸的多种型号,辅助垫圈小于工艺芯轴的高度,工艺芯轴放置在辅助垫圈上后,总高度小于加工后阵列复材管夹层的最小剩余高度。
16.进一步地,所述反面加工夹具的面型与工件正面相匹配。
17.进一步的,所述步骤s3、s5中,在工艺芯轴上加工的定位孔通过钻孔-扩孔-铰孔的工序得到。
18.本发明在夹层结构正反面加工完成后,基于当前坐标系,在阵列复材管孔格内部加工反面所需的定位基准,加工误差仅与钻孔定位误差和下面夹具芯轴与定位工艺孔的间隙相关,有效避免了阵列复材管单元制备误差和定位基准偏移导致的正反面相对位置误差,显著提升了定位可靠性,同时正反面相对位置误差与正面加工的定位精度无关,有利于提高正面的装夹效率,提升生产效率,加工过程中的定位基准都是通过机械加工获得的,所加工定位孔的精度远高于阵列复材管夹层的制备精度。该方法操作方便,具有较好的质量效益与经济效益,同时可为蜂窝类夹层结构双面加工提供一定的参考价值。
附图说明
19.为了更清楚地说明本发明实施例或现有技术中的技术方案,下面将对实施例或现有技术描述中所需要使用的附图做以简单地介绍,显而易见地,下面描述中的附图是本发明的一些实施例,对于本领域普通技术人员来讲,在不付出创造性劳动性的前提下,还可以根据这些附图获得其他的附图。
20.图1为本发明阵列复材管夹层正反面加工流程图。
21.图2为阵列复材管毛坯示意图。
22.图3为本发明工艺芯棒放置示意图。
23.图4为本发明正面定位孔加工示意图。
24.图5为本发明正面加工装夹示意图。
25.图6为本发明反面定位孔加工示意图。
26.图7为本发明反面加工装夹示意图。
27.图8为本发明加工完成后工件示意图。
28.图中:1、正面加工夹具,2、阵列复材管夹层结构毛坯,3、反面定位孔用工艺芯轴,4、正面定位孔用工艺芯轴,5、反面定位孔用辅助垫圈,6、正面定位孔用辅助垫圈,7、定位孔加工刀具,8、正面加工定位销,9、反面加工定位销,10、反面加工夹具,11、加工完成后工件。
具体实施方式
29.为使本发明实施例的目的、技术方案和优点更加清楚,下面将结合本发明实施例中的附图,对本发明实施例中的技术方案进行清楚、完整地描述,显然,所描述的实施例是本发明一部分实施例,而不是全部的实施例。基于本发明中的实施例,本领域普通技术人员在没有做出创造性劳动前提下所获得的所有其他实施例,都属于本发明保护的范围。
30.如图1所示,本发明实施例公开了一种阵列复材管夹层正反面高精度加工方法,以满足阵列复材管夹层在机械加工领域中双面加工的需求,具体加工工艺路径如下:正面装夹、置入辅助垫圈和工艺芯轴、正面定位孔钻孔、按照正面定位孔装夹工件、对刀、正面加工、反面定位孔钻孔、拆卸工件、去除辅助垫圈和正面定位孔用芯轴、按照反面定位孔装夹工件、对刀、反面加工,拆卸工件,完成加工。
31.如图3~8所示,具体包括如下步骤:
32.正面加工:s1、将正面加工夹具1安装在机床操作台上,把阵列复材管夹层结构毛坯2可靠装夹至正面加工夹具;
33.s2、根据加工定位需求,在阵列复材管毛坯四个单元内分别置入辅助垫圈,使其底端与正面加工夹具接触,再将四根工艺芯轴分别放置在对应的正面定位孔用辅助垫圈6和反面定位孔用辅助垫圈5上,最后将工艺芯轴与阵列复材管毛坯固连;其中,四个单元,两个用于正面加工装夹,两个用于反面加工装夹,其位置与夹具上设置的与正面加工定位销8、反面加工定位销9相连的孔位置相符,本实施例中,工艺芯轴与阵列复材管毛坯通过胶结的方式固连,所用的胶可通过相应方法去除,无残留。
34.s3、将定位孔加工刀具7安装至数控机床上,开启数控机床,按正面加工夹具上的预留位置在两个正面定位孔用工艺芯轴4上加工出正面定位孔;
35.s4、通过正面加工定位销对正面加工工件的一面两销定位,按加工出的正面定位孔重新将阵列复材管毛坯可靠装夹至正面加工夹具上,将刀具安装至数控机床上,按尺寸要求进行加工,获得符合要求的工件正面;正面加工完毕后对正面定位孔用辅助垫圈进行拆除;
36.反面加工:s5、按反面加工夹具10上的预留位置,在两根反面定位孔用工艺芯轴3上加工出反面定位孔,拆卸工件,取下两根已加工正面定位孔的工艺芯轴,取下两根正面定位孔的辅助垫圈;
37.s6、将反面加工夹具安装在机床操作台上,通过反面加工定位销对反面加工工件的一面两销定位,按加工出的反面定位孔将已完成正面加工的阵列复材管毛坯装夹至反面加工夹具上,开启数控机床,按尺寸要求进行加工,获得符合要求的工件反面,至此完成阵列复材管夹层的高位姿精度双面加工,得到加工完成后工件11。
38.本实施例中,所述辅助垫圈尺寸小于阵列复材管单元尺寸,使其能便利置入阵列
复材管单元中,且其中心有大于定位孔的通孔。
39.所述工艺芯轴和辅助垫圈均存在预设尺寸的多种型号,辅助垫圈小于工艺芯轴的高度,工艺芯轴放置在辅助垫圈上后,总高度小于加工后阵列复材管夹层的最小剩余高度。
40.所述反面加工夹具的面型与工件正面相匹配。
41.本实施例中,所述定位孔加工刀具选用钻头,所述步骤s3、s5中,在工艺芯轴上加工的定位孔通过钻孔-扩孔-铰孔的工序得到,其精度远高于阵列复材管单元的制备精度。
42.最后应说明的是:以上各实施例仅用以说明本发明的技术方案,而非对其限制;尽管参照前述各实施例对本发明进行了详细的说明,本领域的普通技术人员应当理解:其依然可以对前述各实施例所记载的技术方案进行修改,或者对其中部分或者全部技术特征进行等同替换;而这些修改或者替换,并不使相应技术方案的本质脱离本发明各实施例技术方案的范围。
再多了解一些
本文用于创业者技术爱好者查询,仅供学习研究,如用于商业用途,请联系技术所有人。