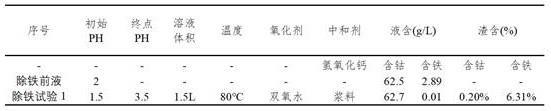
1.本发明属于湿法冶金领域,具体涉及一种降低钴原料浸出液除铁尾料含钴的方法。
背景技术:
2.在含钴原料的湿法冶金过程中,钴原料的浸出液一般含有多种杂质金属元素,例如cu、mn、fe、cd等,钴冶金常用的除杂方法主要为p204萃取除杂以及离子交换柱除杂法。浸出液中的fe离子过多会造成p204萃取过程分相困难,同时还会对有机的寿命造成一定程度的影响。萃取除杂后液在进入电积钴生产前一般还需要进行离子交换柱深度除杂,过高的fe离子浓度会使得离子交换树脂降解,对树脂造成不可逆的破坏,所以一般需要在萃取前对浸出液进行除铁,常见的除铁方式包括黄钠铁矾法和中和水解法两种,这两种方式一般都会造成不同程度的渣含钴情况,进而使得主金属元素进入铁渣中造成有价金属流失。
3.目前,对于硫酸体系的钴浸出液,一般采用对铁渣进行多次酸性洗涤的方式来降低除铁尾渣含钴,这种方式在造成大量试剂消耗的同时还会将铁元素重新反洗回钴体系造成生产成本升高。
4.硫酸体系钴浸出液的除铁一般有如下方式:第一种是中和水解法,该方法通过调节体系ph值并产生氢氧化铁沉淀完成除铁过程,但是这种方法产生的铁渣一般含钴较高,同时由于氢氧化铁自身的粘度较大会使得后续的压滤洗涤等过程变得复杂。第二种是黄钠铁矾除铁法,主要控制除铁过程的温度等条件使得铁元素以黄钠铁矾渣的形式从钴浸出液中脱出,第三种是针铁矿法除铁,这种方式产生的铁渣一般具有较高的含铁量,但是形成针铁矿的难度较大,工艺条件较前两种方式要苛刻的多。
技术实现要素:
5.本发明的目的是为了解决浸出液除铁尾料中含钴的问题,提供了一种降低钴原料浸出液除铁尾料含钴的方法。
6.为了达到上述目的,本发明采用以下技术方案:一种降低钴原料浸出液除铁尾料含钴的方法,包括以下步骤:步骤1、首先将初始ph为2.0-2.5的钴浸出液的ph利用硫酸调整至1.0-1.5,钴浸出溶液中分别含co 50-70g/l,ca 0.5-1.2g/l,fe 2.5-3.5g/l, cu 1-2 g/l,al 0.2-2g/l;步骤2、同时将温度升高至75-95℃,并持续搅拌,搅拌转速为200-500r/min;步骤3、之后将氧化剂加入到溶液中,保证溶液中的二价铁离子被完全氧化;步骤4、之后加入黄钠铁矾晶种浆料,并分次加入中和剂直至溶液ph调至2.5-3.0,且使用中和剂调节溶液ph时,ph为1.5-2.0时保持1-2h,ph为2.0-2.5保持1-2h;步骤5、之后在ph为2.5-3.0陈化2-3h时间;步骤6、之后在50-150r/min的搅拌转速下用继续用中和剂将溶液的ph调整至3.5,之后搅拌半小时后压滤,从而得到含铁量低于0.01g/l的除铁尾液。
7.进一步地,步骤4中的中和剂由na2co3浆料、caco3浆料、ca(oh)2、cao浆料中的一种制备而成,且浆料的液固比为3-5:1;当中和剂为na2co3浆料时,钴浸出液与na2co3浆料体积比为15-20:1;当中和剂为caco3浆料时,钴浸出液与caco3浆料体积比为20-25:1,当中和剂为ca(oh)2时,浆料钴浸出液与ca(oh)2浆料体积比为15-20:1,当中和剂为cao浆料时,钴浸出液与cao浆料体积比为20-25:1。
8.进一步地,步骤3中氧化剂为工业氧气、30%的双氧水、稀释后的次氯酸钠、稀释后的氯酸钠的一种,且稀释后的次氯酸钠中有效氯3-5%,稀释后的氯酸钠中有效氯3-5%;当氧化剂为30%双氧水时,钴浸出液溶与30%双氧水体积比为110-120:1,当氧化剂为稀释后的次氯酸钠时,钴浸出液溶与稀释后的次氯酸钠用量为45-50:1,当氧化剂为稀释后的氯酸钠时,钴浸出液溶与稀释后的氯酸钠用量为40-45:1。
9.本发明相对于现有技术,具有以下有益效果:本发明利用黄钠铁矾的形成机理和晶体学原理控制溶液中黄钠铁矾在较低的ph下形成尽可能多的晶核,并在升高ph的过程中通过搅拌转速控制黄钠铁矾晶粒过速长大防止该过程黄钠铁矾晶体包覆钴离子,同时通过采用合适的氧化剂抑制二价钴离子的氧化以及改变中和剂的加入方式抑制钴离子的水解,进而降低除铁尾料含钴情况。可将以上方法应用于含铁溶液的除铁过程。
10.该除铁过程产生的铁渣为黄钠铁矾渣和中和水解法形成的氢氧化铁渣,目的是保证溶液中的铁离子可以全部形成铁渣实现铁元素与溶液的分离。该方法对环境友好,而且回收效率高,成本低。该方法可以保证产生的铁渣的主价金属含量较低。该方法可以保证产生铁渣中较低含量的主价金属可以在洗涤过程中回到洗水,且铁离子不会回到洗水。
具体实施方式
11.下面结合具体实施方式对本发明作进一步说明。
12.实施例1:步骤1、从生产现场取过滤后的钴浸出液1500ml,该溶液初始ph值为2.0,用硫酸调节其ph值为1.5作为原液待用并取样分析其各元素含量,溶液中金属元素浓度分别为co 62.5g/l、ca 0.6g/l、fe 2.89g/l、cu 1.1 g/l、al 0.2g/l。
13.步骤2、将原液放入烧杯并将其放置于水浴锅中加热至90℃保温,并持续搅拌,转速为500r/min。
14.步骤3、取13ml 30%的双氧水用导流管缓慢加入到溶液中,并用二价铁滴定检测法判定溶液中的二价铁离子被完全氧化。
15.步骤4、事先取25g氢氧化钙放于200ml烧杯中,并加入75ml水,将其搅拌均匀从而制备调整溶液ph的中和浆料100ml。
16.之后加入黄钠铁矾晶种浆料,将步骤4中制备好的浆料多次缓慢加入到烧杯中,并持续搅拌,保持转速为500r/min,直至ph为2.5-3.0,期间在ph为1.5-2.0时保持2h,ph为2.0-2.5保持1h,来保证黄钠铁矾充分形核。
17.步骤5、在ph为2.5-3.0时保温搅拌2h使溶液陈化,这个过程使得溶液中的铁离子充分转化为黄钠铁矾。
18.步骤6、将搅拌的转速调整为80r/min,并用步骤4制备的浆料将溶液ph调整到3.5保温30min,压滤取渣,并对铁渣进行洗涤。
19.将步骤6产生的铁渣烘干用于分析渣中的fe、co元素含量,以判定渣含钴情况。
20.实验结果见表1。
21.表1实施例一浸出液除铁过程参数及除铁后液及铁渣元素含量实施例2:步骤1、从生产现场取过滤后的钴浸出液40l,该溶液初始ph值为2.5,用硫酸调节其ph值为1.0作为原液待用并取样分析其各元素含量,溶液中金属元素浓度分别为co 69.8g/l、ca 0.5g/l、fe 3.5g/l、cu 1.2 g/l、al 0.8g/l。
22.步骤2、将钴浸出液加入60l钛反应釜中并将开启加热部件将溶液加热至95℃保温,并持续搅拌,转速为300r/min。
23.步骤3、取300ml次氯酸钠溶液稀释至800ml后,次氯酸钠中有效氯为 5%,用导流管缓慢加入到溶液中,并用二价铁滴定检测法判定溶液中的二价铁离子被完全氧化。
24.步骤4、取650g氢氧化钙分次用水3:1稀释后制备成2.6l浆料分次加入到反应釜中,并持续搅拌反应釜内溶液。
25.之后加入黄钠铁矾晶种浆料,将步骤4中制备好的浆料多次缓慢加入到烧杯中,并持续搅拌,保持转速为300r/min,直至ph为2.5-3.0,期间在ph为1.5-2.0时保持2h,ph为2.0-2.5保持1h,来保证黄钠铁矾充分形核。
26.步骤5、在ph为2.5-3.0时保温搅拌2h使溶液陈化,这个过程使得溶液中的铁离子充分转化为黄钠铁矾。
27.步骤6、将搅拌的转速调整为150r/min,并用步骤4制备的浆料将溶液ph调整到3.5保温30min,压滤取渣,并对铁渣进行洗涤。
28.将步骤6产生的铁渣烘干用于分析渣中的fe、co元素含量,以判定渣含钴情况。
29.实验结果见表2。
30.表2实施例一浸出液除铁过程参数及除铁后液及铁渣元素含量实施例3:步骤1、从生产现场取过滤后的钴浸出液60l,该溶液初始ph值为2.0,用硫酸调节
其ph值为1.0作为原液待用并取样分析其各元素含量,溶液中金属元素浓度分别为co 50.5g/l、ca 1.2g/l、fe 2.5g/l、cu 2.0 g/l、al 1.9g/l。
31.步骤2、将钴浸出液加入60l钛反应釜中并将开启加热部件将溶液加热至75℃保温,并持续搅拌,转速为200r/min。
32.步骤3、取500ml双氧水,用导流管缓慢加入到溶液中,并用二价铁滴定检测法判定溶液中的二价铁离子被完全氧化。
33.步骤4、取750g氢氧化钙分次用水3:1稀释后制备成3l浆料分次加入到反应釜中,并持续搅拌反应釜内溶液。
34.之后加入黄钠铁矾晶种浆料,将步骤4中制备好的浆料多次缓慢加入到烧杯中,并持续搅拌,保持转速为200r/min,直至ph为2.5-3.0,期间在ph为1.5-2.0时保持2h,ph为2.0-2.5保持1h,来保证黄钠铁矾充分形核。
35.步骤5、在ph为2.5-3.0时保温搅拌2h使溶液陈化,这个过程使得溶液中的铁离子充分转化为黄钠铁矾。
36.步骤6、将搅拌的转速调整为50r/min,并用步骤4制备的浆料将溶液ph调整到3.5保温30min,压滤取渣,并对铁渣进行洗涤。
37.将步骤6产生的铁渣烘干用于分析渣中的fe、co元素含量,以判定渣含钴情况。
38.实验结果见表3。
39.表3实施例一浸出液除铁过程参数及除铁后液及铁渣元素含量
再多了解一些
本文用于创业者技术爱好者查询,仅供学习研究,如用于商业用途,请联系技术所有人。