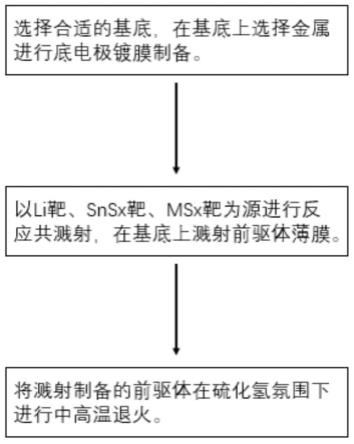
1.本发明属于全固态薄膜锂离子电池领域,尤其涉及一种反应共溅射制备固态电解质薄膜及其制备方法与应用。
背景技术:
2.全固态薄膜锂电池与普通锂电池原理及构成相似,都由正极、电解质和负极构成,并且在内电路中都是依靠li
在电极间的定向移动来产生电流。其不同之处也非常显著,那就是使用固态电解质,并且厚度非常的薄,常规薄膜电池厚度最多不超过100微米。薄膜锂电池体积小、能量密度大,有利于电池一体化、精密化。但这也就在一定程度上限制了全固态薄膜锂电池的发展,目前一般采用物理气相沉积(pvd)的方法进行电解质薄膜制备,比如磁控溅射、原子层沉积、电子束蒸发等工艺。通过pvd制备的薄膜电解质组织致密、厚度均匀,能有效解决界面阻抗的问题,全固态薄膜锂电池作为微米级电池可以有效应用于各种微能源装置,并集成至芯片中实现器件内供电的系统。
3.全固态薄膜电池目前常用的电解质薄膜有lipon薄膜、li2sio3薄膜、li7la3zr2o12薄膜。但目前应用的固体电解质薄膜室温离子电导率都较低,且制备速率普遍较慢。li4–
xmx
sn1–
x
s4作为一种新型固态电解质,室温离子电导率较高,可达到3.5*10-4
s/cm。并且其不同于其他硫化物电解质材料,根据软硬酸碱理论表明它空气稳定性好,不与空气反应释放硫化氢,有效降低了包装密封所带来的复杂性。相对地也进一步提高了薄膜电池的安全性。目前其制备主要采用烧结法制备得到,在厚度方面很难做到微米级别,同时普遍采用li2s作为li源导致成本也比较高。限制了其进一步的发展应用。适用于全固态薄膜锂电的li4–
xmx
sn1–
x
s4固态电解质薄膜制备成为研究的重点。
技术实现要素:
4.本发明的目的就是提供一种li4–
xmx
sn1–
x
s4固体电解质薄膜的制备方法及应用,通过该方法制备得到的固体电解质薄膜的厚度在0.5~3微米,适用于全固态薄膜锂电池的高电导率、高稳定性、大能量密度的应用要求。
5.本发明的目的是通过以下技术方案实现的:
6.一种反应共溅射制备固态电解质薄膜,固态电解质薄膜的化学式为li4–
xmx
sn1–
x
s4(0≤x《1),固态电解质薄膜通过将li靶、sns2靶和m靶对溅射基底进行共溅射制成。
7.优选的,m靶选自as、sb、ta、la、sb2s3、as2s3、tas2、la2s3中的一种。
8.优选的,固态电解质薄膜的厚度为0.5~3μm。
9.本发明还提供了一种电池,电池包含固态电解质薄膜。
10.本发明还提供了该固态电解质薄膜的制备方法,包括以下步骤:
11.(1)靶材选择:
12.按照化学式li4–
xmx
sn1–
x
s4选择li靶、sns2靶、m靶作为溅射靶材;
13.(2)共溅射制备前驱体薄膜:
14.将溅射基底置于溅射炉中,再以ar和h2s为溅射气体,用溅射靶材对溅射基底进行共溅射处理制备前驱体薄膜;
15.(3)制备固态电解质薄膜:
16.将前驱体薄膜密封,在惰性气体和h2s气体氛围下退火制备固态电解质薄膜。
17.优选的,步骤(2)中,ar气体流量为20~40sccm,h2s气体流量为0.5~5sccm,腔体压强为0.5~2pa,衬底温度为150~200℃,沉积时间为2~4h,靶材的射频溅射功率依照化学式调节。
18.优选的,li靶的射频溅射功率为100~150w,sns2靶的射频溅射功率为50~65w,m靶的射频溅射功率为40~70w。
19.优选的,溅射基底选自钠钙玻璃、石英玻璃、高导硅片、镀au/mo硅片中的至少一种。
20.优选的,步骤(3)中,h2s占惰性气体的比例为1~10%,退火温度为400~550℃,退火时间为2~4h。
21.优选的,溅射靶材尺寸为6*75mm,铜背靶尺寸为3*75mm。
22.与现有技术相比,本发明的优点在于:
23.(1)相比于以往的烧结法制备li4–
x
sb
x
sn1–
x
s4,本发明通过采用反应磁控共溅射的制备工艺,分别采用li靶、sns2靶、sb2s3靶作为溅射靶材,在一定h2s氛围下制备li4–
xmx
sn1–
x
s4固态电解质薄膜,降低了生产成本。薄膜成分标准、形貌完整、稳定性好,且厚度达到微米级别,约为0.5~3μm;
24.(2)相比于lipon的电解质薄膜,本发明不仅避免了特定靶材的制作,同时提高了溅射制备的速率,更为难得的是其在空气中能够稳定存在,同时由于掺杂sb
5
离子取代了部分sn
4
,其离子电导率也得到了较大提升。其最高离子电导率可达3.5*10-4
s/cm,可用于全固态薄膜锂离子电池的制备合成。
附图说明
25.此处的附图被并入说明书中并构成说明书的一部分,示出了符合本发明的实施例,并与说明书一起用于解释本发明的原理,其中:
26.图1是本发明实施例的固态电解质薄膜的制备方法的工艺流程图;
27.图2是本发明实施例1制备的固态电解质薄膜的sem表面图;
28.图3是本发明实施例1制备的固态电解质薄膜的sem截面图;
29.图4是本发明实施例1制备的固态电解质与标准的li4sns4相xrd对比图。
30.图5是本发明实施例1和2制备的固态电解质薄膜eis测试对比。
具体实施方式
31.下文的公开提供了许多不同的实施方式或例子用来实现本发明的不同结构。为了简化本发明的公开,下文中对特定例子的部件和设置进行描述。当然,它们仅仅为示例,并且目的不在于限制本发明。此外,本发明可以在不同例子中重复参考数字和/或参考字母,这种重复是为了简化和清楚的目的,其本身不指示所讨论各种实施方式和/或设置之间的关系。
32.其中靶材均为中诺新材市售靶材,磁控溅射采用设备为四靶射频磁控共溅射设备。
33.实施例1
34.以电阻率小于0.0015ω/cm的低阻单面抛光硅片为衬底,用丙酮、无水乙醇、去离子水对单晶硅衬底进行常规清洗,用高纯氮气吹干后用采用磁控溅射在其正表面镀一层厚度约为800nm的导电金属mo,作为基底。
35.在靶材的选用上选用li靶、sns2靶为溅射靶材,将靶材置于溅射炉内相对位置上。将带有mo的基底置于磁控溅射室中,抽真空,保证磁控溅射室本底真空度至少为5
×
10-4
pa,再向磁控溅射室通入气和硫化氢,氩气流量为40sccm,硫化氢流量为5sccm,调节溅射室压强为0.5pa,首先以75w功率对靶材进行预溅射,时间1小时,过程中关闭挡板防止污染基底。将li靶的溅射功率控制在150w,sns2靶溅射功率控制在60w,衬底温度为200℃。开始沉积lisns4电解质薄膜,沉积时间为4h,为了防止li靶过热溅射过程中暂停15~20分钟。之后将前驱体在ar气袋中密封转移到退火炉中,按照4%的硫化氢比例将硫化氢通入氩气中,逐步升高退火温度至500℃并保温3小时,最终得到结晶态的li4sns4薄膜。
36.图2是本发明实施例1制备的固态电解质薄膜的sem表面图;图3是本发明实施例1制备的固态电解质薄膜的sem截面图,本实施例所制备得到的li4sns4薄膜的厚度为0.5~3μm;图4中包含本发明实施例1制备的固态电解质的xrd。
37.实施例2
38.以电阻率小于0.0015ω/cm的低阻单面抛光硅片为衬底,用丙酮、无水乙醇、去离子水对单晶硅衬底进行常规清洗,用高纯氮气吹干后用采用磁控溅射在其正表面镀一层厚度约为800nm的导电金属mo,作为基底。
39.在靶材的选用上选用li靶、sns2靶、sb2s3靶为溅射靶材,将靶材置于溅射炉内三个方位上。将带有mo的基底置于磁控溅射室中,抽真空,保证磁控溅射室本底真空度至少为5
×
10-4
pa,再向磁控溅室通入氩气和硫化氢,氩气流量为40sccm,硫化氢流量为0.5sccm,调节溅射室压强为0.5pa,首先以75w功率对靶材进行预溅射,时间1小时,过程中关闭挡板防止污染基底。将li靶的溅射功率控制在150w,sns2靶溅射功率控制在60w,sb2s3靶功率控制在40w,衬底温度为200℃。开始沉积li
3.8
sb
0.2
sn
0.8
s4电解质薄膜,沉积时间为4h,为了防止li靶过热溅射过程中暂停15~20分钟。之后将前驱体在ar气袋中密封转移到退火炉中,按照4%的硫化氢比例将硫化氢通入氩气中,逐步升高退火温度至500℃并保温3小时,最终得到结晶态的li
3.8
sb
0.2
sn
0.8
s4薄膜。
40.图5是本发明实施例1和2制备的固态电解质薄膜eis测试对比。
41.实施例3
42.以电阻率小于0.0015ω/cm的低阻单面抛光硅片为衬底,用丙酮、无水乙醇、去离子水对单晶硅衬底进行常规清洗,用高纯氮气吹干后用采用磁控溅射在其正表面镀一层厚度约为800nm的导电金属mo,作为基底。
43.在靶材的选用上选用li靶、sns2靶、sb2s3靶为溅射靶材,将靶材置于溅射炉内三个方位上。将带有mo的基底置于磁控溅射室中,抽真空,保证磁控溅射室本底真空度至少为5
×
10-4pa,再向磁控溅室通入氩气和硫化氢,氩气流量为20sccm,硫化氢流量为5sccm,调节溅射室压强为0.5pa,首先以75w功率对靶材进行预溅射,时间1小时,过程中关闭挡板防止
污染基底。将li靶的溅射功率控制在150w,sns2靶溅射功率控制在60w,sb2s3靶功率控制在40w,衬底温度为200℃。开始沉积li
3.8
sb
0.2
sn
0.8
s4电解质薄膜,沉积时间为4h,为了防止li靶过热溅射过程中暂停15~20分钟。之后将前驱体在ar气袋中密封转移到退火炉中,按照4%的硫化氢比例将硫化氢通入氩气中,逐步升高退火温度至500℃并保温3小时,通过改变溅射气体中h2s的流速,即提高溅射腔内的h2s比例。溅射制备得到的前驱体薄膜厚度相对于实施例2有所变薄,性能差异在认可范围内变化说明随ar比例的下降,溅射速率下降。
44.实施例4
45.以电阻率小于0.0015ω/cm的低阻单面抛光硅片为衬底,用丙酮、无水乙醇、去离子水对单晶硅衬底进行常规清洗,用高纯氮气吹干后用采用磁控溅射在其正表面镀一层厚度约为800nm的导电金属mo,作为基底。
46.在靶材的选用上选用li靶、sns2靶、sb2s3靶为溅射靶材,将靶材置于溅射炉内三个方位上。将带有mo的基底置于磁控溅射室中,抽真空,保证磁控溅射室本底真空度至少为5
×
10-4
pa,再向磁控溅室通入氩气和硫化氢,氩气流量为30sccm,硫化氢流量为0.5sccm,调节溅射室压强为0.5pa,首先以75w功率对靶材进行预溅射,时间1小时,过程中关闭挡板防止污染基底。将li靶的溅射功率控制在150w,sns2靶溅射功率控制在60w,sb2s3靶功率控制在65w,衬底温度为200℃。开始沉积li
3.2
sb
0.8
sn
0.2
s4电解质薄膜,沉积时间为4h,为了防止li靶过热溅射过程中暂停15~20分钟。之后将前驱体在ar气袋中密封转移到退火炉中,按照4%的硫化氢比例将硫化氢通入氩气中,逐步升高退火温度至500℃并保温3小时,最终得到结晶态的li
3.2
sb
0.8
sn
0.2
s4薄膜。该退火得到的样品结晶性较好,但离子电导率略有下降,该结果在认可范围内出现。这是由于过多的sb元素的掺杂导致li空位减少。
47.综上分析,本发明实施例提供的全固态薄膜锂离子电池的制备方法能够快速有效的制备出空气稳定、离子电导率高的电解质薄膜,有效解决了粉末烧结不能制备薄膜电解质的缺点,开发了新的电解质薄膜制备工艺体系;且本发明所制备得到的电解质薄膜可应用于制备薄膜固态电池、微型电池、芯片一体化电池等方向。
48.本领域技术人员在考虑说明书及实践这里的发明后,将容易想到本发明的其它实施方案。本发明旨在涵盖本发明的任何变型、用途或者适应性变化,这些变型、用途或者适应性变化遵循本发明的一般性原理并包括本发明的本技术领域中的公知常识或惯用技术手段。说明书和实施例仅被视为示例性的,本发明的真正范围和精神由权利要求指出。
49.应当理解的是,本发明并不局限于上面已经描述并在附图中示出的精确结构,并且可以在不脱离其范围进行各种修改和改变。本发明的范围仅由所附的权利要求来限制。
再多了解一些
本文用于创业者技术爱好者查询,仅供学习研究,如用于商业用途,请联系技术所有人。