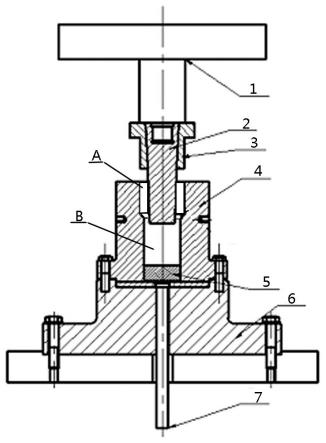
1.本实用新型涉及一种带台阶水平连铸结晶器热挤成型及退料装置。
背景技术:
2.水平连铸结晶器,材质多为铬青铜或铬锆铜,传统挤压成型方式为先挤压出铜管,然后对其铜管进行加热翻边压台阶,即加工工艺为:挤压成型铜管(薄壁管)
‑‑
锯端面
‑‑
加热翻边
‑‑
精加工。加工薄壁铜管翻边装置,包括热挤压上模、热挤芯杆,与之配合的退料压圈,及成型模具,垫板及顶出杆、热挤下模组成了带台阶水平连铸结晶器热挤成型装置。由于热挤成型装置中,热挤上模与热挤芯杆通过螺纹连接,退料压圈与热挤芯杆通过内腔锥度活动配合,成型模具与热挤下模固定连接,垫板放置在成型模具底部。上述中的成型模具是一个等径的内腔,该内腔的顶部有一个与铜管壁厚相等的台阶翻边沉孔,该台阶翻边沉孔与内腔之间有一个过渡弧。当薄壁铜管加热到温度后,放入成型模具,并在位于台阶翻边沉孔部位的薄壁铜管上端放置退料压圈,此时热挤压上模在油压机作用下向下运行,使热挤芯杆同步下行,在压力作用下使热挤芯杆端面作用在退料压圈上,通过退料压圈对薄壁铜管进行压型翻边,到达限位时停止下行,并回程。此时,在液压缸作用下,顶出杆上行,作用在垫板上移,将最终成型的铜管顶出模腔外。上述挤压成型过程中,使用的坯料为薄壁铜管坯料,外径138mm,壁厚13mm,铜管压型使坯料翻边成型,由于压型过程属于镦粗过程,金属属于自由状态流动,因受到模具尺寸约束,获得翻边台阶形状。但是在压型过程中,模具外周边缘以及内孔有气流阻碍,因此成型的铜管在台阶外圆圆周翻边的台阶不易充满,以及内孔圆周局部会出现不规则的缺肉情况,除此之外,在压型过程中,产件整体受力,产品的台阶以下的部分也会发生变形,造成圆度公差较大。影响产品加工质量。根据生产批次跟踪,这种加工方式的合格率在50%。
技术实现要素:
3.鉴于上述现状,本实用新型提供了一种带台阶水平连铸结晶器热挤成型及退料装置,通过该装置的设计,使产品工艺参数及挤压方法进行改变,该装置使用的坯料为厚壁铜管,外径能够满足台阶加工尺寸,坯料通过正挤压成型,产品工艺由原来翻边工艺改为模腔内正挤压,工艺路线由原来的“细变粗”改为“粗变细”坯料原外径138mm,壁厚13mm,改进后外径168mm,壁厚26mm,这样一来,产品的台阶尺寸完全能够保证,使得产品合格率达到99%以上,加工效率大大提升。
4.本实用新型的技术解决方案是; 一种带台阶水平连铸结晶器热挤成型及退料装置,包括热挤压上模及连接的热挤芯杆,对应热挤芯杆下部设有同一中心并安装在热挤下模上的成型模具,在成型模具内设置垫板及其上的顶出杆穿过热挤下模;其中所述热挤芯杆是一个锥度杆,该热挤芯杆安装有带有台肩的退料压型模;所述成型模具有一个上下段变径的内腔,该成型模具上段三分之二位置为放置坯料及能够嵌入退料压型模的内腔,剩余三分之一位置及成型模具下段为挤压成型铜管的台阶及外形,在成型模具上下段变径之
间带有成型铜管翻边台阶过渡倾斜倒角。
5.本新型中,所述退料压型模的内孔是一个锥度孔,该锥度孔与热挤芯杆外径锥度相等,通过两体的锥度固定连接成一体。
6.本新型中,所述成型模具上段内腔的深度应小于退料压型模的轴向长度。这样方便退料压型模挤压限位的设定,确保挤压到位。
7.本新型中,所述退料压型模端部与嵌入成型模具上下段变径过渡端位置有一个挤压翻边台阶厚度间隙。
8.本新型中,所述成型铜管及台阶是通过坯料热挤压一次成型。
9.本实用新型的有益效果是:通过一种带台阶水平连铸结晶器热挤成型及退料装置,将工艺路线由原来的“细变粗”改为“粗变细”坯料原外径138mm,壁厚13mm,改进后外径168mm,壁厚26mm,这样一来,由翻边工艺优化为模腔内正挤压,坯料在整个挤压过程中,通过退料压型模这一关键部件,产品的台阶尺寸完全能够保证。在压力机作用下,通过退料压型模作用在坯料进行挤压实现产件成型。在回程时,退料压型模又作为退料装置,避免了铜管抱死在热挤芯杆上,使热挤芯杆顺利回程。在铜管被顶出模具之外时,退料压型模随之与铜管分离,可连续进行生产。相比传统的翻边压型工艺,优化后的正挤压工艺的坯料尺寸即为翻边尺寸,因此翻边成型出现的台阶部位“缺肉”现场得以解决,在后续加工过程中,找正也极其方便,有效提高铜管成型合格率达到99%以上,加工效率大大提升。
附图说明
10.图1是本新型的结构视图;
11.图2是图1放置铜管坯料挤压前视图;
12.图3是图2铜管坯料挤压铜管成型视图;
13.图4是图2挤压后的铜管视图。
14.图中:1热挤压上模、2热挤芯杆、3退料压型模、4成型模具、5垫板、6热挤下模、7顶出杆、8铜管坯料、9铜管、10翻边台阶。
具体实施方式
15.下面将结合附图实施例对本实用新型作进一步说明。
16.图1所示的一种带台阶水平连铸结晶器热挤成型及退料装置,包括热挤压上模1,该热挤压上模1与外置的油压机连接(图中未示意),热挤压上模1在油压机的作用下可上下移动。所述热挤压上模1上连接有热挤芯杆2,对应热挤芯杆2下部设有同一中心的成型模具4,该成型模具4安装在热挤下模6上,通过铜管螺栓锁紧(图中未标注)固定。在成型模具4内腔的底部设置垫板5及其上设有连接一体的顶出杆7,通过顶出杆7部分穿过热挤下模6通孔并引出,使其顶出杆7的引出端与外置的液压缸连接(图中未示意)。在液压缸的作用下,作用顶出杆7及垫板5上下移动。本实施例中,所述热挤芯杆2是一个锥度杆,在是热挤芯杆2安装有带有台肩的退料压型模3;所述成型模具4具有一个上下段变径的内腔,该成型模具4上段三分之二位置为放置铜管坯料及能够嵌入退料压型模3的内腔a,成型模具4下段剩余三分之一位置内腔b与挤压成型后铜管外径相同,在成型模具4上、下段变径之间有一个成型铜管的翻边台阶的过渡倾斜倒角(倾斜倒角为45
°
)。本新型中,所述退料压型模3的内孔是
一个锥度孔,该锥度孔与热挤芯杆2外径锥度相等,通过两体的锥度固定连接成一体。本新型中,所述成型模具4上段内腔a的深度应小于退料压型模3的轴向长度。这样方便退料压型模3挤压后的退出及限位设定。上述中,所述退料压型模3嵌入成型模具4内,使退料压型模3端部与上下段变径过渡端之间有一个挤压成型铜管的翻边台阶厚度间隙。
17.见图2给出了铜管坯料8放置在图1成型模具4中的上段内腔a中,待热挤压上模1、热挤芯杆2及退料压型模3下移对其铜管坯料8进行待热挤压成型状态。
18.见图3给出了铜管坯料挤压铜管成型视图。当热挤压上模1、热挤芯杆2及退料压型模3受到油压机作用时同步下移,通过退料压型模3对其铜管坯料8进行热挤压,使铜管坯料8挤压进入到成型模具4中的下段内腔b成型为铜管9及翻边台阶10,所述成型铜管9及翻边台阶10是通过铜管坯料8热挤压一次成型,挤压成型后即可脱模。
19.见图4给出了挤压成型后的铜管9,在铜管9的一端带有翻边台阶10。
20.具体挤压成型过程:将铜管坯料8加热到温后,放入成型模具4上段的腔体a内,在油压机的压力作用下,作用热挤压上模1、热挤芯杆2及退料压型模3同步下移,作用退料压型模3挤压铜管坯料从成型模具4上段的内腔a,挤压进入成型模具4下段内腔b,挤压成热挤芯杆2外径与成型模具4下段内腔b内径之间的径向间隙形具有管壁厚度的铜管9,利用退料压型模3的端部与成型模具4上下段变径过渡端之间的间隙,挤压出成型铜管9上翻边台阶10(见图4)。到达挤压限位时停止下移并回程,此时,在液压缸作用下,作用顶出杆7及垫板5上移将最终成型的铜管9顶出成型模具4。在整个挤压过程中,退料压型模3为该装置的关键部位,在压力机下行时,它作为下压模作用在铜管坯料8上,使铜管坯料成型,在回程时,它作为退料装置,避免了成型后的铜管抱死在热挤芯杆2之上,保证热挤芯杆2顺利回程,在铜管9被顶出成型模具4时,退料压型模3随之与铜管9分离,如此连续进行生产。因此,带台阶水平连铸结晶器热挤成型及退料装置,通过正挤压,水平连铸结晶器的台阶自然形成,不存在缺肉及加工余量小的问题,使产品的合格率大大增加。
21.本实用新型的挤压成型工艺为:铜管坯料挤压(厚壁)
‑‑
锯端面
‑‑
加热正挤压—精加工。
22.本新型主要解决挤压成型工艺中的铜管坯料挤压成型及翻边台阶部位“缺肉”问题。
再多了解一些
本文用于创业者技术爱好者查询,仅供学习研究,如用于商业用途,请联系技术所有人。