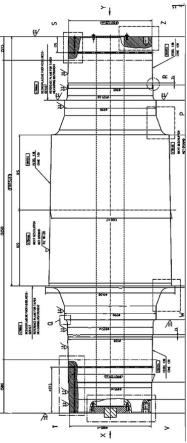
0.125)尺寸,确认后续加工余量及作为后续对刀点使用;同时手工测量的直线段尺寸与三坐标测量尺寸进行比较,确认尺寸误差。
③
半精加工锥度部分完成后进三坐标测量锥度明确机床锥度误差并为后续加工中补偿锥度提供标准依据,在锥度合格的情况下角度误差小于
±
0.005
°
,三坐标打出φ1300h7(0~-0.125)及直线测量段目前尺寸确认加工余量(测量直线段如下所示长度约为20mm)。2、在磨床加工两侧1:30锥度外圆时为减少对工件外圆的损伤在图纸右端端面设计一个磨床带动工装盘与端面m48x3螺纹孔连接,保证在不装夹到锥度外圆的情况下调头一次即可加工全部外圆并最大限度减少对工件外圆的损伤,粗磨锥度后进三坐标检测锥度及尺寸,通过尖头百分表打表小头尺寸确认加工余量,后续加工到最终尺寸φ901.128js6( 0.028~-0.028)后通过打与其余直线段外圆的落差来再次确认尺寸公差,见图3。3、为解决两端面大螺纹孔的加工效率问题,经资料查阅、市场调研最后确定采用高速浅孔钻刀具代替现有普通麻花钻,将多次钻、扩改进为一次钻削到位。高速浅孔钻普遍钻速在1000r/min以上,必须配合高压的切削液内冷却系统以降低高速切削过程中产生的高温影响和辅助孔内切屑的流畅排出,在机床设备和切削刀具之间联接过渡的bt50刀柄(侧固外转内冷刀柄bt50-ohs40-165),通过安装外部高压水泵,刀柄部位增加进液及密封装置的方法,将外部切削液加压后转移到刀柄内部,然后从钻头内部喷射出去,解决高速钻头切削加工过程中无内部切削液的问题。此改造方案不仅可以大大提高了生产效率,且此套改造设备属于独立设备,适用于所有bt50刀柄,可转移至任一机床配合使用,极其便捷。其次,根据m48x3螺纹底孔φ45,购买相应的φ45“u”钻,应用浅孔钻替换普通的磨花钻,达到了快速、准确的钻孔要求,大幅缩减了加工工时,降低了生产成本。
7.技术方案1:一种超大型矿山破碎设备用主轴,主轴总长达4087.5mm、外圆直径φ1400mm、净重33t;主轴与破碎机外套(roll)配合的轴外锥(中间锥度)锥度要求1:30
±
0.005
°
,从测量面基准轴向825距离处锥度直径尺寸公差φ1300h7; 大锥面为保证使用过程中与roll的摩擦力与常规轴类不同,特别对粗糙度进行了区间限制要求控制在rz10-rz20且不允许磨削加工;轴两端轴承安装位置外圆公差h6,粗糙度ra1.6;轴两端锥度角度比1:30
±
0.005
°
,小端直径公差js6,粗糙度ra1.6;轴两端加工20-m48x3螺孔,深度132.5,底部退刀槽,孔口φ52深43;轴左端端面有一处宽130p6,深53( 0.1~0)键槽。
8.技术方案2:一种超大型矿山破碎设备用主轴加工方法,主轴大外圆中间段1::30锥度由于锥度及公差要求高在制定工艺过程中进行了优化分别为以下几点:1)半精加工时需测试相对应的刀片耐磨程度是否满足要求,确保车加工长锥度外圆一刀不需要更换刀片,刀片无明显磨损,保证加工精度,加工过程中需试验机床合适的转速及进给保证粗糙度rz10-20达到要求;2)为解决测量问题在锥度小端留出长度20mm直线测量段用于测量尺寸并能反映出中间φ1300h7(0~-0.125)尺寸,确认后续加工余量及作为后续对刀点使用;同时手工测量的直线段尺寸与三坐标测量尺寸进行比较,确认尺寸误差;3)半精加工锥度部分完成后进三坐标测量锥度明确机床锥度误差并为后续加工中补偿锥度提供标准依据,在锥度合格的情况下角度误差小于
±
0.005
°
,三坐标打出φ1300h7(0~-0.125)及直线测量段目前尺寸确认加工余量;4)在磨床加工两侧1:30锥度外圆时为减少对工件外圆的损伤在图纸右端端面设计一个磨床带动工装盘与端面m48x3螺纹孔连接,保证在不装夹到锥度外圆的情况下调头一次即可加工全部外圆并最大限度减少对工件外圆的损伤,粗磨锥度后进三坐标检测锥度及尺寸,通过尖头百分表打表小头尺寸确认加工余量,后续加工到最终尺
寸φ901.128js6( 0.028~-0.028)后通过打与其余直线段外圆的落差来再次确认尺寸公差;5)两端m48x3螺纹底孔φ45面大螺纹孔采用高速浅孔钻刀具代替现有普通麻花钻,φ45“u”钻,将多次钻、扩改进为一次钻削到位,高速浅孔钻普遍钻速在1000r/min以上,必须配合高压的切削液内冷却系统以降低高速切削过程中产生的高温影响和辅助孔内切屑的流畅排出。
9.本发明与
背景技术:
相比,实现了超大型主轴特殊参数加艺,不仅加工效率高,而且加工精度高,所加工主轴合格率经第三方华测检测机构检测达到100%。
附图说明
10.图1是主轴技术参数示意图。
11.图2是测量直线段示意图。
12.图3是工装及针式百分表示意图。
13.图4是深孔前粗加工图。
14.图5是半精车图。
具体实施方式
15.实施例1:一种超大型矿山破碎设备用主轴加工方法,主轴大外圆中间段1::30锥度由于锥度及公差要求高在制定工艺过程中进行了优化分别为以下几点:1)半精加工时需测试相对应的刀片耐磨程度是否满足要求,确保车加工长锥度外圆一刀不需要更换刀片,刀片无明显磨损,保证加工精度,加工过程中需试验机床合适的转速及进给保证粗糙度rz10-20达到要求;2)为解决测量问题在锥度小端留出长度20mm直线测量段用于测量尺寸并能反映出中间φ1300h7(0~-0.125)尺寸,确认后续加工余量及作为后续对刀点使用;同时手工测量的直线段尺寸与三坐标测量尺寸进行比较,确认尺寸误差;3)半精加工锥度部分完成后进三坐标测量锥度明确机床锥度误差并为后续加工中补偿锥度提供标准依据,在锥度合格的情况下角度误差小于
±
0.005
°
,三坐标打出φ1300h7(0~-0.125)及直线测量段目前尺寸确认加工余量;4)在磨床加工两侧1:30锥度外圆时为减少对工件外圆的损伤在图纸右端端面设计一个磨床带动工装盘与端面m48x3螺纹孔连接,保证在不装夹到锥度外圆的情况下调头一次即可加工全部外圆并最大限度减少对工件外圆的损伤,粗磨锥度后进三坐标检测锥度及尺寸,通过尖头百分表打表小头尺寸确认加工余量,后续加工到最终尺寸φ901.128js6( 0.028~-0.028)后通过打与其余直线段外圆的落差来再次确认尺寸公差;5)两端m48x3螺纹底孔φ45面大螺纹孔采用高速浅孔钻刀具代替现有普通麻花钻,φ45“u”钻,将多次钻、扩改进为一次钻削到位,高速浅孔钻普遍钻速在1000r/min以上,必须配合高压的切削液内冷却系统以降低高速切削过程中产生的高温影响和辅助孔内切屑的流畅排出。
16.1、深孔前粗加工:按照精加工图纸的尺寸设计并绘制深孔前粗加工图纸,单边留余量10mm,三坐标对锥度部分进行检验,包括锥度、直线度、尺寸;操作工按图均匀加工(见下方图4)。2、深孔加工:产品一夹一托,深孔钻钻、扩、镗深孔尺寸φ300
±
1满足要求,粗糙度ra25。3、一次精车:数控车床校正装夹后,按《半精车图》半精车各档尺寸,全部外圆均留单边3mm余量,总长
至精加工尺寸要求,见图5。4、镗铣:工件置于双v形架,图纸右端朝向主轴,校正工件端面,按车床留台阶平端面取长。校正工件铣g1/4螺纹孔φ28沉孔深7mm,枪钻钻φ11.4深507.5,扩孔钻扩孔口φ11.6底孔,攻g1/4螺纹深20;粗铣宽130p9键槽留余量,深度到尺寸,换四刃硬质合金铣刀精铣两侧保证宽度尺寸至下差,手扶砂纸抛光键槽两侧保证粗糙度0.8。安装外接高压水泵,换高速出水钻与改造后的bt50刀柄配套使用,实现切削液外冷却切换至内冷却的转变,调节水泵压力至合适的喷射水压。调出钻孔程序,经技术人员确认孔位及参数无误后开始钻孔,整个钻孔过程中无需更换其他刀具,钻至深度132.5。5、精车:数控车床校正装夹后,精车各档尺寸,其中φ725h6外圆两档加工至φ925.6,留0.3mm余量,两侧1:30锥度留单边0.3mm余量,其余尺寸精度要求相对不高的精车至尺寸偏上差,中间配合锥度φ1300h7外圆加工至尺寸要求,保证粗糙度rz10~20;测量合格后车除20mm测量段,依《后续精加工图纸》加工锥度两端0.09斜坡,参考w、p视图所示;(检测:刀口尺 0.09塞尺,刀口尺贴平锥度母线,0.09塞尺两端可顺利通过方为合格)。6、磨床:工件上工装卡盘,两顶装夹,图纸左端朝向尾座,磨φ925h6、φ885e7、φ895h6及左端1:30锥度保证粗糙度及尺寸;工件调头,两顶装夹,鸡心夹头垫铜皮防护,带动工件磨右侧1:30锥度外圆至尺寸。
17.需要理解到的是:上述实施例虽然对本发明的设计思路作了比较详细的文字描述,但是这些文字描述,只是对本发明设计思路的简单文字描述,而不是对本发明设计思路的限制,任何不超出本发明设计思路的组合、增加或修改,均落入本发明的保护范围内。
再多了解一些
本文用于创业者技术爱好者查询,仅供学习研究,如用于商业用途,请联系技术所有人。