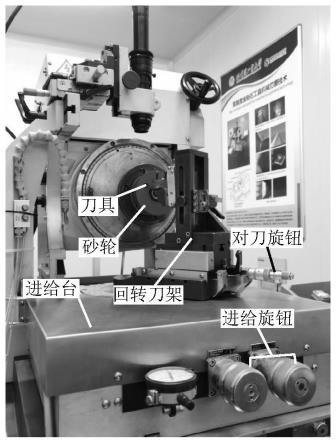
1.本发明属于微纳制造技术领域,涉及一种适合于制造高精度微圆弧金刚石刀具的机械刃磨工艺,应用于功能微结构阵列表面的超精密切削加工。
背景技术:
2.由于微结构阵列表面具有很多优异的特性,在生物医疗、环境保护、光伏能源、光学系统、柔性皮肤、虚拟现实和国防军工等众多高新科技领域均有应用。而如何实现大范围、高效率、低成本的微结构阵列表面加工一直是学术界和工业界关注的热点。经过几十年的发展,金刚石切削加工技术和辊压(或模压)技术被公认为是加工大尺寸功能微结构表面最有效、成本最低的加工技术。功能微结构阵列表面金刚石切削加工技术是采用高精度微小金刚石刀具在超精密机床上直接完成表面加工的技术,目前该技术是大尺寸金属表面微结构阵列加工的唯一方法;辊压(或模压)加工技术是一种用金刚石切削加工的模具基于复制原理把模具表面的微结构转印到聚合物表面的加工技术,该技术非常适用于薄膜微结构的大批量工业生产。在上述两种加工方法中,金刚石切削加工都是必不可少的一环,而高精度微小金刚石刀具是功能微结构阵列表面加工的必备工具,尤其微圆弧金刚石刀具由于对刀方便、切削刃长、耐磨损能力强,是大尺寸微结构阵列表面切削加工的常用刀具。
3.影响微结构阵列表面切削加工质量的主要因素包括机床运动精度和微圆弧金刚石刀具制造精度。刀具制造精度主要包括切削刃形状精度(又叫刀刃圆弧波纹度)、锋利度(又叫切削刃钝圆半径)和微缺陷的多少。由于目前刃磨水平的限制,即使精密研磨的微圆弧金刚石刀具切削刃也不是一条完美的圆弧线,而是一条带有微观缺陷的“锯齿”状圆弧带,这里的微观“锯齿”状就是指刀刃圆弧波纹度,圆弧带就是指切削刃钝圆半径。这些刀具制造误差将影响微结构的形状精度和表面质量。因此,为使功能微结构阵列表面的加工质量满足其设计要求,必须提高微圆弧金刚石刀具的制造精度。
4.金刚石是自然界最硬的材料,并且具有很强的各向异性,因此用常规方法对其加工极其困难,对精度要求极高的微圆弧金刚石刀具的加工更是困难。目前,可用于金刚石加工的工艺方法主要有:机械研磨法、化学辅助抛光法、热化学抛光法、激光加工法、等离子体刻蚀法、聚焦离子束刻蚀法、氧化刻蚀法等。但是,只有机械研磨法是一种兼顾加工质量和加工效率的加工方法,也是工业上金刚石刀具的主流加工方法。
5.机械研磨加工工艺一般是用涂有金刚石微粉的铸铁研磨盘对金刚石刀具进行研磨,凭借微磨粒对金刚石刀具的摩擦和刻划作用实现材料的缓慢微量去除,从而达到获得锋利切削刃的目的。哈尔滨工业大学宗文俊等学者深入研究了大圆弧金刚石刀具的机械刃磨工艺(zl200510010404.x),可控制切削刃钝圆半径优于30~50nm。
6.为了实现高精度微圆弧金刚石刀具的国产化,打破国外技术垄断,需要深入研究每个工艺参数对微圆弧金刚石刀具机械刃磨质量的影响,精确掌握刀刃圆弧波纹度、切削刃钝圆半径和微观缺陷的变化规律,探索微圆弧金刚石刀具刀刃圆弧波纹度、切削刃钝圆半径和微观缺陷的控制方法,优化机械刃磨工艺参数以实现高精度微圆弧金刚石刀具的加
工。
技术实现要素:
7.为了加工刀刃圆弧波纹度优于10nm/115
°
圆弧包角、切削刃钝圆半径优于50nm、刀尖圆弧半径小于10μm、放大10000倍无肉眼可见崩刃的微圆弧金刚石刀具,本发明提供了一种高精度微圆弧金刚石刀具“两步”机械刃磨工艺。本发明主要从抑制金刚石晶体机械研磨材料去除率各向异性入手,结合前期积累的高精度大圆弧金刚石刀具机械刃磨工艺经验,对微圆弧金刚石刀具进行机械刃磨加工。通过大量的微圆弧金刚石刀具机械刃磨工艺实验,详细分析了金刚石磨料粒度、研磨盘基体材料、研磨压力、研磨盘转速、往复运动行程、往复运动频率、摆轴摆动速度、进给量等对微圆弧金刚石刀具刀刃圆弧波纹度、切削刃钝圆半径和微观缺陷的影响规律,并建立优选的微圆弧金刚石刀具机械刃磨工艺,以此获得近无崩刃缺陷和极其锋利的切削刃具,为打破国外的技术壁垒、提高我国微圆弧金刚石刀具的加工水平,迈出了探究性的一步。
8.本发明的目的是通过以下技术方案实现的:
9.一种高精度微圆弧金刚石刀具“两步”机械刃磨工艺,包括如下步骤:
10.步骤一:选择规整的八面体天然金刚石晶体作为刀头材料,用激光切割机沿金刚石{100}晶面切开;选择与金刚石晶体热膨胀系数相近的硬质合金作为刀柄材料,并按刀头设计参数加工成合适的形状;
11.步骤二:用金刚石平磨机把步骤一切开的金刚石晶体沿{100}晶面研磨成厚度为1~1.5mm的薄片,并保证上下研磨表面的平整度,方便后续精磨前刀面;
12.步骤三:用酒精清洗步骤一的刀柄和步骤二的金刚石片,以去除二者表面的污染物;然后,按前、后刀面均为{100}晶面进行定向,在刀柄和金刚石片之间加入银铜钛焊料并将其固定在刀柄之上;最后,把固定有金刚石片和焊料的刀柄置于真空焊接炉内进行钎焊,高温融化后的焊料将金刚石片与刀柄牢固的焊接在一起;
13.步骤四:用激光切割机对步骤三焊好的金刚石片进行粗成型加工,按设计好的刀尖角把金刚石片的前端加工成v型刀头,刀头侧边要伸出刀柄边缘0.2mm以上,方便后续研磨加工;
14.步骤五:用金刚石平磨机对步骤四粗成型加工完成的刀具前刀面进行精磨加工,一是保证前刀面与刀柄底面平行,二是去除步骤二残留的研磨痕迹以减小前刀面粗糙度;
15.步骤六:恒温控制pg3b行星型钻石刀具研磨机周围环境条件为25℃,恒温精度
±
0.5℃;在主轴冷却水循环系统正常工作情况下,空载运行研磨机半小时以上,使其性能达到稳定状态;
16.步骤七:把完成前刀面精磨的刀具安装到pg3b行星型钻石刀具研磨机的刀架上,按照设计好的刀具后角调整刀架的角度;把摆轴摆到左(或右)侧1/2刀尖角对应角度位置;用800#青铜基砂轮盘粗磨刀头的侧刀面,粗磨工艺参数为:金刚石刀具侧面与砂轮盘的接触点位置偏离主轴中心15mm,开启砂轮盘往复运动(往复运动行程30mm、运动频率0.25hz),主轴转速3600rpm,研磨压力19.6n,此工序粗磨左(或右)侧面直到在研磨机自带光学监测系统下观察该侧刃为一条光滑的直线为止;然后,把摆轴摆到右(或左)侧1/2刀尖角对应角度位置,采用相同的粗磨工艺参数,粗磨右(或左)侧刀面直到该侧刃也为一条光滑的直线
并与另一侧刃相交于一点为止;
17.步骤八:用3000#青铜基砂轮盘替换800#砂轮盘,采用与步骤七相同的刃磨工艺参数半精磨左右两侧刀面,左右两侧各去除10μm;
18.步骤九:用铸铁研磨盘替换3000#砂轮盘,把摆轴摆到90
°
位置,用此时的刀具代替金刚石笔对铸铁研磨盘在位修整,研磨压力降为9.8n,研磨盘往复频率降为0.08hz,其他工艺参数与步骤七相同,粗修整单次修整深度2μm,共5次,精修整单次修整深度1μm,共3次;在位修整完成后,采用激光位移传感器对研磨盘端面全跳动进行在位检测,如果研磨盘全盘面跳动小于2μm,结束修整,否则重复精修整步骤直到全盘面跳动小于2μm;修整完成后,v型的刀尖已变成一个带有微小平台的梯形刀头,该形状可以缩短步骤十二和步骤十三的精磨时间,有利于提高精磨效率;
19.步骤十:在铸铁研磨盘表面均匀涂覆w0.5的金刚石研磨膏,接着用研磨块在铸铁研磨盘表面手工预研15~20分钟后刮除铸铁研磨盘表面多余研磨膏,使金刚石研磨颗粒均匀镶嵌于铸铁研磨盘表面的孔隙内;
20.步骤十一:借助研磨机在位光学监测系统,精密调节金刚石刀具在刀架上的左右位置,使摆轴回转轴线穿过刀尖角的角平分线,即刀尖角的角平分线过光学系统的中心;打开光学监测系统的辅助测量功能,精密调节刀具在刀架的前后位置,使梯形刀头的上边缘处于光学系统中心上方并偏离中心30μm;启动主轴,进给刀架,注意观察监测系统屏幕,当刀尖快要接触研磨盘时,放慢进给速度或者采用微进给系统进给,并借助研磨机自带的声音监测系统判断刀尖是否与铸铁研磨盘接触,当听到微弱的沙沙声时停止进给,并将此时的位置设为零位;然后,快速退出刀架,设置精磨工艺参数为:金刚石刀具刀尖与研磨盘接触点位置偏离主轴中心35mm,研磨盘附加往复运动(行程1mm、频率0.08hz),主轴转速3000rpm,摆轴摆速8
°
/s,研磨压力9.8n,设置左右两侧驻留时间各1s;
21.步骤十二:启动主轴,开启往复运动和摆轴,用进给旋钮把刀架进给到接近零位,改用微进给系统进给直到刀尖与研磨盘接触,先进给1μm,待研磨盘完成1~2个往复运动后,第二次进给1μm,待研磨盘完成1~2个往复运动后,第三次进给1μm,以此类推,直到完成第五次进给,此时记为一次有效进给,等待刃磨直到声音监测系统无沙沙声发出;重复本步骤上述有效进给3~4次,确保切削刃无明显崩刃的前提下实现多余刀具材料的快速去除,该步骤为“两步”机械刃磨工艺方法的第一步;
22.步骤十三:把步骤十二的进给方式改为每次进给0.6μm,只进给一次,等待刃磨直到声音监测系统无沙沙声发出;重复本步骤上述进给运动4~5次,确保刀刃圆弧波纹度优于10nm/115
°
圆弧包角、切削刃钝圆半径优于50nm,该步骤为“两步”机械刃磨工艺方法的第二步;
23.步骤十四:从刀架取下刃磨完成的微圆弧金刚石刀具,用酒精清洗干净后,先用光学显微镜在1000
×
的放大倍数下观察刀尖形貌无肉眼可见崩刃的情况下,进一步采用扫描电子显微镜(sem)在10000
×
的放大倍数下观察刀尖形貌无肉眼可见的微崩刃缺陷,再用金刚石刀具半径波幅测量仪测量刀刃圆弧波纹度,在刀刃圆弧波纹度优于10nm/115
°
的情况下,最后用原子力显微镜(afm)在1μm
×
1μm的范围内检测切削刃钝圆半径,如果钝圆半径小于50nm则该刀具刃磨质量合格,如果以上检测结果有一项不合格则视为该刀具刃磨质量不合格,重复步骤十一至步骤十三重新刃磨,直到上述检测结果都合格为止;
24.步骤十五:对于步骤十四检测质量合格的微圆弧金刚石刀具装盒保护,贴标签标示刀具几何参数和刃磨精度参数。
25.相比于现有技术,本发明具有如下优点:
26.1、本发明提供了一种适用于制造高精度微圆弧金刚石刀具的机械刃磨工艺,基于抑制金刚石晶体机械研磨材料去除率各向异性的工艺思想,综合分析刃磨过程中的磨料粒度、研磨盘基体材料、研磨压力、研磨盘转速、往复运动行程、往复运动频率、摆轴摆动速度、进给量等对微圆弧金刚石刀具刀刃圆弧波纹度、切削刃钝圆半径和微观缺陷的影响规律,优选工艺参数,即采用800#青铜基砂轮盘粗磨刀具的两侧面,快速去除激光烧蚀影响层,再用3000#青铜基砂轮盘半精磨刀具的两侧面,去除侧边粗磨产生的崩口,最后用铸铁研磨盘精密研磨刀尖和侧面,完成高精度微圆弧金刚石刀具的机械刃磨加工。
27.2、本发明通过改变机械刃磨时的进给量大小和进给方式来控制金刚石材料去除率的各向异性大小,即第一步采用单次小进给量1μm,(准)连续进给五次增大有效进给量,以提高材料去除效率,快速完成微圆弧金刚石刀具的精密成型刃磨;第二步采用单次进给0.6μm的断续进给方式,抑制金刚石材料去除率的各向异性,以保证微圆弧金刚石刀具的刃磨精度和切削刃钝圆半径,并抑制切削刃微观缺陷的产生。
28.3、本发明不仅加工效率高,而且消除了传统刃磨工艺对修磨操作人员经验手法的依赖性,凭借刃磨机床的高精度即可在刃磨机上完成高精度微圆弧金刚石刀具的机械刃磨,最终获得刀刃圆弧波纹度优于10nm/115
°
圆弧包角、切削刃钝圆半径优于50nm、刀尖圆弧半径小于10μm、放大10000倍无肉眼可见崩刃的高精度微圆弧金刚石刀具。
附图说明
29.图1是用于加工高精度微圆弧金刚石刀具的pg3b行星型钻石刀具研磨机;
30.图2是刀具毛坯准备流程图,a)八面体金刚石原石,b)沿{100}晶面切开的金刚石,c)硬质合金刀柄,d)金刚石钎焊,e)精磨前刀面;
31.图3是对刀操作示意图,a)左右对刀示意图,b)前后对刀示意图;
32.图4是加工完成的刀尖形貌及检测结果,a)1000
×
光学显微镜观察,b)10000
×
sem观察,c)刀刃圆弧波纹度,d)afm检测的切削刃形貌,e)切削刃钝圆半径。
具体实施方式
33.下面结合附图对本发明的技术方案作进一步的说明,但并不局限于此,凡是对本发明技术方案进行修改或者等同替换,而不脱离本发明技术方案的精神和范围,均应涵盖在本发明的保护范围中。
34.本发明提供了一种高精度微圆弧金刚石刀具“两步”机械刃磨工艺,从抑制金刚石晶体机械研磨材料去除率各向异性入手,综合分析刃磨过程中的磨料粒度、研磨盘基体材料、研磨压力、研磨盘转速、往复运动行程、往复运动频率、摆轴摆动速度、进给量等对微圆弧金刚石刀具刀刃圆弧波纹度、切削刃钝圆半径和微观缺陷的影响规律,建立优选后的微圆弧金刚石刀具机械刃磨工艺,以此获得刀刃圆弧波纹度优于10nm/115
°
圆弧包角、切削刃钝圆半径优于50nm、刀尖圆弧半径小于10μm、放大10000倍无肉眼可见崩刃的微圆弧金刚石刀具。具体实现步骤如下:
35.步骤一:选择规整的八面体天然金刚石晶体作为刀头材料,如图2a)所示,并用激光切割机沿金刚石{100}晶面切开,如图2b)所示;选择与金刚石晶体热膨胀系数相近的硬质合金作为刀柄材料,这种材料可以有效降低后续焊接表面的残余应力,并按刀头设计参数加工成合适的形状,如图2c)所示。
36.步骤二:用金刚石平磨机把步骤一切开的金刚石晶体沿{100}晶面研磨成厚度为1~1.5mm的薄片,并保证上下研磨表面的平整度,方便步骤五精磨前刀面。
37.步骤三:用酒精清洗步骤一的刀柄和步骤二的金刚石片,以去除二者表面的污染物;然后,按前、后刀面均为{100}晶面进行定向,在刀柄和金刚石片之间加入银铜钛焊料并将其固定在刀柄之上;最后,把固定有金刚石片和焊料的刀柄置于真空焊接炉内进行钎焊,高温融化后的焊料将金刚石片与刀柄牢固的焊接在一起,钎焊完成的刀具毛坯如图2d)所示。
38.步骤四:用激光切割机对步骤三焊好的金刚石片进行粗成型加工,按设计好的刀尖角把金刚石片的前端加工成v型刀头,刀头侧边要伸出刀柄边缘0.2mm以上,方便后续研磨加工。
39.步骤五:用金刚石平磨机对步骤四成型粗加工完成的刀具前刀面进行精磨加工,一是保证前刀面与刀柄底面平行,二是去除步骤二残留的研磨痕迹以减小前刀面粗糙度,如图2e)所示。
40.步骤六:恒温控制pg3b行星型钻石刀具研磨机周围环境条件为25℃,恒温精度
±
0.5℃;在主轴冷却水循环系统正常工作情况下,空载运行研磨机半小时以上,使其性能达到稳定状态。
41.步骤七:把完成前刀面精磨的刀具安装到pg3b行星型钻石刀具研磨机的刀架上,按照设计好的刀具后角调整刀架的角度;把摆轴摆到左(或右)侧1/2刀尖角对应角度位置。用800#青铜基砂轮盘粗磨刀头的侧刀面,粗磨工艺参数为:金刚石刀具侧面与砂轮盘的接触点位置偏离主轴中心15mm,开启砂轮盘往复运动(往复运动行程30mm、运动频率0.25hz),主轴转速3600rpm,研磨压力19.6n。此工序粗磨左(或右)侧面直到在研磨机自带光学监测系统下观察该侧刃为一条光滑的直线为止。然后,把摆轴摆到右(或左)侧1/2刀尖角对应角度位置,采用相同的工艺参数,粗磨右(或左)侧刀面直到该侧刃也为一条光滑的直线并与另一侧刃相交于一点为止。
42.步骤八:用3000#青铜基砂轮盘替换800#砂轮盘,采用与步骤七相同的刃磨工艺参数半精磨左右两侧刀面,左右两侧各去除10μm。
43.步骤九:用铸铁研磨盘替换3000#砂轮盘,把摆轴摆到90
°
位置,用此时的刀具代替金刚石笔对铸铁研磨盘在位修整,研磨压力降为9.8n,研磨盘往复频率降为0.08hz,其他工艺参数与步骤七相同。粗修整单次修整深度2μm,共5次,精修整单次修整深度1μm,共3次。在位修整完成后,采用激光位移传感器对研磨盘端面全跳动进行在位检测,如果研磨盘全盘面跳动小于2μm,结束修整,否则重复精修步骤直到全盘面跳动小于2μm。修整完成后,v型的刀尖已变成一个带有微小平台的梯形刀头,该形状可以所短步骤十二和步骤十三的精磨时间,有利于提高精磨效率。
44.步骤十:在铸铁研磨盘表面均匀涂覆w0.5的金刚石研磨膏,接着用研磨块在研磨盘表面手工预研15~20分钟后刮除研磨盘表面多余研磨膏,使金刚石研磨颗粒均匀镶嵌于
铸铁研磨盘表面的孔隙内。
45.步骤十一:借助研磨机在位光学监测系统,精密调节金刚石刀具在刀架上的左右位置,使摆轴回转轴线穿过刀尖角的角平分线,即刀尖角的角平分线过光学系统的中心,如图3a)所示;打开光学监测系统的辅助测量功能,精密调节刀具在刀架的前后位置,使梯形刀头的上边缘处于光学系统中心上方并偏离中心30μm,如图3b)所示。启动主轴,进给刀架,注意观察监测系统屏幕,当刀尖快要接触研磨盘时,放慢进给速度或者采用微进给系统进给,并借助研磨机自带的声音检测系统判断刀尖是否与研磨盘接触,当听到微弱的沙沙声时停止进给,并将此时的位置设为零位。然后,快速退出刀架。设置精磨工艺参数为:金刚石刀具刀尖与研磨盘接触点位置偏离主轴中心35mm,研磨盘附加往复运动(行程1mm、频率0.08hz),主轴转速3000rpm,摆轴摆速8
°
/s,研磨压力9.8n,设置左右两侧驻留时间各1s。
46.步骤十二:启动主轴,开启往复运动和摆轴,用进给旋钮把刀架进给到接近零位。改用微进给系统进给直到刀尖与研磨盘接触,先进给1μm,待研磨盘完成1~2个往复运动后,第二次进给1μm,待研磨盘完成1~2个往复运动后,第三次进给1μm,以此类推,直到完成第五次进给,此时记为一次有效进给,等待刃磨直到声音监测系统无沙沙声发出。重复本步骤上述有效进给3~4次,确保切削刃无明显崩刃的前提下实现多余刀具材料的快速去除。该步骤为“两步”机械刃磨工艺方法的第一步。
47.步骤十三:把步骤十二的进给方式改为每次进给0.6μm,只进给一次,等待刃磨直到声音监测系统无沙沙声发出。重复本步骤上述进给运动4~5次,确保刀刃圆弧波纹度优于10nm/115
°
圆弧包角、切削刃钝圆半径优于50nm。该步骤为“两步”机械刃磨工艺方法的第二步。
48.步骤十四:从刀架取下刃磨完成的微圆弧金刚石刀具,用酒精清洗干净后,先用光学显微镜在1000
×
的放大倍数下观察刀尖形貌无肉眼可见崩刃,如图4a)所示,进一步采用sem在10000
×
的放大倍数下观察刀尖形貌无肉眼可见的微崩刃缺陷,如图4b)所示,再用金刚石刀具半径波幅测量仪测量刀刃圆弧波纹度,若刀刃圆弧波纹度优于10nm/115
°
,如图4c)所示,最后用afm在1μm
×
1μm的范围内检测切削刃钝圆半径,如果钝圆半径小于50nm则该刀具刃磨质量合格,如图4d)和4e)所示,如果以上检测结果有一项不合格则视为该刀具刃磨质量不合格,应重复步骤十一至步骤十三重新刃磨,直到上述检测结果都合格为止。
49.步骤十五:对于步骤十四检测质量合格的微圆弧金刚石刀具装盒保护,贴标签标示刀具几何参数和刃磨精度参数。
再多了解一些
本文用于创业者技术爱好者查询,仅供学习研究,如用于商业用途,请联系技术所有人。