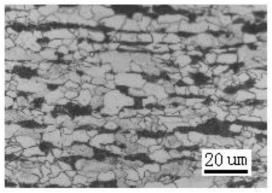
一种低成本q550d钢板生产方法
技术领域
1.本发明涉及轧钢技术领域,尤其涉及一种低成本q550d钢板生产方法。
背景技术:
2.q550d是一种屈服强度为550mpa级的结构钢。该钢种广泛应用于建筑、工程机械领域。q550d钢板要求较高的强度、良好的冲击韧性和焊接性能,对于较宽、较厚的规格一般都是采用宽厚板轧机生产。现在宽厚板线生产q550d钢板生产主要采用以下两种工艺,一是采用tmcp 回火工艺,这种方法要求钢板在控轧、控冷完成后,进行回火热处理,钢板的生产成本高、生产周期长,同时轧机采用tmcp工艺生产,钢板板形不好控制,对冷却设备、矫直设备要求较高。另一种是钢板轧制完成后,热处理采用调质工艺生产,这种工艺生产的钢板性能稳定,板形也比较好,但是工序成本高,制造周期长。q550d是高强度结构钢,板形和综合性能控制难度均较大,因此如何在较短制造周期内,低成本的生产板形和性能良好q550d钢板很重要。
3.公布号cn 103276301 a的专利“一种屈服强度≥550mpa的低温工程用钢及其生产方法”提供了一种q550d厚规格钢板生产方法,该方法生产的q550d性能满足要求,但该方法钢板轧后终冷温度在400~450℃之间,板形不好控制,对冷却设备要求高。
4.公布号cn 102433498 a的专利“一种q550d优质结构钢中厚板及其生产方法”提供了一种q550d钢板生产方法,该方法生产的q550d性能满足要求,但该方法钢板轧后终冷温度在450~600℃之间,板形不好控制,对冷却设备和矫直设备要求高。
5.公布号cn 103276301 a的专利“一种550mpa级大厚度s550q钢板及生产方法”提供了一种q550d厚规格钢板生产方法,该方法生产的q550d性能满足要求,但该方法要求两次淬火,工艺复杂,生产成本高。
技术实现要素:
6.为了解决上述技术问题,本发明的目的是提供一种低成本q550d钢板生产方法。
7.为解决上述技术问题,本发明采用如下技术方案:
8.本发明一种低成本q550d钢板生产方法,包括:
9.(1)为保证一定的压缩比及满足钢板质量需要,选用250mm厚、2000mm宽的连铸坯;
10.(2)铁水冶炼前必须安排脱硫,脱硫后必须扒渣;冶炼时不得加入渣钢、海绵铁;
11.(3)rh精炼真空处理过程保证4.5分钟内降到130pa以下,小于130pa时间保持大于15分钟;rh精炼软吹时间保证不小于11分钟;
12.(4)、连铸坯的厚度为250mm,钢水浇铸时过热度控制在15~32℃,连铸时采用轻压下,轻压下位置为6、7、8、9四段,总压下量为7.8mm;使用电磁搅拌,电磁搅拌位置为4、5段,电磁搅拌的频率为5hz,电磁搅拌的电流为370a;换包时中包液位不小于28吨,使用中碳低合金钢保护渣,渣子要保持干燥,液渣层厚度控制在10~12mm;浇注时,采用保护浇注,长水口密封氩气压力控制在≥0.35mpa,流量控制在130~140l/min;中间包浸入水口密封氩气
压力0.22mpa,流量15~18l/min;
13.(5)、加热工艺:板坯加热时采用步进式加热炉,连铸坯出炉温度1230-1260℃,加热时间230~260分钟,板坯在均热段的加热时间不低于30分钟;板坯在加热炉中加热时活动梁托起板坯的移动速度为1.1-1.5m/min;加热时使用高炉煤气和焦炉煤气的混合煤气,混合煤气热值控制在2300~2500kcal/m3之间;
14.(6)轧制及冷却工艺:将板坯加热好之后进行控制轧制,第一阶段开轧厚度为板坯厚度,第一阶段开轧温度1220~1250℃,第一阶段轧制速度为1.2m/s,咬入速度为0.60m/s,咬入长度为0.20m,机架加速度为1.0m/s2;第一阶段终轧温度≥1142℃;轧制时设定扭矩为2250knm,设定单位轧制力为18~20mn/m;第二阶段钢板的开轧厚度为4倍成品钢板厚度,第二阶段钢板开轧温度为870~910℃,第二阶段终轧温度为790~810℃,第二阶段轧制6~8道次,第二阶段的轧制速度为3.6~4.8m/s,咬入速度为1.6m/s,咬入长度为0.3m,机架加速度为2.0m/s2,钢板轧制时设定抛钢距离为3.2m;钢板轧完后进行层流冷却,acc上喷梁的水量为480l~560l/(m2
·
min),下喷梁水量为960l~1120l/(m2·
min)acc水温为16℃~18℃,终冷温度为640℃~660℃,acc冷却时使用头部遮蔽和边部遮蔽;
15.(7)本发明所述钢板厚度为14mm~22mm厚,在宽厚板轧机上生产。
16.进一步的,板坯在加热炉中加热时活动梁托起板坯的移动速度为1.3m/min。
17.进一步的,所述头部遮蔽的长度1.5m,遮蔽系数为0.6,所述边部遮蔽的宽度为0.15m。
18.进一步的,所述q550d钢板按重量百分比的化学成分包括:c:0.175~0.190%;si:0.2~0.4%;mn:1.60~1.70%;nb:0.045~0.055%;v:0.055~0.065%;p:≤0.011%;s:≤0.003%;als:0.013~0.028%;ca:0.0012~0.0027%;ti:0.012~0.022%;h≤1.2ppm;o:≤0.003%;n:≤0.0042%;其余为铁和不可避免杂质。
19.进一步的,钢板的屈服强度在568mpa~592mpa之间,抗拉强度在689mpa~712mpa之间,延伸率在16.5%~18.5%之间,-20℃冲击功在138j~176j之间。
20.与现有技术相比,本发明的有益技术效果:
21.该钢种的微合金nb、ti含量较高,为了使这些合金在板坯加热时充分固溶进奥氏体晶粒里,在轧制时和后续的冷却过程中,析出来强化金属基体,因此板坯加热时,采用较高的加热温度和较长的加热时间。
22.由于该钢种含有一定量的nb、v、ti,因此对上述加热好的连铸坯在奥氏体再结晶区和非再结晶区进行控制轧制。该钢种采用两阶段控制轧制,第一阶段控制轧制属于高温区的奥氏体再结晶控制轧制,这一阶段采用大压下的轧制策略。较大的单道次压下率能使轧制变形充分渗透至钢板中心,充分细化奥氏体晶粒并均匀奥氏体组织,同时轧制产生的高温焊合作用很大程度上消除了铸坯内部的疏松、微裂纹等缺陷,使钢板的致密度提高,材料综合性能改善。在第一阶段轧制时,前三个道次轧制采用较小的咬入速度、机架加速度和轧制速度,是为了加强除鳞效果,有利于氧化铁皮去除,除鳞后钢板待温摆动5~8秒后再进行下一道次的轧制,这样有利于钢板除鳞后上下表面温度均匀,钢板板形容易控制。后面由于钢板上氧化铁皮已减少,所以减少除鳞频率,减为偶数道次除鳞。第一阶段后面的轧制道次数咬入速度、机架加速度和轧制速度都较大,一是经过前四道次除鳞、轧制,钢板表面氧化铁皮有所减少,二是为了控制钢板的终轧温度,满足第二阶段对钢板开轧温度的要求。第
一阶段轧制结束后,中间坯在辊道上摆动降温,降温至第二阶段开轧温度时开始轧制,第二阶段前两个道次轧制时采用较小的咬入速度、机架加速度和轧制速度,是为了加强除鳞效果,有利于钢板在待温过程中形成的氧化铁皮的去除,采用反除方式并轧完后待温摆动一定时间是为了钢板温度均匀,有利于钢板板形控制。第二阶段的轧制属于低温非再结晶控轧,通过nb、v、ti等的碳氮化物析出,钉扎位错,晶粒内部在轧制变形下产生应变,通过多道次轧制,较大的累积压下量,晶粒内部积累了大量的形变能和相变形核位置。钢板轧后经acc快速冷却,通过轧后快速冷却到较低的温度,使钢板在较低温度下完成γ相
→
α相转变,获得晶粒细小的α相组织,从而使钢板具有良好的韧性。
23.本发明直接采用控轧、控冷工艺生产q550d,不需要进行热处理和添加昂贵合金,生产工艺简单,制造周期短,制造成本和合金成本低。
24.钢板的强度、塑性、韧性良好,组织为细小的铁素体 珠光体。钢板的屈服强度在568mpa~592mpa之间,抗拉强度在689mpa~712mpa之间,延伸率在16.5%~18.5%之间,-20℃冲击功在138j~176j之间。
附图说明
25.下面结合附图说明对本发明作进一步说明。
26.图1为实施例1的金相组织图;
27.图2为实施例2的金相组织图;
28.图3为实施例3的金相组织图。
具体实施方式
29.以下结合实施例对本发明作进一步描述。
30.实施例1
31.采用250mm厚、2000mm宽板坯,轧制成厚度为14mm厚钢板,在宽厚板轧机上生产。板坯中心偏析为c2.5,中心疏松为2.0级。铁水冶炼前脱硫,脱硫后拔渣,冶炼时不加入轧钢、海绵铁。rh精炼真空处理过程在4.5分钟降到128pa,小于130pa保持时间为15.5分钟,rh精炼软吹时间为11分钟。钢水浇铸时过热度为15℃,连铸时采用轻压下,轻压下位置为6、7、8、9四段,总压下量为7.8mm。使用电磁搅拌,电磁搅拌位置为4、5段,电磁搅拌频率为5hz,电磁搅拌电流为370a。换包时中包液位为28吨,使用中碳低合金保护渣,渣子干燥,液渣层厚度为10mm。浇注时,采用保护浇注,长水口密封氩气压力为0.35mpa,流量为130l/min;中间包浸入水口密封氩气压力为0.22mpa,流量为18l/min。板坯加热时采用步进式加热炉,连铸坯出炉温度1230℃,加热时间230分钟,板坯在均热段的加热时间为30分钟。板坯在加热炉中加热时活动梁托起板坯的移动速度为1.3m/min。加热时使用高炉煤气和焦炉煤气的混合煤气,混合煤气热值为2300kcal/m3。板坯的(重量百分比)化学成分为:c 0.175%,si 0.2%,mn 1.70%,nb:0.045%;v:0.065%;p 0.011%,s 0.003%,al s0.028%,ca0.0027%,ti0.012%,h 1.2ppm,o 0.003%,n 0.0042%;余量为fe和不可避免的杂质。钢板轧完后进行层流冷却,acc上喷梁的水量为480l/(m2·
min),下喷梁水量为960l/(m2·
min)acc水温为16℃,终冷温度为660℃,acc冷却时使用头部遮蔽和边部遮蔽,头部遮蔽长度1.5m,遮蔽系数为0.6,边部遮蔽宽度为0.15m。详细的轧制及冷去工艺见表1,其力学性能见表2。
32.表1轧制及冷却工艺
[0033][0034][0035]
表2钢板力学性能
[0036][0037]
实施例2
[0038]
采用250mm厚、2000mm宽板坯,轧制成厚度为22mm厚钢板,在宽厚板轧机上生产。板坯中心偏析为c1.0,中心疏松为1.5级。铁水冶炼前脱硫,脱硫后拔渣,冶炼时不加入轧钢、海绵铁。rh精炼真空处理过程在4.2分钟降到125pa,小于130pa保持时间为17分钟,rh精炼软吹时间为12.5分钟。钢水浇铸时过热度为32℃,连铸时采用轻压下,轻压下位置为6、7、8、9四段,总压下量为7.8mm。使用电磁搅拌,电磁搅拌位置为4、5段,电磁搅拌频率为5hz,电磁搅拌电流为370a。换包时中包液位为29.5吨,使用中碳低合金保护渣,渣子干燥,液渣层厚度为12mm。浇注时,采用保护浇注,长水口密封氩气压力为0.42mpa,流量为140l/min;中间包浸入水口密封氩气压力为0.22mpa,流量为15l/min。板坯加热时采用步进式加热炉,连铸坯出炉温度1260℃,加热时间260分钟,板坯在均热段的加热时间为42分钟。板坯在加热炉中加热时活动梁托起板坯的移动速度为1.3m/min。加热时使用高炉煤气和焦炉煤气的混合煤气,混合煤气热值为2500kcal/m3。板坯的(重量百分比)化学成分为:c 0.190%,si 0.4%,mn 1.60%,nb:0.055%;v:0.055%;p 0.010%,s 0.001%,al s0.013%,ca0.0012%,ti0.022%,h 1.0ppm,o 0.002%,n 0.0028%;余量为fe和不可避免的杂质。钢板轧完后进行层流冷却,acc上喷梁的水量为560l/(m2·
min),下喷梁水量为1120l/(m2·
min)acc水温为18℃,终冷温度为640℃,acc冷却时使用头部遮蔽和边部遮蔽,头部遮蔽长度1.5m,遮蔽系数为0.6,边部遮蔽宽度为0.15m。详细的轧制及冷去工艺见表3,其力学性能见表4。
[0039]
表3轧制及冷却工艺
[0040][0041]
表4钢板力学性能
[0042][0043]
实施例3
[0044]
采用250mm厚、2000mm宽板坯,轧制成厚度为20mm厚钢板,在宽厚板轧机上生产。板坯中心偏析为c1.5,中心疏松为1.0级。铁水冶炼前脱硫,脱硫后拔渣,冶炼时不加入轧钢、海绵铁。rh精炼真空处理过程在4.1分钟降到120pa,小于130pa保持时间为16.5分钟,rh精炼软吹时间为13分钟。钢水浇铸时过热度为26℃,连铸时采用轻压下,轻压下位置为6、7、8、9四段,总压下量为7.8mm。使用电磁搅拌,电磁搅拌位置为4、5段,电磁搅拌频率为5hz,电磁搅拌电流为370a。换包时中包液位为29.8吨,使用中碳低合金保护渣,渣子干燥,液渣层厚度为11mm。浇注时,采用保护浇注,长水口密封氩气压力为0.40mpa,流量为134l/min;中间包浸入水口密封氩气压力为0.22mpa,流量为16.5l/min。板坯加热时采用步进式加热炉,连铸坯出炉温度1252℃,加热时间253分钟,板坯在均热段的加热时间为40分钟。板坯在加热炉中加热时活动梁托起板坯的移动速度为1.3m/min。加热时使用高炉煤气和焦炉煤气的混合煤气,混合煤气热值为2453kcal/m3。板坯的(重量百分比)化学成分为:c 0.185%,si 0.28%,mn 1.65%,nb:0.051%;v:0.058%;p 0.009%,s 0.002%,al s0.018%,ca0.0021%,ti0.017%,h 1.1ppm,o 0.0022%,n 0.0029%;余量为fe和不可避免的杂质。钢板轧完后进行层流冷却,acc上喷梁的水量为526l/(m2·
min),下喷梁水量为1080l/(m2·
min)acc水温为17.4℃,终冷温度为652℃,acc冷却时使用头部遮蔽和边部遮蔽,头部遮蔽长度1.5m,遮蔽系数为0.6,边部遮蔽宽度为0.15m。详细的轧制及冷去工艺见表5,其力学性能见表6。
[0045]
表5轧制及冷却工艺
[0046][0047]
表6钢板力学性能
[0048][0049]
以上所述的实施例仅是对本发明的优选方式进行描述,并非对本发明的范围进行限定,在不脱离本发明设计精神的前提下,本领域普通技术人员对本发明的技术方案做出的各种变形和改进,均应落入本发明权利要求书确定的保护范围内。
再多了解一些
本文用于创业者技术爱好者查询,仅供学习研究,如用于商业用途,请联系技术所有人。