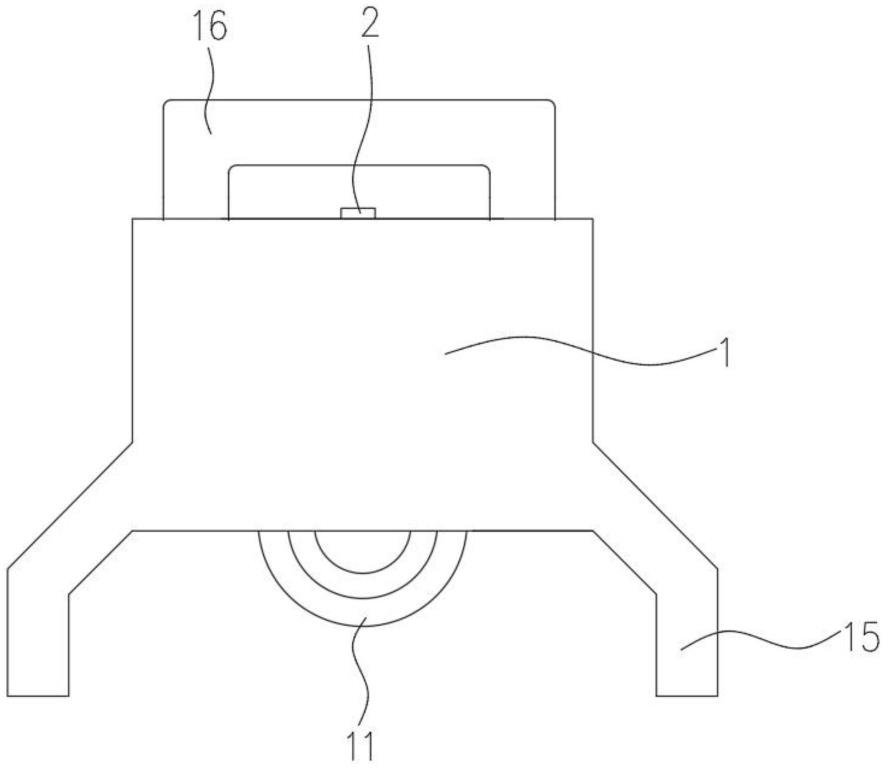
1.本技术涉及钢管生产技术领域,尤其是一种连轧机前台芯棒支撑托辊高度快 速标定校验装置及方法。
背景技术:
2.连轧管机作为热轧无缝钢管生产的主要变形工序之一,芯棒是连轧管机关 键的内变形工具,轧制过程中芯棒与连轧机轧辊共同作用,将毛管轧制到预设 壁厚。
3.连轧机生产过程中,一组芯棒循环使用,轧制后的芯棒经冷却、润滑后返 回连轧机前台等待再次轧制。轧制开始前,润滑后的芯棒被横移到芯棒支撑辊 上,由限动齿条驱动穿入毛管内部,随后与毛管一起进入连轧机轧制。
4.芯棒穿入毛管过程中,芯棒中心高度要与连轧机轧制中心线高度保持一致, 以保证连轧后荒管壁厚精度,同时降低芯棒消耗,提高芯棒寿命。对于不同直 径的芯棒,为保证芯棒中心高度与轧制中心线高度保持一致,需要根据芯棒直 径变化准确调整芯棒支撑辊的高度。
5.实际生产线上,芯棒支撑辊高度调整通常是通过液压缸组件驱动,液压缸 组件配置有位移传感器,自动化控制程序输出位移指令,液压缸组件根据收到 的位移指令驱动芯棒支撑辊运行高预设高度。自动化控制程序输出位移指令之 前,需要对应芯棒支撑辊液压缸组件位置进行标定及拟合计算:在液压缸组件 运行范围内,任意选取一系列位置点,测量芯棒支撑辊高度,并换算出其对应 的与轧制中心线高度一致的芯棒直径值,通过数据分析拟合出液压缸组件位移 值与芯棒支撑辊芯棒位高度的数学关系式,然后将实际生产所用芯棒直径值, 输入得到的数学关系式,计算其对应的液压缸组件位移值。
6.常规芯棒支撑辊标定过程中,需要手动多次测量芯棒支撑辊辊面的高度, 实际操作通常测量辊身外缘处圆柱区域的高度,再通过理论辊身外缘直径换算 芯棒中心高度。由于手动测量极不方便,即便设计辅助测量工具,也无法避免 测量结果存在随机偏差,同时辊身加工精度、设备磨损等因素,也会导致测量 偏差,多个因素累积,进一步扩大测量偏差;使用存在随机偏差的一组数据拟 合出的数学关系式,计算出液压缸组件的位移数据,也必然与实际值有出入, 最终导致芯棒中心高度与轧制中心线高度有偏差,影响产品质量及芯棒寿命。
技术实现要素:
7.为了改善常规芯棒支撑辊标定过程中,需要手动多次测量芯棒支撑辊辊面 的高度容易产生误差,最终导致芯棒中心高度与轧制中心线高度有偏差,影响 产品质量及芯棒寿命的问题,本技术提供一种连轧机前台芯棒支撑托辊高度快 速标定校验装置及方法。
8.本技术提供的一种连轧机前台芯棒支撑托辊高度快速标定校验装置及方法 采用以下技术方案:
9.第一方面,一种连轧机前台芯棒支撑托辊高度快速标定校验装置,包括主 体件和
多个以可独立的被驱动的上下移动的方式设置于所述主体件的多个标定 校验件,所述标定校验件设有标定校验圆弧,且每个标定校验件的标定校验圆 弧的直径与对应型号的芯棒的直径相同;在标定或者校验时,对应于某一芯棒 的所述标定校验件被驱动下移,使其标定校验圆弧的轴线与该芯棒的标准位置 的中心线重合,从而标定并校验用于该芯棒的托辊的位置。
10.可选的,所述主体件底侧沿竖直方向设有与标定校验件数量相同的移动槽, 多个所述标定校验件可滑动插设于移动槽内;所述主体件内设有多组用于更换 标定校验件的调节螺杆,所述调节螺杆沿竖直方向转动插设于主体件,所述调 节螺杆插设于主体件的一端与标定校验件螺纹配合使用。
11.可选的,多个所述标定校验件插设于主体件内的一端均设有连接板,所述 连接板的两侧均设有限位板,所述主体件位于移动槽的侧壁上沿竖直方向设有 限位槽,所述限位板插设于限位槽内使标定校验件刚好移动至主体件外。
12.可选的,所述标定校验件与移动板可拆卸连接。
13.可选的,所述标定校验件的平面侧设有沿竖直方向设有连接板,所述连接 板插设于移动板内,所述移动板内设有用于将连接板固定的卡固件。
14.可选的,所述移动板的底侧沿竖直方向设有安装槽,所述连接杆插设于连 接槽内,所述安装槽的两侧槽壁上设有安装孔,所述卡固件设置于安装孔内; 所述卡固件为弹簧插销,且插销头呈圆弧状,所述连接板的侧壁上设有呈弧形 的卡槽,所述弹簧插销插设于卡槽将连接板固定在安装槽内。
15.可选的,所述主体件位于顶部设有与移动槽连通的检修口,所述主体件上 设有用于将检修口封闭的盖板,多根所述调节螺杆转动设置于盖板上,所述盖 板通过螺钉固定于主体件上。
16.可选的,所述主体件的两端设有支撑板,两块所述支撑板分别放置于芯棒 位的两侧。
17.可选的,所述标定校验件的中心到支撑板的距离与轧制中心线到支撑板的 水平距离相同。
18.第二方面,一种连轧机前台芯棒支撑托辊高度快速标定校验方法,包括以 下步骤:
19.s1、标定时,根据芯棒尺寸,选择相应的标定校验件,转动调节螺杆,使 相应的标定校验件移动至主体件下侧;
20.s2、将主体件竖直放置在芯棒位上方,检查确认主体件两侧支撑板处于同 一水平线上,用水平仪检查确认支撑板处于竖直状态;
21.s3、缓慢移动芯棒支撑辊,让芯棒支撑辊v型辊面两侧都与标定校验件的 弧面刚好接触;
22.s4、自动化程序记录此时液压缸位移传感器的读数,完成芯棒支撑辊对应 该规格芯棒的芯棒位标定;
23.s5、更换不同直径的芯棒,同时选择相应的标定校验件,重复s1-s4;
24.s6、校验时,将芯棒支撑辊自动运行到当前使用芯棒的芯棒位;
25.s6、将主体件竖直放置在芯棒位上方,使主体件位于芯棒支撑辊横截面的 正上
方;
26.s8、用塞尺测量标定校验件与芯棒支撑辊v型辊面两侧的间隙,根据间隙 测量结果判断芯棒支撑辊位置是否满足生产要求。
27.综上所述,本技术包含以下至少一种有益效果:
28.1.标定时,按照实际使用芯棒的直径规格,设计相应的主体件,标定校验 件在竖直平面的投影与当前使用相应芯棒在芯棒位时的横截面投影重合,标定 校验件圆弧面与芯棒支撑辊的接触状态,即是实际使用芯棒在芯棒位与芯棒支 撑辊的接触状态,这样就可直接确定实际生产中芯棒支撑辊芯棒位的准确高度 位置,工具简单易得,标定时间少,标定高度位置准确,可有效提高标定工作 的效率及效果;
29.2.校验时,只需将芯棒支撑辊自动运行到当前使用芯棒的芯棒位,然后将 对应的主体件竖直放置在限动齿条导轨上,横移主体件使其位于芯棒支撑辊横 截面的正上方,用塞尺测量标定校验件与芯棒支撑辊v型辊面两侧的间隙,根 据间隙测量结果判断芯棒支撑辊位置是否满足生产要求,如不满足即需要重新 标定;
30.3.标定不同直径的芯棒时,可以通过调节螺杆选择使用相同的标定校验件, 使用更加方便,不需要根据不同尺寸的芯棒生产不同的标定卡尺,通用性更好, 同时标定校验件可拆卸,方便定期对标定校验件进行更换,能够避免标定校验 件受损对测量造成误差。
附图说明
31.图1是本技术实施例的结构示意图。
32.图2本技术实施例的正面剖视图。
33.图3是图2中a部分的放大图。
34.图4是本技术实施例的仰视图。
35.图5是本技术实施例的俯视图。
36.图6是本技术实施例的使用状态图。
37.附图标记说明:
38.1、主体件;11、标定校验件;111、连接板;112、卡槽;12、移动槽;121、 限位槽;13、移动板;131、限位板;132、安装槽;133、安装孔;14、卡固件;15、支撑板;16、把手;17、检修口;18、盖板;2、调节螺杆。
具体实施方式
39.以下通过特定的具体实例说明本技术的实施方式,本领域技术人员可由本 说明书所揭露的内容轻易地了解本技术的其他优点与功效。本技术还可以通过 另外不同的具体实施方式加以实施或应用,本说明书中的各项细节也可以基于 不同观点与应用,在没有背离本技术的精神下进行各种修饰或改变。需要说明 的是,以下实施例中所提供的图示仅以示意方式说明本技术的基本构想,在不 冲突的情况下,以下实施例及实施例中的特征可以相互组合。
40.其中,附图仅用于示例性说明,表示的仅是示意图,而非实物图,不能理 解为对本技术的限制;为了更好地说明本技术的实施例,附图某些部件会有省 略、放大或缩小,并不代表实际产品的尺寸;对本领域技术人员来说,附图中 某些公知结构及其说明可能省略是
可以理解的。
41.以下结合附图1-6对本技术实施例作进一步详细说明。
42.本技术实施例提供一种连轧机前台芯棒支撑托辊高度快速标定校验装置及 方法。参照图1和图2,连轧机前台芯棒支撑托辊高度快速标定校验装置包括 主体件1,主体件1包括主体件1和多个与不同直径的芯棒相对应的标定校验 件11,标定校验件11的底侧设有直径与不同直径的芯棒分别对应的圆弧面, 本实施例中标定校验件11为半圆板,多个标定校验件11的平面侧设置于主体 件下侧,且标定校验件11的圆心位于同一条水平线上,本实施例中标定校验件 11设置有三块,三块标定校验件11由大到小依次排列设置,且多个标定校验 件11均能够移动至主体件1内部,标定校验件11的圆弧面与芯棒位的面接触, 标定校验件11在竖直平面的投影与实际使用的芯棒在芯棒位时的横截面投影 重合。
43.参照图2和图4,在主体件1的底侧向上设置有移动槽12,移动槽12的数 量与标定校验件11的数量相同,三块标定校验件11平面侧分别插设于三个移 动槽12内,标定校验件11能够完全移动至移动槽12内。在主体件1的顶部沿 竖直方向设置有调节螺杆2,调节螺杆2的低端插设于主体件1内,且转动设 置于主体件1上,调节螺杆2插设于主体件1的一端插设于标定校验件11内, 且标定校验件11的平面侧固定有螺纹套,调节螺杆2与螺纹套螺纹配合,通过 转动调节螺杆2能够使标定校验件11竖向移动,能够根据标定的芯棒尺寸更换 相应的标定校验件11,使用更加方便,通用性更好。为了方便转动调节螺杆2, 调节螺杆2的顶部设置为内六角螺母。
44.参照图2,为了避免在更换标定校验件11时,标定校验件11的位置不准 确导致标定误差的情况出现,标定校验件11的平面侧沿竖直方向设置有移动板 13,移动板13插设与移动槽12内,调节螺杆2插设于移动板13内,且螺纹套 固定在移动板13上。移动板13的两侧沿竖直方向设置有限位板231,主体件1 位于移动槽12的两侧槽壁上沿竖直方向设置有限位槽121,限位槽121延伸至 靠近移动槽12槽口的位置,限位板231插设于限位槽121内。更换标定校验件 11时,标定校验件11刚好移动至主体件1外时,限位板131抵触在限位槽121 底部的槽壁上,能够对标定校验件11的移动行程起到限制的作用,同时也能够 对标定校验件11的位置起到定位的作用,标定时更加准确。
45.参照图2和图3,标定校验件11在长期使用过程中容易出现摩擦,使得标 定校验件11收到磨损,对标定结果容易出现误差,为了减小标定的误差,需要 定期对标定校验件11继续宁更换,为了方便对标定校验件11进行更换,在移 动板13的底部沿竖直方向开设有安装槽131,在标定校验件11的平面侧沿竖 直方向设置有连接板111,连接板111插设于安装槽131内,在安装槽131内 的两侧槽壁上开设有安装孔132,在安装孔132内固定有用于将连接板111固 定的卡固件14,本实施例中卡固件14为弹簧插销,且插销头呈圆弧状并伸出 安装孔132,在连接板111的两侧侧壁上开设有呈弧形的卡槽112。
46.将连接板111插入安装槽131时,连接板111将插销挤压至安装孔132内, 插销在弹簧的作用下插入连接板111的卡槽112内,将标定校验件11固定在移 动板13上,方便定期对标定校验件11进行更换。同时连接板111的位置需要 与调节螺杆2错开,且同一块标定校验件11上的连接板111对称设置有两块, 安装槽131也对称设置有两个,调节螺杆2位于两块连接板111之间,能够使 标定校验件11安装受力更加均匀,安装更加稳固。
47.参照图2和图5,主体件1在长期使用过程中容易出现损坏,为了方便进 行维修或
者更换零部件,在主体件1的顶部开设有2检修口17,检修口17与 移动槽12和限位槽132连通,主体件1上还设置有盖板114,盖板114能够将 检修口17封闭,盖板1145通过螺钉固定在主体件1上。调节螺杆2转动设置 在盖板114上,打开盖板114,能够将调节螺杆2、连接板23以及标定校验件 11取出主体件1,进行维修或者更换,同时也能够通过检修口17向移动槽12 内添加润滑油,减小移动板13和移动槽12槽壁之间摩擦,使得移动板13移动 更加顺畅的同时,也能够减小移动板13和主体件1的磨损。
48.参照图1和图2,在主体件1的两端设置有两块相同的支撑板15,两块支 撑板23分别放置于设备的两根限动齿条导轨上,标定校验件11的中心到支撑 板15的距离与轧制中心线到限动齿条导轨面的距离相同。
49.同时,为了方便拿放主体件1,在主体件1的顶侧中间位置还设置有把手 14。
50.一种连轧机前台芯棒支撑托辊高度快速标定校验方法,包括以下步骤:
51.步骤一、标定时,根据芯棒尺寸,选择相应的标定校验件11,转动调节螺 杆2,使相应的标定校验件11移动至主体件1下侧;
52.步骤二、将主体件1竖直放置在芯棒位上方,检查确认主体件1两侧支撑 板15处于同一水平线上,用水平仪检查确认支撑板15处于竖直状态;
53.步骤三、缓慢移动芯棒支撑辊,让芯棒支撑辊v型辊面两侧都与标定校验 件11的弧面刚好接触;
54.步骤四、自动化程序记录此时液压缸位移传感器的读数,完成芯棒支撑辊 对应该规格芯棒的芯棒位标定;
55.步骤五、更换不同直径的芯棒,同时选择相应的标定校验件11,重复步骤 一-步骤四;
56.步骤六、校验时,将芯棒支撑辊自动运行到当前使用芯棒的芯棒位;
57.步骤七、将主体件1竖直放置在芯棒位上方,使主体件1位于芯棒支撑辊 横截面的正上方;
58.步骤八、用塞尺测量标定校验件11与芯棒支撑辊v型辊面两侧的间隙, 根据间隙测量结果判断芯棒支撑辊位置是否满足生产要求。
59.最后说明的是,以上实施例仅用以说明本技术的技术方案而非限制,尽管 参照较佳实施例对本技术进行了详细说明,本领域的普通技术人员应当理解, 可以对本技术的技术方案进行修改或者等同替换,而不脱离本技术方案的宗旨 和范围,其均应涵盖在本技术的权利要求范围当中。
再多了解一些
本文用于创业者技术爱好者查询,仅供学习研究,如用于商业用途,请联系技术所有人。