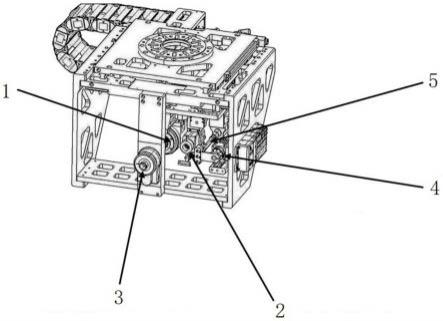
1.本发明涉及末端执行器技术领域,具体地,涉及一种基于钻铆铣一体化的工业机器人末端执行器。
背景技术:
2.航天装备制造业是高科技支柱的基础产业,具有知识技术密集、系统复杂、质量可靠性要求高等特点。我国航空航天制造企业相比较大环境下的“工业4.0”浪潮有着较大的差距,主要表现在以下两个方面:制造技术基础薄弱,先进制造技术研究应用不够,整体工艺水平不高。航天制造企业一直遵循以研制为主、单件及小批量生产为主的生产制造模式,制造技术能力及水平在某些单项方面处于领先地位,但整体工艺技术水平仍然不高;制造装备柔性化和智能化程度低,大量采用专用工装和夹具,难以适应航天产品多品种、小批量的特性,增加了企业的生产成本,降低了企业的生产效率,制约了航天装备制造业的发展。
3.航天装备制造作为中国制造业的重要组成部分,对于制造技术的先进性、智能化和可靠性的需求尤为关键,其发展也能大力促进制造业的发展。智能制造作为新的制造模式和技术,可为高品质复杂零件制造提供新的解决方案,更适应多品种小批量产品生产的需要。智能制造可以利用机器人技术、传感技术、智能技术实现制造过程的无人化,提高产品的生产效率和可靠性。
4.近几年,机器人锤铆已成为国内外学者研究的热点,国内外众多学者、专家就机器人锤铆振动对铆接质量影响进行了分析,指出在机器人锤铆过程中,应对工艺参数进行优化,从而避免振动频率接近机器人固有频率,合理规划机器人姿态,从而进一步提高机器人锤铆质量。另有学者对机器人铆接在航空航天制造和装配中的典型场景(梁肋组合)应用时,对机器人锤铆工具的可达性,及障碍规避的路径规划进行了研究。
技术实现要素:
5.基于此,本发明提供了一种基于钻铆铣一体化的工业机器人末端执行器,具有模块化程度高、控制可靠性高的特点。
6.为实现上述目的,本发明采用如下技术方案:一种基于钻铆铣一体化的工业机器人末端执行器,包括:设置于工业机器人末端的模块化集成主轴系统、机器视觉基准孔位检测系统、法向找正压力脚系统、插钉送钉系统、铆接系统,所述法向找正压力脚系统设置于工业机器人末端最前端,所述模块化集成主轴系统的中心与法向找正压力脚系统的中心位于同一条轴线上,所述模块化集成主轴系统的侧边依次设有机器视觉基准孔位检测系统、铆接系统和插钉送钉系统,所述视觉基准孔位检测系统、铆接系统均与模块化集成主轴系统位于同一水平面上,所述视觉基准孔位检测系统、铆接系统均与模块化集成主轴系统均与伺服电机连接,所述铆接系统和插钉送钉系统连接。
7.进一步地,所述法向找正压力脚系统包括:控制器、外壳以及设置于外壳中的力传感器、压力角鼻尖、吸尘通道、自动除屑装置、找正调节系统,所述找正调节系统设置于压力
角鼻尖的后方,所述力传感器设置于找正调节系统的后方,所述控制器分别与力传感器、找正调节系统连接,所述压力角鼻尖与加工件进行接触,所述压力角鼻尖中设有内孔,所述内孔与吸尘通道连接,所述吸尘通道与自动除屑装置连接。
8.进一步地,所述机器视觉基准孔位检测系统包括:框架、相机和光学镜头组成,所述框架中设有相机,相机的前端设有光学镜头,所述框架上设有凹槽,通过滑轨与工业机器人末端连接。
9.进一步地,所述模块化集成主轴系统包括:电主轴、刀具、刀柄、进给滑台、限位开关、进给伺服、plc控制系统,所述进给伺服通过丝杆与电主轴连接,所述电主轴设置于进给滑台上,所述刀柄设置于电主轴上,所述刀柄上设有刀具,所述电主轴的下方设有限位开关;所述限位开关、进给伺服均与plc控制系统连接。
10.进一步地,还包括刀具检测系统,所述刀具检测系统由对射光电开关、报警模块组成,所述对射光电开关设置于工业机器人末端上,与模块化集成主轴系统相对,所述报警模块设置于工业机器人末端上,所述对射光电开关、报警模块均与plc控制系统连接。
11.进一步地,所述插钉送钉系统包括:储钉装置、铆钉吸盘、铆钉、吹气装置、吹钉装置,所述储钉装置设置于工业机器人末端上,所述储钉装置中设有铆钉,所述铆钉通过吹气装置与吹钉装置连接,所述吹钉装置与铆接系统连接。
12.进一步地,所述铆接系统包括:铆锤枪、气锤支架、锤铆杆、锤铆驱动装置、铆钉锤头、选钉机构,所述锤铆枪和锤铆杆的一端通过气锤支架连接,且所述锤铆枪、气锤支架均设置于锤铆驱动装置上,所述锤铆驱动装置与工业机器人末端滑动连接,所述锤铆杆的另一端与铆钉锤头连接,所述铆钉锤头与选钉机构连接,所述选钉机构与工业机器人末端连接。
13.与现有技术相比,本发明具有如下有益效果:本发明基于钻铆铣一体化的工业机器人末端执行器将机器视觉基准孔位检测系统、法向找正压力脚系统、插钉送钉系统、铆接系统集成于一体,实现了一台设备完成多项功能的要求,提高了生产效率,实现了生产自动化;本发明法向找正压力脚系统中设有自动除屑装置,可以保证在加工过程中生产场地的清洁问题,防止加工废屑飞溅;本发明插钉送钉系统可以实现多种不同规格铆钉的输送,提高了兼容性,满足了多种不同工况的需求。
附图说明
14.图1为本发明基于钻铆铣一体化的工业机器人末端执行器的结构示意图;
15.图2为本发明中法向找正压力脚系统的结构示意图;
16.图3为本发明中机器视觉基准孔位检测系统的结构示意图;
17.图4为本发明中模块化集成主轴系统的结构示意图;
18.图5为本发明中气锤铆接系统的结构示意图。
具体实施方式
19.下面结合附图对本发明的技术方案作进一步地解释说明。
20.如图1为本发明基于钻铆铣一体化的工业机器人末端执行器的结构示意图,该工业机器人末端执行器具有基准检测、法向找正、自动钻孔、锪窝以及气锤铆接功能,该工业
机器人末端执行器包括:设置于工业机器人末端的模块化集成主轴系统1、机器视觉基准孔位检测系统2、法向找正压力脚系统3、插钉送钉系统4、铆接系统5,法向找正压力脚系统3设置于工业机器人末端最前端,法向找正压力脚系统3的主要作用是找准法向和压紧工件;模块化集成主轴系统1的中心与法向找正压力脚系统3的中心位于同一条轴线上,模块化集成主轴系统1是钻孔主要的执行机构;模块化集成主轴系统1的侧边依次设有机器视觉基准孔位检测系统2、铆接系统5和插钉送钉系统4,机器视觉基准孔位检测系统2、铆接系统5均与模块化集成主轴系统1位于同一水平面上,机器视觉基准孔位检测系统2、铆接系统5均与模块化集成主轴系统1均与伺服电机连接,通过伺服电机驱动机器视觉基准孔位检测系统2、铆接系统5均与模块化集成主轴系统1在水平和竖直方向上水平移动,铆接系统5和插钉送钉系统4连接;机器视觉基准孔位检测系统1主要用来对基准孔进行检测,铆接系统5的主要作用是把铆钉铆接在工件上,插钉送钉系统4的主要作用是把铆钉送到铆接系统5中。本发明工业机器人末端执行器可实现钻铆加工、检测等功能,包括:压力脚压紧、进给控制、主轴变速、刀具检测、锪窝深度检测等。
21.如图2,本发明中法向找正压力脚系统3包括:控制器、外壳31以及设置于外壳31中的力传感器32、压力角鼻尖33、吸尘通道34、自动除屑装置、找正调节系统35,找正调节系统35设置于压力角鼻尖33的后方,力传感器32设置于找正调节系统35的后方,控制器分别与力传感器32、找正调节系统35连接,压力角鼻尖33与加工件进行接触,压力角鼻尖33中设有内孔,内孔与吸尘通道34连接,吸尘通道34与自动除屑装置连接,吸尘通道34是废屑排出的通道,然后进入废屑收集装置。本发明中力传感器32用来测量压力角鼻尖33上各个方向的力的均匀性是否一致,如果力不一致,则通过找正调节系统35进行位置调节,使得力传感器32测得的各个方向的力相同。本发明中法向找正压力脚系统3具备自动法向找正功能,使刀具轴线与加工表面垂直,该法向找正压力脚系统3具有保护功能,防止压力脚系统将产品压紧后产生位移损伤产品。在制孔时,自动确定孔位以及孔法向检测与调整,调整精度≤0.25
°
,调整角度范围
±3°
,具有法向自动校准功能。本发明中法向找正压力脚系统对工件表面的压紧力作用可以减少夹层间隙,增加制孔过程中的刚性,提高制孔质量。
22.由于工件在制造、装配过程中存在误差,造成待加工孔位与理论数模存在偏差,系统在加工前需对工件上的基准孔进行拍照,从而对理论数模的孔位信息进行修正;基准找正是机器人自动制孔中的一个重要环节,该环节直接影响整个制孔过程中的位置精度。基准检测的任务就是检测基准孔在产品坐标系下的实际位置,修正实际位置与理论位置的偏差,继而根据待加工孔在数模中的位置控制工业机器人进行制孔工作。如图3,本发明中机器视觉基准孔位检测系统2包括:框架21、相机22和光学镜头23组成,框架21中设有相机22,相机22的前端设有光学镜头23,框架21上设有凹槽,通过滑轨与工业机器人末端连接。本发明中相机22能够实现工装基准以及产品基准的自动检测,根据基准检测信息,结合工业机器人的位置和姿态信息,实现对加工基准坐标的提取,确保精确测量工件上的基准点位置满足基准孔自动找正误差≤0.05mm,具有误差补偿功能。该机器视觉基准孔位检测系统可以检测圆孔、柱形钉帽、边缘等功能。
23.如图4,本发明中模块化集成主轴系统1包括:电主轴11、刀具12、刀柄、进给滑台13、限位开关14、进给伺服15、plc控制系统,进给伺服13通过丝杆与电主轴11连接,进给伺服13主要用来驱动电主轴11进行进给运动,通过进给伺服13进行相应的运动配合光栅尺能
实现高精度的定位;电主轴11设置于进给滑台13上,刀柄设置于电主轴11上,刀柄上设有刀具12,可以根据钻孔的大小选择对应刀具的安装;电主轴11的下方设有限位开关14,对电主轴11移动进给进行的软限位;限位开关14、进给伺服13均与plc控制系统连接。本发明模块化集成主轴系统采用标准化smfee生产技术,模块化快速装拆,极大的提高了集成的效率和可靠性。具体地,在压力脚压紧工件并接到plc控制系统的钻孔信号之后,plc控制系统控制进给伺服13带动电主轴11转动,从而带动刀具12进给,同时自动除屑装置开启,吸除钻削过程产生的废屑。当钉孔将要钻透时,plc控制系统控制进给伺服13,从而调整电动主轴11进给速度,控制钻头轴向力,减小铆钉出口的毛刺,提高铆钉孔的质量。然后进给伺服13控制钻、铰、锪一体化刀具继续进给,刀具铰削段工作,完成铰削工作后,进给伺服13再次进给,刀具锪窝段工作,完成锪窝工序。在锪窝过程中,电主轴11进给传感器精确检测电主轴11进给量并反馈至控制单元,精确控制主轴锪窝进给量,保证锪窝深度性能指标。在制孔时,具有切削力、切削功率、主轴扭矩、主轴转速以及进给速度等同步显示。
24.本发明中电主轴11采用航空加工高精度电主轴为国际一线品牌fischer主轴,刀具尾柄采用标准的hsk系列,主轴扭矩10n
·
m,主轴最大转速24000r/min,主轴功率≥15kw,电主轴径向跳动0.005mm,电主轴轴向窜动≤0.003mm,电主轴进给行程:150mm;外部具有润滑及防护措施。制孔效率:在铝合金叠层材料6mm的标准试件上,紧固件直径为3.5mm时,单台自动制孔设备的制孔速度≥6个/min;任意状态下主轴端面径向跳动0.005mm,轴向跳动≤0.003mm,定位精度标准按iso230-2-1997。电主轴进给定位精度≤0.01mm,钻孔主轴圆跳动:0.005mm,孔径精度h7。电主轴采用水冷却方式进行冷却,具有自动润滑和温度异常报警功能;有冷却钻头的功能,并设置润滑剂回收装置,避免污染产品;配有一套装刀装置,方便刀具安装等功能。
25.本发明模块化集成主轴系统中还包括刀具检测系统,刀具检测系统由对射光电开关、报警模块组成,对射光电开关设置于工业机器人末端上,与模块化集成主轴系统相对,报警模块设置于工业机器人末端上,对射光电开关、报警模块均与plc控制系统连接。本发明中刀具检测系统通过对射光电开关照射刀具,如果加工刀具发生断裂,则对射光电开关将异常信号传送给plc控制系统,plc控制系统触发报警模块进行预警。
26.本发明中插钉送钉系统包括:储钉装置、铆钉吸盘、铆钉、吹钉装置,储钉装置设置于工业机器人末端上,储钉装置中设有铆钉,铆钉通过铆钉吸盘与吹钉装置连接,吹钉装置与铆接系统连接。通过铆钉吸盘吸取储钉装置中的铆钉,送入吹钉装置中,从而进入铆接系统中,进行铆接。
27.如图5,本发明中铆接系统5包括:铆锤枪51、气锤支架52、锤铆杆53、锤铆驱动装置54、铆钉锤头55、选钉机构56,锤铆枪51和锤铆杆53的一端通过气锤支架52连接,且锤铆枪51、气锤支架52均设置于锤铆驱动装置54上,锤铆驱动装置54与工业机器人末端滑动连接,锤铆驱动装置54带到铆接系统5在工业机器人末端上移动;锤铆杆53的另一端与铆钉锤头55连接,铆钉锤头55与选钉机构56连接,选钉机构56与工业机器人末端连接。选钉机构56与吹钉装置连接,将铆钉送入锤铆锤头55中,通过锤铆枪51带动锤铆杆53的往复运动,撞击铆钉。
28.本发明基于钻铆铣一体化的工业机器人末端执行器将机器视觉基准孔位检测系统、法向找正压力脚系统、插钉送钉系统、铆接系统集成于一体,实现了一台设备完成多项
功能的要求,提高了生产效率,实现了生产自动化。
29.以上仅是本发明的优选实施方式,本发明的保护范围并不仅局限于上述实施方式,凡属于本发明思路下的技术方案均属于本发明的保护范围。应当指出,对于本技术领域的普通技术人员来说,在不脱离本发明原理前提下的若干改进和润饰,应视为本发明的保护范围。
再多了解一些
本文用于创业者技术爱好者查询,仅供学习研究,如用于商业用途,请联系技术所有人。