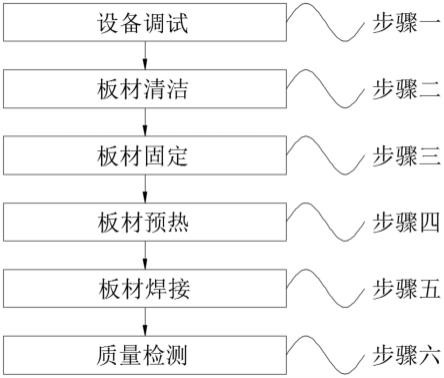
1.本发明涉及焊接技术领域,具体为一种铝合金厚板搅拌摩擦焊接工艺。
背景技术:
2.搅拌摩擦焊接技术利用摩擦热软化和连接构件,不需要常规焊接技术所必需的焊接填充材料和保护气体,且输入工件的热量较低,产生的热收缩也很小,在连接后几乎没有变形;但现有的搅拌摩擦焊接技术存在以下缺陷:一是搅拌摩擦焊接易产生飞边毛刺,通常是在完成焊接后磨光去除,增添了额外的生产工序;二是在进行焊接前,需要根据板材的材质及厚度对设备进行参数预设,然而设备间的性能存在差异,且已知的工艺参数仅仅为理论参数,并非是该设备的最优工艺参数;三是焊接前需要去除油污及氧化膜,但该步骤缺乏严格的质量管控,无法确认氧化膜是否完全去除。
技术实现要素:
3.本发明的目的在于提供一种铝合金厚板搅拌摩擦焊接工艺,以解决上述背景技术中提出的问题。
4.为实现上述目的,本发明提供如下技术方案:一种铝合金厚板搅拌摩擦焊接工艺,包括以下步骤:步骤一,设备调试;步骤二,板材清洁;步骤三,板材固定;步骤四,板材预热;步骤五,板材焊接;步骤六,质量检测;
5.其中在上述步骤一中,首先根据样板的厚度选择对应的工艺参数模板,对样板进行焊接加工,参数调节系统自动为工艺参数添加补偿值,经过多次调试,参数调节系统不断对工艺参数模板进行优化,直至焊接头在不同动作下的工作温度均趋于最优值,则此时的工艺参数模板为最优工艺参数模板;
6.其中在上述步骤二中,使用清洗剂和脱膜剂清洗待加工板材,去除油污和氧化膜,热风吹干后,使用涡流测厚仪检测氧化膜是否完全去除;
7.其中在上述步骤三中,使用夹具将预处理后的板材固定在垫板上,调节夹具,使板材焊接部位对接;
8.其中在上述步骤四中,对板材进行预热处理,预热时间为50-70s,预热后温度为220-270℃;
9.其中在上述步骤五中,启动设备,根据待加工板材的厚度选择对应的最优工艺参数模板,运行加工程序,焊接头定位至板材待焊接的缝隙处,并按照设定工艺参数旋转进入,旋转停留一段时间后,沿焊接方向进行移动焊接,待完成焊接后,焊接头旋转移出,得到成品;
10.其中在上述步骤六中,利用超声波检测仪对步骤五中焊接好的成品进行质量检验。
11.优选的,所述步骤一中,参数调节系统包括数据存储模块、数据处理模块、温度监测模块、参数补偿模块和控制器,且数据处理模块分别与数据存储模块、温度监测模块、参
数补偿模块和控制器建立数据连接,数据存储模块中设置有工艺参数模板数据库。
12.优选的,所述参数调节系统具体工作方法为:由数据处理模块读取数据存储模块中的工艺参数模板,并据此发出指令给控制器,控制器根据指令控制电机的运转,焊接头按程序动作,温度监测模块采集焊接头各动作下的温度数据,并传输给数据处理模块,数据处理模块分析焊接头在各项动作中的实际温度与最优温度的差值,并传输给参数补偿模块,参数补偿模块据此为各项动作中的工艺参数添加补偿值,获得优化后的工艺参数,并传输给数据处理模块,由数据处理模块更新数据库,其中,当实际温度与最优温度的差值符合要求时,则判定当前工艺参数模板为最优工艺参数模板,否则继续对工艺参数模板进行优化。
13.优选的,所述步骤一中,第一次调试采用的是无补偿值的工艺参数模板,余下几次调试采用的是基于上一次参数优化后所得到的工艺参数模板,优化次数为3-6次。
14.优选的,所述步骤一中,工艺参数模板包括以下参数:旋转速度、插入深度、插入速度、插入停留时间、焊接速度、焊接压力、回抽停留时间和回抽速度,焊接头的动作包括插入、停留、移动及拔出。
15.优选的,所述焊接头包括焊接头本体,焊接头本体上固定连接有第一限位圈,第一限位圈的上表面开设有凹槽,第一限位圈上套接有套筒,套筒的外壁上固定连接有刀片,套筒的内壁上固定连接有第二限位圈,第二限位圈的下表面固定连接有凸块,且凸块插接于凹槽的内部。
16.优选的,所述第二限位圈的上表面安装有螺丝,且第二限位圈通过螺丝固定连接于第一限位圈上。
17.优选的,所述步骤六中,采用横波法检测焊缝缺陷,若声波在传播途中遇到缺陷,部分声波将反射回来,在荧光屏上显示缺陷回波。
18.与现有技术相比,本发明的有益效果是:本发明通过在焊接头上增加铣刀结构,可以实现自动去毛刺的功能,从而减少了加工工序,提高了工作效率;本发明通过不断优化工艺参数模板,可以得到最优工艺参数,以此保证了产品的焊接质量;本发明通过使用涡流测厚仪检测板材的氧化膜是否去除,实现对板材清洁工序的严格管控,从而降低了焊缝不良率。
附图说明
19.图1为本发明的焊接头整体立体结构示意图;
20.图2为本发明的焊接头整体结构爆炸图;
21.图3为本发明的参数调节系统流程图;
22.图4为本发明的工艺流程图;
23.图中:1、焊接头本体;10、第一限位圈;11、凹槽;2、套筒;20、刀片;21、第二限位圈;22、凸块;23、螺丝。
具体实施方式
24.下面将结合本发明实施例中的附图,对本发明实施例中的技术方案进行清楚、完整地描述,显然,所描述的实施例仅仅是本发明一部分实施例,而不是全部的实施例。基于本发明中的实施例,本领域普通技术人员在没有做出创造性劳动前提下所获得的所有其他
实施例,都属于本发明保护的范围。
25.请参阅图1-4,本发明提供的一种实施例:一种铝合金厚板搅拌摩擦焊接工艺,包括以下步骤:步骤一,设备调试;步骤二,板材清洁;步骤三,板材固定;步骤四,板材预热;步骤五,板材焊接;步骤六,质量检测;
26.其中在上述步骤一中,首先根据样板的厚度选择对应的工艺参数模板,对样板进行焊接加工,参数调节系统自动为工艺参数添加补偿值,经过多次调试,参数调节系统不断对工艺参数模板进行优化,直至焊接头在不同动作下的工作温度均趋于最优值,则此时的工艺参数模板为最优工艺参数模板;其中,参数调节系统包括数据存储模块、数据处理模块、温度监测模块、参数补偿模块和控制器,且数据处理模块分别与数据存储模块、温度监测模块、参数补偿模块和控制器建立数据连接,数据存储模块中设置有工艺参数模板数据库;参数调节系统具体工作方法为:由数据处理模块读取数据存储模块中的工艺参数模板,并据此发出指令给控制器,控制器根据指令控制电机的运转,焊接头按程序动作,温度监测模块采集焊接头各动作下的温度数据,并传输给数据处理模块,数据处理模块分析焊接头在各项动作中的实际温度与最优温度的差值,并传输给参数补偿模块,参数补偿模块据此为各项动作中的工艺参数添加补偿值,获得优化后的工艺参数,并传输给数据处理模块,由数据处理模块更新数据库,其中,当实际温度与最优温度的差值符合要求时,则判定当前工艺参数模板为最优工艺参数模板,否则继续对工艺参数模板进行优化;第一次调试采用的是无补偿值的工艺参数模板,余下几次调试采用的是基于上一次参数优化后所得到的工艺参数模板,优化次数为3-6次;工艺参数模板包括以下参数:旋转速度、插入深度、插入速度、插入停留时间、焊接速度、焊接压力、回抽停留时间和回抽速度,焊接头的动作包括插入、停留、移动及拔出;焊接头包括焊接头本体1,焊接头本体1上固定连接有第一限位圈10,第一限位圈10的上表面开设有凹槽11,第一限位圈10上套接有套筒2,套筒2的外壁上固定连接有刀片20,套筒2的内壁上固定连接有第二限位圈21,第二限位圈21的下表面固定连接有凸块22,且凸块22插接于凹槽11的内部,第二限位圈21的上表面安装有螺丝23,且第二限位圈21通过螺丝23固定连接于第一限位圈10上;
27.其中在上述步骤二中,使用清洗剂和脱膜剂清洗待加工板材,去除油污和氧化膜,热风吹干后,使用涡流测厚仪检测氧化膜是否完全去除;
28.其中在上述步骤三中,使用夹具将预处理后的板材固定在垫板上,调节夹具,使板材焊接部位对接;
29.其中在上述步骤四中,对板材进行预热处理,预热时间为50-70s,预热后温度为220-270℃;
30.其中在上述步骤五中,启动设备,根据待加工板材的厚度选择对应的最优工艺参数模板,运行加工程序,焊接头定位至板材待焊接的缝隙处,并按照设定工艺参数旋转进入,旋转停留一段时间后,沿焊接方向进行移动焊接,待完成焊接后,焊接头旋转移出,得到成品;
31.其中在上述步骤六中,利用超声波检测仪对步骤五中焊接好的成品进行质量检验,采用横波法检测焊缝缺陷,若声波在传播途中遇到缺陷,部分声波将反射回来,在荧光屏上显示缺陷回波。
32.基于上述,本发明的优点在于,该发明使用时,将套筒2安装在焊接头本体1上,使
凸块22插接于凹槽11的内部,并通过螺丝23将第二限位圈21和第一限位圈10固定,其中,套筒2、第二限位圈21和凸块22为一体式结构,焊接头本体1和第一限位圈10为一体式结构,在焊接头本体1旋转时,刀片20会销去毛刺;本发明通过获取最优工艺参数模板,实现对加工温度的最优控制,以此保障了产品质量;同时,本发明从根源上对板材的质量进行管控,减少杂质的引入,从而降低了焊缝不良。
33.对于本领域技术人员而言,显然本发明不限于上述示范性实施例的细节,而且在不背离本发明的精神或基本特征的情况下,能够以其他的具体形式实现本发明。因此,无论从哪一点来看,均应将实施例看作是示范性的,而且是非限制性的,本发明的范围由所附权利要求而不是上述说明限定,因此旨在将落在权利要求的等同要件的含义和范围内的所有变化囊括在本发明内。不应将权利要求中的任何附图标记视为限制所涉及的权利要求。
再多了解一些
本文用于创业者技术爱好者查询,仅供学习研究,如用于商业用途,请联系技术所有人。