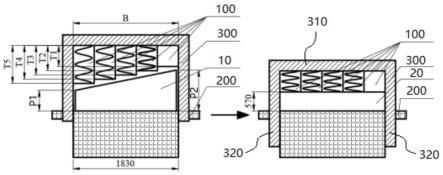
1.本发明涉及锻造领域,尤其涉及一种弧形锻件的差速锻造方法及成形模具。
背景技术:
2.现有弧形锻件锻造方法如图2所示,即将钢锭锻造成能够包络覆盖住弧形锻件的宽板锻件,再通过机械加工方式加工至弧形锻件的尺寸形状。但该方法成形困难,锻件机械加工余量极大,材料利用率极低,且锻件纤维组织方向与弧形构件走向不一致,尤其是对于超大型弧形锻件特殊的形状和巨大的尺寸特点,其问题更为突出。
3.超大型扁截面弧形锻件特征如图1所示,该锻件特点是锻件弧形直径大于8000mm,截面宽度大于1600mm,截面宽高比大于3,弧度大于180
°
。
4.针对上述问题现有技术中也有相应改进,如公开日为2020-6-30,公开号为cn111346998a的中国专利申请公开了一种带圆柱体弧形锻件的制备方法。该方法包括:(1)锻造板坯:对铸锭镦粗、拔长,并锻造成板坯;(2)热轧钢坯:对板坯进行多道次轧制得到热轧扁长钢坯;(3)局部堆积镦粗:使用局部镦粗成形装置对扁长钢坯局部位置进行多道次局部堆积镦粗,经整形及机械加工制得带圆柱体扁长钢坯;(4)热推弯成形:使用热推弯成形设备对带圆柱体扁长钢坯进行分段式弯制成形,最终得到带圆柱体弧形锻件;(5)性能热处理:成形锻件经性能热处理满足产品性能要求。本发明可较高效实现大型带圆柱体弧形锻件的成形,减少加工余量,提高材料利用率,并得到一致性良好的晶粒及组织,保证了锻件的综合性能。该技术方案的核心技术关键在于热推弯成形。该技术需要进行连续弯制,这需要先通过中频感应加热线圈,快速地、在线地、连续地对成形区前的坯料加热至1000℃以上,即如说明书中[0083]所述,也即需要进行高温塑性成形,坯料需要在短时间内全截面加热到很高的温度,该方法对感应加热线圈的加热能力要求很高。对于空心件或截面尺寸较小的零件,该方法可行。但对于截面宽度大于1600mm的超大型锻件,所需的感应加热线圈功率极高,所需的中频感应加热线圈机器配套设备及其庞大复杂,同时热推弯成形区前可供感应线圈布置的空间有限,难以实现利用感应加热线圈快速地、在线地、连续地对成形区前的坯料加热至1000℃以上这一需求。因此,该技术方案对设备瞬时功率要求极高,所需配套设备复杂,同时不适用于超大型弧形锻件。
[0005]
又例如公开日为2020-12-1,公开号为cn112008025a的中国专利申请公开了一种大型弯刀板类锻件的自由锻成形工艺及模具,涉及锻造技术领域,包括步骤一,以长方坯为初始坯料,使用凸面型砧进行高温自由锻成形,得到截面为哑铃形的长条坯料;步骤二,将长条坯料沿中心线切割,得到两块两侧的厚度不同且平滑过渡的预制坯;步骤三,使用带有导流槽和两侧非对称挡板的自由锻终锻拔长模具将切开后的预制坯进行高温锻造拔长,使预制坯外侧区域的材料厚度减薄并沿送进方向伸长,迫使预制坯向内侧弯曲,从而成形得到大型弯刀板类锻件。通过以上所述自由锻工艺方法和模具,实现了大型弯刀板类锻件的锻造成形,能够提高锻件性能和材料利用率,降低设备载荷,改善锻件成形效果并提高生产效率。该技术方案存在两个问题,(1)其坯料上、下面均为斜面,特别是下侧斜面,使得坯料
无法稳定有效的支撑,在模具上无法稳定,受重力或设备压力时,易向某侧倾斜转动,使其在终锻成形过程中坯料发生扭曲,锻件的曲率一致性和平面度都难以控制保证;(2)其终锻成形上下模具的成形面为两个平面,成形模具与坯料接触时,只先与坯料高侧接触,且压下过程中坯料横向流动无阻挡,根据金属塑性成形的最小阻力定律,坯料会优先从坯料高侧向坯料低侧流动,在高低两侧坯料均与模具接触后,此时高低两侧坯料高度已近相同,才能有效的沿坯料轴向方向流动,但此时高低两侧坯料高度已近相同,坯料向内弯曲动力不足,而当坯料向内弯曲动力不足时,两侧的挡板非但不能帮助坯料弯曲成形,还会因为坯料流向与挡板流向不一致,挡住坯料,造成其在模具型腔内卡住。根据本公司对该工艺方案的研究,在该工艺方案下,坯料弯曲角度实际只能达到90
°
左右,远远无法满足弧度大于180
°
的需求,同时锻件纤维组织方向较为杂乱。
[0006]
因此,针对上述问题,有必要提出进一步地解决方案,以至少解决其中一个问题。
技术实现要素:
[0007]
为了解决相关的弧形锻件成形困难和纤维组织流向与其走向不一致的问题,本发明提供一种弧形锻件的差速锻造方法及成形模具。所述技术方案是:
[0008]
一种弧形锻件的差速锻造方法,采用梯形直坯进行锻造,所述梯形直坯的截面为直角梯形,包括:将所述梯形直坯放置于组合弹性模组和下平砧之间,逐步向前送进锻压,并重复送进锻压操作,以实现拔长并弯曲成形,其中,
[0009]
所述梯形直坯以其直角腰面贴合所述下平砧;
[0010]
所述组合弹性模组包括多个弹性模,多个所述弹性模沿所述梯形直坯的斜腰方向并列排布,多个所述弹性模对所述梯形直坯锻压时,同时接触所述梯形直坯。
[0011]
本发明的一个较佳实施例中,除位于所述梯形直坯最高侧的所述弹性模以外的所述弹性模包括弹性件和与所述弹性件连接的平砧,所述平砧用于与所述梯形直坯的斜腰面接触,且所述平砧位于所述弹性件的形变方向上。
[0012]
本发明的一个较佳实施例中,还采用支撑模,所述支撑模位于多个所述弹性模的上方,多个所述弹性模在所述支撑模的带动下锻压所述梯形直坯。
[0013]
本发明的一个较佳实施例中,所述支撑模包括顶面和分别位于所述顶面两侧的两侧面,多个所述弹性模位于两所述侧面之间,且由一所述侧面向另一所述侧面排布。
[0014]
本发明的一个较佳实施例中,所述支撑模和所述下平砧之间设置有上下导向组件。
[0015]
本发明的一个较佳实施例中,所述上下导向组件包括设置于所述支撑模上的导向柱和设置于所述下平砧对应位置的导向孔,所述导向柱的高度方向和所述导向孔的深度方向均与所述弹性模的锻压方向一致。
[0016]
本发明的一个较佳实施例中,多个所述弹性模的自然高度满足:
[0017][0018]
其中,p1、p2为梯形直坯的梯形截面上底与下底长度,n为弹性模的个数,tn为第n个弹性模的高度。
[0019]
本发明的一个较佳实施例中,n在3~8之间。
[0020]
本发明的一个较佳实施例中,多个所述弹性模与所述梯形直坯的接触面的纵向宽度s一致,向前送进时的每砧的进砧量m在之间。
[0021]
另一技术方案是:
[0022]
一种应用于以上任一所述的弧形锻件的差速锻造方法的成形模具,包括组合弹性模组,所述组合弹性模组包括多个弹性模,多个所述弹性模并列排布,且锻压时同时接触坯料。
[0023]
与现有技术相比,本发明的有益效果是:
[0024]
(1)本发明利用梯形直坯两侧金属流动速度差实现坯料弯曲,成形简单,同时通过使用组合弹性模组阻碍坯料拔长过程中金属的横向流动,使金属沿坯料轴向流动,确保坯料曲率半径。
[0025]
(2)本发明通过支撑模确保多个弹性模同步移动,进一步通过支撑模和下平砧之间设置的上下导向组件确保在组合弹性模组下压和回程上行的过程中,上下模具在锻压成形过程中始终有效的限制坯料横向流动,增强坯料轴向流动;同时,通过导向孔与导向柱的作用,确保工装始终在设计的轨道上运行,确保锻件截面形状。
附图说明
[0026]
图1为超大型扁截面弧形锻件结构示意图;
[0027]
图2为现有扁截面弧形锻件锻造方法示意图;
[0028]
图3为电渣锭拔长下料示意图,其中,t表示冒口端,b表示底部端;
[0029]
图4(a)为胎模结构示意图;
[0030]
图4(b)为胎模拔长制坯示意图;
[0031]
图4(c)为胎模拔长得到的梯形直坯的结构示意图;
[0032]
图5为本方法拔长示意图;
[0033]
图6为本方法弯曲成形示意图。
[0034]
具体地,10、梯形直坯;20、弧形锻件;
[0035]
100、弹性模;200、下平砧;300、支撑模;310、顶面;320、侧面。
具体实施方式
[0036]
参选以下本发明的优选实施方法的详述以及包括的实施例可更容易地理解本发明的内容。除非另有限定,本文使用的所有技术以及科学术语具有与本发明所属领域普通技术人员通常理解的相同的含义。当存在矛盾时,以本说明书中的定义为准。如本文所用术语“由
…
制备”与“包含”同义。本文中所用的术语“包含”、“包括”、“具有”、“含有”或其任何其它变形,意在覆盖非排它性的包括。例如,包含所列要素的组合物、步骤、方法、制品或装置不必仅限于那些要素,而是可以包括未明确列出的其它要素或此种组合物、步骤、方法、制品或装置所固有的要素。
[0037]
当量、浓度、或者其它值或参数以范围、优选范围、或一系列上限优选值和下限优选值限定的范围表示时,这应当被理解为具体公开了由任何范围上限或优选值与任何范围下限或优选值的任一配对所形成的所有范围,而不论该范围是否单独公开了。例如,当公开
了范围“1~5”时,所描述的范围应被解释为包括范围“1~4”、“1~3”、“1~2”、“1~2和4~5”、“1~3和5”等。当数值范围在本文中被描述时,除非另外说明,否则该范围意图包括其端值和在该范围内的所有整数和分数。
[0038]
单数形式包括复数讨论对象,除非上下文中另外清楚地指明。“任选的”或者“任意一种”是指其后描述的事项或事件可以发生或不发生,而且该描述包括事件发生的情形和事件不发生的情形。
[0039]
说明书和权利要求书中的近似用语用来修饰数量,表示本发明并不限定于该具体数量,还包括与该数量接近的可接受的而不会导致相关基本功能的改变的修正的部分。相应的,用“大约”、“约”等修饰一个数值,意为本发明不限于该精确数值。在某些例子中,近似用语可能对应于测量数值的仪器的精度。在本技术说明书和权利要求书中,范围限定可以组合和/或互换,如果没有另外说明这些范围包括其间所含有的所有子范围。
[0040]
此外,本发明要素或组分前的不定冠词“一种”和“一个”对要素或组分的数量要求(即出现次数)无限制性。因此“一个”或“一种”应被解读为包括一个或至少一个,并且单数形式的要素或组分也包括复数形式,除非所述数量明显旨指单数形式。
[0041]
实施例1:
[0042]
一种弧形锻件的差速锻造方法,采用如图4(c)所示的梯形直坯10进行锻造,梯形直坯10的截面为直角梯形。且本实施例中,成形锻件为超大型扁截面弧形锻件,其尺寸要求如图1所示。
[0043]
该梯形直坯10可以采用胎模拔长制取,具体地:
[0044]
s1下料:如图3所示,对电渣锭轻压滚圆,然后拔长锭身,冒口端逐压钳把,将钢锭拔成锭身高径比小于2的圆柱形毛坯。
[0045]
s2制坯:如图4(a)-4(c)所示,通过镦粗、拔长、胎模拔长成截面为直角梯形的梯形直坯10。且梯形直坯10的尺寸与最终成形的弧形锻件20的尺寸满足:
[0046][0047]
p1=(1.05~1.1)m
[0048]
p1、p2为梯形直坯的梯形截面上底与下底长度,q为梯形直坯厚度,l为梯形直坯长度;
[0049]
d1为弧形锻件外径,d2为弧形锻件内径,m为弧形锻件厚度,θ为弧形锻件弧度;
[0050]
γ为损耗值,是在锻造成形过程中,因加热氧化烧损,裂纹、折皮清理等原因造成的坯料损耗,γ通常在1%~4%左右,实际数值受现场生产过程影响会有所不同。
[0051]
再拔长梯形直坯10,利用梯形直坯10两侧金属流动速度差实现坯料弯曲,即梯形直坯10高侧金属拔长速度快,低侧金属流动速度慢,两侧金属流速不同,坯料拔长同时自然向坯料低侧弯曲。同时通过使用组合弹性模组阻碍坯料拔长过程中金属的横向流动,使金属沿坯料轴向流动,确保坯料曲率半径。具体地:如图5和图6所示,将梯形直坯10放置于组合弹性模组和下平砧200之间,逐步向前送进锻压,并重复送进锻压操作,以实现拔长并弯曲成形。
[0052]
如图5所示,梯形直坯10以其直角腰面贴合下平砧200,即梯形直坯10垂直放置于下平砧200上,使其保持稳定状态。同时,可以理解的是,向前送进为沿其长度方向向前送
进,从而将梯形直坯10锻造为弧形锻件20。
[0053]
组合弹性模组包括多个弹性模100,多个弹性模100沿梯形直坯10的斜腰方向并列排布,即多个弹性模100沿梯形直坯10的直角梯形截面的斜腰依次排列,也即多个弹性模100沿与梯形直坯10的长度方向垂直的方向依次排列。
[0054]
多个弹性模100对梯形直坯10锻压时,同时接触梯形直坯10。本实施例中,多个弹性模100的上端齐平,下端与梯形直坯10的斜腰相适配,即多个弹性模100的自然高度沿梯形直坯10的斜腰从低到高的方向依次递减,也即组合弹性模组的斜率与梯形直坯10的斜面斜率相同。弹性模100的自然高度指弹性模100在自由状态下的高度。
[0055]
优选地,多个弹性模100的自然高度满足:
[0056][0057]
其中,p1、p2为梯形直坯的梯形截面上底与下底长度,n为弹性模100的个数,tn为第n个弹性模100的高度。n在3~8之间,更为优选地n为5。
[0058]
除位于梯形直坯10最高侧的弹性模100以外的弹性模100包括弹性件和与弹性件连接的平砧,平砧用于与梯形直坯10的斜腰面接触,且平砧位于弹性件的形变方向上。以5个弹性模100的组合为例,组合弹性模组从梯形直坯10的高侧向低侧依次包括第一弹性模,其高度为t1;第二弹性模,其高度为t2;第三弹性模,其高度为t3;第四弹性模,其高度为t4;和,第五弹性模,其高度为t5,第二弹性模至第五弹性模采用弹性件和平砧连接而成,弹性件可采用弹簧或其他等同的弹性结构件,第一弹性模可同样采用弹性件和平砧连接而成,但由于梯形直坯10的最高侧形变量最大,且最终成形时,五个弹性模100的下端齐平,因此,第一弹性模优选其弹性为0,即采用刚性模,可直接采用平砧。可以理解的是,5个弹性模100中的弹性件长度不一。5个弹性模100可以采用工作面相同尺寸的平砧,工作面即与梯形直坯10的接触面。
[0059]
本实施例中,组合弹性模组由5块从左向右刚性逐渐增大的弹性模100组成,其中最右边第五块为刚性模,组合弹性模组在锻压梯形截面坯料时,组合弹性模组同时与梯形直坯10斜面不同位置发生接触挤压,使坯料不同区域同步变形,同时,弹性模100可以阻挡高侧金属向低侧金属横向流动,保证高侧金属沿轴向流动以保证两侧金属流动的速度差。弹性模100在下压过程中受到不断增大的金属抗力,直至左侧4个弹性模100最终压缩至与右侧刚性模高度齐平,使锻件截面为矩形,也即压至锻件厚度时,组合弹性模组被同时压缩至同一高度,使锻造后的坯料表面平整。
[0060]
为确保多个弹性模100同步移动,本方法还采用支撑模300,支撑模300位于多个弹性模100的上方,多个弹性模100在支撑模300的带动下锻压梯形直坯10。支撑模300包括顶面310和分别位于顶面310两侧的两侧面320,多个弹性模100位于两侧面320之间,且由一侧面320向另一侧面320排布,从而将弹性模100限制在顶面310和两侧面320形成的空间内。
[0061]
优选地,支撑模300和下平砧200之间设置有上下导向组件,从而确保在组合弹性模组下压和回程上行的过程中,上下模具在锻压成形过程中始终有效的限制坯料横向流动,增强坯料轴向流动,同时确保工装始终在设计的轨道上运行,确保锻件截面形状。具体地,上下导向组件可包括设置于支撑模300上的导向柱和设置于下平砧200对应位置的导向孔,导向柱的高度方向和导向孔的深度方向均与弹性模100的锻压方向一致。
[0062]
本方法中多个弹性模100与梯形直坯10的接触面的纵向宽度s一致,向前送进时的每砧的进砧量m在之间,从而使坯料塑性变形时更容易沿轴向流动。弹性模100的纵向宽度即其平行于坯料进料方向的侧面320宽度。
[0063]
本实施例中,弹性模100的的纵向宽度与支撑模300的纵向宽度一致,图6示出了支撑模300的纵向宽度为s,弹性模100位于支撑模300的正下方,且其纵向宽度同样为s。
[0064]
实施例2:
[0065]
一种成形模具,应用于实施例1中。该模具包括组合弹性模组,组合弹性模组包括多个弹性模100,多个弹性模100并列排布,且锻压时同时接触坯料。
[0066]
可设置为多个弹性模100的上端齐平,下端呈台阶状,且斜率与坯料锻压面斜率相同,即与梯形直坯10的斜面斜率相同。
[0067]
多个弹性模100的自然高度满足:
[0068][0069]
其中,p1、p2为梯形直坯的梯形截面上底与下底长度,n为弹性模100的个数,tn为第n个弹性模100的高度。n在3~8之间,更为优选地n为5。
[0070]
除位于坯料最高侧的弹性模100以外的弹性模100包括弹性件和与弹性件连接的平砧,平砧用于与坯料接触,且平砧位于弹性件的形变方向上。以5个弹性模100的组合为例,组合弹性模组从坯料的高侧向低侧依次包括第一弹性模,其高度为t1;第二弹性模,其高度为t2;第三弹性模,其高度为t3;第四弹性模,其高度为t4;和,第五弹性模,其高度为t5,第二弹性模至第五弹性模采用弹性件和平砧连接而成,弹性件可采用弹簧或其他等同的弹性结构件,第一弹性模可同样采用弹性件和平砧连接而成,但由于坯料的最高侧形变量最大,且最终成形时,五个弹性模100的下端齐平,因此,第一弹性模优选其弹性为0,即采用刚性模,可直接采用平砧。可以理解的是,5个弹性模100中的弹性件长度不一。5个弹性模100可以采用工作面相同尺寸的平砧,工作面即与坯料的接触面。
[0071]
本实施例中,组合弹性模组由5块从左向右刚性逐渐增大的弹性模100组成,其中最右边第五块为刚性模,组合弹性模组在锻压坯料时,组合弹性模组同时与坯料斜面不同位置发生接触挤压,使坯料不同区域同步变形,同时,弹性模100可以阻挡高侧金属向低侧金属横向流动,保证高侧金属沿轴向流动以保证两侧金属流动的速度差。弹性模100在下压过程中受到不断增大的金属抗力,直至左侧4个弹性模100最终压缩至与右侧刚性模高度齐平,使锻件截面为矩形,也即压至锻件厚度时,组合弹性模组被同时压缩至同一高度,使锻造后的坯料表面平整。
[0072]
为确保多个弹性模100同步移动,本模具还包括支撑模300,支撑模300位于多个弹性模100的上方,多个弹性模100在支撑模300的带动下锻压坯料。支撑模300包括顶面310和分别位于顶面310两侧的两侧面320,多个弹性模100位于两侧面320之间,且由一侧面320向另一侧面320排布,从而将弹性模100限制在顶面310和两侧面320形成的空间内。
[0073]
优选地,支撑模300和下平砧200之间设置有上下导向组件,从而确保在组合弹性模组下压和回程上行的过程中,上下模具在锻压成形过程中始终有效的限制坯料横向流动,增强坯料轴向流动,同时确保工装始终在设计的轨道上运行,确保锻件截面形状。具体
地,上下导向组件可包括设置于支撑模300上的导向柱和设置于下平砧200对应位置的导向孔,导向柱的高度方向和导向孔的深度方向均与弹性模100的锻压方向一致。
[0074]
综上所述,本发明利用梯形直坯两侧金属流动速度差实现坯料弯曲,同时通过使用组合弹性模组阻碍坯料拔长过程中金属的横向流动,使金属沿坯料轴向流动,确保坯料曲率半径。
[0075]
对于本领域技术人员而言,显然本发明不限于上述示范性实施例的细节,而且在不背离本发明的精神或基本特征的情况下,能够以其他的具体形式实现本发明。因此,无论从哪一点来看,均应将实施例看作是示范性的,而且是非限制性的,本发明的范围由所附权利要求而不是上述说明限定,因此旨在将落在权利要求的等同要件的含义和范围内的所有变化囊括在本发明内。
再多了解一些
本文用于创业者技术爱好者查询,仅供学习研究,如用于商业用途,请联系技术所有人。