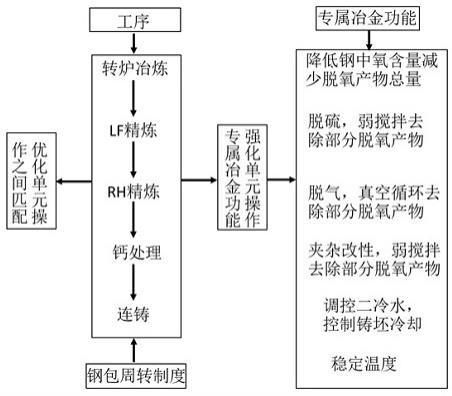
1.本发明属于炼钢技术领域,进一步是一种精冲钢板坯角部裂纹的综合控制方法。
背景技术:
2.精冲工艺是一种把精密冲裁和板料成型相结合的制造精密、复杂冲压件的高效而经济的加工技术,能够获得优质的零件,对钢材的化学成分、尺寸的精度、表面质量、加工性能都有严格的要求。在生产过程中,由于其碳及合金含量均高于传统热连轧企业生产的低碳低合金产品,连铸坯易产生角部横裂纹,进而引起热轧板卷边部产生翘皮缺陷,造成板卷直接判废。
3.铸坯产生角部裂纹具有普遍性特点,尤以微合金钢(含nb、v、ti、b)严重,国内外针对微合金钢的连铸角部裂纹控制进行了大量研究,而针对碳及合金含量较高的精冲钢研究较少。微合金钢角部裂纹控制措施主要集中在如下方面:(1)控制钢水成分。减少铸坯凝固过程组织晶界p、s等溶质的偏析;(2)精炼过程中采用控氮固氮工艺,从而减少连铸坯凝固过程碳氮化物析出,提高铸坯角部组织强度;(3)控制二冷弧形及矫直区配水,使铸坯在弯曲和矫直过程表面温度避开钢的第三脆性温度区间;(4)调整结晶器锥度、振动及冷却强度、保护渣物性参数等,缓冷铸坯初凝组织并减轻铸坯表面振痕,防止铸坯角部裂纹产生。
4.然而,实际精冲钢生产过程中,造成其角部裂纹的主要原因:(1)浇注时操作条件不稳定,导致钢中大颗粒的非金属夹杂物卷入,破坏了金属基体连续性,在弯曲过程中产生应力集中;(2)连铸坯进入弯曲段时,角部温度处于第三脆性区间,恶化了铸坯角部的高温热塑性;(3)铸坯出结晶器至进入弯曲段之前,冷却强度低,导致连铸坯角部晶界处网状先铁素体析出严重,恶化了铸坯高温塑性。因此,从根本上控制精冲钢生产的关键是控制钢液洁净度,稳定各单元操作工艺,保证浇铸条件的稳定;加强出结晶器至进入弯曲段之前的二冷配水,使连铸坯进入弯曲段时角部温度避开第三脆性区间,同时减少晶间网状析铁素体的析出。目前,钢铁企业在精冲钢生产过程尚无有效控制其连铸角部裂纹产生的工艺或方法。
技术实现要素:
5.为了解决上述问题,本发明的目的在于提供一种能够有效解决连铸角部裂纹产生的方法。
6.为了达到上述目的,本发明提供以下技术方案:一种精冲钢板坯角部裂纹的综合控制方法,包括以下步骤:步骤一:过程温降控制:δt
总
=δt1 δt2 δt3 δt4 δt5δt
总
钢水过程总温降;δt1出钢温降;δt2出钢后到钢水炉外精炼运输过程温降;δt3钢水在钢包处理过程的温降;δt4钢包运至中间包处过程温降;δt5钢水在中间包内温降。
7.控制转炉终点氧含量降低合金加入量,周转钢包≤6,红包出钢,出钢时间6-8min,δt1≤20℃;合理安排统筹生产计划,非处理时间全程加盖,每炉钢水等待时间≤5min,降温速率小于1℃/min,δt2≤10℃;lf处理过程钢水的升温速度控制在3-4℃/min,确认钢包蓄热状态(降温速率小于0.5℃/min),调整生产节凑,确保后续合适处理时间,rh处理温降控制即δt3≤25℃;开浇镇静时间控制在20min,δt4≤10℃;中间包烘烤时间不小于150分钟,并选用中间包低密度碳化稻壳保温剂覆盖钢水表面,确保浇注一炉钢水温度差δt5≤5℃。在lf炉补温条件下,控制从转炉出钢(钢包内钢水)到连铸浇注(中间包内钢水)过程总温降δt
总
≤70℃。
8.步骤二:转炉冶炼的控制:控制转炉终点的氧含量、碳含量和硫含量,降低出钢温度,通过全脱氧工艺出钢减少钢中一次脱氧产物,利用出钢对流混冲预造脱硫渣;步骤三:lf快速精炼:lf进站补加脱硫石灰,化渣后调整底吹并进行一次主加热升温,温度满足要求后,配加铝脱氧和强搅拌脱硫,脱硫完毕后合金化,软搅拌取出部分脱氧产物,最后出站;步骤四:rh循环脱气:rh进站后常规脱气循环处理,然后进行钙处理,软搅拌后充分上浮夹杂物并去除;步骤五:连铸二冷水控制:调整二冷比水量为0.89,增加足辊段、冷却区一至三区冷却水量,其余保持原水量。
9.步骤六:吹氩控制:调整塞棒、浸入式水口吹氩气流量为2-3l/min,中间包上水口与浸入式水口之间的氩封流量5l/min。
10.上述方案的进一步改进为:所述温降控制具体如下:通过控制转炉终点氧含量,降低合金加入量,控制δt1≤20℃;通过非处理时间全程加盖,每炉钢水等待时间≤5min,控制δt2≤10℃;通过控制lf处理过程钢水的升温速度在3-4℃/min与rh处理温降,控制δt3≤25℃;通过开浇镇静时间控制在20min,控制δt4≤10℃;中间包烘烤时间不小于150分钟,并选用中间包低密度碳化稻壳保温剂覆盖钢水表面,控制浇注一炉钢水温度差δt5≤5℃;在lf炉补温条件下,控制从转炉出钢到连铸浇注过程总温降δt
总
≤70℃。
11.上述方案的进一步改进为:所示步骤一中,控制周转包≤6,出钢时间6-8min,每炉钢水非正常等待时间≤5min,过程总温降≤70℃,保证浇铸过程过热度的稳定。
12.上述方案的进一步改进为:所述步骤二中,转炉终点碳含量范围控制在0.06
±
0.02%,出钢温度的范围控制在1610
±
5℃。降低出钢氧含量,减少脱氧产出生成。
13.上述方案的进一步改进为:所述步骤二中,出钢时加入铝锰钙,并预加入脱硫石灰和钢包渣改性剂。
14.上述方案的进一步改进为:所述步骤一、三、四中,延长rh出站到连铸开浇之间钢水镇静时间为20min,延长lf、rh弱搅拌时间为8min,使内生夹杂物上浮。
15.上述方案的进一步改进为:所述步骤四中,所述钙处理为复压喂入纯钙线,再软搅拌和软吹。
16.上述方案的进一步改进为:所述步骤五中,增加了连铸二次冷却区一至三区冷却水量,确保弯曲操作时,铸坯表面温度避开710-765℃脆性温度区间。
17.上述方案的进一步改进为:所述步骤六中,减少了塞棒、水口及氩封气体流量。
18.本发明的有益效果是:通过本发明可对全工序各操作单进行优化匹配,并充分发挥各冶炼单元的专属冶金功能,提高钢液洁净度、稳定浇注温度、结合具体钢种进行二冷水调整,有效消除了减少由于钢中非金属夹杂物、铸坯表面晶界网状先共析铁素体的析出,第三脆性区间引起的角部裂纹;通过改进转炉冶炼降低钢种氧含量;通过lf精炼、rh精炼和钙处理进一步的去除部分脱氧产物。
附图说明
19.图1是本发明实施例的流程示意图。
具体实施方式
20.实施例1如图1所示,本发明应用在精冲钢a生产实践,第一炉具体步骤如下:步骤一:过程温降控制:双联钢种采用5个周转包,且本钢种禁止使用提温包。红包出钢,出钢时间6min,δt1=20℃;非处理时间全程加盖,钢水等待时间1min,δt2=8℃;lf处理过程钢水的升温速度控制在3-4℃/min,rh处理温降控制,δt3=25℃;开浇镇静20min,δt4=10℃;中间包烘烤时间不小于150分钟,并选用中间包低密度碳化稻壳保温剂覆盖钢水表面,确保浇注一炉钢水温度差δt5=5℃。过程总温降δt
总
=68℃。
21.步骤二:转炉冶炼的控制:转炉出钢终点各成分控制在碳含量为0.05%、氧含量为500ppm、硫含量0.012%,出钢温度控制在1610℃;出钢加铝锰钙400kg、硅铁600kg、中碳铬铁4000kg、金属锰800kg和增碳剂500kg脱氧预合金化,脱硫石灰500kg、钢包渣改性剂1000kg利用出钢对流混冲预造精炼渣;步骤三:lf快速精炼:lf进站al含量0.006%、s含量0.007%,温度1580℃;加入600kg脱硫石灰350kg钢包渣改性剂,化渣加热10min升温至1610℃,然后配加70kg铝脱氧强搅拌脱硫,脱硫完毕后配加其他合金至钢种化学成分标准要求的下限,混匀后底吹氩气并使用软搅拌模式,软搅拌5-8min,出站;步骤三:rh循环脱气:rh进站硫含量为0.0018%,其他合金含量均配加至钢种化学成分标准要求的下限,温度1590℃;然后抽真空、补加合金至目标成分,在真空度达到0.27kpa时开始循环脱气12min,复压喂入355m大约80kg的纯钙线,软吹8min,出站,此时温度在1580℃。
22.步骤五:连铸二冷水控制:根据常规技术得知精冲钢种高温脆性区间为710-765℃;控制上台温度,保证钢水浇注参数稳定,调整二冷区比水量及水量分布,即调整二冷比水量为0.89,增加足辊段、冷却区一至三区冷却水量,通过增加结晶器足辊与弯曲段的冷却速率,使铸坯角部温度在弯曲段避开易产生裂纹缺陷的温度脆性区间,其余保持原水量。
23.步骤六:吹氩控制:调整塞棒、浸入式水口吹氩气流量为2-3l/min,中间包上水口与浸入式水口之间的氩封流量5l/min。
24.实施例2如图1所示,本发明应用在精冲钢a生产实践,第二炉具体步骤如下:双联钢种采用5个周转包,且本钢种禁止使用提温包。红包出钢,出钢时间8min,δt1=22℃;非处理时间全程加盖,钢水等待时间5min,δt2=10℃;lf处理过程钢水的升温速度控制在3-4℃/min,rh处理温降控制,δt3=20℃;开浇镇静20min,δt4=8℃;中间包烘烤时间不小于150分钟,并选用中间包低密度碳化稻壳保温剂覆盖钢水表面,确保浇注一炉钢水温度差δt5=6℃。过程总温降δt
总
=66℃。
25.步骤二:转炉冶炼的控制:转炉出钢终点各成分控制在碳含量0.069%、氧含量350ppm、硫含量0.016%,出钢温度控制在1600℃;出钢加铝锰钙400kg、硅铁600kg、中碳铬铁4000kg金属锰700kg和增碳剂440kg脱氧预合金化,脱硫石灰530kg、钢包渣改性剂1400kg利用出钢对流混冲预造精炼渣;步骤三:lf快速精炼:lf进站铝含量0.0018%、硫含量0.010%,温度1570℃;加入700kg脱硫石灰、600kg钢包渣改性剂,化渣加热15min升温至1610℃,配加25kg铝脱氧强搅拌脱硫,脱硫完毕配加其他合金至下限,混匀后底吹调至软搅拌模式,软搅拌5-8min,最后出站;步骤四:rh循环脱气:rh进站硫含量0.0019%,其他合金含量均在下限,温度控制在1590℃;抽真空、补加合金至目标成分,真空度达到0.27kpa时开始循环脱气12min,再复压喂入355m纯钙线(80kg),软吹8min,出站,此时温度1580℃;步骤五:连铸二冷水控制:根据常规技术得知精冲钢种高温脆性区间为710-765℃;控制上台温度,保证钢水浇注参数稳定,调整二冷区比水量及水量分布,即调整二冷比水量为0.89,增加足辊段、冷却区一至三区冷却水量,控制进入弯曲段时铸坯角部温度避开高温脆性区间,其余保持原水量。
26.步骤六:吹氩控制:调整塞棒、浸入式水口吹氩气流量为2-3l/min,中间包上水口与浸入式水口之间的氩封流量5l/min。
27.上述实施例中,精冲钢a生产2炉次,12块连铸坯均未发现角部裂纹,而对比流板坯裂纹率为6%。
28.上述实施例中,通过步骤一转炉冶炼的控制,降低了钢中氧含量并减少了脱氧产物总量,步骤二中lf精炼通过脱硫和弱搅拌减少了脱氧产物总量,步骤三中rh精炼和钙处理通过脱气和真空循环减少了脱氧产物总量,步骤四中连铸控制二冷水和铸坯冷却减少了脱氧产物总量。脱氧产物减少(即内生夹杂物减少),铸坯基体连续性提高,由于夹杂物导致的微裂纹源得到有效控制,铸坯角部裂纹的产生几率降低。
29.本发明不局限于上述实施例,凡采用等同替换形成的技术方案,均落在本发明的保护范围。
再多了解一些
本文用于创业者技术爱好者查询,仅供学习研究,如用于商业用途,请联系技术所有人。