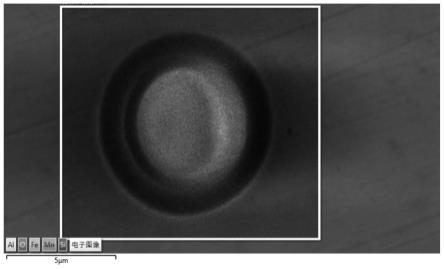
一种改善钢中条带型mns夹杂物的方法及其生产的钢板
技术领域
1.本发明属于高性能钢制备技术领域,具体涉及一种改善钢中条带型mns夹杂物的方法及其生产的钢板。
背景技术:
2.海工、桥梁、建筑用高性能钢在轧制过程中,钢中的硅酸盐和硫化物夹杂会发生变形并沿着轧制方向延伸成条状,这种条状的夹杂物破坏了钢材的整体连续性,降低了钢材的力学性能,会造成性能的各向异性,特别是使钢材横断面塑性大幅度下降。为此常规的冶炼工艺采取了深脱硫工艺,不断减少和控制钢中硫化物含量,进一步改善低合金钢的性能。
3.申请号为202111254550.2、专利名称为“一种控制中碳钢中硫化锰夹杂物在连铸板坯厚度方向上分布的连铸方法”的专利,公开了一种采用非常规的连铸方法,即低过热度 弱冷 凝固末端强冷模式,缩小mns尺寸在连铸板坯厚度方向上的差异,促使mns在连铸板坯厚度方向上分布的均匀化,降低mns夹杂物尺寸分布不均带来的危害,其主要是对连铸工序的过热度、二冷水模式进行专项配合,对中碳钢中硫化锰夹杂物进行改善。
4.申请号为201410715579.x、专利名称为“屈服345mpa级抗氢致裂纹容器用钢的冶炼方法”的专利,该专利对铝、氧夹杂物的控制的关键点在于:转炉炉后加铝强脱氧,使用大流量氩气底吹以促进脱氧反应,lf精炼促进夹杂物上浮,rh不再进行调铝,rh软吹促进夹杂物上浮,rh处理结束后采用静置的方法促进铝、氧夹杂物上浮。mns夹杂物控制的关键点在于:铁水预处理采用两次扒渣操作,lf深脱硫处理,rh精炼采用钙处理,以固定钢液中的游离状态硫元素。其获得的抗酸容器钢,其抗hic性能检验的clr、ctr和csr指标均为0。
5.综上,采用非常规的低过热度 弱冷 凝固末端强冷连铸模式,低过热度的要求对浇注顺行造成影响,复杂的二冷水控制模式也增加了连铸控制难度,难以对凝固末端进行精准定位,存在理论与现实难以结合等现实问题;采用铁水多次扒渣、转炉强脱氧、lf深脱硫工艺等常规手段固然可以降低钢中s含量,但会造成工艺成本增加、转炉炉衬侵蚀严重、钢中残存的硫化物仍以条带性mns形式存在。因此迫切需要开发一种能有效改善钢中条带型mns夹杂物的经济方法。
技术实现要素:
6.本发明的目的在于针对已经达到洁净钢控制水平(s含量在30-60ppm)的钢中仍存在影响纵横向性能的条带型mns夹杂物的现状,提供一种改善钢中条带型mns夹杂物的特殊合金处理方法。
7.本发明的另一目的在于提供利用改善钢中条带型mns夹杂物的特殊合金处理方法生产的钢板,钢板夹杂物数量显著降低,夹杂物尺寸大幅度降低,明显提升钢的韧塑性指标,且钢板表面抗锈效果好。
8.本发明解决其技术问题所采用的技术方案是:一种改善钢中条带型mns夹杂物的方法,包括以下步骤:
9.a)控制转炉冶炼时的底吹和炉况,保证出钢时自由氧的水平;
10.b)转炉出钢用硅铁进行脱氧,不得采用含al材料脱氧;
11.c)lf工序补充脱氧精炼3分钟以上,根据钢水中的氧含量水平确定脱硫工艺操作,s含量控制在30-60ppm时,根据目标成分加入al线;
12.d)rh工序真空度达到100pa后按3分钟的间隔时间顺序加入钛铁、特殊合金,最后连铸成合格钢坯。
13.进一步地,所述步骤a)中出钢时的自由氧范围在400-600ppm。
14.进一步地,所述步骤c)中脱硫工艺操作时机选择在钢水中的氧含量小于60ppm时。
15.进一步地,所述步骤c)中脱硫工艺采用在渣中加入少量al粉,氩气按静搅方式控制。
16.进一步地,所述步骤d)中特殊合金为稀土合金或锆镁合金,添加量为0.1-0.2kg/t钢。
17.一种利用改善钢中条带型mns夹杂物的方法生产的钢板,钢板的fatt韧脆转变温度达到-80℃,纵、横向低温冲击值差控制在50j以内;其夹杂物尺寸大小≤5um;钢板表面富含特殊合金的非晶态尖晶石型氧化铁厚度达15-50μm,钢板整体防锈蚀。
18.本发明具有以下有益效果:
19.本发明结合现行洁净钢生产工艺与装备条件,通过对冶炼全过程的氧含量控制、摒弃传统al脱氧的方式,转而采用si脱氧;精准确定脱硫工艺的时机,以此改变钢中氧化物类型和进一步降低钢中硫化物水平;且利用特殊合金对夹杂物变性、改质、细化的特性,使得条带型mns变性为球化、细化的特殊合金硫氧化物,从而减少对钢材纵、横各向性能的影响。
20.经本发明处理方法生产的钢板产品具备良好的韧塑性指标,尤其是表面抗锈效果好。因本发明将钢中条带型、带腐蚀化学活性的mns通过特殊合金化改质变性为球化、细化且均匀分布的硫氧化物,使得容易发生在条带型硫化物处的阳极反应因组织致密、孔隙少、电解液的通路少而不能进行,进而避免了不均匀腐蚀的产生,且钢板表面形成厚度为15-50μm的富含特殊合金的非晶态尖晶石型氧化铁,钢板抗锈蚀能力强;同时特殊合金的加入明显细化晶粒、改善了夹杂物等级,对钢材韧塑性的提高效果明显,满足钢材耐疲劳性能、冷热成型性能等功能性指标要求。
附图说明
21.图1是实施例1中制备的钢板检测的夹杂物细化程度图。
22.图2是实施例2中制备的钢板的表面抗锈蚀的feooh层显微形貌图。
具体实施方式
23.以下是本发明的具体实施例,对本发明的技术方案做进一步描述,但是本发明的保护范围并不限于这些实施例。凡是不背离本发明构思的改变或等同替代均包括在本发明的保护范围之内。
24.一种改善钢中条带型mns夹杂物的方法,包括以下步骤:
25.a)控制转炉冶炼时的底吹和炉况,保证出钢时自由氧范围在400-600ppm。
26.b)转炉出钢用硅铁进行脱氧,不得采用含al材料脱氧。
27.c)lf工序补充脱氧精炼3分钟以上,根据钢水中的氧含量水平确定脱硫工艺操作,s含量控制在30-60ppm时,根据目标成分加入al线;脱硫工艺操作时机选择在钢水中的氧含量小于60ppm时;脱硫工艺采用在渣中加入少量al粉,氩气按静搅方式控制。
28.d)rh工序真空度达到100pa后按3分钟的间隔时间顺序加入钛铁、特殊合金,最后连铸成合格钢坯;特殊合金为稀土合金或锆镁合金,添加量为0.1-0.2kg/t钢。
29.实施例1
30.一种改善钢中条带型mns夹杂物的特殊合金处理方法如下:
31.a)转炉冶炼时的底吹和炉况良好,出钢时自由氧为480ppm。
32.b)转炉出钢用硅铁、锰铁进行脱氧和合金化,不采用al脱氧。
33.c)在lf工序补充脱氧精炼4分钟后测得钢水中的氧含量为20ppm,采用在渣中加入al粉的方式开始进行钢水脱硫,氩气选择静搅模式,脱硫至s=0.004%后加入al线0.18kg/t。
34.d)经rh夹杂物去除和脱气处理,rh工序真空度达到100pa后开始计时,按3分钟的间隔时间顺序先后加入钛铁、锆镁合金,锆镁合金添加量按0.2kg/t钢计算。
35.最后连铸成合格钢坯。
36.所生产的30mm钢板的伸长率a达到32%,fatt韧脆转变温度达到-80℃,纵、横向低温冲击值差为35j;检测的夹杂物尺寸在0.1-5um,夹杂物细化程度如图1所示;钢板表面富含锆、镁的非晶态尖晶石型氧化铁厚度达22-36μm。
37.实施例2
38.一种改善钢中条带型mns夹杂物的特殊合金处理方法如下:
39.c)转炉冶炼时的底吹和炉况良好,出钢时自由氧为590ppm。
40.d)转炉出钢用硅铁、锰铁进行脱氧和合金化,不采用al脱氧。
41.c)在lf工序补充脱氧精炼5分钟后测得钢水中的氧含量为40ppm,采用在渣中加入al粉的方式开始进行钢水脱硫,氩气选择静搅模式,脱硫至s=0.005%后加入al线0.23kg/t。
42.d)经rh夹杂物去除和脱气处理,rh工序真空度达到100pa后开始计时,按3分钟的间隔时间顺序先后加入钛铁、稀土合金,稀土合金添加量按0.15kg/t钢计算,最后连铸成合格钢坯。
43.所生产的16mm钢板的伸长率a达到28%,fatt韧脆转变温度达到-80℃,纵、横向低温冲击值差为46j;检测的夹杂物尺寸在0.05-3um;钢板表面富含稀土的非晶态尖晶石型氧化铁厚度达15-28μm,钢板的表面抗锈蚀的feooh层显微形貌如图2所示。
44.本发明不局限于上述实施方式,任何人应得知在本发明的启示下作出的结构变化,凡是与本发明具有相同或相近的技术方案,均落入本发明的保护范围之内。
45.本发明未详细描述的技术、形状、构造部分均为公知技术。
再多了解一些
本文用于创业者技术爱好者查询,仅供学习研究,如用于商业用途,请联系技术所有人。