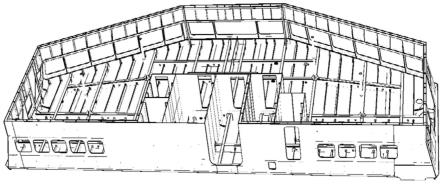
1.本发明属于船舶建造技术领域,具体涉及一种舰船全宽型钢制上层建筑分段建造方法。
背景技术:
2.船舶建造过程中,上层建筑中薄壁板结构应用广泛,上层建筑的制作质量直接影响船舶的使用功能和观感感受。薄壁板结构切割下料的精度、结构装配精度以及焊接热输出的控制将影响整个上层建筑的制作质量,因此,薄板结构的制作精度和焊接热量是工艺控制的关键。
技术实现要素:
3.针对现有技术中存在的问题,本发明提供一种船舶全宽型钢制上层建筑分段建造方法,本发明能够提高上层建筑的制作质量,加快分段的建造速度,缩短建造周期。
4.为实现上述目的,本发明采用以下技术方案:
5.本发明提供一种船舶全宽型钢制上层建筑分段建造方法,包括以下步骤:
6.步骤一、胎架原料检测;
7.步骤二、胎架制造;依照胎架图纸,制作胎架;
8.步骤三、甲板板与外板板分别进行铺板焊接;按照图纸顺序吊装铺板,清理焊缝,焊前标注焊接顺序;
9.步骤四、在甲板板上划甲板构架装配线,在外板板上划外板构架装配线,根据肋距、纵骨间距及加放的焊接收缩补偿值划线,并标注构架理论线方向;
10.步骤五、外板构架及甲板构架焊接,得到外板与甲板;外板构架焊接时从中间向两侧焊接,先对接焊,后角接焊,最后进行平角焊;
11.步骤六、舷部小分段定位安装;
12.步骤七、分段内轻围壁安装;
13.步骤八、将外板、甲板、轻围壁在分段内进行焊定位接;
14.步骤九、对分段段进行翻身前加强;
15.步骤十、翻身后电焊;外板与甲板的铰接焊缝焊接,焊接后对外板企口的焊接变形进行火工矫正,甲板对接缝碳刨清根后采用埋弧自动焊封底。
16.作为优选的技术方案,所述步骤二具体如下:胎架制造时用白油漆标注胎架中心线、肋骨检验线、肋位号,甲板胎架胎板间距为300mm,胎板划线采用钢针,线宽小于0.5mm,激光配合划出胎架高度和水平线,胎架抛势依木制胎架抛势样板划线并切割打磨光顺,胎架立柱与拉条搭接满焊,胎板与拉条搭接50mm间断焊。
17.作为优选的技术方案,所述步骤三具体如下:将拼接好的甲板板从胎架中心处向两舷铺板,从中间向两侧定位、安装,胎架下方用弓型马进行拉紧密贴固定,弓型马间距为300mm,甲板板铺板时的横向板缝距肋骨检验线的距离与设计值的偏差小于3mm,铺板定位
焊间距为200mm~300mm,定位焊长度为30~50mm,甲板板焊接方法采用双面埋弧自动焊;外板板从胎架中心处向两边铺板,铺板定位焊间距为200mm~300mm,定位焊长度为30mm。
18.作为优选的技术方案,所述步骤四具体为:甲板构架与甲板板之间的间隙控制小于1mm,外板构架与外板板之间的间隙控制小于1mm,纵、横构架之间的间隙控制在2mm之内。
19.作为优选的技术方案,所述步骤五具体为:外板构架与外板板的角焊缝采用二氧化碳保护焊,焊接时在相应位置根据图纸要求标明焊脚高度,按照工艺要求标注焊接顺序,角焊缝长度大于1500mm时,采用分钟逐步退焊发,每段退焊长度为1000mm,对称施焊;甲板构架与外板板焊接时从中间向两侧焊接,先对接焊,后角接焊,最后平角焊,甲板纵谷、甲板横梁与外板板的角接缝采用二氧化碳保护焊,角焊缝长度大于1500mm时,采用分中逐步退焊法,每段退焊长度为1000mm,对称施焊。
20.作为优选的技术方案,所述步骤六中,舷部小分段定位时半宽按理论型值加放5mm,定位时,肋位线、中心线、水平线控制在3mm以内。
21.作为优选的技术方案,所述步骤八中,外板与甲板的焊接采用手工电弧焊,焊接电流为90~100a,分段施工中安装2mm、3mm轻围壁时,只焊围壁与甲板的角焊缝,围壁立对接缝在分段内不得焊接。
22.作为优选的技术方案,所述步骤九中,按照分段加强图要求,对分段进行加强,加强结构烧焊在甲板构架或外板构架上,外板光面距下口100mm加槽钢加强。
23.作为优选的技术方案,所述步骤十中,分段翻身后对甲板面及外板的马脚用碳刨留根1~2mm后再用细砂轮进行打磨光顺,外板与甲板的角接缝焊接,焊后对外板企口的焊接变形进行火工矫正,甲板对接缝碳刨清根后采用埋弧自动焊封底。
24.与现有技术相比,本发明基于以下技术效果:本发明规范了舰船全宽型钢制上层建筑分段建造流程,提高了分段的建造速度,缩短了建造周期,减少了因施工不规范造成的返工,确保舰船全宽型钢制上层建筑符合要求。
附图说明
25.为了更清楚地说明本发明实施例或现有技术中的技术方案,下面将对实施例或现有技术描述中所需要使用的附图作简单地介绍,显而易见地,下面描述中的附图仅仅是本发明的一些实施例,对于本领域普通技术人员来讲,在不付出创造性劳动的前提下,还可以根据这些附图获得其他的附图。
26.图1为本发明钢制上层建筑分段的结构示意图。
27.图2为本发明胎架的结构示意图。
28.图3为本发明舷部分段的结构示意图。
29.图4为本发明外板与甲板的装配示意图。
30.图5为本发明分段内轻围壁的安装结构示意图之一。
31.图6为本发明分段内轻围壁的安装结构示意图之二。
32.图7为本发明外板、甲板、轻围壁的焊接示意图。
33.图8为本发明分段翻身前加强结构示意图。
34.其中,附图标记具体说明如下:胎板1、拉条2、肋骨检验线3、胎架中心线4、
具体实施方式
35.在本发明的描述中,需要理解的是,术语“纵向”、“横向”、“上”、“下”、“前”、“后”、“左”、“右”、“竖直”、“水平”、“顶”、“底”“内”、“外”等指示的方位或位置关系为基于附图所示的方位或位置关系,仅是为了便于描述本发明和简化描述,而不是指示或暗示所指的装置或元件必须具有特定的方位、以特定的方位构造和操作,因此不能理解为对本发明的限制。
36.本实施例提供一种舰船全宽型钢制上层建筑分段建造方法,该方法包括以下步骤:
37.步骤一、原材料检查验收。钢材到场检查验收,按规定的检验程序,严格落实抽检频率和抽检量。一般材料抽样复验,关重件逐件检验,落实好不合格产品的处置措施。围壁板及型材原材料观感良好,无麻点凹坑,材质及板厚符合设计要求,下料精度符合使用要求,对因多道加工工序造成的变形,型材零件和板材零件应进行撑直和校平,达到要求后方能转入下道工序。
38.步骤二、胎架制造。胎架制造时用白油漆标注胎架中心线4、肋骨检验线3、肋位号。甲板胎架胎板1间距为300mm,胎板1纵、横向必须注意直线度,胎板1划线必须用钢针,线宽小于0.5mm,激光配合划出胎架高度和水平线,胎架抛势依木制胎架抛势样板划线并切割打磨光顺,见图1。胎架立柱与拉条2搭接满焊,胎板1与拉条2搭接50mm间断焊。木制胎架样板用完后立即归还至样板仓库,以便后续分段使用。
39.步骤三、铺板焊接。将拼接好的甲板板从胎架中心处向两舷铺板,从中间向两侧定位、安装,胎架下方用弓型马进行拉紧密贴固定,弓型马间距为300mm。甲板板铺板时的横向板缝距肋骨检验线3的距离偏差小于3mm。铺板定位焊间距为200mm~300mm,定位焊长度为30~50mm。焊接前板缝两端安装标准的引熄弧板(t*100*100),t=拼板中较薄板的板厚,引熄弧板必须由加工车间提供,引熄弧板坡口应与母材一致。焊接前将甲板面清扫干净,清除焊道两侧各30mm范围内氧化皮、铁锈、水分、油污、铁渣等。甲板板焊接方法采用双面埋弧自动焊。铺板前检查是否有麻点,如发现麻点视严重程度而定,较严重的应更换外板零件,轻度麻点则可使用砂轮机打磨抛光,并测量打磨后外板厚度,保证大于理论厚度。将外板板从胎架中心处向两边铺板,外板纵向、横向板缝与胎架误差严格控制在3mm以内。铺板定位焊间距为200mm~300mm,定位焊长度为30mm。焊接前板缝两端安装标准的引熄弧板(t*100*100),t=拼板中较薄板的板厚。焊接前将甲板面清扫干净,清除焊道两侧各30mm范围内氧化皮、铁锈、水分、油污、铁渣等,焊前标注焊接顺序。外板板焊接方法采用双面埋弧自动焊,确保外观质量。
40.步骤四、甲板构架与外板划线装配。根据肋距、纵骨间距及加放的焊接收缩补偿值划线,并标注构架理论线方向。划线时要保持线的粗细均匀,线宽小于1mm。根据甲板和外板的划线图及划线型值从中间向两侧划,分段阶段开口必须按图纸要求划出,构架定位时要看清构架的理论线位置,纵骨的点焊点在构架非理论线面一侧。构架与甲板(外板)之间的间隙控制小于1mm,纵、横构架之间的间隙应控制在2mm之内。构架定位焊要求见下表1。
41.表1构架定位焊要求
[0042][0043]
为保证强构架的安装角度,强构架安装定位后要进行加强。需要拼接的球扁钢必须在平台上拼接并打磨光顺后再安装,拼接时要安装引熄弧板。安装顺序遵循由中间向两边安装的原则,以减少内应力。对狭小封闭的区域内(如风道等),必须随装随焊,提交合格后,再进行下道工序。
[0044]
步骤五、外板构架及甲板构架焊接。外板构架焊接人数每只分段控制在2人以内,焊接时应从中间向两侧焊接,遵循先对接焊,后角接焊,最后平角焊的原则。焊前要做好除锈、清渣工作,焊接过程中要控制电流、电压和焊丝焊条的直径,焊脚高度。外板构架与外板的角接缝采用co2焊接,焊接时在相应位置根据图纸要求标明焊脚高度,按工艺要求标注焊接顺序。角焊缝长度大于1500mm时,需采用分中逐步退焊法,每段退焊长度约为1000mm,对称施焊。甲板构架焊接人数控制在8人以内,焊接时应从中间向两侧焊接,遵循先对接焊,后角接焊,最后平角焊的原则。甲板纵骨、甲板横梁与外板的角接缝采用co2焊接。甲板区域与舷部小分段区域接口处500mm暂不施焊,等舷部分段安装结束后一起施焊。角焊缝长度大于1500mm时,需采用分中逐步退焊法,每段退焊长度约为1000mm,对称施焊。
[0045]
步骤六、舷部小分段定位安装。舷部小分段定位时半宽按理论型值加放5mm,定位时,肋位线、中心线、水平线控制在3mm以内,确保立体分段精度,见图二。舷部小分段定位加强应安装在构架上且应避开安装轻围壁的肋位,原则上每档肋位须加强见图2。舷侧分段与甲板企口处节点如果为熔透焊的,甲板与外板相接的坡口用自动割刀切割并打磨光顺,坡口形式见图3,舷侧分段安装,施焊,待分段翻身后再清根施焊。
[0046]
步骤七、分段内轻围壁安装。轻围壁安装修割余量必须弹线,打磨后安装后续部件,割刀必须用0号头子。安装轻围壁加强必须安装在构架面,安装时不允许使用火工。纵横轻围壁的丁字接缝的间隙小于2mm,反面用角铁进行加强,对于局部间隙偏大处,采用co2焊密集点焊修补,然后用砂轮磨平,见图4。装配的过程中不得采用强力装配。板缝拼接时有不齐的不得使用割刀切割,要用砂轮进行打磨。轻围壁在分段装焊时不得在钢板光面上装马板,如有需要装马板的必须装在球扁钢上。重点控制主通道轻围壁安装,确保其平整度。
[0047]
步骤八、外板与甲板、轻围壁在分段内焊接。外板与甲板的焊接采用手工电弧焊,焊接电流为90~100a。分段施工中安装2mm、3mm轻围壁时,只焊围壁与甲板的角焊缝,围壁立对接缝在分段内不得焊接,留待船台船坞总组后再焊。为保证棚脚平直,先行割除靠近棚脚200mm范围内余量(其他余量待船台总组后割除,切割采用等离子切割),并对该段密集点焊,然后焊接围壁与甲板角焊缝,如图5所示。
[0048]
轻围壁在分段上焊接尽量采用自动焊,以减少变形,保证成型美观,分段内平角焊每焊段长度200~300mm,主通道光面对接缝采用自动焊盖面。
[0049]
步骤九、翻身前加强。按照分段加强图要求,对分段进行加强,加强必须烧焊在构架上。安装翻身吊环并对企口进行加强。外板光面距下口100mm加槽钢加强。分段翻身前必须对加强、吊环等仔细检查,确保安全和质量。胎架预埋的分段首中尾三档抛势加强随分段一起翻身,以保证甲板抛势,见图6。
[0050]
步骤十、翻身电焊。分段翻身后对甲板面及外板的马脚用碳刨留根1~2mm后再用细砂轮进行打磨光顺。外板与甲板的角接缝焊接(如该处熔透还需清根后焊接),焊后对外板企口的焊接变形进行火工矫正,甲板对接缝碳刨清根后采用埋弧自动焊封底。
[0051]
尽管上述实施例已对本发明作出具体描述,但是对于本领域的普通技术人员来说,应该理解为可以在不脱离本发明的精神以及范围之内基于本发明公开的内容进行修改或改进,这些修改和改进都在本发明的精神以及范围之内。
再多了解一些
本文用于创业者技术爱好者查询,仅供学习研究,如用于商业用途,请联系技术所有人。