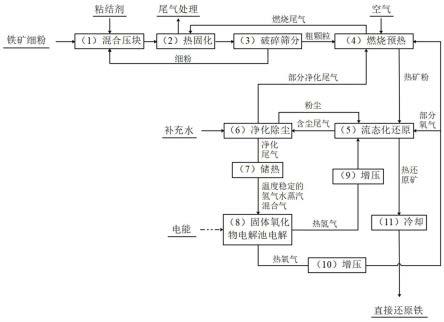
1.本发明属于化工、冶金领域,特别涉及一种铁矿细粉氢能高效流态化还原的方法。
背景技术:
2.作为一种典型的气基直接还原反应器,与竖炉相比,流化床省去了球团矿制备环节,可以直接处理粉矿,具有气固相间传质传热效率高、还原速率快等优点,是一种很有发展前途的铁矿冶炼技术。比较典型的流态化直接还原炼铁工艺有fior工艺、finmet工艺和circored工艺等。
3.1973年mckee公司基于fior法在委内瑞拉设计了一套年产40万吨的流态化直接还原炼铁工厂,并于1976年建成,1998年实际年产量达39万吨。fior工艺中,粒度小于5mm的铁矿粉依次经过4个流化床反应器,一级流化床将矿粉预热至760℃,二至四级流化床反应器的还原温度为690-780℃,压力为1.11mpa。还原后铁矿粉的金属化率达92%,可热压成块(us5082251)。流化还原气由天然气水蒸汽重整得到,h2含量超过90%,与净化循环气混合进入四级流化床反应器,继而三级和二级,床内呈气固逆流状态。fior工艺中铁矿粉还原时需添加适量的非粘惰性粉体如cao、mgo等来防止失流。20世纪90年代末期,fior委内瑞拉公司联合奥钢联(vai)通过改进fior法开发了finmet工艺,已在澳大利亚和委内瑞拉建厂。在finmet工艺中,粒度小于12.7mm的铁矿粉依次经过4个串联的流化床反应器,与流化还原气逆向流动。一级流化床反应器的温度约为550℃,向下逐渐升高,四级流化床反应器的温度约为800℃,压力为1.1-1.4mpa。四级流化床出口产品的金属化率达93%,含c约0.5-3%。还原铁粉送至热压机,热压成块,密度大于5g/cm3,较为致密,可减少产品氧化(us5833734)。finmet工艺所用流化还原气由天然气水蒸汽重整后得到的新鲜气和循环气组成,进入四级反应器前需加热至850℃。为了避免发生粘结失流,finmet工艺所用原料主要为不易粘结的粗矿粉,细矿粉(粒度小于0.1mm)含量必须控制在20%以内,否则就需要加入cao、mgo等惰性粉体。德国奥图泰公司(outotec,原lurgi metallurgie,鲁奇冶金公司)基于铁矿粉气基快速直接还原技术开发了circored工艺(us5527379,us5603748)。circored还原系统由一级循环流化床(cfb)和二级鼓泡流化床(fb)组成。生产能力为50万吨/年的工厂所用cfb反应器外径为5.2m,高为29.6m,外循环旋风器外径为5.5m,fb反应器外径为7.0m,总长为17.5m,内部有四个料室。流化还原气为纯h2。一级快速流化床的还原温度为630-650℃,二级鼓泡流化床的还原温度约为680℃,压力为0.4mpa。所得还原铁粉可以热压成块或者直接用于粉末冶金。为了避免铁矿粉流化还原过程中发生粘结失流,circored工艺中的还原温度均控制在680℃以下,并且选取1mm左右的不易粘结铁矿粉作为原料。
4.此外,许多中国专利也提出了流态化直接还原炼铁工艺,如cn103667571b、cn103725819b、cn106319126b、cn106467930b等。对于铁矿气基直接还原这一典型的气-固非催化反应,其动力学过程可以采用未反应核模型(缩核模型)描述,由缩合模型中不同控制步骤(外扩散、内扩散和界面化学反应)下颗粒完全转化时间与粒径的关系可知,颗粒越小,所需的完全转化时间越短,即还原反应速率越快。由气固流态化基础理论可知,颗粒的
起始流化速度与粒径的平方成正比,即颗粒越小,维持流化状态所需的气量越少。因此,理论上原料矿粉越细对流态化直接还原越有利,然而现有上述流态化直接还原炼铁工艺仅适合处理不易粘结的粗矿粉,或需要添加惰性物质抑制细矿粉失流,这些会对流态化还原效率产生较大影响,不能充分发挥流态化高效还原的优势。这主要是因为细矿粉(小于0.1mm)在高温(600℃以上)流态化还原过程中极易发生粘结,形成粒径较大的聚团并沉积在流化床底部,最终会导致整个床层的失流。一旦发生失流,还原系统将不得不中止,这会给生产造成极大的损失(komatina m,gudenau h w.metalurgija,2004,10(204):309-328)。
5.另外,现有流态化炼铁工艺均直接或间接依赖于化石燃料,如煤或天然气燃烧提供热量、煤气化或天然气重整提供还原性气体(h2、co)等,化石燃料的参与必然会导致流态化炼铁排放大量co2,加剧温室效应。为此,冶金学者开始探索利用清洁能源炼铁。1999年北京第125次香山科学会议上,徐匡迪院士首次提出了铁矿氢还原工艺设想,2002年中国国家自然科学基金委在上海大学举办的冶金战略论坛上,徐匡迪院士再次提出了氢冶金的技术思想。氢能是世界上最干净的能源,具有燃烧热值高和来源丰富等优点,除化石燃料外,氢气可以由水电解大规模制备。氢能在炼铁工业中用作燃料的燃烧产物和还原剂的还原产物只有水,是未来炼铁工业可持续发展的重要方向。
6.电解水制氢是一种成熟的工业制造氢气的技术,通过电能供给能量,使得电解槽内水分子在电极上发生电化学反应,分解成氢气和氧气。水分解反应主要包括:阴极析氢(hydrogen evolution reaction,her)和阳极析氧(oxygen evolution reaction,oer)两个半反应。目前,根据电解质的不同,电解水制氢技术可分为三类,分别是碱性电解水制氢(alkaline water electrolysis,awe)、质子交换膜电解水制氢(proton exchange membranes,pem)、固体氧化物电解水制氢(solid oxide electrolytic cells,soec)。其中,碱性电解水技术最为成熟,广泛应用于储能、冶金、制药和食品等行业。碱性电解水制氢系统结构较为简单,无需使用贵金属催化剂,具有技术安全可靠、制造成本低、操作简单、运行寿命长等优点,然而碱性电解水技术存在电解效率低、能耗高等问题。此外,碱性电解水技术在室温下工作,与高温气基直接还原炼铁的工艺匹配性较差,室温碱性电解水-高温还原炼铁系统热损耗较高,过程能效较低。质子交换膜电解技术具有反应无污染、装置结构紧凑、转化效率高等优点,但其质子交换膜和铂电极催化成本较高,导致其尚未实现大规模应用。固体氧化物电解技术具有高效、简单、灵活和环境友好等优势,因其工作温度高达600-1000℃,高温操作降低了水的理论分解电压,即有效降低了反应过电势,降低了能耗,使其电解制氢效率接近100%,然而高温操作尤其是温度波动,对固体氧化物电解池材料(包括电解质、阴极和阳极)的热稳定性、化学稳定性和耐久性影响较大,严重限制了其发展应用。
7.综上所述,通过工艺和技术创新,改善小于0.1mm铁矿细粉的高温还原流化质量,提高还原效率,同时利用电解水高效制氢,以氢为还原剂和燃料进行流态化直接还原炼铁,增强制氢系统与还原系统的工艺匹配性,提升过程能效和稳定性,提高能量利用率,是实现我国铁矿资源高效利用和高能效零碳炼铁的重要途径。
技术实现要素:
8.针对现有技术存在的问题,本发明的目的在于提供一种铁矿细粉氢能高效流态化还原的方法。所述方法能够实现铁矿细粉的高效利用和炼铁过程的零碳排放,原料适应性
广,环境友好,资源利用率、能量利用率和反应效率高,具有良好的经济效益和社会效益。
9.为达此目的,本发明采用以下技术方案:
10.一种铁矿细粉氢能高效流态化还原的方法,所述方法包括混合压块工序1、热固化工序2、破碎筛分工序3、燃烧预热工序4、流态化还原工序5、净化除尘工序6、储热工序7、固体氧化物电解池电解工序8、氢气增压工序9、氧气增压工序10及冷却工序11,具体包括以下步骤:
11.1)在混合压块工序1中,铁矿细粉和/或来自破碎筛分工序3的细粉配加粘结剂经研磨混合均匀,压制成块;
12.2)在热固化工序2中,压制块料经来自燃烧预热工序4的燃烧尾气加热,得到固化料;
13.3)在破碎筛分工序3中,固化料经破碎筛分得到符合高温流态化还原要求的粗颗粒矿粉,余下的细粉返回混合压块工序1循环利用;
14.4)在燃烧预热工序4中,通入空气与来自氧气增压工序10的热氧气一起将来自净化除尘工序6的部分净化尾气充分燃烧,预热粗颗粒矿粉,得到热矿粉和燃烧尾气,燃烧尾气送热固化工序2;
15.5)在流态化还原工序5中,热矿粉经来自氢气增压工序9的热氢气还原,同时通入来自氧气增压工序10的部分热氧气补热,得到热还原矿和含尘尾气;
16.6)在净化除尘工序6中,含尘尾气经净化除尘并补充水,得到净化尾气,部分净化尾气送燃烧预热工序4,其余净化尾气送储热工序7;
17.7)在固体氧化物电解池电解工序8中,来自储热工序7的温度稳定的氢气水蒸汽混合气在电能作用下经固体氧化物电解池电解,得到热氢气和热氧气,热氢气送氢气增压工序9,热氧气送氧气增压工序10;
18.8)在冷却工序11中,来自流态化还原工序5的热还原矿经冷却,得到直接还原铁。
19.所述铁矿细粉为铁精矿细粉,铁矿细粉的粒径小于0.1mm。
20.所述混合压块工序1中,细矿粉与粘结剂的混合方法为研磨混合。混合料通过压制成形,其中压力为0.2-20mpa。所述粘结剂是指水玻璃、膨润土、水泥、石灰中的一种或几种。所述粘结剂添加质量为细矿粉质量的0.5-10%。
21.所述热固化工序2中,固化温度为20-300℃,固化时间为1-10h。
22.所述破碎筛分工序3中,控制粗矿粉筛分粒径在0.1-5mm之间。
23.所述流态化还原工序5中,还原温度为600-900℃,还原时间为0.5-2h,还原压力为0.1-1mpa。
24.所述储热工序7中,储热技术为相变储热,储热材料为熔盐类、金属合金类中的一种或两种组合。
25.所述固体氧化物电解池电解工序8中,固体氧化物电解池的电解质材料为y2o3稳定的zro2基电解质,固体氧化物电解池的阴极材料为ni掺杂的y2o3稳定的zro2金属陶瓷,固体氧化物电解池的阳极材料为钙钛矿型氧化物基材料,电解温度为600-900℃。
26.优选的,所述固体氧化物电解池的电解质材料为8mol%的y2o3稳定的zro2。
27.优选的,所述固体氧化物电解池的阳极材料为la
0.8
sr
0.2
mno
3-x-ysz(y2o3稳定的zro2)、la
0.8
sr
0.2
feo
3-x-ysz(y2o3稳定的zro2)、la
0.8
sr
0.2
coo
3-x-ysz(y2o3稳定的zro2)、
la
0.6
sr
0.4
co
0.2
fe
0.8o3-x-ysz中的一种。
28.所述氢气增压工序9中,热氢气出口压力为0.11-1.1mpa。
29.所述氧气增压工序10中,热氧气出口压力为0.11-1.1mpa。
30.所述冷却工序11中,直接还原铁的金属化率不低于92%。
31.相对于现有技术,本发明具有如下突出的优点:
32.(1)本发明通过将小于0.1mm铁矿细粉配加粘结剂造粒得到0.1-5mm的粗颗粒用于高温流态化还原,显著改善了其高温还原流化质量,有效抑制了失流,实现了小于0.1mm铁矿细粉的高效还原;
33.(2)本发明通过将铁矿粉流态化还原与固体氧化物电解池制氢耦合,电解产生的高温氢气既作为还原剂炼铁,又作为燃料供热,同时还原产生的高温水蒸汽循环用于固体氧化物电解池电解制氢,增强了电解制氢系统与流态化还原炼铁系统的工艺匹配性,提高了整个过程的能效,从而实现了铁矿细粉氢能高效流态化还原;
34.(3)本发明通过还原尾气燃烧预热,燃烧尾气为热固化工序提供热量,提高了气体利用率和系统能量利用率。
35.(4)本发明通过高温储热技术稳定氢气水蒸汽混合气温度,提高了固体氧化物电解池使用寿命。
附图说明
36.图1为本发明的一种铁矿细粉氢能高效流态化还原的方法的流程图;
37.图2为小于0.1mm的铁矿细粉与实施例2所述方法的改性料在高温流态化还原中金属化率随时间的变化规律;
38.图3为小于0.1mm的铁矿细粉与实施例3所述方法的改性料在高温流态化还原中金属化率随时间的变化规律。
具体实施方式
39.下面以附图和具体实施方式对本发明作进一步详细的说明。
40.实施例1
41.如图1所示,一种铁矿细粉氢能高效流态化还原的方法,所述方法包括混合压块工序1、热固化工序2、破碎筛分工序3、燃烧预热工序4、流态化还原工序5、净化除尘工序6、储热工序7、固体氧化物电解池电解工序8、氢气增压工序9、氧气增压工序10及冷却工序11,具体包括以下步骤:
42.1)在混合压块工序1中,铁矿细粉和/或来自破碎筛分工序3的细粉配加粘结剂经研磨混合均匀,压制成块;
43.2)在热固化工序2中,压制块料经来自燃烧预热工序4的燃烧尾气加热,得到固化料;
44.3)在破碎筛分工序3中,固化料经破碎筛分得到符合高温流态化还原要求的粗颗粒矿粉,余下的细粉返回混合压块工序1循环利用;
45.4)在燃烧预热工序4中,通入空气与来自氧气增压工序10的热氧气一起将来自净化除尘工序6的部分净化尾气充分燃烧,预热粗颗粒矿粉,得到热矿粉和燃烧尾气,燃烧尾
气送热固化工序2;
46.5)在流态化还原工序5中,热矿粉经来自氢气增压工序9的热氢气还原,同时通入来自氧气增压工序10的部分热氧气补热,得到热还原矿和含尘尾气;
47.6)在净化除尘工序6中,含尘尾气经净化除尘并补充水,得到净化尾气,部分净化尾气送燃烧预热工序4,其余净化尾气送储热工序7;
48.7)在固体氧化物电解池电解工序8中,来自储热工序7的温度稳定的氢气水蒸汽混合气在电能作用下经固体氧化物电解池电解,得到热氢气和热氧气,热氢气送氢气增压工序9,热氧气送氧气增压工序10;
49.8)在冷却工序11中,来自流态化还原工序5的热还原矿经冷却,得到直接还原铁。
50.实施例2
51.本实施例采用实施例1所述一种铁矿细粉氢能高效流态化还原的方法。首先将粒径小于0.1mm的铁矿细粉(全铁含量约60%)加入4%水玻璃经研磨混合均匀并在0.2mpa下压制成块,再置于300℃下固化1h,得到固化料。固化料经破碎筛分得到0.1-5mm的粗颗粒,粗颗粒经还原尾气燃烧预热,得到热矿粉。热矿粉在600℃下氢气中流态化还原2h,还原压力为1mpa,得到热还原矿和还原尾气。还原尾气经净化除尘后部分用于燃烧预热,其余净化尾气经储热技术稳定温度后送入固体氧化物电解池,其中储热材料为金属合金类,固体氧化物电解池的电解质材料为8mol%的y2o3稳定的zro2,固体氧化物电解池的阴极材料为ni掺杂的y2o3稳定的zro2金属陶瓷,固体氧化物电解池的阳极材料为la
0.8
sr
0.2
feo
3-x-ysz,在600℃下电解得到热氢气和热氧气,热氢气经增压至1.1mpa后循环应用于流态化还原铁矿粉,热氧气经增压至1.1mpa后部分用于流态化还原补热,其余增压热氧气用于燃烧预热。热还原矿经冷却后可得到金属化率约94%的直接还原铁。如图2所示,小于0.1mm的铁矿细粉与本发明所述方法的改性料在高温流态化还原中金属化率随时间的变化规律。小于0.1mm的铁矿细粉在实验条件下不能正常的流态化还原,而本发明所述方法的改性料可以稳定地流态化还原2h至金属化率94%左右。此外,本发明所述方法的改性料的流态化还原速率显著高于小于0.1mm的铁矿细粉的。
52.实施例3
53.本实施例采用实施例1所述一种铁矿细粉氢能高效流态化还原的方法。首先将粒径小于0.1mm的铁矿细粉(全铁含量约50%)和来自破碎筛分工序3的细粉中加入10%石灰经研磨混合均匀并在20mpa下压制成块,再置于200℃下固化5h,得到固化料。固化料经破碎筛分得到0.1-5mm的粗颗粒,粗颗粒经还原尾气燃烧预热,得到热矿粉。热矿粉在900℃下氢气中流态化还原0.5h,还原压力为0.1mpa,得到热还原矿和还原尾气。还原尾气经净化除尘后部分用于燃烧预热,其余净化尾气经储热技术稳定温度后送入固体氧化物电解池,其中储热材料为熔盐类,固体氧化物电解池的电解质材料为8mol%的y2o3稳定的zro2,固体氧化物电解池的阴极材料为ni掺杂的y2o3稳定的zro2金属陶瓷,固体氧化物电解池的阳极材料为la
0.8
sr
0.2
mno
3-x-ysz,在900℃下电解得到热氢气和热氧气,热氢气经增压至0.11mpa后循环应用于流态化还原铁矿粉,热氧气经增压至0.11mpa后部分用于流态化还原补热,其余增压热氧气用于燃烧预热。热还原矿经冷却后可得到金属化率约93%的直接还原铁。如图3所示,小于0.1mm的铁矿细粉与本发明所述方法的改性料在高温流态化还原中金属化率随时间的变化规律。小于0.1mm的铁矿细粉在实验条件下不能正常的流态化还原,而本发明所述
方法的改性料可以稳定地流态化还原0.5h至金属化率93%左右。此外,本发明所述方法的改性料的流态化还原速率显著高于小于0.1mm的铁矿细粉的。
54.实施例4
55.本实施例采用实施例1所述一种铁矿细粉氢能高效流态化还原的方法。首先将粒径小于0.1mm的铁矿细粉(全铁含量约65%)加入0.5%水泥经研磨混合均匀并在10mpa下压制成块,再置于20℃下固化10h,得到固化料。固化料经破碎筛分得到0.1-5mm的粗颗粒,粗颗粒经还原尾气燃烧预热,得到热矿粉。热矿粉在800℃下氢气中流态化还原0.5h,还原压力为0.4mpa,得到热还原矿和还原尾气。还原尾气经净化除尘后部分用于燃烧预热,其余净化尾气经储热技术稳定温度后送入固体氧化物电解池,其中储热材料为熔盐类,固体氧化物电解池的电解质材料为8mol%的y2o3稳定的zro2,固体氧化物电解池的阴极材料为ni掺杂的y2o3稳定的zro2金属陶瓷,固体氧化物电解池的阳极材料为la
0.8
sr
0.2
coo
3-x-ysz,在760℃下电解得到热氢气和热氧气,热氢气经增压至0.45mpa后循环应用于流态化还原铁矿粉,热氧气经增压至0.6mpa后部分用于流态化还原补热,其余增压热氧气用于燃烧预热。热还原矿经冷却后可得到金属化率约93%的直接还原铁。
56.实施例5
57.本实施例采用实施例1所述一种铁矿细粉氢能高效流态化还原的方法。首先将粒径小于0.1mm的铁矿细粉(全铁含量约70%)加入2%膨润土经研磨混合均匀并在15mpa下压制成块,再置于90℃下固化8h,得到固化料。固化料经破碎筛分得到0.1-5mm的粗颗粒,粗颗粒经还原尾气燃烧预热,得到热矿粉。热矿粉在700℃下氢气中流态化还原1.5h,还原压力为0.8mpa,得到热还原矿和还原尾气。还原尾气经净化除尘后部分用于燃烧预热,其余净化尾气经储热技术稳定温度后送入固体氧化物电解池,其中储热材料为金属合金类,固体氧化物电解池的电解质材料为8mol%的y2o3稳定的zro2,固体氧化物电解池的阴极材料为ni掺杂的y2o3稳定的zro2金属陶瓷,固体氧化物电解池的阳极材料为la
0.6
sr
0.4
co
0.2
fe
0.8o3-x-ysz,在650℃下电解得到热氢气和热氧气,热氢气经增压至0.9mpa后循环应用于流态化还原铁矿粉,热氧气经增压至0.85mpa后部分用于流态化还原补热,其余增压热氧气用于燃烧预热。热还原矿经冷却后可得到金属化率约95%的直接还原铁。
58.本发明中%未进行说明的,均为质量百分比含量。
59.本发明的工艺参数(如温度、时间等)区间上下限取值以及区间值都能实现本法,在此不一一列举实施例。
60.本发明未详细说明的内容均可采用本领域的常规技术知识。
61.最后所应说明的是,以上实施例仅用以说明本发明的技术方案而非限制。尽管参照实施例对本发明进行了详细说明,本领域的普通技术人员应该理解,对本发明的技术方案进行修改或者等同替换,都不脱离本发明技术方案的精神和范围,其均应涵盖在本发明的权利要求范围当中。
再多了解一些
本文用于创业者技术爱好者查询,仅供学习研究,如用于商业用途,请联系技术所有人。