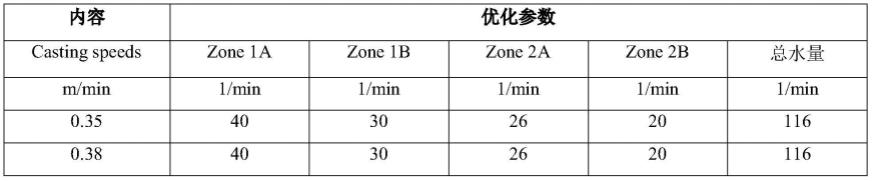
1.本发明涉及特殊钢冶炼、加工技术领域,具体涉及一种消除大规格曲轴磁痕缺陷的钢材生产方法。
背景技术:
2.国ⅵ船用曲轴项目对曲轴磁痕缺陷有很高的要求。申请人首批试验料提供用户,加工调质曲轴磁粉探伤后磁痕出现率接近90%,针对该问题,发明人开展了专项研究,发现造成磁痕显示的主要原因为钢材经模锻加工曲轴时,由于局部变形量大,钢材等轴晶区金属流动于曲轴主轴颈、连杆颈等表面,见附图1。曲轴经表面感应淬火后主轴颈、连杆颈表面成分偏析区与正常基体组织存在差异,见附图2,差异性组织磁粉探伤过程中由于磁通量不一致,最终导致磁痕显示。另据用户反馈,对标国内其他钢厂生产钢材加工同款曲轴,国内兴澄特钢、大冶特钢等生产钢材加工曲轴磁痕出现率也高达50%以上。
3.针对上述问题,很有必要研究出一种降低曲轴磁痕缺陷的钢材生产方法,保证大规格船用曲轴的产品质量。
技术实现要素:
4.针对现有技术存在的上述不足,本发明的目的在于提供一种消除大规格曲轴磁痕缺陷的钢材生产方法。
5.为实现以上目的,本发明采用如下技术方案:
6.一种消除大规格曲轴磁痕缺陷的钢材生产方法,包括以下步骤:
7.(一)铸坯冶炼、连铸技术
8.1)consteel电炉冶炼;
9.2)lf精炼;
10.3)vd脱气;
11.4)弱氩搅拌;
12.5)、连铸:目标过热度控制在20-30℃范围内,结晶器二冷水配比采用强冷曲线,电磁搅拌m-ems电流100a,频率1.5hz,f-ems电流750a,频率7.5hz;
13.(二)连铸大方坯轧制生产钢材:
14.1)连铸大方坯加热;
15.2)连铸大方坯开坯
16.采用大压下开坯工艺:大压下采用9道次翻转开坯,开坯至255mm
×
255mm过程方坯,单道次最大压下量达75mm,最小压下量为28mm;
17.3)连铸大方坯产材。
18.优选的,所述连铸大方坯加热时,大方坯按照下述加热制度进行加热:预热段≤850℃,加热ⅰ段温度1050
±
50℃,加热ⅱ段温度1240
±
30℃,均热ⅰ段温度1240
±
30℃,均热ⅱ段温度1230
±
30℃,总加热时间8~12h,高温扩散时间≥3.5h,出炉。
19.优选的,所述连铸大方坯产材:255mm
×
255mm过程方坯经6架连轧机组轧制产材;产材总轧制比控制在6.0以上。
20.优选的,所述步骤(一)中,浇注过热度由20-35℃控制至20-30℃;电磁搅拌m-ems电流由500a降低至100a,f-ems电流由660a提高至750a,频率不变。
21.优选的,所述步骤(一)中,结晶器二冷水配比中:喷淋水zone 1a由31l/min提高至40l/min,喷淋水zone 1b由25l/min提高至30l/min,喷淋水zone 2a由17l/min提高至26l/min,喷淋水zone 2b由13l/min提高至20l/min。
22.优选的,所述步骤(二)中,连铸大方坯开坯道次由11道次降低至9道,单道次最大压下量由60mm增加至75mm,最小压下量由0mm增加至28mm。
23.优选的,所述consteel电炉冶炼采用consteel电炉全废钢或钢水 废钢冶炼。
24.优选的,所述lf精炼,进入lf温度:≥1500℃,氩气保护流量:200~400nl/min,出lf温度:1620~1650℃。
25.优选的,所述vd脱气,氩气控制:粗真空氩气流量50~150nl/min,极真空氩气流量100~200nl/min;vd要求:真空度≤0.5乇下保持时间≥18min,vd后h≤2.0ppm。
26.优选的,所述弱氩搅拌,弱氩流量100
±
50nl/min,弱氩搅拌时间≥15min。
27.与现有技术相比,本发明具有以下有益效果:
28.(1)通过提高连铸坯浇注过热度、降低电磁搅拌m-ems电流、提高电磁搅拌f-ems电流,增加二冷水中喷淋水配比,来降低连铸坯等轴晶率,由常规33.73%降低至26.66%,降幅7.07%。改善连铸坯芯部质量,降低连铸坯中心缩孔,由常规1级降低至0级;
29.(2)通过连铸大方坯大压下开坯、连轧机组产材的钢材,降低钢材等轴晶率及长宽比比率,等轴晶率由常规34.8%降低至29.5%,降幅5.3%,等轴晶长宽比比率由常规1.42降低至1.03,降幅0.39。
30.(3)采用本发明的方法生产出来的钢材具有等轴晶尺寸及等轴晶长宽比比率低的特点,经过大变形锻造加工曲轴后,磁粉探伤时无严重磁痕缺陷,磁痕缺陷占比(轻微磁痕)为≤10%,且轻微磁痕弥散分布,对存在轻微磁痕的船用曲轴经装机进行台架试验后疲劳性能均合格,未产生任何质量问题。钢材综合性能与进口钢材相当,完全能够满足国ⅵ船用大规格曲轴用钢选材的要求,对我国船用曲轴用钢的设计、制造和安全稳定运行有着重要的意义。
附图说明
31.通过阅读参照以下附图对非限制性实施例所作的详细描述,本发明的其它特征、目的和优点将会变得更明显:
32.图1是曲轴主轴颈、连杆颈酸洗低倍组织;参见图1a,可见对应钢材芯部等轴晶区流动于曲轴杆颈表面;参见图1b,可见对应钢材芯部及钢材等轴晶区流动于表面。
33.图2是曲轴磁痕区(a)和正常区高倍显微组织(b)。
具体实施方式
34.下面结合具体实施例对本发明进行详细说明。以下实施例将有助于本领域的技术人员进一步理解本发明,但不以任何形式限制本发明。应当指出的是,对本领域的普通技术
人员来说,在不脱离本发明构思的前提下,还可以做出若干变形和改进。这些都属于本发明的保护范围。
35.一种消除大规格曲轴磁痕缺陷的钢材生产方法,包括以下步骤:
36.(一)铸坯的冶炼、连铸
[0037]ⅰ.consteel电炉冶炼:
[0038]
钢铁料由二、三级废钢或返回钢、铁水及生铁组成。
[0039]
氧化除磷渣料总加入量:石灰1000~3500kg、白云石500~1200kg;氧化除磷渣料分批次加入,每批次加入量为200~500kg。
[0040]
电炉出钢终点成分控制c:≥0.08%p:≤0.018%(残余合格)。
[0041]ⅱ.lf精炼:
[0042]
进入lf温度:≥1500℃。
[0043]
氩气保护流量:200~400nl/min。
[0044]
lf精炼渣料配比:石灰:550
±
50kg/炉;脱氧剂:100kg/炉;预熔渣:180
±
20kg/炉;低硅脱氧精炼渣100kg,脱氧铝控制范围:1.0~1.3kg/t。
[0045]
过程调渣:采用si-c粉、碳粉等扩散脱氧剂调渣,总量控制在1.0-2.0kg/t。
[0046]
白渣精炼时间:≥40分钟。
[0047]
精炼过程目标铝:0.020~0.040%。
[0048]
目标渣系:feo≤0.4%;sio2:8%~10%;cao:50%~55%;mgo:3%~7%;al2o3:20%~28%;碱度:5~7。
[0049]
出lf温度:1620~1650℃。
[0050]ⅲ.vd脱气:
[0051]
氩气控制:粗真空(》200乇)氩气流量50~150nl/min,极真空氩气流量100~200nl/min。
[0052]
vd要求:真空度≤0.5乇下保持时间≥18min,vd后h≤2.0ppm。
[0053]ⅳ.弱氩搅拌:
[0054]
弱氩流量100
±
50nl/min,弱氩搅拌时间≥15min。
[0055]
ⅴ
.连铸:
[0056]
吊包温度:第一包1574
±
5℃;连浇包1554
±
5℃。
[0057]
浇注过热度:20~30℃;电磁搅拌:m-ems电流100a,频率1.5hz;f-ems电流750a,频率7.5hz;拉速控制:0.38m/min。
[0058]
结晶器二冷水配比见表1。
[0059]
表1结晶器二冷水配比
[0060][0061]
[0062]
注:连铸坯要求红送装炉或入坑保温,及时入坑缓冷,入坑后加保温盖,缓冷时间大于48小时。
[0063]
钢材的化学成分以质量百分比计为:碳:0.39-0.41、硅:0.22-0.32、锰:0.70-0.76、磷:≤0.018、硫:≤0.015、铬:1.10-1.16、钼:0.18-0.22、铜:≤0.15、镍:≤0.15、铝:0.020-0.040、氢:≤0.0002,锡≤0.015、砷≤0.015、锑≤0.015,余量为铁。
[0064]
(二)连铸大方坯轧制生产钢材
[0065]
1)连铸大方坯加热:
[0066]
大方坯加热制度:预热段≤850℃,加热ⅰ段温度1050
±
50℃,加热ⅱ段温度1240
±
30℃,均热ⅰ段温度1240
±
30℃,均热ⅱ段温度1230
±
30℃,总加热时间8~12h,高温扩散时间≥3.5h,出炉;
[0067]
2)连铸大方坯开坯:
[0068]
连铸大方坯出炉后通过高压水箱进行水除磷处理,有效清除表面氧化铁皮。开坯开轧温度:≥1100℃。
[0069]
采用大压下开坯工艺:大压下采用9道次翻转开坯,开坯至255mm
×
255mm过程方坯,单道次最大压下量75mm,最小压下量28mm,见表2。
[0070]
3)连铸大方坯产材:
[0071]
连轧开轧温度:≥980℃。
[0072]
连轧机组产材:255mm
×
255mm过程方坯采用6架连轧机组轧制产材;产材总轧制比控制在6.0以上。
[0073]
4)钢材保温:
[0074]
钢材轧制完毕经过热锯锯切后采用快床收集,下快床后及时入保温坑保温,保温时间≥48h,入坑温度500℃~700℃。
[0075][0076]
检测:
[0077]
1.铸坯、棒材检测
[0078]
比较连铸常规与优化生产铸坯等轴晶区尺寸及晶率,结果见下表3。
[0079]
表3连铸常规与优化生产铸坯等轴晶区尺寸及晶率比较表
[0080][0081]
对比常规生产,优化连铸参数生产后铸坯在保证化学成分偏析度基础上等轴晶区尺寸及占比可明显降低。
[0082]
2.比较连铸坯开坯时,普通压下与大压下钢材等轴晶区尺寸及长宽比比率,结果见下表4。
[0083]
表4普通压下与大压下钢材等轴晶区尺寸及长宽比比率比较表
[0084]
压下规格等轴晶区尺寸,mm比率普通压下160100
×
701.42大压下16081
×
781.04大压下16082
×
801.03
[0085]
检测结果表明:通过本生产工艺发明,铸坯等轴晶区尺寸、等轴晶率、钢材等轴晶区尺寸与长宽比比率显著降低。
[0086]
本发明的方法通过对炼钢连铸系统、连铸坯加热开坯工序生产工艺的创造发明优化,使得钢材质量得到大幅提升,进而提高下游用户模锻曲轴大变形后,成品曲轴件经磁粉探伤时,磁痕出现率大幅降低,由原试验料到后期批量供货阶段,磁痕出现率降幅达80%以上,有效提高了大规格船用曲轴综合性能及质量。
[0087]
本发明方法,还可以应用于同类调质结构件用钢、非调曲轴用钢等项目中,生产钢材,以降低曲轴磁痕出现率。
[0088]
以上对本发明的具体实施例进行了描述。需要理解的是,本发明并不局限于上述特定实施方式,本领域技术人员可以在权利要求的范围内做出各种变形或修改,这并不影响本发明的实质内容。
再多了解一些
本文用于创业者技术爱好者查询,仅供学习研究,如用于商业用途,请联系技术所有人。