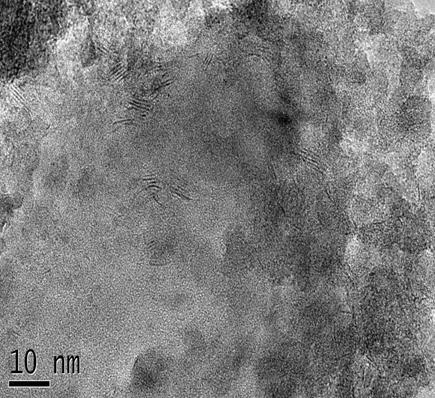
1.本发明涉及一种汽油加氢脱硫方法。
背景技术:
2.随着环保法规的日趋严格,世界各国为了有效控制汽车尾气中有害物质排放量,对清洁汽油中的硫含量要求越来越低。我国汽油池组成中催化裂化(fcc)汽油比例大,是成品汽油中硫的最主要贡献者,因此fcc汽油的深度脱硫是满足我国成品汽油标准的关键。
3.目前,国外具有代表性的fcc汽油选择性加氢脱硫工艺有法国axens公司开发的prime-g 技术、exxon mobil公司开发scanfining技术。国内工业应用广泛的是oct-m、oct-md、oct-me系列技术以及rsds-i、rsds-、rsds-系列技术,这些技术为炼油企业应对油品质量升级提供了有效的技术支撑。这些技术的核心是有效提高重汽油加氢脱硫的选择性。因而,高选择性重汽油加氢脱硫催化剂及工艺技术开发显得至关重要。
4.oct-m技术通过选择合适的切割点温度将fcc汽油切割成轻、重汽油馏分,重汽油馏分进行选择性加氢脱硫,精制重汽油与轻汽油馏分混合进行无碱脱臭,以保证出装置精制汽油产品硫醇硫含量和腐蚀指标合格。oct-md技术将无碱脱臭单元前移,用于处理fcc汽油全馏分,而后,脱臭汽油进预分馏塔切割,轻汽油馏分直接去产品调合,重汽油馏分去选择性加氢脱硫单元加工,精制重汽油经气提脱除硫化氢后出装置去产品调合。oct-me技术在催化裂化装置内进行轻/重汽油切割分离,轻汽油采用无碱脱臭技术进行脱硫醇处理;脱臭后轻汽油与来自fcc装置的空冷前热柴油一起进原oct-md装置的预分馏塔。从塔顶分离出轻汽油直接出装置去产品调合系统;从侧线抽出少量的中汽油既可以和重汽油一起去下游加氢单元进行选择性加氢脱硫,加氢重汽油经汽提脱除硫化氢后出装置去产品调合系统。上述工艺流程重汽油加氢单元都采用原料及氢气上进料方式。
5.cn1488721a公开了一种汽油选择性加氢催化剂及工艺,工艺为在加氢脱硫条件下,原料油依次通过活性金属逐渐增加的多个催化剂床层,催化剂及工艺技术提高了反应活性及选择性,催化剂活性及选择性都需要进一步提升。
技术实现要素:
6.针对现有技术的不足,本发明提供一种汽油加氢脱硫方法。该方法通过反应进料方式与催化剂合理匹配,可以有效提高汽油加氢脱硫反应的活性和选择性,实现装置的稳定运行,适用于工业应用。
7.本发明的汽油加氢脱硫方法,包括如下内容:固定床加氢反应器由上至下设置三个加氢脱硫催化剂床层,原料及氢气以气液并流的形式分为三股从反应器顶部及催化剂床层间进入反应器,与催化剂床层接触进行加氢脱硫反应,反应产物由反应器底部排出;其中,催化剂床层内装填硫化型加氢脱硫催化剂;以硫化型加氢脱硫催化剂总重量为基准,mos2为2.0%~30.0%,优选为2.0%~25.0%,co9s8为0.1%~7.0%,优选为0.1%~6.0%,fes为0.7%~11%,优选为0.7%~9%,碳含量为0.5%~18.0%,载体含量为50%~96.7%;
本发明方法中,反应器内由上至下三股原料的体积分别为30~80%、10~35%、10~35%,优选为50~70%、15~25%、15~25%,三股原料体积百分含量之和为100%。
8.本发明方法中,所述的加氢脱硫反应条件为:压力1.0~4.0mpa,优选1.0~2.0mpa;氢油体积比100:1~1000:1,优选200:1~500:1;体积空速0.1~10.0h-1
,优选0.5~6.0h-1
;反应温度200~350℃,优选230~300℃。
9.本发明方法中,三个加氢脱硫催化剂床层装填的体积比例分别为30~80%、10~35%、10~35%,优选为50~70%、15~25%、15~25%,三个加氢脱硫催化剂床层装填体积百分比之和为100%。
10.本发明方法中,所述的硫化型加氢脱硫催化剂的孔容为0.3~1.3ml/g,比表面积为150~400m2/g,强度100~250n/cm,堆积密度0.65~0.90g/ml。
11.本发明方法中,所述的硫化型加氢脱硫催化剂还可以根据需要加入助剂,如k、na、mg、si、p、zr或ti等助剂元素中的一种或多种,以催化剂总重量为基准,助剂以氧化物计加入量为1.0%~10%,催化剂各组分含量之和为100%。
12.本发明的硫化型加氢脱硫催化剂的制备方法,包括如下内容:(1)用含有活性金属fe和mo的溶液浸渍载体,浸渍后载体进行干燥,干燥后进行第一次硫化处理;(2)用液态烯烃饱和浸渍步骤(1)得到的物料,然后热处理;(3)用含有活性金属co的溶液浸渍步骤(2)得到的物料,经干燥、焙烧后,进行第二次硫化处理,得到硫化型加氢脱硫催化剂。
13.其中,步骤(1)所述的载体为无机耐熔氧化物,选自氧化铝、氧化硅、氧化锆、氧化钛、氧化镁中的一种或多种,优选为氧化铝。载体可以添加助剂改性处理,所述的改性助剂可以为k、na、mg、si、p、zr、ti。
14.步骤(1)所述的含有活性金属fe和mo的浸渍液i的配制方式为本领域技术人员熟知,如可以采用如下方式:先将柠檬酸溶净水中,加入乙酸亚铁,煮沸溶解,冷却后,再加入氨水,加入钼酸铵于上述溶液中,溶解后用氨水将溶液体积调至终体积,密闭保存。
15.步骤(1)所述的干燥条件为:100~120℃下干燥1~5小时。
16.步骤(1)所述的第一次硫化处理采用器内或器外硫化过程,引入硫化剂的量为催化剂理论需硫量的90%~150%、硫化过程采用程序升温,温度升至200~350℃恒温1~16小时。硫化剂一般为二硫化碳、二甲基二硫醚、甲基硫醚、正丁基硫醚中的一种或多种。
17.步骤(2)所述的液态烯烃为为碳原子数2~10 的烯烃、二烯烃中的一种或多种,优选为已二烯和/或正庚烯。
18.步骤(2)所述的热处理过程为:在50~250℃加热1~8小时,升温至250~300℃加热1~72小时,再升温至300~400℃加热1~72小时。
19.步骤(3)所述的含有活性金属co的浸渍液ii的配制方式是先将柠檬酸溶于净水中,加入碳酸钴,煮沸溶解,冷却后,将溶液体积用净水调至终体积,密闭保存。
20.步骤(3)所述的干燥温度为100~120℃,干燥时间为1~5小时;焙烧温度为300~350℃,焙烧时间为3~4小时。
21.步骤(3)所述的第二次硫化处理采用器内或器外硫化过程,引入硫化剂的量为催化剂理论需硫量的90%~150%、硫化过程采用程序升温,温度升至200~350℃恒温1~16小时。
硫化剂一般为二硫化碳、二甲基二硫醚、甲基硫醚、正丁基硫醚中的一种或多种。
22.上述方法得到的硫化型加氢脱硫催化剂,活性相mos2的平均片晶长度4~14nm,优选为7~11nm,单个垛层中的平均片晶层数为1~12层,优选为5.5~12层,以垛层总个数为基准,层数大于5层的垛层的比例为15%~30%。
23.本发明与现有技术相比具有如下优点:1、固定床加氢反应器内原料及氢气分为三股以并流形式进入,在反应器内各床层反应空速由上至下一个逐渐增加的过程,原料及氢气的逐步进入也利于反应各区间温度的控制,使反应更接近于等温反应过程,反应趋于缓和,利于增加催化剂的加氢脱硫选择性。
24.2、催化剂采用分步硫化处理,由于mo与co金属相比更难于硫化,易造成硫化态mo被co金属包裹的现象,先硫化mo和fe,然后在硫化态vib族金属mo以及fe金属上再浸渍第第viii族co金属进行分步浸渍硫化,降低了每一步活性金属浸渍和活化的难度;同时,通过特殊的积炭方式再进行硫化处理,形成fe修饰的mos2,即可避免硫化态mo金属被硫化态co金属包裹的现象,又可覆盖载体表面较强吸附位,削弱了后续浸渍co活性金属与载体表面的相互作用力,更有利于mo活性金属在fe金属修饰下的分散,能够充分发挥co金属助剂作用,催化剂mos2活性相片晶的长度更长,垛层层数更多,这种结构的硫化态催化剂具有更好的加氢脱硫选择性,即保证了加氢脱硫活性,又更好的抑制了烯烃的饱和;同时,fe源采用乙酸亚铁,可以克服以往采用无机铁盐在溶液配制过程中与第viii族co金属与第vib族mo金属的竞争结合。
附图说明
25.图1本发明实施例1催化剂的透射电镜图。
26.图2本发明对比例1催化剂的透射电镜图。
27.图3本发明实施例5工艺示意图。
28.图4本发明对比例5工艺示意图。
29.其中,1-原料1,2-氢气1,3第一加氢脱硫催化剂床层,4-第二加氢脱硫催化剂床层,5-第三加氢脱硫催化剂床层,6-汽油产品,7-原料2,8-氢气1,9-原料3,10-氢气3。
具体实施方式
30.以下用实施例具体说明本发明汽油加氢脱硫方法及所使用的催化剂。本发明中,催化剂比表面积和孔容采用低温液氮吸附法测定的。片晶长度及垛层层数比例采用场发射透射电子显微镜测定:选取多于350个mos2片晶统计整理平均层数、平均长度及大于5层晶片比例,统计公式为:其中li代表晶片长度,ni代表i层的数目,ai代表晶片li的数目,bi代表层数ni的数
目。
31.本发明催化剂的具体制备过程如下:(1)将载体置于滚锅中,在转动条件下,向滚锅中的载体以雾化方式喷入载体饱和吸水量的的mo、fe氨溶液,溶液喷完后,在滚锅中继续转动10~60分钟,然后放置1~24小时,在100~120℃下干燥1~5小时,采用器内或器外硫化过程进行硫化处理,引入硫化剂的量为催化剂理论需硫量的90%~150%、硫化过程采用程序升温,温度升至200~350℃恒温1~16小时;(2)用液态烯烃饱和浸渍步骤(1)得到的物料,在50~250℃加热1~8h,升温至250~300℃加热1~72h,再升温至300~400℃加热1~72h进行热处理;(3)将步骤(2)得到的物料置于滚锅中,在转动条件下,向滚锅中以雾化方式喷入饱和吸水量的的含有活性金属co的溶液浸渍溶液,溶液喷完后,在滚锅中继续转动10~60分钟,然后放置1~24小时,在100~120℃下干燥1~5小时,采用器内或器外硫化过程进行第二次硫化处理,引入硫化剂的量为催化剂理论需硫量的90%~150%、硫化过程采用程序升温,温度升至200~350℃恒温1~16小时,得到成品催化剂。
32.在上述制备方法中,浸渍液的浓度由吸水率和所要求的催化剂组成(含量)确定。
33.实施例1(1)将7.7g柠檬酸溶于60ml净水中,加12.7g乙酸亚铁,加入19.2g钼酸铵于上述溶液中,用25%氨水将溶液体积调至150ml,密闭保存。将200 g载体置于滚锅中,用150ml所配含有活性金属fe和mo的溶液浸渍进行喷浸,溶液喷完后,在滚锅中继续转动30分钟,然后放置18小时,在110℃下干燥3小时;采用器内硫化过程进行硫化处理,引入硫化剂的量为催化剂理论需硫量的120%、硫化过程采用程序升温,温度升至280℃恒温10h;(2)用600ml己二烯饱和浸渍步骤(1)得到的物料4小时,然后,在200℃加热4h,升温至300℃加热24h,再升温至400℃加热10h进行热处理;(3)将14.3g柠檬酸溶于60ml净水中,加10.2g碳酸钴,煮沸溶解,将溶液体积调至80ml,浸渍步骤(2)得到的物料,溶液喷完后,在滚锅中继续转动30分钟,然后放置18小时,在110℃下干燥3小时,采用器内硫化过程进行硫化处理,引入硫化剂的量为催化剂理论需硫量的120%、硫化过程采用程序升温,温度升至280℃恒温10h,得成品催化剂a。
34.实施例2(1)将4.2g柠檬酸溶于105ml净水中,加6.9g乙酸亚铁,加入10.5g钼酸铵于上述溶液中,用25%氨水将溶液体积调至150ml,密闭保存。将200 g载体置于滚锅中,用150ml所配含有活性金属fe和mo的溶液浸渍进行喷浸,溶液喷完后,在滚锅中继续转动30分钟,然后放置18小时,在110℃下干燥3小时;采用器内硫化过程进行硫化处理,引入硫化剂的量为催化剂理论需硫量的120%、硫化过程采用程序升温,温度升至280℃恒温10h;(2)用600ml己二烯饱和浸渍步骤(1)得到的物料4小时,然后,在200℃加热4h,升温至300℃加热24h,再升温至400℃加热10h进行热处理;(3)将8.3g柠檬酸溶于60ml净水中,加5.9g碳酸钴,煮沸溶解,将溶液体积调至90ml,浸渍步骤(2)得到的物料,溶液喷完后,在滚锅中继续转动30分钟,然后放置18小时,在110℃下干燥3小时,采用器内硫化过程进行硫化处理,引入硫化剂的量为催化剂理论需
硫量的120%、硫化过程采用程序升温,温度升至280℃恒温10h,得成品催化剂b。
35.实施例3(1)将11.7g柠檬酸溶于47ml净水中,加19.4g乙酸亚铁,加入29.4g钼酸铵于上述溶液中,用25%氨水将溶液体积调至150ml,密闭保存。将200 g载体置于滚锅中,用150ml所配含有活性金属fe和mo的溶液浸渍进行喷浸,溶液喷完后,在滚锅中继续转动30分钟,然后放置18小时,在110℃下干燥3小时;采用器内硫化过程进行硫化处理,引入硫化剂的量为催化剂理论需硫量的120%、硫化过程采用程序升温,温度升至280℃恒温10h;(2)用600ml己二烯饱和浸渍步骤(1)得到的物料4小时,然后,在200℃加热4h,升温至300℃加热24h,再升温至400℃加热10h进行热处理;(3)将17.3g柠檬酸溶于60ml净水中,加12.4g碳酸钴,煮沸溶解,将溶液体积调至76ml,浸渍步骤(2)得到的物料,溶液喷完后,在滚锅中继续转动30分钟,然后放置18小时,在110℃下干燥3小时,采用器内硫化过程进行硫化处理,引入硫化剂的量为催化剂理论需硫量的120%、硫化过程采用程序升温,温度升至280℃恒温10h,得成品催化剂c。
36.实施例4(1)将16g柠檬酸溶于41ml净水中,加26.5g乙酸亚铁,加入40.1g钼酸铵于上述溶液中,用25%氨水将溶液体积调至150ml,密闭保存。将200 g载体置于滚锅中,用150ml所配含有活性金属fe和mo的溶液浸渍进行喷浸,溶液喷完后,在滚锅中继续转动30分钟,然后放置18小时,在110℃下干燥3小时;采用器内硫化过程进行硫化处理,引入硫化剂的量为催化剂理论需硫量的120%、硫化过程采用程序升温,温度升至280℃恒温10h;(2)用600ml己二烯饱和浸渍步骤(1)得到的物料4小时,然后,在200℃加热4h,升温至300℃加热24h,再升温至400℃加热10h进行热处理;(3)将19.4g柠檬酸溶于50ml净水中,加13.8g碳酸钴,煮沸溶解,将溶液体积调至76ml,浸渍步骤(2)得到的物料,溶液喷完后,在滚锅中继续转动30分钟,然后放置18小时,在110℃下干燥3小时,采用器内硫化过程进行硫化处理,引入硫化剂的量为催化剂理论需硫量的120%、硫化过程采用程序升温,温度升至280℃恒温10h,得成品催化剂d。
37.对比例1同实施例1,只是未经过液态烯烃浸渍及热处理,得成品催化剂e。
38.对比例2同实施例1,只是浸渍mo、fe后,不进行第一次硫化处理,得成品催化剂f。
39.对比例3同实施例1,只是浸渍mo、fe后,不进行第一次硫化处理;也未经过液态烯烃浸渍及热处理,得成品催化剂g。
40.对比例4同实施例1,只是浸渍液中不含有fe,得成品催化剂h。
41.实施例5催化剂a~h的性质见表1。
42.在200ml固定床小型加氢装置进行汽油选择性加氢脱硫反应,装填三个催化剂床层,反应条件为:反应压力1.6mpa、液时体积空速4.0h-1
、氢油体积比为300nm3/m3、反应温度275℃,原料的硫含量为564μg/g、ron为92.8。具体装填比例、装填催化剂种类、运转600小时
的评价结果见表2对比例5按照图4的工艺流程图,即原料和氢气同时从反应器顶部进料,气液并流向下进入反应器,反应器内催化剂床层设置及反应条件同表2中的装填情况1。
43.表1催化剂主要性质表2 催化剂床层装填情况及评价结果表2结果表明,本发明选择性加氢脱硫过程,在同等脱硫率的情况下,辛烷值损失小。经过一定运转时间后,本发明催化剂的活性和选择性好,选择性加氢脱硫性能较对比催化剂稳定。
再多了解一些
本文用于创业者技术爱好者查询,仅供学习研究,如用于商业用途,请联系技术所有人。