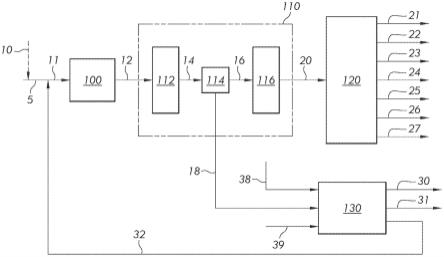
用于原油转化的系统和方法
1.本技术是pct国际申请pct/us2018/028592对应的中国国家阶段申请(申请号为201880026541.8,发明名称为“用于原油转化的系统和方法”)的分案申请。
2.相关申请的交叉引用
3.本技术要求2017年4月26日提交的题为“用于原油转化的系统和方法(systems and processes for conversion of crude oil)”的美国临时专利申请第62/490,175号和2018年4月3日提交的题为“用于原油转化的系统和方法(systems and processes for conversion of crude oil)”的美国专利申请第15/944,068号的优先权,所述申请均以全文引用的方式并入本文中。
技术领域
4.本公开的实施例涉及用于由原油产生烯族和芳香族石化产品的系统和方法,并且具体来说涉及利用加氢处理反应器由原油产生烯族和芳香族石化产品的系统和方法。
背景技术:
5.烯烃(例如,乙烯、丙烯、丁烯、丁二烯)和btx(苯、甲苯和二甲苯)是石化行业的基础且必需的中间物。其主要通过石油气和如石脑油、煤油或甚至气态油的馏出物的热裂解(或蒸汽热解)产生。为了获得高产率的烯烃和btx,蒸汽裂解器的优选进料应为高度链烷烃性且芳香烃含量低的进料,因为这些进料特性有助于减少不希望的产物和焦炭形成。
6.通过在加氢处理反应器中提质原油,直链链烷烃特性得到改良,并且可以将其直接进料到蒸汽裂解器中,从而使得能够直接由原油产生更大量的烯烃和芳香烃。
技术实现要素:
7.为了确保原油被转化成具有所需量的链烷烃和最小化量的芳香烃的进料,对于加氢处理反应器或粗调节单元存在显著氢气需求。尽管蒸汽裂解器单元产生可以再循环到加氢处理反应器的氢气,但来自蒸汽裂解器的再循环氢气的量无法使系统在其氢气需求方面自给自足。因此,持续需要为加氢处理反应器产生足够氢气的自给自足系统。
8.本公开的实施例通过气化不希望的原油馏分以产生氢气来增加用于加氢处理反应器的氢气产生。在原油转化方法中,必须排出约10到15重量(wt)%的低价值、高沸点(例如,540℃和更高)馏分(以下称为“较高沸点馏分”)以减少蒸汽裂解器内的焦炭形成。本公开的实施例使用这种较高沸点馏分作为进入气化单元的进料以产生更多的氢气并且产生动力。除了热解氢气之外,从气化单元产生的氢气使得本发明的原油转化方法在氢气需求方面能够自给自足。
9.根据一个实施例,可以通过一种方法由原油产生石化产品,所述方法可以包含将原油和氢气传递到加氢处理反应器中,将加氢处理的油分离成较低沸点馏分和较高沸点馏分,将较低沸点馏分传递到蒸汽裂解器的热解段以产生包含烯烃、芳香烃或两者的热解流出物,以及将较高沸点馏分传递到气化炉。气化炉可以产生氢气,并且由气化炉产生的氢气
的至少一部分可以被传递到加氢处理反应器。加氢处理反应器包含一种或多种加氢处理催化剂,其产生加氢处理的油。
10.根据另一实施例,提供了一种用于产生烯族和芳香族石化产品的方法。所述方法包括将氢气与原油混合以产生包含氢气和原油的进料流,和将原油与氢气混合物传递到加氢处理反应器,所述加氢处理反应器在300℃到450℃的温度和30到200巴的氢分压下操作,所述加氢处理反应器包含加氢处理催化剂,其由原油与氢气混合物产生加氢处理的混合物。将加氢处理的混合物传递到至少一个蒸汽裂解器,所述蒸汽裂解器包含在700℃到900℃的温度下操作的对流段,以产生加热的加氢处理的混合物,将混合物分离成较低沸点馏分和较高沸点馏分。将较低沸点馏分传递到对流段下游的蒸汽裂解器的热解段,以产生包含烯烃和芳香烃的热解流出物,并且将热解流出物输送到至少一个分离器,其中分离器将热解流出物转化成一种或多种包含烯烃、芳香烃或其组合的产物流。将较高沸点馏分传递到在至少900℃的温度下操作的气化炉,其中气化炉产生氢气,并且将气化炉中产生的氢气再循环,以便在加氢处理反应器的上游与原油混合。
11.实施例的额外特征和优点将在下文的具体实施方式中进行阐述,并且将部分地由所属领域的技术人员从所述描述而容易地清楚或通过实践本文所描述的实施例(包括下文的具体实施方式、权利要求书以及附图)而认识到。
附图说明
12.图1是根据本公开的一个或多个实施例的原油转化系统的示意性绘图。
13.图2是根据本公开的一个或多个实施例的原油转化系统的另一示意性绘图。
14.图3是根据本公开的一个或多个实施例的原油转化系统的又一示意性绘图。
15.图4是根据本公开的一个或多个实施例的原油转化系统的另一示意性绘图。
16.出于描述图1到4的简化示意图示和描述的目的,不包括可以采用并且对于某些化学处理操作领域的普通技术人员公知的众多阀、温度传感器、电子控制器等。此外,未描绘如精炼厂的典型化学处理操作中经常包括的伴随组件,例如空气供应器、催化剂料斗和烟道气操作装置。应理解,这些组件处于所公开的本发明实施例的精神和范围内。然而,可在本公开中所描述的实施例中增加操作组件,如本公开中所描述的那些组件。
17.现将更详细参考各种实施例,其中一些实施例在附图中说明。只要可能,将贯穿附图使用相同参考标号来指代相同或类似的零件。
18.附图中阐述的实施例在本质上是说明性的,并且不旨在对权利要求书进行限制。此外,附图的单独特征通过具体实施方式将变得更加清楚和明白。
具体实施方式
19.如本技术中所使用,“原油”应理解为包括来自常规来源的全原油,以及已经经历一些预处理的原油。在一些实施例中,“原油”可以包括来自非常规来源的原油,如压裂轻质油和其它天然气冷凝物。术语“原油”还应理解为包括已经历水-油分离、气-油分离、脱盐、稳定化或其组合的原油。在某些实施例中,原油流5具有25
°
到50
°
的api比重(以度(
°
)为单位)。
20.如本公开中所使用,“反应器”是指其中一种或多种化学反应可以在一种或多种反
应物之间任选地在一种或多种催化剂存在下发生的一种或多种容器。举例来说,反应器可以包括被配置成以分批反应器、连续搅拌槽反应器(continuous stirred-tank reactor;cstr)或活塞流动反应器形式操作的槽或管式反应器,其随后将更详细地描述。示例性反应器包括如固定床反应器的填充床反应器,和流化床反应器。在本发明描述的实施例中,加氢处理反应器可以包括多个串联的反应器,如其中已连接各自含有不同催化剂的多个容器。
21.如本公开中所使用,“分离单元”或分离器是指任何分离装置,其至少部分地将工艺流中混合的一种或多种化学品彼此分离。举例来说,分离单元可以选择性地将不同化学物种彼此分离,形成一种或多种化学部分。分离单元的实例包括但不限于蒸馏塔、闪蒸罐、分离罐、分离壶、离心机、漩涡分离器、过滤装置、捕集器、擦洗器、膨胀装置、膜、溶剂萃取装置、其组合等。应理解,本公开中所描述的分离方法可能不会将一种化学成分的全部与另一化学成分的全部完全分开。应理解,本公开中所描述的分离方法“至少部分地”将不同的化学组分彼此分开,并且即使没有明确说明,应理解,分离可以仅包括部分分离。
22.参考图1到4的实施例,描绘了用于由原油产生烯族和芳香族石化产品的系统和方法。如图1所示,系统包含将氢气与原油混合以产生包含氢气和原油的进料流11。如所展示,可存在方法开始时为加氢处理反应器100提供的任选氢气进料10;然而,如将随后描述,本系统将为加氢处理反应器100产生氢气32。
23.应理解,设想了原油的其它任选预处理步骤。举例来说,在与氢气混合以产生包含氢气和原油的进料流11之前,可以首先使原油流5任选地通过泵(未展示)以产生加压的原油流。在其它实施例中,可以使原油流5或加压的原油流通过加热器(未展示)以分别产生预热的原油流或预热或加压的原油蒸汽。因此,在某些实施例中,所述方法包括在与氢气混合之前将原油流5预热到至少300℃的温度。
24.如下文所描述,氢气可以是引进的氢气、来自下游单元的再循环氢气或其组合。像原油一样,与原油混合的氢气可以任选地通过加热器以产生预热的氢气流,或也可以加压以产生预热并且加压的氢气流,随后与原油、加压的原油流或预热并且加压的原油蒸汽混合。在一些实施例中,加热器用以将氢气流(或加压的氢气流)加热到至少300℃的温度。
25.如图1和图4所示,系统涉及将原油与氢气混合物的进料流11在300℃到450℃的温度和30到200巴的氢分压下传递到加氢处理反应器100。加氢处理反应器100,也可以称为加氢处理机(hydrotreater)或粗调节单元,包含加氢处理催化剂,其产生由进料流的加氢处理产生的加氢处理的混合物12。如将随后描述,在图2和3中,进料流211可以包括额外氢气源32。
26.在一个实施例中,加氢处理反应器100包括一个或多个加氢处理催化剂床。加氢处理反应器100能够使芳香烃,尤其多环芳香烃(polyaromatic)饱和并且转化成链烷烃和环烷烃。同时,加氢处理还可以去除油中的大多数杂质,如金属、硫和氮。因此,通过选择适当加氢处理催化剂和方法,可以纯化一些原油,并且所述原油因此适用作蒸汽裂解器进料。加氢处理催化剂可以包括以下中的一种或多种:加氢脱金属催化剂、加氢裂解催化剂、加氢脱芳香烃催化剂、加氢脱氮催化剂、加氢脱硫催化剂或两者。在一个实施例中,将加氢脱金属催化剂安置于其它加氢处理催化剂上游的催化剂床中。如本技术中所使用,“加氢处理的混合物”意思指原油与氢气的氢处理的掺合物,其已经历选自加氢脱金属、加氢脱芳香烃、加氢脱氮和加氢脱硫的一种或多种方法,并且“加氢处理的油”是指已经过加氢处理,并且可
以含于加氢处理的混合物中的原油。
27.加氢处理反应器100可以包括一个反应器或多个并联或串联的反应容器。举例来说,加氢处理反应器100可以包括多个反应容器,其各自含有有效量的一种或多种催化剂,如加氢脱金属催化剂,和具有加氢脱芳香烃、加氢脱氮、加氢脱硫、加氢裂解功能或其组合的加氢处理催化剂。在一个替代性实施例中,加氢处理反应器100可以包括一个或多个分离区,其各自含有有效量的加氢脱金属催化剂,和有效量的具有加氢脱芳香烃、加氢脱氮、加氢脱硫、加氢裂解功能或其组合的加氢处理催化剂。可替代地,加氢处理反应器100可以包括一个或多个含有有效量的加氢脱金属催化剂的催化剂层,和一个或多个含有有效量的额外加氢处理催化剂的催化剂层,所述额外加氢处理催化剂具有加氢脱芳香烃、加氢脱氮、加氢脱硫、加氢裂解功能或其组合。在额外实施例中,加氢处理反应器100包括加氢脱金属催化剂。在其它实施例中,加氢脱金属催化剂可以包括在单独反应容器(未展示)或单独分离区中。举例来说,在某些实施例中,加氢脱金属催化剂包括在与其它催化剂层分开的催化剂层中。
28.在一些实施例中,如所属领域的技术人员已知,加氢处理反应器100可以包括一个或多个氢气骤冷。一个或多个氢气骤冷用于控制加氢处理反应器100中的反应温度,并且通过在加氢处理反应器100的一个或多个反应容器、一个或多个分离区或一个或多个催化剂层之间引入氢气流来实现。用于氢气骤冷的氢气流可以是引进的氢气、如随后所描述的来自下游单元的再循环氢气或其组合。
29.在一个特定实施例中,进料流11传递到含有加氢脱金属催化剂的加氢处理反应器100,以去除存在的金属。脱金属后,可以将进料流11随后进料到下游的另一个催化剂床,在所述另一个催化剂床中存在额外加氢处理催化剂,且添加有至少30%额外氢气用于加氢脱芳香烃、加氢脱氮、加氢脱硫、加氢裂解或所有这些。在一个或多个实施例中,加氢处理的混合物12包括比进料流11更多的氢气。
30.加氢处理反应器100可以在对加氢脱金属、加氢脱芳香烃、加氢脱氮、加氢脱硫、加氢裂解或其组合有效的参数下操作。举例来说,在一些实施例中,加氢处理反应器100可以在300℃到450℃的温度下操作。其它温度范围包括300℃到330℃、300℃到350℃、320℃到360℃、340℃到380℃、360℃到400℃、380℃到420℃、400℃到430℃和420℃到450℃。在一些实施例中,加氢处理反应器100可以在30到200巴的氢分压下操作。其它氢分压范围包括30到60巴、30到100巴、50到100巴、75到125巴、100到150巴、125到175巴和150到200巴。在一些实施例中,加氢处理反应器100的液时空速(lhsv)是0.1到2.0h-1
。其它lhsv范围包括0.1到0.5h-1
、0.5到1.0h-1
、1.0到1.5h-1
和1.5到2.0h-1
。
31.认为各种组合物适用于加氢处理催化剂。在一个或多个实施例中,加氢处理催化剂包含来自国际纯粹与应用化学联合会(iupac)周期表的第8到10族的至少一种金属,例如,fe、co、ni或其组合。此外,加氢处理催化剂可以包括来自iupac周期表的第6族的至少一种金属,例如,mo、w或其组合。预期各种载体材料是适合的。举例来说,载体可以包含氧化铝(al2o3)。
32.在某些实施例中,加氢脱金属催化剂可以负载于载体材料上。在一些实施例中,载体材料包括氧化铝。在某些实施例中,加氢脱金属催化剂可以包括γ氧化铝载体材料上的金属催化剂,表面积为140到240平方米/克(m2/g)。其它表面积范围包括140到160m2/g、160
到180m2/g、180到200m2/g、200到220m2/g和220到240m2/g。这种催化剂可以具有极高孔隙体积,例如,超过1厘米3/克(cm3/g)。孔隙大小本身通常主要是大孔(macroporous)的,其是大于75微米(μm)的孔隙。这是为了提供催化剂表面和任选地掺杂剂上金属吸收的大容量。催化剂表面上的活性金属可以包含ni和mo的硫化物,其比率为ni/ni mo《0.15。加氢脱金属催化剂上的ni浓度低于其它催化剂,因为预期一些ni和钒(v)在去除期间从进料本身沉积,充当催化剂。使用的掺杂剂可以是磷(p)、硼(b)、硅(si)和卤素中的一种或多种。在某些实施例中,催化剂可以呈氧化铝挤出物或氧化铝珠粒的形式。在其它实施例中,氧化铝珠粒用于促进催化剂加氢脱金属层在反应器中的卸载,因为金属吸收在层顶部的范围在30%到100%之间。
33.在某些实施例中,加氢处理反应器100包括中间催化剂。中间催化剂还可以用于进行加氢脱金属与加氢脱硫或另一加氢处理功能之间的转变。在一些实施例中,中间催化剂可以包括在单独反应容器(未展示)或分离区中。在一些实施例中,中间催化剂包括在加氢脱金属催化剂中。举例来说,中间催化剂可以包括在加氢金属化催化剂层中。在一些实施例中,中间催化剂包括在加氢脱硫催化剂中。举例来说,中间催化剂可以包括在加氢脱硫催化剂层中。在某些实施例中,中间催化剂包括在单独催化剂层中。举例来说,加氢脱金属催化剂、中间催化剂和加氢脱硫催化剂包括在单独催化剂层中。在一些实施例中,中间催化剂可以负载于载体材料上,在一个实施例中,所述载体材料可以包括氧化铝。中间催化剂可以包括中间金属负载量和孔隙大小分布。催化剂可以包括呈挤出物形式的氧化铝基载体,任选地至少一种来自第6族的催化金属(例如,mo、w或其组合)或至少一种来自第8到10族的催化金属(例如,ni、co或其组合)或其组合。中间催化剂还可以任选地含有至少一种选自b、p、si和卤素的掺杂剂。物理特性包括140到200m2/g的表面积。其它表面积范围包括140到160m2/g、160到180m2/g或180到200m2/g。物理特性还包括至少0.6cm3/g的孔隙体积。物理特性进一步包括为中孔(mesoporous)并且在12到50纳米(nm)范围内的孔隙。其它范围包括12到20nm、20到30nm、30到40nm或40到50nm。
34.加氢处理反应器100还可以包括加氢脱硫催化剂。在一些实施例中,加氢脱硫催化剂可以包括在单独反应容器(未展示)或分离区中。举例来说,加氢脱硫催化剂可以包括在与其它催化剂层分开的催化剂层中。在某些实施例中,加氢脱金属催化剂、中间催化剂和加氢脱硫催化剂包括在单独催化剂层中。在某些实施例中,加氢脱金属催化剂可以负载于载体材料上。在一些实施例中,载体材料包括氧化铝。在一些实施例中,加氢脱硫催化剂可以包括具有氧化铝基载体材料的那些,其表面积朝加氢脱金属范围的上端,例如范围为180到240m2/g。其它范围包括180到195m2/g、195到210m2/g、210到225m2/g或225到240m2/g。这需要较大的加氢脱硫表面,导致相对较小的孔隙体积,例如小于1cm3/g。加氢脱硫催化剂含有至少一种来自第6族的元素,如mo;和至少一种来自第8到10族的元素,如ni。催化剂还包含至少一种选自b、p、si和卤素的掺杂剂。在某些实施例中,钴用于提供相对提高的脱硫水平。随着所需活性的增加,活性相的金属负载量增加,使得ni/ni mo的摩尔比在0.1到0.3范围内,并且(co ni)/mo摩尔比在0.25到0.85范围内。
35.在某些实施例中,加氢处理反应器100可以包括设计成进行进料氢化(而不是加氢脱硫的主要功能)的催化剂。在其它实施例中,催化剂可以包括在单独反应容器(未展示)或分离区或与其它催化剂层分开的催化剂层中。在某些实施例中,最终催化剂可以负载于载
体材料上。在某些实施例中,载体材料可以包括氧化铝。最终催化剂可以由ni促进。物理特性包括朝向范围的较高端的表面积,例如180到240m2/g。其它范围包括180到195m2/g、195到210m2/g、210到225m2/g和225到240m2/g。这需要增加的表面进行氢化,导致相对较小的孔隙体积,例如小于1cm3/g。
36.再次参考图1到4,随后可以将加氢处理的混合物12传递到至少一个蒸汽裂解器110,所述蒸汽裂解器包含在700℃到900℃的温度下操作的对流段112,以产生加热的加氢处理的混合物14。其它适合的温度范围可以包括700℃到750℃、750℃到800℃、800℃到850℃或850℃到900℃。还将蒸汽添加到对流段112,以在加热的加氢处理的混合物14中产生较高沸点馏分和较低沸点馏分。因此,加热的加氢处理的混合物14可以包含较高沸点馏分和较低沸点馏分以用于后续分离。
37.在另一实施例中,蒸汽裂解器110可以包含在对流段112下游的重质残留物排出段114。设想了重质残留物排出段114将加热的加氢处理的混合物14分离成较低沸点馏分16和较高沸点馏分18。如图1到4所示,较高沸点馏分18可以是从重质残留物排出段114的底部排放的液体流,而较低沸点馏分16是从重质残留物排出段114上的不同位置排放的蒸气流。任何适合的分离容器可以将加氢处理的混合物分成较低沸点馏分16和较高沸点馏分18。这种分离可以包括闪蒸容器或任何适合的蒸气-液体分离器。在一些实施例中,可以使用气液分离器、油液分离器、分馏器等。
38.如本技术中所使用,较高沸点馏分是沸点为至少500℃的含烃流,并且较低沸点馏分是沸点低于500℃的含烃流。在其它实施例中,较低沸点馏分是沸点范围低于540℃的含烃流,而较高沸点馏分是沸点范围高于540℃的含烃流。较低沸点馏分的特征和组成包括轻石脑油馏分、重石脑油馏分、煤油馏分、柴油馏分和沸点在370℃与540℃之间的气态油馏分。较高沸点馏分的特征和组成包括沸点高于540℃的减压渣油(vacuum residue)馏分。因此,较低沸点馏分包括比较高沸点馏分更高浓度的“《c
40
烃”(具有少于40个碳原子的烃),而较高沸点馏分具有比较低沸点馏分更高浓度的“》c
40”烃(具有多于40个碳原子的烃)。另外,较高沸点馏分可以包括比较低沸点馏分更大浓度的芳香烃。
39.在一些实施例中,较高沸点馏分18可以含有减压渣油。较高沸点馏分18可以含有固体物质。在一些实施例中,较高沸点馏分18可以含有产生灰分的组分,如天然或合成氧化物。举例来说,较高沸点馏分18可以含有si、al、fe、ca、mg、p、k、na、s、ti或这些的组合的天然和合成氧化物。不受任何具体理论束缚,较高沸点馏分18中存在固体可以保护反应器壁。
40.虽然图1到4描绘了在分离方法中使用的重质残留物排出段114,但可以通过其它机制将加热的加氢处理的混合物14分离成较低沸点馏分和较高沸点馏分。举例来说,在图1到4中,重质残留物排出段114被描绘为与对流段112分开的容器;然而,设想了对流段112可以在将加氢处理的混合物12预热之后,将加热的加氢处理的混合物14分离成较低沸点馏分和较高沸点馏分。
41.如图1到4所示,将较低沸点馏分16传递到对流段112下游的热解段116,以产生包含烯烃和芳香烃的热解流出物20。作为蒸汽裂解器110的一部分的热解段116在可有效地将较低沸点馏分16裂解成热解流出物20的参数下操作。热解流出物20可以包括烯烃(包括乙烯、丙烯、丁烯和丁二烯)、芳香烃(包括苯、甲苯和二甲苯)和热解汽油。此外,热解段116可以产生氢气,其可以再循环到加氢处理反应器100。
42.可以基于所需组成热解流出物来调节加工参数。举例来说,热解段116可以具有0.3:1到2:0.1的蒸汽与轻质馏分的比率。此外,热解段114可以具有0.05到2秒的反应停留时间。
43.再次参考图1到4,可以将热解流出物20进料到至少一个分离器120。分离器120将热解流出物20转化成一种或多种包含烯烃、芳香烃或其组合的产物流。在一些实施例中,一种或多种产物流可以在热解燃料油27中包括btx(苯、甲苯和二甲苯)。在图1的实施例中,分离器120可以产生甲烷21、乙烯和乙烷22、丙烯和丙烷23、丁二烯24、混合丁烯25、热解汽油26和热解燃料油27。在一些实施例中,乙烷和丙烷可以再循环回到蒸汽裂解器110中,并且进一步转化成乙烯和丙烯。
44.另外,如图2和3所示,分离器120进一步产生另一氢气流28,其可以再循环回以便与原油5混合。在具体实施例中,将氢气流28传递到氢气纯化单元140以产生经处理的氢气流40。随后将经处理的氢气流40转移以便与原油5混合。如图2和3的实施例所示,进料流211包含经处理的氢气流40和来自气化炉130的氢气32。这些分离器产物流出于说明而展示,并且不应被理解为分离器120中产生的唯一产物流。
45.设想了分离器120的各种容器。在某些实施例中,分离器120可以包含闪蒸容器、分馏器、蒸馏容器或其组合。在一些实施例中,分离器120可以包括一个或多个闪蒸容器。在某些实施例中,闪蒸容器是闪蒸罐。在一些实施例中,分离器120可以包括一个或多个蒸馏容器。蒸馏容器可以是蒸馏塔,如真空蒸馏塔。此外,分离器120的另外实施例可以包括气液分离器、油液分离器或其组合。
46.再次参考图1到4的系统实施例,将较高沸点馏分18进料到在至少900℃的温度下操作的气化炉130。在一个或多个实施例中,气化炉130可以在大于或等于900℃(如900℃到1700℃)的温度和20到100巴的氢分压下操作。此外,气化炉130可以以0.3:1到10:0.1的氧气与碳的比率和0.1:1到10:0.1的蒸汽与碳的比率操作。
47.在一些实施例中,气化炉130可以含有移动床系统、流化床系统、夹带流系统或这些中任一种的组合。气化炉130可以包括折射壁或膜,其可以帮助隔绝气化炉130。
48.气化炉130产生氢气32,其再循环以便在加氢处理反应器100的上游与原油5混合。不受理论束缚,来自气化炉130的这种氢气32有助于使本系统在氢气需求方面能够自给自足。如本技术中所使用,“自给自足”意思指本系统为加氢处理反应器产生足够的氢气,使得不持续需要新鲜氢气进料10。在一些实施例中,可以将蒸汽38和氧气39供应到气化炉130。气化炉还可以产生一氧化碳30和加热的流31以及氢气32。
49.如图2和3所示,加氢处理反应器100的氢气需求由分离器120和气化炉130供应,其各自产生可以再循环以便与原油5混合的氢气28、32。在一些实施例中,可以将由分离器120产生的氢气28传递到纯化单元140以便进行进一步提质和纯化步骤。随后可以将经处理的氢气40再循环以用于进料流211。在图3的实施例中,可以将分离器120中产生的热解燃料油27传递到气化炉130,因此气化炉130可以将热解油的至少一部分转化成另外的氢气32。
50.气化是通过将含碳材料在蒸汽或可控制量的氧气存在下加热到高温以促进部分氧化,将含碳材料转化成更有价值的材料(主要是合成气)的方法。术语“合成气”是指合成气体,其为主要含有氢气、一氧化碳和一些二氧化碳的燃料气体混合物。可以包括氢气32、热量31或一氧化碳30中的一种或多种的合成气随后可以进一步加工以产生纯氢气、液体运
输燃料或发电。
51.如图4所示,在一些实施例中,可以在气化炉的下游使用水煤气变换反应器150以便进一步提质。如所展示,可以将可以包括氢气、二氧化碳和一氧化碳的气化炉合成气流出物131与水41一起传递到水煤气变换反应器150以允许进一步提质,同时还将蒸汽流出物133从气化炉130排放。水煤气变换反应器150可以在大于或等于150℃(如150℃到400℃)的温度下操作。水煤气变换反应器150可以在1到60巴的氢分压下操作。在一些实施例中,水煤气变换反应器150可以含有5:1到3:1的水与一氧化碳的摩尔比。在其它实施例中,气化炉130可以含有多个水煤气变换反应器,以将一氧化碳转化成二氧化碳151和额外的氢气132,其可以再循环回到进料流11中。虽然为方便起见描绘为分开的二氧化碳151和氢气132的流,但设想了还可以在水煤气变换反应器150、气化炉130或两者的下游利用其它分离单元来分离合成气组分。
52.本发明实施例的特征将在下面的实例中进一步加以说明。
53.实例
54.实例1
55.实例1是使用spyro软件进行的中试工厂(pilot plant)模拟。如以下数据所示,模拟结果表明,当使用提质的阿拉伯轻质原油(arab light crude oil)作为进料时,蒸汽裂解单元的石化产品产率高,并且形成的焦炭少。
56.如下表1列出了在进料到加氢处理反应器之前和在加氢处理反应器中进行加氢处理之后的阿拉伯轻质原油的特性。粗调节在380到400℃的反应温度下进行,液时空速(lhsv)为0.2到0.5h-1
,氢分压为150巴,并且h2/油比为1200v/v。
57.表1
[0058][0059]
表2列出了在蒸汽裂解器的对流段中将提质的阿拉伯轻质原油预热并且在重质残留物排出段中分离后,排出的较高沸点馏分的特性。所述蒸汽裂解器在840℃的盘管出口(coil out)温度和1.8巴表压的盘管出口压力下操作,其中蒸汽与油的比率(以重量计)为1:1并且停留时间为0.2秒。
[0060]
表2
[0061][0062]
表3列出了当将排出的较高沸点馏分进料到气化炉时产生的氢气。将1000kg减压渣油作为加压进料引入到气化区中的气化反应器中(如图1所示)。表1包括减压渣油进料的元素组成。气化反应器在1045℃和30巴下操作。蒸汽与碳的重量比为0.6:1。氧气与碳的重量比为1:1。将减压渣油馏分部分氧化以产生氢气、一氧化碳和动力。将氢气和一氧化碳作为热的粗合成气体回收,并且传送到水煤气变换反应容器中以提高氢气产率。水煤气变换反应在318℃和1巴下进行。蒸汽与一氧化碳的摩尔比为3:1。
[0063]
表3
[0064] 气化炉,输入(kg)气化炉,输出(kg)进料1000 氧气1000 ch
4 6.5h
2 271.3co 92.4co
2 3153.9h2o2175648.5其它* 2.4
[0065]
*h2s、cos、n2、ar、nh3[0066]
表4列出了来自分离器的石化产品产率,所述分离器将以下芳香烃和烯烃从热解流出物中分离出来。将加氢处理的提质产品在中试工厂单元中进行蒸汽裂解。将液态油进料和蒸汽引入到反应器中。反应条件如下:压力=1.8巴,油/蒸汽比=1kg/kg,反应温度840℃,油质量流动速率:3.6千克/小时。在冷却裂解流出物之前,取得样品以便通过全面二维gc(gc
×
gc)进行在线c5 分析。借助分离罐和漩涡分离器将液体与焦油从冷却器出口分离。随后取出一部分产物气体用于在线c4分析。分离容器和漩涡分离器连接到用于收集热解燃料油的容器。
[0067]
表4
[0068]
产物产率,wt%氢气0.6甲烷11.5乙烯25.7丙烯13.3丁二烯5.2丁烯3.6苯5.8甲苯3.4热解汽油10.6热解燃料油10.1燃料油8.1
[0069]
实例2
[0070]
实例2包括在不同加氢处理条件下进行的加氢处理器(hydroprocessor)模拟的结果。表5中列出了进料。
[0071]
表5
[0072][0073][0074]
表6列出了各种加氢处理条件下的加氢处理结果。
[0075]
表6
[0076][0077]
将总液体样品ht-5-390分馏成《540℃和》540℃的馏分。《540℃的馏分命名为ht-5-390(《540)。选择ht-5-390(《540)和ht-2-390液体样品用于中试工厂蒸汽裂解测试。结果总结在表7中。
[0078]
表7
[0079]
进料ht-2-390ht-5-390(《540)操作条件
ꢀꢀ
油/蒸汽比,kg/kg11反应器温度,℃840840反应器压力,巴1.81.8产率,wt%
ꢀꢀ
h20.80.7甲烷12.211.3乙烷32.7乙烯25.123.2丙烷0.40.4丙烯12.311.6丁烷0.10.1丁烯3.33.21,3-c4h64.54.6苯3.44.8甲苯1.64二甲苯0.31.1热解汽油10.317.8热解燃料油14.812.8燃料油11.810.2
[0080]
实例3
[0081]
实例3与气化方法有关,并且同样是基于大量商业气化数据使用内部开发软件进行的中试工厂模拟。对于实例3,将1000kg减压渣油作为加压进料引入到气化区中的气化反应器中(如图4所示)。表8包括减压渣油进料的元素组成。气化反应器在1045℃和30巴下操作。蒸汽与碳的重量比为0.6:1。氧气与碳的重量比为1:1。将减压渣油馏分部分氧化以产生氢气、一氧化碳和动力。将氢气和一氧化碳作为热的粗合成气体回收,并且传送到水煤气变换反应容器中以提高氢气产率。水煤气变换反应在318℃和1巴下进行。蒸汽与一氧化碳的摩尔比为3:1。产物产率总结在表9中。
[0082]
表8
[0083]
减压渣油组分wt%c87.3h12.45s0.05n0.1o0灰分0
[0084]
表8展示引入到气化反应器中的减压渣油馏分的进料特性。分子量估计为800kg/kg-mol。
[0085]
表9
[0086][0087]
如表9所示,在水煤气变换反应后,由1000kg的减压渣油产生了将近278kg的氢气。
[0088]
对于所属领域技术人员应显而易见的是,可以在不脱离所要求保护的主题的精神和范围的情况下对所描述的实施例进行各种修改。因此,希望本说明书涵盖对各种所描述的实施例的修改和变化,其条件是此类修改和变化在所附权利要求书和其等效物的范围内。
[0089]
根据本公开的第一方面,用于由原油产生烯族和芳香族石化产品的方法,所述方法可以包含将氢气与原油混合以产生包含氢气和原油的进料流;将原油与氢气混合物传递到加氢处理反应器中,所述加氢处理反应器在300℃到450℃的温度和30到200巴的氢分压下操作,所述加氢处理反应器包含加氢处理催化剂,其由原油与氢气混合物产生加氢处理的混合物;将加氢处理的混合物传递到至少一个蒸汽裂解器,所述蒸汽裂解器包含在700℃到900℃的温度下操作的对流段,以产生加热的加氢处理的混合物;将加热的加氢处理的混合物分离成较低沸点馏分和较高沸点馏分;将较低沸点馏分传递到对流段下游的蒸汽裂解器的热解段,以产生包含烯烃和芳香烃的热解流出物;将热解流出物输送到至少一个分离器,其中分离器将热解流出物转化成一种或多种产物流,其包含烯烃、芳香烃或其组合;将较高沸点馏分传递到在至少900℃的温度下操作的气化炉中,其中气化炉产生氢气;以及再循环气化炉中产生的氢气,以便在加氢处理反应器的上游与原油混合。
[0090]
本公开的第二方面可以包括第一方面,其中加氢处理催化剂包括以下中的一种或多种:加氢脱金属催化剂、加氢处理催化剂、加氢脱芳香烃化催化剂、加氢脱氮催化剂、加氢脱硫催化剂或两者。
[0091]
本公开的第三方面可以包括第二方面,其中加氢脱金属催化剂安置在加氢处理催化剂上游的催化剂床中。
[0092]
本公开的第四方面可以包括前述方面中的任一个,其中加氢处理催化剂可以包含来自国际纯粹与应用化学联合会(iupac)周期表的第8到10族的至少一种金属;和来自iupac周期表的第6族的至少一种金属;和至少一种载体材料。
[0093]
本公开的第五方面可以包括第四方面,其中加氢处理催化剂包含fe、co、ni、mo、w或其组合。
[0094]
本公开的第六方面可以包括第四方面,其中加氢处理催化剂包含负载在包含氧化铝(al2o3)的载体材料上的mo和w。
[0095]
本公开的第七方面可以包括前述方面中的任一个,其中加氢处理催化剂使原油与氢气混合物脱硫并且脱金属,以产生加氢处理的混合物。
[0096]
本公开的第八方面可以包括前述方面中的任一个,其进一步包含在对流段下游的重质残留物排出段,其中所述重质残留物排出段将加热的加氢处理的混合物分离成较低沸点馏分和较高沸点馏分。
[0097]
本公开的第九方面可以包括前述方面中的任一个,其中热解流出物进一步包含氢气,并且其中与进料流混合的氢气包含来自热解流出物的氢气。
[0098]
本公开的第十方面可以包括前述方面中的任一个,其中裂解流出物的芳香烃包含苯、甲苯和二甲苯中的一种或多种。
[0099]
本公开的第十一方面可以包括前述方面中的任一个,其中气化炉在900℃到1700℃的温度、20到100巴的氢分压或两者下操作。
[0100]
本公开的第十二方面可以包括前述方面中的任一个,其中气化炉的氧气与碳的体积比为0.3:1到10:0.1,蒸汽与碳的体积比为0.1:1到10:0.1,或具有这两种比率。
[0101]
本公开的第十三方面可以包括前述方面中的任一个,其中气化炉包含移动床系统、流化床系统、夹带流系统或其组合。
[0102]
本公开的第十四方面可以包括前述方面中的任一个,其中传递到气化炉的较高沸点馏分包含固体物质。
[0103]
本公开的第十五方面可以包括第十四方面,其中固体物质包含产生灰分的组分,所述产生灰分的组分选自由以下的天然和合成氧化物组成的组:si、al、fe、ca、mg、p、k、na、s、ti和其组合。
[0104]
本公开的第十六方面可以包括前述方面中的任一个,其进一步包含将分离器中产生的氢气传递到氢气纯化单元,其中氢气纯化产生经处理的氢气流,和传递经处理的氢气流以便在加氢处理反应器的上游与原油混合。
[0105]
本公开的第十七方面可以包括前述方面中的任一个,其进一步包含气液分离器、油液分离器、分馏器或其组合。
[0106]
本公开的第十八方面可以包括前述方面中的任一个,其进一步包含将分离器中产生的热解油传递到气化炉,其中气化炉将热解油的一部分转化成氢气。
[0107]
本公开的第十九方面可以包括前述方面中的任一个,其中分离器包含闪蒸容器、蒸馏容器或其组合。
[0108]
本公开的第二十方面可以包括前述方面中的任一个,其中原油流具有10
°
到40
°
的api比重(
°
)。
[0109]
本公开的第二十一方面可以包括前述方面中的任一个,其进一步包含在与氢气流混合之前将原油预热到至少300℃的温度。
[0110]
本公开的第二十二方面可以包括前述方面中的任一个,其中较高沸点馏分包含减压渣油。
[0111]
本公开的第二十三方面可以包括前述方面中的任一个,其中气化炉产生氢气、一氧化碳、热量或其组合。
[0112]
本公开的第二十四方面可以包括第二十三方面,其进一步包含回收氢气或一氧化碳中的至少一种作为合成气;将合成气传递到热交换器以产生蒸汽和冷却的合成气;回收冷却的合成气;和将蒸汽传递到涡轮机以发电。
[0113]
本公开的第二十五方面可以包括第二十四方面,其进一步包含将冷却的合成气传递到水煤气变换反应器,其中水煤气变换反应器在150℃到400℃的温度、1到60巴的压力或两者下操作。
[0114]
本公开的第二十六方面可以包括第二十五方面,其中水煤气变换反应器包含5:1到3:1的水与一氧化碳摩尔比。
[0115]
根据本公开的第二十七方面,一种用于由原油产生石化产品的方法可以包括前述方面中的任一个,并且可以包括将原油和氢气传递到加氢处理反应器中,加氢处理反应器包含一种或多种加氢处理催化剂,其产生加氢处理的油;将加氢处理的油分离成较低沸点馏分和较高沸点馏分;将较低沸点馏分传递到蒸汽裂解器的热解段,以产生包含烯烃、芳香烃或两者的热解流出物;将较高沸点馏分传递到气化炉,其中气化炉产生氢气;和将由气化炉产生的氢气的至少一部分传递到加氢处理反应器。
[0116]
本公开的第二十八方面可以包括第一方面,其中将原油与氢气组合以形成混合流,所述混合流被传递到加氢处理反应器中。
[0117]
本公开的第二十九方面可以包括前述方面中的任一个,其中加氢处理反应器在300℃到450℃的温度和30到200巴的氢分压下操作。
[0118]
本公开的第三十方面可以包括前述方面中的任一个,其中所述方法进一步包括将加氢处理的油传递到蒸汽裂解器,所述蒸汽裂解器包含在700℃到900℃的温度下操作的对流段,以产生加热的加氢处理的油。
[0119]
本公开的第三十一方面可以包括前述方面中的任一个,其中所述方法进一步包括将热解流出物输送到至少一个分离器,其中所述分离器将热解流出物转化成一种或多种包含烯烃、芳香烃或两者的产物流。
[0120]
本公开的第三十二方面可以包括前述方面中的任一个,其中气化炉在至少900℃的温度下操作。
[0121]
本公开的第三十三方面可以包括前述方面中的任一个,其中加氢处理反应器包含加氢脱金属催化剂、加氢裂解催化剂、加氢脱芳香烃催化剂、加氢脱氮催化剂或加氢脱硫催化剂中的一种或多种。
[0122]
本公开的第三十四方面可以包括前述方面中的任一个,其中加氢处理反应器包含安置在其它加氢处理催化剂上游的加氢脱金属催化剂。
[0123]
本公开的第三十五方面可以包括前述方面中的任一个,其中一种或多种加氢处理催化剂降低原油中硫和金属的含量。
[0124]
本公开的第三十六方面可以包括前述方面中的任一个,其中热解流出物进一步包含氢气,所述氢气被传递到加氢处理反应器。
[0125]
本公开的第三十七方面可以包括前述方面中的任一个,其中热解流出物包含选自苯、甲苯或二甲苯中的一种或多种的芳香烃。
[0126]
本公开的第三十八方面可以包括前述方面中的任一个,其中气化炉包含移动床系统、流化床系统、夹带流系统或其组合。
[0127]
本公开的第三十九方面可以包括前述方面中的任一个,其中较高沸点馏分包含固体物质。
[0128]
本公开的第四十方面可以包括前述方面中的任一个,其中固体物质包含产生灰分的组分,所述产生灰分的组分选自由以下的天然和合成氧化物组成的组:si、al、fe、ca、mg、p、k、na、s、ti或其组合。
[0129]
本公开的第四十一方面可以包括前述方面中的任一个,其中所述方法进一步包括将分离器中产生的氢气传递到氢气纯化单元,其中氢气纯化产生经处理的氢气流;和传递经处理的氢气流以便在加氢处理反应器的上游与原油混合。
[0130]
本公开的第四十二方面可以包括前述方面中的任一个,其中所述方法进一步包括将分离器中产生的热解油传递到气化炉,其中气化炉将热解油的至少一部分转化成氢气。
[0131]
本公开的第四十三方面可以包括前述方面中的任一个,其中原油流具有10度到40度的api比重。
[0132]
本公开的第四十四方面可以包括前述方面中的任一个,其进一步包含在原油进入加氢处理反应器之前,将原油预热到至少300℃的温度。
[0133]
本公开的第四十五方面可以包括前述方面中的任一个,其中较高沸点馏分包含减压渣油。
[0134]
本公开的第四十六方面可以包括前述方面中的任一个,其中气化炉产生氢气、一氧化碳、加热的流或其组合。
再多了解一些
本文用于创业者技术爱好者查询,仅供学习研究,如用于商业用途,请联系技术所有人。