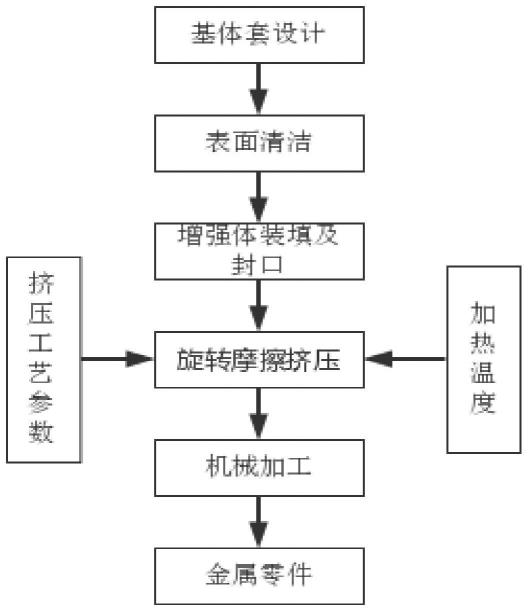
:
1.本发明涉及复合材料制备和成型领域,尤其涉及一种金属基复合材料制备和成型一体化的方法。
背景技术:
2.复合材料是由两种或两种以上物理和化学性质不同的物质组合而成的一种多相固体材料。复合材料不仅保持各组分材料性能的优点,而且通过各组分性能的互补和关联可以获得单一组成材料所不能达到的综合性能,扩大材料的应用范围。由于复合材料具有重量轻、强度高、加工成型方便、弹性优良、耐化学腐蚀和耐候性好等特点,已逐步取代木材及金属合金,广泛应用于航空航天、汽车、电子电气、建筑、健身器材等领域,在近几年更是得到了飞速发展。
3.目前金属基复合材料制造工艺面临着加工温度高、性能波动、成本高以及制造工艺中的金属基复合材料中的金属与增强物的相容性等问题。在复合材料制备过程中,为了确保基体的浸润性和流动性,需要采用很高的加工温度。然而高温往往会对增强材料造成损害。绝大多数的金属基复合材料的基体对增强材料浸润性差,有时根本不发生润湿现象。然而旋转摩擦挤压技术是一种新的合金化技术,该技术是基于搅拌摩擦焊的技术上研发出来的。该方法加工温度没有达到材料的熔化温度,避免了增强材料在高温环境受到损害。而加工过程是旋转的,对加工区域起搅拌作用,增强了材料的流动性。并且由于是挤压成型,材料的晶粒细小,组织性能优异。金属基材料的成型方法有很多,如手糊成型工艺、rtm成型技术、模压成型及层压工艺等,各个成型方法都有各自的优缺点。目前如何克服金属基复合材料制造和成型工艺面临的问题,是实现金属基复合材料广泛应用的主要问题。
4.复合材料的制备和成型技术都是影响金属基复合材料迅速发展和广泛应用的关键问题。目前,国内外学者对于复合材料的研究主要关注于如何开发有效的制造方法或者成型方法,然而关于复合材料制备和成型一体化的研究少之又少。复合材料的制备和成型一体化技术打破了以往先制备复合材料后再进行成型加工的方法,避免了复合材料在后续成型过程中对晶体结构的破坏和缺陷的引入,同时一体化理念也可以简化操作过程和降低操作成本,更容易实现复合材料的广泛应用。本发明采用自制模具,基于旋转摩擦挤压的方法,实现了金属基复合材料制备和成型一体化的方法。
技术实现要素:
5.本发明是采用自行设计的制备和成型一体化模具,基于旋转摩擦挤压的方法,通过调控旋转摩擦挤压的工艺参数和辅助热源来共同控制零件的组织及性能。
6.本发明的一种金属基复合材料制备和成型一体化的方法,其步骤为:
7.(1)根据要加入增强体的含量设计一个母材基体套,并将其表面清洁处理去除氧化膜和油污等杂质。
8.(2)将增强体干燥后装填入基体套中并压实,然后将基体套进行封口处理。
9.(3)把自行设计的制备和成型一体化模具和后续封口的端面作为加工面的基体套固定在机床上,将模具上加热装置的温度控制在一个适当温度范围,采用旋转摩擦挤压的方法来实现金属基复合材料的制备和成型一体化过程。
10.(4)将零件从模具中取出后进行切割和打磨等机械加工后得到一个组织和性能良好的金属零件。
11.所述的制备和成型一体化方法,其特征在于所述母材基体套是由若干个长度相同,内径和外径都不同,且共用一个封闭端面的同中心轴盲孔圆柱组成的基体套;
12.所述的制备和成型一体化方法,其特征在于所述封口处理是采用摩擦焊的方法实现的。
13.所述加热装置为电磁感应加热线圈,作用在于让材料成型过程中保持粘塑性状态。
14.与现有技术相比,本发明具有如下优点:
15.1)本方法实现了制备和成型一体化,打破了以往先制备复合材料后再进行成型加工的方法,避免了复合材料在后续的成型过程中对晶体结构的破坏和缺陷的引入。
16.2)本方法由于是旋转挤压,对加工区域起到搅拌的作用,使增强体和基体能够混合均匀,克服了一般复合材料由于增强体含量的增加而引起的偏析和团聚现象。
17.3)本方法操作简单,且成本较低。
附图说明
18.图1为本发明的一种金属基复合材料制备和成型一体化的工艺流程图。
具体实施方式
19.为了更加清晰的表述本发明的制造优点,下面结合实施例对本发明作进一步详细说明,以下所述的实施例在以本发明技术方案为前提的条件下进行实施,但本发明的保护范围却不限于以下所述的实施例。
20.本实施例基体材料采用5038铝合金、增强体采用ni粉末。
21.采用长度为100mm、孔深70mm的5083铝合金,一个内径为10mm、外径为16mm,另一个内径为2mm、外径为9mm,且共用一个封闭端面的同中心轴盲孔圆柱组成的基体套,增强体的体积分数为5%。将其表面用砂纸打磨,并用丙酮超声清洗去除氧化膜和油污等杂质,最后进行干燥处理。
22.将ni粉用干燥箱烘干后,装填入基体套中并压实,然后将基体套与另一5083铝合金用旋转速度750rpm、下压速度20mm/min、下压量为1mm的摩擦焊,将基体套端口处的开口封闭,之后先用砂轮将端口的卷边打磨掉再用砂纸打磨干净。
23.把自行设计的制备和成型一体化模具和后续封口的端面作为加工面的基体套固定在机床上,将模具上加热装置的温度控制在380~450℃,采用旋转速度600rpm、下压速度15mm/min旋转摩擦挤压的方法来实现金属基复合材料的制备和成型。
24.将零件从模具中取出后用线切割的方式把零件的加工端口切除,并用砂纸将零件表面打磨光滑。
技术特征:
1.一种金属基复合材料制备和成型一体化的方法,其步骤包括:(1)根据要加入增强体的含量设计一个母材基体套,并将其表面清洁处理去除氧化膜和油污等杂质;(2)将增强体干燥后装填入基体套中并压实,然后将基体套进行封口处理;(3)把自行设计的制备和成型一体化模具和后续封口的端面作为加工面的基体套固定在机床上,将模具上加热装置的温度控制在一个适当温度范围,采用旋转摩擦挤压的方法来实现金属基复合材料的制备和成型一体化过程;(4)将零件从模具中取出后进行切割和打磨等机械加工后得到一个组织和性能良好的金属零件。2.根据权利要求1所述的制备和成型一体化方法,其特征在于所述母材基体套是由若干个长度相同,内径和外径都不同,且共用一个封闭端面的同中心轴盲孔圆柱组成的基体套。3.根据权利要求1所述的制备和成型一体化方法,其特征在于所述封口处理是采用摩擦焊的方法实现的。4.根据权利要求1所述的制备和成型一体化方法,其特征在于所述加热装置为电磁感应加热线圈,作用在于让材料成型过程中保持粘塑性状态。
技术总结
本发明公开了一种金属基复合材料制备和成型一体化的方法,采用自行设计的制备和成型一体化模具,基于旋转摩擦挤压的方法,通过调控旋转摩擦挤压的工艺参数和辅助热源来共同控制零件的组织及性能。该技术可以实现增强体对基体性能增强的同时,完成复合材料成型,打破了以往先制备复合材料再进行成型加工的方法,避免了材料在成型过程中对晶体结构破坏和缺陷引入。缺陷引入。
技术研发人员:钱锦文 余剑飞 欧艳 肖逸锋 李冰阳 吴靓 张乾坤
受保护的技术使用者:湘潭大学
技术研发日:2022.06.16
技术公布日:2022/9/13
再多了解一些
本文用于企业家、创业者技术爱好者查询,结果仅供参考。