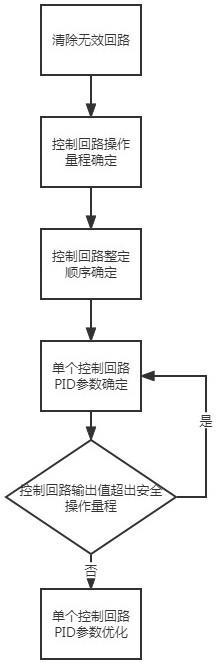
一种基于pid的催化装置整定方法
技术领域
1.本发明涉及石油化工领域,尤其涉及一种基于pid的催化装置整定方法。
背景技术:
2.催化装置是炼油化工厂的核心生产装置,作为炼油二次加工装置,在一定的生产工况条件下,将重质馏分油与高温催化剂接触,从而将原料转化为轻质油品的生产加工工艺。催化装置主要产品为汽油、轻柴油和液化气。我国车用汽油用量的80%,由催化装置生产,然而催化装置的自控率普遍较低,通常不足50%,严重影响了产品质量、产品收率,同时对安全生产也有较大隐患。
3.目前,全国催化装置超过100套,全部采用pid(proportional-integral-differential,比例—积分—微分) 控制器,但由于pid控制方法涉及自动化控制原理、工艺操作、电气仪表等专业,整定难度大、无统一标准方法,导致催化装置控制回路投用率低、控制回路性能差、维护难度大。
技术实现要素:
4.本发明的目的在于提供一种基于pid的催化装置整定方法,解决目前催化装置控制回路自动投用率低、控制回路性能差、控制回路难以维护的问题。
5.本发明的目的是通过以下技术手段实现的,一种基于pid的催化装置整定方法,包括以下步骤:s1、清除无效回路,将催化装置不存在的控制回路、仪表或设备故障对应的控制回路、停用或间歇使用的控制回路、工艺要求的控制回路排除;s2、控制回路操作量程确定,根据控制回路所在工艺要求,确定回路的安全操作量程;s3、控制回路整定顺序确定;s4、单个控制回路pid参数确定,根据s3中整定顺序逐个确定单个控制回路pid控制模块比例度p、积分时间ti、微分时间td,并根据s2中安全操作量程设定整定优化控制回路的操作上下限;s5、单个控制回路pid参数优化,单个控制回路pid控制模块比例度p、积分时间ti、微分时间td参数优化;s5.1将控制回路状态投入到闭合的控制系统中 ,根据s4所计算的结果 ,选出一个合适的 p、 ti 值作为起始值 ,将系统投入自动;s5.2 改变 p、 ti 设定值对控制系统施加一个干扰 ,观察判断控制曲线形状,若曲线不够理想 ,可改变 p或 ti ,再观察控制过程曲线 ,直到控制系统符合动态过程品质要求为止 ,这时的 p和 ti 就是最佳值。
6.所述s5后,还对整定前后催化装置有效自控率进行比较,从而确定优化效果,催化装置有效自控率rc = cc/ cv(公式3);
cv = ca
ꢀ–ꢀ
cn
ꢀ‑ꢀ
cf(公式1)cv: 催化装置有效控制回路数量;ca:dcs系统后端记录的催化装置控制回路总数;cn:dcs系统前端界面不存在的控制回路总数;cf:自动仪表或调节阀故障的控制回路总数;cc = cv
ꢀ–ꢀ
ce
ꢀ–ꢀ
cd
ꢀ–ꢀ
ci
ꢀ–ꢀ
cw(公式2)cc:催化装置具备自动投用条件的控制回路数量;ce:控制回路所控制的设备故障数量;cd:停用控制回路数量;ci:间歇使用控制回路数量,且当前状态为停用;cw:催化装置生产工艺要求控制回路手动条件数量。
7.所述s4中,若控制回路输出值超出安全操作量程,则重新确定该控制回路pid参数。
8.所述s4中,根据工程数据采样拟合曲线分析,比例度p、积分时间ti、微分时间td满足(公式4)ti = t(公式5)td = 0(公式6)其中:t:时间常数;τ:纯滞后时间;λ:闭环时间常数;k:比例增益;p:控制器比例度;ti:控制器积分时间;td:控制器微分时间。
9.所述s5中, 如果pid调节器是 pid 三作用方式 ,那么s5.2确定一个 td 值后 ,可把整定好的 p 和 ti 值减小再进行现场凑试 ,直到 p、 ti 和 td 取得最佳值为止,至此完成该控制回路pid整定。
10.所述s3中,控制回路整定优化顺序与工艺顺序一致,若是串级控制回路,则遵循先子回路后父回路的原则,若是分程控制回路,则遵循并行优化的原则。
11.本发明的有益效果在于:1、在考虑催化工艺过程,以及各控制回路的安全量程的基础上,对装置控制回路进行标准化整定,使得整定结果更适用于对应工艺的催化装置,在降低整定难度的同时,提高了整定效果,从而提高装置有效自控率,2、对整定后的参数进行优化,得到在整定的基础上得到更适合催化装置工作的参数。
附图说明
12.图1为基于pid的催化装置整定方法流程示意图;
图2为催化装置工序逻辑图;图3为pid控制器框图;图4为催化装置的控制回路一阶过程动态过程;图5为催化装置的流量控制回路一阶过程动态过程;图6为催化装置的压力控制回路一阶过程动态过程;以下将结合附图及实施例对本发明做进一步详细说明。
具体实施方式
13.【实施例1】如图1所示,一种基于pid的催化装置整定方法,包括以下步骤,s1、清除无效回路,将催化装置不存在的控制回路、仪表或设备故障对应的控制回路、停用或间歇使用的控制回路、工艺要求的控制回路排除;目前,炼油化工厂的有效自控率仅仅是已投用自控回路数量与总自控率的比率,并未考虑装置自身运行情况及工艺要求,从公式3可知,催化装置的有效自控率是将装置中不存在的控制回路、仪表或设备故障对应的控制回路、停用或间歇使用的控制回路、工艺要求的控制回路(如调节阀全开、全关、复杂联锁或自保等)排除在外,如此所得的装置自控率更接近装置生产实际情况,其中催化装置不存在的控制回路是指后台数据库中没有删除,但是实际上生产装置中已经删掉的回路;仪表或设备故障对应的控制回路,是指由于催化装置停工损失太大,只能隔一段时间才能停工维修,在非维修时间段,就算控制回路出现故障也无法停工去维修,因此要把这些故障但没法维修的回路排除掉;停用或间歇使用的控制回路,是指正常运行时不使用,只在开工或者停工时才用的控制回路;工艺要求的控制回路,其他回路可能会开50%,30%这种,但是部分回路只有开与关两种状态,做不到开50%这样,因此也就没有整定必要,这部分回路也排除。
14.s2、控制回路操作量程确定,根据控制回路所在工艺要求,确定回路的安全操作量程,s3、控制回路整定顺序确定;传统控制回路自动投用整定属于自动化控制领域,整定人员以自控专业为主,采用z-n法、试凑法、4:1临界震荡法等,均忽略控制回路所在工艺要求,本专利提供的整定方法须界定控制回路操作要求,设定回路安全量程、掌握控制回路工艺要求,工艺逻辑如图2所示,如:原料油与回炼油(回炼油浆)混合后进入催化一反应系统,经过催化剂作用,生成产品油气,油气进入分馏系统分离生成富气、粗汽油、轻柴油,粗汽油与压缩富气进入吸收稳定系统,通过逆向接触,形成产品干气、液化气与稳定汽油出厂销售,催化一反应系统内催化剂经过主风灼烧后产生的烟气,经热工系统内水取热后,再经脱硫脱硝单元处理外排大气。
15.所述s3中,控制回路整定优化顺序与工艺顺序一致,若是串级控制回路,则遵循先子回路后父回路的原则,若是分程控制回路,则遵循并行优化的原则。
16.按照工艺逻辑图2,油料和烟气分开整定,以催化-反应系统、分馏系统、吸收稳定
系统的顺序整定其中涉及油料的控制回路,以催化-反应系统、热工系统、脱硫脱硝单元的顺序整定涉及烟气的控制回路,三机系统不需要整定。
17.s4、单个控制回路pid参数确定,根据s3中整定顺序逐个确定单个控制回路pid控制模块比例度p、积分时间ti、微分时间td,并根据s2中安全操作量程设定整定优化控制回路的操作上下限;s5、单个控制回路pid参数优化,单个控制回路pid控制模块比例度p、积分时间ti、微分时间td参数优化;s5.1将控制回路状态投入到闭合的控制系统中 ,根据s4所计算的结果 ,选出一个合适的 p、 ti 值作为起始值 ,将系统投入自动。
18.s5.2 改变 p、 ti 设定值对控制系统施加一个干扰 ,观察判断控制曲线形状,若曲线不够理想 ,可改变 p或 ti ,再观察控制过程曲线 ,直到控制系统符合动态过程品质要求为止 ,这时的 p和 ti 就是最佳值。
19.所述s5后,还对整定前后催化装置有效自控率进行比较,从而确定优化效果,催化装置有效自控率rc = cc/ cv(公式3);cv = ca
ꢀ–ꢀ
cn
ꢀ‑ꢀ
cf(公式1)cv: 催化装置有效控制回路数量;ca:dcs系统后端记录的催化装置控制回路总数;cn:dcs系统前端界面不存在的控制回路总数;cf:自动仪表或调节阀故障的控制回路总数;cc = cv
ꢀ–ꢀ
ce
ꢀ–ꢀ
cd
ꢀ–ꢀ
ci
ꢀ–ꢀ
cw(公式2)cc:催化装置具备自动投用条件的控制回路数量;ce:控制回路所控制的设备故障数量;cd:停用控制回路数量;ci:间歇使用控制回路数量,且当前状态为停用;cw:催化装置生产工艺要求控制回路手动条件数量;催化装置全部自控回路整定优化工作,是对装置有效自控回路数量cv、具备投用自动的控制回路数量cc的重新梳理,根据公式1、2、3,根据整定前的数据可以得到整定前的旧自控率,根据整定后的数据可以得到整定优化后的新自控率,因此采用同样的根据公式1、2、3,可知装置整定优化前的旧自控率和整定优化后的新自控率rc,从而对此次全装置的整定优化工作做工作量鉴定等评估。如有效自控率从30%提升至92%,可以看出有了很明显的提高。
20.所述s4中,若控制回路输出值超出安全操作量程,则重新确定该控制回路pid参数。
21.若确定控制回路pid参数,即控制模块比例度p、积分时间ti、微分时间td后,若输出的波动值超了安全操作量程的上限,说明参数过大,减小后再次得到输出参数,直至输出值在安全操作量程内。
22.所述s4中,根据工程数据采样拟合曲线分析,比例度p、积分时间ti、微分时间td满足
(公式4)ti = t(公式5)td = 0(公式6)其中:t:时间常数;τ:纯滞后时间;λ:闭环时间常数;k:比例增益;p:控制器比例度;ti:控制器积分时间;td:控制器微分时间。
23.t:时间常数;τ:纯滞后时间;λ:闭环时间常数,通常为τ的整数倍;k:比例增益均为给定的值。
24.pid控制器框图如图3所示,催化装置的控制回路一阶过程动态如图4-6所示,图中时间常数t为设定值pv值达到设定值sp的63%,在此过程中纯滞后时间为τ,比例增益为k,k为控制器设定常数。根据工程数据采样拟合曲线分析,比例度p、积分时间ti、微分时间td满足:(公式4)ti = t(公式5)td = 0(公式6)通过公式4、5、6,对永坪炼油厂120万吨/年催化装置具备条件的自控进行比例度p、积分时间ti、微分时间td计算,对应比例度p、积分时间ti、微分时间td的取值范围如下表所示:
调节系统比例度p(%)积分时间ti(分)微分时间td(分)说明流量40-1000.1-10对象时间常数小,并有杂散扰动,p应大,ti较短,不必用微分。压力30-700.4-30对象滞后一般不大,p略小,ti略大,不用微分。液位20-801-50p小,ti较大,要求不高时可不用积分,不用微分。温度20-603-100.5-3对象容量滞后较大。p小,ti大,加微分作用。
所述s5中, 如果pid调节器是 pid 三作用方式 ,那么s5.2确定一个 td 值后 ,可把整定好的 p 和 ti 值减小再进行现场凑试 ,直到 p、 ti 和 td 取得最佳值为止,至此完成该控制回路pid整定。
25.如果调节器是 pid 三作用方式 ,那么在s5.2集成上加进微分作用。由于微分作用有抵制偏差变化的能力 ,所以确定一个 td 值后 ,可把整定好的 p 和 ti 值减小一点再进行现场凑试。
26.具体的,将控制回路状态投入到闭合的控制系统中 ,根据根据s4所计算的结果 ,选出一个合适的 p、 ti 值作为起始值 ,将系统投入自动。以加热炉出口温度调节控制回路为例,其pv量程为0-100,比例增益k为1,手动状态下阶跃测试,pv值由50阶跃至55,测量所得,经过60秒的时间滞后(即滞后时间τ),sp值发生变化,经过120秒(即时间常数t)sp值到达pv值的63.21%,取闭环时间常数λ为3τ,带入公式4计算所得p为30,ti为120秒,即2分
钟,td取值为0。
27.通过改变设定值对控制系统施加一个干扰 ,现场观察判断控制曲线形状。若曲线不够理想或无法判断是否有优化空间,则围绕s5.1所得的p值、ti值上下调整,如上例,ti值保持不变,p值调整为25、35,再观察控制过程曲发现有上调优化空间,经反复凑试直到p值为38、ti值为120秒时控制回路符合动态过程品质要求,这时的 p和 ti 就是最佳值,sp变化趋势曲线如图6所示。其他控制回路优化同理。
28.如果调节器是 pid 三作用方式 ,那么s5.2基础上加进微分作用。由于微分作用有抵制偏差变化的能力 ,所以确定一个 td 值后 ,可把整定好的 p 和 ti 值减小一点再进行现场凑试,凑试过程同s5.2,直到 p、ti和td 取得最佳值为止,至此完成该控制回路pid整定。
29.以永坪炼油厂120万吨/年催化装置为例,dcs后端146个控制回路,其中前端不存在回路3个、仪表故障6个、停用间歇使用备用控制回路3个,具备自动投用条件控制数量为134个,通过本专利提供的整定方法,共计整定96个,优化29个,有效自控率从30%提升至92%,操作人员工作量每日操作300次下降到60次,装置预警报警数量从100个下降至20个。此外,在并在同厂250万吨/年常压蒸馏装置、15万吨/年催化重整装置、20万吨/年航煤加氢装置、其它炼油化工厂的催化装置验证,本发明提供的pid整定具有良好的适用性。
再多了解一些
本文用于企业家、创业者技术爱好者查询,结果仅供参考。