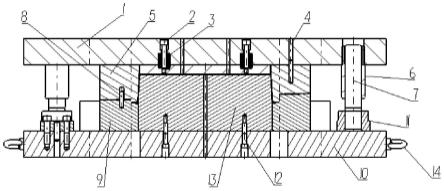
1.本发明属于航空飞机铝合金钣金加工技术领域,具体涉及一种变高度半圆筒形防锈铝零件成形工装及其使用方法,用于铝合金拉深成形。
背景技术:
2.飞机支座类零件通常为为两个半圆筒形防锈铝零件组成,此类桶形零件传统方式采用落压成形进行加工。由于防锈铝材料延伸率较低、塑性差,并且桶形零件自身为半圆形,导致零件在落压成形过程中由于压力快速施加,零件延伸过程不充分而导致起皱、破裂现象发生,并且落压成形后的零件表面质量和加工精度不稳定,零件易产生报废,工人后期修整工作量较大。此外零件在装配时需要将左右对称的两个半圆筒形防锈铝零件进行对缝焊接,形成一个圆筒形结构件,里面安装飞机使用的成品件,成品件为球形,球形的直径与焊接后的圆形开口直径相差2mm,安装时成品件放入焊接后的圆形开口中,保证与桶形结构件圆形开口间隙均匀,所以对于桶形形面的加工精度也要求较高,需要每一个半圆桶形零件的加工精度均不大于0.5mm。因此急需要采用新的加工方法来提高产品的加工精度和加工效率。
技术实现要素:
3.本发明的目的在于发明了一种变高度半圆筒形防锈铝零件的加工工装及制造方法,该方法可以实现两个不同高度桶形防锈铝零件同时高质量加工,成形后零件不发生破裂、表面不产生起皱等表面缺陷,为了达到上述目的,本发明的技术方案为:
4.设计了一组全新的桶形防锈铝零件拉深成形工装及工艺流程,通过使用液压机连接上模及下模,使用“凸模”及“凹模”的结合方式加工出合格的零件。
5.一种变高度半圆筒形防锈铝零件成形工装,包括拉深模和配套模胎;
6.所述的拉深模包括下模板1、卸料螺钉2、弹簧3、圆柱销4、凹模5、导套6、导柱7、压边圈圆柱销8、压边圈9、上模板10、导柱座11、螺钉12、凸模13、吊环14、u形连接槽15和对称轴冲点16;
7.所述的下模板1为工装的底面,下模板1上面安装有卸料螺钉2,卸料螺钉2上安装有弹簧3,合模时,卸料螺钉2的末端顶在零件表面,用于在施加反向力时将成形后的零件弹起;下模板1上表面安装有圆柱销4,用于与凹模5的下表面固定连接;凹模5的形面与零件的形面一致;下模板1四周安装有导套6,导套6里面安装有导柱7,导柱7与上模板10上的导柱座11对接,用于上模板10和下模板1在零件加工过程中的导向;
8.凹模5上表面四周安装有压边圈圆柱销8;压边圈圆柱销8上端连接压边圈9,压边圈9用于将待加工的零件压住,便于后续凸模13进行冲压拉深;凸模13上表面与上模板10通过螺钉12连接,凸模13轴线上设置有两个对称轴冲点16,用于冲压拉深过程中在零件上制出两个冲点,便于与冲点定位孔18对齐定位;上模板10两侧安装有吊环14用于吊车的起吊,没有安装吊环14的上模板10的边缘设置有u形连接槽15,u形连接槽15的作用在于通过使用
螺栓杆将上模板10与液压机工作平台进行固定连接;下模板1边缘也设置有u形连接槽15;
9.所述的配套模胎包括配套模胎胎体17,配套模胎胎体17的形面与零件理论形面一致,便于零件拉深成形后的修整,配套模胎胎体17上面设置有两个冲点定位孔18用于零件在上工序制出的冲点进行定位。
10.变高度半圆筒形防锈铝零件成形工装的使用方法,包括以下步骤:
11.第一步使用吊车将下模板1吊运至液压机工作平台中心位置上,使用螺栓通过下模板1上的u形连接槽15将其拧紧在工作平台上,保证其在液压机拉深成形过程中不发生位移;然后将卸料螺钉2安装在下模板1上面并套上弹簧3,保证垂直度不大于1度;
12.第二步将凹模5插入圆柱销4内进行定位安装,将准备加工的板料加工成圆形,保证可以一次拉深成形制出两个零件;将加工好的板料放在凹模5上,保证板料直径大于凹模5最大轮廓20-30mm,多余的板料用于压边圈9进行施加压力固定零件毛料;
13.第三步使用螺栓通过上模板10上的u形连接槽15与液压机上工作台进行连接,连接好后启动液压机将凸模13向下运动,进行试模,保证凸模13可以顺利与下工作台上的凹模5闭合;根据拉深模的闭合高度,以及已选择设备的滑块行程,决定是否在设备工作台上增加垫铁;若需要增加垫铁,则根据拉深模外形尺寸,将垫铁每隔200~300mm均匀摆放在设备工作台上,保证左右对称;
14.第四步试模合格后将压边圈圆柱销8插入凹模5内,然后将压边圈9沿压边圈圆柱销8进行导向与凹模5进行连接,将板料压在两者之间,板料与上下模间隙不大于3mm;
15.第五步按铝合金板料尺寸,手工剪切两块试压毛料;将一块试压毛料放在拉深模凹模5连接的压边圈9上,保证周边余量均匀;设定液压机压力及首次拉深试压的深度;滑块下行,模具合模,保压超过5秒钟后,滑块上行,模具开启;利用卸料螺钉2上面的弹簧3反作用力,使试压毛料从凹模5中掉出;零件取出后,观察零件的拉深成形情况,是否出现皱纹或破裂;
16.第六步调整拉深试压条件:根据试压零件的材料流动情况,手工修整未进行拉深的毛料,将材料流动不畅的位置适当去除;若出现皱纹,则增加压边力;若出现破裂,则减小压边力或在凹模5和压边圈9上涂润滑油;未破裂的零件,手工平皱后,增加拉深深度继续进行拉深试压;
17.破裂的零件,需要更换,按修整后的毛料重新剪切试压料后进行试压;通过多次试压,并逐次增加拉深深度,直至达到所用拉深模的最终成形状态,记录每次成形的深度和压边力,确定拉深的板料尺寸和形状;
18.第七步按试压确定的板料尺寸和形状,剪切或铣切拉深板料;按拉深试压时确定的成形过程来进行拉深成形:液压机进行拉深成形时,按试压记录分步骤进行拉深,所用零件都按同一深度进行拉深,取出后进行手工平皱,然后再按下一深度值进行拉深,直至达到所用拉深模最终的拉深成形状态;
19.第八步将拉深成形好的板料放入配套模胎胎体17上,根据凸模13上的对称轴冲点16在零件留下的冲点进行定位,保证板料上的冲点与冲点定位孔18对齐并将两个冲点连线,后续划线将圆形拉深零件进行剪切,制出两个对称零件,完成最终的零件加工。
20.本发明的有益效果:
21.通过使用全新的桶形防锈铝零件拉深成形工装,一次成形可以加工两个零件,通
过工装上对称摆放的方式,拉深成形过程有效的抵消了加工过程中带来的形变,避免了板料的断裂,使成形后的零件贴模度提高至不大于0.5mm,减少工人修整量,提高了产品质量。
附图说明
22.图1为拉深模侧视图
23.图2为拉深模凸模俯视图
24.图3为拉深模组装后示意图
25.图4为配套模胎俯视图
26.图5为零件在配套模胎上的定位视图
27.图中:下模板1、卸料螺钉2、弹簧3、圆柱销4、凹模5、导套6、导柱7、压边圈圆柱销8、压边圈9、上模板10、导柱座11、螺钉12、凸模13、吊环14、u形连接槽15、对称轴冲点16、配套模胎胎体17、冲点定位孔18
具体实施方式
28.以下结合具体实施例对本发明做进一步说明。
29.一种变高度半圆筒形防锈铝零件拉深成形工装,其特征在于,包括所述的制造方法主要由拉深成形和配套修整构成,零件拉深成形使用的工装为“包括拉深模”,配套修整使用的工装名称为“配套模胎”;
30.所述的拉深模包括下模板1、卸料螺钉2、弹簧3、圆柱销4、凹模5、导套6、导柱7、压边圈圆柱销8、压边圈9、上模板10、导柱座11、螺钉12、凸模13、吊环14、u形连接槽15和对称轴冲点16;
31.所述的下模板1为工装的底面,厚度可控制在30-50mm之间,下模板1上面安装一定数量的有卸料螺钉2,卸料螺钉2上安装有弹簧3,用于在施加反向力时将成形后的零件弹起;下模板1上表面安装有四个圆柱销4,用于与凹模5的下表面固定连接;凹模5的形面与零件的形面一致,可采用数控加工;下模板1四周安装一定数量的有导套6,导套6里面安装有导柱7,导柱7与上模板10上的导柱座11对接,用于上模板10和下模板1在零件加工过程中的导向;
32.凹模5上表面四周安装有压边圈圆柱销8,压边圈圆柱销8高度为10-15mm均可;压边圈圆柱销8上端连接压边圈9,压边圈9用于将待加工的零件压住,便于后续凸模13进行冲压拉深;凸模13上表面与上模板10通过螺钉12连接,凸模13轴线上设置有两个对称轴冲点16,用于冲压拉深过程中在零件上制出两个冲点,便于下步工序定位;上模板10两侧安装有吊环14用于吊车的起吊,非安装吊环14的边缘制出一定数量的设置有u形连接槽15,此处u形连接槽15的作用在于通过使用螺栓杆将上模板10与液压机工作平台进行固定连接;
33.所述的配套模胎为配套模胎胎体17,此结构需通过五轴数控机床进行加工,配套模胎胎体17的形面与零件理论形面一致,便于零件拉深成形后的修整,配套模胎胎体17上面设置有两个冲点定位孔18用于零件在上工序制出的冲点进行定位;
34.此种工装设计结构及其制造方法,可以通过液压机缓慢的拉深运动将防锈铝板料逐渐延展,最终达到桶形结构。
35.第一步使用吊车将下模板1吊运至液压机工作平台中心位置上,使用螺栓通过下
模板1上的u形连接槽15将其拧紧在工作平台上,保证其在液压机拉深成形过程中不发生位移。然后将卸料螺钉2安装在下模板1上面并套上弹簧3,保证垂直度不大于1度。
36.第二步将凹模5插入圆柱销4内进行定位安装,将准备加工的防锈铝合金板料加工成圆形,保证可以一次拉深成形制出两个零件。将加工好的板料放在凹模5上,保证板料直径大于凹模5最大轮廓20-30mm,多余的板料用于压边圈9进行施加压力固定零件毛料。
37.第三步使用螺栓通过上模板10上的u形连接槽15与液压机上工作台进行连接,连接好后启动液压机将凸模13向下运动,进行试模,保证凸模13可以顺利与下工作台上的凹模5闭合。根据拉深模的闭合高度,以及已选择设备的滑块行程,决定是否在设备工作台上增加垫铁。若需要增加垫铁,则根据拉深模外形尺寸,将垫铁每隔200~300mm均匀摆放在设备工作台上,保证左右对称。
38.第四步试模合格后将压边圈圆柱销8插入凹模5内,然后将压边圈9沿压边圈圆柱销8进行导向与凹模5进行连接,将防锈铝板料压在两者之间,板料与上下模间隙不大于3mm。
39.第五步按铝合金板料尺寸,手工剪切两块试压料。将一块试压毛料放在拉深模凹模5连接的压边圈9上,保证周边余量均匀。设定液压机压力及首次拉深试压的深度。滑块下行,模具合模,保压超过5秒钟后,滑块上行,模具开启。利用卸料螺钉2上面的弹簧3反作用力,使试压零件从凹模5中掉出。零件取出后,观察零件的拉深成形情况,是否出现皱纹或破裂。
40.第六步调整拉深试压条件:根据试压零件的材料流动情况,手工修整未进行拉深的毛料,将材料流动不畅的位置适当去除;若出现皱纹,则增加压边力;若出现破裂,则减小压边力或在凹模5和压边圈9上涂润滑油。未破裂的零件,手工平皱后,增加拉深深度继续进行拉深试压;
41.破裂的零件,需要更换,按修整后的毛料重新剪切试压料后进行试压。通过多次试压,并逐次增加拉深深度,直至达到所用拉深模的最终成形状态,记录每次成形的深度和压边力,确定拉深的板料尺寸和形状。
42.第七步按试压确定的板料尺寸和形状,剪切或铣切拉深板料。按拉深试压时确定的成形过程来进行拉深成形:液压机进行拉深成形时,按试压记录分步骤进行拉深,所用零件都按同一深度进行拉深,取出后进行手工平皱,然后再按下一深度值进行拉深,直至达到所用拉深模最终的拉深成形状态。
43.第八步将拉深成形好的零件板料放入配套模胎胎体17上,根据凸模13上的对称轴冲点16在零件留下的冲点进行定位,保证板料上的冲点与冲点定位孔18对齐并将两个冲点连线,后续划线将圆形拉深零件进行剪切,制出两个对称零件,完成最终的零件加工。
再多了解一些
本文用于企业家、创业者技术爱好者查询,结果仅供参考。