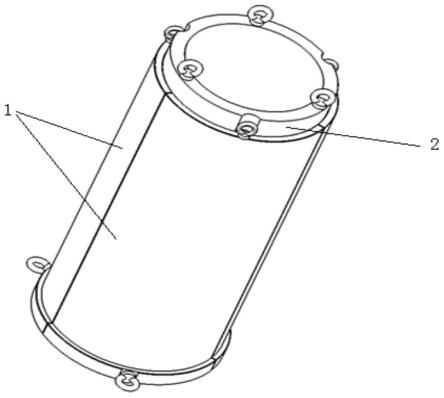
1.本发明属于航空钛合金薄壁零件热成形技术领域,涉及一种基于热胀型模的钛合金圆筒精准成形方法。
背景技术:
2.目前多个在产重点型号飞机的圆筒均采用钛合金材料,其外形尺寸精度要求高,以往生产中采用传统的滚弯和稳定热处理的工艺方法进行校形,但由于滚弯质量和热处理模具结构等原因,很难保证圆筒的圆度要求。因此亟需对该项钛合金圆筒的制造难题找到解决方法,提高该类零件的成形质量。
3.本发明所针对的圆筒零件为封闭的圆环结构,由钛合金板材卷制而成,在对缝处通过氩弧焊连接。零件选用tc2钛合金材料,强度极限бb一般为685~ 885mpa,板材厚度为δ2.0,内径尺寸要求φ340(公差-0.3~0)mm。其主要技术指标是保证筒形件的内径尺寸满足φ340(公差-0.3~0)mm,由于钛合金蒙皮强度较高,滚弯成形后在零件的对缝位置及开口边缘位置会留存一定的直线段,而且圆筒焊接后存在很大的焊接变形,因此如何校正零件滚弯变形及焊后变形,保证零件成形精度是成形过程中需要控制的重点。
4.钛合金圆筒的传统制造采用滚弯和稳定热处理校形的工艺方法,但存在以下问题:
5.(1)稳定热处理工装问题:现有的稳定热处理工装选用钛合金ta15材料,工装材料与零件材料的热膨胀系数基本相同,工装设计尺寸与零件尺寸完全一致,未考虑零件滚弯后的直线段及焊接后变形问题,导致零件向热处理夹具中安放十分困难;
6.(2)展开毛料问题:钛合金圆筒的展开毛料尺寸是按理论尺寸计算得出,依据该毛料尺寸可推算零件滚弯后内径值为φ340mm,此时如果存在滚弯后的直线段或焊接变形问题,仅利用稳定热处理夹具已经很难校正。
技术实现要素:
7.为解决上述问题,本发明提出了一种基于热胀型模的钛合金圆筒精准成形方法,以保证钛合金筒形件成形精度为目标,通过对传统圆筒加工工艺中存在的问题进行分析,由工装结构改良设计和校正展开毛料尺寸入手进行工艺方法创新,大大提高了钛合金圆筒零件的成形效率与产品合格率。
8.本发明的技术方案为:
9.一种基于热胀型模的钛合金圆筒精准成形方法,其具体步骤:
10.s1:在原有内形芯轴与外形夹具相配合的基础上,对原有热处理校形工装进行了改良,针对钛合金圆筒这种闭合结构的筒形件,运用热胀形的方法原理对其进行圆度校正。该步骤所运用的热胀形工艺原理,是利用不同材料在高温条件下热膨胀系数的差异,随着温度的不断升高,零件尺寸将随着模具外型尺寸发生永久的胀量变形,从而得到符合尺寸精度要求的圆筒零件;
11.s2:基于所述步骤s1的方法内容,利用热胀成形原理加工圆筒零件,需要选择合适的模具材料并准确计算出模具尺寸,因此,需要按热胀成形后的模具尺寸对零件的展开毛料尺寸进行重新计算,预留出足够的零件胀形量,以消除零件局部变形和直线段。
12.具体的,采用专用滚弯设备,对钛合金板料进行整圆滚制。
13.进一步的,步骤s1设计了一种热胀型模,用以对圆筒零件进行热处理校形该热胀型模包括:分瓣膜1、模型芯轴2。热胀型模设计为分瓣膜1的结构形式,将模具工作面分成三瓣,内部用带有锥度的模型芯轴2进行支撑,使用时将圆筒零件先套在分瓣膜1上,通过调整模型芯轴2的打夹量,来控制分瓣膜1的外径尺寸,进而控制圆筒零件的内形尺寸。
14.步骤s2所用的热胀成形方法,是利用不同材料高温下热膨胀系数的差异,因此工装材料与成形零件材料的热膨胀系数需要有一定的差值。考虑到工装的稳定性与制造成本,所选用的工装材料为不锈钢1cr18ni9ti,在600℃时钛合金的热膨胀系数为9.2
×
10-6
,不锈钢1cr18ni9ti的热膨胀系数为18.2
×
10-6
,二者热膨胀能力存在较大的差异。设模具和零件尺寸热胀量的差值为δls,则可得计算公式(1):
15.δls=l
cm-l
cj
=ksl
cj
ꢀꢀꢀꢀꢀꢀꢀꢀꢀꢀꢀꢀꢀꢀꢀꢀꢀꢀꢀ
(1)
16.式中:l
cm
—模具常温下的名义尺寸,mm;
17.l
cj
—零件常温下的名义尺寸,mm;
18.ks—放尺或缩尺系数,且正放负缩,按以下公式(2)计算:
[0019][0020]
t0—室温,℃;
[0021]aj
—成形温度时,所成形钛合金材料的热膨胀系数,1/℃;
[0022]am
—成形温度时,所用模具材料的热膨胀系数,1/℃。
[0023]
计算可得:δls=-1.85mm;热胀型模具尺寸为φ338.15mm。
[0024]
考虑到零件公差要求,因此将热胀型模具尺寸设计为φ388(公差 0.1~0) mm
[0025]
进一步的,步骤s2以热胀型模具尺寸φ388mm作为理论基准尺寸,计算得出展开毛料长度尺寸为1068.1mm。实际上毛料尺寸与热胀型模理论尺寸不需要完全一致,且为打夹方便,将毛料尺寸增大,将其尺寸设计为1070mm,该毛料尺寸对比零件理论尺寸展开毛料1075mm在直径上预留出约1.6mm的胀形量。
[0026]
最后,基于以上方法步骤对钛合金圆筒零件进行了精准成形,成形圆筒零件。
[0027]
本发明方法通过对钛合金圆筒的结构和技术要求进行分析,确定了影响目前舱筒类零件成形质量的主要原因,并提出了合理优化后的工艺方法,利用热胀成形技术对钛合金圆筒进行热处理校形,很好地保证了圆筒零件的圆度要求。钛合金圆筒零件制造质量的提高,有效缓解和解决了长期困扰舱筒类零件生产的诸多实际问题。
附图说明
[0028]
图1是本发明方法所用热胀型模的等轴示意图。
[0029]
图2是本发明方法所制的钛合金圆筒零件示意图。
[0030]
图中:1分瓣膜;2模型芯轴。
具体实施方式
[0031]
下面结合附图和技术方案对本发明的具体实施例加以说明,其实施流程如下:
[0032]
1、计算热胀型模尺寸:根据不同材料在高温条件下热膨胀系数的差异,针对拟采用的热胀成形法,计算热胀型模和零件尺寸热胀量的差值,并根据钛合金圆筒零件的公差要求,对热胀型模的制作尺寸进行校正设计;
[0033]
2、计算展开毛料尺寸:在得到热胀型模尺寸后,以此为理论基准尺寸,计算展开毛料长度尺寸,并根据实际打夹操作的便捷性需求,对毛料尺寸进行适当增大调整,预留出约1.6mm的胀型量;
[0034]
3、进行钛合金舱筒弯制:采用专用滚弯机,将滚弯机上辊轴的下母线与下辊轴的上母线之间的间距,此间距应略大于板料厚度。再将板料一端送入到达下辊轴的中部,将上辊轴降下,而后夹紧右端部的钢制翻转机构。进一步的,拧转工作辊驱动上、下辊轴运动,以对板料进行弯曲。该操作过程可通过调整上辊轴的升降程度,来调节所成形舱筒的曲率半径大小,可反复调试直至达到所需的曲率半径为止;
[0035]
4、舱筒零件热处理校形:将舱筒件先套在热胀型模的分瓣膜1上,通过调整热胀型模的模型芯轴2的打夹量,来控制分瓣膜1的外径尺寸,进而控制舱筒件的内形尺寸。在热校形完毕后,即可得到符合精度要求的钛合金圆筒零件。
[0036]
针对本实施例中对基于热胀型模的钛合金圆筒精准成形方法的描述,需要特别指出的是,本实用说明已描述了该方法实施例的具体内容,因此本领域的相关技术人员能够做到理解并实施的程度,且在不脱离本发明原理和宗旨的情况下可以对所述发明方法的内容进行多样化改进、修正、替换或变型,但本发明方法的公开范围由其相关权利要求及其等同物限定。
再多了解一些
本文用于企业家、创业者技术爱好者查询,结果仅供参考。