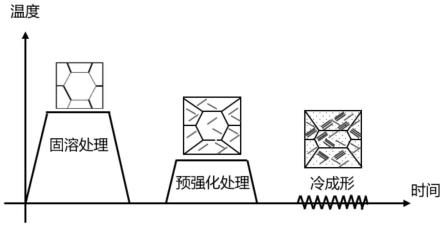
1.本发明涉及金属板材成形加工技术领域,具体涉及一种高强铝合金短流程高性能成形技术方法及其应用。
背景技术:
2.近年来,铝合金在航空航天领域的应用越来越广泛。铝合金零部件的成形方法主要分为冷成形和热成形,可热处理强化铝合金冷成形性能差,热成形可以获得成形良好、精度高的铝合金零部件。但是热成形工序复杂,生产成本较高,而且热成形或温成形对温度敏感,很容易影响析出相的分布进而使得铝合金板材强度降低。可热处理铝合金的冷成形受到限制主要是因为:1.冷成形性差,除了软态的o态板材,其余热处理状态很难室温成形;2.成形后为了获得所需要的力学性能,需要进行固溶处理(导致精度低)和长时间的人工时效处理(如7xxx系铝合金需要120℃-24h的人工时效),生产效率低。由此可见,迫切需要一种流程简单、生产效率高、成形性能和成形后性能满足需求的冷成形工艺。
3.目前针对铝合金的冷成形的研究,主要集中在铝合金成分设计和铝合金成形前的处理方式。专利文献cn110066931b公开了一种适于冷成形的铝合金及其制备方法,在铝合金组织中引入znyb强化相、zntb强化相、mgzn强化相,并用sc和zr元素进行晶粒细化,获得冷成形性能良好的高强铝合金,但此方法仅适用于特定铝合金材料。
4.专利文献cn111549266b公开了一种提高车身结构铝合金板材成形性能的组织调控方法,通过热轧—均匀化—超低温冷轧—双级热处理—超低温冷轧—双级固溶—淬火——低温时效获得粗/细晶交替分布组织,拥有良好的室温冲压成形性能,但此方法生产板材的工艺非常复杂,成形后的性能低于7系铝合金的室温性能仍需要长时间的人工时效处理。
技术实现要素:
5.针对目前存在的技术问题,本发明提供一种高强铝合金短流程高性能成形技术方法及其应用,该方法在冷成形之前,对铝合金坯料进行预硬化处理,经预硬化处理的合金组织中,尺寸较大的gpii区占主导地位,其冷成形性能超过传统o态处理的板材;通过成形过程中gpii区与位错的相互作用机制,使得成形后的强度和韧性超过t6和t8态。本发明在获得较好的冷成形性能的同时,保证了成形后构件的力学性能。另外,铝合金坯料的预硬化处理是由板材供应商提前完成的,且板料在室温下的组织稳定性保证了批量供货的可靠性,因此进货后可以直接投入冷成形生产线进行成形,有效缩短生产周期,降低成本,提高生产效率。
6.为实现上述目的,本发明采取的技术方案如下:
7.一种高强铝合金短流程高性能成形技术方法,其特征在于,包括下列步骤:
8.步骤s1.将可热处理强化铝合金板料进行固溶和淬火处理,获得w态铝合金板料;
9.步骤s2.对w态铝合金板料进行预硬化处理,2000系铝合金处理温度为60-180℃,
6000系铝合金处理温度为70-160℃,7000系铝合金处理温度为70-100℃,预硬化处理时间为1-24h;板料经过预硬化处理后,2000系铝合金形成直径为1-5nm长度为1-15nm的gpii区,7000系铝合金形成直径为1-15nm厚度为1-2个原子层的gpii区,6000系铝合金形成直径为1-5nm长度为1-30nm的gpii区,其包括initialβ”和pre-β”,所有预硬化板料所形成的gpii区占比为60%-100%;
10.步骤s3.将预硬化处理完成后的板料作为冷成形批量供货坯料;
11.步骤s4.将预硬化处理后的坯料进行冷成形,坯料各处变形量处于1%-20%之间,即可获得最终构件。
12.进一步地,所述可热处理强化铝合金包括2000系、6000系、7000系铝合金板材。
13.进一步地,所述2000系铝合金固溶、淬火和预硬化处理后应用于火箭燃料贮箱箱底的分瓣成形和整体成形。
14.进一步地,所述火箭燃料贮箱箱底的分瓣成形具体包括如下步骤:
15.步骤s1.将可热处理强化铝合金板料进行固溶和淬火处理,获得w态铝合金板料;
16.步骤s2.对w态铝合金板料进行预硬化处理,2000系铝合金处理温度为60-180℃板料经过预硬化处理后,直径为1-5nm长度为1-15nm的gpii区占比为60%-100%;
17.步骤s3.将预硬化处理完成后的板料作为冷成形批量供货坯料,预硬化的坯料可立即进行成形,也可库存不超过18个月后成形;
18.步骤s4.将预硬化处理后的坯料进行冷成形,坯料变形量处于1%-20%之间;
19.步骤s5.利用搅拌摩擦焊将分瓣构件焊接成整体构件后,无需固溶和人工时效处理,即可获得超过t6和t8态力学性能的燃料贮箱箱底。
20.进一步地,所述火箭燃料贮箱箱底的整体成形具体包括如下步骤:
21.步骤s1.将可热处理强化铝合金板料进行固溶和淬火处理,获得w态铝合金板料;
22.步骤s2.对w态铝合金板料进行预硬化处理,2000系铝合金处理温度为60-180℃板料经过预硬化处理后,直径为1-5nm长度为1-15nm的gpii区占比为60%-100%;
23.步骤s3.将预硬化处理完成后的板料作为冷成形批量供货坯料,预硬化的坯料可立即进行成形,也可库存不超过18个月后成形;
24.步骤s4.利用搅拌摩擦焊将预硬化态坯料焊接后冷成形,坯料变形量处于1%-20%之间,成形后无需固溶和人工时效处理,即可获得超过t6和t8态力学性能的燃料贮箱箱底。
25.进一步地,所述火箭燃料贮箱箱底的整体成形具体包括如下步骤:
26.步骤s1.利用搅拌摩擦焊将2000系坯料焊接,焊接后的板料进行固溶和淬火处理,获得w态铝合金板料;
27.步骤s2.对w态铝合金板料进行预硬化处理,2000系铝合金处理温度为60-180℃板料经过预硬化处理后,直径为1-5nm长度为1-15nm的gpii区占比为60%-100%,预硬化的坯料可立即进行成形,也可库存不超过18个月后成形;
28.步骤s3.将预硬化焊接坯料进行冷成形,成形后无需固溶和人工时效处理,即可获得超过t6和t8态力学性能的燃料贮箱箱底。
29.因此,与现有技术相比,本发明具有如下优点:
30.(1)经过预硬化处理后的铝合金坯料处于组织稳定状态,不会因自然时效产生组
织变化,预硬化处理后的坯料可以放置长达18个月,因此便于储存、运输,有利于板料供应商进行批量处理和供货,提高生产效率,降低成本;
31.(2)预硬化铝合金坯料冷成形后的零部件,不会因自然时效产生组织变化,因此便于储存、运输,有利于零部件生产厂家进行批量处理和供货,提高生产效率,降低成本;
32.(3)预硬化后的合金拥有尺寸较大、稳定性良好的gpii区组织,高强铝合金板材经预硬化处理后可以形成比t4态尺寸更大、更加稳定的gpii区组织,室温成形性能超过传统软态(o态)板材,并且gpii区组织在成形过程中与位错产生的交互作用,产生了平面滑移,可以更有效地抑制大范围的动态恢复,提高了成形后构件的加工硬化能力。同时在变形过程中产生大量的纳米层错,纳米层错的强化作用进一步提高了成形后构件的强度,使成形后的力学性能优于t6和t8态铝合金的力学性能;
33.(4)使用本发明所述冷成形工艺,成形工序由7道(传统冷成形工艺)减少到4道,全工序耗时减少了12小时以上,冷成形后可以获得满足需求的力学性能,成形后不需要进行固溶、时效等热处理步骤,大大降低了成形过程的能耗,缩短了生产周期,提高了生产效率。
附图说明
34.图1为本发明所述预硬化冷成形工艺路线
35.图2为传统铝合金冷成形工序流程图
36.图3为本发明所述预硬化冷成形工艺工序流程图
37.图4为铝合金零件的应力-应变曲线图
具体实施方式
38.下面通过实施例,并结合附图,对本发明的技术方案作进一步具体的说明。
39.如图1和3所示,本发明提供铝合金短流程高性能成形技术方法,包括如下步骤:
40.(1)将可热处理强化铝合金板料进行固溶和淬火处理,获得w态铝合金板料;
41.(2)2000系铝合金处理温度为60-180℃,6000系铝合金处理温度为70-160℃,7000系铝合金处理温度为70-100℃,预硬化处理时间为1-24h。板料经过预硬化处理后,2000系铝合金形成直径为1-5nm长度为1-15nm的gpii区,7000系铝合金形成直径为1-15nm厚度为1-2个原子层的gpii区,6000系铝合金形成直径为1-5nm长度为1-30nm的gpii区,其包括initialβ”和pre-β”,所有预硬化板料所形成的gpii区占比为60%-100%;
42.(3)将预硬化处理完成后的板料作为冷成形批量供货坯料;
43.(4)将预硬化处理后的坯料进行冷成形,即可获得最终零件,无需后续时效处理。
44.其中,2000系铝合金固溶、淬火和预硬化处理后应用于火箭燃料贮箱箱底的分瓣成形和整体成形。
45.火箭燃料贮箱箱底的分瓣成形具体包括如下步骤:
46.步骤s1.将可热处理强化铝合金板料进行固溶和淬火处理,获得w态铝合金板料;
47.步骤s2.对w态铝合金板料进行预硬化处理,2000系铝合金处理温度为60-180℃板料经过预硬化处理后,直径为1-5nm长度为1-15nm的gpii区占比为60%-100%;
48.步骤s3.将预硬化处理完成后的板料作为冷成形批量供货坯料,预硬化的坯料可立即进行成形,也可库存不超过18个月后成形;
49.步骤s4.将预硬化处理后的坯料进行冷成形,坯料变形量处于1%-20%之间;
50.步骤s5.利用搅拌摩擦焊将分瓣构件焊接成整体构件后,无需固溶和人工时效处理,即可获得超过t6和t8态力学性能的燃料贮箱箱底。
51.火箭燃料贮箱箱底的整体成形具体包括如下步骤:
52.步骤s1.将可热处理强化铝合金板料进行固溶和淬火处理,获得w态铝合金板料;
53.步骤s2.对w态铝合金板料进行预硬化处理,2000系铝合金处理温度为60-180℃板料经过预硬化处理后,直径为1-5nm长度为1-15nm的gpii区占比为60%-100%;
54.步骤s3.将预硬化处理完成后的板料作为冷成形批量供货坯料,预硬化的坯料可立即进行成形,也可库存不超过18个月后成形;
55.步骤s4.利用搅拌摩擦焊将预硬化态坯料焊接后冷成形,坯料变形量处于1%-20%之间,成形后无需固溶和人工时效处理,即可获得超过t6和t8态力学性能的燃料贮箱箱底。
56.如图2所示,传统铝合金冷成形工序流程需要经过软态胚料、预变形、固溶淬火、切边整形、终成形、加热、人工时效和t6态零件等8道工序,预计耗时大于12小时。如图3所示,本发明只需要经过预硬化态胚料、冷成形、切边整形、超过t6态零件等4道工序,时间小于5分钟。
57.火箭燃料贮箱箱底的整体成形具体包括如下步骤:
58.步骤s1.利用搅拌摩擦焊将2000系坯料焊接,焊接后的板料进行固溶和淬火处理,获得w态铝合金板料;
59.步骤s2.对w态铝合金板料进行预硬化处理,2000系铝合金处理温度为60-180℃板料经过预硬化处理后,直径为1-5nm长度为1-15nm的gpii区占比为60%-100%,预硬化的坯料可立即进行成形,也可库存不超过18个月后成形;
60.步骤s3.将预硬化焊接坯料进行冷成形,成形后无需固溶和人工时效处理,即可获得超过t6和t8态力学性能的燃料贮箱箱底。
61.实施例一:
62.以2219铝合金为坯料,一种高强铝合金短流程高性能成形技术方法,包括如下步骤:
63.(1)将2219铝合金坯料置于电阻炉中加热至529-541℃保温40分钟,获得w态铝合金;
64.(2)在10分钟内将w态铝合金板进行预硬化处理,即加热至90℃,并保温24小时,获得冷成形坯料;
65.(3)将坯料进行冷冲压成形,获得最终制件,无需后续时效热处理;
66.在冲压成形后的零件上切取拉伸试样,进行单向拉伸试验测试其成形后力学性能,多个拉伸试样取平均值,其抗拉强度可达441mpa,屈服强度可达418mpa。
67.实施例二:
68.以2219铝合金为坯料,一种高强铝合金短流程高性能成形技术方法,包括如下步骤:
69.(1)将2219铝合金坯料置于电阻炉中加热至529-541℃保温40分钟,获得w态铝合金;
70.(2)在10分钟内将w态铝合金板进行预硬化处理,即加热至130℃,并保温12小时,获得冷成形坯料;
71.(3)将坯料进行冷冲压成形,获得最终制件,无需后续时效热处理;
72.在冲压成形后的零件上切取拉伸试样,进行单向拉伸试验测试其成形后力学性能,多个拉伸试样取平均值,其抗拉强度可达450mpa,屈服强度可达413mpa。
73.实施例三:
74.以2219铝合金为坯料,一种高强铝合金短流程高性能成形技术方法,包括如下步骤:
75.(1)将2219铝合金坯料置于电阻炉中加热至529-541℃保温40分钟,获得w态铝合金;
76.(2)在10分钟内将w态铝合金板进行预硬化处理,即加热至160℃,并保温5小时,获得冷成形坯料;
77.(3)将坯料进行冷冲压成形,获得最终制件,无需后续时效热处理;
78.如图4中(a)为2219铝合金160℃-5h预硬化冷成形后取样拉伸的应力-应变曲线图。在冲压成形后的零件上切取拉伸试样,进行单向拉伸试验测试其成形后力学性能,多个拉伸试样取平均值,其抗拉强度可达449mpa,屈服强度可达425mpa。
79.实施例四:
80.以6061铝合金为坯料,一种高强铝合金短流程高性能成形技术方法,包括如下步骤:
81.(1)将6061铝合金坯料置于电阻炉中加热至516-579℃保温40分钟,获得w态铝合金;
82.(2)在10分钟内将w态铝合金板进行预硬化处理,即加热至100℃,并保温12小时,获得冷成形坯料;
83.(3)将坯料进行冷冲压成形,获得最终制件,无需后续时效热处理;
84.在冲压成形后的零件上切取拉伸试样,进行单向拉伸试验测试其成形后力学性能,多个拉伸试样取平均值,其抗拉强度可达429mpa,屈服强度可达354mpa。
85.实施例五:
86.以6061铝合金为坯料,一种高强铝合金短流程高性能成形技术方法,包括如下步骤:
87.(1)将6061铝合金坯料置于电阻炉中加热至516-579℃保温40分钟,获得w态铝合金;
88.(2)在10分钟内将w态铝合金板进行预硬化处理,即加热至130℃,并保温6小时,获得冷成形坯料;
89.(3)将坯料进行冷冲压成形,获得最终制件,无需后续时效热处理;
90.在冲压成形后的零件上切取拉伸试样,进行单向拉伸试验测试其成形后力学性能,多个拉伸试样取平均值,其抗拉强度可达426mpa,屈服强度可达346mpa。
91.实施例六:
92.以6061铝合金为坯料,一种高强铝合金短流程高性能成形技术方法,包括如下步骤:
93.(1)将6061铝合金坯料置于电阻炉中加热至516-579℃保温40分钟,获得w态铝合金;
94.(2)在10分钟内将w态铝合金板进行预硬化处理,即加热至160℃,并保温4小时,获得冷成形坯料;
95.(3)将坯料进行冷冲压成形,获得最终制件,无需后续时效热处理;
96.图4中(c)为6061铝合金160℃-4h预硬化冷成形后取样拉伸的应力-应变曲线图。在冲压成形后的零件上切取拉伸试样,进行单向拉伸试验测试其成形后力学性能,多个拉伸试样取平均值,其抗拉强度可达435mpa,屈服强度可达367mpa。
97.实施例七:
98.以7075铝合金为坯料,一种高强铝合金短流程高性能成形技术方法,包括如下步骤:
99.(1)将7075铝合金坯料置于电阻炉中加热至450-499℃保温30分钟,获得w态铝合金;
100.(2)在10分钟内将w态铝合金板进行预硬化处理,即加热至70℃,并保温12小时,获得冷成形坯料;
101.(3)将坯料进行冷冲压成形,获得最终制件,无需后续时效热处理;
102.在冲压成形后的零件上切取拉伸试样,进行单向拉伸试验测试其成形后力学性能,多个拉伸试样取平均值,其抗拉强度可达579mpa,屈服强度可达514mpa。
103.实施例八:
104.以7075铝合金为坯料,一种高强铝合金短流程高性能成形技术方法,包括如下步骤:
105.(1)将7075铝合金坯料置于电阻炉中加热至450-499℃保温30分钟,获得w态铝合金;
106.(2)在10分钟内将w态铝合金板进行预硬化处理,即加热至80℃,并保温6小时,获得冷成形坯料;
107.图4中(b)为7075铝合金80℃-6h预硬化冷成形后取样拉伸的应力-应变曲线图。(3)将坯料进行冷冲压成形,获得最终制件,无需后续时效热处理;
108.在冲压成形后的零件上切取拉伸试样,进行单向拉伸试验测试其成形后力学性能,多个拉伸试样取平均值,其抗拉强度可达581mpa,屈服强度可达526mpa。
109.实施例九:
110.以7075铝合金为坯料,一种高强铝合金短流程高性能成形技术方法,包括如下步骤:
111.(1)将7075铝合金坯料置于电阻炉中加热至450-499℃保温30分钟,获得w态铝合金;
112.(2)在10分钟内将w态铝合金板进行预硬化处理,即加热至100℃,并保温3小时,获得冷成形坯料;
113.(3)将坯料进行冷冲压成形,获得最终制件,无需后续时效热处理;
114.在冲压成形后的零件上切取拉伸试样,进行单向拉伸试验测试其成形后力学性能,多个拉伸试样取平均值,其抗拉强度可达575mpa,屈服强度可达523mpa。
115.实施实例十:
116.以2219铝合金为坯料,一种应用于火箭燃料贮箱箱底的种高强铝合金短流程高性能成形技术方法,包括如下步骤:
117.(1)将2219铝合金坯料置于电阻炉中加热至529-541℃保温40分钟,获得w态铝合金;
118.(2)在10分钟内将w态铝合金板进行预硬化处理,即加热至160℃,并保温3小时,获得冷成形坯料;
119.(3)将坯料进行冷冲压成形,获得瓜瓣制件;
120.在冲压成形后的零件上切取拉伸试样,进行单向拉伸试验测试其成形后力学性能,多个拉伸试样取平均值,其抗拉强度可达449mpa,屈服强度可达425mpa。
121.实施实例十一:
122.以2219铝合金为坯料,一种应用于火箭燃料贮箱箱底的种高强铝合金短流程高性能成形技术方法,包括如下步骤:
123.(1)将2219铝合金坯料置于电阻炉中加热至529-541℃保温40分钟,获得w态铝合金;
124.(2)在10分钟内将w态铝合金板进行预硬化处理,即加热至120℃,并保温15小时,获得冷成形坯料;
125.(3)利用搅拌摩擦焊将预硬化态坯料焊接获得成形坯料;
126.(4)将成形坯料进行冷冲压成形,获得贮箱箱底整体制件;
127.在冲压成形后的零件上切取拉伸试样,进行单向拉伸试验测试其成形后力学性能,多个拉伸试样取平均值,其抗拉强度可达413mpa,屈服强度可达365mpa。
128.实施实例十二:
129.以2219铝合金为坯料,一种应用于火箭燃料贮箱箱底的种高强铝合金短流程高性能成形技术方法,包括如下步骤:
130.(1)利用搅拌摩擦焊将2219铝合金坯料进行焊接;
131.(2)将焊后2219铝合金坯料置于电阻炉中加热至529-541℃保温40分钟,获得w态铝合金;
132.(3)在10分钟内将w态铝合金板进行预硬化处理,即加热至140℃,并保温7小时,获得冷成形坯料;
133.(4)将成形坯料进行冷冲压成形,获得贮箱箱底整体制件;
134.图4中(d)为2219火箭燃料贮箱箱底140℃-7h预硬化冷成形处理后取样拉伸的应力-应变曲线图。在冲压成形后的零件上切取拉伸试样,进行单向拉伸试验测试其成形后力学性能,多个拉伸试样取平均值,其抗拉强度可达411mpa,屈服强度可达374mpa。
135.综上所述,实施例一至实施例十二中力学性能如下表所示:
136.表1实施例中构件力学性能总结
[0137][0138]
本文中所描述的具体实施例仅仅是对本发明精神作举例说明。本发明所属技术领域的技术人员可以对所描述的具体实施例做各种各样的修改或补充或采用类似的方式替代,但并不会偏离本发明的精神或者超越所附权利要求书所定义的范围。
再多了解一些
本文用于企业家、创业者技术爱好者查询,结果仅供参考。