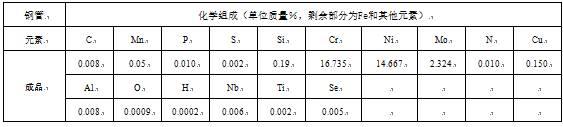
集成电路及ic产业制备装置用超高洁净度不锈钢无缝管的制备方法和不锈钢无缝管
技术领域
1.本发明涉及金属冶炼及压延加工领域,特别是涉及一种集成电路及ic产业制备装置用超高洁净度不锈钢无缝管的制备方法和不锈钢无缝管。
背景技术:
2.近年来,随着我国通信、计算机、工业控制、消费电子、汽车电子等半导体应用领域需求旺盛,ai、量子计算、5g、物联网和智慧城市等新兴应用发展势头迅猛,加快了集成电路产业规模和先进制程的发展速度,国内正在推进14nm、7nm甚至更先进制造工艺实现规模量产,但与世界先进水平存在代差。目前,高性能高端集成电路芯片完全依赖进口,受制于人的问题突出,特别是近年来国际“逆全球化”潮流不断涌现,对我国高端集成电路芯片的断供,使集成电路产业链不稳定性风险增大。在国家、地方产业投资基金的有力推动下,促进了半导体产业链的发展。但应用于半导体器件、化合物半导体、激光器、液晶显示器件、光导纤维、太阳能电池、生物医药等领域的超高洁净度不锈钢管,其生产制造核心技术基本掌握在欧美及日韩等国家手中,危及我国集成电路产业和相关工业体系的安全。
3.随着超大规模集成电路芯片先进制程的不断升级,芯片的线宽越做越小,其对特种气体纯度、颗粒度、杂质含量、露点的要求越来越高。集成电路芯片的干蚀刻、氧化、离子布植、薄膜沉积等制程以及半导体器件、激光器、液晶显示器件、光导纤维、太阳能电池等均使用用大量各类超净高纯特种气体,特种气体的洁净度对产品性能、产品良率有着决定性影响。为了确保输送的特种气体的超高洁净度,不仅要求不锈钢管内表面有一个极高的光滑度,而且,具有很高的耐腐蚀、耐磨特性。因此半导体器件、化合物半导体、液晶显示器件、激光器、光导纤维、太阳能电池等的工艺气体输送,还可应用于生物医药、食品安全等领域气、液体输送,必须选用具备超高洁净度的316l不锈钢管。对不锈钢管材必须要超低c,减少钢中碳化物的形成,又要满足力学性能要求,通过添加n来提高力学性能。同时,cr、ni金属成分达到相关标准,还要求材料中的杂质p、s、mn、si、al、cu等有害元素以及o和h等尽可能的最低,采用铁水三脱预处理 低杂质元素合金兑入k-obm-s强脱氧、真空脱碳(vod),再通过真空感应熔炼(vim),真空电弧再熔化(var)处理v/v、铸造/热轧、热穿孔和冷加工获得纯度高,细晶和完全奥氏体金相组织。钢管内壁经电解抛光处理,内表面粗糙度达到ra ≤ 0.2μm,甚至更低。提高管内壁表面平滑性、富铬层和耐腐蚀性,再经纯化工艺去除表面游离铁离子,达到半导体行业semi国际标准中uhp等级中标准要求:cr/fe比>1.5,crox/feox比>2。再经超高洁净度清洗和内孔冲氮显著地提高洁净度。超高洁净度不锈钢无缝管主要规格
¢
9.53 mm *0.89mm~
¢
76.2 mm *2.54mm,长度一般为6m。
技术实现要素:
4.本发明主要解决的技术问题是提供一种集成电路及ic产业制备装置用超高洁净度不锈钢无缝管的制备方法和超净高纯不锈钢无缝管,可影响持久强度、疲劳强度的o、h含
量加以控制,降低对输送气体的污染,通过vod冶炼、真空var炉和真空压炉精炼把有害元素控制到最低,从而满足表面质量、力学性能等综合性能要求。
5.为解决上述技术问题,本发明采用的一个技术方案是:提供一种集成电路及ic产业制备装置用超高洁净度不锈钢无缝管的制备方法,包括以下步骤:a:不锈钢精炼工艺:以316l不锈钢作为基材,通过添加合金在eaf电炉中初炼和铁水三脱预处理,使铁水中s、si、p和c含量降低,制成不锈钢预熔液;将不锈钢预熔液在k-obm-转炉内进行预吹氧,沸腾脱碳,使炉渣渣系中的c≤0.9%;接着通过vod炉精炼,使al≤0.03%,氧含量≤0.0030%;然后通过lf炉精炼,钢中铝含量控制为0.012-0.018%,氧含量0.0011%-0.0020%,h含量0.0005%-0.0010%,使钢液中非金属夹杂物细化且弥散分布;b:真空感应炉精炼和真空自耗电渣重溶工艺:通过真空感应炉精炼,去除钢液中的c、0、h以及低溶点杂质,使钢液中o、h等的溶解度降低,将钢液中mo、ca、c、al、p、s、si、as以及低熔点元素形成的化合物通过渣附上浮去除,然后浇注制得钢锭;钢锭作为真空自耗重溶的电极,在电极溶化形成液滴/渣洗凝固过程中,使钢进一步纯净化,使铁素体含量≤0.5%,h≤0.0002%,o≤0.0015%;c:不锈钢锻造工艺:采用钢锭锻造和连续钢棒轧制法制造圆管坯;d:热穿孔处理工艺:对圆管坯进行热穿孔后生产出合格的荒管;e:冷加工工艺:对荒管进行中间品冷加工和终轧冷加工,制得不锈钢无缝管;f.内孔电解抛光和酸洗钝化工艺:将步骤e制得的不锈钢无缝管挂在定制夹具上,电解槽内不锈钢管作为电解阳极,电加热棒加热并控制酸液温度为43~55℃,直流多脉冲电压≤30v,电流密度为5-50a/dm,对抛光液进行搅拌对流,减少电解液的温度差,防止阳极过热,电解抛光时间5~15 min,抛光完成后进行酸洗钝化,达到cr/fe比>1.5,crox/feox比>2,去除表面游离铁离子,使表面形成富铬层以提高耐腐蚀性;g.清理工艺:对步骤f制得的不锈钢无缝管进行脱脂和清洗,第一次在采用超声波和清洗剂震洗,清洗后再用高压循环水喷枪对内孔进行逐根冲洗,外表面喷淋漂洗,清洗水温度控制在60℃
±
5℃,沥干表面水分,再逐根对管内壁吹扫去除水分;第二次用纯水作为清洗水,采用超声波清洗机清洗:管内孔用高压水冲洗1~5min,漂洗时间3-5 min,漂洗后沥干水分并逐支用压缩空气对管内吹扫去除水分,最后获得超高洁净度不锈钢无缝管。
6.在本发明一个较佳实施例中,所述步骤f中电解抛光液由98%浓度h2so4、85%浓度h3po4、离子水配置而成,其中电解液成分%(质量分数)h2so4为15~20%、h3po4为63~67%、h2o为12~22%、添加剂等,将比重调节至1.5~1.7;钝化液为质量百分比为20%-35%的hno3溶液,316l不锈钢管在钝化槽中钝化,钝化时间10~30 min。
7.在本发明一个较佳实施例中,所述步骤a中铁水通过脱s、脱si、脱p的三脱预处理,冶炼时对杂质元素进行去除,减少炼钢过程中除去硅、磷所需的石灰造渣料,减少渣量,使s含量减少到0.05-0.06%,si含量减少到0.3-1.0%,p含量减少到0.14-0.3%,钢液的c含量为4%-6%。
8.在本发明一个较佳实施例中,所述步骤a中k-obm-s转炉采取强搅拌顶吹氧气、底吹氧气和氮气或氩气脱碳,提高脱碳速率减少cr损失,预吹氧和沸腾脱碳强底吹搅拌控制,使夹杂物控制在低熔点范围,促进夹杂物快速上浮去除;添加ni合金,使温度保持在1680-1750℃,脱c速率0.15-0.3%min,控制钢中c含量,减少vod冶炼脱c压力,使p、s有害元素等得到去除,提高钢液的洁净度。
9.在本发明一个较佳实施例中,所述步骤a中vod炉中,采用强吹氩搅拌方式,选择al
丸作为强脱氧剂,al脱氧后,配入的cao和mgo量并控制碱度,经底吹强搅拌,脱氧产物以a12o3夹杂形式存在钢液中,大幅增加钢液的中a12o3夹杂数量;添加高铝碱性精炼渣成分为:cao40%-60%,sio210%-20%,mgo6%-12%,a12o315%-25%,碱度r2-3.5,被渣吸附上浮去除,消除大尺寸的夹杂物,使钢中的夹杂物成分从复合夹杂物变成纯镁铝尖晶石夹杂物;不锈钢中p、s、si、al进一步降低,真空vod精炼使o、h含量进一步降低。
10.在本发明一个较佳实施例中,所述步骤a中lf钢包精炼中通过形成高含量mgo和a12o3渣系进一步去除钢中的o、h,再通过较弱的氩气搅拌一方面通过气泡去除10
µ
m或更小的夹杂物,另一方面小尺寸夹杂物相互碰撞、聚集、更快形成大颗粒的夹杂物,使夹杂物迅速上浮排除。通过al粉强化脱氧、渣系优化、钙处理和弱搅拌技术,使钢中铝含量控制为0.012-0.018%,从而保证氧含量≤0.0015%,h含量0.0002%-0.005%。
11.在本发明一个较佳实施例中,所述步骤b中在真空感应炉精炼,钢液控制在1620-1670℃,4-10pa的真空条件下,精炼15-21min,吹氩强搅拌,有效地降低c-o分压,降低碳氧积,使钢液成分均匀,通过钢液表面易于去除钢液中c、o、h以及低溶点杂质,然后调整钢液的金属成分,保证316l不锈钢中杂质降到最低并且成分均匀;钢液在炉内冷凝,停电降温不锈钢液至1450-1490℃时,对钢液进行冷凝处理,钢液中o、h等的溶解度降低,使钢液表面会出现解析的气体从钢液中释放出来;真空感应熔炼继续通电升温,再升温到稍高于不锈钢溶点的1545
±
10℃,在吹氩搅拌下,向钢中添加sio2、脱硫剂cao、mgo,低熔点高碱度渣系,按质量百分比为:cao45%,sio218%,mgo6%,a12o330%,碱度r2-3.0,加入时边加边搅拌,使渣进一步吸附上浮去除,使得钢液表面富集的o、s、h最终被有效脱除,在该温度下继续抽真空5
±
1min,真空度小于5pa,在钢液中mo、ca、c、al、p、s、si、as以及其它低熔点元素形成不同的化合物,通过渣附上浮去除。
12.在本发明一个较佳实施例中,所述步骤b中真空自耗重溶过程中,选用cao17%,sio22%,mg03%,a12o315%,碱度r1.0-1.5的低碱度精炼渣,化渣时加入的al粉,把渣液中的氧化性物质消耗掉,夹杂物去除是通过渣洗和在熔池中上浮;当自耗电极剩余重量为20%时,进行最后热封顶阶段,降低电流值且电流值逐渐降低至1.4-1.8ka,保证电弧不断并持续进行熔炼补缩,电压控制在22.0-25.0v,自耗电极熔化率控制在1.0-1.5kg/min,坩埚进水与出水温度控制在30-32℃,熔炼过程中全程通氩气保护,直至最后熔炼结束;对钢中的化学成分进会检验,o、h以及有害杂质元素超标时,必须进行第二次真空自耗电渣重溶,铸锭在真空条件下连续冷却至≤400℃后出炉。
13.在本发明一个较佳实施例中,所述步骤d中不锈钢荒管温度-转速匹配的热穿孔工艺技术参数满足以下条件:荒管规格≤直径65mm时,加热炉出口温度控制1160-1200℃,加热时间控制在140-160min,保温时间控制在15-28min,对应的60穿孔机变形速度控制在89-92转/min;荒管规格直径75-直径135mm时,加热炉出口温度控制1170-1220℃,加热时间控制在170-290min,保温时间控制在23-64min,对应的90穿孔机变形速度控制在74-77转/min,通过穿孔后管坯的浸入式快速冷却,由于管壁尺寸的减少使固态下铁素体相的在高温下回溶常温下的固溶体中,沿管壁厚度方向的铁素体含量进一步梯度减小,使管坯中残留的铁素体含量≤0.5%。
14.在本发明一个较佳实施例中,所述步骤e中采用二辊冷轧管机轧制时根据荒管晶粒度等级,对应相应的轧制变形延伸系数1.5-2.3,晶粒沿变形方向拉长成纤维状,位错密
度的逐步增加,使组织内的畸变程度提高,晶粒被压缩或拉长程度提高,晶粒形核驱动力及长大驱动力显著增大,充分的冷轧变形,避免管子出现晶粒不均匀,冷轧管变形延伸系数1.5-2.3,控制在减径率达32%-50%,减壁率达到30%-55%,与冷扩拔和轧相结合发挥冷轧管变形量大和冷扩拔生产灵活的优点,通过变形量的累积较大变形量,对奥氏体晶粒尺寸、形貌等进行调控,每道次一般延伸系数控制在1.05-1.7,控制在减径率达10%-40%,减壁率达到10%-48%,采用辊道式固溶热处理炉,固溶热处理温度控制在1100℃
±
10℃区间,在制品的保温时间控制在1.5-2.5*壁厚min,经多道次拔/轧制管变形量的累积,满足晶粒细化要求较大的变形量使管子晶粒更均匀;通过二辊精密冷轧管机,通过前道冷轧以或冷扩拔积累变形量,终轧管轧制时,还要满足其它综合性能要求,冷轧管精轧变形延伸系数相对细调,冷轧精密管变形延伸系数1.2-1.6,控制在减径率达12%-31%,减壁率达到12%-32%,管径尺寸公差控制在
±
0.05mm,晶粒度控制在5-7级,达到相应的外径和壁厚尺寸及公差要求范围内;终轧管固溶热处理:温度控制在1080℃
±
5℃区间,在保证管体长度和截面温度一致性下,使冷加工应力释放,采用全氢幅射管加热辊道式光亮固溶热处理炉,管子加热后快速冷却,晶粒得到有效调控,消除加工硬化,恢复其组织和性能,固溶温度控制在1080℃
±
10℃区间,成品的保温时间控制在1.0-1.5*壁厚min,使全部残留铁素体含量快速回溶到奥氏体不锈钢管中。
15.为解决上述技术问题,本发明采用的另一个技术方案是:提供一种集成电路及ic产业制备装置用超高洁净度不锈钢无缝管,通过上述的集成电路及ic产业制备装置用超高洁净度不锈钢无缝管的制备方法制得,成分组成以质量%计含有:c≤0.010%,p≤0.020%、s≤0.010%、mn≤0.10%、si≤0.30%、se≤0.010%、al≤0.010%、cu≤0.20%,cr16.50-17.00%、ni14.50-15.00%、mo2.20-2.50%、n≤0.010%、ni≤0.010%、ti≤0.010%;其余为fe和杂质,铬当量和镍当量组成元素含量进行调控,使creq/nieq当量控制在1.10-1.30。
16.本发明的有益效果是:本发明集成电路及ic产业制备装置用超高洁净度不锈钢无缝管的制备方法和超净高纯不锈钢无缝管,主要发生晶内孪晶变化以及位错的回复,从原始粗晶到更容易晶粒细化,细晶能提高力学性能,而且细晶可提高单位面积csl晶界,固溶热处理更容易保留的特点。经大量实验和研究,热加工过程中,使浇注中产生较粗的晶粒,经锻造开坯去除枝晶、反复锻打,再热轧制成钢棒,使锻造压缩比控制为3-5,热穿孔制管坯,开坯后的快速冷却,避免碳化物在晶界析出,再经多道次扩拔、轧管变形累积 固溶热处理,冷加工管中进一步调控使晶粒尺寸和形貌以及使碳氮化物完善熔于奥氏体不锈钢固溶体中,使晶粒得到细化。
17.通过经多道次冷轧或冷拔管变形累积及充分固溶热处理消除加工应力,使晶粒尺寸变细,在此基础上通过成品冷轧管加工形成细小晶粒尺寸,在成品热处理后形成更多密排面平行外表面的形貌结构,使耐晶间腐蚀性能提高。
18.冶炼时通过c元素和ni、ti元素的精确控制和匹配,控制精度达到
±
0.002%,使钢无晶间腐蚀的倾向。ti元素的加入会形成夹杂物,因此需要严格控制含量。调高ni、mo作为强碳化物形成元素,可提高热强性和腐蚀性能,减少钢中c在γ中溶解度,加速生成m
23
c6相;在范围内适度调高n元素含量,n元素在高温长效时有较强结合力,同时固溶于γ基体中能降低cr和c的扩散率,抑制m
23
c6粗化,起到固溶强化作用,显著地提高钢的抗疲劳和断裂韧
性性能。提高316l不锈钢无缝管在650℃*2h敏化态时抗晶间腐蚀能力。
19.在满足镍当量在范围内的情况下,通过小变形冷轧和固溶热处理工艺控制,使碳化物充分固溶于奥氏体不锈钢中,满足晶间腐蚀敏化试验基本要求。
具体实施方式
20.下面将对本发明实施例中的技术方案进行清楚、完整地描述。
21.集成电路及ic产业制备装置用超高洁净度不锈钢无缝管,在冶炼时每吨钢中可吸收大约200g的气体。使管材表面粘有各种污染物,其金属晶格内也吸留有一定量的气体。当管路通气时,管内壁表面吸留这部分气体会重新进入输送气体中,污染超纯净化工业气体。当管内气流不流动时,管材内气体在压力下又吸附,气流停止时,管材所吸附的气体又形成降压解析,而解析的气体同样作为杂质进入管内纯净工业气体中。同时,吸附、解析周而复始,使得管材内表面金属也会产生一定的微小颗粒,这种不锈钢微小颗粒会污染管内纯净气体,从而影响半导体制备的良品率。同时,有些输送的腐蚀性的气体在内表面会对高纯气体输送管道带来表面腐蚀。因此,为满足半导体制备装置输送超高纯气体一般选用超高纯净316l不锈钢管。
22.要求所使用的超高洁净度不锈钢无缝管,不锈钢材料要高纯净化,选用316l不锈钢的基础上,根据半导休制备装置输送超高洁净管道的具体要求,首先是c含量控制到最低,c≤0.010%,还要求材料中的杂质p≤0.02%、s≤0.010%、mn≤0.10%、si≤0.30%、al≤0.010%、h≤0.0002%,o≤0.0015%等有害元素尽可能最低;cr16.50-17.00%、ni14.50-15.00%、mo2.20-2.50%、cu≤0.20%、n≤0.010%;成分达到gb/t222钢的成品化学成分允许偏差要求;为确保不锈钢成分中合金元素的精确控制,特别是对非金属夹杂物要严格控制,铁水三脱预处理后,eaf溶炼、在k-obm-s转炉和真空脱碳vod炉,炉外lf精炼、将不锈钢中的p、s、mn、si、cu等有害元素以及o、h等降低到80%以上,再通过真空感应熔炼(vim)和真空电弧再熔化(var)处理、锻造和热轧、热穿孔、冷加工到规定的尺寸规格。所得的不锈钢无缝管纯度高,奥氏体金相组织均匀一致。通过严格冶炼控制的316l不锈钢在电解抛光和纯化处理效果最佳,经电解抛光处理后在洁净厂房完成管子的检验和包装,保证出厂的316l不锈钢管除满足管材力学、理化等相关指标要求外,还必须达到管子超高洁净度要求。
23.为了达到上述目的,对316l不锈钢无缝管优选化学成分组成,各元素的含量(%)表示质量%。
24.在316l不锈钢的基础上,添加n提高铁素体当量、碳含量降到最低,严格控制cr,ni,mo元素偏差,同时考虑不锈钢纯净化精炼工艺,把杂质元素p、s、mn、si、al,以及气体元素h、o等有害元素尽可能调控到最低,可影响持久强度、疲劳强度的o、h含量加以控制,降低对输送气体的污染,通过vod冶炼、真空var炉和真空压炉精炼把有害元素控制到最低,从而满足表面质量、力学性能等综合性能要求。
25.材料的化学成分决定其组织与性能,优选奥氏体不锈钢化学成分组成,实现对组织性能的精确控制。
26.c:c≤0.010%,c是一种间隙元素,也是强烈的扩大奥氏体区域元素,其镍当量为30,c对增加奥氏体不锈钢的强度作用非常明显,但由于c与cr非常容易化合生成碳化铬,造
成奥氏体晶界贫铬,显著降低抗晶间腐蚀性能。因此降低含c量是防止晶间腐蚀最有效的措施。同时,由于本c含量的波动范围对奥氏体不锈钢的当量值的影响较大。c含量增加能提高力学性能,但形成的碳化物析出,使晶格留有一定量的气体,从而影响输送气体纯度。含c过高的不锈钢管在焊接时,受焊接部位的透气,使得管内外气体的相互渗透,破坏输送气体的纯度、干燥度和洁净度,因此,c含量控制在≤0.010%的范围。
27.si:si≤0.30%,si是强铁素体形成元素,不锈钢熔炼时有脱氧作用。对钢的力学性能的作用是提高奥氏体不锈钢的强度、弹性极限、屈服强度和屈强比;同时在钢表面形成细小弥散分布的sio2颗粒,细小颗粒会污染管内纯净输送气体提高抗氧化性。si含量控制在≤0.30%的范围。
28.mn:mn≤0.10%,mn是奥氏体相稳定化的元素,且抑制s所导致的热加工脆性以及溶炼时的脱氧有效元素。在不锈钢中溶炼时mn和s形成mns,钢中锰量增加,会mns量增加,mns夹杂在腐蚀气体中引起点蚀、缝隙腐蚀等。另外,mn在cr、mo不锈钢中还会促进σ相等脆性相的析出,降低钢的塑、韧性。因此,mn含量控制在≤0.10%的范围。
29.cr:16.50-17.00%,cr是铁素体形成元素。在奥氏体不锈钢中固溶于fe基体中,使基体电极电位提高,通过形成一层致密的cr2o3保护膜,阻碍金属离子的向外扩散以及氧原子的向内扩散。但cr是铁素体元素,cr与fe形成连续固溶体,缩小奥氏体相区。缩小cr含量的偏差,可精准地调控cr/ni当量比。因此,cr含量控制在16.5
〜
17.0%的范围。
30.ni:14.50-15.00%,ni含量的提高,扩大奥氏体相区的元素,它能提高奥氏体不锈钢的电位和纯化倾向。为了把钢中铁素体含量控制在≤1%,随着镍含量的增加,高温下的凝固模式逐渐向全奥氏体凝固模式转变。ni在钢中能抑制σ相形成,在一定程度上促进cr2n相的形成。缩小ni含量的偏差,可精准地调控cr/ni当量比,ni含量控制在在14.50-15.00%的范围。
31.mo:mo2.20-2.50%,mo为难熔金属,是稳定铁素体元素,能提高奥氏体不锈钢抗点蚀腐蚀能力。mo还具有抑制cr碳化物的晶界析出的作用。可减少c在奥氏体不锈钢中溶解度,加速cr
23
c6的生成。但过多mo会促进高温下σ相的析出,导致脆性;同时因为mo是一种贵重金属,太高的mo含量会导致成本增加。因此,mo含量控制在2.20-2.50%的范围。
32.p:p≤0.02%,p能促进晶界腐蚀,且引起晶界强度降低,在输送气体中腐蚀性劣化。因此,p含量控制在≤0.02%的范围。
33.s:s≤0.010%,使晶界腐蚀且引起晶界强度的降低,s含量优选≤0.0010%的范围。
34.n:n≤0.010%,n是强烈的扩大奥氏体区域元素,其镍当量为30,在钢中能发挥固溶强化和降低堆垛层错能,增加奥氏体组织的稳定性,抑制碳化物析出和延缓σ(χ)相折出。可以提高固溶态奥氏体不锈钢的硬度和耐蚀性。氮在奥氏体不锈钢中能降低cr和c的扩散率,有助于抑制cr23c6粗化。因此,n含量控制在≤0.010%的范围。
35.cu:cu≤0.20%,cu是奥氏体稳定元素,冶炼时不锈钢中进入cu元素,可以提高奥氏体不锈钢的晶粒边界腐蚀能力和耐蚀性。但cu在高温时效后不锈钢中形成大量细小弥散富铜。在热加工、焊接过程中易产生裂纹,钢中含量需要严加控制。因此,cu含量控制在≤0.20%的范围。
36.al:al≤0.010%,al是铝与氧和氮有很强的亲和力,是炼钢时的脱氧定氮剂,当钢中的固溶金属铝含量超过一定值时,奥氏体晶粒容易长大粗化,必然加以严格控制。因此al
含量控制在≤0.010%的范围。
37.nb:nb≤0.010%,nb是强碳化物稳定元素,nb在不锈钢以nbc,nb(cn)的形式存在,析出物质点的“钉扎”作用可防止晶界发生移动,与溶质nb原子的拖曳作用,避免再结晶,从而细化晶粒。增加了不锈钢的强度和耐晶间腐蚀性能。因此nb含量控制在≤0.010%的范围。
38.ti:ti≤0.010%,是强碳化物形成元素,在钢中强脱氧剂,易形成夹杂物。还能使钢的内部组织致密,细化晶粒;降低时效敏感性和冷脆性。能提高钢的耐晶间腐蚀能力,因此,ti含量严格控制在≤0.010%的范围。
39.se:se≤0.010%、se与fe形成化合物在钢的溶解度很低,在钢中形成硫化物夹杂以及导致的mn、ti、zr等有效含量及钢的淬透性下降,硒化物颗粒较硫化物更为细小和分散,在半导体高纯气体管道表面会产生微小颗粒。se含量严格控制在≤0.010%的范围。
40.o:o≤0.0015%,o是不锈钢炉外精炼后残留在钢中。o对钢的性能影响主要与氧化夹杂物的组成、性质、分布和数量有关,所有夹杂物都在不同程度上降低钢的塑性、韧性和疲劳强度,特别是在输送高纯气体中释放造成气体污染,应作为有害元素来控制。因此,o含量控制在0.0015%的范围。
41.h:h≤0.0002%,h是不锈钢炼钢后残留在钢中,是有害元素,应尽量降低钢中的h含量,防止由h造成的各种缺陷和性能下降,特别是对钢的使用疲劳强度和寿命影响较大。在输送高纯气体中释放造成气体污染,因此,h含量控制在≤0.0002%的范围。
42.关于成分控制和优化方法,金属成分决定不锈钢无缝管的组织和性能。
43.集成电路及ic产业制备装置用超高洁净度不锈钢无缝管及制造方法,成分组成以质量%计含有:将成分组成以质量%计含有:c≤0.010%,p≤0.02%、s≤0.010%、mn≤0.10%、si≤0.30%、cu≤0.20%,al≤0.010%,h≤0.0002%,o≤0.0015%,cr16.50-17.00%,ni14.50-15.00%,mo2.20-2.50%,n≤0.010%;在316l的成分基础上,调控元素含量,控制铁素体含量≤1%,提升半导体制备装置用高洁净度管材服役要求。为提高钢的超高洁净度,且其余为fe和不可避免的杂质组成的原材制成的预定尺寸的不锈钢无缝钢管,外径为直径9.53mm-直径76.2mm。
44.基于316l不锈钢基材基础上,铬当量和镍当量组成元素含量进行调控,使creq/nieq当量控制在1.10-1.30内,减少了钢中的铁素体含量。再通过控制冶炼过程中浇注钢水过热度、锭坯凝固过程冷却强度、自耗重溶结晶器冷却温度、固态下铁素体相的高温热处理回溶技术,彻底消除不锈钢无缝管内的残余铁素体,使成品316l不锈钢无缝管铁素体含量为0%。
45.为了解决钢中铁素体含量控制在≤1%,因316l奥氏体不锈钢基体结构中,有mo、cr、si等铁素体形成元素和ni、mn、c、n、cu等元素奥氏体形成元素等组成,通常316l不锈钢无缝管都会有一定数量的铁素体(δ铁素体含量为3%-15%)。奥氏体不锈钢无缝管金属凝固时,控制铁素体含量主要是控制铬当量和镍当量的比值,即creq/nieq,通过调整成分(铬镍当量比)来调整最终奥氏体不锈钢无缝管的铁素体含量。
46.creq当量=16.5%cr 1.5*2.2%mo 1.5*0.1%si=19.8%nieq当量=14.8%ni 0.5*0.10%mn 30(0.01 0.01)%(c n) 0.3*0.20%cu=15.51%creq/nieq当量比=19.8
÷
15.51=1.27。有效地提高了316l不锈钢的组织预测准确
性,creq/nieq当量控制在1.10-1.30,后续通过316l热轧、热穿孔及固溶热处理,使钢中残余铁素体回溶奥氏体不锈钢组织中,奥氏体不锈钢回溶技术把铁素体降到最低。
47.,316l不锈钢通过奥氏体形成元素的细调,使不锈钢结晶模式为先奥氏体模式,钢液凝固时先产生奥氏体相保证先结晶折出γ奥氏体初相,然后发生l γ δ,最后凝固成γ δ,在晶界产生δ铁素体组织。通过铬镍当量比的调控,从关键形成ni奥氏体元素的含量上细调,添加氮使奥氏体形成元素含量增加,从而降低creq/nieq当量比,钢中铁素体含量显著下降。
48.,316l为18-10不锈钢属于亚稳态结构,在凝固组织中必然存在一定量的高温铁素体。通过钢液凝固过程中铁素体相的析出行为和固态下铁素体相的高温扩散行为的研究,通过优化钢水冷却过冷度以及提高冷却强度,使得钢中的铁素体含量显著降低。同时在钢锭的热轧过程中,通过锻造工艺优化,使残留在钢锭中的铁素体相,通过高温固溶热处理,使残留的铁素体相充分回溶于常温下的奥氏体组织中,使钢中的铁素体含量要控制在≤1%。
49.基于不锈钢加工过程晶粒度控制技术,在从热轧到成品轧制过程中,通过压缩变形及固溶热处理(晶界工程处理),从锻造—热轧—热穿孔—中间品冷加工(轧制变形 过程固溶热处理)—成品冷加工(冷轧或冷拔 成品固溶热处理)的一体化晶粒细化工程处理关键技术,主要发生晶内孪晶变化以及位错的回复,从原始粗晶到更容易晶粒细化,细晶能提高力学性能,而且细晶可提高单位面积csl晶界,固溶热处理更容易保留的特点。经大量实验和研究,热加工过程中,使浇注中产生较粗的晶粒,经锻造开坯去除枝晶、反复锻打,再热轧制成钢棒,使锻造压缩比控制为3-5,晶粒度达到3级甚至更细。热穿孔制管坯,开坯后的快速冷却,避免碳化物在晶界析出,再经多道次扩拔、轧管变形累积 固溶热处理,冷加工管中进一步调控使晶粒尺寸和形貌以及使碳氮化物完善熔于奥氏体不锈钢固溶体中,使晶粒得到细化。建立热轧穿孔和冷加工联合变形的许用变形量与轧制成形工位数之间的关联函数,掌握了不锈钢管材穿轧联合制备过程各工位间载荷与变形量的分配规律,制定了合理调整穿轧变形量分配,变形量累积和匹配的固溶热处理技术,使晶粒得到了细化且组织均匀一致,晶粒度控制在5-7级。
50.,表面氧化膜生长密度对晶体取向有很大的关系。为了提高晶粒度等级和晶间腐蚀综合性能,对不同晶面氧化速率分析,更高堆垛密度的晶粒氧化更强烈。钢的溶解速率与原子堆垛密度成反比,密排面的溶解速度小,钢中密排面上氧化膜生长速度更强,通过经多道次冷轧或冷拔管变形累积及充分固溶热处理消除加工应力,使晶粒尺寸变细,在此基础上通过成品冷轧管加工形成细小晶粒尺寸,在成品热处理后形成更多密排面平行外表面的形貌结构,使耐晶间腐蚀性能提高。
51.降低钢中c含量,可显著地减少m
23
c6相数量,但降低钢的强度,而微量化加入稳定元素ni、ti能固定钢中游离c、n元素,提高抗晶间腐蚀性能,冶炼时通过c元素和ni、ti元素的精确控制和匹配,控制精度达到
±
0.002%,使钢中无晶间腐蚀的倾向。同时控制冷轧管单次变形量,合适的终轧变形量在固溶热处理后不产生大量随机晶界产生,使晶界之间发生相互反应生成大量低能晶界,网格联通性进一步弥散化,从而提高抗晶间腐蚀性能。因此,通过多道次轧制的累积使晶粒细化的同时,提高316l不锈钢无缝管在650℃*2h敏化态时抗晶间腐蚀能力。
52.考虑到后续半导体制备管道安装需要焊接,焊接热影响区会影响敏化,要求316l不锈钢无缝管具备650℃*2h敏化态晶间腐蚀能力。按照经典冶金物理理论,降低c含量在高温时减少m
23
c6相数量,但降低钢的强度,而加入微量稳定元素ni、ti能固定钢中游离c、n元素,提高抗晶间腐蚀性能,冶炼时通过c元素和ni、ti元素的精确控制和匹配,控制精度达到
±
0.002%,使钢无晶间腐蚀的倾向。ti元素的加入会形成夹杂物,因此需要严格控制含量。调高ni、mo作为强碳化物形成元素,可提高热强性和腐蚀性能,减少钢中c在γ中溶解度,加速生成m23c6相;在范围内适度调高n元素含量,n元素在高温长效时有较强结合力,同时固溶于γ基体中能降低cr和c的扩散率,抑制m
23
c6粗化,起到固溶强化作用,显著地提高钢的抗疲劳和断裂韧性性能。提高316l不锈钢无缝管在650℃*2h敏化态时抗晶间腐蚀能力。
53.为满足力学性能、晶粒度、晶间腐蚀、铁素体含量、表面质量的综合性能要求,按微合金化316l不锈钢的设计思路、对钢中合金元素进行优化并精确控制,适应非金属夹杂物纯净化冶金技术、满足多指标控制和协同,再通过完全奥氏体组织的不锈钢材料热加工工艺、中变形冷轧量和匹配的固溶热处理工艺控制,使碳化物充分固溶于奥氏体不锈钢中,满足力学性能、晶粒度、晶间腐蚀、铁素体含量、表面质量的基本要求。
54.超高洁净度的奥氏体316l不锈钢既要达到规模化、大批量制造要求,又要满足高纯净不锈冶炼,主要采取的工艺流程:三脱预处理铁水 低杂质合金元素兑入k-obm-s冶炼
→
vod精炼
→
lf钢包精炼
→
真空感应熔炼(vam)
→
真空自耗精炼(var)v/v。
55.不锈钢精炼工艺:首先通过三脱预处理的铁水和添加合金在eaf电炉初炼,出钢温度为≥1670℃,钢液成分均匀,制造成不锈钢预熔液;然后在k-obm-转炉上预吹氧,沸腾脱碳强低吹搅拌控制,使c≤0.9%;通过vod炉精炼,添加高铝碱性精炼渣系,使渣附于钢表面,使al≤0.03%,氧含量≤0.0030%以下;接着,lf炉精炼,通入较弱氩气搅拌,气泡去除小尺寸夹杂物,钢中铝含量控制为0.012-0.018%,从而保证氧含量0.0011%-0.0020%,h含量0.0005%-0.0010%,同时,使钢中非金属夹杂物细化且弥散分布;合理控制浇注过热度,控制好凝固过程。
56.,铁水通过脱s、脱si、脱p的三脱预处理,冶炼时对杂质元素进行去除,可减少炼钢过程中除去硅、磷所需的石灰造渣料,减少渣量,使s含量减少到0.05-0.06%,si含量减少到0.3-1.0%,p含量减少到0.14-0.3%,钢液的c含量为4%-6%,减少后续冶炼处理有害元素的难度。
57.,采用eaf电炉熔化合金和三脱预处理铁水兑水k-obm-s转炉,钢液温度为t≥1450℃。避免在转炉吹炼时降温过多。
58.,k-obm-s转炉冶炼开始时预吹氧,采用大氧量调整吹炼,沸腾脱碳强低吹搅拌控制,把冶炼温度提高到t=1700℃左右,脱去大部分碳。当碳含量≤1.20%时,采用顶吹氮气,控制钢液温度,低吹氧气和强搅拌,在调整脱碳时,能够有效地抑制cr的氧化。
59.如上所述,k-obm-s转炉主要采取强搅拌顶吹氧气和底吹氧气,和氮气(氩气)脱碳,提高脱碳速率减少cr损失,预吹氧和沸腾脱碳强底吹搅拌控制,合理控制过程真空度。通过控制合理的不锈钢炉渣渣系,使夹杂物控制在低熔点范围,促进夹杂物快速上浮去除和添加ni合金,使温度保持在1680-1750℃。脱c速率0.15-0.3%min,合理控制钢中c含量,减少vod冶炼脱c压力。同时,使p、s有害元素等得到去除。出钢时采用档渣出钢,提高钢的洁净度。
60.为满足超低o含量和夹杂物细小化的要求,,在vod炉钢水入罐后,调节氩气流量到钢液微翻转后合盖,流量控制在12-25nl/min,抽真空真空度控制在15kpa左右,氧枪枪咀到液面高度调整到900
±
100mm。首先开始约2分钟高碳区吹氧脱硅和脱小量碳。随后开始脱碳。吹氧时氧压控制0.37-0.42mpa,流量为120m3/h,平均脱碳速度0.0188%-0.0125%∕min,采用强吹氩搅拌方式,底部吹氩强度达到0.01-0.02nm3∕(t.min)可显著地提高脱碳速度和减少铬的氧化损失。为使钢中c含量降低,在达到c含量为0.08%后再在停氧高真空度下强低吹搅拌脱h、o、n,适当降低真空度,脱碳时间控制在15-30min。
61.为使钢的夹杂物细小化、弥散化,在真空vod精炼化渣时,氩气流量30-60nl∕min,低真空化渣时间控制在≥10min。首先在钢中,选择了脱氧效果好的al丸作为强脱氧剂,通过添加(含量≥99.7%)脱氧铝丸,保证钢的脱氧量。al脱氧后,配入的cao和mgo量并控制碱度,经底吹强搅拌,脱氧产物以a12o3夹杂形式存在钢液中,大幅增加钢液的中a12o3夹杂数量。通过添加高铝碱性精炼渣成分为:cao40%-60%,sio210%-20%,mgo6%-12%,a12o315%-25%,碱度(r)2-3.5,被渣吸附上浮去除,消除大尺寸的夹杂物,使钢中的夹杂物成分从复合夹杂物变成纯镁铝尖晶石夹杂物。不锈钢中p、s、si、al等有害元素进一步降低,同时真空vod精炼使o、h含量进一步降低。
62.在lf钢包精炼中通过形成高含量mgo a12o3渣系进一步去除钢中的o、h,再通过较弱的氩气搅拌一方面通过气泡去除10
µ
m或更小的夹杂物,另一方面小尺寸夹杂物相互碰撞、聚集、更快形成大颗粒的夹杂物,使夹杂物迅速上浮排除。通过al粉强化脱氧、渣系优化、钙处理和弱搅拌技术,使钢中铝含量控制为0.012-0.018%,从而保证氧含量≤0.0015%,h含量0.0002%-0.005%,达到了316l钢的超低氧和夹杂物细小化,弥散化精炼要求,显著地提高钢的纯净度以及提高力学性能、断裂韧性和疲劳强度。
63.计算出316l不锈钢钢液液相线温度,合理控制连铸过热度。vod真空精炼结束后,然后实施密封连铸,防止大气污染,使包内气氛中氧含量≤0.1%,连铸过程在钢水增氮,控制凝固过程,减少凝固过程的铁素体形成数量,有效地控制了宏观偏析及枝晶间的偏析。做好保护渣吊桂,保证全密闭保护罩使用效果。
64.为满足后续真空感应熔炼要求,铸锭的外观尺寸必须符合相应要求,出模后需对铸锭表面进行打磨,使表面光滑,去除各种缺陷和杂质。
65.,为满足晶间腐蚀试样试验要求,在满足镍当量在范围内的情况下,通过小变形冷轧和固溶热处理工艺控制,使碳化物充分固溶于奥氏体不锈钢中,满足晶间腐蚀敏化试验基本要求。
66.真空感应vim和真空自耗电渣重溶(var)工艺:var的对升温溶化、高真度下吹氩强搅拌的精炼,去除c、h、o及低溶点杂质,再通过停电炉内冷凝使o、h进一步从钢液中释放。继续通电升温在吹氩搅拌下,向钢中添加低溶点高硬度渣系,使钢液表面富集s、h、o,同时低溶点元素形成不同的化合物,被渣去除。把var溶炼的钢锭作为真空自耗重溶的电极,在电极溶化形成液滴/渣洗凝固过程中,使钢进一步纯净化,同时控制钢中坩埚的冷却水温度,使铁素体含量控制≤0.5%。对重溶后对钢化学成分进行检验,假若不合格,采取二次真空自耗电渣重溶,钢中h≤0.0002%,o≤0.0015%。
67.为满足超高纯净316l不锈钢综合性能要求,真空感应熔炼炉(vim)的工艺流程:装炉
→
升温熔化
→
保温精炼
→
冷凝
→
脱氧、脱硫期
→
浇注。
68.采用cao坩埚,减少坩埚供氧,熔化真空感应炉(vim)装料熔化时,开始以较低的功率加热炉料至发红,然后在一定真空度下,大功率尽快熔化炉料,熔化速度控制在1500kg/h,控制钢反应终点温度控制在≤1650℃,熔化期在真空条件下进行,为获得熔化期内碳脱氧效果,不加保护性气氛,仅通过真空阀门的关闭来有效地控制碳-氧反应的程度,并使溶化过程正常进行,从而脱碳脱氧的目的。同时进行采样为精炼期调整合金化学成分作准备。
69.真空感应炉(vim)精炼,钢液控制在1620-1670℃,4-10pa的真空条件下,精炼15-21min,在吹氩强搅拌下,开动全部高真空泵进行抽气,提高真空度,在高温、高真空度条件下,有效地降低c-o分压,从而降低碳氧积,在调整好化学成分后,以再进行搅拌一定时间,使钢液成分均匀,通过钢液表面易于去除钢液中c、o、h以及低溶点杂质,然后调整钢液的金属成分,保证316l不锈钢中杂质降到最低并且成分均匀。
70.通过停电使316l不锈钢在(vim)炉内冷凝,停电降温不锈钢液至1450-1490℃时,对钢液进行冷凝处理,钢液中o、h等的溶解度降低,使钢液表面会出现解析的气体从钢液中释放出来。
71.真空感应熔炼(vim)炉继续通电升温,再升温到稍高于不锈钢溶点的1545
±
10℃,在吹氩搅拌下,向钢中添加sio2、脱硫剂cao、mgo,低熔点高碱度渣系,按质量百分比为:cao45%,sio218%,mgo6%,a12o330%,碱度(r)2-3.0,加入时边加边搅拌,使渣进一步吸附上浮去除,使得钢液表面富集的o、s、h最终被有效脱除。在该温度下继续抽真空5
±
1min,真空度小于5pa,在钢液中mo、ca、c、al、p、s、si、as以及其它低熔点元素等形成不同的化合物,通过渣附上浮去除。
72.经大量实验和研究,钢液中吸氮速率随氮的分压的增大而增大,溶解度随温度的降低而升高。对钢液中氮含量进行检测,根据实际氮含量,再确定实际的吹氮压力和时间,吹氮压力控制在50-100kpa,吹氮时间控制在5-30min。超低碳不锈钢需要通过增氮来调控力学性能,因此氮含量尽量控制在偏差的上限。
73.浇注是316l不锈钢熔炼最后一道程序,为了获得高质量的316l不锈钢锭,应选择合适的较低浇注温度,1450-1480℃之间,降低钢液凝固过程中锭坯的冷却速率,降低铁素体的含量且尺寸小,锭坯中心到边部冷却温度是呈梯度衰减,芯部铁素体含量高且尺寸大,从优化凝固速度方面入手,使钢锭芯部铁素体得到有效控制。再经过两层挡渣和陶瓷过滤保证钢水的纯洁度,提高钢水洁净度。以保证不锈钢铸锭表面光洁及内部无缩孔。生产出直径直径550mm、重量达6吨的优质真空316l棒料。
74.经真空感应熔炼炉精炼后,钢中的杂质元素含量明显降低,有利于铸锭杂质元素的控制,有利于熔炼过程电极溶化的均匀性。把铸锭进行表面打磨清理,把铸锭加工成var熔炼用自耗电极。
75.自耗电极设置于真空自耗炉的升降主轴下端并输送至真空自耗炉坩埚内,电极x-y调整系统,可保证熔炼环隙一致。真空炉密封整个熔炼过程真空度保持在0.08pa;如上所述,真空自耗炉(var)通电使得自耗电极与坩埚底部预设的起电弧剂之间产生弧光放电,渣料完全的融化均匀并保证需要的温度,有效改善电渣锭起弧段的表面质量。形成熔池后,将熔炼功率逐渐提高,在随后的熔炼阶段,电压控制在30.0-44.0v,电流控制在2.0-2.4ka,自耗电极熔化率控制在1.0-2.0kg/min,通过控制底水箱和结晶器的进水量来保持渣液的温度,改善表面质量,减少电耗。电渣锭结晶器冷却水流量调大,坩埚进水
与出水温度为30-35℃,保证对渣液有足够的热量供给和保证真空自耗重溶过程中熔速稳定,钢中铁素体谁是明显降低,表面质量好。氦气冷却和急流层水套的设计,控制合金元素的偏析,增加了电渣电流与底水箱铜板导电的有效性,可最大限度的减少钢锭偏析;优化补缩工艺,保证电渣锭的头部有足够的钢液补充,减少缩孔,提高成材率。
76.自耗电炉电渣重熔在自耗电极熔化形成液滴/渣洗这一凝固的过程中,发生一系列的冶金反应。在316l的重熔工艺制度下,在真空自耗重溶过程中,选用cao17%,sio22%,mg03%,a12o315%,碱度(r)1.0-1.5的低碱度精炼渣,其锭坯重熔前后的化学成份发生不同程度的变化,将精炼渣成分控制在低溶点范围内显著提升钢的纯净度。在化渣时加入一定量的al粉,把渣液中的氧化性物质消耗掉,夹杂物去除是通过渣洗和在熔池中上浮,真空自耗重熔可以改善钢的铸态组织,减少成分偏析。当自耗电极剩余重量为20%时,进行最后热封顶阶段,降低电流值且电流值逐渐降低至1.4-1.8ka,保证电弧不断并持续进行熔炼补缩,电压控制在22.0-25.0v,自耗电极熔化率控制在1.0-1.5kg/min,坩埚进水与出水温度控制在30-32℃,熔炼过程中全程通氩气保护,直至最后熔炼结束。
77.进行第二次真空自耗电渣重溶,主要控制如上所述,使钢中的杂质元素c、si、mn、al、cu、p、s等有害元素和o、h控制到最低点。真空自耗重溶过程的焊接、起弧、熔炼、充填在内的重溶过程实现计算机控制,保证金属化学成分精确控制。实时记录并生成趋势图,可即时观察及自动储存,保持了产品永久的可追溯性。
78.铸锭在真空条件下连续冷却至≤400℃后出炉。
79.通过自耗电极在直流电弧的高温作用下迅速熔化,并以液滴的形式在水冷铜坩埚内凝固成铸锭,使316l不锈钢的成分均匀性,改善结晶结构和铸锭质量,减少铸锭头部的缩孔与疏松区,提供了超高洁净度的不锈钢铸坯。同时,不锈钢低h、o以及al、p、s杂质含量低的精炼技术、实现ds类夹杂物细化及弥散分布。
80.通过真空感应(vim)和真空自耗重溶(var)过程钢液非平衡凝固过程中铁素体相的析出行为和固溶态下铁素体相的高温扩散行为分析,锭坯表面冷却强度大铁素体含量低且尺寸小,锭坯内部不易温度扩散冷却强度低于锭坯表面。优化钢水的过热度、以及电渣锭结晶器冷却水流量,使得铁素体含量明显下降。
81.经预三脱预处理的铁水和低杂质元素合金
→
k-obm-s转炉
→
vod精炼
→
lf钢包精炼
→
真空感应熔炼(vam)
→
真空自耗精炼(var)v/v的超高纯净化冶炼过程,采取不同渣系以及不锈钢的超低氧和夹杂物细小化、弥散化精炼技术, vod的硅脱氧工艺消除钢中大尺寸的夹杂物, lf配制高含量mgo al2o3渣系并使用强铝镁脱氧,使夹杂物由复合夹杂物变成纯镁铝尖晶石夹杂物;、真空感应熔炼的sio2、脱硫剂cao、mg0,低熔点高碱度渣系以及直空自耗电渣重溶的低碱度精炼渣系,使316l不锈钢中非金属夹杂物被渣附近上浮去除,同时,使钢中o、h超低含量和ds类夹杂物细小化、弥散化,达到半导体制备装置用316l钢种非金属夹杂物的纯净化要求。
82.不锈钢锻造工艺:采用钢锭锻造 连续钢棒轧制法制造圆管坯。通过工艺仿真及分析的基础上,利用现有室式炉天然气加热、快锻和热轧制钢棒制造技术,通过锻件全尺寸温度场与应变场耦合控制,消除锻造枝晶及相尺寸细化,铁素体含量降低,力学性能显著提高,硬度hv≤200的的组织。
83.钢锭在4m*6m的室式炉内加热,锭子底部垫耐火砖使锭与炉底留有空隙,这样可使
锭的加热更均匀。加热制度遵循升温时缓慢加热,避免表面出现加热温度过高,而内部还没有达到要求的温度。在均热段时把加热时间和保温时间上均延长。温度控制,热塑性加工温度为1100-1180℃,在锻造时考虑到温降与变形方式以及加热的火次,终锻温度过低会引起不完全再结晶,导致晶粒大小不均的混合晶粒组织,终锻温度要求≥920℃,否则均需要及时回炉。
84.初锻的过程中要轻击,要边锤边滚在25mw快锻机快速破碎表面柱状晶,以小变形为主来控制变形量,当表面柱状晶破碎并且变形量大于30%之后,在温度适当的情况下加大锻造变形量。一火变形程度低会落入临界变形区,也会导致晶粒度不均。在最后一火进行滚圆,此时控制临界变形量大于15%来保证组织均匀。锻造总压缩比3-5。钢锭锻造后回炉继续加热,达到1160℃
±
20℃并使锻坯内外沿横向截面温度保持一致性,避免外部达到温度而内部未达到变形温度而产生各种缺陷。
85.不锈钢锻坯在加热制度下,在棒材轧机轧制成不锈钢棒材轧制成直径65mm、直径115mm和直径135mm规格钢棒,外径公差控制到
±
0.1mm,椭圆度≤0.12mm。锻造和轧制过程中控制加热温度和变形量,提高压缩比技术工艺控制,使锻造总压缩比3-5,以便获得均匀的晶粒组织和消除钢中的铁素体。
86.热穿孔处理工艺:对斜底炉各温度段的升温曲率、保温时间、翻缸次数工艺参数的调控,使加热温度为1160℃-1220℃,加热时间控制在140-290min,保温时间15-64min,对大碾角斜轧穿孔所对应的应力应变场和温度场和顶头穿孔过程温度场变分析和调控形成热穿孔成形与组织性能协同控制,生产出合格的荒管。为满足超高纯净316l不锈钢管的力学性能、晶粒度、晶间腐蚀,建立许用变形量与轧制成形道次之间相匹配,掌握了热穿孔和冷轧变形量分配与性能调控规律,满足力学性能、耐晶间腐蚀、晶粒细化的超高纯净不锈钢成品管材条件。建立热穿孔—中间冷轧—成品道次冷轧关系函数及相应匹配模型及变形量分配,形成热穿孔—高温中间固溶热处理、变形量及分配的一体化冷变形调控关键工艺。通过较高中间固溶热处理温度进行软化,为后续的成品冷轧管加工作准备。为此,以轧管变形与组织性能要求为约束条件,结合轧制硬化效应、硬化梯度分布及道次传递作用,形成冷轧成形变形量及分配工艺,合理分配每道次加工变形量。
87.圆钢的前道处理,采用旋风切削量1.5mm-3mm,锯成相应规格管坯重量的圆钢,在一头打v形定心孔,圆钢外表面检查、发现表面发纹等缺陷用手持砂轮机磨除,对钢棒进行清洗,清除表面残留的皂化液、油污等,保持钢管表面清洁;不锈钢热穿孔是实心管坯在多因素协同作用下向空心荒管转变过程,基于热穿孔过程中温度-应力应变多场耦合的数字化模型。在热穿孔的过程中,圆管坯从实心向空心转移过程中内部发生了多物理场的交互作用,精确地模拟热穿孔过程多耦合条件下提升工艺特性行为,在此基础上建立斜底炉加热工艺制度,增加翻钢频次,保证不锈钢圆钢内外加热温度的一致性,避免变形温度和内外温度一致性控制不当,极易导致在相界裂纹成核和扩展,避免穿孔裂纹的发生。
88.如上所述,基于超高纯净316l不锈钢不同口径的热穿孔特性,通过优化炉窑加热的各段的升温曲率及时间等工艺参数,并结合大碾角斜轧热穿孔应力应变场和温度场和顶头穿孔过程中温度场变化分布特征,实现热穿孔成型与组织、性能协同控制的高质量热穿孔,通过合理选择穿孔工艺参数,如坯料加热温度、保温时间、导板距、轧辊距、轧辊转速等,
尽量降低穿孔变形区的不均匀变形及其产生的附加拉应力。达到生产高效率及高成材率。不锈钢荒管温度-转速匹配的热穿孔工艺技术参数满足以下条件:荒管规格≤直径65mm时,加热炉出口温度控制1160-1200℃,加热时间控制在140-160min,保温时间控制在15-28min,对应的60穿孔机变形速度控制在89-92转/min;荒管规格直径75-直径135mm时,加热炉出口温度控制1170-1220℃,加热时间控制在170-290min,保温时间控制在23-64min,对应的90穿孔机变形速度控制在74-77转/min。同时,通过穿孔后管坯的浸入式快速冷却,由于管壁尺寸的减少使固态下铁素体相的在高温下回溶常温下的固溶体中,沿管壁厚度方向的铁素体含量进一步梯度减小,使管坯中残留的铁素体含量≤0.5%。
89.中间品冷加工工艺:采用多道次扩、拔、轧制变形量累积,满足晶粒细化和碳化物协周控制要求,首道次冷轧管为调控晶粒度,变形延伸系数1.5-2.3,控制在减径率达32%-50%,减壁率达到32%-55%,中间扩、拔、轧管道次单道次一般延伸系数控制在1.05-1.7,控制在减径率达10%-40%,减壁率达到10%-48%,之后进行过程固溶热处理,过程固溶热处理温度控制在1100
±
10℃。终轧冷加工:对管子晶粒度进行检测,精密冷轧管机变形延伸系数1.2-1.6,控制在减径率达12%-31%,减壁率达到12%-32%,最后进行光亮固溶热处理炉,温度控制在在1080
±
5℃。固态下铁素体回溶技术,使铁素体含量为0,表面粗糙度ra≤0.8μm。
90.冷加工工艺采用冷轧为主、冷拔为辅的短流程生产工艺,符合不锈钢管生产多工序和多道次循环的特点,适应多种规格、减少工艺道次和节约成本。即满足小批量、多批次、多规格的工艺要求,具有良好的经济性和高效率。
91.需要说明的是,不锈钢无缝管冷轧涉及到影响晶间腐蚀性能,多道次轧/拔管变形量的累积,使管体变形均匀,内部形核率提高,经固溶热处理再结晶后内部晶粒度较细。而当冷轧量过大时,固溶热处理过程中诱发再结晶行为,大规模的再结晶行为会生成更多的大角度自由晶界,新生成的大角度晶界在高温加热过程中迅速地大规模地迁移,迁移过程中不可避免地会与晶格位错发生反应,会促使生成平直的共格孪晶界,呈明显的网络连续状的大角度晶界,对晶界特征分布带来负面影响,此时晶界析出严重,晶粒被深的腐蚀沟壑所包围。晶粒尺寸的激剧减小使晶界数量增加,碳氮原子扩散至晶界的距离减小,晶界处铬的浓度降低,晶间腐蚀程度加剧。而小变形冷轧管在固溶热处理后没有大量随机晶界产生,较小的变形可以更多促使自由晶界的迁移,使晶界之间发生相互反应生成大量低能晶界,网格联通性进一步弥散化,晶界特征得到显著优化,从而提高抗晶间腐蚀性能。因此,在轧制管时要统筹兼顾轧制力与晶间腐蚀关系,通过在合适的冷轧管延伸系数的基础上,通过多道次轧制的累积使晶粒细化,同时又满足晶间腐蚀要求。
92.进行冷轧不锈钢管前,对荒管内外表面进行修磨,减少不锈钢管材在冷轧管加工后易引起表面粗糙度增大,荒管采用粗砂轮修磨去除表面螺旋节,精抛去除粗修磨产生的毛刺、碎颗粒,精磨后管子表面粗糙度提高至ra≤3.2,保证了中间轧制管的表面质量。
93.选择既能够通过高温固溶热处理进行软化,又保证组织均匀、相尺寸逐级细化的温度进行中间退火,为获得较大变形量奠定基础,同时防止组织过分长大给固溶态管材组织及性能控制带来不利影响,实现在冷变形和中间退火过程中相尺寸的不断细化。同时,保证晶间腐蚀满足要求,铁素体含量降到最低。
94.优选316l不锈钢无缝管中间固溶热处理温度对组织数值的变化,掌握了晶粒尺寸
随中间退火温度的变化而发生长大的形成规律,超高纯316l不锈钢无缝管晶粒尺寸细化的固溶温度在1080℃
±
5℃。在此基础上,检测组织及软化数值与热处理温度的对应数值,进一步优选超高纯净316l不锈钢管中间固溶热处理温度。
95.针对不锈钢难冷变形的特点,轧管中易产生工模具与金属管材表面相对异步滑动现象,引起内外表面产生摩擦划伤,终轧管达不到粗糙度ra0.8mm要求。采取环向喷淋强制润滑方式,增大润滑油流量并根据轧制情况1.5-3l/s可调,喷嘴压力提高到0.3-0.5mpa,优选粘稠度较大的轧制油。
96.首轧是破碎晶粒度的关键工艺,采用二辊冷轧管机轧制时根据荒管晶粒度等级,对应相应的轧制变形延伸系数1.5-2.3,晶粒沿变形方向拉长成纤维状,位错密度的逐步增加,使组织内的畸变程度提高,晶粒被压缩或拉长程度提高,晶粒形核驱动力及长大驱动力显著增大,充分的冷轧变形,避免管子出现晶粒不均匀,冷轧管变形延伸系数1.5-2.3,控制在减径率达32%-50%,减壁率达到30%-55%,与冷扩拔和轧相结合发挥冷轧管变形量大和冷扩拔生产灵活的优点,通过变形量的累积较大变形量,对奥氏体晶粒尺寸、形貌等进行调控,每道次一般延伸系数控制在1.05-1.7,控制在减径率达10%-40%,减壁率达到10%-48%,采用辊道式固溶热处理炉,固溶热处理温度控制在1100℃
±
10℃区间,在制品的保温时间控制在(1.5-2.5)*壁厚min,使固溶强化使不锈钢的力学性能提高,经多道次拔/轧制管变形量的累积,满足晶粒细化要求,同时,较大的变形量使管子晶粒更均匀。
97.终轧管采用内外壁两用抛光机,对成品轧制前的中间管材修磨后用320目及以上砂皮进行抛光,在抛光力作用下,基体表面发生塑性变形,并使周边高温氧化下瞬间形成的金属表面的极薄氧化膜反复地被磨削下来,从而变得越来越光亮。整个抛光过程既具有机械的磨削作用,又同时发生物理和化学作用。使不锈钢管内表面粗糙度ra0.8μm甚至更小。
98.由于终轧管多指标协同细调要求,冷轧加工和固溶热处理过程中的数值变化均会改变晶粒的尺寸和均匀性,很容易出现晶粒尺寸不合格或“混晶”的问题,晶粒度控制成为终轧不锈钢管制造中的要点和难题。采用二辊精密冷轧管机,通过前道冷轧以或冷扩拔积累变形量,终轧管轧制时,还要满足其它综合性能要求,冷轧管精轧变形延伸系数相对细调,冷轧精密管变形延伸系数1.2-1.6,控制在减径率达12%-31%,减壁率达到12%-32%,管径尺寸公差控制在
±
0.05mm,晶粒度控制在5-7级,实现不锈钢管全壁厚组织、性能高均匀性、高稳定性,达到相应的外径和壁厚尺寸及公差要求范围内;终轧管固溶热处理:温度控制在1080℃
±
5℃区间,在保证管体长度和截面温度一致性下,使冷加工应力释放,采用全氢幅射管加热辊道式光亮固溶热处理炉,管子加热后快速冷却,晶粒得到有效调控,消除加工硬化,恢复其组织和性能,固溶温度控制在1080℃
±
10℃区间,成品的保温时间控制在(1.0-1.5)*壁厚min,使全部残留铁素体含量快速回溶到奥氏体不锈钢管中。
99.精密冷轧管机设置有与轧边同步送进的管外壁清洗装置,清洗速度为3.5-5.5m/min。由管口封堵、刮油器、一级脱脂、二级脱脂机构和刮脱脂液机构、一次漂洗和二次漂洗和刮水、环形风刀吹干等工序组成。通过聚乙烯纤维线缠绕旋转刮去管子外表面油液,一、二级脱脂机构,脱脂液喷淋在管表面经多道对列式海绵夹持件相反旋转,使管子表面的粘的油污被分散、乳化、剥离,温度控制在25-30℃,第一级漂洗采用40-50℃的温水,经对列式链传动海绵擦拭进一步去除表面油污,第二级采用较高温清水喷淋或冲洗,温度控制在50-60℃,再经刮水装置刮去表面水分,经高压环形风刀吹扫。系统采用plc自动控制。
100.接上述管内壁清洗装置,管子输送到清洗箱内,脱脂液位漫过管子表面,通过清洗箱底部超声波振子发出超声波在液体中空化、加速度及直进流作用,使污垢被分散、乳化、剥离,同时升温并加入合适的清洗球,在水流循环往复作用下实际往复清洗,时间控制在4-9min。完成后排出脱脂液并用压缩空气吹出余液。再通过注入清水,在超声波振子作用下,在正逆循环水的推动下完成清水漂洗,时间控制在2-3.5min,压缩空气吹扫。
101.为满足成品管制造工艺要求,成品管采用辊底式不锈钢管全氢光亮固溶炉,采用高温抗氧化燃烧加热技术与热处理相结合的综合技术,可实现无氧化、无脱碳、无渗碳,从而达到表面光亮净化的效果。采用纯氢作为保护气体,可显著提高传热效率,并提高炉内保护气体的循环量。氢气除保护光亮作用外,还具有较强的还原作用,提高钢管的光洁度;同时,使再结晶更加均匀化,使材料的力学性能更加均匀。采用天然气和空气在陶瓷辐射管间接加热,有效保护保证陶瓷辐射管内的废气不进入炉体内,热处理炉为随道式密闭设施,炉温均匀性
±
5℃,控温精度≤
±
1℃。天然气作为燃烧热源,对不锈钢管进行加热,加热后的不锈钢管在一个专门的密闭冷却隧道内通过采用n2喷淋快速冷却,再通过辐射水冷段缓慢冷却,风冷室采用强对流循环系统,通过高效换热循环热技术,避免与空气接触而氧化。
102.关于高精度不锈钢无缝管矫直方法,利用十一辊高精度矫直机进行矫直,从而提高管子的直线度。进料口设置管子导向筒,十一辊矫直机由相面对的孔型矫辊呈交错状地配置,通过调整上下矫辊装置的偏置量,为矫直机进入口管的外径的3.5-5%之间,首根管子矫直时,根据实际矫直后直线度情况进行调整,成品冷轧或冷拔不锈钢管达到管径公差
±
0.05mm。
103.采用超声波、涡流一体化无损检测设备对管子进行无损检测,信操比ut≥8db,et≥10db,周向灵敏度差波动控制在≤2 db,测厚精度控制在
±
0.05mm。终轧管采用内外壁两用抛光机,对成品轧制前的中间管材修磨后用320目及以上砂皮进行抛光,在抛光力作用下,基体产生高温从而表面发生塑性变形,并使周边高温氧化下瞬间形成的金属表面的极薄氧化膜反复地被磨削下来,从而变得越来越光亮。整个抛光过程既具有机械的磨削作用,又同时发生物理和化学作用。使不锈钢管内表面粗糙度ra0.4-0.6μm甚至更小。
104.通过电解抛光处理和纯化工艺制造超高洁净度316l不锈钢管管内表面粗糙度和富铬膜的方法制造:电解抛光处理是在电解槽内可优选溶解掉金属表面的形变层、位错、空穴聚积等电位相组织,从而获得等电位表面,使表面粗糙度下降,光亮度提高。电解槽内电解抛光液由98%浓度h2so4、85%浓度h3po4、离子水配置而成,其中电解液成分%(质量分数)h2so4为15-20%、h3po4为63-67%、h2o为12-22%,将比重调节至1.5-1.7。抛光液各组分添加顺序:水、h3po4、h2so4等。
105.如上述抛光液调制的基础上,把不锈钢管挂在定制夹具上,电解槽内不锈钢管作为电解阳极,电加热器加热并控制酸液温度为43-55℃,直流多脉冲电压≤30v,电流密度为5-50a/dm2,对抛光液进行搅拌对流,减少电解液的温度差,防止阳极过热。电解抛光时间5-15min。
106.前述的电解抛光处理要符合《astm e1558 金相试样电解抛光指南》《astm a380不锈钢零件、设备及系统的清洁、除锈及钝化》规程,满足半导体制备装置316l不锈钢管内表面粗糙度控制在ra0.13μm~0.20μm,以提高管子流道的平滑性。
107.为提高水清洗水的使用效率和保证经济性,一般采取水质逐级使用原则,初次清
洗水采用第二次清洗水作为漂洗用水,水量不足是可使用纯水设备处理过的纯水。
108.纯水设备(反渗膜)处理过的纯水主要指标:电阻率≥17.5kω.cm,总有机碳(toc)<20ppb,二氧化硅<5ppb,细菌<10个类群/100毫升,热去离子温度最小值176f(80℃)。
109.为了提高电解抛光后的酸液能快速清理,第一次在流动水中采用自动冲淋装置清洗,管子外表面,再用高压循环水枪对内孔进行逐根冲洗。冲洗后移到热水缸内浸泡4-10min,温度控制在60℃
±
5℃,漂洗后沥干表面水分,再逐根用压缩空气把管内壁吹扫。
110.第二次用纯水作为清洗水,采用超声波清洗机漂洗:漂洗时间3-5min,持管子口径内孔用高压水冲洗1-5min,漂洗后沥干水分并逐支用压缩空气对管内吹扫。
111.上述316l不锈钢无缝管电化学抛光后,表面形成的富铬氧化膜,含铬比例越高,其耐腐蚀性则更好。为进一步提高富铬氧化膜层,还对管子进行酸洗钝化处理,钝化液为质量百分比为20%-35%的hno3溶液,316l不锈钢管在钝化槽中钝化,钝化时间10-30min,随后沥干管内hno3溶液;该膜层成分与316l锈钢本体相比,按semi标准uhp等级中要求:cr/fe比>1.5,crox/feox比>2,去除表面游离铁离子,使表面形成富铬层以提高耐腐蚀性。
112.采用上述第一次清洗和第二次清洗同样方法对管子进行漂洗,去除管子表面酸液,采取相同漂洗工艺方法进行漂洗,沥干内外表面水分并逐支用压缩空气对管内吹扫。
113.电解抛光后超高洁净的管子,验证遵循“用电抛光法测定不锈钢钝化astmb912-2002(2013)”规范要求中第6部分的测试方法,管内通入纯水,压力为0.03-0.08mpa,在管端两侧均设置在线电阻率计,当两侧管端数值均达到18*106ωcm时,管子内表面达到超高洁净度要求。否则,重新漂洗。
114.超高洁净度的不锈钢无缝管需要在无尘洁净厂房内完成成品管内吹扫、包装等工序,无尘洁净厂房基础设施要符合《iso14644-1洁净室和相关控制环境》等技术规范,空气洁净度必须达到
ⅴ
级及以上等级,满足超高洁净度不锈钢管制备要求。
115.进入无尘厂房内的316l不锈钢无缝管,首先要在净化室内吹扫,使316l不锈钢无缝管保持超高洁净。
116.在洁净厂房内,按“semi e49.6用于不锈钢系统的子系统组装和测试流程的指南”要求,316l不锈钢无缝管内需要用含量为99.999%的氮气(经0.001μm过滤器过滤),温度到60℃
±
5℃,对管子内吹扫,达到超高洁净度的要求。
117.管子的密封和包装要符合《semie49.6,用于不锈钢系统的子系统组装和测试流程的指南》的要求,保证管子运输中的洁净度。
118.不锈钢管两侧管端,应使用洁净保护膜并套上聚乙烯保护帽。
119.实施例1:成分组成的钢水利用eaf电炉、k-obm-s转炉、vod lf、真空vim和var精炼进行熔炼,通过模铸成钢坯(钢管的原材料),化学成分允许偏差符合gb/t222标准的规定,表1所示。
120.表1.316l超高洁净度不锈钢化学成分检验结果wt/%
热轧的钢棒按gb/t226进行低倍检验,横截面酸浸低倍组织试样上无目视可见的缩孔、气小泡、夹杂、白点和翻皮等缺陷。按gb/t1979标准评级,其级别如下表2。
121.表2低倍组织(级)按gb/t10561的a法检查316l不锈钢管的非金属夹杂物,夹杂物的级别及semif20指标如下表3表3316l不锈钢管非金属夹杂物级别(级)按gb/t13305方法,在钢管纵向检难选取任意检测面上最严重的视场,在显微镜放大倍率为280-320倍下检测出铁素体含量为0%。
122.以316l不同规格不锈钢坯为原料,通过热穿孔制成荒管,对荒管100%进行表面目视检查和修磨,去除内外表面的各种缺陷,精整后荒管的外径、壁厚尺寸等要求表4所示。
123.表4冷加工以冷轧为主,冷拔为辅为主,利用冷轧管机控制变形量制造出钢管,实施固溶热处理,控制温度、时间制作具有成品相同晶粒度的钢管,按gb/t6394标准要求。冷轧加工实施方案如表5所示。
124.表5冷轧加工实施方案表(mm/级)
中间品管在lg60/120-h冷轧管机上轧制;成品道次分别在lg15/40/110-ghls二辊精密冷轧管机机上轧制. 中间品热处理采用天然气辊底式固溶热处理炉。温度为1100℃、成品为光亮固溶炉,温度为1080℃。
125.按gb/t228.1标准要求,从这样实施的成品不锈钢无缝管在头尾两端各取试样做室温拉伸性能试验,拉伸采用整管和剖试样;按gb/t4340.1,进行硬度试验;按照gb4334 e法,从成品不锈钢无缝管在头尾两端各取试样做晶间腐蚀试验。试验结果如表6所示。
126.表6 力学、硬度和晶间腐蚀试验(mpa、%、hv)按semif19“不锈钢元件与介质接触表面条件”和semif37“用于气体分配系统元件确定表面粗糙度参数的方法”规范要求,把管子剖开作目视检验,钢管内表面呈电解抛光面,无任何肉眼可见缺陷。同时对以上规格不锈钢管的每根管子的两端和中间各取3个位置两点用粗糙度仪进行检测,数值均小于ra≤0.2μm管内各点表面粗糙度数值如下表7所示。
127.表7 管内表面粗糙度ra数值统计表(μm)
按半导体行业国际标准测试方法分别对管内表面用原子发射光谱xps进行氧化层厚度和表面x射线光电子能谱xps检测和分析,如下表8所示:表8实施例2:与实施例1区别在于,冷轧管变形工艺对晶粒度和晶间腐蚀的影响;电加热器加热并控制酸液温度为55℃,抛光电压≤30v,电流密度为50a/dm2,电解抛光时间10 min。钝化液为质量百分比为35%的hno3溶液,钝化时间30 min。
128.集成电路及ic产业制备装置用超高洁净度不锈钢无缝管,成分组成以质量%计含有:0.009%c,0.011%p、0.003%s、0.06%mn、0.20%si、0.007%al、0.014%cu,16.804%cr、14.711ni、2.326%mo、0.008%n、0.006%nb、0.003%ti、0.005%se;其余为fe和杂质。
129.按gb/t10561的a法检查316l不锈钢管的非金属夹杂物,夹杂物的级别,a细0级、a粗0级,b细0级、b粗0级,c细0级、c粗0级,d细0级、d粗0级;满足semi f20指标要求(指标可见表3)荒管直径65mm、直径112mm、直径132mm三个规格,分别在lg60-h和lg120-h冷轧管机上轧制;成品道次分别在lg15-hddg、lg30-hddg、lg60-hddg二辊精密冷轧管机机上轧制和部分拔制到成品。中间品热处理采用天然气辊底式固溶热处理炉。温度为1100℃、成品为光亮固溶炉,温度为1080℃、送进速度根据实外径和壁厚,速度为0.6-2.0m/min可调。工艺流程如下表9所示。
130.表9轧制工艺流程表(mm/级)按gb/t228.1标准要求,从这样实施的成品不锈钢无缝管在头尾两端各取试样做室温拉伸性能试验,拉伸采用整管和剖试样;按gb/t4340.1,进行硬度试验;试验结果如表10所示。
131.表10力学、硬度和晶间腐蚀试验(mpa、%、hv)按gb/t13305方法,在钢管纵向检难选取任意检测面上最严重的视场,在显微镜放大倍率为280~320倍下检测出铁素体含量为0.11%。
132.按semi f19
ꢀ“
不锈钢元件与介质接触表面条件”和 semi f37“用于气体分配系统元件确定表面粗糙度参数的方法”规范要求,把管子剖开作目视检验,钢管内表面呈电解抛光面,无任何肉眼可见缺陷。同时对以上规格不锈钢管的每根管子的两端和中间各取3个位置两点用粗糙度仪进行检测,数值均小于ra≤0.2μm管内各点表面粗糙度数值如下表11所示。
133.表11管内表面粗糙度ra数值统计表(μm)
按半导体行业国际标准测试方法分别对管内表面用原子发射光谱xps进行氧化层厚度和表面x射线光电子能谱aes检测和分析,如下表12所示表12实施例3:钢中添加铌和钛,冷轧管变形工艺对晶粒度和晶间腐蚀的影响;电加热器加热并控制酸液温度为43℃,抛光电压≤30v,电流密度为5a/dm2,电解抛光时间15 min。钝化液为质量百分比为20%的hno3溶液,钝化时间10 min。
134.集成电路及ic产业制备装置用超高洁净度不锈钢无缝管,成分组成以质量%计含有:0.008%c,0.010%p、0.002%s、0.06%mn、0.21%si、0.007%al、0.015%cu,16.791%cr、14.685ni、2.322%mo、0.009%n、0.007%nb、0.002%ti、0.006%se;其余为fe和杂质。
135.按gb/t10561的a法检查316l不锈钢管的非金属夹杂物,夹杂物的级别及semi f20指标,a细0级、a粗0级,b细0.5级、b粗0级,c细0级、c粗0级,d细0级、d粗0级。
136.荒管直径65mm、直径112mm、直径132mm两个规格,分别在lg60-h和lg120-h冷轧管机上轧制;成品道次分别在lg15-hddg、lg30-hddg、lg60-hddg二辊精密冷轧管机机上轧制和部分拔制到成品。中间品热处理采用天然气辊底式固溶热处理炉。温度为1140℃、成品为
光亮固溶炉,温度为1120℃、送进速度根据实外径和壁厚,速度为0.6-2.0m/min可调。工艺流程如下表13所示。
137.表13轧制工艺流程表mm/级按gb/t228.1标准要求,从这样实施的成品不锈钢无缝管在头尾两端各取试样做室温拉伸性能试验,拉伸采用整管和剖试样;按gb/t4340.1,进行硬度试验;试验结果均达到标准要求。
138.试验结果如表14所示。
139.表14力学、硬度和晶间腐蚀试验( mpa、%、hv)按gb/t13305方法,在钢管纵向检难选取任意检测面上最严重的视场,在显微镜放大倍率为280~320倍下检测出铁素体含量为0%。
140.按semi f19
ꢀ“
不锈钢元件与介质接触表面条件”和 semi f37“用于气体分配系统元件确定表面粗糙度参数的方法”规范要求,把管子剖开作目视检验,钢管内表面呈电解抛光面,无任何肉眼可见缺陷。同时对以上规格不锈钢管的每根管子的两端和中间各取3个位置两点用粗糙度仪进行检测,管内各点表面粗糙度数值如下表15所示。
141.表15管内表面粗糙度ra数值统计表(μm)
按半导体行业国际标准测试方法分别对管内表面用原子发射光谱xps进行氧化层厚度和表面x射线光电子能谱aes检测和分析,如下表16所示表16无损检测结果如下:采用sst-40无线传输旋转式超声波涡流一体化联合检测设备,脉冲反射式超声波检测系统,按nb/t20003进行内外表面纵向和横向超声波检测,标准试样矩形槽的深度0.1-1.0mm,宽度不大于1.6mm,长度不大于12.5mm。超声波探伤合格率超过95%。数字涡流探伤系统,对于公称外径小于65mm,按照nb/t20003标准进行纵向和环向涡流探伤试验,标准试样通孔的直径不大于1.5mm,切槽深度不大于0.1mm,宽不大于1.5mm,切槽长度不大于25mm,涡流探伤合格率达到100%。按astme165标准,对100%管端不少于50mm进行渗透试验,内表面根据内径,检验长度尽量长。从这样实施了成品不锈钢无缝管全部进行水压试验,按照astma999标准进行水压试验,试验压力按公式计算p=2sr/d,水压试验合格率超过100%。
142.以上示意性的对本发明及其实施方式进行了描述,该描述没有限制性,中所示的也只是本发明的实施方式之一,实际的结构并不局限于此。所以,如果本领域的普通技术人员受其启示,在不脱离本发明创造宗旨的情况下,不经创造性的设计出与该技术方案相似的结构方式及实施例,均应属于本发明的保护范围。
再多了解一些
本文用于企业家、创业者技术爱好者查询,结果仅供参考。