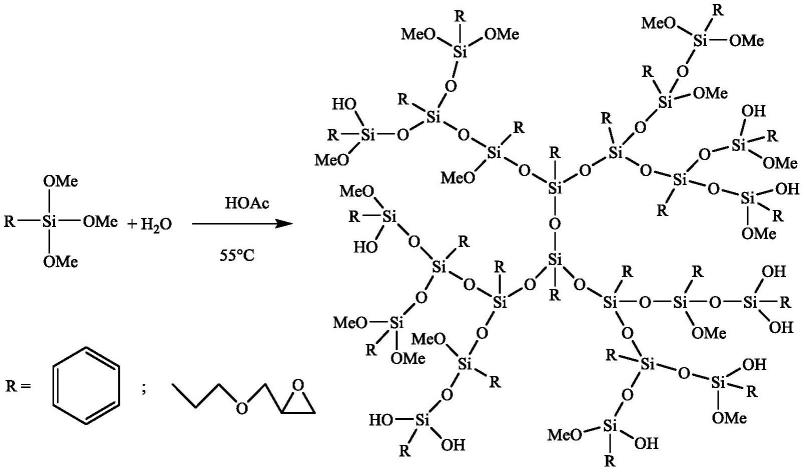
1.本发明属于功能涂料技术领域,特别涉及一种超支化聚硅氧烷-环氧树脂自分层涂料及其制备方法。
背景技术:
2.金属材料在人类的生产和生活中广泛使用,金属的腐蚀一直是人类面临的一个挑战。据统计,全世界每年因金属腐蚀造成的直接经济损失约为7000亿美元。我国因金属腐蚀造成的损失占国民生产总值的4%,钢铁因腐蚀而报废的数量占钢铁当年产量的24-30%。采用涂料对钢铁进行防腐保护是最有效的方式之一。自分层涂料是由两种或多种不相容或部分相容的树脂组成,可以一次涂装后随溶剂挥发,以表面能之差为驱动力,使得各组分自发产生相分离和迁移现象,进而形成梯度分层的多功能涂料,这种自分层涂料每一层都能显示出不同的性能。
3.环氧树脂因带有大量的低极性苯环刚性基团,反应性的环氧基,羟基等基团,而具有高绝缘性,高耐腐蚀性,高粘结性等特点,成为了最受欢迎的防腐涂料组分。但他固化后交联密度过高,脆性大,漆膜容易碎裂,且不耐候,在户外太阳光的照射下容易黄变。在户外使用的金属材料等应用场景中,不仅要求有超强的耐腐蚀性能,还要求漆膜具有较强的耐紫外老化性能。针对这种问题,往往需要在金属材料防腐底漆的表面再涂覆耐候的面漆,如丙烯酸酯,聚氨酯涂料,有机硅氧烷涂料,以分别发挥底漆的耐腐蚀和面漆的耐老化作用。过程繁琐,耗时耗力成本较高。
4.针对这种问题,提出了自分层防腐涂料的概念,将两种具有一定不相容性,表面能差距适中的树脂共混,涂装在基材表面,即可使得两种具有不同功能的聚合物由于表面张力的差,自发迁移至适合的位置并固化。实现一次涂装,得到两种功能涂层的目标,有效减少需要消耗的人力物力。但分层的程度需要控制,分层太明显,也容易出现层间附着力低,整体漆膜机械性能差的问题。
5.有机硅树脂(聚硅氧烷树脂)具有耐候耐热等优点,适合作为面漆使用,但多数聚硅氧烷表面能太低,与环氧树脂相容性很差,易出现层间附着的问题。通过水解缩合法制备的超支化聚硅氧烷含有大量活性si-oh及极性可调的有机r基团。有利于降低与环氧树脂的表面能差并提高二者的相容性。此外,超支化聚硅氧烷分子间链缠结程度很低且有大量空腔结构,可以减少涂料树脂在迁移分层过程中的阻力,同时降低涂料粘度,提高固含量,增强聚合物韧性。当然,有机r基团的选择也非常重要,专利cn112795307a单独利用硅醇封端的甲基聚硅氧烷与环氧树脂配置自分层涂料时,仅能得到低附着力,低硬度,低抗冲击强度的自分层漆膜。因此,如何通过调整聚硅氧烷分子的r基团来调整树脂的极性,进而控制聚硅氧烷与环氧树脂的相容性和分层程度,非常关键。同时由于环保要求的逐渐提高,减少溶剂型涂料的voc含量,至关重要。
6.目前基于聚硅氧烷和环氧树脂的自分层涂料存在的主要问题是:(1)涂层的性能和分层效果难以有效平衡。(2)如何提高涂料的固含量,降低voc的排放。
技术实现要素:
7.为了解决这两个问题,本发明采用超支化聚硅氧烷与环氧树脂复配自分层涂料,希望能够通过苯基三甲氧基硅烷(ptmos)和γ-缩水甘油醚氧丙基三甲氧基硅烷(gopts)反应来合成含有苯基和环氧基的超支化聚硅氧烷,通过改变超支化聚硅氧烷与环氧树脂的相容性来控制分层程度,一方面解决层间附着的问题,保证良好的分层效果,耐腐蚀性,耐候性等性能,同时提高整体涂料的固含量,降低voc含量。本发明提供了一种低粘度,高耐腐蚀性,漆膜基本性能较好的超支化聚硅氧烷-环氧树脂自分层涂料的制备方法。
8.本发明达到该目标采用的技术方案是一种超支化聚硅氧烷-环氧树脂自分层涂料,包括组分甲和乙,按重量份计,组分甲包括超支化聚硅氧烷60-150份,环氧树脂30-200份,有机溶剂35-150份,组分乙包括胺类固化剂20-200份,有机溶剂5-90份。
9.进一步地,组分甲中超支化聚硅氧烷和环氧树脂的质量和占组分甲质量的70%,超支化聚硅氧烷与环氧树脂的质量比为0.5-1.5:1,组分乙中胺类固化剂与有机溶剂的质量比为7:3。
10.进一步地,环氧树脂环氧值为0.21-0.51eq/100g。
11.进一步地,胺类固化剂包括改性脂环胺固化剂,腰果酚改性脂肪胺固化剂,聚酰胺固化剂,有机溶剂均为质量比7:3的二甲苯-正丁醇混合溶剂。
12.进一步地,改性脂环胺固化剂是一种活泼氢当量为142的胺类固化剂,腰果酚改性脂肪胺固化剂是一种活泼氢当量为255的胺类固化剂,聚酰胺固化剂是一种活泼氢当量为170的胺类固化剂。
13.进一步地,超支化聚硅氧烷是以苯基三甲氧基硅烷(ptmos)和γ-缩水甘油醚氧丙基三甲氧基硅烷(gopts)为单体经酸催化水解缩合得到的,制备路线如下所示:
[0014][0015]
其中r为苯基或γ-缩水甘油醚氧丙基,苯基与γ-缩水甘油醚氧丙基的摩尔比为4:6-8:2,这里的苯基与γ-缩水甘油醚氧丙基的摩尔比等同于苯基三甲氧基硅烷单体和γ-缩水甘油醚氧丙基三甲氧基硅烷单体的摩尔比为4:6-8:2。
[0016]
进一步的,苯基三甲氧基硅烷单体与γ-缩水甘油醚氧丙基三甲氧基硅烷单体的摩尔比为8:2。
[0017]
进一步地,一种超支化聚硅氧烷-环氧树脂自分层涂料的制备步骤如下:
[0018]
(1)配制ph值为3的醋酸水溶液;
[0019]
(2)将步骤(1)得到的醋酸水溶液在常温下边机械搅拌边缓慢加入装有苯基三甲氧基硅烷单体和γ-缩水甘油醚氧丙基三甲氧基硅烷单体的容器中,再升温至55℃,并在20min后加入四氢呋喃继续反应4-6h,然后旋蒸除去溶剂和水,得到无色透明粘稠液体状的超支化聚硅氧烷。
[0020]
(3)按照配比,将超支化聚硅氧烷溶解于有机溶剂,使固含量为70%,环氧树脂溶解于有机溶剂,使固含量为70%,然后在超支化聚硅氧烷溶液中加入环氧树脂溶液,充分混合均匀得到组份甲;将固化剂和有机溶剂混合得到组分乙,将甲、乙组分常温下混合搅拌均匀制得超支化聚硅氧烷-环氧树脂自分层涂料。
[0021]
本发明的有益效果如下:
[0022]
(1)超支化聚硅氧烷的加入减少了分子链缠结降低了涂料的粘度;
[0023]
(2)通过超支化聚硅氧烷与环氧树脂的表面能差,使得低表面能的超支化聚硅氧烷迁移到上表面而环氧树脂留在底层形成自分层漆膜;
[0024]
(3)通过调整环氧基苯基超支化聚硅氧烷的共聚组成,改善了超支化聚硅氧烷与环氧树脂的相容性,取消了两种树脂之间的相界面,解决了层间附着问题,有效提高了自分层涂料的各项性能。
[0025]
(4)超支化聚硅氧烷通过与环氧基团的反应可以在常温下进行固化,施工方便。
附图说明
[0026]
图1为超支化聚硅氧烷1的核磁共振硅谱图;
[0027]
图2为超支化聚硅氧烷1的核磁共振氢谱图;
[0028]
图3为实施例3(a),实施例4(b),对比例2(c)自分层涂料断面的sem-eds;
[0029]
图4为实施例1-7和对比例2自分层涂料断面的sem-eds点扫数据图;
[0030]
图5为实施例和对比例配方制备出的涂料的漆膜的阻抗分析(eis);
[0031]
图6为实施例和对比例配方制备出的涂料色差随老化时间变化曲线。
具体实施方式
[0032]
现在结合具体实施例对本发明作进一步说明,以下实施例旨在说明本发明而不是对本发明的进一步限定。
[0033]
制备五种不同共聚组成的超支化聚硅氧烷,其中,r全为苯基则产物标记为hpsi-p,r同时含有苯基和环氧基且二者摩尔比为4:6,5:5,6:4,8:2时产物分别标记为hpsi-pg(4-6),hpsi-pg(5-5),hpsi-pg(6-4),hpsi-pg(8-2);再将超支化聚硅氧烷复配甲、乙组分中的其他原料配制成自分层涂料,具体制备方法如下:
[0034]
实施例1
[0035]
(1)在100ml去离子水中加入3g左右冰醋酸配制成ph值为3的醋酸水溶液;
[0036]
(2)首先在装有15.86g(0.08mol)苯基三甲氧基硅烷(ptmos)单体和28.36g(0.12mol)γ-缩水甘油醚氧丙基三甲氧基硅烷(gopts)单体的250ml三口烧瓶中常温边机械搅拌边缓慢加入事先配制好的ph值为3的醋酸水溶液14.41g,再升温至55℃,并在20min
后加入四氢呋喃43.27g继续反应6h,最后50-65℃旋蒸30min除去溶剂和水,得到无色透明粘稠液体状的环氧基苯基超支化聚硅氧烷hpsi-pg(4-6),标记为超支化聚硅氧烷1;
[0037]
(3)称取10g超支化聚硅氧烷1加入4.29g二甲苯-正丁醇混合有机溶剂进行溶解并保存,使其固含量为70%;称取10g环氧树脂e-20加入4.29g二甲苯-正丁醇混合有机溶剂进行溶解并保存,使其固含量也为70%;在14.29g的70%固含量的超支化聚硅氧烷1溶液中加入14.29g的70%固含量的环氧树脂e-20溶液,使其总固含量为70%,并充分溶解混合均匀为组份甲;称取改性脂环胺固化剂,具体为4,4'-二氨基二环己基甲烷与叔碳酸缩水甘油酯e-10p摩尔比1:1的加成物8.27g和二甲苯-正丁醇混合有机溶剂3.54g组成70%固含量的组分乙,将甲、乙组分混合搅拌均匀制得超支化聚硅氧烷-环氧树脂自分层涂料,涂料采用120μm的线棒刮涂在打磨后的马口铁片上制版。
[0038]
超支化聚硅氧烷1的核磁硅谱结果如图1所示。
[0039]
图1中,r代表苯基或者γ-缩水甘油醚氧丙基,r0代表甲基,单体t0峰非常小,无法积分,说明体系中只有极少量未反应单体,t1,t2,t3峰分别对应末端单元,线形单元,支化单元的摩尔含量,证明超支化聚硅氧烷1是拥有支化结构的超支化聚硅氧烷。
[0040]
实施例2
[0041]
使用19.83g(0.1mol)苯基三甲氧基硅烷(ptmos)单体和23.63g(0.1mol)γ-缩水甘油醚氧丙基三甲氧基硅烷(gopts)单体反应,产物为hpsi-pg(5-5),标记为超支化聚硅氧烷2,然后按照表格1中的配比制得涂料,所用固化剂为改性脂环胺固化剂,具体为4,4'-二氨基二环己基甲烷与叔碳酸缩水甘油酯e-10p摩尔比1:1的加成物。涂料采用120μm的线棒刮涂在打磨后的马口铁片上制版。
[0042]
产物hpsi-pg(5-5)的核磁共振氢谱图如图2所示,图2表明:a,b峰为ptmos苯环上的质子峰,f为gopts环氧基上的质子峰,可以计算两种单体的实际共聚组成为:(5.2/5):(1)=1.04:1,与投料比非常接近,结合图1硅谱中明显的支化聚合物结构特征峰,可以判定合成的超支化聚硅氧烷是由两种单体缩合形成,且共聚组成与预期一致。
[0043]
实施例3
[0044]
使用23.79g(0.12mol)苯基三甲氧基硅烷单体和18.91g(0.08mol)γ-缩水甘油醚氧丙基三甲氧基硅烷单体反应,产物为hpsi-pg(6-4),标记为超支化聚硅氧烷3,然后按照表格1中的配比制得涂料,所用固化剂为改性脂环胺固化剂,具体为4,4'-二氨基二环己基甲烷与叔碳酸缩水甘油酯e-10p摩尔比1:1的加成物。涂料采用120μm的线棒刮涂在打磨后的马口铁片上制版。
[0045]
实施例4
[0046]
使用31.73g(0.16mol)苯基三甲氧基硅烷单体和9.45g(0.04mol)γ-缩水甘油醚氧丙基三甲氧基硅烷单体反应,产物为hpsi-pg(8-2),标记为超支化聚硅氧烷4,然后按照表格1中的配比制得涂料,所用固化剂为改性脂环胺固化剂,具体为4,4'-二氨基二环己基甲烷与叔碳酸缩水甘油酯e-10p摩尔比1:1的加成物。涂料采用120μm的线棒刮涂在打磨后的马口铁片上制版。
[0047]
实施例5
[0048]
采用超支化聚硅氧烷4、环氧树脂e-20和改性脂环胺固化剂,具体为4,4'-二氨基二环己基甲烷与叔碳酸缩水甘油酯e-10p摩尔比1:1的加成物。涂料采用120μm的线棒刮涂
在打磨后的马口铁片上制版。
[0049]
实施例6
[0050]
采用超支化聚硅氧烷4、环氧树脂e-44和腰果酚改性脂肪胺固化剂cx-1151,涂料采用120μm的线棒刮涂在打磨后的马口铁片上制版。
[0051]
实施例7
[0052]
采用超支化聚硅氧烷4、环氧树脂e-51和聚酰胺固化剂8115,涂料采用120μm的线棒刮涂在打磨后的马口铁片上制版。
[0053]
对比例1
[0054]
按照表格1中的配比采用e-20环氧树脂直接加改性脂环胺固化剂,具体为4,4'-二氨基二环己基甲烷与叔碳酸缩水甘油酯e-10p摩尔比1:1的加成物,再添加二甲苯-正丁醇混合有机溶剂配制成70%固含量的环氧涂料,涂料采用120μm的线棒刮涂在打磨后的马口铁片上制版与自分层涂料进行性能对比。
[0055]
对比例2
[0056]
仅使用39.66g(0.2mol)苯基三甲氧基硅烷单体反应,产物为hpsi-p,标记为超支化聚硅氧烷5,然后按照表格1中的配比制得涂料,固化剂为改性脂环胺固化剂,具体为4,4'-二氨基二环己基甲烷与叔碳酸缩水甘油酯e-10p摩尔比1:1的加成物,再添加二甲苯-正丁醇混合有机溶剂配制成70%固含量的环氧涂料。涂料采用120μm的线棒刮涂在打磨后的马口铁片上制版。
[0057]
上述实施例与对比例的配方如表1所示,其中环氧树脂e-20的环氧值为0.2eq/100g,环氧树脂e-44的环氧值为0.44eq/100g,环氧树脂e-51的环氧值为0.51eq/100g,溶剂等均为常规市售产品。
[0058]
表1超支化聚硅氧烷-环氧树脂自分层涂料对比例和实施例配方
[0059]
[0060]
根据上述实施例配方制备出自分层涂料,并对其分层情况进行扫描电子显微镜-能谱分析(sem-eds),结果如图3所示,由图3结果可以看出对比例2(c),不仅从sem图中可以看到上下层的分层界面,eds图中更是可以明显发现富集在上表面的硅元素,该体系为有明显界面的分层;对于实施例4(b),未在sem图中发现明显分层界面,从其eds图中可以看到漆膜的界面层已经模糊了,这说明硅元素在不同深度区域的含量差正在变小,成为了具有一定硅元素浓度梯度的自分层漆膜。对于实施例3(a),sem图中出现了相比于实施例4(b)更加明显的韧性断裂亮纹,说明环氧基团的引入确实提高了体系的韧性,另外,从eds图中可以看到此时不同深度区域内的硅元素含量的差已经比较小了,从上表面到下表面均能看到明显的硅元素分布。
[0061]
进一步地,切换eds工作模式为点扫制得图4。
[0062]
从图4中可以看到,各组分漆膜自上而下硅元素含量均是不断递减的,说明他们均具有自分层行为,仅是分层效果不同,且随着带有环氧基团的γ-缩水甘油醚氧丙基三甲氧基硅烷摩尔含量越高,与环氧树脂的相容性越好,分层越不明显,结合图3可以看出,通过引入γ-缩水甘油醚氧丙基三甲氧基硅烷成功提高了超支化聚硅氧烷与环氧树脂之间的相容性,使其在能够自发分层的情况下取消了两者之间的相界面,解决了层间附着的问题。此外,对比实施例4和实施例5可以发现,改变超支化聚硅氧烷与环氧树脂的质量比对漆膜分层效果无明显影响;对比实施例4、实施例6和实施例7可以发现,使用不同种类的环氧树脂和固化剂,对漆膜的分层效果也没有明显影响,漆膜截面硅元素分布近乎一致。
[0063]
根据上述实施例和对比例配方将制备出的涂料进行电化学阻抗(eis)分析,结果如图5所示:当氯化钠溶液没有进入漆膜的时候,漆膜表现为一个电容的性质,阻抗很高。当氯化钠水溶液逐渐渗透进入漆膜,漆膜的阻抗开始下降,阻抗下降的越慢,表示漆膜的阻隔性越好,防腐性能越好。
[0064]
相比于有明显相相界面的对比例2,实施例1-4在3.5%氯化钠水溶液中浸泡20天后的漆膜电阻更高,这主要是由于有明显相界面的自分层漆膜往往存在层间附着的问题,表面层容易脱落,导致腐蚀介质更容易渗透到漆膜内部进而腐蚀基材表面,同时,实施例4与实施例5-7的阻抗基本一致,这说明无论是改变固化剂和环氧树脂种类还是超支化聚硅氧烷与环氧树脂的质量比,均对漆膜的耐腐蚀性能无明显影响。此外,相比纯环氧树脂的对比样,无明显相界面的自分层涂料明显有更好的耐腐蚀性能。
[0065]
根据上述实施例和对比例的配方将制备出的涂料进行耐老化性能测试,结果如图6所示。
[0066]
涂料经过紫外老化会发生颜色的改变,通过色差仪可以定量表征颜色的改变程度,从而反映涂料的耐老化性能。如图6各组分漆膜老化后的色差随时间变化曲线所示,经过200h的紫外老化箱老化,超支化聚硅氧烷-环氧树脂自分层涂料均具有较好的耐紫外老化能力,这主要是由于上层聚集的聚硅氧烷有良好的耐紫外性能,减少了紫外光对下层富集的环氧树脂的直接照射,同时,漆膜分层程度越高,耐候性能越强,而对比例1的纯环氧树脂,由于缺少上层超支化聚硅氧烷的保护,黄化非常严重。此外,无论是改变固化剂和环氧树脂种类还是改变超支化聚硅氧烷与环氧树脂的质量比,漆膜的耐老化性能无明显改变。
[0067]
根据上述实施例配方将制备出的涂料进行漆膜基本性能测试,结果如表2所示。
[0068]
表2漆膜的基本性能
[0069][0070]
如表2所示,可以明显发现对比例2的抗冲击强度等性能在引入环氧树脂后比实施例1-4更低,这印证了sem-eds表征中对其分层有明显相界面的判定。当漆膜有明显层间界面,会降低漆膜的层间附着力,受到外力时更容易脱落表现出低于对比例的抗冲击性能,相比之下,没有明显分层界面的实施例1-4,抗冲击强度更高,大幅领先于对比例,实用性大幅提升,达到了预期目标,根据实施例5-7可以看出,无论是改变固化剂及环氧树脂种类还是改变超支化聚硅氧烷与环氧树脂的质量比,都对漆膜基本性能无明显影响。
[0071]
综上,通过本发明的方法,制备出了一种具有优秀耐腐蚀,耐候,高漆膜基本性能的超支化聚硅氧烷-环氧树脂自分层涂料。
[0072]
以上依据本发明的理想实施例为启示,通过上述的说明内容,相关工作人员完全可以在不偏离本项发明技术思想的范围内,进行多样的变更及修改。本项发明的技术性范围并不局限与说明书上的内容,必须要根据权利要求范围来确定其技术性范围。
再多了解一些
本文用于企业家、创业者技术爱好者查询,结果仅供参考。