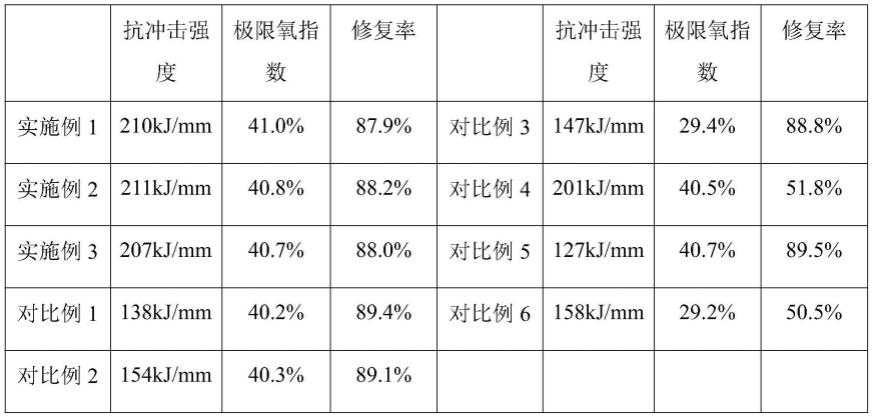
1.本发明涉及电线电缆技术领域,具体为一种柔性电缆及其制备方法。
背景技术:
2.电缆是一种电能或信号传输装置,通常是由几根或几组导线组成。电线电缆的衍生/新产品主要是因应用场合、应用要求不同及装备的方便性和降低装备成本等的要求,而采用新材料、特殊材料、或改变产品结构、或提高工艺要求、或将不同品种的产品进行组合而产生。
3.随着电力电缆应用的迅速发展,对电缆保护提出的更高要求,电缆线路常见的故障有机械损伤、绝缘损伤、绝缘受潮、绝缘老化变质、过电压、电缆过热故障等。在高温、振动、冲击的特定场合,还需要具有柔性和阻燃的效果,以达到更好更持久的使用效果。
技术实现要素:
4.本发明的目的在于提供一种柔性电缆及其制备方法,以解决现有技术中存在的问题。
5.为了解决上述技术问题,本发明提供如下技术方案:
6.一种柔性电缆的制备方法,其特征在于,所述柔性电缆是由聚合物微球喷涂在缆芯上得到喷涂后的缆芯,将改性氧化石墨烯、n,n'-(4,4'-亚甲基二苯基)双马来酰亚胺、聚1,3-丁二烯、聚乙烯混炼制成护套材料,用高压汞灯对喷涂后的缆芯表面照射后,将护套材料包裹在照射后的缆芯表面上辊压制得。
7.作为优化,所述聚合物微球是将甲基丙烯酸甲酯、丙烯酸甲酯、正庚烷、过氧化二月桂酰、改性超支化聚酸酯混合成油相,并在水相中搅拌制得。
8.作为优化,所述改性超支化聚酸酯是由4-氯-4'-羟基二苯甲酮和三羟甲基丙烷三缩水甘油醚反应制得预聚体,将预聚体依次和对苯二甲酸、三羟甲基丙烷三缩水甘油醚、对乙烯基苯甲酸反应制得超支化聚酸酯,将聚乙二醇依次和丁二酸酐、氯化亚砜、对氨基苯硫酚反应制得苯硫酚基聚乙二醇,将超支化聚酸酯和苯硫酚基聚乙二醇反应制得。
9.作为优化,所述改性氧化石墨烯是由4,4'-亚甲基双(异氰酸苯酯)和端羟基乙烯基聚硅氧烷反应后和氧化石墨烯反应,再和糠醇反应制得。
10.作为优化,所述柔性电缆的制备方法包括以下制备步骤:
11.(1)超支化聚酸酯的制备:将预聚体、对苯二甲酸、四丁基溴化铵和n,n-二甲基甲酰胺按质量比10:5:1:20~10:7:1:25混合均匀,在氮气氛围中,80~90℃,800~1000r/min搅拌反应2~3h,再加入预聚体质量1.4~1.8倍的三羟甲基丙烷三缩水甘油醚,继续搅拌反应2~3h,再加入预聚体质量0.8~1倍的对乙烯基苯甲酸,继续搅拌反应2~3h,在40~50℃,1~2kpa静置8~10h,再加入预聚体质量3~5倍的乙酸乙酯,依次用质量分数5~6%的碳酸氢钠溶液、质量分数15~20%氯化钠溶液溶液和去离子水各洗涤3~5次,将洗涤后溶液用无水硫酸镁干燥并过滤取滤液,在40~50℃,1~2kpa静置8~10h,制得超支化聚酸酯;
12.(2)超支化聚酸酯的改性:将超支化聚酸酯、苯硫酚基聚乙二醇、氢氧化钾、甲苯和n-甲基吡咯烷酮按质量比6:1:2:50:20~6:2:3:60:25混合均匀,在10~30℃,300~500r/min搅拌20~30min,升温至120~130℃并保持3~4h,继续升温至150~160℃并保持3~4h,冷却至室温过滤取滤液,将滤液以1~2ml/min的速率滴加到0~3℃,300~500r/min搅拌的滤液质量6~8倍的质量分数36~38%的盐酸中,过滤并用纯水和石油醚各洗涤3~5次,再浸没在饱和醋酸钠溶液中,用30~40khz超声20~30min,过滤并用纯水和石油醚各洗涤3~5次,在-10~-1℃,1~2kpa静置6~8h,制得改性超支化聚酸酯;
13.(3)弹性微球的制备:将甲基丙烯酸甲酯、丙烯酸甲酯、正庚烷、过氧化二月桂酰、改性超支化聚酸酯按质量比40:14:30:2:25~50:18:35:4:30在0℃混合均匀配制成油相,将聚乙烯醇和纯水按质量比1:140~1:160混合均匀配制成水相,将油相和水相按质量比1:4~1:6倒入反应釜中,密封并保持氮气氛围,以500~700r/min搅拌20~30min,在90~100℃反应10~12h,冷却至室温后过滤,在20~30℃,1~2kpa干燥6~8h,制得弹性微球;
14.(4)缆芯喷涂:将聚合物微球和纯水按质量比1:4~1:6混合均匀,制得喷涂液,再以0.06~0.08g/cm2的量喷涂在缆芯表面,在-1~-10℃,1~10pa干燥6~8h,制得喷涂后的缆芯;
15.(5)氧化石墨烯的改性:将端羟基乙烯基聚硅氧烷、n,n-二甲基甲酰胺按质量比1:10~1:15混合均匀配制成滴定液;将4,4'-亚甲基双(异氰酸苯酯)和n,n-二甲基甲酰胺按质量比1:6~1:8混合均匀,在氮气氛围中,70~90℃,800~1000r/min搅拌条件下,将4,4'-亚甲基双(异氰酸苯酯)质量0.8~1.2倍的滴定液以0.1~0.2ml/s的速度进行滴加,滴加结束后保持条件不变继续反应2~3h,加入4,4'-亚甲基双(异氰酸苯酯)质量1.2~1.6倍的氧化石墨烯分散液,在氮气氛围中继续反应4~6h,再加入4,4'-亚甲基双(异氰酸苯酯)质量0.5~0.7倍的糠醇,在氮气氛围中继续反应3~4h,制得改性氧化石墨烯;
16.(6)辊压组装:将改性氧化石墨烯、n,n'-(4,4'-亚甲基二苯基)双马来酰亚胺、聚1,3-丁二烯、聚乙烯按质量比1:1:1:3~2:1:1:4混合均匀,在140~160℃混炼20~30min,制备得到厚度为2~3mm的护套材料,将喷涂后的缆芯表面用800~1000w的高压汞灯照射5~7min后,将护套材料包裹在照射后的缆芯表面上,将温度升至100~120℃静置8~10min,再用8~10mpa的压力以220~240m/min辊压2~3次,制得柔性电缆。
17.作为优化,步骤(1)所述预聚体的制备方法为:将4-氯-4'-羟基二苯甲酮、三羟甲基丙烷三缩水甘油醚、四丁基溴化铵和n,n-二甲基甲酰胺按质量比10:8:1:20~10:10:1:25混合均匀,在氮气氛围中,80~90℃,800~1000r/min搅拌反应2~3h,在40~50℃,1~2kpa静置8~10h,制备而成。
18.作为优化,步骤(2)所述苯硫酚基聚乙二醇的制备方法为:将对氨基苯硫酚、三乙胺、二氯甲烷按质量比3:1:30~4:1:40在0~5℃混合均匀配制成对氨基苯硫酚溶液;将丁二酸酐和分子量为500~600的聚乙二醇按质量比1:3~1:4混合均匀,在70~80℃,800~1000r/min搅拌3~4h,再与氯化亚砜、四氢呋喃按质量比15:100:1~40:300:1混合均匀,在40~50℃,300~500r/min搅拌反应2~3h,再升温至60~70℃继续搅拌反应2~3h,在10~30℃,1~2kpa静置30~40min,再加入聚乙二醇质量2~3倍的对氨基苯硫酚溶液,在0~5℃,300~500r/min搅拌2~3h,在室温下静置20~24h,在-10~-1℃,1~2kpa静置6~8h,制备而成。
19.作为优化,步骤(4)所述缆芯是将直径0.03~0.05mm的铜丝集束固定成0.8~1.2mm的铜丝束,并在铜丝束外围包裹一层厚度为0.8~1mm的聚乙烯层,制得导线,将多根导线固定,并在外围缠绕一圈铝带进行固定制得,铝带厚0.3~0.5mm,宽1~3cm,缠绕间隙1~3cm。
20.作为优化,步骤(5)所述端羟基乙烯基聚硅氧烷的制备方法为:八甲基环四硅氧烷、2,4,6,8-四甲基-2,4,6,8-四乙烯基环四硅氧烷按质量比20:1~30:1混合均匀,再加入八甲基环四硅氧烷质量0.03~0.05倍的四甲基氢氧化铵混合均匀,在100~120℃,500~700r/min搅拌3~4h后,在160~180℃,1~2kpa静置3~4h,制备而成。
21.作为优化,步骤(5)所述氧化石墨烯分散液是将氧化石墨烯、n,n-二甲基甲酰胺按质量比1:10~1:15混合均匀,在20~30℃,30~40khz超声10~15min配制而成。
22.与现有技术相比,本发明所达到的有益效果是:
23.本发明在制备柔性电缆时,将甲基丙烯酸甲酯、丙烯酸甲酯、正庚烷、过氧化二月桂酰、改性超支化聚酸酯混合成油相,并在水相中搅拌制得聚合物微球,将聚合物微球喷涂在缆芯上得到喷涂后的缆芯,将改性氧化石墨烯、n,n'-(4,4'-亚甲基二苯基)双马来酰亚胺、聚1,3-丁二烯、聚乙烯混炼制成护套材料,用高压汞灯对喷涂后的缆芯表面照射后,将护套材料包裹在照射后的缆芯表面上辊压制得柔性电缆。
24.首先,将4-氯-4'-羟基二苯甲酮和三羟甲基丙烷三缩水甘油醚反应制得预聚体,将预聚体依次和对苯二甲酸、三羟甲基丙烷三缩水甘油醚、对乙烯基苯甲酸反应制得超支化聚酸酯,将聚乙二醇依次和丁二酸酐、氯化亚砜、对氨基苯硫酚反应制得苯硫酚基聚乙二醇,将超支化聚酸酯和苯硫酚基聚乙二醇反应制得改性超支化聚酸酯,对超支化聚酸酯进行改性,取代的硫促进了二苯甲酮的夺氢光引发效果,二苯硫醚基团在光照下形成硫自由基,引发主体材料中碳碳双键的交联聚合,形成交联网络结构,聚乙二醇支链可以促进弹性微球的稳定形成,并使弹性微球喷涂过程中在缆芯上具有良好的粘附效果,避免弹性微球的脱落,超支化结构可以使弹性微球表面的结构更加的稳定,使弹性微球受热膨胀成中空气囊保持结构的稳定,不破碎坍塌,从而提高了柔性电缆的抗冲击性能。
25.其次,将4,4'-亚甲基双(异氰酸苯酯)和端羟基乙烯基聚硅氧烷反应后和氧化石墨烯反应,再和糠醇反应制得改性氧化石墨烯,使用端羟基乙烯基聚硅氧烷,使改性氧化石墨烯在高温时易形成二氧化硅和碳层附着在主体表面,从而提高了材料的阻燃性能,同时端羟基乙烯基聚硅氧烷上的乙烯基,使改性氧化石墨烯在后续能参与紫外光引发的自由基聚合反应,提高了柔性电缆的抗冲击性能;使用糠醇进行改性,使改性石墨烯可以和主体中的马来酰亚胺基团发生热可逆反应,提高了柔性电缆的自修复效果。
具体实施方式
26.下面将结合本发明实施例,对本发明实施例中的技术方案进行清楚、完整地描述,显然,所描述的实施例仅仅是本发明一部分实施例,而不是全部的实施例。基于本发明中的实施例,本领域普通技术人员在没有做出创造性劳动前提下所获得的所有其他实施例,都属于本发明保护的范围。
27.为了更清楚的说明本发明提供的方法通过以下实施例进行详细说明,在以下实施例中制作的柔性电缆的各指标测试方法如下:
28.抗冲击性能:将各实施例所得的柔性电缆与对比例材料取相同大小质量,按照qj1632标准测定抗冲击强度。
29.阻燃性能:将各实施例所得的柔性电缆与对比例材料取相同大小质量,按照gb/t2406标准法测定极氧指数来测试阻燃性。
30.自修复性能:将各实施例所得的柔性电缆与对比例材料取相同大小质量,用小刀划刻相同深度、大小、密度的伤口,在100℃静置相同时间,再次测量抗冲击强度,计算修复率=修复后抗冲击强度/初始抗冲击强度
31.实施例1
32.一种柔性电缆的制备方法,所述柔性电缆的制备方法主要包括以下制备步骤:
33.(1)超支化聚酸酯的制备:将4-氯-4'-羟基二苯甲酮、三羟甲基丙烷三缩水甘油醚、四丁基溴化铵和n,n-二甲基甲酰胺按质量比10:8:1:20混合均匀,在氮气氛围中,80℃,800r/min搅拌反应3h,在40℃,1kpa静置10h,制得预聚体;将预聚体、对苯二甲酸、四丁基溴化铵和n,n-二甲基甲酰胺按质量比10:5:1:20混合均匀,在氮气氛围中,80℃,800r/min搅拌反应3h,再加入预聚体质量1.4倍的三羟甲基丙烷三缩水甘油醚,继续搅拌反应3h,再加入预聚体质量0.8倍的对乙烯基苯甲酸,继续搅拌反应2h,在40℃,1kpa静置10h,再加入预聚体质量3倍的乙酸乙酯,依次用质量分数5%的碳酸氢钠溶液、质量分数15%氯化钠溶液溶液和去离子水各洗涤5次,将洗涤后溶液用无水硫酸镁干燥并过滤取滤液,在40℃,1kpa静置10h,制得超支化聚酸酯;
34.(2)超支化聚酸酯的改性:将对氨基苯硫酚、三乙胺、二氯甲烷按质量比3:1:30在0℃混合均匀配制成对氨基苯硫酚溶液;将丁二酸酐和分子量为500的聚乙二醇按质量比1:3混合均匀,在70℃,800r/min搅拌4h,再与氯化亚砜、四氢呋喃按质量比15:100:1混合均匀,在40℃,300r/min搅拌反应3h,再升温至60℃继续搅拌反应3h,在10℃,1kpa静置40min,再加入聚乙二醇质量2倍的对氨基苯硫酚溶液,在0℃,300r/min搅拌3h,在室温下静置20h,在-10℃,1kpa静置8h,制得苯硫酚基聚乙二醇;将超支化聚酸酯、苯硫酚基聚乙二醇、氢氧化钾、甲苯和n-甲基吡咯烷酮按质量比6:1:2:50:20混合均匀,在10℃,300r/min搅拌30min,升温至120℃并保持4h,继续升温至150℃并保持4h,冷却至室温过滤取滤液,将滤液以1ml/min的速率滴加到0℃,300r/min搅拌的滤液质量6倍的质量分数38%的盐酸中,过滤并用纯水和石油醚各洗涤3次,再浸没在饱和醋酸钠溶液中,用30khz超声30min,过滤并用纯水和石油醚各洗涤3次,在-10℃,1kpa静置8h,制得改性超支化聚酸酯;
35.(3)弹性微球的制备:将甲基丙烯酸甲酯、丙烯酸甲酯、正庚烷、过氧化二月桂酰、改性超支化聚酸酯按质量比40:14:30:2:25在0℃混合均匀配制成油相,将聚乙烯醇和纯水按质量比1:140混合均匀配制成水相,将油相和水相按质量比1:4倒入反应釜中,密封并保持氮气氛围,以500r/min搅拌30min,在90℃反应12h,冷却至室温后过滤,在20℃,1kpa干燥8h,制得弹性微球;
36.(4)缆芯喷涂:将直径0.04mm的铜丝集束固定成1mm的铜丝束,并在铜丝束外围包裹一层厚度为0.9mm的聚乙烯层,制得导线,将多根导线固定,并在外围缠绕一圈铝带进行固定,铝带厚0.4mm,宽2cm,缠绕间隙2cm,制得缆芯;将聚合物微球和纯水按质量比1:4混合均匀,制得喷涂液,再以0.06g/cm2的量喷涂在缆芯表面,在-1℃,1pa干燥8h,制得喷涂后的缆芯;
37.(5)氧化石墨烯的改性:将八甲基环四硅氧烷、2,4,6,8-四甲基-2,4,6,8-四乙烯基环四硅氧烷按质量比20:1混合均匀,再加入八甲基环四硅氧烷质量0.03倍的四甲基氢氧化铵混合均匀,在100℃,500r/min搅拌4h后,在160℃,1kpa静置4h,端羟基乙烯基聚硅氧烷;将端羟基乙烯基聚硅氧烷、n,n-二甲基甲酰胺按质量比1:10混合均匀配制成滴定液;将氧化石墨烯、n,n-二甲基甲酰胺按质量比1:10混合均匀,在20℃,30khz超声10min配制成氧化石墨烯分散液;将4,4'-亚甲基双(异氰酸苯酯)和n,n-二甲基甲酰胺按质量比1:6混合均匀,在氮气氛围中,70℃,800r/min搅拌条件下,将4,4'-亚甲基双(异氰酸苯酯)质量0.8倍的滴定液以0.1ml/s的速度进行滴加,滴加结束后保持条件不变继续反应2h,加入4,4'-亚甲基双(异氰酸苯酯)质量1.2倍的氧化石墨烯分散液,在氮气氛围中继续反应6h,再加入4,4'-亚甲基双(异氰酸苯酯)质量0.5倍的糠醇,在氮气氛围中继续反应4h,制得改性氧化石墨烯;
38.(6)辊压组装:将改性氧化石墨烯、n,n'-(4,4'-亚甲基二苯基)双马来酰亚胺、聚1,3-丁二烯、聚乙烯按质量比1:1:1:3混合均匀,在140℃混炼30min,制备得到厚度为2mm的护套材料,将喷涂后的缆芯表面用800w的高压汞灯照射5min后,将护套材料包裹在照射后的缆芯表面上,将温度升至100℃静置10min,再用8mpa的压力以220m/min辊压3次,制得柔性电缆。
39.实施例2
40.一种柔性电缆的制备方法,所述柔性电缆的制备方法主要包括以下制备步骤:
41.(1)超支化聚酸酯的制备:将4-氯-4'-羟基二苯甲酮、三羟甲基丙烷三缩水甘油醚、四丁基溴化铵和n,n-二甲基甲酰胺按质量比10:9:1:22混合均匀,在氮气氛围中,85℃,900r/min搅拌反应2.5h,在45℃,1.5kpa静置9h,制得预聚体;将预聚体、对苯二甲酸、四丁基溴化铵和n,n-二甲基甲酰胺按质量比10:6:1:22混合均匀,在氮气氛围中,85℃,900r/min搅拌反应2.5h,再加入预聚体质量1.6倍的三羟甲基丙烷三缩水甘油醚,继续搅拌反应2.5h,再加入预聚体质量0.9倍的对乙烯基苯甲酸,继续搅拌反应2.5h,在45℃,1.5kpa静置9h,再加入预聚体质量4倍的乙酸乙酯,依次用质量分数5.5%的碳酸氢钠溶液、质量分数17%氯化钠溶液溶液和去离子水各洗涤4次,将洗涤后溶液用无水硫酸镁干燥并过滤取滤液,在45℃,1.5kpa静置9h,制得超支化聚酸酯;
42.(2)超支化聚酸酯的改性:将对氨基苯硫酚、三乙胺、二氯甲烷按质量比3:1:35在3℃混合均匀配制成对氨基苯硫酚溶液;将丁二酸酐和分子量为550的聚乙二醇按质量比1:3.5混合均匀,在75℃,900r/min搅拌3.5h,再与氯化亚砜、四氢呋喃按质量比25:350:1混合均匀,在45℃,400r/min搅拌反应2.5h,再升温至65℃继续搅拌反应2.5h,在20℃,1.5kpa静置35min,再加入聚乙二醇质量2.5倍的对氨基苯硫酚溶液,在3℃,400r/min搅拌2.5h,在室温下静置22h,在-5℃,1.5kpa静置7h,制得苯硫酚基聚乙二醇;将超支化聚酸酯、苯硫酚基聚乙二醇、氢氧化钾、甲苯和n-甲基吡咯烷酮按质量比6:1:2.5:55:22混合均匀,在20℃,400r/min搅拌25min,升温至125℃并保持3.5h,继续升温至155℃并保持3.5h,冷却至室温过滤取滤液,将滤液以1.5ml/min的速率滴加到2℃,400r/min搅拌的滤液质量7倍的质量分数37%的盐酸中,过滤并用纯水和石油醚各洗涤4次,再浸没在饱和醋酸钠溶液中,用35khz超声25min,过滤并用纯水和石油醚各洗涤4次,在-5℃,1.5kpa静置7h,制得改性超支化聚酸酯;
43.(3)弹性微球的制备:将甲基丙烯酸甲酯、丙烯酸甲酯、正庚烷、过氧化二月桂酰、改性超支化聚酸酯按质量比45:16:32:3:27在0℃混合均匀配制成油相,将聚乙烯醇和纯水按质量比1:150混合均匀配制成水相,将油相和水相按质量比1:5倒入反应釜中,密封并保持氮气氛围,以600r/min搅拌25min,在95℃反应11h,冷却至室温后过滤,在25℃,1.5kpa干燥7h,制得弹性微球;
44.(4)缆芯喷涂:将直径0.04mm的铜丝集束固定成1mm的铜丝束,并在铜丝束外围包裹一层厚度为0.9mm的聚乙烯层,制得导线,将多根导线固定,并在外围缠绕一圈铝带进行固定,铝带厚0.4mm,宽2cm,缠绕间隙2cm,制得缆芯;将聚合物微球和纯水按质量比1:5混合均匀,制得喷涂液,再以0.07g/cm2的量喷涂在缆芯表面,在-5℃,5pa干燥7h,制得喷涂后的缆芯;
45.(5)氧化石墨烯的改性:将八甲基环四硅氧烷、2,4,6,8-四甲基-2,4,6,8-四乙烯基环四硅氧烷按质量比25:1混合均匀,再加入八甲基环四硅氧烷质量0.04倍的四甲基氢氧化铵混合均匀,在110℃,600r/min搅拌3.5h后,在170℃,1.5kpa静置3.5h,端羟基乙烯基聚硅氧烷;将端羟基乙烯基聚硅氧烷、n,n-二甲基甲酰胺按质量比1:12混合均匀配制成滴定液;将氧化石墨烯、n,n-二甲基甲酰胺按质量比1:12混合均匀,在25℃,35khz超声12min配制成氧化石墨烯分散液;将4,4'-亚甲基双(异氰酸苯酯)和n,n-二甲基甲酰胺按质量比1:7混合均匀,在氮气氛围中,80℃,900r/min搅拌条件下,将4,4'-亚甲基双(异氰酸苯酯)质量1倍的滴定液以0.15ml/s的速度进行滴加,滴加结束后保持条件不变继续反应2.5h,加入4,4'-亚甲基双(异氰酸苯酯)质量1.4倍的氧化石墨烯分散液,在氮气氛围中继续反应5h,再加入4,4'-亚甲基双(异氰酸苯酯)质量0.6倍的糠醇,在氮气氛围中继续反应3.5h,制得改性氧化石墨烯;
46.(6)辊压组装:将改性氧化石墨烯、n,n'-(4,4'-亚甲基二苯基)双马来酰亚胺、聚1,3-丁二烯、聚乙烯按质量比1.5:1:1:3.5混合均匀,在150℃混炼25min,制备得到厚度为2.5mm的护套材料,将喷涂后的缆芯表面用900w的高压汞灯照射6min后,将护套材料包裹在照射后的缆芯表面上,将温度升至110℃静置9min,再用9mpa的压力以230m/min辊压2次,制得柔性电缆。
47.实施例3
48.一种柔性电缆的制备方法,所述柔性电缆的制备方法主要包括以下制备步骤:
49.(1)超支化聚酸酯的制备:将4-氯-4'-羟基二苯甲酮、三羟甲基丙烷三缩水甘油醚、四丁基溴化铵和n,n-二甲基甲酰胺按质量比10:10:1:25混合均匀,在氮气氛围中,90℃,1000r/min搅拌反应2h,在50℃,2kpa静置8h,制得预聚体;将预聚体、对苯二甲酸、四丁基溴化铵和n,n-二甲基甲酰胺按质量比10:7:1:25混合均匀,在氮气氛围中,90℃,1000r/min搅拌反应2h,再加入预聚体质量1.8倍的三羟甲基丙烷三缩水甘油醚,继续搅拌反应3h,再加入预聚体质量1倍的对乙烯基苯甲酸,继续搅拌反应2h,在50℃,2kpa静置8h,再加入预聚体质量5倍的乙酸乙酯,依次用质量分数6%的碳酸氢钠溶液、质量分数20%氯化钠溶液溶液和去离子水各洗涤3次,将洗涤后溶液用无水硫酸镁干燥并过滤取滤液,在50℃,2kpa静置8h,制得超支化聚酸酯;
50.(2)超支化聚酸酯的改性:将对氨基苯硫酚、三乙胺、二氯甲烷按质量比4:1:40在5℃混合均匀配制成对氨基苯硫酚溶液;将丁二酸酐和分子量为600的聚乙二醇按质量比1:4
混合均匀,在80℃,1000r/min搅拌3h,再与氯化亚砜、四氢呋喃按质量比40:300:1混合均匀,在50℃,500r/min搅拌反应2h,再升温至70℃继续搅拌反应2h,在30℃,2kpa静置30min,再加入聚乙二醇质量3倍的对氨基苯硫酚溶液,在5℃,500r/min搅拌2h,在室温下静置24h,在-1℃,2kpa静置6h,制得苯硫酚基聚乙二醇;将超支化聚酸酯、苯硫酚基聚乙二醇、氢氧化钾、甲苯和n-甲基吡咯烷酮按质量比6:2:3:60:25混合均匀,在30℃,500r/min搅拌20min,升温至130℃并保持3h,继续升温至160℃并保持3h,冷却至室温过滤取滤液,将滤液以2ml/min的速率滴加到3℃,500r/min搅拌的滤液质量6倍的质量分数36%的盐酸中,过滤并用纯水和石油醚各洗涤5次,再浸没在饱和醋酸钠溶液中,用40khz超声20min,过滤并用纯水和石油醚各洗涤5次,在-1℃,2kpa静置6h,制得改性超支化聚酸酯;
51.(3)弹性微球的制备:将甲基丙烯酸甲酯、丙烯酸甲酯、正庚烷、过氧化二月桂酰、改性超支化聚酸酯按质量比50:18:35:4:30在0℃混合均匀配制成油相,将聚乙烯醇和纯水按质量比1:160混合均匀配制成水相,将油相和水相按质量比1:6倒入反应釜中,密封并保持氮气氛围,以700r/min搅拌20min,在100℃反应10h,冷却至室温后过滤,在30℃,2kpa干燥6h,制得弹性微球;
52.(4)缆芯喷涂:将直径0.04mm的铜丝集束固定成1mm的铜丝束,并在铜丝束外围包裹一层厚度为0.9mm的聚乙烯层,制得导线,将多根导线固定,并在外围缠绕一圈铝带进行固定,铝带厚0.4mm,宽2cm,缠绕间隙2cm,制得缆芯;将聚合物微球和纯水按质量比1:6混合均匀,制得喷涂液,再以0.08g/cm2的量喷涂在缆芯表面,在-10℃,10pa干燥6h,制得喷涂后的缆芯;
53.(5)氧化石墨烯的改性:将八甲基环四硅氧烷、2,4,6,8-四甲基-2,4,6,8-四乙烯基环四硅氧烷按质量比30:1混合均匀,再加入八甲基环四硅氧烷质量0.05倍的四甲基氢氧化铵混合均匀,在120℃,700r/min搅拌3h后,在180℃,2kpa静置3h,端羟基乙烯基聚硅氧烷;将端羟基乙烯基聚硅氧烷、n,n-二甲基甲酰胺按质量比1:15混合均匀配制成滴定液;将氧化石墨烯、n,n-二甲基甲酰胺按质量比1:15混合均匀,在30℃,40khz超声10min配制成氧化石墨烯分散液;将4,4'-亚甲基双(异氰酸苯酯)和n,n-二甲基甲酰胺按质量比1:8混合均匀,在氮气氛围中,90℃,1000r/min搅拌条件下,将4,4'-亚甲基双(异氰酸苯酯)质量1.2倍的滴定液以0.2ml/s的速度进行滴加,滴加结束后保持条件不变继续反应3h,加入4,4'-亚甲基双(异氰酸苯酯)质量1.6倍的氧化石墨烯分散液,在氮气氛围中继续反应6h,再加入4,4'-亚甲基双(异氰酸苯酯)质量0.7倍的糠醇,在氮气氛围中继续反应3h,制得改性氧化石墨烯;
54.(6)辊压组装:将改性氧化石墨烯、n,n'-(4,4'-亚甲基二苯基)双马来酰亚胺、聚1,3-丁二烯、聚乙烯按质量比2:1:1:4混合均匀,在160℃混炼20min,制备得到厚度为3mm的护套材料,将喷涂后的缆芯表面用1000w的高压汞灯照射5min后,将护套材料包裹在照射后的缆芯表面上,将温度升至120℃静置8min,再用10mpa的压力以240m/min辊压2次,制得柔性电缆。
55.对比例1
56.对比例1的柔性电缆的制备方法与实施例2的区别仅在于步骤(1)的不同,将步骤(1)修改为:将4-氯-4'-羟基二苯甲酮、二缩水甘油醚、四丁基溴化铵和n,n-二甲基甲酰胺按质量比10:9:1:22混合均匀,在氮气氛围中,85℃,900r/min搅拌反应2.5h,在45℃,
1.5kpa静置9h,制得预聚体;将预聚体、对苯二甲酸、四丁基溴化铵和n,n-二甲基甲酰胺按质量比10:6:1:22混合均匀,在氮气氛围中,85℃,900r/min搅拌反应2.5h,再加入预聚体质量1.6倍的二缩水甘油醚,继续搅拌反应2.5h,再加入预聚体质量0.9倍的对乙烯基苯甲酸,继续搅拌反应2.5h,在45℃,1.5kpa静置9h,再加入预聚体质量4倍的乙酸乙酯,依次用质量分数5.5%的碳酸氢钠溶液、质量分数17%氯化钠溶液溶液和去离子水各洗涤4次,将洗涤后溶液用无水硫酸镁干燥并过滤取滤液,在45℃,1.5kpa静置9h,制得线性聚酸酯。并将后续步骤中的“超支化聚酸酯”和“改性超支化聚酸酯”替换成“线性聚酸酯”和“改性线性聚酸酯”,其余步骤同时实施例2。
57.对比例2
58.对比例2的柔性电缆的制备方法与实施例2的区别仅在于不进行步骤(2)并将步骤(3)修改为:将甲基丙烯酸甲酯、丙烯酸甲酯、正庚烷、过氧化二月桂酰、超支化聚酸酯、聚乙二醇月桂酸酯按质量比45:16:32:3:20:7在0℃混合均匀配制成油相,将聚乙烯醇和纯水按质量比1:150混合均匀配制成水相,将油相和水相按质量比1:5倒入反应釜中,密封并保持氮气氛围,以600r/min搅拌25min,在95℃反应11h,冷却至室温后过滤,在25℃,1.5kpa干燥7h,制得弹性微球。其余步骤同时实施例2。
59.对比例3
60.对比例3的柔性电缆的制备方法与实施例2的区别仅在于步骤(5)的不同,将步骤(5)修改为:将聚乙二醇、n,n-二甲基甲酰胺按质量比1:12混合均匀配制成滴定液;将氧化石墨烯、n,n-二甲基甲酰胺按质量比1:12混合均匀,在25℃,35khz超声12min配制成氧化石墨烯分散液;将4,4'-亚甲基双(异氰酸苯酯)和n,n-二甲基甲酰胺按质量比1:7混合均匀,在氮气氛围中,80℃,900r/min搅拌条件下,将4,4'-亚甲基双(异氰酸苯酯)质量1倍的滴定液以0.15ml/s的速度进行滴加,滴加结束后保持条件不变继续反应2.5h,加入4,4'-亚甲基双(异氰酸苯酯)质量1.4倍的氧化石墨烯分散液,在氮气氛围中继续反应5h,再加入4,4'-亚甲基双(异氰酸苯酯)质量0.6倍的糠醇,在氮气氛围中继续反应3.5h,制得改性氧化石墨烯。其余步骤同时实施例2。
61.对比例4
62.对比例4的柔性电缆的制备方法与实施例2的区别仅在于步骤(5)的不同,将步骤(5)修改为:将八甲基环四硅氧烷、2,4,6,8-四甲基-2,4,6,8-四乙烯基环四硅氧烷按质量比25:1混合均匀,再加入八甲基环四硅氧烷质量0.04倍的四甲基氢氧化铵混合均匀,在110℃,600r/min搅拌3.5h后,在170℃,1.5kpa静置3.5h,端羟基乙烯基聚硅氧烷;将端羟基乙烯基聚硅氧烷、n,n-二甲基甲酰胺按质量比1:12混合均匀配制成滴定液;将氧化石墨烯、n,n-二甲基甲酰胺按质量比1:12混合均匀,在25℃,35khz超声12min配制成氧化石墨烯分散液;将4,4'-亚甲基双(异氰酸苯酯)和n,n-二甲基甲酰胺按质量比1:7混合均匀,在氮气氛围中,80℃,900r/min搅拌条件下,将4,4'-亚甲基双(异氰酸苯酯)质量1倍的滴定液以0.15ml/s的速度进行滴加,滴加结束后保持条件不变继续反应2.5h,加入4,4'-亚甲基双(异氰酸苯酯)质量1.4倍的氧化石墨烯分散液,在氮气氛围中继续反应5h,制得改性氧化石墨烯。其余步骤同时实施例2。
63.对比例5
64.一种柔性电缆的制备方法,所述柔性电缆的制备方法主要包括以下制备步骤:
65.(1)缆芯:将直径0.04mm的铜丝集束固定成1mm的铜丝束,并在铜丝束外围包裹一层厚度为0.9mm的聚乙烯层,制得导线,将多根导线固定,并在外围缠绕一圈铝带进行固定,铝带厚0.4mm,宽2cm,缠绕间隙2cm,制得缆芯;
66.(2)氧化石墨烯的改性:将八甲基环四硅氧烷、2,4,6,8-四甲基-2,4,6,8-四乙烯基环四硅氧烷按质量比25:1混合均匀,再加入八甲基环四硅氧烷质量0.04倍的四甲基氢氧化铵混合均匀,在110℃,600r/min搅拌3.5h后,在170℃,1.5kpa静置3.5h,端羟基乙烯基聚硅氧烷;将端羟基乙烯基聚硅氧烷、n,n-二甲基甲酰胺按质量比1:12混合均匀配制成滴定液;将氧化石墨烯、n,n-二甲基甲酰胺按质量比1:12混合均匀,在25℃,35khz超声12min配制成氧化石墨烯分散液;将4,4'-亚甲基双(异氰酸苯酯)和n,n-二甲基甲酰胺按质量比1:7混合均匀,在氮气氛围中,80℃,900r/min搅拌条件下,将4,4'-亚甲基双(异氰酸苯酯)质量1倍的滴定液以0.15ml/s的速度进行滴加,滴加结束后保持条件不变继续反应2.5h,加入4,4'-亚甲基双(异氰酸苯酯)质量1.4倍的氧化石墨烯分散液,在氮气氛围中继续反应5h,再加入4,4'-亚甲基双(异氰酸苯酯)质量0.6倍的糠醇,在氮气氛围中继续反应3.5h,制得改性氧化石墨烯;
67.(3)辊压组装:将改性氧化石墨烯、n,n'-(4,4'-亚甲基二苯基)双马来酰亚胺、聚1,3-丁二烯、聚乙烯按质量比1.5:1:1:3.5混合均匀,在150℃混炼25min,制备得到厚度为2.5mm的护套材料,将缆芯表面用900w的高压汞灯照射6min后,将护套材料包裹在照射后的缆芯表面上,将温度升至110℃静置9min,再用9mpa的压力以230m/min辊压2次,制得柔性电缆。
68.对比例6
69.一种柔性电缆的制备方法,所述柔性电缆的制备方法主要包括以下制备步骤:
70.(1)缆芯:将直径0.04mm的铜丝集束固定成1mm的铜丝束,并在铜丝束外围包裹一层厚度为0.9mm的聚乙烯层,制得导线,将多根导线固定,并在外围缠绕一圈铝带进行固定,铝带厚0.4mm,宽2cm,缠绕间隙2cm,制得缆芯;
71.(2)辊压组装:将氧化石墨烯、n,n'-(4,4'-亚甲基二苯基)双马来酰亚胺、聚1,3-丁二烯、聚乙烯按质量比1.5:1:1:3.5混合均匀,在150℃混炼25min,制备得到厚度为2.5mm的护套材料,将缆芯表面用900w的高压汞灯照射6min后,将护套材料包裹在照射后的缆芯表面上,将温度升至110℃静置9min,再用9mpa的压力以230m/min辊压2次,制得柔性电缆。
72.效果例
73.下表1给出了采用本发明实施例1~3与对比例1~6的柔性电缆的抗冲击性能、阻燃性能和自修复性能的性能分析结果。
74.表1
[0075][0076]
从表1中实施例1~3和对比例1~6的实验数据比较可发现,本发明制得的柔性电缆具有良好的抗冲击性能、阻燃性能和自修复性能。
[0077]
从实施例1、2、3和对比例1的实验数据比较可发现,实施例1、2、3对比对比例1的抗冲击强度高,说明了改性超支化聚酸酯相较于线性结构而言,可以使弹性微球表面的结构更加的稳定,使弹性微球受热膨胀成中空气囊保持结构的稳定,不破碎坍塌,从而提高了柔性电缆的抗冲击性能;从实施例1、2、3和对比例2的实验数据比较可发现,实施例1、2、3对比对比例2的抗冲击强度高,说明了对超支化聚酸酯进行改性,取代的硫促进了二苯甲酮的夺氢光引发效果,二苯硫醚基团在光照下形成硫自由基,引发主体材料中碳碳双键的交联聚合,形成交联网络结构,聚乙二醇支链可以促进弹性微球的稳定形成,并使弹性微球喷涂过程中在缆芯上具有良好的粘附效果,避免弹性微球的脱落,从而提高了柔性电缆的抗冲击性能;从实施例1、2、3和对比例3的实验数据比较可发现,实施例1、2、3对比对比例3的抗冲击强度和极限氧指数高,说明了在改性氧化石墨烯制备过程中使用端羟基乙烯基聚硅氧烷,使改性氧化石墨烯在高温时易形成二氧化硅和碳层附着在主体表面,从而提高了材料的阻燃性能,同时端羟基乙烯基聚硅氧烷上的乙烯基,使改性氧化石墨烯在后续能参与紫外光引发的自由基聚合反应,提高了柔性电缆的抗冲击性能;从实施例1、2、3和对比例4的实验数据比较可发现,实施例1、2、3对比对比例4的修复率高,使用糠醇进行改性,使改性石墨烯可以和主体中的马来酰亚胺基团发生热可逆反应,提高了柔性电缆的自修复效果。
[0078]
对于本领域技术人员而言,显然本发明不限于上述示范性实施例的细节,而且在不背离本发明的精神或基本特征的情况下,能够以其他的具体形式实现本发明。因此,无论从哪一点来看,均应将实施例看作是示范性的,而且是非限制性的,本发明的范围由所附权利要求而不是上述说明限定,因此旨在将落在权利要求的等同要件的含义和范围内的所有变化囊括在本发明内。不应将权利要求中的任何标记视为限制所涉及的权利要求。
再多了解一些
本文用于企业家、创业者技术爱好者查询,结果仅供参考。