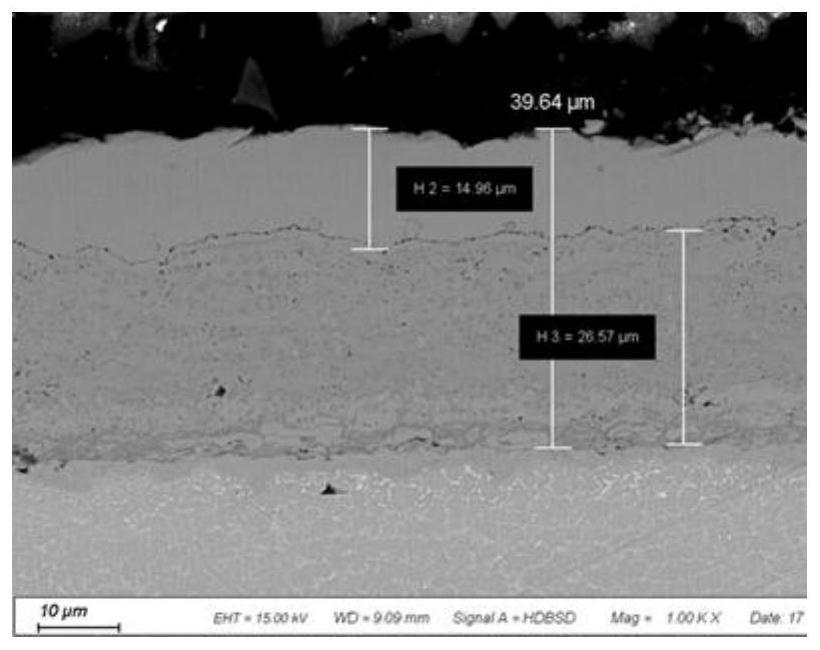
1.本发明涉及热障涂层技术领域,尤其涉及一种铝含量可控的金属粘结层及其制备方法。
背景技术:
2.镍基单晶高温合金叶片广泛应用于燃气涡轮机、航空发动机,热障涂层由于具有优良的隔热、耐高温、抗氧化腐蚀以及抗磨损等性能,在镍基单晶高温合金叶片的表面起到隔热保护的作用。实际应用的涡轮叶片热障涂层的结构为双层结构,即陶瓷层与金属粘结层。其中,金属粘结层的作用是缓解陶瓷层和合金基体的热不匹配,同时由于金属粘结层中含有al元素,在发动机服役过程中,al元素会逐渐氧化,形成一层连续致密的al2o3膜,起到延缓或阻止高温合金继续氧化的作用,从而提高叶片的抗高温氧化腐蚀性能。由于金属粘结层中al元素的含量对al2o3氧化层的生长速度、成分、完整性以及与基体的结合力等因素具有决定作用,而这些因素直接影响着热障涂层的寿命,所以通过对金属粘结层进行渗铝处理,提高金属粘结层中的铝含量,是提高高温合金抗高温氧化和耐热腐蚀性能的普遍方法。
3.现在使用的渗铝方法主要有:包埋渗铝、vpa气相渗铝和cvd气相渗铝,但是由于工艺的优越性,cvd气相渗铝正逐渐取代其他两种渗铝工艺。cvd气相渗铝是指在渗铝过程中工件不与渗铝剂直接接触,而是悬挂在渗铝气氛中,活性al原子通过渗铝气氛传输到合金基体表面并与之发生反应的过程。通常来说,cvd气相渗铝过程包括四个步骤:(1)高温下,铝粉或铁铝合金粉等提供铝原子的原料和氯化氢气体进行反应,生成含有活性al原子[al]的气态的alcl3;(2)含有活性al原子[al]的alcl3扩散传输至基体样品表面;(3)活性al原子[al]吸附于样品表面,同时减少了样品活性表面的面积;(4)吸附后在样品表面的活性al原子[al]与基体中扩散至表面的ni原子结合,形成化合物相。
[0004]
但是在采用cvd气相渗铝形成nial相的过程中,难以对al含量进行控制,很容易导致金属粘结层与高温合金之间的互扩散严重,使得金属粘结层退化速度较快,降低了热障涂层的使用寿命;同时容易使得nial涂层脆性较明显,易于开裂与剥落,限制了热障涂层的使用。
[0005]
因此,提供一种气相渗铝形成nial相过程中铝含量可控的方法,使得金属粘结层不易开裂和剥落,且金属粘结层与基体之间不易相互扩散,成为本领域亟待解决的技术问题。
技术实现要素:
[0006]
本发明的目的在于提供一种铝含量可控的金属粘结层及其制备方法,本发明提供的方法制备的金属粘结层中铝的含量可控,金属粘结层不易开裂和剥落,且金属粘结层与基体之间不会相互扩散。
[0007]
为了实现上述发明目的,本发明提供以下技术方案:
[0008]
本发明提供了一种铝含量可控的金属粘结层的制备方法,包括以下步骤:
[0009]
(1)将高温合金和铝在氢气气氛下进行预热,得到预热高温合金和预热铝;
[0010]
(2)采用氢气和氯化氢的混合气体对所述步骤(1)的预热铝进行活化,得到活化气体;
[0011]
(3)将所述步骤(1)得到的预热高温合金在所述步骤(2)得到的活化气体的氛围中进行渗铝反应,得到金属粘结层;
[0012]
所述步骤(1)中的高温合金为镍基单晶高温合金或表面附有镍基涂层的高温合金;
[0013]
所述步骤(2)中氢气和氯化氢的流量比为(10~80):1;
[0014]
所述步骤(3)中渗铝反应的保温时间为4~8h。
[0015]
优选地,所述步骤(1)中氢气气氛的气压为15~30kpa。
[0016]
优选地,所述步骤(1)中预热的升温速率为5~15℃/min。
[0017]
优选地,所述步骤(1)中预热的温度为850~1080℃,预热的保温时间为0.5~2h。
[0018]
优选地,所述步骤(2)中混合气体的气压为15~30kpa。
[0019]
优选地,所述步骤(2)的混合气体中氯化氢的流量为0.5~1l/min。
[0020]
优选地,所述步骤(3)中渗铝反应的温度为850~1080℃。
[0021]
优选地,所述步骤(3)中渗铝反应的冷却方式为自然冷却。
[0022]
本发明提供了上述技术方案所述制备方法制备得到的金属粘结层,所述金属粘结层的厚度为10~50μm。
[0023]
优选地,所述金属粘结层中的铝含量为30~60at.%。
[0024]
本发明提供了一种铝含量可控的金属粘结层的制备方法,包括以下步骤:(1)将高温合金和铝在氢气气氛下进行预热,得到预热高温合金和预热铝;(2)采用氢气和氯化氢的混合气体对所述步骤(1)的预热铝进行活化,得到活化气体;(3)将所述步骤(1)得到的预热高温合金在所述步骤(2)得到的活化气体的氛围中进行渗铝反应,得到金属粘结层;所述步骤(1)中的高温合金为镍基单晶高温合金或表面附有镍基涂层的高温合金;所述步骤(2)中氢气和氯化氢的流量比为(10~80):1;所述步骤(3)中渗铝反应的保温时间为4~8h。本发明利用氯化氢气体作活化剂对铝进行氯化,形成气相alcl
x
,然后通过气相alcl
x
对镍基涂层进行渗铝,可以提高粘结层中al的含量;将氯化氢和氢气混合后先和铝进行反应,然后再进行气相渗铝,通过控制氢气和氯化氢的流量比,来调整混合气体中含有活性al原子[al]的气态alcl3的含量,从而控制气相渗铝时气氛中铝的含量,同时通过控制渗铝反应的时间,来达到控制金属粘结层中铝含量的作用。实施例的结果显示,本发明提供的制备方法可以使金属粘结层中的铝含量在30~60at.%内可控,从而使其在具有抗高温氧化腐蚀性能的情况下,不易开裂和剥落,且金属粘结层与基体之间互扩散较轻。
附图说明
[0025]
图1为本发明实施例4制备得到的金属粘结层的截面sem形貌。
具体实施方式
[0026]
本发明提供了一种铝含量可控的金属粘结层的制备方法,包括以下步骤:
[0027]
(1)将高温合金和铝在氢气气氛下进行预热,得到预热高温合金和预热铝;
[0028]
(2)采用氢气和氯化氢的混合气体对所述步骤(1)的预热铝进行活化,得到活化气体;
[0029]
(3)将所述步骤(1)得到的预热高温合金在所述步骤(2)得到的活化气体的氛围中进行渗铝反应,得到金属粘结层。
[0030]
本发明将高温合金和铝在氢气气氛下进行预热,得到预热高温合金和预热铝。
[0031]
在本发明中,所述高温合金为镍基单晶高温合金或表面附有镍基涂层的高温合金。在本发明中,所述表面附有镍基涂层的高温合金优选为镍基单晶高温合金或钴基单晶高温合金;所述镍基涂层优选为nicralysi粘结层。本发明对所述合金的具体成分和来源没有特殊的限定,采用本领域技术人员熟知的市售产品或者自行制备均可。本发明对所述合金的制备方法没有特殊的限定,采用本领域技术人员熟知的多弧离子镀等方式进行制备即可。
[0032]
在本发明中,所述高温合金优选为表面清洁干净的高温合金,当所述高温合金不满足上述条件时,本发明优选对所述高温合金进行预处理。在本发明中,所述预处理的方式优选为去油清洗或喷砂清洗。本发明通过预处理,可以去除高温合金表面的杂质。
[0033]
在本发明中,所述预热优选在cvd设备中进行。本发明对所述cvd设备的具体型号没有特殊的限定,采用本领域技术人员熟知的市售产品即可。
[0034]
在本发明中,所述合金优选放置在cvd设备的反应室中,更优选悬挂在反应室内部的上方;所述铝优选放置在所述反应室的石墨迷宫中。本发明对所述铝的用量没有特殊的限定,将石墨迷宫填满即可。
[0035]
预热前,本发明优选对所述cvd设备进行清洗。在本发明中,所述清洗的方式优选为依次进行抽真空和通入氩气。本发明对所述抽真空的真空度没有特殊的限定,根据本领域技术人员的技术常识确定即可。在本发明中,所述通入氩气后的气压优选为大气压。本发明对所述清洗的次数没有特殊的限定,能够将空气完全排除即可。本发明通过清洗,可以去除cvd设备中的空气,从而降低气体中杂质的含量,为后续工艺打下基础,同时排出氧气,提高了工艺的安全性。
[0036]
在本发明中,所述氢气气氛的气压优选为15~30kpa,更优选为20~25kpa。本发明通过在氢气气氛下进行预热,可以使原料的温度更加均匀。
[0037]
在本发明中,所述预热的升温速率优选为5~15℃/min,更优选为10℃/min;所述预热的温度优选为850~1080℃,更优选为900~1000℃,进一步优选为960~980℃;所述预热的保温时间优选为0.5~2h,更优选为1~1.5h。本发明通过控制预热的参数,既能够使原料预热的更加完全,同时可以使温度达到渗铝的温度,便于后续渗铝工艺的进行。
[0038]
得到预热合金和铝后,本发明采用氢气和氯化氢的混合气体对所述预热铝进行活化,得到活化气体。
[0039]
在本发明中,所述混合气体的气压优选为15~30kpa,更优选为20~25kpa;所述混合气体中氯化氢的流量优选为0.5~1l/min,更优选为0.6~0.8l/min;所述氢气和氯化氢的流量比为(10~80):1,优选为(20~60):1,更优选为(30~40):1,进一步优选为30:1。本发明通过控制氢气和氯化氢的流量比,可以起到控制含有活性al原子[al]的气态alcl3的含量的作用,氢气和氯化氢的流量比越大,与铝活化产生的活性al原子越少,流量比越小,
与铝活化产生的活性al原子越多,从而能够控制后续渗铝反应过程中活性al原子与基体的接触量,进而达到了控制金属粘结层中铝含量的目的。
[0040]
在本发明中,所述活化的温度优选为850~1080℃,更优选为900~1000℃,进一步优选为960~980℃。本发明通过使用氢气和氯化氢的混合气体与预热铝进行活化,能够使氯化氢转变为含有活性al原子[al]的气态alcl3,从而便于后续进行气相渗铝。
[0041]
得到活化气体后,本发明将所述预热高温合金在所述活化气体的氛围中进行渗铝反应,得到金属粘结层。
[0042]
在本发明中,所述渗铝反应的温度优选为850~1080℃,更优选为900~1000℃,进一步优选为960~980℃;所述渗铝反应的保温时间为4~8h,优选为5~7h,更优选为6h。本发明通过控制渗铝反应的参数,可以更好的进行渗铝反应,渗铝反应时间越长,铝含量越多,渗铝反应时间短,则铝含量少,通过控制渗铝的时间,可以进一步起到控制铝含量的效果。
[0043]
在本发明中,所述渗铝反应流出的尾气优选通入碱池后排入大气。本发明对所述碱池的具体成分没有特殊的限定,能够将尾气中的氯化氢完全吸收即可。本发明通过上述处理方式可以降低尾气对空气的污染。
[0044]
渗铝反应结束后,本发明优选对所述渗铝反应的产物进行冷却。在本发明中,所述冷却优选在氩气环境中进行;所述冷却的方式优选为自然冷却。本发明通过在上述条件下进行冷却,可以避免冷却过程中进行进一步渗铝,使粘结层中铝含量过高。
[0045]
本发明通过对铝进行活化时,选择采用氢气作为载气将氯化氢和铝混合进行活化,并控制氢气和氯化氢的流量比,能够控制活化铝原子的含量,然后与高温合金接触进行气相渗铝,并控制气相渗铝的时间,达到了控制金属粘结层中铝含量的目的,从而可以对金属粘结层的抗高温氧化和耐热腐蚀性能进行调整,同时克服了金属粘结层容易开裂和剥落的问题,提高了金属粘结层的使用寿命。
[0046]
本发明提供了上述技术方案所述制备方法制备得到的金属粘结层,所述金属粘结层的厚度为10~50μm,优选为15~45μm,更优选为15~40μm,进一步优选为15~30μm。本发明将金属粘结层的厚度控制在上述范围内,即可使金属粘结层具有很好的抗高温氧化和耐热腐蚀性能,同时金属粘结层不易开裂和剥落,金属粘结层与基体的互扩散较轻,涂层不易退化。
[0047]
在本发明中,所述金属粘结层中铝含量优选为30~60at.%。本发明将金属粘结层中铝含量控制在上述范围内,既可以使其具有很好的耐高温和耐腐蚀性能,同时能够使其不易开裂。
[0048]
本发明提供了上述技术方案所述金属粘结层在燃气涡轮机和航空发动机中的应用。
[0049]
在本发明中,所述金属粘结层优选应用于燃气涡轮机和航空发动机中的高温合金叶片中。
[0050]
本发明提供的金属粘结层能够提高燃气涡轮机和航空发动机中高温合金叶片的抗高温氧化和耐热腐蚀性能,同时使叶片不易开裂和剥落,提高了叶片的使用寿命。
[0051]
下面将结合本发明中的实施例,对本发明中的技术方案进行清楚、完整地描述。显然,所描述的实施例仅仅是本发明一部分实施例,而不是全部的实施例。基于本发明中的实
施例,本领域普通技术人员在没有做出创造性劳动前提下所获得的所有其他实施例,都属于本发明保护的范围。
[0052]
实施例1
[0053]
一种铝含量可控的金属粘结层的制备方法:
[0054]
(1)将高温合金经过去油清洗后悬挂在cvd设备反应室的上方,将铝填满所述反应室的石墨迷宫,然后对cvd设备进行清洗,再向cvd设备中通入氢气,在氢气气氛下进行预热,得到预热合金和预热铝;所述高温合金为表面附有镍基涂层的高温合金;所述清洗的方式为依次对cvd设备依次进行抽真空和通入氩气至大气压,清洗的次数为3次;所述氢气气氛的气压为20kpa;所述预热的升温速率为10℃/min,预热的温度为960℃,预热的保温时间为1h;
[0055]
(2)预热结束后,停止通入氢气,然后持续通入经过预热的氢气和氯化氢的混合气体,采用氢气和氯化氢的混合气体对所述步骤(1)的预热铝进行活化,得到活化气体;所述混合气体的气压为20kpa,混合气体中氯化氢的流量为0.6l/min,氢气和氯化氢的流量比为30:1;所述活化的温度为960℃;
[0056]
(3)将所述步骤(1)得到的预热高温合金在所述步骤(2)得到的活化气体的氛围中进行渗铝反应,得到金属粘结层,渗铝反应流出的尾气通过碱池后排入大气,渗铝反应结束后停止通入混合气体,持续通入氩气,自然冷却至室温得到金属粘结层;所述渗铝反应的温度为960℃,渗铝反应的保温时间为4h;
[0057]
所述步骤(1)中高温合金的制备方法为:
[0058]
1)以市售ic21镍基单晶高温合金为基体材料,利用线切割的方法将基体合金切成规格为10
×8×
3mm3的试样,在试样两端分别切一个直径为1mm的孔,以便于在制备金属粘结层时将试样悬挂在支架上;将切好的基体试样依次用200#、600#、800#水磨砂纸将基体六个面全部打磨,使基体表面粗糙度ra《0.8,然后将12条棱全部倒成圆角,将所得试样进行喷砂(所用细砂的目数为20目,压力为0.2mpa),将所得基体试样依次用无水乙醇和丙酮超声清洗15min,烘干,得到预处理的镍基高温合金基体;
[0059]
2)以nicralysi合金为靶材,以质量百分比计,由以下元素组成:cr19.3%、al12.12%、y0.41%、si0.85%和余量的ni,在所述步骤1)得到的预处理的镍基高温合金基体表面进行多弧离子镀,多弧离子镀的弧电流为170a,偏压为15v,本底真空度为2
×
10-3
pa;所述预处理的镍基高温合金基体的温度为350℃,形成nicralysi层,得到高温合金。
[0060]
实施例2
[0061]
一种铝含量可控的金属粘结层的制备方法:
[0062]
(1)将高温合金经过去油清洗后悬挂在cvd设备反应室的上方,将铝填满所述反应室的石墨迷宫,然后对cvd设备进行清洗,再向cvd设备中通入氢气,在氢气气氛下进行预热,得到预热合金和预热铝;所述高温合金为表面附有镍基涂层的高温合金;所述清洗的方式为依次对cvd设备依次进行抽真空和通入氩气至大气压,清洗的次数为3次;所述氢气气氛的气压为20kpa;所述预热的升温速率为10℃/min,预热的温度为960℃,预热的保温时间为1h;
[0063]
(2)预热结束后,停止通入氢气,然后持续通入经过预热的氢气和氯化氢的混合气体,采用氢气和氯化氢的混合气体对所述步骤(1)的预热铝进行活化,得到活化气体;所述
混合气体的气压为20kpa,混合气体中氯化氢的流量为0.6l/min,氢气和氯化氢的流量比为30:1;所述活化的温度为960℃;
[0064]
(3)将所述步骤(1)得到的预热高温合金在所述步骤(2)得到的活化气体的氛围中进行渗铝反应,渗铝反应流出的尾气通过碱池后排入大气,渗铝反应结束后停止通入混合气体,持续通入氩气,自然冷却至室温得到金属粘结层;所述渗铝反应的温度为960℃,渗铝反应的保温时间为6h;
[0065]
所述步骤(1)中的高温合金为ni3al基单晶高温合金ic21,其成分如下(原子百分比):al:16.5%,mo:8.7%,ta:0.8%;cr:2.3%,re:0.2%,y:0.03%和ni:余量;使用线切割将合金沿(001)方向切割成直径为14mm厚度为2mm的圆片。
[0066]
实施例3
[0067]
一种铝含量可控的金属粘结层的制备方法:
[0068]
(1)将高温合金经过去油清洗后悬挂在cvd设备反应室的上方,将铝填满所述反应室的石墨迷宫,然后对cvd设备进行清洗,再向cvd设备中通入氢气,在氢气气氛下进行预热,得到预热合金和预热铝;所述高温合金为表面附有镍基涂层的高温合金;所述清洗的方式为依次对cvd设备依次进行抽真空和通入氩气至大气压,清洗的次数为3次;所述氢气气氛的气压为20kpa;所述预热的升温速率为10℃/min,预热的温度为960℃,预热的保温时间为1h;
[0069]
(2)预热结束后,停止通入氢气,然后持续通入经过预热的氢气和氯化氢的混合气体,采用氢气和氯化氢的混合气体对所述步骤(1)的预热铝进行活化,得到活化气体;所述混合气体的气压为20kpa,混合气体中氯化氢的流量为0.6l/min,氢气和氯化氢的流量比为30:1;所述活化的温度为960℃;
[0070]
(3)将所述步骤(1)得到的预热高温合金在所述步骤(2)得到的活化气体的氛围中进行渗铝反应,渗铝反应流出的尾气通过碱池后排入大气,渗铝反应结束后停止通入混合气体,持续通入氩气,自然冷却至室温得到金属粘结层;渗铝反应的保温时间为8h;
[0071]
所述步骤(1)中的高温合金为ni3al基单晶高温合金ic21,其成分如下(原子百分比):al:16.5%,mo:8.7%,ta:0.8%;cr:2.3%,re:0.2%,y:0.03%和ni:余量;使用线切割将合金沿(001)方向切割成直径为14mm厚度为2mm的圆片。
[0072]
实施例4
[0073]
一种铝含量可控的金属粘结层的制备方法:
[0074]
(1)将高温合金经过去油清洗后悬挂在cvd设备反应室的上方,将铝填满所述反应室的石墨迷宫,然后对cvd设备进行清洗,再向cvd设备中通入氢气,在氢气气氛下进行预热,得到预热合金和预热铝;所述高温合金为表面附有镍基涂层的高温合金;所述清洗的方式为依次对cvd设备依次进行抽真空和通入氩气至大气压,清洗的次数为3次;所述氢气气氛的气压为20kpa;所述预热的升温速率为10℃/min,预热的温度为960℃,预热的保温时间为1h;
[0075]
(2)预热结束后,停止通入氢气,然后持续通入经过预热的氢气和氯化氢的混合气体,采用氢气和氯化氢的混合气体对所述步骤(1)的预热铝进行活化,得到活化气体;所述混合气体的气压为20kpa,混合气体中氯化氢的流量为0.5l/min,氢气和氯化氢的流量比为20:1;所述活化的温度为960℃;
[0076]
(3)将所述步骤(1)得到的预热高温合金在所述步骤(2)得到的活化气体的氛围中进行渗铝反应,渗铝反应流出的尾气通过碱池后排入大气,渗铝反应结束后停止通入混合气体,持续通入氩气,自然冷却至室温得到金属粘结层;所述渗铝反应的温度为960℃,渗铝反应的保温时间为5h;
[0077]
所述步骤(1)中的高温合金和实施例1中的高温合金相同。
[0078]
实施例4制备得到的金属粘结层的厚度为15μm。
[0079]
实施例1~3制备的金属粘结层中铝含量如表1所示:
[0080]
表1实施例1~3制备的金属粘结层中铝含量
[0081]
实施例铝含量(at.%)实施例139.23%实施例245.45%实施例351.83%
[0082]
由表1可以看出,随着渗铝反应时间的延长,金属粘结层中铝含量逐渐增加,说明本发明的技术方案可以起到人为调控金属粘结层中的铝含量的目的。
[0083]
实施例4制备得到的金属粘结层的截面sem形貌如图1所示。由图1可以看出,金属粘结层与基体结合紧密,且互扩散情况较轻,能够避免涂层的退化。
[0084]
以上所述仅是本发明的优选实施方式,应当指出,对于本技术领域的普通技术人员来说,在不脱离本发明原理的前提下,还可以做出若干改进和润饰,这些改进和润饰也应视为本发明的保护范围。
再多了解一些
本文用于企业家、创业者技术爱好者查询,结果仅供参考。