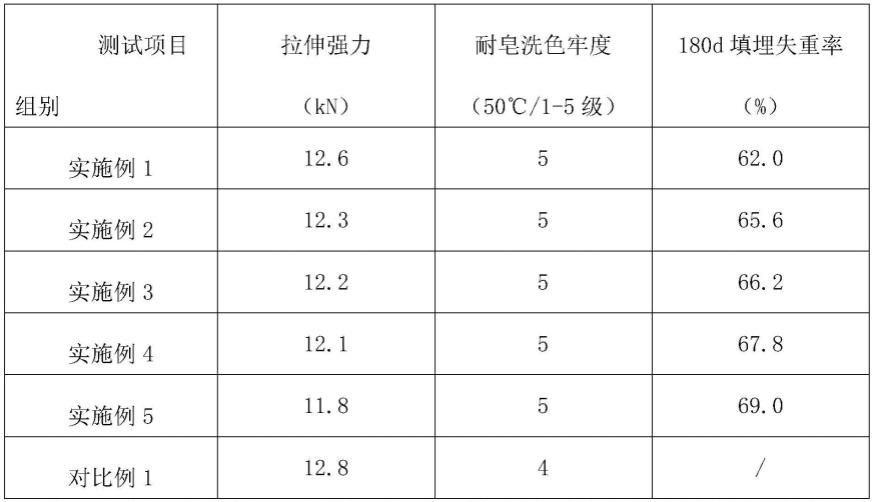
1.本技术涉及纺织面料技术领域,更具体地说,它涉及一种环保型可降解绒布面料及其染色方法。
背景技术:
2.面料,即用来制作编织物的主要材料,作为纺织三要素之一,不仅可以诠释服装的风格和特性,根据其材质不同,还能通过赋予面料不同性能以满足人们多元化的需求,因此以化工材质为主的新型面料也就应运而生。
3.相关技术中的新型面料其为满足人们的性能需求,普遍采用锦纶、绵纶、尼龙之类的合成纤维,上述材质的新型面料虽通过材质本身的特性赋予了新型面料优良的色牢度、舒适度、耐磨性及抗尘性等。
4.但该类新型面料在丢弃之后自然界很难分解,自然降解周期长达数百年,因此对环境污染比较严重,此外使用填埋法或燃烧法对废弃新型面料进行处理时仍会带来一定的污染,因此迫切需要提供一种性能优异、环保型、可自然降解的面料。
技术实现要素:
5.为保障面料综合性能的同时,减少给环境带来的污染和负荷,本技术提供一种环保型可降解绒布面料及其染色方法。
6.第一方面,本技术提供一种环保型可降解绒布面料,采用如下的技术方案:一种环保型可降解绒布面料,由涤纶改性纤维和尼龙纤维按重量比1:(0.3-0.6)复合编制而成;所述涤纶改性纤维的制备步骤如下:s1、先将环糊精、聚乳酸与改性液在碱性条件下加热混合,制得预混料,再将预混料投入双螺杆挤出机,并挤出制得改性母粒;所述改性液由2-辛烯基琥珀酸酐、可降解植物纤维、聚磷酸酯和马来酸酐复配而成;s2、再将聚丁二酸丁二醇酯、聚对苯二甲酸乙二醇酯和s1中的改性母粒混合,得混合料,并进行真空干燥处理;s3、最后将s2中真空干燥处理后的混合料切粒,并与抗菌添加剂、纳米填料粉末混合加入至纺丝机中熔融纺丝,即可制得涤纶改性纤维。
7.通过采用上述技术方案,由上述环糊精、聚乳酸与改性液混合制得的改性母粒,其在与聚丁二酸丁二醇酯、聚对苯二甲酸乙二醇酯熔融纺丝后,可保障涤纶纤维力学性能的同时,赋予绒布面料环保、可降解的能力;分析其原因可能是由于环糊精、聚乳酸与改性液制备改性母粒的过程中,其2-辛烯基琥珀酸酐、聚磷酸酯和马来酸酐可在碱性条件下通过三者间的协同作用与环糊精形成琥珀酸酐环糊精类似物,该琥珀酸酐环糊精类似物可起到显著的交联接枝和粘结作用,继而促使聚乳酸、可降解植物纤维、聚丁二酸丁二醇酯和聚对苯二甲酸乙二醇酯等组分充分
交联改性。
8.上述环保型可降解绒布面料在填埋处理或废弃时,所述的琥珀酸酐环糊精类似物、聚乳酸和聚丁二酸丁二醇酯均可优先发生降解,使得绒布面料表面结构和本身性质可以迅速被破坏,有利于碎片化和小分子化的降解作业进行,此外纺织纤维会因部分结构的降解发生蓬松并引入大量水分,有利于生物降解速率的进一步提升。
9.优选的,所述s1的具体步骤如下:先将环糊精、聚乳酸与改性液按重量比1:(1-2):(2-4)在ph为7.5-8.5的弱碱性条件下加热至60-80℃混合20-30min,制得预混料,再将预混料投入双螺杆挤出机,并挤出制得改性母粒。
10.通过采用上述技术方案,由上述配比环糊精、聚乳酸与改性液以及特定条件制得的改性母粒,其各组分的交联接枝效果最优,聚乳酸、可降解植物纤维、聚丁二酸丁二醇酯和聚对苯二甲酸乙二醇酯等组分可交联粘结成结构密实的复合纤维束,可有效保障面料性能的同时,降解过程中,当部分组分优先降解时,有利于面料和纤维的小分子、碎片化降解进行。
11.优选的,所述改性液由2-辛烯基琥珀酸酐、可降解植物纤维、聚磷酸酯和马来酸酐按重量比1:(0.4-0.6):(0.2-0.3):(0.1-0.2)复配而成。
12.通过采用上述技术方案,由上述组分制得的改性液,其制备过程中形成的琥珀酸酐环糊精类似物结构最为致密、交联接枝和粘结作用最优,可显著促进各组分的改性交联,使得面料兼具了品质和环保性。
13.优选的,所述s2的具体步骤如下:将聚丁二酸丁二醇酯、聚对苯二甲酸乙二醇酯和s1中的改性母粒按重量比1:(1-2):(2-3)混合,得混合料后,于80-100℃的条件对混合料进行真空干燥处理4-8h。
14.通过采用上述技术方案,上述配比的聚丁二酸丁二醇酯、聚对苯二甲酸乙二醇酯和s1中的改性母粒其各组分间的交联粘结效果最优,可有效保障面料性能的同时,降解过程中,当通过部分组分的优先降解,促使面料和纤维进行小分子、碎片化的降解;此外经上述真空干燥处理后的各组分,其内的水分均可被有效去除,含水量低于0.05%,从而减少了因物料含水量过高所导致的水解(自降解)反应进行。
15.优选的,所述s3的具体步骤如下:将s2中真空干燥处理后的混合料切粒,并与抗菌添加剂、纳米填料粉末按重量比1:(0.03-0.05):(0.1-0.2)混合加入至纺丝机中熔融纺丝,即可制得涤纶改性纤维。
16.通过采用上述技术方案,抗菌添加剂、纳米填料粉末的掺入可通过其本身的特性进一步赋予涤纶改性纤维优异的抗菌性能和力学性能,面料的拉伸强度和柔韧度均得以有效保障。
17.优选的,所述纳米填料粉末为纳米碳酸钙、纳米氧化镁和纳米氧化锌中的一种或多种。
18.通过采用上述技术方案,上述组成的纳米填料粉末除能通过其本身的填充改性作用加强涤纶改性纤维的力学性能外,纳米碳酸钙、纳米氧化镁和纳米氧化锌可在面料及纤维部分降解并引入水分后,形成弱电池单元,以此促使小分子及碎片化面料的进一步降解。
19.优选的,所述聚对苯二甲酸乙二醇酯选自废弃涤纶纤维或涤纶废料。
20.通过采用上述技术方案,对废弃涤纶纤维或涤纶废料进行回收改性处理,具有极高的经济效益和环境效益,可有效降低对环境所带来的污染和负荷的同时,还不易对面料本身的特性产生影响。
21.第二方面,本技术提供一种环保型可降解绒布面料的染色方法,采用如下的技术方案:一种环保型可降解绒布面料的染色方法,包括以下步骤:a1、先将所述的环保型可降解绒布面料按浴比1:(3-5)浸入25-40℃的染浴内,然后以0.3-0.5℃/min升温至70-90℃保温40~60min,进行染色;a2、待染色完成后,先对染色后的环保型可降解绒布面料进行第一次水洗,再进行皂洗,然后进行第二次水洗,最后一次经脱水、烘干和开幅定型后,即可得到成品。
22.通过采用上述技术方案,显著简化了染色工艺,相比传统的二浴法或三浴法等工艺,可有效降低能耗损耗,且各项参数条件易于达到,突破常规涤纶dty系列需130℃以上染色的技术壁垒,本技术仅在70-90℃即可完成染色,因此适用于大批量、产业化的生产环保型可降解绒布面料,有利于实现经济效益和环境效益最大化。
23.综上所述,本技术具有以下有益效果:1、本技术由上述环糊精、聚乳酸与改性液混合制得的改性母粒,其在与聚丁二酸丁二醇酯、聚对苯二甲酸乙二醇酯熔融纺丝后,可保障涤纶纤改性维力学性能的同时,赋予绒布面料环保、可降解的能力;2、本技术中涤纶改性纤维的各组分在经熔融纺丝后可交联粘结成结构密实的复合纤维束,有效保障面料性能的同时,降解过程中,通过部分组分优先降解时,有利于面料和纤维的小分子、碎片化降解进行;3、本技术中的染色方法相比传统二浴法或三浴法,显著简化了染色工艺,且能有效降低能耗损耗,仅在70-90℃即可完成染色,适用于大批量、产业化的生产,具有极高的经济效益和环境效益。
具体实施方式
24.以下结合实施例对本技术作进一步详细说明。
25.本技术的各实施例中所用的原料,除下述特殊说明之外,其他均为市售:环糊精为β-环糊精,cas号7585-39-9;聚乳酸,cas号26100-51-6;2-辛烯基琥珀酸酐,cas号42482-06-4;木质素纤维,灰分含量12%、平均长度为1mm;聚磷酸酯,品牌:克拉玛尔/分子量8750;马来酸酐,cas号108-31-6;聚丁二酸丁二醇酯,cas号25777-14-4;聚对苯二甲酸乙二醇酯,cas号25038-59-9;纳米碳酸钙、纳米氧化镁和纳米氧化锌,平均粒径50nm。
26.制备例制备例1
一种涤纶改性纤维,其制备步骤如下:先将环糊精、聚乳酸与改性液按重量比1:1:1在ph为7.5的弱碱性条件下加热至60℃混合30min,制得预混料,再将预混料投入双螺杆挤出机,并挤出制得改性母粒;改性液由2-辛烯基琥珀酸酐、可降解植物纤维、聚磷酸酯和马来酸酐按重量比1:0.3:0.1:0.1复配而成;其中可降解植物纤维为木质素纤维;s2、再将聚丁二酸丁二醇酯、聚对苯二甲酸乙二醇酯和s1中的改性母粒按重量比1:1:1混合,得混合料后,于80℃的条件对混合料进行真空干燥处理8h;s3、最后将s2中真空干燥处理后的混合料切粒,并与抗菌添加剂、纳米填料粉末按重量比1:0.02:0.05混合加入至纺丝机中熔融纺丝,即可制得涤纶改性纤维;其中抗菌添加剂为纳米银离子抗菌剂;纳米填料粉末由纳米氧化镁和纳米氧化锌按重量比1:1组成。
27.制备例2一种涤纶改性纤维,与制备例1的区别之处在于,s1的具体步骤如下:先将环糊精、聚乳酸与改性液按重量比1:1:2在ph为7.5的弱碱性条件下加热至60℃混合30min,制得预混料,再将预混料投入双螺杆挤出机,并挤出制得改性母粒。
28.制备例3一种涤纶改性纤维,与制备例1的区别之处在于,s1的具体步骤如下:先将环糊精、聚乳酸与改性液按重量比1:1.5:3在ph为8.0的弱碱性条件下加热至70℃混合25min,制得预混料,再将预混料投入双螺杆挤出机,并挤出制得改性母粒。
29.制备例4一种涤纶改性纤维,与制备例1的区别之处在于,s1的具体步骤如下:先将环糊精、聚乳酸与改性液按重量比1:2:4在ph为8.5的弱碱性条件下加热至80℃混合20min,制得预混料,再将预混料投入双螺杆挤出机,并挤出制得改性母粒。
30.制备例5一种涤纶改性纤维,与制备例1的区别之处在于,s1的具体步骤如下:先将环糊精、聚乳酸与改性液按重量比1:3:5在ph为8.5的弱碱性条件下加热至80℃混合20min,制得预混料,再将预混料投入双螺杆挤出机,并挤出制得改性母粒。
31.制备例6一种涤纶改性纤维,与制备例1的区别之处在于,改性液由2-辛烯基琥珀酸酐、可降解植物纤维、聚磷酸酯和马来酸酐按重量比1:0.4:0.2:0.1复配而成。
32.制备例7一种涤纶改性纤维,与制备例1的区别之处在于,改性液由2-辛烯基琥珀酸酐、可降解植物纤维、聚磷酸酯和马来酸酐按重量比1:0.5:0.25:0.15复配而成。
33.制备例8一种涤纶改性纤维,与制备例1的区别之处在于,改性液由2-辛烯基琥珀酸酐、可降解植物纤维、聚磷酸酯和马来酸酐按重量比1:0.6:0.3:0.2复配而成。
34.制备例9一种涤纶改性纤维,与制备例1的区别之处在于,改性液由2-辛烯基琥珀酸酐、可
降解植物纤维、聚磷酸酯和马来酸酐按重量比1:0.8:0.4:0.3复配而成。
35.制备例10一种涤纶改性纤维,与制备例1的区别之处在于,s2的具体步骤如下:将聚丁二酸丁二醇酯、聚对苯二甲酸乙二醇酯和s1中的改性母粒按重量比1:1:2混合,得混合料后,于80℃的条件对混合料进行真空干燥处理8h。
36.制备例11一种涤纶改性纤维,与制备例1的区别之处在于,s2的具体步骤如下:将聚丁二酸丁二醇酯、聚对苯二甲酸乙二醇酯和s1中的改性母粒按重量比1:1.5:2.5混合,得混合料后,于90℃的条件对混合料进行真空干燥处理6h。
37.制备例12一种涤纶改性纤维,与制备例1的区别之处在于,s2的具体步骤如下:将聚丁二酸丁二醇酯、聚对苯二甲酸乙二醇酯和s1中的改性母粒按重量比1:2:3混合,得混合料后,于100℃的条件对混合料进行真空干燥处理4h。
38.制备例13一种涤纶改性纤维,与制备例1的区别之处在于,s2的具体步骤如下:将聚丁二酸丁二醇酯、聚对苯二甲酸乙二醇酯和s1中的改性母粒按重量比1:3:4混合,得混合料后,于100℃的条件对混合料进行真空干燥处理4h。
39.制备例14一种涤纶改性纤维,与制备例1的区别之处在于,s3的具体步骤如下:将s2中真空干燥处理后的混合料切粒,并与抗菌添加剂、纳米填料粉末按重量比1:0.03:0.1混合加入至纺丝机中熔融纺丝,即可制得涤纶改性纤维。
40.制备例15一种涤纶改性纤维,与制备例1的区别之处在于,s3的具体步骤如下:将s2中真空干燥处理后的混合料切粒,并与抗菌添加剂、纳米填料粉末按重量比1:0.04:0.15混合加入至纺丝机中熔融纺丝,即可制得涤纶改性纤维。
41.制备例16一种涤纶改性纤维,与制备例1的区别之处在于,s3的具体步骤如下:将s2中真空干燥处理后的混合料切粒,并与抗菌添加剂、纳米填料粉末按重量比1:0.05:0.2混合加入至纺丝机中熔融纺丝,即可制得涤纶改性纤维。
42.制备例17一种涤纶改性纤维,与制备例1的区别之处在于,s3的具体步骤如下:将s2中真空干燥处理后的混合料切粒,并与抗菌添加剂、纳米填料粉末按重量比1:0.05:0.3混合加入至纺丝机中熔融纺丝,即可制得涤纶改性纤维。
43.制备例18一种涤纶改性纤维,与制备例1的区别之处在于,纳米填料粉末由纳米碳酸钙和纳米氧化镁按重量比1:0.6组成。
44.制备例19一种涤纶改性纤维,与制备例1的区别之处在于,纳米填料粉末由纳米碳酸钙、纳米氧化镁和纳米氧化锌按重量比1:2:2组成。
45.制备例20一种涤纶改性纤维,与制备例1的区别之处在于,聚对苯二甲酸乙二醇酯选自废弃涤纶纤维或涤纶废料。
46.性能检测试验先选取实施例和对比例中制得的环保型可降解绒布面料作为测试对象,然后分别测试其力学性能、染色性能和降解性能,具体检测步骤和检测标准如下:(1)面料力学性能:本技术以面料受到直接拉伸到断裂时所需的力,即拉伸强力,来表征面料的力学性能,将每组面料裁切成三组100mm*150mm的样条,以长边为测试方向进行检测,测试结果取平均值记入,具体检测标准可参照astm d5034-2017《面料拉伸强力测试》。
47.(2)面料染色性能:本技术以耐皂洗色牢度来表征面料的染色性能,将每组面料裁切成三组40mm*100mm的样条后,先于50℃进行皂洗45min,再对样条进行冲洗,最后依据aatcc灰色样卡进行评级并记录,可评1-5级,可取半级,具体检测标准可参照gb/t 3921-2008《纺织品色牢度试验耐皂洗色牢度》。
48.(3)面料降解性能:本技术以面料经填埋处理后的失重率来表证其降解性能,先称取(200g)面料并填埋到试验土壤中,其中填埋条件为地下50厘米,土壤平均温度26.3℃、水分80%,待180天后取出残余面料,经干燥除水后,即可根据质量变化量求得失重率。实施例
49.实施例1一种环保型可降解绒布面料,由制备例1中涤纶改性纤维和尼龙纤维按重量比1:0.4捻制而成的复合纱线编制而成;其编制结构为平针横列双珠地网眼结构,纱线规格为280dtex;然后按如下步骤对上述面料进行染色:a1、先将所述的环保型可降解绒布面料按浴比1:5浸入40℃的染浴内,然后以0.4℃/min升温至80℃保温60min,进行染色;本技术中染色工艺仅以上述优选条件为例,在其他实施例中还可以为其他操作条件,上述范围内的条件变更并不影响实际染色性能;染浴由如下重量的组分组成(按每kg计算),本技术仅以常见的染浴配方为例,在其他实施例中还可以选用其他组分的染浴:活性红195120g、分散黄5480g、匀染剂o 5g、乳化剂aeo-95g、分散剂nno 5g、余量为水;a2、待染色完成后,先对染色后的环保型可降解绒布面料进行第一次水洗,再进行皂洗,然后进行第二次水洗,最后一次经脱水、烘干和开幅定型后,即可得到成品。
50.实施例2-5一种环保型可降解绒布面料,与实施例1的不同之处在于,所用涤纶改性纤维的使用情况不同,具体对应关系如下表所示。
51.表:实施例2-5中涤纶改性纤维使用情况对照表
组别涤纶改性纤维实施例2由制备例2制得实施例3由制备例3制得实施例4由制备例4制得实施例5由制备例5制得对比例1一种环保型可降解绒布面料,与实施例1的不同之处在于,由涤纶纤维和尼龙纤维按重量比1:0.4捻制而成的复合纱线编制而成,其中涤纶纤维未经改性处理。
52.抽取上述实施例1-5和对比例1中的环保型可降解绒布面料各三组,按上述测量步骤和测量标准测试其力学性能、染色性能和降解性能,测试结果取平均值记入下表。
53.表:实施例1-5、对比例1测试结果从上表中可以看出,实施例1-5中制得环保型可降解绒布面料均兼具优良的力学性能和降解能力,其拉伸强力高达11.8-12.6kn,与未改性组即对比例1基本持平,填埋180d后的失重率高达62.0-69.0%,而对比例1不具备降解能力;此外本技术的染色工艺相比传统的二浴法或三浴法显著简化,可有效降低能耗损耗,仅在70-90℃即可完成染色,其耐皂洗色牢度为4-5级;综上可见由上述配比环糊精、聚乳酸与改性液以及特定条件制得的改性母粒,其各组分的交联接枝效果最优,聚乳酸、可降解植物纤维、聚丁二酸丁二醇酯和聚对苯二甲酸乙二醇酯等组分可交联粘结成结构密实的复合纤维网,可有效保障面料性能的同时,降解过程中,当部分组分优先降解时,有利于面料和纤维的小分子、碎片化降解进行;分析其原因可能是由于环糊精、聚乳酸与改性液制备改性母粒的过程中,其2-辛烯基琥珀酸酐、聚磷酸酯和马来酸酐可在碱性条件下通过三者间的协同作用与环糊精形成琥珀酸酐环糊精类似物,该琥珀酸酐环糊精类似物可起到显著的交联接枝和粘结作用,继而促使聚乳酸、可降解植物纤维、聚丁二酸丁二醇酯和聚对苯二甲酸乙二醇酯等组分充分交联改性。
54.此外由上表还可以看出实施例4,即制备例4为优选例,上述条件制得的涤纶改性纤维可有效赋予面料优良的力学性能和降解性能,且随着聚乳酸、改性液等组分的比例的增加,虽有利于面料的降解,但会对面料的力学性能造成一定影响,参见实施例1-4。
55.实施例6-9一种环保型可降解绒布面料,与实施例1的不同之处在于,所用涤纶改性纤维的使用情况不同,具体对应关系如下表所示。
56.表:实施例6-9中涤纶改性纤维使用情况对照表组别涤纶改性纤维实施例6由制备例6制得实施例7由制备例7制得实施例8由制备例8制得实施例9由制备例9制得抽取上述实施例6-9中的环保型可降解绒布面料各三组,按上述测量步骤和测量标准测试其力学性能、染色性能和降解性能,测试结果取平均值记入下表。
57.表:实施例6-9测试结果从上表中可以看出,实施例6-9中制得环保型可降解绒布面料均兼具优良的力学性能和降解能力,其拉伸强力高达12.2-12.7kn;填埋180d后的失重率高达62.0-65.2%;耐皂洗色牢度为5级;可见由上述组分制得的改性液,其制备过程中形成的琥珀酸酐环糊精类似物结构最为致密、交联接枝和粘结作用最优,可显著促进各组分的改性交联,使得面料兼具了品质和环保性。
58.此外由上表还可以看出实施例8,即改性液由2-辛烯基琥珀酸酐、可降解植物纤维、聚磷酸酯和马来酸酐按重量比1:(0.4-0.6):(0.2-0.3):(0.1-0.2)复配时为优选比例;上述条件所得的涤纶改性纤维可有效赋予面料优良的力学性能和降解性能,且随着可降解植物纤维、聚磷酸酯和马来酸酐等组分的比例的增加,其降解性能均进一步提升,但超出特定范围后,则会导致面料的力学性能小幅度下降。
59.实施例10-13
一种环保型可降解绒布面料,与实施例1的不同之处在于,所用涤纶改性纤维的使用情况不同,具体对应关系如下表所示。
60.表:实施例10-13中涤纶改性纤维使用情况对照表组别涤纶改性纤维实施例10由制备例10制得实施例11由制备例11制得实施例12由制备例12制得实施例13由制备例13制得抽取上述实施例10-13中的环保型可降解绒布面料各三组,按上述测量步骤和测量标准测试其力学性能、染色性能和降解性能,测试结果取平均值记入下表。
61.表:实施例10-13测试结果从上表中可以看出,实施例1、10-13中制得环保型可降解绒布面料均兼具优良的力学性能和降解能力,其拉伸强力高达11.8-12.6kn;填埋180d后的失重率高达62.0-67.8%;耐皂洗色牢度为5级;可见上述配比聚丁二酸丁二醇酯、聚对苯二甲酸乙二醇酯和改性母粒其各组分间的交联粘结效果最优,可保障面料性能的同时,降解过程中,能有效促使面料和纤维进行小分子、碎片化的降解;此外经上述真空干燥条件处理后的各组分,其内的水分均可被有效去除,含水量低于0.05%,从而减少了因物料含水量过高所导致的水解(自降解)反应进行。
62.实施例14-19一种环保型可降解绒布面料,与实施例1的不同之处在于,所用涤纶改性纤维的使用情况不同,具体对应关系如下表所示。
63.表:实施例14-19中涤纶改性纤维使用情况对照表组别涤纶改性纤维实施例14由制备例14制得实施例15由制备例15制得实施例16由制备例16制得
实施例17由制备例17制得实施例18由制备例18制得实施例19由制备例19制得抽取上述实施例14-19中的环保型可降解绒布面料各三组,按上述测量步骤和测量标准测试其力学性能、染色性能和降解性能,测试结果取平均值记入下表。
64.表:实施例14-19测试结果19测试结果从上表中可以看出,实施例1、14-19中制得环保型可降解绒布面料均兼具优良的力学性能和降解能力,其拉伸强力高达12.6kn;填埋180d后的失重率高达61.2-63.2%;耐皂洗色牢度为5级;可见抗菌添加剂、纳米填料粉末的掺入可通过其本身的特性进一步赋予涤纶改性纤维优异的抗菌性能和力学性能,面料的拉伸强度和柔韧度均得以有效保障;此外纳米碳酸钙、纳米氧化镁和纳米氧化锌可在面料及纤维部分降解并引入水分后,形成弱电池单元,以此促使小分子及碎片化面料的进一步降解,参见实施例1、18-19,即多组分的纳米填料粉末间具有协同效果。
65.实施例20一种环保型可降解绒布面料,与实施例1的不同之处在于,所用涤纶改性纤维由制备例20制得。
66.抽取上述实施例20中的环保型可降解绒布面料各三组,按上述测量步骤和测量标准测试其力学性能、染色性能和降解性能,测试结果取平均值记入下表。
67.表:实施例1、20测试结果
从上表中可以看出,实施例1、20中制得环保型可降解绒布面料均兼具优良的力学性能和降解能力,其拉伸强力高达12.5-126kn;填埋180d后的失重率高达62.0-62.2%;耐皂洗色牢度为5级;可见对废弃涤纶纤维或涤纶废料进行回收改性处理制得的面料,其各项性能得以保障的同时,还可有效降低对环境所带来的污染和负荷,具有极高的经济效益和环境效益。
68.本具体实施例仅仅是对本技术的解释,其并不是对本技术的限制,本领域技术人员在阅读完本说明书后可以根据需要对本实施例做出没有创造性贡献的修改,但只要在本技术的权利要求范围内都受到专利法的保护。
再多了解一些
本文用于企业家、创业者技术爱好者查询,结果仅供参考。