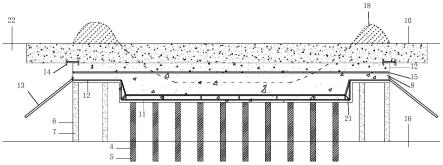
1.本发明属于路面养护技术领域,尤其涉及超宽超深车辙微表处修补结构及施工方法。
背景技术:
2.随着国民经济的高速发展,我国公路建设事业取得了突破性的进展。受气候,地理,交通条件及其它因素的影响,我国早期建成的高等级沥青混凝土路面陆续进入维修养护期。车辙是车辆在路面上行驶后留下的车轮的压痕。绝大多数车辙是由于在交通荷载产生的剪切应力的作用下,路面层材料失稳,凹陷和横向位移形成的。现代路面车辙是路面周期性评价及路面养护中的一个重要指标。路面车辙深度直接反映了车辆行驶的舒适度及路面的安全性和使用期限。
3.微表处快速修复车辙技术是以聚合物改性乳化沥青为粘结料、借助专用的摊铺设备进行施工的一种冷拌沥青混合料不等厚度薄层摊铺技术,具有施工速度快、成本低、开放交通快、效果好等特点,可以迅速恢复和改善原沥青路面的平整度,提高防水性和抗滑性。采用该技术进行车辙修复同传统的铣刨、热摊铺罩面相比具有施工方便、快速、路用性能优良、开放交通快等特点,并且只有按照中心提出的配合比设计方法进行设计,完全可以避免出现二次车辙,这是铣刨、热摊铺罩面技术所无法实现的。但是该技术也有明显缺点,遇到超宽超深车辙修补,所需材料成本较高,且微表处路面噪声明显高于普通沥青路面,不仅严重影响驾乘人员的舒适性,更影响到城市环境及居民生活质量,严重制约了微表处养护技术的全面发展。此外,微表处混合料呈悬浮密实结构,粗集料之间的离散性加大,粗细集料分布极易不均匀,难以形成骨架结构,抗飞散能力差。
技术实现要素:
4.本发明目的在于解决现有技术中存在的上述技术问题,提供超宽超深车辙微表处修补结构及施工方法,能够通过微钻孔注浆和微钻孔高聚物注浆,提高了修补路面的承载力和抗车辙能力,增强了与原路面和路基的整体性,避免重复修补车辙而造成的浪费,提高运营效率。
5.为了解决上述技术问题,本发明采用如下技术方案:
6.超宽超深车辙微表处修补结构,其特征在于:包括自上而下依次排布的第一开挖槽、第二开挖槽和第三开挖槽,第一开挖槽、第二开挖槽和第三开挖槽呈阶梯状,第三开挖槽的底部连通有第一注浆孔,第一注浆孔内设有第一填充物,第二开挖槽的底部设有第二注浆孔,第二注浆孔内设有第二填充物,第三开挖槽、第二开挖槽和第一开挖槽从下而上依次设有再利用层、ms-2型微表处层和ms-3型微表处层。在修复时,通过在底部开设为钻孔注浆,提高修补路面的承载能力和抗车辙能力,增强了与原路面和路基的整体性,避免重复修补车辙而造成的浪费,提高运营效率。通过设置ms-2微表处层过渡到ms-3微表处层,可提高微表处的抗飞散能力,同时显著降低路面噪声。
7.进一步,第三开挖槽的底部设有双层钢丝格栅,通过双层钢丝格栅的设置,能够提高整体强度和耐腐蚀性能,有效分配载荷,提高可承受的最大载荷,提高路面结构整体性和抗车辙能力。
8.进一步,第二开挖槽设有单层钢丝格栅,通过单层钢丝格栅的设置,能够提高整体强度和耐腐蚀性能,有效分配载荷,提高可承受的最大载荷,提高路面结构整体性和抗车辙能力。
9.进一步,第二开挖槽的两侧设有微锚杆,微锚杆与单层钢丝格栅相连接。微锚杆强度大,可承受更大的变载荷,提高路面结构整体性和抗车辙能力。
10.进一步,ms-2型微表处层和ms-3型微表处层之间设有加强段,加强段由加强钢丝格栅、防水布和钢条组成,防水布设于加强钢丝格栅上,钢条设于加强钢丝格栅的两侧。加强段施工简便,有效增强ms-2微表处层和ms-3微表处层的连接薄弱处,提高路面结构整体性和局部防水能力。
11.进一步,再利用层和ms-2型微表处层之间设有粘结层。提高再利用层和ms-2型微表处层之间的粘连效果,提高路面整体性。
12.进一步,再利用层由粒径5.0~10.0mm路面破碎颗粒、粒径1.0mm~5.0mm碎屑轮胎、石灰石粉、水泥浆和早强剂按照一定的配比组成。再利用层有效利用原有路面破碎颗粒中粒径5.0~10.0mm的沥青混合料,同时用石灰石粉替代天然细砂,所制得的浆状混合物性能好,能够大幅度降低微表处的成本,经济环保。
13.进一步,第一填充物采用专用树脂和硬化剂组成的高聚物材料进行微钻孔高聚物注浆;第二填充物采用水泥砂浆微钻孔注浆。通过微钻孔注浆和微钻孔高聚物注浆,提高了修补路面的承载力和抗车辙能力,增强了与原路面和路基的整体性。
14.超宽超深车辙微表处修补结构的施工方法,其特征在于包括以下步骤:
15.1)车辙开挖区施工:根据车辙尺寸确定车辙开挖区开挖宽度和深度,若车辙宽度为l,深度为h,左车辙凸缘宽度为l1,右车辙凸缘宽度为l2,则第一开挖槽的开挖宽度为l 2*l1 2*l2,深度为0.5h,第二开挖槽的开挖宽度为l l1 l2,深度为0.5h,第三开挖槽的开挖宽度为l,深度为0.5h;
16.2)在第三开挖槽下方的路面结构层进行微钻孔形成第一注浆孔,钻入路基层深度达到3-5d,微钻孔间距3-5d,d为微钻孔直径;
17.3)提前准备专用树脂(例如环氧树脂),掺入适量触媒型硬化剂(例如阳离子起始剂),不需要精确配比的情况下,能够让树脂自身聚合组成高聚物材料,然后往第三开挖槽的第一注浆孔内下放注浆管,安装注射帽后,进行微钻孔高聚物注浆形成第一填充物;
18.4)在第二开挖槽两侧下方的路面结构层进行微钻孔形成第二注浆孔,深度钻至路面结构层底部,微钻孔间距5-7d,d为微钻孔直径,若间距不够,至少形成两排钻孔;
19.5)制备好水泥浆,往第二开挖槽的第二注浆孔内下放注浆管并安装注射帽,然后进行微钻孔注浆形成第二填充物;
20.6)在第三开挖槽底部铺设双层钢丝格栅,第二开挖槽两侧底部铺设单层钢丝格栅,单层钢丝格栅和双层钢丝格栅做好搭接,单层钢丝格栅另一侧利用向路面结构层打设微锚杆进行固定;
21.7)将车辙开挖区开挖后的路面碎块进行破碎加工,然后将粒径5.0~10.0mm的沥
青混合料进行筛分出来,同时将粒径5.0~10.0mm的沥青混合料进行清理并收集备用
22.8)按照路面破碎颗粒中粒径5.0~10.0mm的沥青混合料45%-60%、粒径1.0~5.0mm轮胎碎屑10%-20%、石灰石粉10%-15%、水泥浆15%-20%和早强剂1%-2%的配比进行混合搅拌,形成浆状回填混合物;
23.9)将制备好的浆状回填混合物摊铺回填车辙开挖区,形成0.75h厚度的破碎路面回收再利用层,具有一定的可自密性;
24.10)待破碎路面回收再利用层强度达到70%,进行表面拉毛,然后施工粘结层,紧接着在粘结层上方施工铺填ms-2型微表处层,厚度为0.25h;
25.11)提前制作好加强段构件,在第一开挖槽和第二开挖槽拐点处将一端的钢条打设入路面结构层,另一端的钢条打设入ms-2型微表处层;
26.12)将路面破碎颗粒中粒径5.0~10.0mm的沥青混合料,掺入适量石屑、乳化沥青、水和添加剂制备形成再生乳化沥青稀浆混合料,用于施工ms-3型微表处层;
27.13)安装好加强段后,在ms-2型微表处层上方施工铺填ms-3型微表处层,厚度为0.5h,最终完成超宽超深车辙微表处修补结构的施工。
28.本发明由于采用了上述技术方案,具有以下有益效果:
29.1、本发明通过微钻孔注浆和微钻孔高聚物注浆,提高了修补路面的承载力和抗车辙能力,增强了与原路面和路基的整体性,避免重复修补车辙而造成的浪费,提高运营效率,技术效益优势明显。
30.2、本发明中的破碎面回收再利用层,有效利用原有路面废旧料中粒径5.0~10.0mm的沥青混合料,同时用石灰石粉替代天然细砂,所制得的浆状混合物性能好,能够大幅度降低微表处的成本,经济环保。
31.3、本发明通过设置ms-2微表处层过渡到ms-3微表处层,可提高微表处的抗飞散能力,同时显著降低路面噪声,另外设置的连接加强段,有效增强ms-2微表处层和ms-3微表处层的连接薄弱处,提高路面结构整体性和局部防水能力。
32.4、本发明设置的微锚杆和钢丝格栅,强度大、耐腐蚀,施工便捷,有效的分配载荷,可承受更大的变载荷,提高路面结构整体性和抗车辙能力。
33.5、本发明将原有路面废旧料中粒径5.0~10.0mm的沥青混合料用于ms-3微表处层沥青混合料的制备,充分利用路面废旧料中回收的沥青混合料,经济和环保效益明显。
附图说明
34.下面结合附图对本发明作进一步说明:
35.图1是超宽超深车辙微表处修补结构的示意图;
36.图2是车辙开挖区的断面示意图;
37.图3是微钻孔高聚物注浆的布置示意图;
38.图4是微钻孔注浆的布置示意图;
39.图5是钢丝格栅的布置示意图;
40.图6是破碎路面回收再利用层的示意图;
41.图7是ms-2型微表处层的示意图;
42.图8是连接加强段的布置示意图;
43.图9是连接加强段的局部布置立体示意图;
44.图10是超宽超深车辙微表处修补结构的施工工艺流程图。
45.图中,1-第一开挖槽;2-第二开挖槽;3-第三开挖槽;4-第一注浆孔;5-第一填充物;6-第二注浆孔;7-第二填充物;8-再利用层;9-ms-2型微表处层;10-ms-3型微表处层;11-双层钢丝格栅;12-单层钢丝格栅;13-微锚杆;14-加强段;15-粘结层;16-路基层;17-车辙;18-车辙凸缘;19-防水布;20-钢条;21-刚性支撑;22-路面结构层;23-加强钢丝格栅。
具体实施方式
46.如图2所示为路面车辙破损的结构图,车辙17两端形成车辙凸缘18。
47.如图1、图3至图9所示,为本发明超宽超深车辙微表处修补结构,包括自上而下依次排布的第一开挖槽1、第二开挖槽2和第三开挖槽3,第一开挖槽1、第二开挖槽2和第三开挖槽3呈阶梯状,第三开挖槽3的底部连通有第一注浆孔4,第一注浆孔4内设有第一填充物5,第二开挖槽2的底部设有第二注浆孔6,第二注浆孔6内设有第二填充物7,第三开挖槽3、第二开挖槽2和第一开挖槽1从下而上依次设有再利用层8、ms-2型微表处层9和ms-3型微表处层10。在修复时,通过在底部开设为钻孔注浆,提高修补路面的承载能力和抗车辙能力,增强了与原路面和路基的整体性,避免重复修补车辙而造成的浪费,提高运营效率。通过设置ms-2型微表处层9过渡到ms-3型微表处层10,可提高微表处的抗飞散能力,同时显著降低路面噪声。
48.第三开挖槽3的底部设有双层钢丝格栅11,通过双层钢丝格栅11的设置,能够提高整体强度和耐腐蚀性能,有效分配载荷,提高可承受的最大载荷,提高路面结构整体性和抗车辙能力。
49.第二开挖槽2设有单层钢丝格栅12,通过单层钢丝格栅12的设置,能够提高整体强度和耐腐蚀性能,有效分配载荷,提高可承受的最大载荷,提高路面结构整体性和抗车辙能力。
50.第二开挖槽2的两侧设有微锚杆13,微锚杆13与单层钢丝格栅12相连接。微锚杆13强度大,可承受更大的变载荷,提高路面结构整体性和抗车辙能力。
51.ms-2型微表处层9和ms-3型微表处层10之间设有加强段14,加强段14由加强钢丝格栅23、防水布19和钢条20组成,防水布19设于加强钢丝格栅23上,钢条设于加强钢丝格栅的两侧。加强段14施工简便,有效增强ms-2微表处层和ms-3微表处层的连接薄弱处,提高路面结构整体性和局部防水能力。
52.再利用层8和ms-2型微表处层9之间设有粘结层15。提高再利用层8和ms-2型微表处层9之间的粘连效果,提高路面整体性。
53.再利用层由粒径5.0~10.0mm路面破碎颗粒、粒径1.0~5.0mm碎屑轮胎、石灰石粉、水泥浆和早强剂按照一定的配比组成。再利用层有效利用原有路面破碎颗粒中粒径5.0~10.0mm的沥青混合料,同时用石灰石粉替代天然细砂,所制得的浆状混合物性能好,能够大幅度降低微表处的成本,经济环保。
54.第一填充物采用专用树脂和硬化剂组成的高聚物材料进行微钻孔高聚物注浆;第二填充物采用水泥砂浆微钻孔注浆。通过微钻孔注浆和微钻孔高聚物注浆,提高了修补路面的承载力和抗车辙能力,增强了与原路面和路基的整体性。
55.超宽超深车辙微表处修补结构的施工方法,包括以下步骤:
56.1)车辙开挖区施工:根据车辙尺寸确定车辙开挖区开挖宽度和深度,若车辙宽度为l,深度为h,左车辙凸缘宽度为l1,右车辙凸缘宽度为l2,则第一开挖槽(1)的开挖宽度为l 2*l1 2*l2,深度为0.5h,第二开挖槽(2)的开挖宽度为l l1 l2,深度为0.5h,第三开挖槽(3)的开挖宽度为l,深度为0.5h;
57.2)在第三开挖槽(3)下方的路面结构层(22)进行微钻孔形成第一注浆孔(4),钻入路基层(16)深度达到3-5d,微钻孔间距3-5d,d为微钻孔直径;
58.3)提前准备专用树脂(例如环氧树脂),掺入适量触媒型硬化剂(例如阳离子起始剂),不需要精确配比的情况下,能够让树脂自身聚合组成高聚物材料,然后往第三开挖槽(3)的第一注浆孔(4)内下放注浆管,安装注射帽后,进行微钻孔高聚物注浆形成第一填充物(5);
59.4)在第二开挖槽(2)两侧下方的路面结构层(22)进行微钻孔形成第二注浆孔(6),深度钻至路面结构层(22)底部,微钻孔间距5-7d,d为微钻孔直径,若间距不够,至少形成两排钻孔;
60.5)制备好水泥浆,往第二开挖槽(2)的第二注浆孔(6)内下放注浆管并安装注射帽,然后进行微钻孔注浆形成第二填充物(7);
61.6)在第三开挖槽(3)底部铺设双层钢丝格栅(11),第二开挖槽(2)两侧底部铺设单层钢丝格栅(12),单层钢丝格栅(12)和双层钢丝格栅(11)做好搭接,单层钢丝格栅(12)另一侧利用向路面结构层(22)打设微锚杆(13)进行固定;
62.7)将车辙开挖区开挖后的路面碎块进行破碎加工,然后将粒径5.0~10.0mm的沥青混合料进行筛分出来,同时将粒径5.0~10.0mm的沥青混合料进行清理并收集备用
63.8)按照粒径1.0~5.0mm碎屑轮胎10%-20%、石灰石粉10%-15%、水泥浆15%-20%、早强剂1%-2%,其余为路面破碎颗粒中粒径5.0~10.0mm的沥青混合料的配比进行混合搅拌,形成浆状回填混合物;
64.9)将制备好的浆状回填混合物摊铺回填车辙开挖区,形成0.75h厚度的破碎路面回收再利用层(8),具有一定的可自密性;
65.10)待破碎路面回收再利用层(8)强度达到70%,进行表面拉毛,然后施工粘结层(15),紧接着在粘结层(15)上方施工铺填ms-2型微表处层(9),厚度为0.25h;
66.11)提前制作好加强段(14)构件,在第一开挖槽(1)和第二开挖槽(2)拐点处将一端的钢条(20)打设入路面结构层(22),另一端的钢条(20)打设入ms-2型微表处层(9);
67.12)将路面破碎颗粒中粒径5.0~10.0mm的沥青混合料,掺入适量石屑、乳化沥青、水和添加剂制备形成再生乳化沥青稀浆混合料,用于施工ms-3型微表处层;
68.13)安装好加强段(14)后,在ms-2型微表处层(9)上方施工铺填ms-3型微表处层(10),厚度为0.5h,最终完成超宽超深车辙微表处修补结构的施工。
69.本发明由于采用了上述技术方案,具有以下有益效果:
70.1、本发明通过微钻孔注浆和微钻孔高聚物注浆,提高了修补路面的承载力和抗车辙能力,增强了与原路面和路基的整体性,避免重复修补车辙而造成的浪费,提高运营效率,技术效益优势明显。
71.2、本发明中的破碎面回收再利用层,有效利用原有路面废旧料中粒径5.0~
10.0mm的沥青混合料,同时用石灰石粉替代天然细砂,所制得的浆状混合物性能好,能够大幅度降低微表处的成本,经济环保;此外,再利用层中添加适量的碎屑轮胎可有效缓冲和吸收路面的交通冲击荷载,能够延长超宽超深车辙微表处修补结构的使用寿命。
72.3、本发明通过设置ms-2微表处层过渡到ms-3微表处层,可提高微表处的抗飞散能力,同时显著降低路面噪声,另外设置的连接加强段,有效增强ms-2微表处层和ms-3微表处层的连接薄弱处,提高路面结构整体性和局部防水能力。
73.4、本发明设置的微锚杆和钢丝格栅,强度大、耐腐蚀,施工便捷,有效的分配载荷,可承受更大的变载荷,提高路面结构整体性和抗车辙能力。
74.5、本发明将原有路面废旧料中粒径5.0~10.0mm的沥青混合料用于ms-3微表处层沥青混合料的制备,充分利用路面废旧料中回收的沥青混合料,经济和环保效益明显。
75.以上仅为本发明的具体实施例,但本发明的技术特征并不局限于此。任何以本发明为基础,为解决基本相同的技术问题,实现基本相同的技术效果,所作出的简单变化、等同替换或者修饰等,皆涵盖于本发明的保护范围之中。
再多了解一些
本文用于企业家、创业者技术爱好者查询,结果仅供参考。