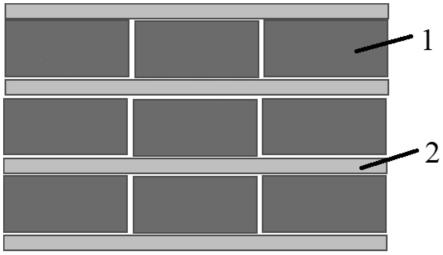
一种用于r-fe-b系稀土永磁材料的扩散源、其制备方法及其在晶界扩散方法中的应用
技术领域
1.本发明涉及稀土永磁材料制备技术领域,尤其涉及一种用于r-fe-b系稀土永磁材料的扩散源、其制备方法及其在晶界扩散方法中的应用。
背景技术:
2.稀土永磁材料磁性能出色,促进了永磁器件向小型化发展。为提高r-fe-b系稀土永磁材料的矫顽力和稳定性,常常需要添加cu、al、ga等元素优化微观结构,同时添加一定量的dy、tb、ho等重稀土元素。但主相晶粒中cu、al、ga等元素含量增加会造成剩磁的下降,并且重稀土元素较为稀缺,其价格高昂,重稀土元素用量成为衡量r-fe-b系稀土永磁材料性价比的重要指标。晶界扩散方法是采用沉积、涂敷等工艺,在加工成一定厚度的磁体表面设置含重稀土元素的合金或化合物作为扩散源,在高温热处理过程中,重稀土元素和cu、al、ga等元素沿晶界快速进入磁体内部,既满足了提高矫顽力和稳定性的要求,又大大减少了主相晶粒内部的添加元素的含量,并使得磁体的剩磁得以保持。因此,晶界扩散方法成为高性能r-fe-b系稀土永磁材料的核心制造工艺。
3.目前的晶界扩散方法采用pvd进行扩散源镀膜或者利用粉末喷涂或者印刷在磁体表面,前者的制造效率和靶材利用率低,设备成本高昂,后者为保证扩散源不易脱落,往往需要添加一定量的有机粘结剂,粘结剂中的碳原子在热处理过程中也会进入磁体,造成磁性能的劣化,而且由于喷涂等粉末堆积方法的致密度略高于松装密度,外层扩散源扩散到磁体内部需要先经过扩散源层,扩散效率和扩散源利用率大大降低。而利用重稀土金属或合金板材作为扩散源时,由于基材表面经过机械加工,难免有一定的油、水汽杂质等吸附,致密的板材影响了其挥发,温度升高以后与基材和扩散源反应形成杂质污染,造成品质劣化。
4.例如,在中国专利文献上公开的“稀土永磁体的晶界扩散方法”,其公告号为cn112908667a,包括:一级脉冲电流处理:将涂覆后的烧结钕铁硼毛坯磁体在真空条件上进行热处理的同时施加一定的脉冲电流,其中所述热处理的温度为500~800℃,所述脉冲电流的频率为400~1000hz,电流大小为500~2000a,作用时间4~15h;二级脉冲电流处理:将处理得到的烧结钕铁硼毛坯磁体置于真空条件下进行热处理的同时施加一定的脉冲电流,其中热处理的温度为25~400℃,脉冲电流的频率为10~200hz,电流大小为10~400a,作用时间0.5~4h;随即将涂覆后的烧结钕铁硼毛坯磁体冷却至100℃以下,且后者热处理温度不高于前者热处理温度。该方法对设备要求较高,其扩散源为将重稀土金属或者重稀土金属化合物与有机溶剂混合物,扩散源致密度低且引入了有机溶剂。
技术实现要素:
5.本发明为了克服现有技术下扩散效率和扩散源利用率低,且会引入一定杂质的问题,提供一种用于r-fe-b系稀土永磁材料的扩散源、其制备方法及其在晶界扩散方法中的
应用,使用该扩散源对r-fe-b系稀土永磁材料进行晶界扩散,可提高永磁材料的矫顽力和稳定性,并且保持了永磁材料的剩磁,引入杂质少同时避免永磁材料被污染。
6.为了实现上述目的,本发明采用以下技术方案:一种用于r-fe-b系稀土永磁材料的扩散源,所述扩散源包括重稀土金属元素以及辅助金属元素,重稀土金属元素为dy、tb和ho中的一种或几种,辅助金属元素为cu、al和ga中的一种或几种,辅助金属元素含量占总质量的1~10%,扩散源的孔隙率为30~50%。
7.在r-fe-b系稀土永磁材料中掺杂重稀土元素dy、tb、ho可提高r-fe-b系稀土永磁材料的矫顽力和稳定性,少量辅助金属元素cu、al和ga可优化r-fe-b系稀土永磁材料的微观结构,辅助金属元素还可提高扩散源晶界相的连续性并降低其熔点,进而提高重稀土元素沿晶界的扩散效率。在30~50%的孔隙率范围内,扩散源的扩散距离小,扩散效率高,并且该孔隙率范围保证在升温过程中覆盖在磁体表面的油气和水汽能在与扩散源反应前及时挥发并被真空系统抽走,减少磁体杂质污染导致的磁体性能下降。
8.一种用于r-fe-b系稀土永磁材料的扩散源的制备方法,包括如下步骤:1)将重稀土金属粉末或合金粉末与辅助金属粉末或合金粉末混合均匀;2)将混合好的粉末轧制为复合材料,复合材料即为扩散源。
9.采用粉末轧制得到扩散源易控制孔隙率,并保证了扩散源的致密度,降低了外层扩散源的扩散距离,提高了扩散效率,同时与将重稀土金属与cu、al、ga直接合金化的工艺相比,粉末轧制得到扩散源避免了熔炼铸造产生的成分偏析,提高扩散后磁体性能的一致性。
10.作为优选,所述重稀土金属粉末或合金粉末与辅助金属粉末或合金粉末的平均粒度均不大于0.1mm。
11.当粉末粒度较大时,扩散源中重稀土金属与辅助金属粉末分布不均匀,进而导致重稀土元素扩散不均匀,造成磁体的性能波动。
12.作为优选,所述制备步骤在惰性气体保护下进行。
13.扩散源的制备步骤在惰性气体保护下进行,避免重稀土金属及辅助金属氧化。
14.扩散源在r-fe-b系稀土永磁材料的晶界扩散方法的应用,包括如下步骤:a、将扩散源与磁体交替排列,在真空环境下将扩散源与磁体加热至扩散温度后保温一段时间再冷却至冷却温度;b、再在真空环境下将扩散源与磁体加热至回火温度,保温一段时间后冷却至室温。
15.将扩散源与磁体交替排列后进行晶界扩散,提高磁体的处理效率,高温热处理过程中,重稀土金属元素和辅助金属元素可沿晶界快速进入磁体内部。
16.作为优选,所述步骤a中扩散温度为850~1000℃,保温时间为8~10h。
17.扩散温度较低时,扩散速度慢,重稀土金属元素和辅助金属元素进入磁体的量较少;扩散温度较高时,重稀土金属元素和辅助金属元素进入磁体的量较多,对磁体剩磁的影响较大。
18.作为优选,冷却温度低于200℃。
19.作为优选,所述步骤b中回火温度为450~500℃,保温时间为2~4h。
20.作为优选,所述步骤a以及步骤b中的真空环境为气压不高于1
×
10-2
pa。
21.扩散时真空度不佳会导致扩散效果不佳,进而影响磁体性能。
22.因此,本发明具有如下有益效果:(1)扩散源中含有的少量辅助金属cu、al和ga可提高晶界相的连续性并降低其熔点,有利于提高重稀土元素沿晶界的扩散效率,同时cu和al的塑性好,ga的熔点接近室温,可作为粘结剂,提高扩散源的强度;(2)与重稀土金属与辅助金属直接合金化相比,常规粉末轧制方法得到的扩散源避免了熔炼铸造产生的成分偏析,提高扩散后产品性能的一致性,并且保证了扩散源的致密度,降低外层扩散源的扩散距离,进而提高扩散效率,并且使得扩散源有一定的孔隙率,保证在升温过程中覆盖在磁体表面的油气和水汽能在与基体反应前及时挥发并被真空系统抽走,避免永磁材料被污染;(3)本发明所述的晶界扩散方法提高了r-fe-b系稀土永磁材料的矫顽力和稳定性,并且保持了永磁材料的剩磁。
附图说明
23.图1是扩散源磁体排列的位置示意图,其中1-磁体,2-扩散源。
具体实施方式
24.下面结合附图与具体实施方法对本发明做进一步的描述。
25.实施例1~3一种r-fe-b系稀土永磁材料的晶界扩散方法,步骤如下:a、将n48h牌号磁体用线切割加工成30
×
35
×
5mm3的形状,酸洗出油然后烘干;b、将tb金属粉末与cu粉末在高速混料机里面混合30min,利用粉末轧制机轧成厚度为2mm的薄板,薄板即为扩散源,扩散源参数按如表1所示,扩散源的制备混料过程、轧制过程以及保持均在手套箱等氩气环境中进行;c、将扩散源与磁体如图1所示垂直交替排列摆放在烧结盒中,放入真空烧结炉进行扩散热处理,对烧结炉抽真空,真空度达到1
×
10-2
pa以后,开始加热,加热到900℃后保温10h后冷却至200℃以下,再加热到500℃保温3h后冷却至室温。
26.对比例1一种r-fe-b系稀土永磁材料的晶界扩散方法,步骤如下:a、将n48h牌号磁体用线切割加工成30
×
35
×
5mm3的形状,酸洗出油然后烘干;b、将tbcu合金铸锭线切割加工成厚度为2mm的薄片状合金片作为扩散源;c、将扩散源与磁体垂直交替排列摆放在烧结盒中,放入真空烧结炉进行扩散热处理,对烧结炉抽真空,真空度达到1
×
10-2
pa以后,开始加热,加热到900℃后保温10h后冷却至200℃以下,再加热到500℃保温3h后冷却至室温。
27.对比例2一种r-fe-b系稀土永磁材料的晶界扩散方法,步骤如下:a、将n48h牌号磁体用线切割加工成30
×
35
×
5mm3的形状,酸洗出油然后烘干;b、将tb金属粉末与cu粉末在高速混料机里面混合30min,利用粉末轧制机轧成厚度为2mm的薄板,薄板即为扩散源,扩散源参数按如表1所示,扩散源的制备混料过程、轧制过程以及保持均在手套箱等氩气环境中进行;c、将扩散源与磁体垂直交替排列摆放在烧结盒中,放入真空烧结炉进行扩散热处
理,开始加热,加热时开始对烧结炉抽真空,在温度升至200℃时使真空度达到1
×
10-2
pa,加热到900℃后保温10h后冷却至200℃以下,再加热到500℃保温3h后冷却至室温。
28.对比例3~4一种r-fe-b系稀土永磁材料的晶界扩散方法,步骤如下:a、将n48h牌号磁体用线切割加工成30
×
35
×
5mm3的形状,酸洗出油然后烘干;b、将tb金属粉末与cu粉末按如表1所示的配比在高速混料机里面混合30min,利用粉末轧制机轧成厚度为2mm的薄板,薄板即为扩散源,扩散源的制备混料过程、轧制过程以及保持均在手套箱等氩气环境中进行;c、将扩散源与磁体垂直交替排列摆放在烧结盒中,放入真空烧结炉进行扩散热处理,对烧结炉抽真空,真空度达到1
×
10-2
pa以后,开始加热,加热到900℃保温10h后冷却至200℃以下,再加热到500℃保温3h后冷却至室温。
29.表1.实施例1~3以及对比例1~4的扩散源参数。
30.上述实施例及对比例所得磁体冷却后,分别检测在未经晶界扩散处理的基体与上述实施例及对比例所得磁体的磁性能和杂质含量,检测步骤如下:利用电火花线磁体的30
×
35mm2面内对角线方向切割出3个ф10
×
5mm的圆柱,在nim6200磁性能测量仪上测量圆柱的最终磁性能,并取平均值和标准差;利用线切割在磁体表层切下1.5mm厚度磁体,利用砂纸打磨减薄0.5mm,从而实现利用氧碳分析仪测试磁体最靠近表面1mm厚度的氧和碳杂质含量,检测结果如表2所示。
31.表2.实施例1~3以及对比例1~4的检测结果。
项目剩磁br/kgs标准差矫顽力hcj/koe标准差氧含量/ppm碳含量/ppm基体14.00\18.5\521475实施例113.920.0130.30.2580468实施例213.930.0130.50.3536496实施例313.850.0229.80.3562512对比例113.900.0528.10.5867751对比例213.880.1128.31.5921713对比例313.910.0329.80.6543485对比例413.870.1127.12.2514493
32.由表2可知,本发明所述的晶界扩散方法提高了磁体的矫顽力,并且对剩磁影响较小,引入氧和碳杂质较少。对比例1使用的扩散源为金属致密板,在扩散时磁体表面的油气和水汽不能及时挥发,导致磁体表面氧含量和碳含量偏高,进而使磁性能下降,并且金属致
密板中成分分布不均匀,对比例1的得到的磁体性能波动大于实施例1~3;对比例2加热时才开始抽真空,导致烧结盒中真空度不够,磁体表面氧含量和碳含量也偏高,扩散后磁体的磁性能下降;对比例3以及对比例4的粉末粒度较大,tb和cu的不均匀性不能通过元素表面扩散克服,导致重稀土元素扩散不均匀,而矫顽力一般与磁体局部矫顽力最低值一致,因此造成了对比例3和对比例4制备的磁体的性能波动高于r-fe-b系稀土永磁材料常规产品控制要求。
33.实施例4~8一种r-fe-b系稀土永磁材料的晶界扩散方法,步骤如下:a、将n50m牌号磁体用线切割加工成40
×
30
×
4mm3的形状,酸洗出油然后烘干;b、将dy金属粉末与al粉末在高速混料机里面混合30min,利用粉末轧制机轧成厚度为1mm的薄板,薄板即为扩散源,扩散源参数按如表3所示,扩散源的制备混料过程、轧制过程以及保持均在手套箱等氩气环境中进行;c、将扩散源与磁体垂直交替排列摆放在烧结盒中,放入真空烧结炉进行扩散热处理,对烧结炉抽真空,真空度达到1
×
10-2
pa以后,开始加热,加热到如表2所示的扩散温度后保温8h后冷却至200℃以下,再加热到485℃保温3h后冷却至室温。
34.对比例5~7一种r-fe-b系稀土永磁材料的晶界扩散方法,步骤如下:a、将n50m牌号磁体用线切割加工成40
×
30
×
4mm3的形状,酸洗出油然后烘干;b、将dy金属粉末与al粉末在高速混料机里面混合30min,利用粉末轧制机轧成厚度为1mm的薄板,薄板即为扩散源,扩散源参数按如表3所示,扩散源的制备混料过程、轧制过程以及保持均在手套箱等氩气环境中进行;c、将扩散源与磁体垂直交替排列摆放在烧结盒中,放入真空烧结炉进行扩散热处理,对烧结炉抽真空,真空度达到1
×
10-2
pa以后,开始加热,加热到如表2所示的扩散温度后保温8h后冷却至200℃以下,再加热到485℃保温3h后冷却至室温。
35.表3.实施例4~8以及对比例5~7的扩散源参数及扩散温度。
36.上述实施例及对比例所得磁体冷却后,检查磁体是否有粘片现象,即磁体与扩散源黏在一起或磁体表面粘有扩散源。分别检测在未经晶界扩散处理的基体与上述实施例及对比例所得磁体的磁性能和杂质含量,检测步骤如下:利用电火花线磁体的40
×
30mm2面内对角线方向切割出3个ф10
×
5mm的圆柱,在nim6200磁性能测量仪上测量圆柱的最终磁性能,检测结果如表4所示。
37.表4.实施例4~8以及对比例5~7的检测结果。项目剩磁br/kgs标准差矫顽力hcj/koe标准差粘片比例/%基体14.20\15.3\\实施例414.110.0222.80.10.00实施例514.080.0323.10.20.02实施例614.020.0223.50.30.05实施例714.130.0223.20.20.00实施例814.050.0322.90.30.06对比例513.810.1324.21.70.08对比例614.140.1523.41.10.01对比例713.760.3121.52.24.20
38.从表4可以看出,实施例4~6的扩散温度依次升高,而剩磁逐渐下降,扩散温度升高时,al和dy进入磁体内部的量增加,造成剩磁下降;由对比例5可知,相较于实施例6剩磁的下降幅度,当扩散温度超过1000℃时,剩磁下降幅度迅速增加。由对比例6和对比例7可知,当辅助金属al含量过少时,扩散源强度过低,容易碎裂,影响性能一致性;当辅助金属al的添加比例过高时,高温下al液相过多,渗入到基体和扩散源之间,容易粘片影响收率,同时大量的al进入磁体造成剩磁下降。
39.实施例9~10a、将n45sh牌号磁体用线切割加工成30
×
25
×
2.5mm3的形状,酸洗出油然后烘干;b、将ho金属粉末与ga粉末在高速混料机里面混合30min,利用粉末轧制机轧成厚度为1mm的薄板,薄板即为扩散源,扩散源参数按如表5所示,扩散源的制备混料过程、轧制过程以及保持均在手套箱等氩气环境中进行;c、将扩散源与磁体垂直交替排列摆放在烧结盒中,放入真空烧结炉进行扩散热处理,对烧结炉抽真空,真空度达到1
×
10-2
pa以后,开始加热,加热到950℃后保温8h后冷却至200℃以下,再加热到485℃保温3h后冷却至室温。
40.对比例8~9a、将n45sh牌号磁体用线切割加工成30
×
25
×
2.5mm3的形状,酸洗出油然后烘干;b、将ho金属粉末与ga粉末在高速混料机里面混合30min,利用粉末轧制机轧成厚度为1mm的薄板,薄板即为扩散源,扩散源参数按如表5所示,扩散源的制备混料过程、轧制过程以及保持均在手套箱等氩气环境中进行;c、将扩散源与磁体垂直交替排列摆放在烧结盒中,放入真空烧结炉进行扩散热处理,对烧结炉抽真空,真空度达到1
×
10-2
pa以后,开始加热,加热到950℃后保温8h后冷却至200℃以下,再加热到485℃保温3h后冷却至室温。
41.表5.实施例9~10以及对比例8~9的扩散源参数。
42.分别检测在未经晶界扩散处理的基体与上述实施例及对比例所得磁体的磁性能和杂质含量,检测步骤如下:利用电火花线磁体的30
×
25mm2面内对角线方向切割出2个ф10
×
5mm的圆柱,在nim6200磁性能测量仪上测量圆柱的最终磁性能,检测结果如表6所示。
43.表6.实施例9~10以及对比例8~9的检测结果。
44.对比例8使用了60%孔隙率的扩散源,表层扩散源扩散距离过长,导致利用率偏低,矫顽力增加量显著下降;因为常规粉末松装孔隙率为73,过高的孔隙率难以将粉末通过轧制方式制成复合材料,如对比例9,其孔隙率为70%,在扩散过程中难以维持其复合状态,导致碎裂进而无法完成扩散。
再多了解一些
本文用于企业家、创业者技术爱好者查询,结果仅供参考。