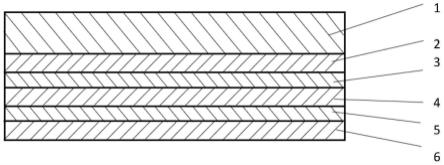
1.本发明属于锂离子电池用外包装材料及锂离子电池的制备技术领域,具体涉及一种耐电解液铝塑膜、制备方法及其锂离子电池。
背景技术:
2.锂离子电池其结构包括:由正极集电材料/正极活性物质层/隔膜/电解液层/负极活性物质层/负极集电材料构成的电池主体,以及包装所述电池主体的外包装材料-锂离子电池用外包装材料。锂离子电池用外包装材料是由包括耐热性树脂膜的外层、铝箔及包括热塑性树脂膜的内层层叠而形成的,其中铝箔和内外层膜通过粘接剂粘合。与作为电池要素的容器使用的以往的金属制罐不同,在重量轻、放热性高、形状自由度高等方面性能优异。
3.锂离子电池用外包装材料长期处在以下环境中:热塑性树脂内层直接与电解液接触。锂离子电池用外包装材料实际使用过程中主要存在以下问题:
①
电解液中的六氟磷酸锂高温下与水反应生成氢氟酸,氢氟酸渗透进热塑性材料,氢氟酸腐蚀粘接剂,导致铝箔和热塑性树脂剥离力降低,严重时会产生分层。
4.现有技术解决上述问题是通过提高材料抗氢氟酸的能力,但氢氟酸具有的强腐蚀性,因此,这一问题难以得到有效抑制,况且,外包装膜提高抗腐蚀性能的提升显著提高生产成本。
5.本发明要解决的是现有电池封装用铝塑膜在长期使用过程中高温长期浸泡电解液产生铝箔同热塑性树脂剥离强度降低的问题。
技术实现要素:
6.本发明的目的在于克服现有技术的不足之处,提供了一种耐电解液铝塑膜、制备方法及其锂离子电池,解决了锂离子电池用外包装材料在长期使用过程中由于氢氟酸腐蚀导致的热塑性树脂和铝箔之间剥离强度降低的问题。
7.本发明解决其技术问题所采用的技术方案之一是:提供了一种耐电解液铝塑膜,包括耐热树脂层、铝箔层、热塑性树脂层和中和反应层;所述耐热树脂层、铝箔层、热塑性树脂层依次层叠设置,所述中和反应层设置于热塑性树脂层内部或热塑性树脂层远离铝箔层一侧的表面,且厚度为10~40μm;所述中和反应层由胺基化合物和热塑性树脂组成,所述胺基化合物的质量百分比为0.1~2.5wt%。
8.在本发明一较佳实施例中,所述胺基化合物包括4,4
′‑
二胺基二苯醚、吡咯烷、三乙醇胺、三乙烯二胺和邻苯二甲酰亚胺。
9.在本发明一较佳实施例中,所述耐热树脂层为拉伸聚酯或尼龙膜,厚度为20-100μm,且熔点高于所述热塑性树脂层,在实施热封时不会对外层耐热性树脂膜产生不良影响。
10.锂离子电池用外包装材料的外层为含有1层或2层以上的耐热性树脂膜,当外层由2层以上的耐热性树脂膜构成时,优选使用2层以上的耐热性树脂膜之间通过粘接剂而叠
层。作为耐热性树脂膜的外层,可以使用拉伸聚酯或尼龙膜,作为聚酯树脂可以列举,聚对苯二甲酸乙二醇酯、聚对苯二甲酸丁二醇酯、聚萘二甲酸乙二醇酯、聚萘二甲酸丁二醇酯、共聚聚酯、聚碳酸酯等,作为尼龙,可以列举出聚酰胺树脂,即尼龙6、尼龙66、尼龙6和尼龙66的共聚物、尼龙6,10、聚间二甲苯己二酰二胺等。上述耐热性树脂层可进行易粘接处理,如等离子体处理、臭氧处理、电晕放电处理及底涂处理等。
11.在本发明一较佳实施例中,所述耐热树脂层与铝箔层间通过厚度为1-10μm的干式层合用粘接剂层连接。
12.粘接剂层是为了使尼龙基材外层与铝箔层牢固地粘接而根据需要设置于它们之间的层。用于形成粘接剂层的粘接剂可以为双液固化型粘接剂,也可以为单液固化型粘接剂。另外,对于用于形成粘接剂层的粘接剂的粘接机理,也没有特别限制,化学反应型、溶剂挥发型、热熔融型、热压型等的任意类型均可。具体可以列举:聚对苯二甲酸乙二醇酯、聚对苯二甲酸丁二醇酯、聚萘二甲酸乙二醇酯、聚萘二甲酸丁二醇酯、聚间苯二甲酸乙二醇酯、共聚聚酯等的聚酯系树脂;聚醚系粘接剂;聚氨酯系粘接剂;环氧系树脂;酚醛系树脂;尼龙6、尼龙66、尼龙12、共聚聚酰胺等的聚酰胺系树脂;聚烯烃、羧酸改性聚烯烃、金属改性聚烯烃等的聚烯烃系树脂、聚乙酸乙烯酯系树脂;纤维素系粘接剂;(甲基)丙烯酸系树脂;聚酰亚胺系树脂;聚碳酸酯;尿素树脂、三聚氰胺树脂等的氨基树脂;氯丁二烯橡胶、丁腈橡胶、苯乙烯-丁二烯橡胶等的橡胶;有机硅系树脂等。这些粘接成分可以单独使用1种,也可以将2种以上组合使用。在这些粘接成分中,优选列举聚氨酯系粘接剂。
13.在本发明一较佳实施例中,所述铝箔层采用厚度为10-80μm的软质铝箔。
14.铝箔层除了提高铝塑膜的强度以外、还具有防止水蒸气、氧、光等侵入电池内部的功能。从防止在铝箔层产生褶皱或针孔的观点考虑,优选由经退火处理的如jis h4160:1994a8021h-o、jis h4160:1994a8079h-o、jis h4000:2014a8021p-o和jis h4000:2014a8079p-o等软质铝合金箔。铝箔层的厚度足以能够发挥作为水蒸气等的阻隔层的功能外,为了保证冲压过程中铝箔的完整性,综合电池用铝塑膜的薄膜化、轻质化的观点,作为上限,可以列举约120μm以下、优选约100μm以下、更优选约80μm以下、更加优选约50μm以下,作为下限,可以列举优选约20μm以上,作为该厚度的范围,能够设为20-120μm、20-100μm、优选20-80μm、20-50μm。
15.在本发明一较佳实施例中,所述铝箔层的内侧表面为化学处理层。
16.化学处理层是为了提升铝箔层内层与其他层之间的粘接力,同时防止电池长时间使用后电解液的腐蚀导致粘接力下降。化学处理层由磷酸盐、铬酸盐以及水溶性树脂按照质量比4:1:95组成。水溶性树脂是丙烯酸类树脂或酚醛类树脂或磺酸基类树脂中的一种或多种。
17.在本发明一较佳实施例中,所述热塑性树脂层为聚丙烯、马来酸改性聚丙烯、乙烯-丙烯酸酯共聚物或离聚物树脂的未拉伸膜。
18.热塑性树脂层的作用是使得针对电池中使用的腐蚀性强的电解液等具备优异的耐化学药品性,并且赋予铝塑膜热封性。热塑性树脂层的厚度,从使电池用铝塑膜薄型化、并且发挥优异的成型性的观点出发,作为上限,优选列举约80μm以下,能够减少树脂使用量,可实现成本的降低,作为下限,优选列举约10μm以上,能够充分防止针孔的产生,因此优选列举为10μm-80μm左右,更优选为10-40μm左右。
19.本发明解决其技术问题所采用的技术方案之二是:提供了上述耐电解液铝塑膜的制备方法,包括如下步骤:
20.铝箔处理:包括内表面的化学处理;
21.复合热塑性树脂层:采用热法流延机高温将热塑性树脂和处理后的铝箔内表面复合或者采用干法利用胶粘剂将热塑性树脂与铝箔内表面复合;
22.复合中和反应层:将胺基化合物与热塑性树脂基材搅拌均匀,投入挤出机,流延在已经复合在铝箔上的热塑性树脂表面;
23.复合耐热树脂层:将至少一层耐热树脂利用粘接剂复合于铝箔的外表面;
24.后处理:于60-120℃下老化加热3-4天,得到耐电解液所述铝塑膜。
25.在本发明一较佳实施例中,所述步骤(1)铝箔经退火处理后,外表面经过碱洗除油、水洗、酸洗中和和水洗,最后利用涂布机在铝箔的内表面涂布化学处理液,涂布时间为2-60s,得到内表面带有化学处理层的铝箔;所述化学处理层由磷酸盐、铬酸盐以及水溶性树脂按照质量比4:1:95组成。
26.本发明解决其技术问题所采用的技术方案之三是:提供了一种锂离子电池,外包装采用上述一种耐电解液铝塑膜,且中和反应层与电解液直接接触。
27.在使用上述耐电解液铝塑膜收纳电池元件时,以热塑性树脂部分成为内侧,将至少具有正极、负极和电解质的电池元件在与上述正极和负极各自连接的金属端子向外侧突出的状态下、以能够在电池元件的边缘形成凸缘部(热塑性树脂彼此相接触的区域)的方式进行覆盖,将上述凸缘部的热塑性树脂层彼此热封来进行密封,由此能够提供使用了的电池用铝塑膜的电池。
28.本技术方案与背景技术相比,它具有如下优点:
29.1.本发明设置中和反应层,通过添加胺基类化合物,利用胺基的碱性中和电解液中的六氟磷酸锂在高温条件下分解产生的氢氟酸,抑制氢氟酸对铝塑膜的腐蚀,从而提升铝塑膜整体高温耐电解液的效果;
30.2.本发明通过控制胺基类化合物的添加量,既保证了中和效果,又避免添加过度导致热塑性树脂链断裂、降解,影响热封强度;
31.3.本发明通过控制各层间厚度,既保证了铝塑膜作为锂离子电池外包装包括热封性在内的性能要求,又最大程度节约成本。
附图说明
32.图1为实施例1中铝塑膜的层结构图。
33.图2为不同胺基化合物添加量对耐电解液剥离强度的影响。
34.其中,1-耐热树脂层、2-粘接剂层、3-铝箔层、4-化学处理层、5-热塑性树脂层、6-中和反应层。
具体实施方式
35.实施例1
36.本实施例一种耐电解液铝塑膜,制备方式如下:
37.(1)采用40μm铝箔层经过碱洗除油、水洗、酸洗中和、水洗,得到干净的铝箔层(3);
然后在铝箔层(3)内表面辊涂处理液,经过75℃高温固化,从而得到化学处理涂层(4);
38.(2)接着将粘接剂均匀的涂在铝箔层外表面,形成粘接剂层(2),控制粘接剂的用量,使粘接剂层(2)厚度为4μm;
39.(3)然后将厚度为25μm的尼龙层(1)(耐热性树脂)复合至铝箔层的外表面;
40.(4)再将厚度为40μm的pp层(热塑性树脂)热压复合于已涂布化学处理层铝箔层的内表面,形成热塑性树脂层(5);
41.(5)按质量比为1:49的比例将4,4
′‑
二胺基二苯醚与pp基材混合均匀后放入挤出机,在已经复合在铝箔内表面的热塑性树脂外表面流延成胺基化合物和树脂共挤出层(中和反应层6),控制厚度为40μm,最终得到耐电解液铝塑膜;
42.(6)将其于75℃下老化加热4天,即得到图1所示结构的铝塑复合材料,耐热树脂层(1、)铝箔层(3)、热塑性树脂层(4)依次层叠设置,所述耐热树脂层(1)通过粘接剂(2)与铝箔层(3)复合,所述中和反应层(5)设置于热塑性树脂层(4)接触电解液一侧的表面。
43.将本实施例制备的耐电解液铝塑膜作为外包装进行电池封装,得到封装后的锂离子电池。
44.实施例2
45.实施例2与实施例1的区别在于:
46.(1)采用40μm铝箔层经过碱洗除油、水洗、酸洗中和、水洗,得到干净的铝箔层(3);然后在铝箔层内表面辊涂处理液,经过75℃高温固化,从而得到化学处理层(4);
47.(2)接着将粘接剂均匀的涂在铝箔层外表面,形成粘接剂层(2),控制粘接剂的用量,使粘接剂层厚度为4μm;
48.(3)然后将厚度为25μm的尼龙层(1)(耐热性树脂)复合至铝箔层的外表面;
49.(4)再将厚度为40μm的pp层(热塑性树脂)复合于已涂布化学处理层铝箔层的内表面,形成热塑性树脂层(5);
50.(5)按质量比为1.5:48.5的比例将4,4
′‑
二胺基二苯醚与pp基材混合均匀后放入挤出机,在已经复合在铝箔内表面的热塑性树脂外表面流延成胺基化合物和树脂共挤出层(中和反应层6),控制厚度为40μm;
51.(6)将步骤(5)产物于75℃下老化加热4天,即得到可用于电池外包装的耐电解液铝塑膜。
52.实施例3
53.(1)采用40μm铝箔层经过碱洗除油、水洗、酸洗中和、水洗,得到干净的铝箔层(3);然后在铝箔层内表面辊涂处理液,经过75℃高温固化,从而得到化学处理层(4);
54.(2)接着将粘接剂均匀的涂在铝箔层外表面,形成粘接剂层(2),控制粘接剂的用量,使粘接剂层厚度为4μm;
55.(3)然后将厚度为25μm的尼龙层(1)(耐热性树脂)复合至铝箔层的外表面;
56.(4)再将厚度为60μm的pp层(热塑性树脂)复合于已涂布化学处理层铝箔层的内表面,形成热塑性树脂层(5);
57.(5)按质量比为1:49的比例将4,4
′‑
二胺基二苯醚与pp基材混合均匀后放入挤出机,在已经复合在铝箔内表面的热塑性树脂外表面流延成胺基化合物和树脂共挤出层(中和反应层6),控制厚度为20μm;
58.(6)将步骤(5)产物于75℃下老化加热4天。
59.实施例4
60.(1)采用40μm铝箔层经过碱洗除油、水洗、酸洗中和、水洗,得到干净的铝箔层(3);然后在铝箔层内表面辊涂处理液,经过75℃高温固化,从而得到化学处理层(4);
61.(2)接着将粘接剂均匀的涂在铝箔层外表面,形成粘接剂层(2),控制粘接剂的用量,使粘接剂层厚度为4μm;
62.(3)然后将厚度为25μm的尼龙层(1)(耐热性树脂)复合至铝箔层的外表面;
63.(4)再将厚度为60μm的pp层(热塑性树脂)复合于已涂布化学处理层铝箔层的内表面,形成热塑性树脂层(5);
64.(5)按质量比为1.5:48.5的比例将4,4
′‑
二胺基二苯醚与pp基材混合均匀后放入挤出机,在已经复合在铝箔内表面的热塑性树脂外表面流延成胺基化合物和树脂共挤出层(中和反应层6),控制厚度为20μm;
65.(6)将步骤(5)产物于75℃下老化加热4天。
66.实施例5
67.(1)采用40μm铝箔层经过碱洗除油、水洗、酸洗中和、水洗,得到干净的铝箔层(3);然后在铝箔层内表面辊涂处理液,经过75℃高温固化,从而得到化学处理层(4);
68.(2)接着将粘接剂均匀的涂在铝箔层外表面,形成粘接剂层(2),控制粘接剂的用量,使粘接剂层厚度为4μm;
69.(3)然后将厚度为25μm的尼龙层(1)(耐热性树脂)复合至铝箔层的外表面;
70.(4)再将厚度为60μm的pp层(热塑性树脂)复合于已涂布化学处理层铝箔层的内表面,形成热塑性树脂层(5);
71.(5)按质量比为1.5:48.5的比例将吡咯烷与pp基材混合均匀后放入挤出机,在已经复合在铝箔内表面的热塑性树脂外表面流延成胺基化合物和树脂共挤出层(中和反应层6),控制厚度为20μm;
72.(6)将步骤(5)产物于75℃下老化加热4天。
73.实施例6
74.(1)采用40μm铝箔层经过碱洗除油、水洗、酸洗中和、水洗,得到干净的铝箔层(3);然后在铝箔层内表面辊涂处理液,经过75℃高温固化,从而得到化学处理层(4);
75.(2)接着将粘接剂均匀的涂在铝箔层外表面,形成粘接剂层(2),控制粘接剂的用量,使粘接剂层厚度为4μm;
76.(3)然后将厚度为25μm的尼龙层(1)(耐热性树脂)复合至铝箔层的外表面;
77.(4)再将厚度为60μm的pp层(热塑性树脂)复合于已涂布化学处理层铝箔层的内表面,形成热塑性树脂层(5);
78.(5)按质量比为1:49的比例将吡咯烷与pp基材混合均匀后放入挤出机,在已经复合在铝箔内表面的热塑性树脂外表面流延成胺基化合物和树脂共挤出层(中和反应层6),控制厚度为20μm;
79.(6)将步骤(5)产物于75℃下老化加热4天。
80.实施例7
81.(1)采用40μm铝箔层经过碱洗除油、水洗、酸洗中和、水洗,得到干净的铝箔层(3);
然后在铝箔层内表面辊涂处理液,经过75℃高温固化,从而得到化学处理层(4);
82.(2)接着将粘接剂均匀的涂在铝箔层外表面,形成粘接剂层(2),控制粘接剂的用量,使粘接剂层厚度为4μm;
83.(3)然后将厚度为25μm的尼龙层((1)耐热性树脂)复合至铝箔层的外表面;
84.(4)再将厚度为60μm的pp层(热塑性树脂)复合于已涂布化学处理层铝箔层的内表面,形成热塑性树脂层(5);
85.(5)按质量比为1.5:48.5的比例将三乙烯二胺与pp基材混合均匀后放入挤出机,在已经复合在铝箔内表面的热塑性树脂外表面流延成胺基化合物和树脂共挤出层(中和反应层6),控制厚度为20μm;
86.(6)将步骤(5)产物于75℃下老化加热4天。
87.实施例8
88.(1)采用40μm铝箔层经过碱洗除油、水洗、酸洗中和、水洗,得到干净的铝箔层(3);然后在铝箔层内表面辊涂处理液,经过75℃高温固化,从而得到化学处理层(4);
89.(2)接着将粘接剂均匀的涂在铝箔层外表面,形成粘接剂层(2),控制粘接剂的用量,使粘接剂层厚度为4μm;
90.(3)然后将厚度为25μm的尼龙层(1)(耐热性树脂)复合至铝箔层的外表面;
91.(4)再将厚度为60μm的pp层(热塑性树脂)复合于已涂布化学处理层铝箔层的内表面,形成热塑性树脂层(5);
92.(5)按质量比为1:49的比例将三乙烯二胺与pp基材混合均匀后放入挤出机,在已经复合在铝箔内表面的热塑性树脂外表面流延成胺基化合物和树脂共挤出层(中和反应层6),控制厚度为20μm;
93.(6)将步骤(5)产物于75℃下老化加热4天。
94.实施例9
95.实施例9与实施例1的区别在于:
96.(1)采用40μm铝箔层经过碱洗除油、水洗、酸洗中和、水洗,得到干净的铝箔层(3);然后在铝箔层内表面辊涂处理液,经过75℃高温固化,从而得到化学处理涂层(4);
97.(2)接着将粘接剂均匀的涂在铝箔层外表面,形成粘接剂层(2),控制粘接剂的用量,使粘接剂层厚度为4μm;
98.(3)然后将厚度为25μm的尼龙层(1)(耐热性树脂)复合至铝箔层的外表面;
99.(4)再将厚度为40μm的pp层(热塑性树脂)热压复合于已涂布化学处理层铝箔层的内表面,形成热塑性树脂层(5);
100.(5)按质量比为1:49的比例将4,4
′‑
二胺基二苯醚与pp基材混合均匀后放入挤出机,在已经复合在铝箔内表面的热塑性树脂外表面流延成胺基化合物和树脂共挤出层(中和反应层6),控制厚度为40μm;
101.(6)将其于75℃下老化加热4天,即得到图1所示结构的铝塑复合材料,耐热树脂层、铝箔层、热塑性树脂层依次层叠设置,所述中和反应层设置于热塑性树脂层的外侧。
102.一、耐电解液剥离强度实验
103.按照标准要求,将实施例1~8制成的铝塑膜裁剪一条长100mm、宽15mm的长条于瓶中,注入商用电解液中淹没长条,密封后放入温度为85℃的烘箱中,24h后取出,用清水冲去
残留的电解液,擦干后利用万能拉力机测得耐电解液剥离强度,结果如图2。可见,实施例中中和反应层的胺基化合物和树脂,质量比为1~1.5:48.5~49的比例时具备优异的耐电解液剥离强度。
104.以上实施例仅用以说明本发明的技术方案,而非对其限制;尽管参照前述各实施例对本发明进行了详细的说明,本领域的普通技术人员应当理解:其依然可以对前述各实施例所记载的技术方案进行修改,或者对其中部分或者全部技术特征进行等同替换;而这些修改或者替换,并不使相应技术方案的本质脱离本发明各实施例确定的保护方案的范围。
再多了解一些
本文用于企业家、创业者技术爱好者查询,结果仅供参考。