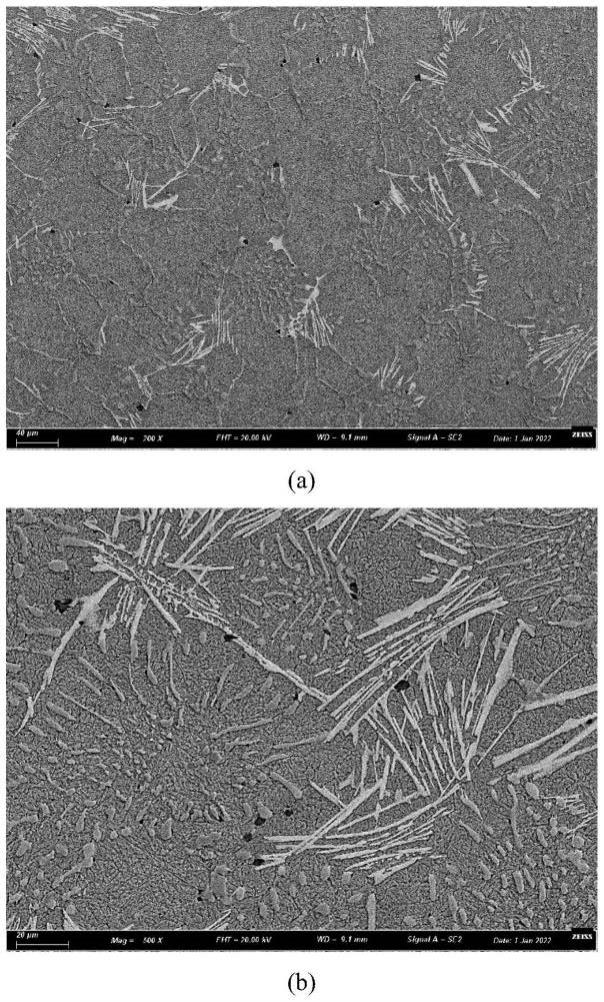
1.本发明为一种高速钢及其热处理方法,特别涉及一种耐磨高速钢及其热处理方法,属于耐磨材料技术领域。
背景技术:
2.钢铁型材的制造,主要依赖于冷轧与热轧工艺。轧辊是轧钢机的重要组成部件,轧辊的质量和性能直接影响了轧机的生产效率、带钢质量以及生产制造成本。由于长期承受高负荷、交变应力、持续摩擦和高温环境,热轧辊必须具备高硬度、优良的耐磨性和热稳定性。此外,为了应对冲击和振动,轧辊还需要具备一定的强度和韧性,以免造成断辊。近30多年来,使用高速钢作为轧辊材料取得了良好的成效。据报道,在20世纪80年代,我国生产每吨钢材所消耗的轧辊非常多,平均消耗量超过3.0kg/t钢,而随着高速钢轧辊技术的发展,目前我国生产每吨钢材所消耗的轧辊约为0.9kg/t钢材左右。
3.高速钢的优良耐磨性和红硬性与其组织构成密切相关。高速钢的金相组织主要是马氏体基体和共晶碳化物构成。高速钢中含有较多的碳和其他金属元素。这些元素中的一部分用来形成硬质合金碳化物,它们分布在组织中,增加高速钢的耐磨性;另一部分则固溶到马氏体中,造成晶格畸变,尤其是碳原子的间隙固溶强化作用,使马氏体的强度和硬度获得极大提升。此外,高速钢还具有二次硬化效应:在高温淬火时,一些合金元素(尤其是w、mo)溶入基体,随后在550℃左右回火时,马氏体中析出细小的二次碳化物mc与m2c,使钢的硬度变得更高。这使高速钢在600℃左右也有较好的硬度保持能力。因此,高速钢的优良性能得益于以下强化机制:固溶强化、第二相强化和弥散强化。然而,随着材料技术的发展,钢铁材料强度不断上升,变形量不断增大,轧辊的硬度与耐磨性仍有待提升。
4.为了进一步提高高速钢轧辊的耐磨性,中国发明专利cn202011606779.3公开了一种耐用型高速钢轧辊及其制造方法。该钢的化学成分及重量百分比为:1.50-2.50%c,0.90~1.50%si,0.40~1.40%mn,9.00~14.00%cr,0.50~2.00%ni,7.00~12.00%mo,1.00-3.00%v,0.50-2.50%w,≤1.0%nb,≤0.03%p;≤0.03%s,其余为fe和不可避免的杂质。热处理工艺为:将铸件开箱后进行去应力退火,退火温度500℃~900℃,保温时间50~80h,保温结束后随炉冷却;然后机械加工需要的尺寸及精度;采用差温淬火方法对轧辊表面进行热处理,淬火温度1000℃~1200℃,淬火保温时间2~10h,采用喷雾或者吹风冷却方式冷却;回火温度450℃~550℃,回火时间共计120~170h。该高速钢组织为马氏体基体 碳化物,基体显微硬度580-670hv,辊身硬度达到了76-85hsd,耐磨性较好,但由于高速钢轧辊的高温红硬性差,高速钢在高温下硬度保持性不佳,轧辊高温耐磨性较差。
5.中国发明专利cn1631565公开了一种高钒高速钢复合轧辊及生产工艺,轧辊分为辊芯和轧辊耐磨层,辊芯采用韧性较好的低合金钢或中碳钢材料制作,轧辊耐磨层采用高钒高速钢材料,该高钒高速钢的主要元素含量为:c:1.8-3.5%、v:7-12%、cr:4-5%、mo:2-4%、ni:0.5-1.5%,余量为铁。其生产工艺为:辊芯与轧辊耐磨层通过感应加热顺序凝固结晶方法复合熔铸为一体。该发明轧辊的钒含量太高,易出现低硬度的m3c型碳化物,降低高
1.3%al,0.9-1.3%nb,《1.0%si,《0.6%mn,《0.03%s,《0.03%p,其余为fe及不可避免的杂质元素。
10.本发明耐磨高速钢用感应电炉熔炼,其制造工艺步骤是:先在感应电炉中加入高速钢废料、废钢、生铁、钼铁、钨铁、铌铁、金属钴、镍板,钢水熔清后加入铬铁,出炉前加入钒铁和硼铁,然后用铝对钢液脱氧和合金化,钢水炉前分析合格后出炉,钢水出炉温度1590~1615℃。将钢水浇铸到卧式离心铸造机中,铸造完成后空气冷却至室温,获得高速钢毛坯;为了高速钢毛坯降低硬度,改善加工性能,将高速钢毛坯经过950℃保温6h,进行炉冷退火,然后进行粗加工;粗加工后的高速钢在1050-1075℃奥氏体化60-120分钟,然后空冷至室温;最后,在500-530℃回火保温6-8h,炉冷至室温,精加工后获得耐磨性和红硬性好的耐磨高速钢。
11.本发明耐磨高速钢中,含有体积分数3.2-3.7%的显微硬度超过4000hv的(cr
0.5v0.5
)b相,(cr
0.5v0.5
)b相的显微硬度,显著高于钨、钼、铬、钒、铌元素形成的碳化物的显微硬度,具有优异的抗磨性能。
12.高速钢的成分首先影响了金相组织中相的种类与组成,进而影响材料的硬度与耐磨性。本发明耐磨高速钢确定的化学成分如下:
13.v:钒是强碳化物形成元素,常与c结合形成vc,高硬度的vc有利于提高高速钢耐磨性。此外,mc碳化物常常在晶界处分布,它阻碍晶界迁移,抑制晶粒生长,进而达到强化材料的效果。但vc数量太多会增大摩擦系数和轧制负荷,增加轧钢能耗,影响带钢表面质量。因此,高速钢中v含量确定为4.1-4.3%。
14.w:钨元素是保证高速钢红硬性的关键。在高速钢的凝固组织中,钨元素通常以m6c共晶碳化物的形式存在。在较高奥氏体化温度下,部分m6c溶入奥氏体,然后回火时析出细小弥散的w2c二次碳化物,实现高速钢的二次硬化。钨的加入会使钢具有抗氧化性,避免高速钢在加热过程中的脱碳现象。但是,由于钨的相对原子质量比较大,若高速钢采用离心铸造生产,则会发生碳化物偏析,较重的钨碳化物富集在材料表层,降低材料表层韧性。综合考虑,w含量选择为4.6-5.1%。
15.mo:钼的作用与钨类似,主要存在形式是mo2c碳化物。钼原子量比钨小,每1%的钼能够取代1.8%的钨,即钼的钨当量是1.8。用钼部分替代w元素,可在一定程度上改善碳化物偏析现象;同时钼还影响回火时碳化物的析出位置,避免晶界处析出碳化物,可以提高钢的韧性。但若用钼全部取代钨,在热处理过程中会加剧氧化和脱碳。mo的含量选择为5.4-6.1%。
16.cr:铬元素能够改善高速钢的淬透性和抗氧化性。在高速钢中,铬元素既可以存在于m6c碳化物中,也可以形成m
23
c6碳化物。后者的溶解温度不高,在淬火保温时可以全部溶入高温奥氏体,并在回火时析出二次碳化物,强化材料。但过量添加cr会造成碳化物的分布不均。因此cr元素含量确定为5.3-5.7%。
17.ni:镍是非碳化物形成元素,主要存在α-fe或γ-fe中,起固溶强化作用。高速钢轧辊中加入ni能够提升抗龟裂和剥落能力,延长使用寿命。但是,钢中加ni会造成残余奥氏体含量增加,导致材料的硬度下降。因此ni含量确定为1.0-1.4%。
18.nb:nb是强碳化物形成元素,与c结合可以形成nbc。当高速钢中同时含有vc与w2c时,由于前者比后者密度小,在离心铸造时会出现碳化物偏析现象,使高速钢的耐磨性不均
匀。此时在高速钢加入适量nb,能够促进形成(nbvmo)c复合碳化物,提高碳化物密度,减轻离心力引起的偏析。nb含量确定为0.9-1.3%。
19.co:钴是非碳化物形成元素,大部分溶于基体中。高速钢中的钴不仅阻碍自回火m3c的形成,还具有细化回火析出的二次碳化物与延缓过时效的作用。因此,钴能够显著提升高速钢的红硬性与耐磨性。但是,世界上钴资源匮乏,其价格十分昂贵,钴的大量添加会提升高速钢的制造成本。因此,钴的添加量为1.0-1.2%。
20.al:铝是非碳化物形成元素,固溶于基体,能够显著提高基体高温性能,铝元素的加入,还可以显著改善高速钢的高温抗氧化能力,特别是铝在凝固过程中,富集在碳化物生长前沿,阻碍碳化物的长大,铝有显著改善碳化物形态和分布的效果,对提高高速钢的强度和韧性有很好的效果。但是,铝降低高速钢淬透性,因此,本发明将铝与提高高速钢淬透性的硼元素共同加入,才会确保耐磨高速钢具有良好的淬透性。适宜的铝加入量为1.1-1.3%al。
21.b:硼加入高钒高速钢中,能与高速钢中钒、铬元素相互作用,当v元素加入量4.1-4.3%,cr元素加入量5.3-5.7%时,加入1.2-1.4%b的,可以生成体积分数3.2-3.7%的显微硬度超过4000hv的(cr
0.5v0.5
)b相,(cr
0.5v0.5
)b相的显微硬度,显著高于钨、钼、铬、钒、铌元素形成的碳化物的硬度,具有优异的抗磨性能。
22.c:碳是形成碳化物的基本元素,其含量直接影响碳化物的数量。另一方面,碳元素能固溶到基体中,起到固溶强化作用。随着c含量增加,高速钢中碳化物数量增多,耐磨性提高。但c含量应与w、cr、mo、v、nb等元素含量相平衡,因此碳含量确定为1.6-2.0%。
23.根据以上原则,耐磨高速钢化学组成及其质量分数设计如下:1.6-2.0%c,4.1-4.3%v,1.2-1.4%b,5.3-5.7%cr,4.6-5.1%w,5.4-6.1%mo,1.0-1.2%co,1.0-1.4%ni,1.1-1.3%al,0.9-1.3%nb,《1.0%si,《0.6%mn,《0.03%s,《0.03%p,其余为fe及不可避免的杂质元素。
24.高速钢铸件中,马氏体数量较多,硬度达到52-56hrc。为了改善高速钢铸件的加工性能,高速钢铸件经过950℃保温6h进行炉冷退火,可以降低硬度至32hrc以下,加工性能良好。然后,在1050-1075℃奥氏体化60-120分钟,并空冷至室温,基体转化为高硬度孪晶马氏体 少量残留奥氏体。最后,高速钢工件在500-530℃回火保温6-8h,炉冷至室温,可以促进残留奥氏体中析出m
23
c6型碳化物,降低残留奥氏体稳定,使残留奥氏体转变成马氏体,促进高速钢硬度的进一步提升。最后获得耐磨性和红硬性好的耐磨高速钢。
25.本发明与现有技术相比,具有以下特点:
26.(1)本发明高速钢中通过加入钒、铬和硼元素,可以生成显微硬度超过4000hv的(cr
0.5v0.5
)b相,v元素加入量4.1-4.3%,cr元素加入量5.3-5.7%,b元素加入量1.2-1.4%时,可以生成体积分数3.2-3.7%的(cr
0.5v0.5
)b相,(cr
0.5v0.5
)b相的显微硬度,显著高于钨、钼、铬、钒、铌元素形成的碳化物的硬度,具有优异的抗磨性能。
27.(2)本发明高速钢中,因钴、硼和铝元素的共同加入,显著提高了高速钢的红硬性和高温耐磨性,硼、铝价格低廉,克服了高钴高速钢成本高的缺陷,与高钴高速钢相比,本发明耐磨高速钢具有良好的成本优势,降低材料成本25%以上。
28.(3)本发明采用淬火后空冷 回火后炉冷的热处理工艺,可以获得硬度大于68hrc,耐磨性优良的耐磨高速钢,600℃的耐磨性比无钴高速钢提高3倍以上,用于制造热轧辊,将
会产生良好的经济效益。
附图说明
29.图1为高速钢经1050℃奥氏体化90分钟后空冷至室温 520℃回火保温6h,炉冷至室温的sem图,(a)200x,(b)500x。
具体实施方式
30.下面结合实例对本发明作进一步阐述,但本发明并不限于以下实施例。
31.实施例1:
32.一种耐磨高速钢及其热处理方法,其特征在于用500公斤中频感应电炉熔炼,其制造工艺步骤是:先在感应电炉中加入高速钢废料、废钢、生铁、钼铁、钨铁、铌铁、金属钴、镍板,钢水熔清后加入铬铁,出炉前加入钒铁和硼铁,然后用铝对钢液脱氧和合金化,钢水化学组成及其质量分数控制为1.83%c,4.11%v,1.27%b,4.77%w,5.59%mo,5.51%cr,1.08%co,1.26%ni,1.09%nb,1.20%al,0.56%si,0.53%mn,0.014%s,0.028%p,其余为fe及不可避免的杂质元素。钢水炉前分析合格后出炉,钢水出炉温度1592℃。将钢水浇铸到卧式离心铸造机中,铸造完成后空气冷却至室温,获得高速钢毛坯。为了降低硬度,将铸件经过950℃保温6h进行炉冷退火。然后,工件在1050℃奥氏体化90分钟后空冷至室温;最后,工件在520℃回火保温6h,炉冷至室温,可获得耐磨性和红硬性好的耐磨高速钢,耐磨高速钢中含有体积分数3.2%的显微硬度超过4000hv的(cr
0.5v0.5
)b相,(cr
0.5v0.5
)b相的显微硬度,显著高于钨、钼、铬、钒、铌元素形成的碳化物的硬度,具有优异的抗磨性能,其力学性能见表1。
33.实施例2:
34.一种耐磨高速钢及其热处理方法,其特征在于用500公斤中频感应电炉熔炼,其制造工艺步骤是:先在感应电炉中加入高速钢废料、废钢、生铁、钼铁、钨铁、铌铁、金属钴、镍板,钢水熔清后加入铬铁,出炉前加入钒铁和硼铁,然后用铝对钢液脱氧和合金化,钢水化学组成及其质量分数控制为1.89%c,4.27%v,4.85%w,5.47%mo,5.31%cr,1.07%co,1.39%b,1.34%ni,1.28%al,1.18%nb,0.49%si,0.57%mn,0.020%s,0.024%p,其余为fe及不可避免的杂质元素。钢水炉前分析合格后出炉,钢水出炉温度1615℃。将钢水浇铸到卧式离心铸造机中,铸造完成后空气冷却至室温,获得高速钢毛坯。为了降低毛坯硬度,使铸件经过950℃保温6h进行炉冷退火。然后,高速钢工件在1075℃奥氏体化60分钟后空冷至室温;最后,工件在530℃回火保温7h,炉冷至室温,可获得耐磨性和红硬性好的耐磨高速钢,耐磨高速钢中含有体积分数3.7%的显微硬度超过4000hv的(cr
0.5v0.5
)b相,(cr
0.5v0.5
)b相的显微硬度,显著高于钨、钼、铬、钒、铌元素形成的碳化物的硬度,具有优异的抗磨性能,其力学性能见表1。
35.实施例3:
36.一种耐磨高速钢及其热处理方法,其特征在于用500公斤中频感应电炉熔炼,其制造工艺步骤是:先在感应电炉中加入高速钢废料、废钢、生铁、钼铁、钨铁、铌铁、金属钴、镍板,钢水熔清后加入铬铁,出炉前加入钒铁,然后用铝对钢液脱氧和合金化,钢水化学组成及其质量分数控制为1.63%c,4.10%v,1.33%b,4.76%w,5.94%mo,5.62%cr,1.04%co,
1.29%ni,1.15%al,1.13%nb,0.51%si,0.42%mn,0.025%s,0.027%p,其余为fe及不可避免的杂质元素。钢水炉前分析合格后出炉,钢水出炉温度1598℃。将钢水浇铸到卧式离心铸造机中,铸造完成后空气冷却至室温,获得高速钢毛坯。为了降低毛坯硬度,使铸件经过950℃保温6h进行炉冷退火。然后,工件在1060℃奥氏体化70分钟后空冷至室温;最后,工件在510℃回火保温8h,炉冷至室温,可获得耐磨性和红硬性较好的耐磨高速钢,耐磨高速钢中含有体积分数3.6%的显微硬度超过4000hv的(cr
0.5v0.5
)b相,(cr
0.5v0.5
)b相的显微硬度,显著高于钨、钼、铬、钒、铌等元素形成的碳化物的硬度,具有优异的抗磨性能,其力学性能见表1。
37.实施例4:
38.一种耐磨高速钢及其热处理方法,其特征在于用500公斤中频感应电炉熔炼,其制造工艺步骤是:先在感应电炉中加入高速钢废料、废钢、生铁、钼铁、钨铁、铌铁、金属钴、镍板,钢水熔清后加入铬铁,出炉前加入钒铁,然后用铝对钢液脱氧和合金化,钢水化学组成及其质量分数控制为1.99%c,4.27%v,1.21%b,4.73%w,6.02%mo,5.35%cr,1.08%co,1.26%al,1.03%ni,1.19%nb,0.57%si,0.54%mn,0.027%s,0.026%p,其余为fe及不可避免的杂质元素。钢水炉前分析合格后出炉,钢水出炉温度1608℃。将钢水浇铸到卧式离心铸造机中,铸造完成后空气冷却至室温,获得高速钢毛坯。为了降低毛坯硬度,使铸件经过950℃保温6h进行炉冷退火。然后,工件在1070℃奥氏体化75分钟后空冷至室温;最后,工件在520℃回火保温7h,炉冷至室温,可获得耐磨性和红硬性好的耐磨高速钢,耐磨高速钢中含有体积分数3.4%的显微硬度超过4000hv的(cr
0.5v0.5
)b相,(cr
0.5v0.5
)b相的显微硬度,显著高于钨、钼、铬、钒、铌元素形成的碳化物的硬度,具有优异的抗磨性能,其力学性能见表1。
39.磨损试验在改装后mm-200型环块磨损试验机上进行,试验载荷为196n,时间为120min,试验温度600℃,试验机转速为200转/分。对磨环材料为gcr15,其硬度为60-62hrc。耐磨高速钢的磨损失重如表1所示。
40.表1耐磨高速钢室温力学性能和600℃时磨损失重数据
41.力学性能硬度/hrc冲击韧性,j/cm2磨损失重/mg实施例168.115.38.8实施例268.716.59.3实施例368.515.78.5实施例468.216.49.0
42.本发明高速钢中通过加入钒、铬和硼元素,生成显微硬度超过4000hv的(cr
0.5v0.5
)b相,v元素加入量4.1-4.3%,cr元素加入量5.3-5.7%,b元素加入量1.2-1.4%时,可以生成体积分数3.2-3.7%的(cr
0.5v0.5
)b相,(cr
0.5v0.5
)b相的显微硬度,显著高于钨、钼、铬、钒、铌元素形成的碳化物的硬度,具有优异的抗磨性能。本发明高速钢中,因钴、硼和铝元素的共同加入,显著提高了高速钢的红硬性和高温耐磨性,硼、铝价格低廉,克服了高钴高速钢成本高的缺陷,与高钴高速钢相比,本发明耐磨高速钢具有良好的成本优势,降低材料成本25%以上。本发明采用淬火后空冷 回火后炉冷的热处理工艺,可以获得硬度大于68hrc,耐磨性优良的耐磨高速钢,600℃的耐磨性比无钴高碳高钒高速钢提高3倍以上,用于制造热轧辊,推广应用将具有良好的经济效益。
再多了解一些
本文用于企业家、创业者技术爱好者查询,结果仅供参考。