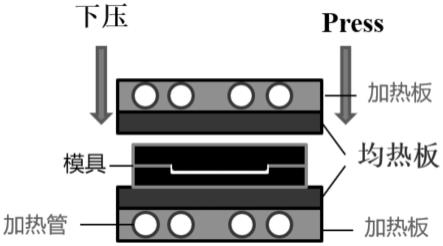
1.本发明涉及一种无碳高速钢材料,具体涉及一种高速钢及其制备方法和应用。
背景技术:
2.3d曲面玻璃及非球面曲面玻璃其较为复杂的形状赋予了玻璃特殊的应用功能,是信息技术、光电通讯、汽车工业和智能设备等产业中的重要元件。其中3d曲面玻璃能够使得显示窗口更加饱满,具有良好的视觉效果,并且在触控手感上更符合人体工程学原理,因此被逐渐广泛应用于移动手机的中高端机型中,数据显示2020年智能手机3d玻璃盖板使用率约在27%左右,我国3d玻璃盖板市场规模约为192亿元。与此同时,平板计算机、头戴式vr设备、智能手表、智能手环等可穿戴式智能产品、车辆中控及便携式仪表盘等场景均陆续出现3d曲面玻璃的应用,需求量持续提升。而非球面曲面玻璃是重要的光学元件,在镜头中可以有效地提高系统成像质量,简化镜头结构,提高光学稳定性,减少重量及成本,被广泛应用于安防、监控和汽车自动驾驶等需要成像的领域中。随着工业智能化、自动化的发展,市场对3d曲面玻璃及非球面曲面玻璃的需求量及精度要求不断提升。但由于3d曲面玻璃及非球面曲面玻璃其具有不规则的复杂形状尺寸,自身的几何特点决定了其加工难度要大大高于平面玻璃和球面玻璃。目前这些形状复杂的玻璃主要通过冷加工和热成形两种工艺,但冷加工需要昂贵的加工设备和较长的加工周期,限制了其在小尺寸、多样化、大产量的民用需求领域的应用。
3.3d曲面玻璃及非球面曲面玻璃的热成形技术是,通过成形模具对加热后的高黏弹性态玻璃施加压力流变成形,从而制备出与模具尺寸一致的高形状和尺寸精度曲面玻璃。3d曲面玻璃的热成形设备被称为3d玻璃热弯机,而非球面曲面玻璃的热成形设备被称为全自动精密光学非球面模压机,两者的生产玻璃元件的制备原理一致,仅在玻璃类型、尺寸、温度、模具等具体细节方面存在差异,本专利将其统一称为玻璃热弯机。
4.在玻璃热弯机的热成形工序中,控温精度、温度均匀性、传力均匀性及加热速率尤为重要,决定了制成玻璃元件的成形精度和生产效率,而这些均受热弯系统各部件所影响。热弯工序是通过加热板、均热板、模具等部件将热量和力传递到玻璃上的,其中加热板是热弯过程的关键零部件,与电加热管、气缸相接触,是热弯系统传热传力的起始部件,是确保玻璃工件均匀变形和高效率生产的前提。而目前热弯机发热板为保证高温抗氧化及抗蠕变性能,如欧洲专利ep2782879b1所述行业中热弯设备均采用310s或相近牌号不锈钢材质。然而作为发热板,310s不锈钢存在导热系数低、热膨胀系数大、高温硬度低等问题。310s不锈钢导热系数低,室温时仅为12-15w/(m
·
k),作为传热初始部件,限制了向其它部件的传热速率及温度均匀性,也加重了加热管的过热及负载;310s不锈钢热膨胀系数大,在高温下与其它部件间存在大的热膨胀系数差异,造成部件悬空及变形等情况;同时材料在高温条件下容易软化,在600℃~900℃使用时硬度低至10hrc以下,在长时间传力过程中易发生划伤及变形。
5.综上所述,310s不锈钢作为热弯机加热板限制了传热效率、受力均匀性和温度均
匀性,长时间使用过程中会造成加热管的寿命下降和影响产品的稳定生产,限制了热弯机设备精度的进一步提升。但目前行业内未找到更合适的替代材料,因而亟需找到一种导热性优良、热膨胀系数较小且同时具有高热硬性的全新加热板材料。
技术实现要素:
6.本发明目的在于,针对热弯机加热板310s不锈钢材质导热系数低、热膨胀系数大、高温硬度低,限制了玻璃热弯稳定性及热弯精度的现状,提出一种导热系数高、热膨胀系数低、高温硬度高的加热板材料,提升热弯过程的热传导速度、传热均匀性及传力均匀性,进一步提升热弯技术的精度及稳定性,满足更高的工业智能化、自动化需求。
7.为了实现上述技术目的,本发明提供了一种高速钢材料。本发明提供的诸多技术方案中的优选技术方案所能产生的诸多技术效果详见下文阐述。
8.本发明提供的一种高速钢材料,所述高速钢为无碳高速钢;或所述高速钢由无碳高速钢作为基体材料,并加入氮化硅晶须及氮化硅粒子进一步强化。
9.本发明所设计的无碳高速钢是一种通过原位生成的金属间化合物进行强化的材料,与传统碳化物高速钢中的强化相碳化物相比,金属间化合物强化相扩散系数低,在高温下难以聚集长大,并且其能够与铁基体保持良好的界面关系,因而赋予了其基体出色的高温硬度、大的导热系数及良好的韧性。针对800℃以上的高温使用工况,在无碳高速钢基体中可添加了适量氮化硅晶须及粒子,通过高导热、高稳定性的氮化硅对材料的韧性、导热性能及抗蠕变性能进行进一步的强化。
10.进一步的,所述无碳高速钢主要由fe、co、ni、mo、w、cr、nb、ti、si、y、la等元素组成。在工程上应用时,根据产品及使用温度可以选择性添加强化相,如:氮化硅晶须及其微米级粒子。
11.作为优选方案,所述无碳高速钢,以质量百分比计,包括下述组分:
12.co占10~30%、ni占0~5%、mo占8~20%、w占0~5%,cr占0~13%、nb占0~2%、ti占0~2%、si占0.2~1%,y和la之和占0~1%,其余为fe。
13.当高速钢中含有氮化硅晶须及氮化硅粒子时,以质量百分比计;si3n4晶须占0.01~2%,si3n4微米级粒子占0.01~3%。
14.进一步的,所述高速钢中,以质量百分比计,包括下述组分:co占15~30%、ni占2~5%、mo占8~20%、w占2~5%,cr占2~13%、nb和ti之和占0.5~2%、si占0.2~1%,y和la之和占0.1~1%,其余为fe。
15.进一步的,当高速钢中含有氮化硅晶须及氮化硅粒子时,以质量百分比计;si3n4晶须占1~2%,si3n4微米级粒子占1~3%。
16.进一步的,所述高速钢,以质量百分比计,包括下述组分:co占15~25%、ni占2~4%、mo占10~18%、w占2~5%,cr占2~13%、nb和ti之和占0.5~2%、si占0.2~0.5%,y和la之和占0.1~1%。
17.进一步的,当高速钢中含有氮化硅晶须及氮化硅粒子时,以质量百分比计;si3n4晶须占1~2%,si3n4微米级粒子占1~3%。
18.更进一步的,所述高速钢,以质量百分比计,包括下述组分:co占20~23%、ni占3~5%、mo占15~16%、w占2~3%,cr占6~13%、nb和ti之和占1.5~2%、si占0.4~0.5%,
y和la之和占0.6~1%。当高速钢中含有氮化硅晶须及氮化硅粒子时,以质量百分比计;si3n4晶须占1~2%,si3n4微米级粒子占1~2%。
19.更进一步的,所述高速钢,以质量百分比计,nb占0.5-1%;ti占0.7-1%。
20.更进一步的,所述高速钢,以质量百分比计,y占0.2-0.5%,la占0.4-0.5%。
21.进一步的,所述无碳高速钢的晶粒大小为10~50μm;当高速钢中含有氮化硅晶须及氮化硅粒子时si3n4晶须直径为0.5~1.5μm,长度为5~20μm,si3n4微米级粒子尺寸为2~5μm。
22.本发明提供的一种高速钢的制备方法,包括下述步骤:
23.当高速钢为无碳高速钢时,其制备方法为:按设计组分配取原料;混合均匀后经压制、烧结,得到烧结坯;烧结坯经热处理,得到所述无碳高速钢。其中混合、压制、烧结,热处理等工序均按照高速钢中含有氮化硅晶须及氮化硅粒子时的对应工艺和参数执行。
24.当高速钢中含有氮化硅晶须及氮化硅粒子时,其制备方法包括下述步骤:
25.(1)氮化硅晶须及微米级粒子酸洗活化
26.将氮化硅晶须及微米级粒子用酸性溶液进行一定时长的酸洗,酸洗结束后用酒精反复冲洗干净,最后通过真空干燥箱干燥;
27.(2)基体原料混合
28.按配比将金属元素粉末、酸洗后的si3n4微米级粒子与额外加入的微量炭黑一同称取混合并过筛,随后加入成型剂,采用湿式球磨方法得到混合料,干燥后得到基体原料混合物;
29.(3)氮化钛晶须添加
30.按配比将步骤(2)得到的基体原料混合物和酸洗后的si3n4晶须按比例称取后进行短时间球磨混合,干燥后得到混合原料;
31.(4)压制成型
32.将步骤(3)得到混合原料进行压制,得到压制坯;
33.(5)烧结
34.将步骤(4)得到的压制坯放入烧结炉进行烧结,冷却后得到烧结坯;烧结温度大于等于1300℃;
35.(6)热处理
36.将步骤(5)得到的烧结坯进行固溶处理及高温时效处理,得到最终的玻璃热弯机加热板用无碳高速钢材料;固溶处理的温度为1200℃~1280℃。
37.进一步的,所述步骤(1)中,酸洗溶液为:氢氟酸与硝酸的混合溶液,氢氟酸与硝酸的体积比为1:(4~6),酸洗时间为12~24小时。
38.进一步的,所述步骤(2)中,过筛所用筛子的目数优选为200~500目;称取混合过筛是为了防止低密度的si3n4微米级粒子团聚。
39.进一步的,所述步骤(2)中,添加的微量炭黑是为了在烧结过程中脱除原料表面的氧元素,不参与材料的构成,炭黑的添加量为(0.1~0.4)wt%。
40.进一步的,所述步骤(2)与(3)中,采用的成形剂和球磨介质可为粉末冶金行业内常用的选择,如石蜡和酒精等,成型剂添加量为3~6wt%。
41.进一步的,球磨在氮气或氩气的保护下进行,球磨方式可采取行星球磨或滚筒球
磨等行业内常用的球磨方式。当采用滚筒球磨时球磨转速为(60~150)rpm,采用行星球磨时球磨转速为(200~250)rpm;在步骤(2)中,球料比为(3~6):1,球磨时间为(48~72)h,采用硬质合金球;步骤(3)中,球料比为(1~2):1,球磨时间为(12~24)h,采用钢球。
42.进一步的,所述步骤(2)与(3)中,所述干燥在真空干燥箱中进行,干燥温度为(75~90)℃,干燥时间为(4~8)h。
43.进一步的,所述步骤(4)中,压制可采用模具冷压及冷等静压等行业常用压制方式,压制压力为100~250mpa。
44.进一步的,所述步骤(5)中,所采用烧结方式为真空烧结,气压为10-2
pa~10pa,烧结温度为1300℃~1450℃,最高温保温时间为2~3h。
45.进一步的,所述步骤(6)中,固溶处理在盐浴、真空或气氛保护下进行,温度为1200℃~1250℃,固溶处理时间为(20~120)min,固溶处理后通过油淬冷却到室温。高温时效温度根据工况设定为700~800℃或900℃~1000℃,时效时间为2~5h。高温时效的作用在于在高于使用工况温度进行过时效处理,促使析出相分布更均匀,并且在使用温度在更为稳定。
46.本发明所设计和制备的高速钢,其抗弯强度为2700~3300mpa、冲击韧性为9.5~11.5j/cm2、室温硬度为62-70hrc、800℃时的硬度为55-62hrc、600℃回火200h后的硬度为57-64hrc、400℃下导热系数为41-45w/(m
·
k)。本发明实现了产品抗弯强度、冲击韧性、室温-高温硬度、导热系数的综合优化。
47.本发明所设计和制备的高速钢的应用,包括将其用于玻璃热弯机的加热板。当然,任何要求材料具有导热性优良、热膨胀系数较小且同时具有高热硬性的领域,也可使用本发明设计和制备的材料。
48.本发明摒弃传统碳化物强化高速钢,采用新型金属间化合物强化无碳高速钢为基体材料。在制备材料基体时,采用co、mo、w、nb、ti等元素用于生成多种金属间化合物;相较于普通无碳高速钢材料,还添加cr、ni元素用于提升材料的高温抗氧化性,si用于提高材料硬度,稀有金属元素y、la两者用于吸附原料中的氧并钉扎于组织中,可有效活化烧结并提高材料韧性及强度。
49.玻璃热弯根据尺寸及玻璃材质的不同,需求不同的工作温度。例如非球面曲面玻璃生产的工作温度为500℃~700℃,3d曲面玻璃生产的工作温度为800℃~950℃,因此对加热板的性能要求有所差异。在低于800℃的工况时,无碳高速钢基体材料即可满足使用需求;而高于800℃的高温工况对材料韧性、导热性能及抗蠕变性能的要求更高,氮化硅晶须的添加能够通过裂纹桥联、裂纹偏转、拔出效应等方式进一步提升材料的韧性,氮化硅微米级粒子有利于细化晶粒,提高材料的组织均匀性,此外氮化硅本身的加入可以提升材料的导热系数及高温稳定性。
50.基于上述技术方案,本发明实施例至少可以产生如下技术效果:
51.(1)本发明提供的高速钢及其制备方法,制备的无碳高速钢材料在常规无碳高速钢基础上,通过其它合金元素添加的方式,提升了材料的高温抗氧化性能,固定了组织中的氧元素,净化晶界并进一步提高力学性能。此外还在基体外通过氮化硅晶须及微米粒子的加入,进一步提升材料韧性、强度、导热系数及抗蠕变性能以满足更高温度工况的需求;
52.(2)相较于碳化物强硬化高速钢和常规加热板材质310s不锈钢,本发明提供的高
速钢材料具有更高的高温硬度、导热系数以及更低的热膨胀系数。在作为玻璃热弯机加热板工作时,能够及时且均匀地将热量传递到均热板上,同时出色的高温硬度和低的热膨胀系数赋予了工件高温下长时间的尺寸稳定性,能够保证压力均匀地传递到均热板及模具上。
53.(3)本发明提供的高速钢用作玻璃热弯机加热板时,在实际应用中,能够将热量的迅速传递,降低其它配件的负担。能够降低加热管的负载,避免局部过热,也减低了对加热板与加热管的配合精度要求,提高加热管及加热板的寿命,降低生产支出。同时本发明所设计和制备的高速钢用作玻璃热弯机加热板时,能够有效提高玻璃的升温速度,保证玻璃热弯的温度及压力均匀性,提高玻璃热弯的精度和效率。
附图说明
54.图1为热弯系统的结构示意图。
55.图2为热弯机加热板外观形状。
56.图3为实施例1所制备无碳高速钢的显微组织形貌。
具体实施方式
57.为使本发明的目的、技术方案和优点更加清楚,下面将对本发明的技术方案进行详细的描述。显然,所描述的实施例仅是本发明一部分实施例,而不是全部的实施例。基于本发明中的实施例,本领域普通技术人员在没有做出创造性劳动的前提下所得到的所有其它实施方式,都属于本发明所保护的范围。
58.一、实施例和对比例
59.在实施例1~实施例5中制备热弯机加热板用无碳高速钢材料,在对比例1~3中制备不在专利成分及工艺优选范围内的无碳高速钢材料:
60.1、原料co粉占10~30%、ni粉占0~5%、mo粉占8~20%、w粉占0~5%,cr粉占0~13%、nb粉占0~2%、ti粉占0~2%、si粉占0.2~1%,y粉和la粉之和占0~1%。其中co粉、ni粉、nb粉、w粉的粒度为3-5微米、mo粉的粒度为5-10微米、cr的粒度为5-10微米、ti粉的粒度为1-3微米、si粉的粒度为1-2微米,y粉、la粉的粒度为200-325目。
61.当需要添加si3n4晶须和si3n4微米级粒子时,所用si3n4晶须的直径为0.5~1.5μm,长度为5~20μm,si3n4微米级粒子尺寸为2~5μm。
62.实施例及对比例制备的原料表(以重量百分比计)如下述表1所示。
63.表1实施例及对比例的原料表(以质量百分比计)
64.[0065][0066]
2、制备方法:
[0067]
实施例1(主要针对玻璃低温热弯使用)
[0068]
(1)氮化硅晶须及微米级粒子酸洗活化
[0069]
主要针对玻璃低温热弯使用,未添加氮化硅晶须及粒子。
[0070]
(2)基体原料混合
[0071]
按配比将金属元素粉末与额外添加的0.2wt%的炭黑相混合后过300目筛,再加入5wt%的石蜡作为成型剂,将混合料放入充满氮气的球磨罐中通过行星球磨进行混合,球磨介质为酒精,采用硬质合金磨球,球料质量比为4:1,球磨时间为72h,球磨转速为220rpm。球磨后采用真空干燥箱在85℃下进行干燥8h,干燥结束后过40目筛得到混合料粉末。
[0072]
(3)氮化钛晶须添加
[0073]
主要针对玻璃低温热弯使用,未添加氮化硅晶须及粒子;
[0074]
(4)压制成型
[0075]
将混合料粉末放置于模具中,采用模具冷压压制,压制压力为200mpa,得到压制坯;
[0076]
(5)烧结
[0077]
将压制坯放置于真空烧结炉中进行烧结,待抽真空至气压降低至10-2
pa后进行烧结,烧结最高温度为1300℃,保温时间为2h,冷却至常温后得到烧结坯;
[0078]
(6)热处理
[0079]
将烧结坯放置于氮气保护中进行固溶处理,固溶处理温度为1200℃,固溶处理保温时间为20分钟,固溶处理结束后通过油淬冷却到室温。待完全冷却至室温后进行高温时效处理,时效温度为700℃,时效时间为3h。时效结束后得到最终的玻璃热弯机加热板用无碳高速钢材料。
[0080]
实施例2
[0081]
(1)氮化硅晶须及微米级粒子酸洗活化
[0082]
将氮化硅晶须及微米级粒子进行酸洗18h,采用的酸液中氢氟酸与硝酸的体积比为1:5,酸洗结束后采用大量酒精冲洗干净,在真空干燥箱中进行烘干;
[0083]
(2)基体原料混合
[0084]
按配比将金属元素粉末、酸洗后的si3n4微米级粒子与额外添加的0.3wt%的炭黑相混合后过400目筛,再加入4wt%的石蜡作为成型剂,将混合料放入充满氮气的球磨罐中通过滚筒球磨机进行混合,球磨介质为酒精,采用硬质合金磨球,球料质量比为5:1,球磨时间为72h,球磨转速为100rpm。球磨后采用真空干燥箱在80℃下进行干燥8h,干燥结束后过40目筛得到基体原料混合粉末。
[0085]
(3)氮化钛晶须添加
[0086]
按成分配比将酸洗后的si3n4晶须与基体原料混合粉末称取后进行球磨混合,球磨介质为酒精,采用钢磨球,球料质量比为1:1,球磨时间为12h,球磨转速为100rpm。球磨后采用真空干燥箱在80℃下进行干燥8h,干燥结束后过40目筛得到混合料粉末。
[0087]
(4)压制成型
[0088]
将混合料粉末放置于模具中,采用模具冷压压制,压制压力为180mpa,得到压制坯;
[0089]
(5)烧结
[0090]
将压制坯放置于真空烧结炉中进行烧结,待抽真空至气压降低至10-2
pa后进行烧结,烧结最高温度为1370℃,保温时间为2h,冷却至常温后得到烧结坯;
[0091]
(6)热处理
[0092]
将烧结坯放置于氮气保护中进行固溶处理,固溶处理温度为1220℃,固溶处理保温时间为40分钟,固溶处理结束后通过油淬冷却到室温。待完全冷却至室温后进行高温时效处理,时效温度为900℃,时效时间为3h。时效结束后得到最终的玻璃热弯机加热板用无碳高速钢材料。
[0093]
实施例3
[0094]
(1)氮化硅晶须及微米级粒子酸洗活化
[0095]
将氮化硅晶须及微米级粒子进行酸洗12h,采用的酸液中氢氟酸与硝酸的体积比为1:4,酸洗结束后采用大量酒精冲洗干净,在真空干燥箱中进行烘干;
[0096]
(2)基体原料混合
[0097]
按配比将金属元素粉末、酸洗后的si3n4微米级粒子与额外添加的0.2wt%的炭黑相混合后过200目筛,再加入5wt%的石蜡作为成型剂,将混合料放入充满氮气的球磨罐中通过滚筒球磨机进行混合,球磨介质为酒精,采用硬质合金磨球,球料质量比为5:1,球磨时间为60h,球磨转速为120rpm。球磨后采用真空干燥箱在80℃下进行干燥8h,干燥结束后过40目筛得到基体原料混合粉末。
[0098]
(3)氮化钛晶须添加
[0099]
按成分配比将酸洗后的si3n4晶须与基体原料混合粉末称取后进行球磨混合,球磨介质为酒精,采用钢磨球,球料质量比为1:1,球磨时间为18h,球磨转速为100rpm。球磨后采用真空干燥箱在80℃下进行干燥8h,干燥结束后过40目筛得到混合料粉末。
[0100]
(4)压制成型
[0101]
将混合料粉末放置于模具中,采用模具冷压压制,压制压力为200mpa,得到压制
坯;
[0102]
(5)烧结
[0103]
将压制坯放置于真空烧结炉中进行烧结,待抽真空至气压降低至10-2
pa后进行烧结,烧结最高温度为1390℃,保温时间为2h,冷却至常温后得到烧结坯;
[0104]
(6)热处理
[0105]
将烧结坯放置于氮气保护中进行固溶处理,固溶处理温度为1220℃,固溶处理保温时间为40分钟,固溶处理结束后通过油淬冷却到室温。待完全冷却至室温后进行高温时效处理,时效温度为900℃,时效时间为3h。时效结束后得到最终的玻璃热弯机加热板用无碳高速钢材料。
[0106]
实施例4
[0107]
(1)氮化硅晶须及微米级粒子酸洗活化
[0108]
将氮化硅晶须及微米级粒子进行酸洗20h,采用的酸液中氢氟酸与硝酸的体积比为1:6,酸洗结束后采用大量酒精冲洗干净,在真空干燥箱中进行烘干;
[0109]
(2)基体原料混合
[0110]
按配比将金属元素粉末、酸洗后的si3n4微米级粒子与额外添加的0.4wt%的炭黑相混合后过300目筛,再加入5wt%的石蜡作为成型剂,将混合料放入充满氮气的球磨罐中通过滚筒球磨机进行混合,球磨介质为酒精,采用硬质合金磨球,球料质量比为4:1,球磨时间为72h,球磨转速为150rpm。球磨后采用真空干燥箱在80℃下进行干燥8h,干燥结束后过40目筛得到基体原料混合粉末。
[0111]
(3)氮化钛晶须添加
[0112]
按成分配比将酸洗后的si3n4晶须与基体原料混合粉末称取后进行球磨混合,球磨介质为酒精,采用钢磨球,球料质量比为2:1,球磨时间为12h,球磨转速为80rpm。球磨后采用真空干燥箱在80℃下进行干燥8h,干燥结束后过40目筛得到混合料粉末。
[0113]
(4)压制成型
[0114]
将混合料粉末放置于模具中,采用冷等静压压制,压制压力为150mpa,得到压制坯;
[0115]
(5)烧结
[0116]
将压制坯放置于真空烧结炉中进行烧结,待抽真空至气压降低至10-2
pa后进行烧结,烧结最高温度为1400℃,保温时间为3h,冷却至常温后得到烧结坯;
[0117]
(6)热处理
[0118]
将烧结坯放置于氮气保护中进行固溶处理,固溶处理温度为1230℃,固溶处理保温时间为60分钟,固溶处理结束后通过油淬冷却到室温。待完全冷却至室温后进行高温时效处理,时效温度为900℃,时效时间为3h。时效结束后得到最终的玻璃热弯机加热板用无碳高速钢材料。
[0119]
实施例5
[0120]
(1)氮化硅晶须及微米级粒子酸洗活化
[0121]
将氮化硅晶须及微米级粒子进行酸洗18h,采用的酸液中氢氟酸与硝酸的体积比为1:5,酸洗结束后采用大量酒精冲洗干净,在真空干燥箱中进行烘干;
[0122]
(2)基体原料混合
[0123]
按配比将金属元素粉末、酸洗后的si3n4微米级粒子与额外添加的0.4wt%的炭黑相混合后过300目筛,再加入5wt%的石蜡作为成型剂,将混合料放入充满氮气的球磨罐中通过滚筒球磨机进行混合,球磨介质为酒精,采用硬质合金磨球,球料质量比为6:1,球磨时间为60h,球磨转速为150rpm。球磨后采用真空干燥箱在80℃下进行干燥8h,干燥结束后过40目筛得到基体原料混合粉末。
[0124]
(3)氮化钛晶须添加
[0125]
按成分配比将酸洗后的si3n4晶须与基体原料混合粉末称取后进行球磨混合,球磨介质为酒精,采用钢磨球,球料质量比为1:1,球磨时间为10h,球磨转速为120rpm。球磨后采用真空干燥箱在80℃下进行干燥8h,干燥结束后过40目筛得到混合料粉末。
[0126]
(4)压制成型
[0127]
将混合料粉末放置于模具中,采用模具冷压压制,压制压力为150mpa,得到压制坯;
[0128]
(5)烧结
[0129]
将压制坯放置于真空烧结炉中进行烧结,待抽真空至气压降低至10-2
pa后进行烧结,烧结最高温度为1420℃,保温时间为3h,冷却至常温后得到烧结坯;
[0130]
(6)热处理
[0131]
将烧结坯放置于氮气保护中进行固溶处理,固溶处理温度为1240℃,固溶处理保温时间为40分钟,固溶处理结束后通过油淬冷却到室温。待完全冷却至室温后进行高温时效处理,时效温度为900℃,时效时间为3h。时效结束后得到最终的玻璃热弯机加热板用无碳高速钢材料。
[0132]
对比例1
[0133]
采用与实施例1相同的制备工艺。
[0134]
对比例2与对比例3
[0135]
采用与实施例3相同的制备工艺。
[0136]
对比例4
[0137]
按配比将金属元素粉末、si3n4晶须、si3n4微米级粒子与额外添加的0.2wt%的炭黑相混合后过300目筛,再加入5wt%的石蜡作为成型剂,将混合料放入充满氮气的球磨罐中通过滚筒球磨机进行混合,球磨介质为酒精,采用硬质合金磨球,球料质量比为5:1,球磨时间为60h,球磨转速为120rpm。球磨后采用真空干燥箱在80℃下进行干燥8h,干燥结束后过40目筛得到基体原料混合粉末。
[0138]
将混合料粉末放置于模具中,采用模具冷压压制,压制压力为200mpa,得到压制坯;
[0139]
将压制坯放置于真空烧结炉中进行烧结,待抽真空至气压降低至10-2
pa后进行烧结,烧结最高温度为1390℃,保温时间为2h,冷却至常温后得到烧结坯;
[0140]
将烧结坯放置于氮气保护中进行固溶处理,固溶处理温度为1220℃,固溶处理保温时间为40分钟,固溶处理结束后通过油淬冷却到室温。待完全冷却至室温后进行高温时效处理,时效温度为900℃,时效时间为3h。时效结束后得到最终的玻璃热弯机加热板用无碳高速钢材料。
[0141]
即在实施例3的基础上,si3n4晶须、si3n4微米级粒子不采用本发明提供的酸洗和
分步加入方案,而是直接加入到成分中。
[0142]
对比例5
[0143]
采用与实施例3相同的制备工艺。
[0144]
对比例6
[0145]
(1)氮化硅晶须及微米级粒子酸洗活化
[0146]
将氮化硅晶须及微米级粒子进行酸洗12h,采用的酸液中氢氟酸与硝酸的体积比为1:4,酸洗结束后采用大量酒精冲洗干净,在真空干燥箱中进行烘干;
[0147]
(2)基体原料混合
[0148]
按配比将金属元素粉末、酸洗后的si3n4微米级粒子与额外添加的0.2wt%的炭黑相混合后过200目筛,再加入5wt%的石蜡作为成型剂,将混合料放入充满氮气的球磨罐中通过滚筒球磨机进行混合,球磨介质为酒精,采用硬质合金磨球,球料质量比为5:1,球磨时间为60h,球磨转速为120rpm。球磨后采用真空干燥箱在80℃下进行干燥8h,干燥结束后过40目筛得到基体原料混合粉末。
[0149]
(3)氮化钛晶须添加
[0150]
按成分配比将酸洗后的si3n4晶须与基体原料混合粉末称取后进行球磨混合,球磨介质为酒精,采用钢磨球,球料质量比为1:1,球磨时间为18h,球磨转速为100rpm。球磨后采用真空干燥箱在80℃下进行干燥8h,干燥结束后过40目筛得到混合料粉末。
[0151]
(4)压制成型
[0152]
将混合料粉末放置于模具中,采用模具冷压压制,压制压力为200mpa,得到压制坯;
[0153]
(5)烧结
[0154]
将压制坯放置于真空烧结炉中进行烧结,待抽真空至气压降低至10pa后进行烧结,烧结最高温度为1250℃,保温时间为2h,冷却至常温后得到烧结坯;
[0155]
(6)热处理
[0156]
将烧结坯放置于氮气保护中进行固溶处理,固溶处理温度为1220℃,固溶处理保温时间为40分钟,固溶处理结束后通过油淬冷却到室温。待完全冷却至室温后进行高温时效处理,时效温度为900℃,时效时间为3h。时效结束后得到最终的玻璃热弯机加热板用无碳高速钢材料。
[0157]
对比例7
[0158]
(1)氮化硅晶须及微米级粒子酸洗活化
[0159]
将氮化硅晶须及微米级粒子进行酸洗12h,采用的酸液中氢氟酸与硝酸的体积比为1:4,酸洗结束后采用大量酒精冲洗干净,在真空干燥箱中进行烘干;
[0160]
(2)基体原料混合
[0161]
按配比将金属元素粉末、酸洗后的si3n4微米级粒子与额外添加的0.2wt%的炭黑相混合后过200目筛,再加入5wt%的石蜡作为成型剂,将混合料放入充满氮气的球磨罐中通过滚筒球磨机进行混合,球磨介质为酒精,采用硬质合金磨球,球料质量比为5:1,球磨时间为60h,球磨转速为120rpm。球磨后采用真空干燥箱在80℃下进行干燥8h,干燥结束后过40目筛得到基体原料混合粉末。
[0162]
(3)氮化钛晶须添加
[0163]
按成分配比将酸洗后的si3n4晶须与基体原料混合粉末称取后进行球磨混合,球磨介质为酒精,采用钢磨球,球料质量比为1:1,球磨时间为18h,球磨转速为100rpm。球磨后采用真空干燥箱在80℃下进行干燥8h,干燥结束后过40目筛得到混合料粉末。
[0164]
(4)压制成型
[0165]
将混合料粉末放置于模具中,采用模具冷压压制,压制压力为200mpa,得到压制坯;
[0166]
(5)烧结
[0167]
将压制坯放置于真空烧结炉中进行烧结,待抽真空至气压降低至10-2
pa后进行烧结,烧结最高温度为1390℃,保温时间为2h,冷却至常温后得到烧结坯;
[0168]
(6)热处理
[0169]
将烧结坯放置于氮气保护中进行固溶处理,固溶处理温度为1150℃,固溶处理保温时间为40分钟,固溶处理结束后通过油淬冷却到室温。待完全冷却至室温后进行高温时效处理,时效温度为900℃,时效时间为3h。时效结束后得到最终的玻璃热弯机加热板用无碳高速钢材料。
[0170]
二、性能检测:
[0171]
由于材料制备在不同温度回火下展现出的性能不同,材料的性能测试将热处理回火温度统一为600℃,3h,从而对材料性能进行评估。表2为实施例及对比例的抗弯强度、冲击韧性、室温硬度、800℃时高温硬度、600℃回火200h后硬度、400℃下导热系数。
[0172]
表2实施例及对比例的性能检测结果
[0173]
[0174][0175]
由表2可知,经过实施例及对比例性能对比,可得知通过本发明技术路线制备的玻璃热弯机加热板用无碳高速钢材料,相对于碳化物粉末冶金高速钢(asp60)和310s不锈钢,具有优越的高温硬度和抗回火性能,能够在持续的高温使用中保持稳定;此外大的导热系数也有利于热量的传输速度及均匀性,有助于提高玻璃热弯过程中玻璃受热均匀性及升温速度,提高热弯技术精度,降低生产成本,是一种极具应用价值的新型粉末冶金高速钢材料。而不在本发明成分范围内的成分,将可能由于添加粒子结合力差、烧结温度过低、合金元素不合适等因素而导致材料致密度及力学性能的下降。
[0176]
以上所述,仅为本发明的具体实施方式,但本发明的保护范围并不局限于此,任何熟悉本技术领域的技术人员在本发明揭露的技术范围内,可轻易想到变化或替换,都应涵盖在本发明的保护范围之内。
[0177]
由图3实施例1所制备无碳高速钢的显微组织形貌,可观察到材料基体晶粒大小为10~50μm。
再多了解一些
本文用于企业家、创业者技术爱好者查询,结果仅供参考。