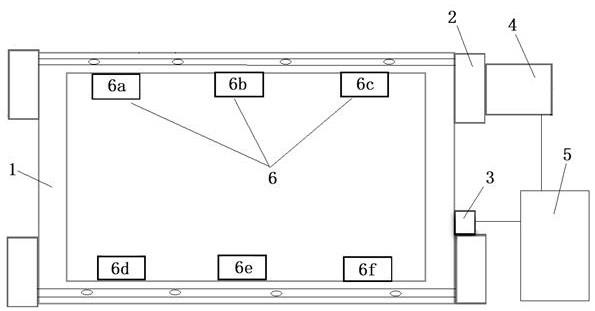
1.本发明涉及无损检测技术领域,尤其涉及一种轧钢支承辊带状堆焊缺陷的跟踪检测方法。
背景技术:
2.支承辊是钢铁制造板带厂的重要消耗备件,一根支承辊长度最大要十米上下,重量在数吨至上百多吨,价值人民币几十万至上千万元,使用周期往往需要数十年之久,是钢铁轧钢厂极为重要的消耗备件。近几年,随着钢铁行业产能升级换代,轧钢冷热厚新轧线投产,由于消耗及事故原因,产生较多报废辊。新品轧辊尤其是支承辊采购市场趋于紧张,部分企业将原来用于冷热轧支承辊堆焊修复技术用于宽厚板支承辊的修复。宽厚板支承辊一般单边使用厚度100mm左右,部分事故辊还需要对深入使用层下的裂纹进行处理和堆焊修复,一般采用多层多道堆焊技术,堆焊及热处理过程要持续长达数月,过程中稍有设备、人员、环境的不稳定因素都可能造成内部缺陷,甚至直接开裂失效的情况。
3.传统冷热支承辊往往仅采用超声波直探头进行堆焊层扫查,对层间开裂及气孔夹渣类缺陷容易检出,但难以发现堆焊搭接面倾斜的缺陷,且难以对缺陷进行定性,造成对部分缺陷漏检概率高,发现的缺陷无法针对危害性进行有效判定。且检测一般依赖于传统仪器手工进行,定位多采用手工测量记录,对人的依赖性较高,数据的偏差较大,难以精确可靠的对带状堆焊缺陷有效跟踪比较,跟踪过程中对缺陷的细微变化敏感度较低,质量风险较大。
技术实现要素:
4.本发明所要解决的技术问题是提供一种轧钢支承辊带状堆焊缺陷的跟踪检测方法,本方法综合利用多种超声波检测手段的优势,能高效、准确、完整的对光滑表面堆焊层进行全面检测,尤其是对带状堆焊缺陷的跟踪检测,提高检测效率及效果,减少人为影响,保证了对堆焊质量及缺陷跟踪检测的有效精确判定。
5.为解决上述技术问题,本发明轧钢支承辊带状堆焊缺陷的跟踪检测方法包括如下步骤:步骤一、制作与支承辊辊面匹配的弧形检测支架,弧形检测支架四角设置磁性滚轮,磁性滚轮设有编码器和驱动马达,驱动马达经磁性滚轮驱动弧形检测支架沿支承辊辊面移动;步骤二、弧形检测支架两侧分别间隔布置六组超声波探头,其中,位于所述弧形检测支架一侧居中的超声波探头是单晶直探头,位于所述弧形检测支架另一侧居中的超声波探头是双晶直探头,其余超声波探头是斜探头;步骤三、多通道超声波检测仪分别与编码器、驱动马达和六组超声波探头电连接,并采集弧形检测支架沿支承辊辊面移动过程六组超声波探头的检测信号;步骤四、根据被检测面长度、曲率半径、堆焊层厚度设置六组超声波探头的扫查路
径、采样模式、记录方式,并对每个探头独立设置超声检测参数、校准灵敏度、设置报警阈值和记录阈值;步骤五、多通道超声波检测仪根据编码器位置及超声波探头检测数据绘制堆焊缺陷的位置-波高曲线,位置-波高曲线记录各次弧形检测支架经过堆焊缺陷后记录的检测数据,采用位置-波高曲线与历次检测结果比较,精确定位并比较堆焊层缺陷的微小变化,实现对堆焊缺陷的跟踪检测。
6.进一步,所述弧形检测支架的直径与支承辊直径匹配,并且所述弧形检测支架至少覆盖支承辊沿圆周方向的1/2辊面,所述弧形检测支架四角同侧的超声波探头分别位于垂直支承辊轴线的上下方向并且为45
°
横波斜探头。
7.进一步,所述弧形检测支架经驱动马达以及磁性滚轮沿支承辊辊面移动过程中,所述六组超声波探头采用水或机油作为耦合剂。由于本发明轧钢支承辊带状堆焊缺陷的跟踪检测方法采用了上述技术方案,即本方法制作与支承辊辊面匹配的弧形检测支架,以及配套的磁性滚轮、编码器、驱动马达,弧形检测支架沿支承辊辊面移动;弧形检测支架两侧布置六组超声波探头,多通道超声波检测仪与编码器、驱动马达和六组超声波探头电连接,采集弧形检测支架沿支承辊辊面移动过程六组超声波探头的检测信号;设置扫查路径等超声检测参数,校准灵敏度,设置报警阈值和记录阈值;多通道超声波检测仪根据编码器位置及超声波探头检测数据绘制位置-波高曲线,通过该曲线与历次检测结果比较,精确定位并比较堆焊层缺陷的微小变化,实现对堆焊缺陷的跟踪检测。本方法综合利用多种超声波检测手段的优势,能高效、准确、完整的对光滑表面堆焊层进行全面检测,尤其是对带状堆焊缺陷的跟踪检测,提高检测效率及效果,减少人为影响,保证了对堆焊质量及缺陷跟踪检测的有效精确判定。
附图说明
8.下面结合附图和实施方式对本发明作进一步的详细说明:图1为本方法中弧形检测支架及配套部件结构示意图;图2为本方法的堆焊缺陷位置-波高曲线示意图。
具体实施方式
9.实施例如图1所示,本发明轧钢支承辊带状堆焊缺陷的跟踪检测方法包括如下步骤:步骤一、制作与支承辊辊面匹配的弧形检测支架1,弧形检测支架1四角设置磁性滚轮2,磁性滚轮2设有编码器3和驱动马达4,驱动马达4经磁性滚轮2驱动弧形检测支架1沿支承辊辊面移动;步骤二、弧形检测支架1两侧分别间隔布置六组超声波探头6,其中,位于所述弧形检测支架1一侧居中的超声波探头6b是单晶直探头,位于所述弧形检测支架1另一侧居中的超声波探头6e是双晶直探头,其余超声波探头6a、6c、6d、6f是斜探头;步骤三、多通道超声波检测仪5分别与编码器3、驱动马达4和六组超声波探头6电连接,并采集弧形检测支架1沿支承辊辊面移动过程六组超声波探头6的检测信号;步骤四、根据被检测面长度、曲率半径、堆焊层厚度设置六组超声波探头6的扫查
路径、采样模式、记录方式,并对每个探头独立设置超声检测参数、校准灵敏度、设置报警阈值和记录阈值;步骤五、多通道超声波检测仪5根据编码器3位置及超声波探头6检测数据绘制堆焊缺陷的位置-波高曲线,位置-波高曲线记录各次弧形检测支架1经过堆焊缺陷后记录的检测数据,采用位置-波高曲线与历次检测结果比较,精确定位并比较堆焊层缺陷的微小变化,实现对堆焊缺陷的跟踪检测。
10.优选的,所述弧形检测支架1的直径与支承辊直径匹配,并且所述弧形检测支架1至少覆盖支承辊沿圆周方向的1/2辊面,所述弧形检测支架1四角同侧的超声波探头分别位于垂直支承辊轴线的上下方向并且为45
°
横波斜探头。
11.优选的,所述弧形检测支架1经驱动马达4以及磁性滚轮2沿支承辊辊面移动过程中,所述六组超声波探头6采用水或机油作为耦合剂。
12.本方法中多组探头布置在一个轻质刚性的支架上,辅以四组磁性滚轮稳定吸附于支承辊表面,采用驱动马达稳定行走,配以编码器配合记录查扫位置,并且根据现场情况可采用喷水耦合或机油耦合。根据支承辊辊身直径、辊身长度、堆焊层厚度等参数设置查扫路径、采样模式、记录方式。并对每个超声波探头独立设置具体超声检测工艺并校准灵敏度,设置报警阈值和记录阈值。
13.图2所示为弧形检测支架1通过同一堆焊缺陷位置时绘制的堆焊缺陷位置-波高曲线,通过对三次所检测的数据进行比较,可清晰的分辨出该位置处堆焊缺陷变化的情况,精确定位比较堆焊层缺陷的微小变化,实现对堆焊缺陷发展状况的把握,实现堆焊缺陷的跟踪检测。
14.本方法采用六组超声波探头实施检测,其中探头6b采用单晶直探头,用于检测30~50mm以外的堆焊层及堆焊打底层临近范围;探头6e采用双晶直探头,用于检测0至30~50mm范围内的近表面范围;探头6a、6c、6d、6f分别布置平行于支承辊轴线正方两个方向及垂直于支承辊轴线上下两个方向的45
°
斜探头;编码器和驱动马达为可记录式的多通道超声波检测仪的配套设备。
15.本方法采用与辊面轴向平行和垂直的四个45度横波斜探头结合垂直于辊面的单晶和双晶直探头,利用数字式多通道多功能超声波探头进行全方位的扫查。本方法检测效率高,自动扫查可根据超声工艺设置在临界最高扫查速度,并稳定运行,一次扫查包含6组探头全部完成,可以达到最快速度的完全检测,直接效率远高于6倍;扫查稳定性高,扫查的覆盖和角度控制完全在机械设置中体现,不会存在偏差,更不会出现由于人员素质和责任心问题造成局部漏检、覆盖率不足的问题;检测探出率高,扫查采用单/双晶直探头分段检测及四个互相垂直方向的斜探头扫查,不仅对分层开裂、气孔夹渣等缺陷反射明细,而且对于焊道错位、斜面未熔合等缺陷都能有效发现,采用可记录的超声波仪器数据分析,还能通过合成多种扫描视图组合,测量和记录缺陷长度,宽度,方向等信息,结合堆焊工艺,较容易判定缺陷性质,对缺陷支承辊后续修复和使用提供结果支撑。并且,检测结果可重现,可记录式多通道超声波仪的运用,对结果重现,结合编码器,可精确的对带状堆焊缺陷每一精确位置的波幅进行详细记录,形成位置-波高曲线,便于二次分析和历史检测数据比较,通过软件工具后期合成可进一步形成超声波的b扫描、c扫描,并且缺陷形貌直观。
16.本方法应用于对某支承辊进行缺陷跟踪检测,该支承辊辊身直径为2300mm,辊身
长度为4950mm,经堆焊修复后手工检测发现距辊身某一侧边部1200mm位置处存在一圆周方向连续缺陷,超声波检测最大当量为φ5mm,深度距表面约为50mm,轴向长度约为1500mm。为有效跟踪该缺陷在支承辊使用过程中是否发展或扩展情况,要求对该缺陷进行定期跟踪。采用本方法进行跟踪检测,并制定相应的跟踪工艺及评定要求,经连续两年跟踪,效果良好,每次均能有效的通过位置-波高曲线重现缺陷的反射情况,得出未明显发展扩展的结论,拟对该缺陷进行持续跟踪检测。
再多了解一些
本文用于企业家、创业者技术爱好者查询,结果仅供参考。