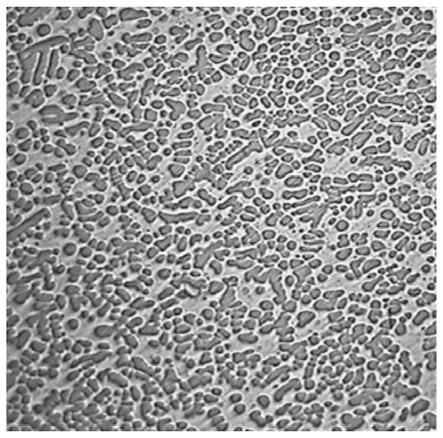
1.本发明涉及合金触头材料的制备方法,具体涉及一种利用铜铬边料制备铜铬触头自耗电极的方法。
背景技术:
2.铜铬触头(cucr触头,铬含量通常为25~50%质量)具有耐电压强度高、开断电流能力大、截流值低、抗熔焊性能好等特性,广泛应用于真空断路器中,是目前主要的真空断路器用触头材料,也是真空开关首选的触头材料。
3.铜铬触头的制备方法主要有固相烧结法、熔渗法、熔铸法和真空自耗电弧熔炼法(简称电弧熔炼法)四种,其中电弧熔炼法制造的铜铬触头综合性能最好,是目前世界上公认性能最好的铜铬触头。本领域公知,在电弧熔炼法中,自耗电极的致密度很关键,当自耗电极的致密度不够理想时,在后续自耗电极的电弧熔炼过程中,原始铜铬颗粒容易从电极脱落到熔池,从而形成产品缺陷。
4.不论采用何种方法制备铜铬触头,在加工过程中都会产生一定量的边料,这些边料主要包括车铣屑和触头废品,不同的铜铬触头制备工艺,加工过程中产生的边料量不同,如采用电弧熔炼法制造铜铬触头时,通常成品率约有80%,材料利用率约有30%(产品重量占投料总重量的比例),因此会产生大量边料,原材料资源消耗大。
5.为了节约成本,已有生产企业利用边料生产铜铬触头,如公布号为cn111593207a的发明专利,公开了一种以cucr下脚料屑制备细晶cucr触头材料的方法,包括以下步骤:(1)清洗烘干、(2)电极压制、(3)装炉、(4)电渣重熔、(5)热处理、(6)机械加工。该发明以生产过程产生的料屑为原材料制备成电极,降低了原材料的使用成本,但是由于电极仅是经过常规压制,致密度不够理想,在后续电极的电弧熔炼过程中,原始铜铬颗粒容易从电极脱落到熔池,从而形成产品缺陷。另一方面,该发明需要进行4次电渣重熔处理使致密度进一步提高,工艺较为繁琐。
6.公布号为cn113293309a的发明专利公开了一种真空自耗电弧熔炼铜铬触头材料组织优化方法,该发明中,在制备自耗电极时,需要先将铜粉和铬粉烧结得到中间合金,然后对中间合金进行熔炼、雾化制粉以得到合金粉末;再将合金粉末置于真空烧结炉中,于真空度为20~50pa,先以10~15℃/min的加热速度加热至炉体内温度达到980~1100℃,然后以15~25℃/min的加热速度加热至炉体内温度达到1100~1350℃;保温1~3h,随炉自然冷却至室温,得到自耗电极棒。一方面,该发明制备自耗电极的步骤较为繁琐,成本较高;另一方面,该发明能够获得性能优良的铜铬触头材料,得益于铜粉的来源、对所得自耗电极的热挤压和退火处理、自耗电极进行自耗熔炼时的工艺等,而不是获得自耗电极的工艺。
技术实现要素:
7.本发明要解决的技术问题是提供一种成本低、所得产品致密度高的利用铜铬边料制备铜铬触头自耗电极的方法。
8.为解决上述技术问题,本发明采用以下技术方案:
9.一种利用铜铬边料制备铜铬触头自耗电极的方法,包括以下步骤:
10.1)收集铜铬边料,破碎,清洗,干燥后得到铜铬碎料;
11.2)将所得铜铬碎料冷压成柱体形状的压块,所得压块进行热压镦实,得到铜铬镦实坯;
12.3)选取成分相同、直径相同的铜铬镦实坯按底面与底面接触的方式进行堆叠,得到所需高度的柱体形状的电极坯,用氧化铝(al2o3)纸包裹电极坯的侧面及其中一个底面,另一个底面敞开;将包裹后的电极坯按纵向且敞开端朝上的方式装入石墨舟,并在包裹后的电极坯与石墨舟的间隙填充氧化铝(al2o3)粉末;
13.4)将装有电极坯的石墨舟置于底部升降真空炉中的物料台上,启动升降机构将物料台上装有电极坯的石墨舟送入加热区,于真空条件下升温至1120~1160℃保温烧结,烧结完成后维持炉温不变,启动升降机构将物料台上的石墨舟缓慢垂直下降进入冷却区,当石墨舟全部离开加热区后停止加热;
14.5)冷却后取出石墨舟中的电极,对电极外表进行清理和修整,即得到铜铬触头自耗电极。
15.上述方法的步骤1)中,优选是按成分分别收集铜铬边料,即相同成分的铜铬边料收集在一起,以便后续制备相应成分的铜铬自耗电极。收集的铜铬边料,优先是破碎成粒度≤5mm的碎料;所述的清洗和干燥操作与现有技术相同,通常采用超声波清洗设备、金属清洗剂(具体如德国汉高铜带清洗剂p3-t7221或天跃ct-213等)将铜铬碎料清洗干净,再置于真空干燥箱于80~110℃温度下干燥。
16.上述方法的步骤2)中,采用现有常规冷压设备(如液压机)将铜铬碎料冷压成柱体形状的压块,压块的尺寸根据需要确定,优选是将铜铬碎料冷压成直径为60~70mm、高度为60~100mm的柱体形状压块。冷压优选是在压力为1000~1200mpa的条件下进行,保压时间优选为10~30s。
17.上述方法的步骤2)中,通过热压镦实以进一步提高压块的致密度。采用现有常规技术对压块进行热压镦实,本技术中优选热压镦实在真空条件下进行,具体可以采用真空热压机进行热压镦实;进一步优选热压镦实在真空度读数≤0.02pa、温度为900~970℃、压力为80~120mpa的条件下进行,保压时间优选为60~90s。
18.上述方法的步骤3)中,在将铜铬镦实坯按底面与底面接触且侧面对齐的方式进行堆叠,根据需要确定柱体形状电极坯的高度。当压块的直径为60~70mm、高度为60~100mm时,电极坯的高度优选为900~1000mm。该步骤中涉及的石墨舟,其内径优选是较电极坯的直径大10~15mm,其深度较电极坯高出10~20mm。在包裹后的电极坯与石墨舟之间间隙填充的氧化铝粉末的粒度优选为-100目。本技术中采用氧化铝纸紧密包裹电极坯并使用氧化铝粉末填充电极坯与石墨舟之间的间隙,使电极坯在高于铜熔点(铜的熔点为1083℃,铬的熔点为1907℃)的温度下进行液相烧结时不变形,铜组分不流失从而确保电极成分不变。
19.上述方法的步骤4)中,优选是在真空度读数为≤0.01pa的条件下进行保温烧结,保温烧结的时间优选为30~60min。烧结完成后,石墨舟必须以垂直下降的方式进入冷却区,垂直下降的速率优选为2~5mm/min。本技术中电极坯在高于铜熔点的温度下进行液相烧结,一方面,液相烧结使铜铬碎料的颗粒之间真正烧结成为一个整体,也使各镦实坯熔接
成为一个整体;之后结合在保持炉温的前提下采用垂直且缓慢下降的方式将石墨舟由加热区过渡到冷却区,使电极坯中正在冷却凝固的铜得到及时和充分的补缩,从而消除因补缩不足而产生的孔洞(现有技术中直接在真空烧结炉中进行液相烧结,由于烧结完成后铜铬熔液一直处于同样的温度环境中,同步进行冷却凝固(随炉冷却),因而导致正在冷却凝固的铜得不到及时而良好的补缩而产生孔洞,进而导致自耗电极致密度不理想),使烧结后的电极成为致密体,且电极的成分符合要求,也使各镦实坯熔接成为一个整体得到保障。
20.本发明所述方法中,在进入烧结之前的镦实坯的相对密度应≥93%,这样才能使后续烧结得到的自耗电极中铬的含量达到国标要求。而仅只采用冷压步骤通常难以使压块达到高于93%的相对密度。
21.上述方法的步骤5)中,对电极外表进行常规的清理和修整。
22.与现有技术相比,本发明的特点在于:
23.1.采用氧化铝纸紧密包裹电极坯并使用氧化铝粉末填充电极坯与石墨舟之间的间隙,使电极坯在高于铜熔点的温度下进行液相烧结时不变形,铜组分不流失从而确保电极成分不变。
24.2.将电极坯在高于铜熔点的温度下进行液相烧结,一方面,液相烧结使铜铬碎料的颗粒之间真正烧结成为一个整体,也使各镦实坯熔接成为一个整体;之后结合在保持炉温的前提下采用垂直且缓慢下降的方式将石墨舟由加热区过渡到冷却区,使电极坯中正在冷却凝固的铜得到及时而充分的补缩,从而消除因补缩不足而产生的孔洞,使烧结后的电极成为致密体,电极的成分符合要求,也使各镦实坯熔接成为一个整体得到保障。
25.3.采用本发明所述方法制备的自耗电极致密度高(相对密度≥99.7%)且成分均匀,将其用于真空自耗电弧熔炼时,可大幅提高电弧熔炼的稳定性,且所制得铜铬触头产品的金相组织均匀,铜基体上铬颗粒细小而均匀,产品力学物理性能优良,综合性能优良,产品的成品率达到92%以上。
26.4.本发明所述方法采用铜铬边料为原料,节约了金属铜、铬资源,也避免了对环境的污染,成本低且方法简单易操作。
附图说明
27.图1为本发明所述方法中涉及的底部升降真空炉的炉体部分的结构示意图。
28.图2为本发明实施例1制备的铜铬25自耗电极的实物照片。
29.图3为采用本发明实施例1制备的铜铬25自耗电极经真空自耗电弧熔炼制得的铜铬25触头产品的的金相组织图。
30.图4为采用本发明实施例2制备的铜铬40自耗电极经真空自耗电弧熔炼制得的铜铬40触头产品的的金相组织图。
31.图5为采用本发明实施例3制备的铜铬50自耗电极经真空自耗电弧熔炼制得的铜铬50触头产品的的金相组织图。
32.图中标号为:
33.1上炉盖,2加热区,3隔热板,4冷却区,5物料台,6下炉盖,7升降机构,8物料。
具体实施方式
34.为了更好的解释本发明的技术方案,下面结合实施例对本发明作进一步详细的描述,但本发明的实施方式不限于此。
35.本发明所述方法中涉及的底部升降真空炉与现有常规的立式真空烧结炉一样具有在真空或气氛保护条件下对物料进行高温烧结,也具有对炉体内环境进行冷却等相应功能,与常规立式真空烧结炉的区别仅在于:炉体内通过隔热板分隔成上下两部分,其中上部为加热区,下部为冷却区;炉体中物料台的底部安装有升降机构,通过升降机构的控制实现物料台在加热区和冷却区之间垂直方向的往复运动,升降机构的实现为现有常规的导轨、滑块和液压缸的配合。下面通过图1简单描述底部升降真空炉的炉体部分。如图1所示,炉体包括上炉盖1、下炉盖6和介于上炉盖和下炉盖之间的炉膛,炉膛的中部设置有隔热板3,将炉膛分隔成上下两部分,其中上部为加热区2,下部为冷却区4;炉膛的下部设置有物料台5,物料台5的底部安装有升降机构7,通过升降机构的控制实现物料台5在加热区2和冷却区4之间在垂直方向上的往复运动,升降机构7的实现为现有常规的导轨、滑块和液压缸的配合;隔热板3上开设有通孔,该通孔的开设位置正对于物料台5且通孔的面积稍小于物料台5的面积,如此当物料台5上的物料8进入加热区2进行加热时,物料台5本身也就将隔热板3上的通孔完全封闭,在完成烧结后,启动升降机构7将物料台5上物料8从加热区2缓慢垂直下降至冷却区4。
36.实施例1
37.1)收集铜铬25边料(铬含量:25%质量分数),将铜铬25边料破碎成小于5mm的碎料,采用超声波清洗设备、金属清洗剂将铜铬25碎料清洗干净,置于真空干燥箱于80℃温度下烘干,得到铜铬25碎料;
38.2)使用液压机将铜铬25碎料冷压成直径为高度为100mm的柱体形状的压块,冷压参数为:压力为1000mpa,保压时间10s;所得压块的相对密度为90%(采用阿基米德排水法进行检测,下同);使用真空热压机对铜铬25压块进行热压镦实,热压参数为:真空度读数≤0.02pa,温度900℃,压力80mpa,保压时间90s,经过热镦实后,得到柱体形状的铜铬25镦实坯,尺寸为:直径为高度为90mm;所得铜铬25镦实坯相对密度为99%;
39.3)将铜铬25镦实坯按底面与底面接触(镦实坯间紧密接触不留缝隙)且侧面对齐的方式进行堆叠,得到长度为990mm的柱体形状的电极坯,使用厚度为0.5mm的氧化铝纸紧密包裹电极坯的侧面及其中一个底面,另一个底面敞开;将紧密包裹后的电极坯按纵向且敞开端朝上的方式装入石墨舟(石墨舟外径为内径70~75mm,深度1010mm),并在包裹后的电极坯与石墨舟的间隙填充-100目的氧化铝粉末;
40.4)将装有电极坯的石墨舟垂直放置,置于底部升降真空炉中的物料台上,启动升降机构将物料台上装有电极坯的石墨舟送入加热区,于真空条件下进行烧结,烧结参数为:真空度读数为≤0.01pa,烧结温度1120℃,保温时间30min;保温完后,维持炉温不变,启动升降机构使电极坯缓慢垂直下降进入冷却区,下降速度为5mm/min,当石墨舟全部离开加热区后停止加热;
41.5)冷却后取出石墨舟中的电极,将电极外表的氧化铝清理干净,修整电极外表,得到致密而成分均匀的铜铬25自耗电极。所得铜铬25自耗电极的实物照片如图2所示,经检
测,其相对密度为99.85%,铬含量为24.7%(国标gb/t26867-2011要求铜铬25触头中铬的含量为23~27%)。
42.将所制得的铜铬25自耗电极用于真空自耗电弧熔炼,熔炼电压23v,熔炼电流2000a,得到铜铬25铸锭,制取铜铬25触头产品,成品率达到94%,所得铜铬25触头产品的金相组织如图3所示。
43.对比例1-1
44.重复实施例1,不同的是:步骤4)中在保温完后即停止加热,随炉冷却(相当于是烧结后将装有电极坯的石墨舟垂直放置后置于常规的立式真空烧结炉中进行烧结,烧结完成后随炉冷却)。冷却后取出石墨舟中的电极,将电极外表的氧化铝清理干净,修整电极外表。
45.从修整后电极的外表可见,电极有较多孔洞,相邻镦实坯之间开裂,电极不合格,电极不能满足自耗电弧熔炼要求(因为在保温完后停止加热随炉冷却的过程中,电极中的各部位同时冷却凝固收缩,均得不到良好的补缩,从而产生孔洞,并造成镦实坯之间开裂)。
46.对比例1-2
47.重复实施例1,不同的是:步骤2)中省略采用真空热压机对铜铬25压块进行热压镦实的操作;直接使用铜铬25压块进行后续步骤3)至步骤5)。
48.经检测,修整后的电极的相对密度为99.8%,铬含量为22.1%。虽然所得电极具有良好的致密度,但由于其铬含量不符合要求(在电极坯缓慢垂直下降过程中,电极坯中正在冷却凝固的铜得到及时而充分的补缩,因此电极的致密度高;但由于在进入烧结工序之前压块的相对密度较低,孔隙度高,在冷却凝固补缩过程中,压块中下部的孔隙被外来的铜液充实,从而致使烧结所得电极中下部铜组分增加,铬含量降低;而所得电极的顶端部分则仅含少量甚至极少量的铜,基本上均为铬),因而不合格。
49.实施例2
50.1)收集铜铬40边料(铬含量:40%质量分数),将铜铬40边料破碎成小于5mm的碎料,采用超声波清洗设备、中性金属清洗剂将铜铬40碎料清洗干净,置于真空干燥箱于110℃温度下烘干,得到铜铬40碎料;
51.2)使用液压机将铜铬40碎料冷压成直径为高度为80mm的柱体形状的压块,冷压参数为:压力为1200mpa,保压时间30s;所得压块的相对密度为87%;使用真空热压机对铜铬40压块进行热压镦实,热压参数为:真空度读数≤0.02pa,温度970℃,压力120mpa,保压时间60s,经过热镦实后,得到柱体形状的铜铬40镦实坯,尺寸为:直径为高度为70mm;所得铜铬40镦实坯相对密度为98%;
52.3)将铜铬40镦实坯按底面与底面接触(镦实坯间紧密接触不留缝隙)且侧面对齐的方式进行堆叠,得到长度为980mm的柱体形状的电极坯,使用厚度为0.5mm的氧化铝纸紧密包裹电极坯的侧面及其中一个底面,另一个底面敞开;将紧密包裹后的电极坯按纵向且敞开端朝上的方式装入石墨舟(石墨舟外径为内径80~85mm,深度1000mm),并在包裹后的电极坯与石墨舟的间隙填充-100目的氧化铝粉末;
53.4)将装有电极坯的石墨舟垂直放置,置于底部升降真空炉中的物料台上,启动升降机构将物料台上装有电极坯的石墨舟送入加热区,于真空条件下进行烧结,烧结参数为:真空度读数为≤0.01pa,烧结温度1140℃,保温时间60min;保温完后,维持炉温不变,启动
下降机构使电极坯缓慢垂直下降进入冷却区,下降速度为3mm/min,当石墨舟全部离开加热区后停止加热;
54.5)冷却后取出石墨舟中的电极,将电极外表的氧化铝清理干净,修整电极外表,得到致密而成分均匀的铜铬40自耗电极。经检测,所得铜铬40自耗电极的相对密度为99.75%,铬含量为39.1%(国标gb/t26867-2011要求铜铬40触头中铬的含量为37~42%)。
55.将所制得的铜铬40自耗电极用于真空自耗电弧熔炼,熔炼电压24v,熔炼电流2900a,得到铸锭,制取铜铬40触头产品,成品率达到92%,所得铜铬40触头产品的金相组织如图4所示。
56.实施例3
57.1)收集铜铬50边料(铬含量:50%质量分数),将铜铬50边料破碎成小于5mm的碎料,采用超声波清洗设备、中性金属清洗剂将铜铬50碎料清洗干净,置于真空干燥箱于110℃温度下烘干,得到铜铬50碎料;
58.2)使用液压机将铜铬50碎料冷压成直径为高度为60mm的柱体形状的压块,冷压参数为:压力为1200mpa,保压时间30s;所得压块的相对密度为83%;使用真空热压机对铜铬50压块进行热压镦实,热压参数为:真空度读数≤0.02pa,温度970℃,压力120mpa,保压时间90s,经过热镦实后,得到柱体形状的铜铬50镦实坯,尺寸为:直径为高度为51mm;所得铜铬50镦实坯相对密度为96%;
59.3)将铜铬50镦实坯按底面与底面接触(镦实坯间紧密接触不留缝隙)且侧面对齐的方式进行堆叠,得到长度为918mm的柱体形状的电极坯,使用厚度为0.5mm的氧化铝纸紧密包裹电极坯的侧面及其中一个底面,另一个底面敞开;将紧密包裹后的电极坯按纵向且敞开端朝上的方式装入石墨舟(石墨舟外径为内径80~85mm,深度938mm),并在包裹后的电极坯与石墨舟的间隙填充-100目的氧化铝粉末;
60.4)将装有电极坯的石墨舟垂直放置,置于底部升降真空炉中的物料台上,启动升降机构将物料台上装有电极坯的石墨舟送入加热区,于真空条件下进行烧结,烧结参数为:真空度读数为≤0.01pa,烧结温度1160℃,保温时间60min;保温完后,维持炉温不变,启动下降机构使电极坯缓慢垂直下降进入冷却区,下降速度为2mm/min,当石墨舟全部离开加热区后停止加热;
61.5)冷却后取出石墨舟中的电极,将电极外表的氧化铝清理干净,修整电极外表,得到致密而成分均匀的铜铬50自耗电极。经检测,所得铜铬50自耗电极的相对密度为99.8%,铬含量为47.7%(国标gb/t26867-2011要求铜铬50触头中铬的含量为47~52%)。
62.将所制得的铜铬50自耗电极用于真空自耗电弧熔炼,熔炼电压27v,熔炼电流3100a,得到铸锭,制取铜铬50触头产品,成品率达到93%,所得铜铬50触头产品的金相组织如图5所示。
再多了解一些
本文用于企业家、创业者技术爱好者查询,结果仅供参考。