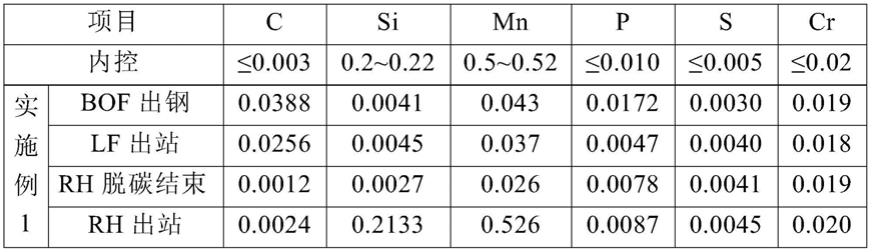
1.本发明涉及钢铁冶金技术领域,特别涉及一种低硫低磷超低碳钢的全流程冶炼方法。
背景技术:
2.对于绝大多数钢种而言,硫和磷属于有害杂质元素。硫容易使钢材产生热脆性,降低钢材的延展性和韧性,容易造成裂纹,同时还会降低钢材的耐腐蚀性。磷虽然能提高钢的强度,但是随着磷含量的增加,钢的塑性和韧性会大幅降低,容易使钢发生冷脆,同时还会降低钢的焊接性能。所以钢中硫和磷的含量需尽量控制较低范围内,才能保证钢材的质量不受影响。
3.目前大部分钢铁企业都会采取各种工艺冶炼低硫低磷钢,包括kr机械搅拌法脱硫、单喷颗粒镁脱硫、使用低磷矿石冶炼铁水、向铁水内加脱磷剂、转炉吹炼脱磷等。在高炉铁水出炉后,转炉氧枪吹炼脱磷是一种效果明显的脱磷方法,该方法利用转炉内部的氧化环境、适宜的钢液温度和充分的渣钢搅拌,及加入大量石灰和白云石等物料造高碱度氧化渣,可以实现较高的脱磷率。
4.但是在转炉吹炼末期,氧枪吹氧脱碳时容易提高钢液温度,发生回磷现象,并且,若是转炉冶炼过程控制不当或者出钢过程下渣严重,也会导致钢液中磷含量超标。当前控制钢包中钢液磷高的常规方法是返回转炉进行二次处理,这严重影响了生产节奏,大大增加了冶炼成本。而且在连续生产中,转炉出站时的钢液成分和温度也难以稳定控制在较窄范围内。而在冶炼超低碳钢时,钢液自转炉出站后还要经过rh真空炉进行脱碳处理。rh炉对于钢液进站条件要求严格,钢液温度和成分的要求范围较窄,若是钢液不能满足条件,只能回返转炉或者调度到其它工序。因此,单单通过铁水
→
kr炉
→
转炉
→
rh炉的工艺路线,难以连续稳定地生产出低硫低磷超低碳钢,并且还会增大转炉和rh炉的冶炼压力大,造成生产成本升高。
5.因此,当前亟需一种工艺过程连续稳定、生产成本较低的低硫低磷超低碳钢的全流程冶炼方法。
技术实现要素:
6.本发明的目的是提供一种工艺过程连续稳定、生产成本较低的低硫低磷超低碳钢的全流程冶炼方法,通过按照kr铁水预处理
→
转炉冶炼
→
lf精炼
→
rh真空处理的工艺流程,并严格从原料和工艺两方面限制和减少钢液中的硫和磷含量,从而生产各类优质的低硫低磷超低碳钢,保证低碳钢的硫和磷含量达到目标要求。
7.为解决上述技术问题,本发明提供了一种低硫低磷超低碳钢的全流程冶炼方法,包括如下步骤:
8.kr铁水预处理,铁水以≥1300℃的温度进站,对铁水扒渣、加脱硫剂搅拌脱硫,使铁水出站时铁水中[s]≤0.001%,温度≥1230℃;
[0009]
转炉冶炼,冶炼结束时控制钢液中[c]≤0.05%、[s]≤0.005%、[p]≤0.020%,温度控制在1660~1680℃出钢,出钢时不进行脱氧合金化,使钢液中氧含量控制在0.080~0.100%;
[0010]
lf精炼,首次向钢液底吹氩气,并向钢液加石灰和萤石造脱磷渣脱磷,加完料后将钢液加热到1500-1700℃,第二次向钢液底吹氩气,将钢液脱磷至[p]≤0.005%,最后将钢液升温送往rh炉;
[0011]
rh真空处理,先对钢液脱碳处理至[c]≤0.0015%,然后对钢液脱氧合金化至[o]≤0.0030。
[0012]
进一步地,所述对铁水扒渣、加脱硫剂搅拌脱硫,包括:
[0013]
铁水进站后先扒去高炉渣,铁水裸露面达到90%,然后用搅拌头以60~80r/min的转速搅拌铁水,搅拌时加入8~12kg/t铁的脱硫剂脱硫,加完脱硫剂后,以90~95r/min的转速搅拌10~12min,然后停止搅拌进行二次扒渣,铁水裸露面达到90%。
[0014]
进一步地,所述脱硫剂的平均粒度为1.0mm,其中,粒度在0.5~1.5mm之间占80%以上,粒度小于0.5mm和大于1.5mm的均在10%以下;所述脱硫剂由石灰和萤石按5:1~15:1的质量比组成,所述石灰的cao≥90%、s≤0.030%,烧损≤2%,活性度≥320ml,所述萤石的caf2≥85%、s≤0.2%、h2o≤1%、sio2≤4%。
[0015]
进一步地,所述转炉冶炼时采用全铁冶炼或者配加5-15%的s≤
[0016]
0.01%、p≤0.030%的废钢冶炼,冶炼使用s≤0.0130%的石灰、s≤0.13%的白云石和s≤0.20%的萤石造渣,采用双渣法操作,控制炉渣碱度在3.2~3.5。
[0017]
进一步地,所述转炉出钢时控制下渣量≤50mm,出钢量时钢包净空控制在300~500mm,钢包全程底吹氩气搅拌,底吹氩气量控制在1~1.5nl/min
·
t钢。
[0018]
进一步地,所述lf精炼中首次向钢液底吹氩气的总流量控制在5~12nl/min
·
t钢,第二次向钢液底吹氩气的总流量控制在8~20nl/min
·
t钢,第二次向钢液底吹氩气的时间为3-8min。
[0019]
进一步地,所述lf精炼中向钢液加石灰是分批次加入,每批次石灰加入量为100~150kg,石灰总加入量控制在8~10kg/t钢,所述萤石的总加入量与石灰总加入量质量比控制在1:5~1:3。
[0020]
进一步地,所述rh真空处理时脱碳处理采用深真空控制模式的深脱碳处理,环流氩气量控制在500~1000nl/min,真空处理15~20min。
[0021]
进一步地,所述rh真空处理时对钢液脱氧合金化是向钢液加入铝、硅铁、锰或其它金属,脱氧合金化时钢液纯脱气循环6~8min后破真空出站,最后送往连铸工序。
[0022]
进一步地,所述低硫低磷超低碳钢以质量百分比计,包括c≤0.003%、si 0.20~0.22%、mn 0.50~0.52%、p≤0.010%、s≤0.005%、cr≤0.02%。
[0023]
本发明提供的一种低硫低磷超低碳钢的全流程冶炼方法,依次按照kr铁水预处理
→
转炉冶炼
→
lf精炼
→
rh真空处理的工艺过程,在kr铁水预处理中,对铁水扒渣与搅拌脱硫,将出站时铁水中[s]控制在0.001%以下。在转炉冶炼过程中转炉出钢时进行留氧操作,保持钢液中的高氧环境和钢渣的氧化状态,然后钢液进入lf炉。在lf精炼过程中,不进行脱氧合金化,通过加热钢液、加入石灰和萤石造高碱度氧化性渣及大气量底吹氩气搅拌钢液,促使脱磷渣和钢液充分接触脱磷,提高脱磷反应的效率,使钢液中的[p]大量脱到渣中,将
钢液中[p]脱至0.005%以下,然后钢液送到rh炉。在rh真空处理中,钢液在真空槽内循环,发生各类冶金反应,此处理过程中钢渣基本不与钢液发生反应,钢渣中[p]难以返回钢液中,可以保证钢液中[p]在目标范围内,同时,rh真空处理还对钢液脱碳处理和脱氧合金化,将钢液中[c]脱到0.003%以下、[o]脱至0.0030%以下。本发明在每个工艺步骤中严格控制钢液中碳、硫、磷及氧等重要元素的含量,以使碳硫磷等元素的含量控制在目标范围内,最终可以冶炼出c≤0.003%、s≤0.008%、p≤0.010%的高洁净度的低硫低磷超低碳钢,从而可以保证碳、硫和磷含量达到低硫低磷超低碳钢的目标要求。同时,本发明提供的一种低硫低磷超低碳钢的全流程冶炼方法,工艺过程连续稳定、生产成本也较低,具有较好的应用价值,其应用前景良好。
附图说明
[0024]
图1为本发明实施例提供的一种低硫低磷超低碳钢的全流程冶炼方法流程图。
具体实施方式
[0025]
参见图1,本发明实施例提供的一种低硫低磷超低碳钢的全流程冶炼方法,依次按照kr铁水预处理
→
转炉冶炼
→
lf精炼
→
rh真空处理的工艺流程,最终可以冶炼得到c≤0.003%、s≤0.008%、p≤0.010%的低硫低磷超低碳钢。该方法的具体冶炼过程如下:
[0026]
步骤1)kr铁水预处理,将铁水进站温度控制在1300℃以上,进站后先扒去高炉渣,使铁水裸露面达到90%。然后使用搅拌头以60~80r/min的转速对铁水搅拌,搅拌时加入8~12kg/t铁的脱硫剂对铁水脱硫。加料完成后,控制搅拌头以90~95r/min的转速搅拌10~12min,然后提起搅拌头对铁水进行二次扒渣,使铁水裸露面达到90%。铁水出站时控制铁水中[s]≤0.001%,温度≥1230℃。其中,脱硫剂的平均粒度1.0mm,其中,粒度在0.5~1.5mm之间占80%以上,粒度小于0.5mm和大于1.5mm的均《10%。其中,脱硫剂由优质的低硫活性石灰和萤石组成,活性石灰和萤石的质量比控制在按5:1~15:1。其中,石灰的cao≥90%、s≤0.030%,烧损≤2%,活性度≥320ml,所述萤石的caf2≥85%、s≤0.2%、h2o≤1%、sio2≤4%。
[0027]
步骤2)转炉冶炼,采用全铁冶炼或者配加5-15%的s≤0.01%、p≤0.030%的优质低硫低磷废钢进行冶炼,冶炼中使用s≤0.0130%的石灰、s≤0.13%的白云石和s≤0.20%的萤石进行造渣,转炉冶炼中不添加铁矿石、渣粒、焦粉等高硫原料,采用双渣法操作,将炉渣碱度控制在3.2~3.5。转炉冶炼结束时将钢液成分控制在[c]≤0.05%、[s]≤0.005%、[p]≤0.020%,温度控制在1660~1680℃出钢。
[0028]
转炉出钢时保证出钢口状况良好,钢流圆整,严格执行挡渣操作,控制下渣量小于50mm。并且出钢时不进行脱氧合金化,将钢液中氧含量控制在0.080~0.100%。钢包全程底吹氩气搅拌,在钢包透气性良好的情况下,底吹氩气总气量控制在1~1.5nl/min
·
t钢,使渣面微动,同时,控制出钢量,使钢包净空达到300~500mm。
[0029]
步骤3)lf精炼,钢液在lf炉进行升温和深脱磷操作,不进行脱氧合金化。钢液到站后先底吹氩气,并采用微正压操作,底吹氩气的总流量控制在5~12nl/min
·
t钢,然后向钢液中加石灰和萤石造脱磷渣,造渣石灰分批次加入,每批次石灰加入量为100~150kg,石灰总加入量控制在8~10kg/t钢,萤石的总加入量按与石灰总加入量的质量比1:5~1:3进行
控制。加造渣料结束后,降下电极并对电极通电加热钢液,当温度升到1500-1700℃时,停止通电加热。然后再次向钢液中底吹大气量氩气搅拌3-10min,底吹氩气的总流量控制在8~20nl/min
·
t钢,以促进渣钢之间的界面反应,提高脱磷效率,在底吹氩气对钢液搅拌时注意时刻观察钢渣搅拌情况,避免炉渣溢出钢包。停止底吹氩气后,取样检测,当钢液脱磷至[p]≤0.005%后,再次对电极通电使电极对钢液加热,当钢液温度升到目标温度后送往rh炉。
[0030]
步骤4)rh真空处理,rh真空处理过程主要是对钢液脱碳和脱氧合金化。在温度和成分符合要求的钢液进站后,先采用深真空控制模式对钢液进行深脱碳处理,脱碳处理过程中保证环流氩气量,氩气流量根据钢液循环效果随时调整,前期碳氧反应剧烈时使用较小氩气流量,中后期碳氧反应减缓和钢液循环减弱时加大氩气流量,环流氩气量整体控制在500~1000nl/min。对钢液进行深脱碳处理15~20min,将钢液中[c]脱到0.0015%以下后,再向钢液中加入铝粒、硅铁、锰或其它金属进行脱氧合金化,将钢液中[o]脱到0.0030%以下。同时根据不同低碳钢成分的要求,可在此时向钢液中添加其它合金使钢液成分达到目标要求,并将钢液纯脱气循环6~8min使钢液混合均匀。最后破真空出站,在钢液温度和成分达到目标范围后,送往连铸工序。
[0031]
下面以成分满足c≤0.003%、si 0.20~0.22%、mn 0.50~0.52%、p≤0.010%、s≤0.005%、cr≤0.02%的超低碳钢的冶炼为例,对本发明实施例提供的一种低硫低磷超低碳钢的全流程冶炼方法做具体说明。
[0032]
实施例1
[0033]
kr铁水预处理:利用kr搅拌法处理50t铁水,进站温度1310℃,首先扒去高炉渣,然后添加活性石灰500kg、萤石50kg,搅拌头转速为95r/min,搅拌12min后再扒去脱硫渣,铁水裸露面达到90%,出站时铁水中[s]是0.0005%,铁水温度1235℃。
[0034]
转炉冶炼:转炉兑铁,添加5t优质废钢,冶炼过程中氧气流量和氧枪高度视吹炼情况变化,共加入石灰1300kg、白云石500kg和萤石150kg造高碱度渣,采用双渣法操作;出钢时钢液终点温度1660℃,钢流圆整,执行挡渣操作;钢包全程底吹氩气使渣面微动,净空达到400mm,出站温度1600℃。
[0035]
lf精炼:钢液进站后,先打开底吹氩气,采用微正压操作,测温取样,钢液温度1590℃,然后共加入石灰500kg和萤石150kg,分成4批加入钢液,再送电埋弧加热10min,钢液温度升到1635℃,底吹氩气搅拌钢液6分钟,氩气流量在750nl/min;之后减小氩气流量,测温取样,钢中[p]达到0.0047%,再次通电升温,温度达到1690℃时钢液出站吊往rh炉。
[0036]
rh真空精炼:钢液进站后测温定氧并取样分析,顶升钢包至浸渍管插入钢液700mm时开始抽真空,真空处理1min时加入80kg铝粒,真空处理6min时真空度达到85pa,环流氩气量控制在750~800nl/min;真空处理15min时,钢中[c]达到12ppm;然后加入200kg硅铁和250kg金属锰进行脱氧合金化,钢液纯脱气循环8min后破真空出站,测温取样,出站温度在1625℃,最后送往连铸工序。本发明实施例的冶炼过程中钢液在部分工序中的化学成分及质量百分比如表1所示。
[0037]
实施例2
[0038]
kr铁水预处理:利用kr搅拌法处理45t铁水,进站温度1320℃,首先扒去高炉渣,然后添加活性石灰400kg、萤石40kg,搅拌头转速为90r/min,搅拌10min后再扒去脱硫渣,铁水
裸露面达到95%,出站时铁水中[s]是0.0006%,铁水温度1230℃。
[0039]
转炉冶炼:转炉兑铁,添加4.5t优质废钢,冶炼过程中氧气流量和氧枪高度视吹炼情况变化,共加入石灰1200kg、白云石500kg和萤石150kg造高碱度渣,采用双渣法操作;出钢时钢液温度1670℃,钢流圆整,执行挡渣操作;钢包全程底吹氩气使渣面微动,净空达到450mm,出站温度1610℃。
[0040]
lf精炼:钢液进站后,先打开底吹氩气,采用微正压操作,测温取样,钢液温度1600℃,然后共加入石灰450kg和萤石150kg,分成4批加入钢液,再送电埋弧加热10min,钢液温度升到1639℃,底吹氩气搅拌钢液6分钟,氩气流量在800nl/min;之后减小氩气流量,测温取样,钢中[p]达到0.0039%,再次通电升温,温度达到1695℃时钢液出站吊往rh炉。
[0041]
rh真空精炼:钢液进站后测温定氧并取样分析,顶升钢包至浸渍管插入钢液700mm时开始抽真空,真空处理1min时加入75kg铝粒,真空处理6min时真空度达到90pa,环流氩气量控制在750~800nl/min;真空处理15min时,钢中[c]达到14ppm;然后加入185kg硅铁和230kg金属锰进行脱氧合金化,钢液纯脱气循环7min后破真空出站,测温取样,出站温度在1629℃,最后送往连铸工序。本发明实施例的冶炼过程中钢液在部分工序中的化学成分及质量百分比如表1所示。
[0042]
实施例3
[0043]
kr铁水预处理:利用kr搅拌法处理52t铁水,进站温度1300℃,首先扒去高炉渣,然后添加活性石灰500kg、萤石50kg,搅拌头转速为95r/min,搅拌12min后再扒去脱硫渣,铁水裸露面达到95%,出站时铁水中[s]是0.0003%,铁水温度1233℃。
[0044]
转炉冶炼:转炉兑铁,添加5t优质废钢,冶炼过程中氧气流量和氧枪高度视吹炼情况变化,共加入石灰1300kg、白云石400kg和萤石160kg造高碱度渣,采用双渣法操作;出钢时钢液温度1680℃,钢流圆整,执行挡渣操作;钢包全程底吹氩气使渣面微动,净空达到400mm,出站温度1620℃。
[0045]
lf精炼:钢液进站后,先打开底吹氩气,采用微正压操作,测温取样,钢液温度1605℃,然后共加入石灰600kg和萤石200kg,分成4批加入钢液,再送电埋弧加热8min,钢液温度升到1625℃,底吹氩气搅拌钢液6分钟,氩气流量在750nl/min;之后减小氩气流量,测温取样,钢中[p]达到0.0040%,再次通电升温,温度达到1679℃时钢液出站吊往rh炉。
[0046]
rh真空精炼:钢液进站后测温定氧并取样分析,顶升钢包至浸渍管插入钢液750mm时开始抽真空,真空处理1min时加入75kg铝粒,真空处理6min时真空度达到80pa,环流氩气量控制在750~800nl/min;真空处理15min时,钢中[c]达到10ppm;然后加入220kg硅铁和250kg金属锰进行脱氧合金化,钢液纯脱气循环8min后破真空出站,测温取样,出站温度在1620℃,最后送往连铸工序。本发明实施例的冶炼过程中钢液在部分工序中的化学成分及质量百分比如表1所示。
[0047]
实施例4
[0048]
kr铁水预处理:利用kr搅拌法处理55t铁水,进站温度1330℃,首先扒去高炉渣,然后添加活性石灰600kg、萤石60kg,搅拌头转速为95r/min,搅拌12min后再扒去脱硫渣,铁水裸露面达到90%,出站时铁水中[s]是0.0008%,铁水温度1240℃。
[0049]
转炉冶炼:全铁冶炼,不添加废钢,冶炼过程中氧气流量和氧枪高度视吹炼情况变化,共加入石灰1500kg、白云石500kg和萤石200kg造高碱度渣,采用双渣法操作;出钢时钢
液温度1680℃,钢流圆整,执行挡渣操作;钢包全程底吹氩气使渣面微动,净空达到300mm,出站温度1620℃。
[0050]
lf精炼:钢液进站后,先打开底吹氩气,采用微正压操作,测温取样,钢液温度1612℃,然后共加入石灰700kg和萤石250kg,分成5批加入钢液,再送电埋弧加热8min,钢液温度升到1621℃,底吹氩气搅拌钢液8分钟,氩气流量在750nl/min;之后减小氩气流量,测温取样,钢中[p]达到0.0038%,再次通电升温,温度达到1672℃时钢液出站吊往rh炉。
[0051]
rh真空精炼:钢液进站后测温定氧并取样分析,顶升钢包至浸渍管插入钢液700mm时开始抽真空,真空处理1min时加入85kg铝粒,真空处理6min时真空度达到78pa,环流氩气量控制在750~800nl/min;真空处理15min时,钢中[c]达到12ppm;然后加入240kg硅铁和280kg金属锰进行脱氧合金化,钢液纯脱气循环6min后破真空出站,测温取样,出站温度在1631℃,最后送往连铸工序。本发明实施例的冶炼过程中钢液在部分工序中的化学成分及质量百分比如表1所示。
[0052]
表1
[0053][0054][0055]
从表1可以看出,本发明实施例提供的一种低硫低磷超低碳钢的全流程冶炼方法,在每个工艺步骤中严格控制钢液中碳、硫、磷等重要元素的含量,以使碳硫磷等元素的含量控制在目标范围内,最终可以冶炼出c≤0.003%、s≤0.008%、p≤0.010%的高洁净度的低硫低磷超低碳钢,从而可以保证碳、硫和磷含量达到了低硫低磷超低碳钢的目标要求。
[0056]
最后所应说明的是,以上具体实施方式仅用以说明本发明的技术方案而非限制,
尽管参照实例对本发明进行了详细说明,本领域的普通技术人员应当理解,可以对本发明的技术方案进行修改或者等同替换,而不脱离本发明技术方案的精神和范围,其均应涵盖在本发明的权利要求范围当中。
再多了解一些
本文用于企业家、创业者技术爱好者查询,结果仅供参考。