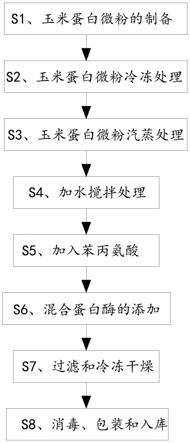
1.本发明涉及玉米蛋白技术领域,具体为一种提高玉米蛋白消化率的工艺。
背景技术:
2.玉米蛋白粉是玉米籽粒经食品工业生产淀粉或酿酒工业提纯后的副产品,其蛋白质营养成分丰富,并具有特殊的味道和色泽,可用作饲料使用,与饲料工业常用的鱼粉、豆饼比较,资源优势明显,饲用价值高,不含有毒有害物质,不需进行再处理,可直接用作蛋白原料,由于作为饲料出售价格低廉,部分企业以玉米蛋白粉为原料,从中提取玉米黄素和玉米朊,开发成功能性食品,附加值大大提高。
3.玉米中含有一定量的蛋白质,其商品形式为玉米蛋白粉或玉米浆,玉米蛋白以醇溶蛋白为主,难于被生物体消化吸收,现代科学研究表明,小分子肽比等量的氨基酸具有更高的生物活性和营养价值,肽类和氨基酸几乎均可以通过小肠绒毛上皮细胞完全被吸收利用,进入到血液中,然后输送到生物体的各个部位,而蛋白质则必须经过消化后才能被吸收利用,肽类被生物体吸收速度快于等量的游离氨基酸,大大快于等量的蛋白质,如果将玉米蛋白转化为小分子肽,将大大提高玉米蛋白的利用率,彻底解决了玉米蛋白不易溶于水,难于消化吸收的问题,为此,我们提出了一种提高玉米蛋白消化率的工艺来解决上述问题。
技术实现要素:
4.针对现有技术的不足,本发明提供了一种提高玉米蛋白消化率的工艺,以解决上述背景技术中提出的问题。
5.为实现上述目的,本发明提供如下技术方案:一种提高玉米蛋白消化率的工艺,包括以下步骤:
6.s1、玉米蛋白微粉的制备:以玉米蛋白粉为原料,碎成细粉,并对细碎的玉米蛋白粉进行筛选处理,得到所需的玉米蛋白微粉;
7.s2、玉米蛋白微粉冷冻处理:将步骤s1中制备的玉米蛋白微粉进行冷冻处理;
8.s3、玉米蛋白微粉汽蒸处理:将步骤s2中冷冻处理后的玉米蛋白微粉进行汽蒸处理,向汽蒸后的玉米蛋白中加入亚硫酸钠水溶液,过滤处理,除去滤液,得到处理后玉米蛋白;
9.s4、加水搅拌处理:向步骤s3所得处理后玉米蛋白中加水,并进行搅拌处理,制备所需的原液;
10.s5、加入苯丙氨酸:向步骤s4所得原液中加入苯丙氨酸,搅拌均匀,得到所需的混合物,备用;
11.s6、混合蛋白酶的添加:将步骤s5制备的混合物调节ph值至8-10,并升温至30-40℃,加入混合蛋白酶和水进行酶解处理,得到所需的酶解液;
12.s7、过滤和冷冻干燥:将步骤s6所得酶解液进行过滤处理,得滤液,将滤液浓缩、喷雾干燥,得玉米蛋白肽;
13.s8、消毒、包装和入库:将步骤s7中制备得到的玉米蛋白肽进行紫外线杀菌消毒后,包装成品入库。
14.进一步优化本技术方案,所述步骤s1中的玉米蛋白粉过50-100目的筛网进行筛选处理。
15.进一步优化本技术方案,所述步骤s2中的玉米蛋白微粉冷冻的时间为30-50min。
16.进一步优化本技术方案,所述步骤s3中亚硫酸钠水溶液的加入量为玉米蛋白微粉质量的2-4倍,浸泡时间为1-2h。
17.进一步优化本技术方案,所述步骤s4中水的加入量为处理后玉米蛋白质量的8-12倍,以150-300r/min的速度搅拌25-35min,得到所需的原液。
18.进一步优化本技术方案,所述步骤s5中苯丙氨酸的添加量为原液量的0.1-0.15%,以140-260r/min的速度搅拌15-30min,得所需的混合料。
19.进一步优化本技术方案,所述步骤s6中的混合蛋白酶为碱性蛋白酶和淀粉酶,碱性蛋白酶的量为混合物质量的2-4%,淀粉的量为混合物质量的1-3%,酶解时间为1-2h,升温至90℃进行酶灭处理。
20.进一步优化本技术方案,所述步骤s6中的淀粉酶为高温液化淀粉酶。
21.进一步优化本技术方案,所述步骤s7中加热温度为150℃-200℃。
22.与现有技术相比,本发明提供了一种提高玉米蛋白消化率的工艺,具备以下有益效果:
23.1、该提高玉米蛋白消化率的工艺,本发明玉米蛋白粉酶解前的碱处理,通过将玉米蛋白转化为小分子肽,大大提高了玉米蛋白的利用率,彻底解决了玉米蛋白不易溶于水,难于消化吸收的问题,具有更高的营养价值,采用本发明提供的玉米蛋白肽的提取方法制得的玉米蛋白肽水解度高,提高了玉米蛋白的利用率,且采用本发明提供的玉米蛋白肽的提取方法制得的玉米蛋白肽消化率好。
24.2、该提高玉米蛋白消化率的工艺,本发明混合蛋白酶的添加,能够提高对蛋白质的消化率,本发明的制备工艺大大提高玉米蛋白与碱性蛋白酶接触的机会,促进玉米蛋白肽的提取,提高玉米蛋白的水解度,本发明提供的玉米蛋白肽的提取方法操作简单,易于工业化规模生产。
附图说明
25.图1为本发明提出的一种提高玉米蛋白消化率的工艺的流程示意图。
具体实施方式
26.下面将结合本发明的实施例,对本发明实施例中的技术方案进行清楚、完整地描述,显然,所描述的实施例仅仅是本发明一部分实施例,而不是全部的实施例。基于本发明中的实施例,本领域普通技术人员在没有做出创造性劳动前提下所获得的所有其他实施例,都属于本发明保护的范围。
27.实施例一:请参考图1所示,本发明公开了一种提高玉米蛋白消化率的工艺,包括以下步骤:
28.s1、玉米蛋白微粉的制备:以玉米蛋白粉为原料,碎成细粉,并对细碎的玉米蛋白
粉进行筛选处理,得到所需的玉米蛋白微粉,玉米蛋白粉过80目的筛网进行筛选处理;
29.s2、玉米蛋白微粉冷冻处理:将步骤s1中制备的玉米蛋白微粉进行冷冻处理,玉米蛋白微粉冷冻的时间为30min;
30.s3、玉米蛋白微粉汽蒸处理:将步骤s2中冷冻处理后的玉米蛋白微粉进行汽蒸处理,向汽蒸后的玉米蛋白中加入亚硫酸钠水溶液,过滤处理,除去滤液,得到处理后玉米蛋白,亚硫酸钠水溶液的加入量为玉米蛋白微粉质量的2倍,浸泡时间为1h;
31.s4、加水搅拌处理:向步骤s3所得处理后玉米蛋白中加水,并进行搅拌处理,制备所需的原液,水的加入量为处理后玉米蛋白质量的8倍,以200r/min的速度搅拌30min,得到所需的原液;
32.s5、加入苯丙氨酸:向步骤s4所得原液中加入苯丙氨酸,搅拌均匀,得到所需的混合物,备用,苯丙氨酸的添加量为原液量的0.12%,以200r/min的速度搅拌25min,得所需的混合料;
33.s6、混合蛋白酶的添加:将步骤s5制备的混合物调节ph值至8,并升温至40℃,加入混合蛋白酶和水进行酶解处理,得到所需的酶解液,混合蛋白酶为碱性蛋白酶和淀粉酶,碱性蛋白酶的量为混合物质量的3%,淀粉的量为混合物质量的2%,酶解时间为1.5h,升温至90℃进行酶灭处理,淀粉酶为高温液化淀粉酶;
34.s7、过滤和冷冻干燥:将步骤s6所得酶解液进行过滤处理,得滤液,将滤液浓缩、喷雾干燥,得玉米蛋白肽,所述步骤s7中加热温度为150℃℃;
35.s8、消毒、包装和入库:将步骤s7中制备得到的玉米蛋白肽进行紫外线杀菌消毒后,包装成品入库。
36.实施例二:请参考图1所示,本发明公开了一种提高玉米蛋白消化率的工艺,包括以下步骤:
37.s1、玉米蛋白微粉的制备:以玉米蛋白粉为原料,碎成细粉,并对细碎的玉米蛋白粉进行筛选处理,得到所需的玉米蛋白微粉,玉米蛋白粉过90目的筛网进行筛选处理;
38.s2、玉米蛋白微粉冷冻处理:将步骤s1中制备的玉米蛋白微粉进行冷冻处理,玉米蛋白微粉冷冻的时间为40min;
39.s3、玉米蛋白微粉汽蒸处理:将步骤s2中冷冻处理后的玉米蛋白微粉进行汽蒸处理,向汽蒸后的玉米蛋白中加入亚硫酸钠水溶液,过滤处理,除去滤液,得到处理后玉米蛋白,亚硫酸钠水溶液的加入量为玉米蛋白微粉质量的3倍,浸泡时间为1.5h;
40.s4、加水搅拌处理:向步骤s3所得处理后玉米蛋白中加水,并进行搅拌处理,制备所需的原液,水的加入量为处理后玉米蛋白质量的10倍,以300r/min的速度搅拌35min,得到所需的原液;
41.s5、加入苯丙氨酸:向步骤s4所得原液中加入苯丙氨酸,搅拌均匀,得到所需的混合物,备用,苯丙氨酸的添加量为原液量的0.15%,以180r/min的速度搅拌30min,得所需的混合料;
42.s6、混合蛋白酶的添加:将步骤s5制备的混合物调节ph值至9,并升温至35℃,加入混合蛋白酶和水进行酶解处理,得到所需的酶解液,混合蛋白酶为碱性蛋白酶和淀粉酶,碱性蛋白酶的量为混合物质量的3%,淀粉的量为混合物质量的2%,酶解时间为1.2h,升温至90℃进行酶灭处理,淀粉酶为高温液化淀粉酶;
43.s7、过滤和冷冻干燥:将步骤s6所得酶解液进行过滤处理,得滤液,将滤液浓缩、喷雾干燥,得玉米蛋白肽,所述步骤s7中加热温度为180℃;
44.s8、消毒、包装和入库:将步骤s7中制备得到的玉米蛋白肽进行紫外线杀菌消毒后,包装成品入库。
45.实施例三:请参考图1所示,本发明公开了一种提高玉米蛋白消化率的工艺,包括以下步骤:
46.s1、玉米蛋白微粉的制备:以玉米蛋白粉为原料,碎成细粉,并对细碎的玉米蛋白粉进行筛选处理,得到所需的玉米蛋白微粉,玉米蛋白粉过50-100目的筛网进行筛选处理;
47.s2、玉米蛋白微粉冷冻处理:将步骤s1中制备的玉米蛋白微粉进行冷冻处理,玉米蛋白微粉冷冻的时间为40min;
48.s3、玉米蛋白微粉汽蒸处理:将步骤s2中冷冻处理后的玉米蛋白微粉进行汽蒸处理,向汽蒸后的玉米蛋白中加入亚硫酸钠水溶液,过滤处理,除去滤液,得到处理后玉米蛋白,亚硫酸钠水溶液的加入量为玉米蛋白微粉质量的3倍,浸泡时间为1.5h;
49.s4、加水搅拌处理:向步骤s3所得处理后玉米蛋白中加水,并进行搅拌处理,制备所需的原液,水的加入量为处理后玉米蛋白质量的12倍,以300r/min的速度搅拌30min,得到所需的原液;
50.s5、加入苯丙氨酸:向步骤s4所得原液中加入苯丙氨酸,搅拌均匀,得到所需的混合物,备用,苯丙氨酸的添加量为原液量的0.15%,以140-260r/min的速度搅拌25min,得所需的混合料;
51.s6、混合蛋白酶的添加:将步骤s5制备的混合物调节ph值至8-10,并升温至35℃,加入混合蛋白酶和水进行酶解处理,得到所需的酶解液,混合蛋白酶为碱性蛋白酶和淀粉酶,碱性蛋白酶的量为混合物质量的3%,淀粉的量为混合物质量的2%,酶解时间为2h,升温至90℃进行酶灭处理,淀粉酶为高温液化淀粉酶;
52.s7、过滤和冷冻干燥:将步骤s6所得酶解液进行过滤处理,得滤液,将滤液浓缩、喷雾干燥,得玉米蛋白肽,所述步骤s7中加热温度为200℃;
53.s8、消毒、包装和入库:将步骤s7中制备得到的玉米蛋白肽进行紫外线杀菌消毒后,包装成品入库。
54.实施例四:请参考图1所示,本发明公开了一种提高玉米蛋白消化率的工艺,包括以下步骤:
55.s1、玉米蛋白微粉的制备:以玉米蛋白粉为原料,碎成细粉,并对细碎的玉米蛋白粉进行筛选处理,得到所需的玉米蛋白微粉,玉米蛋白粉过70目的筛网进行筛选处理;
56.s2、玉米蛋白微粉冷冻处理:将步骤s1中制备的玉米蛋白微粉进行冷冻处理,玉米蛋白微粉冷冻的时间为40min;
57.s3、玉米蛋白微粉汽蒸处理:将步骤s2中冷冻处理后的玉米蛋白微粉进行汽蒸处理,向汽蒸后的玉米蛋白中加入亚硫酸钠水溶液,过滤处理,除去滤液,得到处理后玉米蛋白,亚硫酸钠水溶液的加入量为玉米蛋白微粉质量的3倍,浸泡时间为1.8h;
58.s4、加水搅拌处理:向步骤s3所得处理后玉米蛋白中加水,并进行搅拌处理,制备所需的原液,水的加入量为处理后玉米蛋白质量的8-12倍,以280r/min的速度搅拌30min,得到所需的原液;
59.s5、加入苯丙氨酸:向步骤s4所得原液中加入苯丙氨酸,搅拌均匀,得到所需的混合物,备用,苯丙氨酸的添加量为原液量的0.15%,以180r/min的速度搅拌20min,得所需的混合料;
60.s6、混合蛋白酶的添加:将步骤s5制备的混合物调节ph值至8,并升温至30℃,加入混合蛋白酶和水进行酶解处理,得到所需的酶解液,混合蛋白酶为碱性蛋白酶和淀粉酶,碱性蛋白酶的量为混合物质量的3%,淀粉的量为混合物质量的2%,酶解时间为1.7h,升温至90℃进行酶灭处理,淀粉酶为高温液化淀粉酶;
61.s7、过滤和冷冻干燥:将步骤s6所得酶解液进行过滤处理,得滤液,将滤液浓缩、喷雾干燥,得玉米蛋白肽,所述步骤s7中加热温度为200℃;
62.s8、消毒、包装和入库:将步骤s7中制备得到的玉米蛋白肽进行紫外线杀菌消毒后,包装成品入库。
63.判断标准:
64.将实施例1-4玉米蛋白消化率的工艺的蛋白质水解度,与市售的玉米蛋白消化率的工艺的蛋白质水解度进行试验对比,使用本发明制得的玉米蛋白消化率的工艺的蛋白质水解度如表2所示:
65.表2:实施例1-3与市售产品对比
[0066][0067]
由表可知,采用本发明实施例2的玉米蛋白肽的提取方法的蛋白质水解度明显高于采用实施例一、三、四以及市售的玉米蛋白肽的提取方法的蛋白质水解度,由此可见,通过本发明提供的实施例二玉米蛋白肽的提取方法可以使玉米蛋白具有更高的水解度,通过四个实施例对比,效果最佳者为实施例二,因此,选择实施例二为最佳实施例,具体对量的改变,也属于本技术方案保护的范围。
[0068]
本发明的有益效果:该提高玉米蛋白消化率的工艺,本发明玉米蛋白粉酶解前的碱处理,本发明通过将玉米蛋白转化为小分子肽,大大提高了玉米蛋白的利用率,彻底解决了玉米蛋白不易溶于水,难于消化吸收的问题,具有更高的营养价值,采用本发明提供的玉米蛋白肽的提取方法制得的玉米蛋白肽水解度高,提高了玉米蛋白的利用率,且采用本发
明提供的玉米蛋白肽的提取方法制得的玉米蛋白肽消化率好;本发明混合蛋白酶的添加,能够提高对蛋白质的消化率,本发明的制备工艺大大提高玉米蛋白与碱性蛋白酶接触的机会,促进玉米蛋白肽的提取,提高玉米蛋白的水解度,本发明提供的玉米蛋白肽的提取方法操作简单,易于工业化规模生产。
[0069]
尽管已经示出和描述了本发明的实施例,对于本领域的普通技术人员而言,可以理解在不脱离本发明的原理和精神的情况下可以对这些实施例进行多种变化、修改、替换和变型,本发明的范围由所附权利要求及其等同物限定。
再多了解一些
本文用于企业家、创业者技术爱好者查询,结果仅供参考。