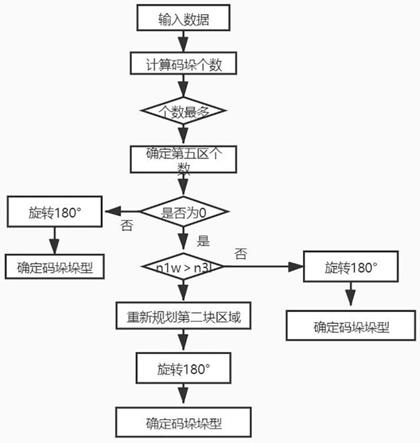
1.本发明属于机器人码垛垛型的应用领域,具体为一种适用于袋装软包的混合码垛规划方法,主要用于用户需根据自身的需求,生成合理的垛型。
背景技术:
2.在袋装水泥装车过程中,装车机器人按照预先规定的垛型将水泥料包放置在指定的地方,货物垛型的设计会直接影响到车厢空间的利用率和货物的稳定性。装车货物垛型设计涉及货物的排布,货物码放的先后顺序,码垛的稳定性等多个因素。但因为软包具有与纸盒,包装箱截然不同的特性,所以到目前为止,袋装料包的垛型主要依靠使用者的经验,这种方法缺少合理的计算,造成了车厢空间的浪费;虽然现有的示教系统可以提供简单的垛型供人们选择使用,但随着机器人在工厂中的进一步应用,这种方式已经不能满足工厂的需求。
3.公开号为cn111483815b的专利公开了一种面向全自动装车的袋装物码垛规划系统包括:输入模块、储存模块、计算模块和显示模块;所述输入模块用于为系统录入装车规划所需信息,在用户界面中输入车厢长、宽、高参数{x,y,z},m种装车袋型长宽高信息{a1,b1,c1,a2,b2,c2,...,ai,bi,ci,...,am,bm,cm}及对应规划装车数量{t1,t2,...,tm},同时设置货物码垛能够高出车厢的预设值和车厢尾部最大容纳间隙预设值,输入模块与计算模块、储存模块连接;所述储存模块将输入模块得到的数据自动保存到系统,并在下次装车时为用户提供对应的装车信息记录,当选择使用过的装车信息记录后,直接将使用过的装车记录信息改写为输入模块信息,存储模块只与输入模块连接;所述计算模块直接读取输入模块中的装车信息,规划出对应的装车方案,并传入显示模块,计算模块与输入模块、显示模块连接;所述显示模块根据计算模块得到的装车数据,将对应的装车规划显示出来,通过文字显示出每种袋型在车厢中的装车位置、装车方式以及装车层数,同时将对应的装车平面示意图显示出来,显示模块仅与计算模块连接。
4.该专利中,在针对通类型的袋装物摆放时,先从前到后横放,横放若干各到不能再继续横放时,继而转为竖放,在一定程度上可以利用车厢的有效空间,但在横放无法继续放的情况下再竖放的方式,根据不同车厢的情况,极大可能依旧还有间隙不能被有效利用的情况。
技术实现要素:
5.本发明的目的在于提供一种适用于袋装软包的混合码垛规划方法,主要用于用户需根据自身的需求,生成合理的垛型。
6.本技术为了解决上述技术问题,提供了一种适用于袋装软包的混合码垛规划方法,包括以下步骤:s1.输入软包的规格:长度l、宽度w、高度h,并扫描存储车厢的规格:长度l、宽度w、高度h;
s2.通过计算规划第一层的最优码垛方式,以确保第一层码垛的软包数量最多,并确定第一层软包码垛位置坐标,并将第一层的最优码垛方式确定为最优垛型;s3.利用第一层得到的最优垛型,依次交错所述最优垛型,确定其他层的码垛方式;s4.根据软包码垛位置坐标,规划软包码垛路径。
7.作为优选,所述步骤s2包括:s21.以车厢的左上角为原点建立空间直角坐标系,其中第一层所在的平面为oxy;s22.将车厢内第一层对应平面oxy的空间随机分为为五个区域,分别为位于左上车厢的第一区域、位于右上车厢的第二区域、位于左下车厢的第三区域、位于右下车厢的第四区域、以及上述车厢内除上述四个区域外的第五区域;s23.假设第一区域中码垛横向的软包、第二区域中码垛竖向的软包、第三区域中码垛竖向的软包、第四区域中码垛横向的软包、第五区域根据实际情况码垛软包,并分情况计算每个区域中的码垛数及第一层总码垛数,并将第一层的总码垛数最多的情况作为第一层最优码垛数;s24.根据每个区域内的码垛数确定每个软包的码垛坐标。
8.作为优选,所述步骤s23包括:s231.设第一区域中,x方向上软包的码垛个数为n
1l
、y方向上软包的码垛个数为n
1w
;第二区域中,x方向上软包的码垛个数为n
2w
、y方向上软包的码垛个数为n
2l
;第三区域中,x方向上软包的码垛个数为n
1l
*l/w、y方向上软包的码垛个数为int((l-n
1w
*w)/l);第四区域中,x方向上软包的码垛个数为n
2w
*w/l、y方向上软包的码垛个数为int((l-n
2l
*l)/w);s232.计算:第一区域中码垛软包的数量:n1=n
1l
*n
1w
;第二区域中码垛软包的数量:n2=int((w-n
1l
*l)/w)*n
2l
;第三区域中码垛软包的数量:n3=int((l-n
1w
*w)/l)*int(n
1l
*l/w);第四区域中码垛软包的数量:n4=int((l-n
2l
*l)/w)*int((n
2w
*w)/l);s233.根据上述假设分情况计算第五区域中码垛数,并对比分析将码垛数最多的情况下的码垛数作为第五区域的最优码垛数n5;s234.计算第一层最优码垛数n=n1 n2 n3 n4 n5;其中,int()表示取整。
9.作为优选,所述步骤s233包括:s2331.假设l3=l-n
1w
*w; l4=l-n
2l
*l; w5=w-int(n
1l
*l/w)-int((n
2w
*w)/l);第一种情况:假设n
1w
*w>n
2l
*l,则第五区域中码垛数为:int(l4/w)*int(w5/l),或者int(l3/w)*(w5/w);第二种情况:假设n
1w
*w<n
2l
*l,则第五区域中码垛数为:int(l3/w)*int(w5/l),或者int(l4/
w)*(w5/w);s2332.取int(l4/w)*int(w5/l)、int(l3/w)*(w5/w)、int(l3/w)*int(w5/l)、int(l4/w)*(w5/w)中的最大值作为n5。
10.作为优选,所述步骤s24中,根据第五区域中码垛数n5是否为o,计算每个区域中软包的码垛坐标。
11.作为优选,所述步骤s24中:若n5》0,则,第一区域中软包码垛位置确定:(a*l,b*w,0),式中a从0到n
1l
;b从0到n
1w
;第二区域中软包码垛位置确定:(e*w,n
1w
*w f*l,0),式中c从0到int((w-n
1l
*l)/w);d从0到n
2l
;第三区域中软包码垛位置确定:(e*w,n
1w
*w f*l,0),式中e从0到int((l-n
1w
*w)/l);f从0到int(n
1l
*l/w);第四区域中软包码垛位置确定:(w-g*l,n
2l
*l h*w,0),式中g从0到int((n
2w
*w)/l);h从0到int((l-n
2l
*l)/w);第五区域中软包码垛位置确定:横包:(int(n
1l
*l/w)*w j*l,n
1w
*w k*w,0)式中j从0到int(w5/l);k从0到int(l3/w);竖包:(int(n
1l
*l/w)*w j*w,n
1w
*w k*l,0)式中j从0到int(w5/l);k从0到int(l3/w)。
12.作为优选,所述步骤s24中:若n5=0,分为以下两种情况:情况一:设n
1w
*w>n
2l
*l,第一区域、第二区域、第四区域中软包码垛位置与n5》0时相同,则,w3=w-int((n
2w
*w)/l)*l;间隙δd1=w3/int(n
1l
*l/w)-w;第三区域中软包码垛位置确定:(e*(w δd1) ,n
1w
*w f*l,0),式中e从0到int((l-n
1w
*w)/l);f从0到int(n
1l
*l/w);情况二:设n
1w
*w<n
2l
*l,第一区域、第二区域、第三区域中软包码垛位置与n5》0时相同,则,w4=l-int(n
1l
*l/w)*w;间隙δd2=w4/int((n
2w
*w)/l)-l;第四区域中软包码垛位置确定:w-g*(l δd2),n
2l
*l h*w,0),式中g从0到int((n
2w
*w)/l);h从0到int((l-n
2l
*l)/w);作为优选,所述步骤s3中,奇数层的最优垛型相同,偶数层的最优垛型相同,且偶数层的最优垛型由奇数层的最优垛型旋转180
°
得到。
13.作为优选,所述步骤s4包括:s41.确定第一层的存放路径;s42.确定其他层的存放参照步骤s41中第一层的存放路径;其中,步骤s41包括:
s411.确定第一区域的存放路径:按照从左到右,进行s型摆放;s412.确定第二区域的存放路径:调整料包姿势,按照从左到右,进行s型摆放;s413.确定第三区域的存放路径:按照从左到右,进行s型摆放;s414.确定第四区域的存放路径:调整料包姿势,按照从左到右,进行s型摆放。
14.作为优选,所述步骤s4后还包括:s5.将码垛软包的方法生成文本数据,并发送给上机位。
15.本发明具有如下技术效果:1.本发明用于所有相同大小的软包的货物码垛。大小相同的物体摆放在车厢内问题,相同于空间布局问题,本发明用以实现尽可能多的把货物摆放在有限的空间内,形成最优垛型;同时结合实际,考虑货物运输中的稳定性,码垛时车厢内软包间孔洞在考虑软包特性的情况下进行微调,而且上下两层形成错位,使垛型最稳定。
16.2.本发明中,任意种类的软包均可以至直接生成码垛机器人所需要的数据,简化了不同类型软包码垛编程的过程,提高了效率。
17.3.本发明为软包的码垛过程奠定了基础,避免了码垛过程中料包相互重叠造成码垛失败。
附图说明
18.图1软包的混合码垛规划方法整体流程图。
19.图2车厢平面分区示意图。
20.图3最优垛型计算示意图。
21.图4车厢坐标系建模示意图。
22.图5路径规划图。
具体实施方式
23.这里使用的术语仅用于描述特定实施例的目的,而不意图限制本发明。除非另外定义,否则本文使用的所有术语具有与本发明所属领域的普通技术人员通常理解的相同的含义。将进一步理解的是,常用术语应该被解释为具有与其在相关领域和本公开内容中的含义一致的含义。本公开将被认为是本发明的示例,并且不旨在将本发明限制到特定实施例。
24.本实施例提供了一种适用于袋装软包的混合码垛规划方法,如图1至图5,包括以下步骤:s1.输入软包的规格:长度l、宽度w、高度h,并扫描存储车厢的规格:长度l、宽度w、高度h;s2.通过计算规划第一层的最优码垛方式,以确保第一层码垛的软包数量最多,并确定第一层软包码垛位置坐标,并将第一层的最优码垛方式确定为最优垛型;s3.利用第一层得到的最优垛型,依次交错所述最优垛型,确定其他层的码垛方式;s4.根据软包码垛位置坐标,规划软包码垛路径。
25.一般车厢的尺寸也采用界面输入的形式,需要前期准确测量并记录车厢的尺寸才能进行输入的操作,针对不同大小的车厢,不够便利,本实施例中,车厢采用激光雷达扫描
得到车厢的方式,根据不同大小的车厢,直接扫描生成尺寸(长l、宽w、高h),不需要手动输入,本实施例中主要针对软包的码垛方法,考虑到软包不像箱体那样棱角分明,本实施例中采用手动输入的方式。本实施例中,根据软包的高度与车厢的高度可确定软包可码垛的层数,就同一层而言,软包的摆放方式分为横向摆放和竖向摆放两种,将横向摆放的软包称为横包,将竖向摆放的软包称为竖包。本实施例中,根据软包长度与宽度之间的补偿作用,合理利用车厢的水平面积,使得车厢上码垛的软包个数最多。
26.本实施例中,所述步骤s2包括:s21.以车厢的左上角为原点建立空间直角坐标系,其中第一层所在的平面为oxy;s22.将车厢内第一层对应平面oxy的空间随机分为五个区域,分别为位于左上车厢的第一区域、位于右上车厢的第二区域、位于左下车厢的第三区域、位于右下车厢的第四区域、以及上述车厢内除上述四个区域外的第五区域;s23.假设第一区域中码垛横向的软包、第二区域中码垛竖向的软包、第三区域中码垛竖向的软包、第四区域中码垛横向的软包、第五区域根据实际情况码垛软包,并分情况计算每个区域中的码垛数及第一层总码垛数,并将第一层的总码垛数最多的情况作为第一层最优码垛数;s24.根据每个区域内的码垛数确定每个软包的码垛坐标。
27.本实施例中通过建立的坐标系确定每个软包在坐标系中的坐标位置,这种记录软包位置的方式比较直观、准确。本实施例随机分配的五个区域中,第一区域、第二区域、第三区域、第四区域称之为使用面积,第五区域称之为间隔面积或再利用面积。其中,在x方向上,第一区域横向的软包和第二区域中的竖向的软包可相互补偿、第三区域横向的软包和第四区域中的竖向的软包可相互补偿;在y方向上,第一区域横向的软包和第三区域中的竖向的软包可相互补偿、第二区域横向的软包和第四区域中的竖向的软包可相互补偿。
28.其中,依照坐标系,所述步骤s23包括:s231.设第一区域中,x方向上软包的码垛个数为n
1l
、y方向上软包的码垛个数为n
1w
;第二区域中,x方向上软包的码垛个数为n
2w
、y方向上软包的码垛个数为n
2l
;第三区域中,x方向上软包的码垛个数为n
1l
*l/w、y方向上软包的码垛个数为int((l-n
1w
*w)/l);第四区域中,x方向上软包的码垛个数为n
2w
*w/l、y方向上软包的码垛个数为int((l-n
2l
*l)/w);s232.计算:第一区域中码垛软包的数量:n1=n
1l
*n
1w
;第二区域中码垛软包的数量:n2=int((w-n
1l
*l)/w)*n
2l
;第三区域中码垛软包的数量:n3=int((l-n
1w
*w)/l)*int(n
1l
*l/w);第四区域中码垛软包的数量:n4=int((l-n
2l
*l)/w)*int((n
2w
*w)/l);s233.根据上述假设分情况计算第五区域中码垛数,并对比分析将码垛数最多的情况下的码垛数作为第五区域的最优码垛数n5;s234.计算第一层最优码垛数n=n1 n2 n3 n4 n5;其中,int()表示取整。
29.进一步的,所述步骤s233包括:s2331.假设l3=l-n
1w
*w; l4=l-n
2l
*l; w5=w-int(n
1l
*l/w)-int((n
2w
*w)/l);第一种情况:假设n
1w
*w>n
2l
*l,则第五区域中码垛数为:int(l4/w)*int(w5/l),或者int(l3/w)*(w5/w);第二种情况:假设n
1w
*w<n
2l
*l,则第五区域中码垛数为:int(l3/w)*int(w5/l),或者int(l4/w)*(w5/w);s2332.取int(l4/w)*int(w5/l)、int(l3/w)*(w5/w)、int(l3/w)*int(w5/l)、int(l4/w)*(w5/w)中的最大值作为n5。
30.根据上述不同的情况再对第五区域中软包的摆放方式进行分析,进而确定第五区域中最优的码垛方式,进而最终实现整个第一次的最优码垛方式。
31.具体的,所述步骤s24中,根据第五区域中码垛数n5是否为o,计算每个区域中软包的码垛坐标。
32.所述步骤s24中:若n5》0,则,第一区域中软包码垛位置确定:(a*l,b*w,0),式中a从0到n
1l
;b从0到n
1w
;第二区域中软包码垛位置确定:(e*w,n
1w
*w f*l,0),式中c从0到int((w-n
1l
*l)/w);d从0到n
2l
;第三区域中软包码垛位置确定:(e*w,n
1w
*w f*l,0),式中e从0到int((l-n
1w
*w)/l);f从0到int(n
1l
*l/w);第四区域中软包码垛位置确定:(w-g*l,n
2l
*l h*w,0),式中g从0到int((n
2w
*w)/l);h从0到int((l-n
2l
*l)/w);第五区域中软包码垛位置确定:横包:(int(n
1l
*l/w)*w j*l,n
1w
*w k*w,0)式中j从0到int(w5/l);k从0到int(l3/w);竖包:(int(n
1l
*l/w)*w j*w,n
1w
*w k*l,0)式中j从0到int(w5/l);k从0到int(l3/w)。
33.进一步的,所述步骤s24中:若n5=0,分为以下两种情况:情况一:设n
1w
*w>n
2l
*l,第一区域、第二区域、第四区域中软包码垛位置与n5》0时相同,则,w3=w-int((n
2w
*w)/l)*l;间隙δd1=w3/int(n
1l
*l/w)-w;第三区域中软包码垛位置确定:(e*(w δd1) ,n
1w
*w f*l,0),式中e从0到int((l-n
1w
*w)/l);f从0到int(n
1l
*l/w);情况二:设n
1w
*w<n
2l
*l,第一区域、第二区域、第三区域中软包码垛位置与n5》0时相同,则,w4=l-int(n
1l
*l/w)*w;
间隙δd2=w4/int((n
2w
*w)/l)-l;第四区域中软包码垛位置确定:w-g*(l δd2),n
2l
*l h*w,0),式中g从0到int((n
2w
*w)/l);h从0到int((l-n
2l
*l)/w);依照上述对第五区域中不同情况下的码垛方式计算与分析,可得到第五区域中最优的码垛方式,进而得到第一层的最优垛型。在不同层之间,最优码垛方式与第一层相同,因此直接采用第一层得到的最优剁型即可。
34.其中,所述步骤s3中,奇数层的最优垛型相同,偶数层的最优垛型相同,且偶数层的最优垛型由奇数层的最优垛型旋转180
°
得到。使得层与层之间的软包相互错位,增大车厢内码垛软包的稳定性,即使得剁型更为稳定。
35.本实施例中,所述步骤s4包括:s41.确定第一层的存放路径;s42.确定其他层的存放参照步骤s41中第一层的存放路径;其中,如图5,步骤s41包括:s411.确定第一区域的存放路径:按照从左到右,进行s型摆放;s412.确定第二区域的存放路径:调整料包姿势,按照从左到右,进行s型摆放;s413.确定第三区域的存放路径:按照从左到右,进行s型摆放;s414.确定第四区域的存放路径:调整料包姿势,按照从左到右,进行s型摆放。
36.所述步骤s4后还包括:s5.将码垛软包的方法生成文本数据,并发送给上机位。装车机器人可以根据此数据将货物按照仿真出来的垛型码垛软包。
37.虽然描述了本发明的实施方式,但是本领域普通技术人员可以在所附权利要求的范围内做出各种变形或修改。
再多了解一些
本文用于企业家、创业者技术爱好者查询,结果仅供参考。