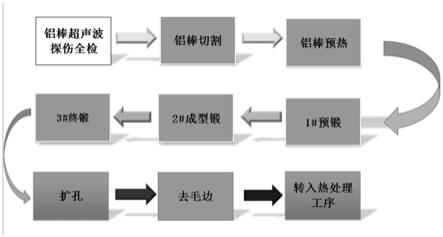
1.本发明涉及汽车轮毂技术领域,具体为一种抗疲劳高承载力的铝合金轮毂及其锻造工艺。
背景技术:
2.轮毂是按汽车零部件中最高安全等级要求的安全件归类的,汽车行驶过程会产生横向和纵向载荷,同时伴随驱动力矩制动力矩等,轮毂需要承受相当一部分载荷。现在的汽车都跑得很快,所以对轮毂的要求也会很高。铝合金轮毂重量轻,仅为钢的1/3,易于锻挤压成型,具有良好的耐腐蚀性、良好的强度和韧性,直锻铝合金车轮凭借自身优势,将作为汽车轻量化发展目标。而国际上只有美国铝业垄断直锻工艺,直锻工艺是在专用设备上采用专用模具,在闭式模腔内进行挤压、直接成型轮毂锻件内轮缘和外轮缘的锻造工艺过程。直锻铝合金轮毂有着重量轻强度高的优势,轻量化作为一项重要的优化指标,对新能源汽车提高综合续航能力起着重要作用。新能源汽车由于具有能源来源广泛及排放低等优点而成为各国汽车行业研发及投资的重点。2016年10月26日,中国汽车工程学会编制的《节能与新能源汽车技术路线图》正式发布,明确了新能源汽车作为未来汽车行业发展方向的必要和必然性,更是确定了汽车轻量化作为七大领域之一,为新能源汽车产业提供关键技术支撑的重要地位。
3.目前大部分的铝合金轮毂是通过铸造工艺生产,该工艺生产铝合金轮毂,具有铸造时间较长,加料、换模具耗时长,且生产的轮毂强度、轻量化指标不够,难以满足日益发展的汽车行业的需求。申请人通过消化吸收、再创新,模具研制、开发,掌握了具有自主知识产权的铝合金轮毂直接锻造、整体超塑一次快速成型工艺技术,填补了国内技术空白。
技术实现要素:
4.针对现有技术的不足,本发明提供了一种抗疲劳高承载力的铝合金轮毂及其锻造工艺,解决了现有铝合金轮毂重量不够轻、强度不够高的问题。
5.为实现以上目的,本发明通过以下技术方案予以实现:一种抗疲劳高承载力的铝合金轮毂,包括以下质量分数的原料:硅:0.30-0.7%,铁:0.50%,铜:0.10%,锰:0.03%,镁:0.35-0.8%,铬:0.03%,锌:0.10%,余量为6061铝合金和不可避免的杂质;其制造方法包括:铝棒成型,铝棒超声波探伤全检,铝棒切割,铝棒预热,1#预锻,2#成型锻,3#终锻,扩孔,去毛边,热处理工序。
6.优选的,一种抗疲劳高承载力的铝合金轮毂的锻造工艺,包括以下步骤:
7.s1、铝棒成型:将上述进行混合熔炼,将熔炼炉内温度升高到835-855℃,待金属熔化后,保持温度固定,熔炼2h,熔炼后,将熔炼炉内铝合金液进行铸造,将其浇注为铝棒,浇注温度为790-810℃,将浇注后的铝合金棒放入电阻炉中进行均匀化处理,均匀化处理温度为500-520℃,处理时间为18h,将均匀化处理后的铝合金锭冷却至室温,最后形成轮毂用铝合金棒材;
8.s2、铝棒超声波探伤全检:超声波探头扫查速度≤180mm/s,重叠扫查覆盖为有效声速的10%,第一次扫查区域为90
°
,并在棒材端标注旋转标记,共旋转四次,每次旋转的角度均为90
°
,以扫查待检测铝合金棒材的全圆周区域;
9.s2、预处理:对铝棒进行切割得到预定长度的铝棒毛坯,对铝棒毛坯预加热,加热温度为450℃-600℃;
10.s3、锻造:将加热后的铝棒毛坯放入凹模,利用凸模向下运动,凸模与凹模精确合模,对铝棒毛坯进行预锻,成型锻,终锻,得到铝合金轮毂;
11.s4、铝合金轮毂进行扩孔,去毛边后,将需要热处理的铝合金轮毂表面的油污及脏物清除,送入回火炉内进行热处理。
12.优选的,所述s3步骤前,设计模具,通过凸模、凹模合模可构成金属的挤压模腔,挤压模腔结构、尺寸根据轮毂热挤压件图的结构尺寸设计、加工。
13.优选的,在挤压过程中,要求凸凹模在足够的合模力下精确合模,凸模向下运动时,由导向杆导引,保证与凹模的合模精度。
14.优选的,利用顶出杆在挤压过程结束后,使凸模升起,设备下缸伸出的顶出杆通过顶出孔作用,把锻压件顶出凹模,产品与模具脱离。
15.优选的,所述铝液出炉后经过高纯度氮气除气,再转入保温炉以620-730℃进行保温。
16.优选的,所述热处理工序包括把固熔炉温度设定在545℃,待到固熔炉温度达到545℃后进行保温160分钟,让铝合金内部组织在高温下进行重组,保温时间到达160分钟,在炉门打开15秒内进行淬火,提升铝合金硬度,热处理去应力温度设定在170-180℃,保温时间为8小时;随炉冷却至室温;在失效过程中可以有效的消除因机加工产生的机械残余应力,减小轮毂变形量。
17.本发明提供了一种抗疲劳高承载力的铝合金轮毂及其锻造工艺。具备以下有益效果:
18.1、本发明通过采用优化的配方作为轮毂的材质,利用铝棒超声波探伤全检,铝棒切割,铝棒预热,1#预锻,2#成型锻,3#终锻,扩孔,去毛边,热处理等工序,实现铝合金轮毂具备质量轻,重量约为钢圈的1/2,节省燃油等优点,能够减轻轮毂对轮胎的磨损,降低刹车系统的维护保养费用,承载能力更高,是钢圈的5倍,能延长发动机使用寿命,散热性好、真圆度高、高速平衡,可塑性强、可随意定制,质感一流,抗疲劳、撞击强度更高,安全系数高,能适应各种复杂的驾驶环境,尺寸精确,美观,便于回收。
19.2、本发明通过用超声波技术对铝合金棒材无损探伤,不存在重叠无法检测的区域,实现的全方位检测,有效地提高检测棒材内部损伤的准确率,工作效率高,误差小。
20.3、本发明直锻轮毂是铝锭预热后经上万吨压力等温锻压机锻造成的毛坯,该工艺整体超塑一次成型,解决了生产环节上的制约,可以实现高效率、高制成率、低成本的大批量稳定生产,锻造工艺不经历固态、液态、固态的转变过程,避免杂质、气泡等缺陷,由于承受高压撞击,所以合金之间的分子会更小、间隙更细、密度更高,材质分子之间相互作用力更强,韧性高,且材料利用率高,轮毂重量轻,直接锻造、整体超塑一次快速成型工艺技术,国际上只有美国铝业垄断直锻工艺,通过消化吸收、再创新,填补了国内技术空白。
21.4、本发明通过直锻一次成型的智能工艺,完美地保证了原材料成分的完整性、均
匀性,更紧密的原材料组织排列、更合理的原材料密度分布、就会有更疯狂的抗作用力冲击能力。
22.5、经多年使用后,铝合金轮毂仍可以以铝均价的92%回收,再利用率高,更符合环保要求。
附图说明
23.图1为本发明的工艺流程图。
具体实施方式
24.下面将结合本发明实施例中的附图,对本发明实施例中的技术方案进行清楚、完整地描述,显然,所描述的实施例仅仅是本发明一部分实施例,而不是全部的实施例。基于本发明中的实施例,本领域普通技术人员在没有做出创造性劳动前提下所获得的所有其他实施例,都属于本发明保护的范围。
25.实施例一:
26.如图1所示,本发明实施例提供一种抗疲劳高承载力的铝合金轮毂,包括以下质量分数的原料:硅:0.30-0.7%,铁:0.50%,铜:0.10%,锰:0.03%,镁:0.35-0.8%,铬:0.03%,锌:0.10%,余量为6061铝合金和不可避免的杂质;其制造方法包括:铝棒成型,铝棒超声波探伤全检,铝棒切割,铝棒预热,1#预锻,2#成型锻,3#终锻,扩孔,去毛边,热处理等工序。
27.通过锻造模拟理论与实践数据的对比分析,利用红外线成像仪对欧美产品实施温度监控,总结温度规律,通过锻造模拟分析,结合实际监控数据进行对比分析,形成锻造模拟技术,然后设计模具,通过凸模、凹模合模可构成金属的挤压模腔,其结构、尺寸根据轮毂热挤压件图的结构尺寸设计、加工。在挤压过程中,要求凸凹模在足够的合模力下精确合模,则凸模向下运动时,由导向杆导引,保证与凹模的合模精度。顶出杆是当挤压过程结束后,凸模升起,设备下缸伸出的顶杆通过顶出孔作用,把锻压件顶出凹模,从而实现模具一次成型。
28.直锻一次成型的智能工艺,完美地保证了原材料成分的完整性、均匀性。更紧密的原材料组织排列、更合理的原材料密度分布、就会有更疯狂的抗作用力冲击能力。
29.针对各种不同使用环境,对车轮外表面处理有着各式各样的需求,通过抛光涂装电镀电泳、阳极氧化等表面处理工艺,外形个性美观防腐抗氧。
30.利用直锻成型模具,该模具采用收缩模,可以实现轮辋造型一次成型,不需要经历旋压工序,简化了成型工艺,提高了生产效率,而且铝合金轮毂的机械性能相比于锻旋铝轮、铸造铝轮、钢轮的机械性能有所提高。
31.采用先进的设计软件与加工制造设备制造出样品,然后在严格的试验条件测试产品的寿命与工作性能。
32.在产品设计和生产过程中考虑反复试验,提高制成率和效率。
33.生产执行gb/t 5909 2009,质量运行iatf16949质量体系标准,严格控制采购、检验、制程、包装和售后服务的质量过程,产品质量符合国家标准、行业标准和客户要求。我司的产品机械性能试验超出国家标准(抗拉σb≧320mpa、屈服σs≧290mpa、δs≧11%);中汽协
车轮质量检验中心检测,依据《gb/t5909-2009商用车辆车轮性能要求和试验方法》,其中弯曲疲劳试验m=27632n.m,完成500万转无裂纹;径向疲劳试验,载荷8250kg,完成400万转无裂纹,均超出国标标准,锻造铝合金轮毂有着重量轻,省油,散热性好,强度高,安全性能好,可延长轮胎使用寿命等优点。
34.直锻轮毂是铝锭预热后经上万吨压力等温锻压机锻造成的毛坯,该工艺整体超塑一次成型,解决了生产环节上的制约,可以实现高效率、高制成率、低成本的大批量稳定生产,锻造工艺不经历固态、液态、固态的转变过程,避免杂质、气泡等缺陷,由于承受高压撞击,所以合金之间的分子会更小、间隙更细、密度更高,材质分子之间相互作用力更强,韧性高。且材料利用率高,轮毂重量轻,直接锻造、整体超塑一次快速成型工艺技术,国际上只有美国铝业垄断直锻工艺,通过消化吸收、再创新,填补了国内技术空白。
35.对铝合金轮毂进行性能试验,结果如下:
36.[0037][0038]
实施例二:
[0039]
一种抗疲劳高承载力的铝合金轮毂的锻造工艺,具体包括以下步骤:
[0040]
s1、铝棒成型:将铝合金轮毂的原料进行混合熔炼,将熔炼炉内温度升高到835-855℃,待金属熔化后,保持温度固定,熔炼2h,熔炼后,将熔炼炉内铝合金液进行铸造,将其浇注为铝棒,浇注温度为790-810℃,将浇注后的铝合金棒放入电阻炉中进行均匀化处理,均匀化处理温度为500-520℃,处理时间为18h,将均匀化处理后的铝合金锭冷却至室温,最后形成轮毂用铝合金材料;
[0041]
s2、铝棒超声波探伤全检:超声波探头扫查速度≤180mm/s,重叠扫查覆盖为有效声速的10%,第一次扫查区域为90
°
,并在棒材端标注旋转标记,共旋转四次,每次旋转的角度均为90
°
,以扫查待检测铝合金棒材的全圆周区域;
[0042]
s2、预处理:对铝棒进行切割得到预定长度的铝棒毛坯,对铝棒毛坯预加热,加热温度为450℃-600℃;
[0043]
s3、锻造:将加热后的铝棒毛坯放入凹模,利用凸模向下运动,凸模与凹模精确合模,对铝棒毛坯进行预锻,成型锻,终锻,得到铝合金轮毂;
[0044]
s4、铝合金轮毂进行扩孔,去毛边后,将需要热处理的铝合金轮毂表面的油污及脏物清除,送入回火炉内进行热处理。
[0045]
热处理工序包括把固熔炉温度设定在545℃,待到固熔炉温度达到545℃后进行保温160分钟,让铝合金内部组织在高温下进行重组,保温时间到达160分钟,在炉门打开15秒内进行淬火,提升铝合金硬度,热处理去应力温度设定在170-180℃,保温时间为8小时;随炉冷却至室温;在失效过程中可以有效的消除因机加工产生的机械残余应力,减小轮毂变形量。
[0046]
不需要经历旋压工序,简化了成型工艺,提高了生产效率,而且铝合金轮毂的机械性能相比于锻旋铝轮、铸造铝轮、钢轮的机械性能有所提高,增强了轮毂的性能和使用寿命,性能稳定、安全可靠、方便实用。
[0047]
s3步骤前,设计模具,通过凸模、凹模合模可构成金属的挤压模腔,挤压模腔结构、尺寸根据轮毂热挤压件图的结构尺寸设计、加工。
[0048]
在挤压过程中,要求凸凹模在足够的合模力下精确合模,凸模向下运动时,由导向杆导引,保证与凹模的合模精度。
[0049]
利用顶出杆在挤压过程结束后,使凸模升起,设备下缸伸出的顶出杆通过顶出孔作用,把锻压件顶出凹模,产品与模具脱离。
[0050]
尽管已经示出和描述了本发明的实施例,对于本领域的普通技术人员而言,可以理解在不脱离本发明的原理和精神的情况下可以对这些实施例进行多种变化、修改、替换和变型,本发明的范围由所附权利要求及其等同物限定。
再多了解一些
本文用于企业家、创业者技术爱好者查询,结果仅供参考。