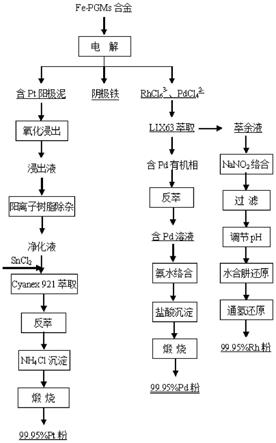
1.本发明属于铂族金属循环利用的技术领域,涉及一种铁合金中铂族金属分离提纯的方法。
背景技术:
2.铂族金属(platinum group metals,简写pgms)矿产资源稀缺,分布不均匀,99%以上在南非、俄罗斯、赞比亚、美国等国家。特别是我国的pgms储量不足400吨,而年需求量超过150吨,对外依存度高,达90%以上,供需矛盾极为突出。
3.pgms主要用于催化剂,汽车尾气催化剂消耗了全球45%pt、65%pd和85%rh,从而使的废汽车尾气催化剂成为pgms回收利用最重要的二次资源。
4.然而,传统采用铅、铜、镍火法富集废汽车催化剂中铂族金属工艺重金属的方法对环境污染严重,即使等离子体铁捕集虽处理能力大、捕集率高,但是其存在熔炼温度高(1600-2000℃),形成难溶硅铁合金致后续pgms分离困难的技术问题,且等离子体铁捕集的pgms回收率较低,不足60%。
5.针对上述问题,发明人研发了一系列的低温铁捕集铂族金属技术,实现了铂族金属的绿色高效富集,申请并授权了多项中国发明专利,如zl 201611141140.6、zl201911253313.7、zl202010631384.2、zl202010835163.7、zl 201911188785.9等,且成果已在多家企业实现产业化。
6.目前,为分离提纯pgms,行业内主要采用铝碎化fe-pgms合金,再用盐酸或硫酸溶解fe和al等;由于al与pgms形成一系列al-pgms合金(如al2pt、al3pd2、al3rh等),提高了pgms的反应活性,从而提高了其溶解效率。根据合金中pgms含量,al添加量为fe-pgms合金质量的0.5-3倍。
7.然而,上述al的加入会导致酸溶过程物耗高,废水量大,且易形成al(oh)3胶体影响pgms回收效率。为避免铝硅胶体形成,发明人团队通过添加zn,在空气条件下形成fe-zn复合氧化物,再利用盐酸溶解碎化产物,得到的pgms富集物再进行提纯(zl 202010113616.5)。
8.同时为进一步减少物耗和废水排放,发明人团队研发了fe-pgms电解回收pgms的方法(申请号:201911012903.0),即以fe-pgms合金为阳极,惰性电极为阴极,采用恒压电解得到富含pgms阳极泥和阴极纯铁。该方法能经济、绿色、高效的分别fe和pgms,得到的pgms经分离提纯即可得到高纯pt、pd、rh。
9.综上,现有的fe-pgms回收pgms的高效方法已经研发出来,但是由于回收pgms中的pt、pd、rh性质相似,分离困难,传统沉淀法试剂消耗大、流程长、废水量大,而且直收率低;故而现有的pgms的分离提纯效率低,不利于工业生产和推广。特别是大多数都是通过先分离铁合金中的fe和pgms,然后再分离提纯pt、pd、rh,不仅增大了分离难度,而且操作工序复杂,亟需一种有别于现有技术的、能够简单、便捷、高效的分离提纯pt、pd、rh的方法,提高直收率,经济、环境效益显著。
技术实现要素:
10.本发明解决的技术问题是现有湿法除铁富集pgms废水量大、pgms分离提纯流程长、直收率低等难题,且大多数都是通过先分离铁合金中的fe和pgms,然后再分离提纯pt、pd、rh,不仅增大了分离难度,而且操作工序复杂。
11.为解决上述技术问题,本发明提供如下技术方案:
12.一种铁合金中铂族金属分离提纯的方法,所述方法包括如下步骤:
13.s1、电解:以铁合金为阳极,以惰性材料为阴极,通过控制电压将铁合金中的fe、pd和rh氧化为fe
2
、pdcl
42-和rhcl
63-进入电解液中,pt以单质形式富集在阳极泥中形成含pt阳极泥,fe在阴极析出;
14.s2、pt的分离提纯:将步骤s1中的含pt阳极泥氧化溶解得到含pt溶液,依次经过阳离子树脂除杂、萃取剂cyanex 921萃取、nh4cl沉淀提纯,最后煅烧得到99.95%以上的海绵pt;
15.s3、pd的分离提纯:对步骤s1中的电解液采用水合肼还原得到pd和rh,之后过滤得到pd、rh富集物和滤液,其中:滤液返回步骤s1中的电解液中,而pd、rh富集物采用王水溶解得到溶解液,溶解液依次经过赶硝、阳离子树脂除杂、萃取剂lix63选择性萃取分离得到pd和萃pd余液,pd经反萃后再采用化学沉淀法提纯、煅烧得到99.95%以上的海绵pd;
16.s4、rh的分离提纯:将步骤s3中的萃pd余液加入nano2以络合rh,再调节ph去除贱金属杂质,煮沸使得其他离子络合物形成氢氧化物沉淀,过滤之后水合肼还原得到rh粉,最后通氢还原rh粉得到99.95%以上的海绵rh。
17.优选地,所述步骤s1中电解分离pt与fe、pd、rh的工艺条件为:电解质ph 0-2.5,cl-浓度0.01-1.0mol/l,so
42-2.0-4.0mol/l,fe
2
0.5-2.0mol/l,电压0.60-0.72v。
18.优选地,所述步骤s2中含pt阳极泥采用hcl nacl h2o2体系氧化浸出,所述萃取剂cyanex 921的组成为5-15vol.%的cyanex 921和85-95vol.%的磺化煤油,有机相与水相体积比为0.5:1-2:1,萃取时间为5-20min;反萃条件为:hno3浓度为0.5-5.0mol/l,有机相与水相体积比为0.5:1-2:1。
19.优选地,所述hcl nacl h2o2体系中h
浓度3.0-10.0mol/l、cl-浓度3.0-10.0mol/l、h2o2用量为理论用量的1.2-2倍,sncl2添加量为pt摩尔质量分数的20-40%;所述hcl nacl h2o2浸出体系的固液比为1:10,浸出温度为90℃,浸出时间为120min。
20.优选地,所述步骤s2中nh4cl沉淀提纯得到的是氯铂酸铵,沉淀次数为2-3次。
21.优选地,所述步骤s3中萃取剂lix 63萃取分离pd的条件为:有机相包括10-20vol.%的lix 63和80-90vol.%的磺化煤油,有机相与水相体积比为0.5:1-2:1,萃取时间为5-30min;反萃条件为:ch4n2s浓度为0.5-5mol/l,有机相与水相体积比为0.5:1-2:1。
22.优选地,所述步骤s3中pd经反萃后再采用化学沉淀法提纯中的方法为反萃液经氨水络合、盐酸沉淀1-2次,得到纯化的二氯二氨钯沉淀。
23.优选地,所述步骤s4中nano2的络合温度为60-90℃,nano2加入量为rh质量的5.0-8.0倍,采用na2co3调节ph至7-9。
24.优选地,所述铁合金为通过铁捕集铂族金属物料得到的fe-pgms合金,其中的pgms质量百分含量为0.1-30%。
25.优选地,所述步骤s4中萃pd余液加入nano2络合形成na2rh(no2)5。
26.优选地,所述fe-pgms合金中pt的直收率为97.4-99.0%,pd的直收率为98.3-99.2%,rh的直收率为98.3-99.1%。
27.本发明技术原理如下:
28.根据铁合金中的fe、pt、pd和rh在标准电极电位上的差异,在氯盐电解质体系中,通过控制电位,fe、pd和rh在阳极电解为fe
2
、pdcl
42-和rhcl
63-进入电解质溶液中,pt因氧化电位高以单质形式富集在阳极泥中,fe
2
在阴极还原得到单质fe,实现fe、pt与pd和rh的高效分离。利用杂质离子与ptcl
62-赋存状态的差异,采用阳离子交换树脂选择性去除杂质阳离子。
29.依据萃取动力学及rh易发生水合、羟合等反应形成难萃取络合物的原理,确定选择萃取分离顺序为:pd(pdcl
42-)》pt(ptcl
62-)》rh。
30.lix 63萃取pd的原理为:pdcl
42-aq
2ha
org
=pdcl2(ha)
2,org
2cl-aq
,其中ha代表lix 63。
31.利用sncl2将pt(iv)氯化物络合物还原生成[pt(sncl3)5]
3-,提高了cyanex 921选择性萃取ptcl
62-的能力,促进了pt的萃取分离。
[0032]
本发明实施例提供的上述技术方案,至少具有如下有益效果:
[0033]
上述方案中,本发明不仅避免了传统酸溶铁合金的物耗高、污染大问题,同时实现了pt与pd、rh的高效分离,解决了铂钯铑分离难题,具有成本低、流程短、节能环保等优点,具有重大的产业化意义。
[0034]
本发明提供了一种fe-pgms合金高效分离提纯pt、pd、rh的方法,通过电解控制电压和电解质组成选择性将fe、pd和rh氧化为fe
2
、pdcl
42-和rhcl
63-进入电解液中,其中fe
2
迁移至阴极析出,而pt以单质形式在阳极泥中富集,实现fe、pt与pd、rh的分离。
[0035]
本发明与传统的先分离铁合金中的fe和pgms、然后再分离提纯pt、pd、rh的技术相比,从源头上分离了pt,简化了pt与pd、rh的分离提纯,不仅提高了pt的直收率和纯度,而且为后续的快速分离pd、rh和提高二者的直收率和纯度奠定了坚实的基础。
[0036]
本发明通过采用lix63选择性萃取分离pd和rh,分离系数高,提高了pd、rh直收率和纯度。
[0037]
综上,本发明具有流程短、物耗能耗低、pgms直收率高、废水近零排放等优势,解决了现有湿法除铁富集pgms废水量大、pgms分离提纯流程长、直收率低等难题,绿色环保,利于工业大规模生产和推广。
附图说明
[0038]
为了更清楚地说明本发明实施例中的技术方案,下面将对实施例描述中所需要使用的附图作简单地介绍,显而易见地,下面描述中的附图仅仅是本发明的一些实施例,对于本领域普通技术人员来讲,在不付出创造性劳动的前提下,还可以根据这些附图获得其他的附图。
[0039]
图1为本发明一种铁合金中铂族金属分离提纯的方法的工艺流程图。
具体实施方式
[0040]
为使本发明要解决的技术问题、技术方案和优点更加清楚,下面将结合附图及具
体实施例进行详细描述。应当注意的是,下述实施例中描述的技术特征或者技术特征的组合不应当被认为是孤立的,它们可以被相互组合从而达到更好的技术效果。在下述实施例的附图中,各附图所出现的相同标号代表相同的特征或者部件,可应用于不同实施例中。
[0041]
实施例1
[0042]
如图1所示,以fe-pgms合金为阳极,其中的pgms质量百分含量为0.1%,以石墨电极为阴极,控制电压0.60v,电解液ph 0,cl-浓度0.01mol/l,so
42-2.0mol/l,fe
2
0.5mol/l,电解结束后,fe在阴极析出,pt富集在阳极泥中,pd和rh分别以pdcl
42-和rhcl
63-溶解在电解液中。
[0043]
采用3.0mol/l hcl、3.0mol/l nacl和1.2倍理论用量的h2o2体系氧化浸出阳极泥中pt,固液比1:10、浸出温度90℃、时间2h,氧化结束后过滤,浸出液经阳离子树脂除杂后,采用体积分数5vol.%的cyanex 921和95vol.%的磺化煤油为萃取剂、sncl2添加量为pt摩尔质量分数的20-40%,有机相与水相体积比为0.5:1,萃取时间为5min;以0.5mol/l hno3反萃、有机相与水相体积比为0.5:1。反萃液用nh4cl沉淀2次进一步除去杂质元素,最后将纯化的氯铂酸铵煅烧,得到纯度99.95%以上的海绵pt。
[0044]
采用水合肼还原电解液中的pd和rh,过滤,滤液返回电解;pd、rh富集物采用王水溶解,溶液经阳离子树脂除杂后,采用体积分数为10vol.%的lix 63和90vol.%的磺化煤油选择性萃取分离pd,有机相与水相体积比为0.5:1,萃取5min后用0.5mol/l ch4n2s反萃,有机相与水相体积比为0.5:1。反萃液经氨水络合、盐酸沉淀1次后,得到纯化的二氯二氨钯沉淀,最后经煅烧得到纯度99.95%以上的海绵pd。
[0045]
萃pd余液用5.0倍rh质量的nano2络合形成na2rh(no2)5,络合温度60℃,络合结束后用na2co3调节ph至7后煮沸,其他离子络合物形成氢氧化物沉淀,过滤后再采用水合肼还原得到rh粉,最后通氢还原得到99.95%以上的海绵rh。
[0046]
其中:fe-pgms合金中pt的直收率为98.2%,pd的直收率为98.6%,rh的直收率为99.1%。
[0047]
实施例2
[0048]
如图1所示,以fe-pgms合金为阳极,其中的pgms质量百分含量为1%,以石墨电极为阴极,控制电压0.62v,电解液ph 1,cl-浓度0.1mol/l,so
42-2.5mol/l,fe
2
0.9mol/l,电解结束后,fe在阴极析出,pt富集在阳极泥中,pd和rh分别以pdcl
42-和rhcl
63-溶解在电解液中。
[0049]
采用5.0mol/l hcl、5.0mol/l nacl和1.3倍理论用量的h2o2体系氧化浸出阳极泥中pt,固液比1:10、浸出温度90℃、时间2h,氧化结束后过滤,浸出液经阳离子树脂除杂后,采用体积分数7vol.%的cyanex 921和93vol.%的磺化煤油为萃取剂、sncl2添加量为pt摩尔质量分数的25%,有机相与水相体积比为0.7:1,萃取时间为10min;以1.2mol/l hno3反萃、有机相与水相体积比为0.7:1。反萃液用nh4cl沉淀3次进一步除去杂质元素,最后将纯化的氯铂酸铵煅烧,得到纯度99.95%以上的海绵pt。
[0050]
采用水合肼还原电解液中的pd和rh,过滤,滤液返回电解;pd、rh富集物采用王水溶解,溶液经阳离子树脂除杂后,采用体积分数为13vol.%的lix63和87vol.%的磺化煤油选择性萃取分离pd,有机相与水相体积比为0.5:1,萃取10min后用3mol/l ch4n2s反萃,有机相与水相体积比为0.5:1。反萃液经氨水络合、盐酸沉淀2次后,得到纯化的二氯二氨钯沉
淀,最后经煅烧得到纯度99.95%以上的海绵pd。
[0051]
萃pd余液用6.0倍rh质量的nano2络合形成na2rh(no2)5,络合温度70℃,络合结束后用na2co3调节ph至8后煮沸,其他离子络合物形成氢氧化物沉淀,过滤后再采用水合肼还原得到rh粉,最后通氢还原得到99.95%以上的海绵rh。
[0052]
其中:fe-pgms合金中pt的直收率为98.2%,pd的直收率为98.8%,rh的直收率为98.4%。
[0053]
实施例3
[0054]
如图1所示,以fe-pgms合金为阳极,其中的pgms质量百分含量为5%,以石墨电极为阴极,控制电压0.66v,电解液ph 1.5,cl-浓度0.3mol/l,so
42-2.9mol/l,fe
2
0.8mol/l,电解结束后,fe在阴极析出,pt富集在阳极泥中,pd和rh分别以pdcl
42-和rhcl
63-溶解在电解液中。
[0055]
采用7.0mol/l hcl、3.0mol/l nacl和1.5倍理论用量的h2o2体系氧化浸出阳极泥中pt,固液比1:10、浸出温度90℃、时间2h,氧化结束后过滤,浸出液经阳离子树脂除杂后,采用体积分数9vol.%的cyanex 921和91vol.%的磺化煤油为萃取剂、sncl2添加量为pt摩尔质量分数的27%,有机相与水相体积比为0.9:1,萃取时间为7min;以2mol/l hno3反萃、有机相与水相体积比为0.9:1。反萃液用nh4cl沉淀2次进一步除去杂质元素,最后将纯化的氯铂酸铵煅烧,得到纯度99.95%以上的海绵pt。
[0056]
采用水合肼还原电解液中的pd和rh,过滤,滤液返回电解;pd、rh富集物采用王水溶解,溶液经阳离子树脂除杂后,采用体积分数为17vol.%的lix 63和83vol.%的磺化煤油选择性萃取分离pd,有机相与水相体积比为1:1,萃取10min后用3mol/l ch4n2s反萃,有机相与水相体积比为1:1。反萃液经氨水络合、盐酸沉淀1次后,得到纯化的二氯二氨钯沉淀,最后经煅烧得到纯度99.95%以上的海绵pd。
[0057]
萃pd余液用7.0倍rh质量的nano2络合形成na2rh(no2)5,络合温度80℃,络合结束后用na2co3调节ph至9后煮沸,其他离子络合物形成氢氧化物沉淀,过滤后再采用水合肼还原得到rh粉,最后通氢还原得到99.95%以上的海绵rh。
[0058]
其中:fe-pgms合金中pt的直收率为98.1%,pd的直收率为98.9%,rh的直收率为98.6%。
[0059]
实施例4
[0060]
如图1所示,以fe-pgms合金为阳极,其中的pgms质量百分含量为10%,以石墨电极为阴极,控制电压0.69v,电解液ph 2.0,cl-浓度0.07mol/l,so
42-3.5mol/l,fe
2
1.7mol/l,电解结束后,fe在阴极析出,pt富集在阳极泥中,pd和rh分别以pdcl
42-和rhcl
63-溶解在电解液中。
[0061]
采用8.0mol/l hcl、4.0mol/l nacl和1.7倍理论用量的h2o2体系氧化浸出阳极泥中pt,固液比1:10、浸出温度90℃、时间2h,氧化结束后过滤,浸出液经阳离子树脂除杂后,采用体积分数12vol.%的cyanex 921和88vol.%的磺化煤油为萃取剂、sncl2添加量为pt摩尔质量分数的35%,有机相与水相体积比为1.5:1,萃取时间为15min;以3mol/l hno3反萃、有机相与水相体积比为1.5:1。反萃液用nh4cl沉淀3次进一步除去杂质元素,最后将纯化的氯铂酸铵煅烧,得到纯度99.95%以上的海绵pt。
[0062]
采用水合肼还原电解液中的pd和rh,过滤,滤液返回电解;pd、rh富集物采用王水
溶解,溶液经阳离子树脂除杂后,采用体积分数为15vol.%的lix 63和85vol.%的磺化煤油选择性萃取分离pd,有机相与水相体积比为1.5:1,萃取20min后用4mol/l ch4n2s反萃,有机相与水相体积比为1.5:1。反萃液经氨水络合、盐酸沉淀1次后,得到纯化的二氯二氨钯沉淀,最后经煅烧得到纯度99.95%以上的海绵pd。
[0063]
萃pd余液用8.0倍rh质量的nano2络合形成na2rh(no2)5,络合温度90℃,络合结束后用na2co3调节ph至9后煮沸,其他离子络合物形成氢氧化物沉淀,过滤后再采用水合肼还原得到rh粉,最后通氢还原得到99.95%以上的海绵rh。
[0064]
其中:fe-pgms合金中pt的直收率为97.8%,pd的直收率为99.2%,rh的直收率为98.3%。
[0065]
实施例5
[0066]
如图1所示,以fe-pgms合金为阳极,其中的pgms质量百分含量为15%,以石墨电极为阴极,控制电压0.72v,电解液ph 2.5,cl-浓度0.5mol/l,so
42-4.0mol/l,fe
2
2.0mol/l,电解结束后,fe在阴极析出,pt富集在阳极泥中,pd和rh分别以pdcl
42-和rhcl
63-溶解在电解液中。
[0067]
采用9.0mol/l hcl、5.0mol/l nacl和1.9倍理论用量的h2o2体系氧化浸出阳极泥中pt,固液比1:10、浸出温度90℃、时间2h,氧化结束后过滤,浸出液经阳离子树脂除杂后,采用体积分数15vol.%的cyanex 921和85vol.%的磺化煤油为萃取剂、sncl2添加量为pt摩尔质量分数的40%,有机相与水相体积比为2:1,萃取时间为5-20min;以2mol/l hno3反萃、有机相与水相体积比为2:1。反萃液用nh4cl沉淀2次进一步除去杂质元素,最后将纯化的氯铂酸铵煅烧,得到纯度99.95%以上的海绵pt。
[0068]
采用水合肼还原电解液中的pd和rh,过滤,滤液返回电解;pd、rh富集物采用王水溶解,溶液经阳离子树脂除杂后,采用体积分数为20vol.%的lix 63和80vol.%的磺化煤油选择性萃取分离pd,有机相与水相体积比为2:1,萃取10min后用4.5mol/l ch4n2s反萃,有机相与水相体积比为2:1。反萃液经氨水络合、盐酸沉淀2次后,得到纯化的二氯二氨钯沉淀,最后经煅烧得到纯度99.95%以上的海绵pd。
[0069]
萃pd余液用7.0倍rh质量的nano2络合形成na2rh(no2)5,络合温度90℃,络合结束后用na2co3调节ph至9后煮沸,其他离子络合物形成氢氧化物沉淀,过滤后再采用水合肼还原得到rh粉,最后通氢还原得到99.95%以上的海绵rh。
[0070]
其中:fe-pgms合金中pt的直收率为98.0%,pd的直收率为98.9%,rh的直收率为99.1%。
[0071]
实施例6
[0072]
如图1所示,以fe-pgms合金为阳极,其中的pgms质量百分含量为20%,以石墨电极为阴极,控制电压0.71v,电解液ph 1.8,cl-浓度0.8mol/l,so
42-2.5mol/l,fe
2
1.5mol/l,电解结束后,fe在阴极析出,pt富集在阳极泥中,pd和rh分别以pdcl
42-和rhcl
63-溶解在电解液中。
[0073]
采用10.0mol/l hcl、3.0mol/l nacl和2.0倍理论用量的h2o2体系氧化浸出阳极泥中pt,固液比1:10、浸出温度90℃、时间2h,氧化结束后过滤,浸出液经阳离子树脂除杂后,采用体积分数14vol.%的cyanex 921和86vol.%的磺化煤油为萃取剂、sncl2添加量为pt摩尔质量分数的23%,有机相与水相体积比为1.6:1,萃取时间为12min;以5mol/l hno3反
萃、有机相与水相体积比为1.6:1。反萃液用nh4cl沉淀2次进一步除去杂质元素,最后将纯化的氯铂酸铵煅烧,得到纯度99.95%以上的海绵pt。
[0074]
采用水合肼还原电解液中的pd和rh,过滤,滤液返回电解;pd、rh富集物采用王水溶解,溶液经阳离子树脂除杂后,采用体积分数为13vol.%的lix 63和87vol.%的磺化煤油选择性萃取分离pd,有机相与水相体积比为0.6:1,萃取20min后用3mol/l ch4n2s反萃,有机相与水相体积比为0.6:1。反萃液经氨水络合、盐酸沉淀2次后,得到纯化的二氯二氨钯沉淀,最后经煅烧得到纯度99.95%以上的海绵pd。
[0075]
萃pd余液用7.2倍rh质量的nano2络合形成na2rh(no2)5,络合温度72℃,络合结束后用na2co3调节ph至8.5后煮沸,其他离子络合物形成氢氧化物沉淀,过滤后再采用水合肼还原得到rh粉,最后通氢还原得到99.95%以上的海绵rh。
[0076]
其中:fe-pgms合金中pt的直收率为98.2%,pd的直收率为98.8%,rh的直收率为99.1%。
[0077]
实施例7
[0078]
如图1所示,以fe-pgms合金为阳极,其中的pgms质量百分含量为25%,以石墨电极为阴极,控制电压0.67v,电解液ph 1.8,cl-浓度0.4mol/l,so
42-2.6mol/l,fe
2
1.4mol/l,电解结束后,fe在阴极析出,pt富集在阳极泥中,pd和rh分别以pdcl
42-和rhcl
63-溶解在电解液中。
[0079]
采用7.0mol/l hcl、5.0mol/l nacl和2.0倍理论用量的h2o2体系氧化浸出阳极泥中pt,固液比1:10、浸出温度90℃、时间2h,氧化结束后过滤,浸出液经阳离子树脂除杂后,采用体积分数10vol.%的cyanex 921和90vol.%的磺化煤油为萃取剂、sncl2添加量为pt摩尔质量分数的36%,有机相与水相体积比为1.2:1,萃取时间为10min;以2.6mol/l hno3反萃、有机相与水相体积比为1.2:1。反萃液用nh4cl沉淀3次进一步除去杂质元素,最后将纯化的氯铂酸铵煅烧,得到纯度99.95%以上的海绵pt。
[0080]
采用水合肼还原电解液中的pd和rh,过滤,滤液返回电解;pd、rh富集物采用王水溶解,溶液经阳离子树脂除杂后,采用体积分数为15vol.%的lix 63和85vol.%的磺化煤油选择性萃取分离pd,有机相与水相体积比为0.9:1,萃取8min后用3.1mol/l ch4n2s反萃,有机相与水相体积比为0.9:1。反萃液经氨水络合、盐酸沉淀2次后,得到纯化的二氯二氨钯沉淀,最后经煅烧得到纯度99.95%以上的海绵pd。
[0081]
萃pd余液用5.8倍rh质量的nano2络合形成na2rh(no2)5,络合温度68℃,络合结束后用na2co3调节ph至7.2后煮沸,其他离子络合物形成氢氧化物沉淀,过滤后再采用水合肼还原得到rh粉,最后通氢还原得到99.95%以上的海绵rh。
[0082]
其中:fe-pgms合金中pt的直收率为97.4%,pd的直收率为98.3%,rh的直收率为98.5%。
[0083]
实施例8
[0084]
如图1所示,以fe-pgms合金为阳极,其中的pgms质量百分含量为30%,以石墨电极为阴极,控制电压0.60v,电解液ph 2.5,cl-浓度1.0mol/l,so
42-2.0mol/l,fe
2
0.5mol/l,电解结束后,fe在阴极析出,pt富集在阳极泥中,pd和rh分别以pdcl
42-和rhcl
63-溶解在电解液中。
[0085]
采用10.0mol/l hcl、3.0mol/l nacl和1.8倍理论用量的h2o2体系氧化浸出阳极泥
中pt,固液比1:10、浸出温度90℃、时间2h,氧化结束后过滤,浸出液经阳离子树脂除杂后,采用体积分数7vol.%的cyanex 921和93vol.%的磺化煤油为萃取剂、sncl2添加量为pt摩尔质量分数的34%,有机相与水相体积比为0.5:1,萃取时间为20min;以0.5mol/l hno3反萃、有机相与水相体积比为0.5:1。反萃液用nh4cl沉淀3次进一步除去杂质元素,最后将纯化的氯铂酸铵煅烧,得到纯度99.95%以上的海绵pt。
[0086]
采用水合肼还原电解液中的pd和rh,过滤,滤液返回电解;pd、rh富集物采用王水溶解,溶液经阳离子树脂除杂后,采用体积分数为10vol.%的lix 63和90vol.%的磺化煤油选择性萃取分离pd,有机相与水相体积比为2:1,萃取15min后用2mol/l ch4n2s反萃,有机相与水相体积比为2:1。反萃液经氨水络合、盐酸沉淀1次后,得到纯化的二氯二氨钯沉淀,最后经煅烧得到纯度99.95%以上的海绵pd。
[0087]
萃pd余液用6.3倍rh质量的nano2络合形成na2rh(no2)5,络合温度78℃,络合结束后用na2co3调节ph至8.2后煮沸,其他离子络合物形成氢氧化物沉淀,过滤后再采用水合肼还原得到rh粉,最后通氢还原得到99.95%以上的海绵rh。
[0088]
其中:fe-pgms合金中pt的直收率为99.0%,pd的直收率为98.3%,rh的直收率为98.6%。
[0089]
实施例9
[0090]
如图1所示,以fe-pgms合金为阳极,其中的pgms质量百分含量为0.7%,以石墨电极为阴极,控制电压00.72v,电解液ph 0,cl-浓度0.01mol/l,so
42-2.0mol/l,fe
2
2.0mol/l,电解结束后,fe在阴极析出,pt富集在阳极泥中,pd和rh分别以pdcl
42-和rhcl
63-溶解在电解液中。
[0091]
采用6.0mol/l hcl、4.0mol/l nacl和1.5倍理论用量的h2o2体系氧化浸出阳极泥中pt,固液比1:10、浸出温度90℃、时间2h,氧化结束后过滤,浸出液经阳离子树脂除杂后,采用体积分数13vol.%的cyanex 921和87vol.%的磺化煤油为萃取剂、sncl2添加量为pt摩尔质量分数的23%,有机相与水相体积比为0.9:1,萃取时间为12min;以3mol/l hno3反萃、有机相与水相体积比为0.9:1。反萃液用nh4cl沉淀3次进一步除去杂质元素,最后将纯化的氯铂酸铵煅烧,得到纯度99.95%以上的海绵pt。
[0092]
采用水合肼还原电解液中的pd和rh,过滤,滤液返回电解;pd、rh富集物采用王水溶解,溶液经阳离子树脂除杂后,采用体积分数为11vol.%的lix 63和89vol.%的磺化煤油选择性萃取分离pd,有机相与水相体积比为0.7:1,萃取10min后用1mol/l ch4n2s反萃,有机相与水相体积比为0.7:1。反萃液经氨水络合、盐酸沉淀2次后,得到纯化的二氯二氨钯沉淀,最后经煅烧得到纯度99.95%以上的海绵pd。
[0093]
萃pd余液用7.3倍rh质量的nano2络合形成na2rh(no2)5,络合温度80℃,络合结束后用na2co3调节ph至7后煮沸,其他离子络合物形成氢氧化物沉淀,过滤后再采用水合肼还原得到rh粉,最后通氢还原得到99.95%以上的海绵rh。
[0094]
其中:fe-pgms合金中pt的直收率为98.0%,pd的直收率为99.2%,rh的直收率为98.8%。
[0095]
实施例10
[0096]
如图1所示,以fe-pgms合金为阳极,其中的pgms质量百分含量为23%,以石墨电极为阴极,控制电压0.69v,电解液ph 1.5,cl-浓度0.4mol/l,so
42-2.3mol/l,fe
2
2.0mol/l,电
解结束后,fe在阴极析出,pt富集在阳极泥中,pd和rh分别以pdcl
42-和rhcl
63-溶解在电解液中。
[0097]
采用3.0mol/l hcl、7.0mol/l nacl和2.0倍理论用量的h2o2体系氧化浸出阳极泥中pt,固液比1:10、浸出温度90℃、时间2h,氧化结束后过滤,浸出液经阳离子树脂除杂后,采用体积分数9vol.%的cyanex 921和91vol.%的磺化煤油为萃取剂、sncl2添加量为pt摩尔质量分数的31%,有机相与水相体积比为1.4:1,萃取时间为10min;以4.5mol/l hno3反萃、有机相与水相体积比为1.4:1。反萃液用nh4cl沉淀2次进一步除去杂质元素,最后将纯化的氯铂酸铵煅烧,得到纯度99.95%以上的海绵pt。
[0098]
采用水合肼还原电解液中的pd和rh,过滤,滤液返回电解;pd、rh富集物采用王水溶解,溶液经阳离子树脂除杂后,采用体积分数为17vol.%的lix 63和83vol.%的磺化煤油选择性萃取分离pd,有机相与水相体积比为1.3:1,萃取7min后用4.2mol/l ch4n2s反萃,有机相与水相体积比为1.3:1。反萃液经氨水络合、盐酸沉淀2次后,得到纯化的二氯二氨钯沉淀,最后经煅烧得到纯度99.95%以上的海绵pd。
[0099]
萃pd余液用7.3倍rh质量的nano2络合形成na2rh(no2)5,络合温度73℃,络合结束后用na2co3调节ph至9后煮沸,其他离子络合物形成氢氧化物沉淀,过滤后再采用水合肼还原得到rh粉,最后通氢还原得到99.95%以上的海绵rh。
[0100]
其中:fe-pgms合金中pt的直收率为98.1%,pd的直收率为98.5%,rh的直收率为99.0%。
[0101]
上述方案中,本发明不仅避免了传统酸溶铁合金的物耗高、污染大问题,同时实现了pt与pd、rh的高效分离,解决了铂钯铑分离难题,具有成本低、流程短、节能环保等优点,具有重大的产业化意义。
[0102]
本发明提供了一种fe-pgms合金高效分离提纯pt、pd、rh的方法,通过电解控制电压和电解质组成选择性将fe、pd和rh氧化为fe
2
、pdcl
42-和rhcl
63-进入电解液中,其中fe
2
迁移至阴极析出,而pt以单质形式在阳极泥中富集,实现fe、pt与pd、rh的分离。
[0103]
本发明与传统的先分离铁合金中的fe和pgms、然后再分离提纯pt、pd、rh的技术相比,从源头上分离了pt,简化了pt与pd、rh的分离提纯,不仅提高了pt的直收率和纯度,而且为后续的快速分离pd、rh和提高二者的直收率和纯度奠定了坚实的基础。
[0104]
本发明通过采用lix63选择性萃取分离pd和rh,分离系数高,提高了pd、rh直收率和纯度。
[0105]
综上,本发明具有流程短、物耗能耗低、pgms直收率高、废水近零排放等优势,解决了现有湿法除铁富集pgms废水量大、pgms分离提纯流程长、直收率低等难题,绿色环保,利于工业大规模生产和推广。
[0106]
以上所述是本发明的优选实施方式,应当指出,对于本技术领域的普通技术人员来说,在不脱离本发明所述原理的前提下,还可以做出若干改进和润饰,这些改进和润饰也应视为本发明的保护范围。
再多了解一些
本文用于企业家、创业者技术爱好者查询,结果仅供参考。