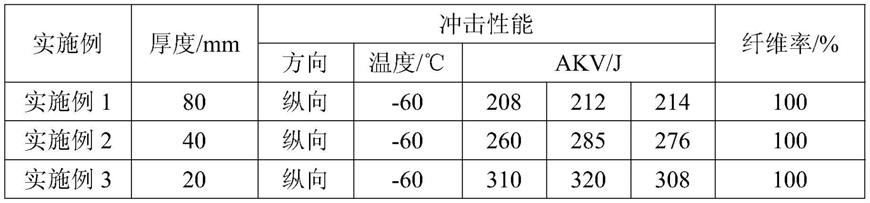
1.本发明涉及钢的冶炼技术领域,具体涉及一种低屈强比高韧性钢及其制备方法。
背景技术:
2.随着大型结构桥梁、建筑向大跨度、重载荷、全焊接结构方向发展,桥梁结构的安全可靠性要求越来越严格,也对钢材质量提出了更高的要求。一般来说,钢材强度提高,钢材屈强比也会随之升高,如果屈强比过高,一旦结构发生过载,如地震等条件下,钢材容易快速到达极限强度从而引发事故。因此,高屈强比限制了高强度钢在桥梁、建筑工程上的应用,低屈强比、高强、高韧、高塑是桥梁、建筑发展的必然趋势。
3.中国专利申请cn111455287a公开了一种成分为c:0.04%~0.09%、v:0.010%~0.030%,ni:0.30%~0.45%,cr:0.45%~0.60%,mo:0.08%~0.15%,余量的fe及不可避免的杂质的500mpa低屈强比耐候桥梁钢,合金添加量高,生产成本高。
4.中国专利申请cn102080192a公开了一种低屈强比高塑性超细晶粒高强钢的制造方法,其采用两相区淬火 两相区回火,生产周期长,组织困难,成本高。
5.中国专利申请cn109161793a公开了一种成分为c:0.08~0.10%,si:0.25~0.30%,mn:1.30~1.50%,p≤0.010%,s≤0.010%,ni:0.25~0.30%,cr:0.45~0.50%,cu:0.25~0.35%,al:0.02~0.04%,nb:0.020~0.030%,ti:0.010~0.020%,余量为fe和不可避免的杂质元素的低屈强比高强度桥梁用钢,合金添加量高,生产成本高。
技术实现要素:
6.针对现有低屈强比钢合金元素cu、cr、ni添加量偏高的技术问题,本发明提供一种低屈强比高韧性钢及其制备方法,本发明采用低成本微合金化设计,配合tmcp工艺,添加合金元素cu、cr、ni改善焊接性能、低温韧性、屈强比及综合力学性能,降低了贵重元素用量,制备方法生产成本低、工艺简单,适用于大工业稳定生产,制得的低屈强比高韧性钢的组织细小均匀,主要为铁素体 贝氏体组织,具有优异的强韧性、强塑性、低屈强比、焊接性能等性能,适用于大型建筑和桥梁结构件制造领域。经本发明制造的钢板屈服强度可稳定达到500mpa以上,-60℃低温冲击功稳定达到大于200j,满足现代钢结构工程建设、桥梁对高强高韧低屈强比高性能钢板的要求,同时具备较高耐候性、较低的碳当量及焊接敏感系数。
7.第一方面,本发明提供一种低屈强比高韧性钢的制备方法,包括如下步骤:
8.(1)原料通过冶炼、精炼、合金化、钙处理,得到钢水,最终连铸成铸坯,铸坯化学成分重量百分比符合c:0.09%~0.11%,si:0.10%~0.20%,mn:1.40%~1.50%,p≤0.015%,s≤0.003%,als:0.010%~0.040%,cr:0.15%~0.25%,cu:0.15%~0.20%,ni:0.20%~0.30%,nb:0.025%~0.040%,ti:0.010%~0.040%,其余为fe和不可避免的杂质,铸坯切割后缓冷;
9.(2)加热;
10.(3)采用二阶段轧制,第一阶段采用横-纵轧制方式,第一阶段轧制完毕后加速冷
却中间坯,冷却至730~735℃;当返红温度到达760~765℃进行第二阶段轧制,第二阶段轧制完毕后弛豫到钢板表面720~725℃;
11.(4)钢板轧后水冷;
12.(5)堆冷。
13.其中步骤(3)~(5)属于控轧控冷(tmcp)工艺。
14.进一步的,所述步骤(1)采用转炉冶炼,顶底复吹,充分脱碳、脱磷;通过lf/rh精炼,降低有害元素/杂质含量,进行微合金化;全程保护浇铸,浇铸末端采用重压下技术。
15.进一步的,所述步骤(1)lf/rh精炼过程中,真空达到100pa以下,保压时间≥15min,纯脱气时间≥10min,软吹时间≥10min,rh处理后镇静时间≥40min,重压下的压下率≥12%。
16.进一步的,所述步骤(1)铸坯开始缓冷温度≥500℃,缓冷时间不少于72h。
17.进一步的,所述步骤(2)采用预热段、加热段和均热段的三段加热工艺,其中,
18.预热段温度设定为700℃~850℃;
19.加热段分为加热一段和加热二段,加热一段温度设定为1050℃~1200℃,加热二段温度设定为1180℃~1230℃;
20.均热段温度设定为1150℃~1200℃;
21.出钢铸坯温度为1150℃~1180℃。
22.进一步的,所述步骤(4)的开冷温度为720~725℃,终冷温度为250℃~300℃,冷却速度6~26℃/s。
23.进一步的,所述步骤(5)为钢板水冷后,快速将钢板放在300℃~400℃钢板间堆冷,堆冷时间不少于24h。
24.第二方面,本发明提供一种采用上述制备方法制得的低屈强比高韧性钢。
25.进一步的,所述低屈强比高韧性钢的厚度≤80mm。
26.进一步的,所述低屈强比高韧性钢的屈服强度≥500mpa,抗拉强度≥640mpa,断后伸长率≥20.0%,屈强比≤0.80,-60kv2》200j。
27.化学成分是影响钢板综合性能的重要因素之一,对本发明的化学成分范围说明如下。
28.c:钢中主要的固溶强化元素,能够显著提高钢板强度,但较高的碳含量对钢板焊接、韧性及塑性不利。为有效减少偏析,提高显微组织均匀性,避免异相之间的电位差引起原电池腐蚀,提高钢的耐蚀性能,同时考虑经济性;因此限定其质量百分比含量为c:0.09%~0.011%。
29.si:硅是炼钢过程有效的脱氧和放热元素之一,有一定的固溶强化作用,有利于致密锈层的形成,能提高钢的耐大气腐蚀性能,但硅含量过高会降低钢的表面质量、焊接性能和低温韧性,本发明硅含量控制在0.10%~0.20%。
30.mn:锰具有较强的固溶强化作用,能显著降低钢的相变温度,细化钢的显微组织,而且成本低廉,是提高强度的有效元素,为了实现足够高的拉伸强度,获得低屈强比,含量不应低于0.80%;但含量过高容易造成铸坯偏析,会形成带状组织,降低钢板的可焊性和焊接热影响区韧性,以及耐腐蚀性;本发明锰含量控制在1.40%~1.50%。
31.p:磷能提高钢的耐候性,增加钢的冷脆性,恶化焊接性能;因而本发明不采用高含
量的磷来增加耐候性,而是通过其它合金元素的合理组合来达到高的耐腐蚀性能;本发明磷含量控制在≤0.015%。
32.s:硫使钢产生热脆,降低钢的延展性和韧性,还促进钢板的各向异性,并且硫化物夹杂还显著降低钢的耐腐蚀性能,应严格控制钢中的硫含量;本发明硫含量控制在≤0.003%。
33.al:铝是炼钢过程有效的脱氧元素之一,可有效减少钢中夹杂物含量,细化晶粒,但含量过高,容易使铸坯表面产生裂纹,本发明铝含量控制在0.010%~0.040%。
34.cr:铬不仅是提高钢淬透性的元素,还是提高钢耐候性的有效元素之一,本发明采用铬提高钢的淬透性,因此铬含量不能过低;另一方面,铬含量过高将影响钢的韧性,且焊接性也会变差,因而cr含量宜控制在0.15%~0.25%。
35.cu:铜是提高钢耐候性的有效元素之一,它的电化学电位比高,能够使钢板表面的铁锈致密化,促进稳定锈层的形成,但含量过高时将引起钢坯在加热或热轧过程中产生裂纹,恶化钢板表面性能,铜应控制在0.15%~0.20%。
36.ni:镍可以改善钢板耐候性,可防止铜脆现象发生,降低浇铸、热轧及焊接过程的热裂纹敏感性,此外,镍也是钢板获得优良低温韧性不可缺少的合金元素,但是成本高;综合考虑,镍应控制在0.20%~0.30%。
37.nb:铌是细晶强化的重要元素之一,提高奥氏体再结晶温度,阻止奥氏体再结晶和抑制晶粒长大,细化奥氏体晶粒;其碳氮化物在位错上析出和奥氏体晶界偏聚,提高强度和韧性;但铌含量过高,铸坯容易产生表面裂纹,同时恶化焊接性能,本发明铌含量控制在0.025%~0.040%。
38.ti:产生强烈的沉淀强化及中等程度的晶粒细化作用,钢中加入微量的钛,目的是与钢中氮结合,生成稳定性很高的氮化钛粒子,抑制焊接haz区奥氏体晶粒长大和改变二次相变产物,改善大线能量焊接的低温韧性。钢中添加的钛含量要与钢中的氮含量匹配,当加入钛含量过少,形成氮化钛粒子数量不足,不足以抑制haz的奥氏体晶粒长大和改变二次相变产物而改善大线能量焊接haz的低温韧性,加入钛含量过多时,在钢液凝固过程中析出大尺寸的氮化钛粒子,这种大尺寸粒子不但不能抑制haz的奥氏体晶粒长大,反而成为裂纹萌生的起始点;本发明钛含量控制在0.010%~0.040%。
39.本发明的有益效果在于:
40.1.本发明涉及钢成分设计简单,微观组织均匀性好,加工性能好,极佳的强韧性匹配,优异的低温韧性,80mm厚钢板-60℃低温冲击功大于200j,同时具有优异的焊接性能、低屈强比、耐疲劳和耐腐蚀性能。
41.2.本发明涉及钢具有较高强度、低温韧性、低屈强比,相对普通高强度低合金钢,止裂性能、加工性能、抗震性能优异,可应用于建筑、桥梁及户外塔架等安全性要求高的结构件制造领域。
42.3.本发明涉及钢采用低碳 微量cu、cr、ni等合金元素,不依赖粗轧大压下率,通过tmcp工艺生产,生产周期短、成本低,利于推广应用。
具体实施方式
43.为了使本技术领域的人员更好地理解本发明中的技术方案,下面将对本发明实施
例中的技术方案进行清楚、完整地描述,显然,所描述的实施例仅仅是本发明一部分实施例,而不是全部的实施例。基于本发明中的实施例,本领域普通技术人员在没有做出创造性劳动前提下所获得的所有其他实施例,都应当属于本发明保护的范围。
44.实施例1
45.一种厚度为80mm的低屈强比高韧性钢,化学成分为c:0.11%,si:0.20%,mn:1.46%,p:0.009%,s:0.003%,als:0.031%,cr:0.23%,cu:0.20%,ni:0.24%,nb:0.035%,ti:0.018%,其余为fe和不可避免的杂质。
46.该低屈强比高韧性钢的工艺流程为铁水预处理
→
bof炼钢
→
lf精炼
→
rh真空处理
→
连铸
→
缓冷
→
铸坯检验、清理、判定
→
加热
→
除鳞
→
轧制
→
冷却
→
堆冷
→
探伤
→
喷印标识
→
切割取样
→
入库。过程关键参数控制如下:
47.(1)原料采用转炉冶炼,顶底复吹,充分脱碳、脱磷,通过lf/rh精炼,真空达到100pa以下,保压时间为16min,纯脱气时间为10min,软吹时间为12min,rh处理后镇静时间为43min,降低有害元素/杂质含量,进行微合金化、钙处理,得到钢水,全程保护浇铸,浇铸末端采用重压下技术,重压下的压下率为12.2%,最终连铸成铸坯,铸坯化学成分与最终成品对应,铸坯切割后于700℃开始缓冷,缓冷时间为73h;
48.(2)采用预热段、加热段和均热段的三段加热工艺,其中,
49.预热段温度设定为700℃~850℃;
50.加热段分为加热一段和加热二段,加热一段温度设定为1050℃~1200℃,加热二段温度设定为1180℃~1230℃;
51.均热段温度设定为1150℃~1200℃;
52.出钢铸坯温度为1180℃;
53.(3)采用二阶段轧制,第一阶段采用横-纵轧制方式,第一阶段轧制完毕后加速冷却中间坯,冷却至734℃;当返红温度到达762℃进行第二阶段轧制,第二阶段轧制完毕后弛豫到钢板表面722℃;
54.(4)水冷开冷温度为722℃,终冷温度为260℃,冷却速度7℃/s;
55.(5)钢板水冷后,快速将钢板放在300~400℃钢板间堆冷,堆冷时间40h。
56.实施例2
57.一种厚度为40mm的低屈强比高韧性钢,化学成分为c:0.09%,si:0.18%,mn:1.42%,p:0.010%,s:0.002%,al:0.032%,cr:0.21%,cu:0.16%,ni:0.21%,nb:0.032%,ti:0.017%,其余为fe和不可避免的杂质。
58.该低屈强比高韧性钢的工艺流程为铁水预处理
→
bof炼钢
→
lf精炼
→
rh真空处理
→
连铸
→
缓冷
→
铸坯检验、清理、判定
→
加热
→
除鳞
→
轧制
→
冷却
→
堆冷
→
探伤
→
喷印标识
→
切割取样
→
入库。过程关键参数控制如下:
59.(1)原料采用转炉冶炼,顶底复吹,充分脱碳、脱磷,通过lf/rh精炼,真空达到100pa以下,保压时间为17min,纯脱气时间为10min,软吹时间为11min,rh处理后镇静时间为41min,降低有害元素/杂质含量,进行微合金化、钙处理,得到钢水,全程保护浇铸,浇铸末端采用重压下技术,重压下的压下率为12.3%,最终连铸成铸坯,铸坯化学成分与最终成品对应,铸坯切割后于600℃开始缓冷,缓冷时间为72h;
60.(2)采用预热段、加热段和均热段的三段加热工艺,其中,
61.预热段温度设定为700℃~850℃;
62.加热段分为加热一段和加热二段,加热一段温度设定为1050℃~1200℃,加热二段温度设定为1180℃~1230℃;
63.均热段温度设定为1150℃~1200℃;
64.出钢铸坯温度为1190℃;
65.(3)采用二阶段轧制,第一阶段采用横-纵轧制方式,第一阶段轧制完毕后加速冷却中间坯,冷却至732℃;当返红温度到达761℃进行第二阶段轧制,第二阶段轧制完毕后弛豫到钢板表面723℃;
66.(4)水冷开冷温度为723℃,终冷温度为263℃,冷却速度12℃/s;
67.(5)钢板水冷后,快速将钢板放在300~400℃钢板间堆冷,堆冷时间36h。
68.实施例3
69.一种厚度为20mm的低屈强比高韧性钢,化学成分为c:0.09%,si:0.18%,mn:1.42%,p:0.010%,s:0.002%,al:0.032%,cr:0.21%,cu:0.16%,ni:0.21%,nb:0.032%,ti:0.017%。
70.该低屈强比高韧性钢的工艺流程为铁水预处理
→
bof炼钢
→
lf精炼
→
rh真空处理
→
连铸
→
缓冷
→
铸坯检验、清理、判定
→
加热
→
除鳞
→
轧制
→
冷却
→
堆冷
→
探伤
→
喷印标识
→
切割取样
→
入库。过程关键参数控制如下:
71.(1)原料采用转炉冶炼,顶底复吹,充分脱碳、脱磷,通过lf/rh精炼,真空达到100pa以下,保压时间为17min,纯脱气时间为10min,软吹时间为11min,rh处理后镇静时间为41min,降低有害元素/杂质含量,进行微合金化、钙处理,得到钢水,全程保护浇铸,浇铸末端采用重压下技术,重压下的压下率为12.3%,最终连铸成铸坯,铸坯化学成分与最终成品对应,铸坯切割后于600℃开始缓冷,缓冷时间为72h;
72.(2)采用预热段、加热段和均热段的三段加热工艺,其中,
73.预热段温度设定为700℃~850℃;
74.加热段分为加热一段和加热二段,加热一段温度设定为1050℃~1200℃,加热二段温度设定为1180℃~1230℃;
75.均热段温度设定为1150℃~1200℃;
76.出钢铸坯温度为1200℃;
77.(3)采用二阶段轧制,第一阶段采用横-纵轧制方式,第一阶段轧制完毕后加速冷却中间坯,冷却至730℃;当返红温度到达763℃进行第二阶段轧制,第二阶段轧制完毕后弛豫到钢板表面722℃;
78.(4)水冷开冷温度为722℃,终冷温度为264℃,冷却速度16℃/s;
79.(5)钢板水冷后,快速将钢板放在300~400℃钢板间堆冷,堆冷时间25h。
80.对实施例1~3的低屈强比高韧性钢的拉伸性能和低温韧性进行测试,解释结果如下表1~2所示。
81.表1钢板的拉伸性能
82.实施例厚度/mm屈服强度/mpa抗拉强度/mpa断后伸长率/%屈强比实施例18053070021.50.76实施例24054571022.00.77
实施例32054071523.50.76
83.表2钢板的低温韧性
[0084][0085]
尽管通过优选实施例的方式对本发明进行了详细描述,但本发明并不限于此。在不脱离本发明的精神和实质的前提下,本领域普通技术人员可以对本发明的实施例进行各种等效的修改或替换,而这些修改或替换都应在本发明的涵盖范围内/任何熟悉本技术领域的技术人员在本发明揭露的技术范围内,可轻易想到变化或替换,都应涵盖在本发明的保护范围之内。
再多了解一些
本文用于企业家、创业者技术爱好者查询,结果仅供参考。