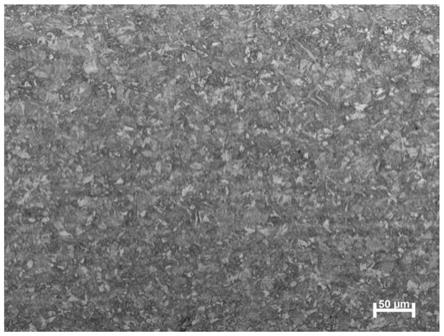
一种屈服强度960mpa级高强钢板及其制造方法
技术领域
1.本发明涉及金属材料制造技术领域,具体涉及一种屈服强度960mpa级高强钢板及其制造方法。
背景技术:
2.近年来,工程机械行业日益呈现大型化、轻量化、智能化以及参与国际化竞争的发展趋势,工程机械用钢量增长趋势明显,高强度结构钢被视为工程机械行业的关键材料,强度级别越来越高的高强钢产品被广泛应用于起重机、履带吊、装载机等大型装备的关键部位,这些部位因承载力大、受力情况复杂、使用环境苛刻等条件,普遍使用屈服强度在700mpa~900mpa甚至更高级别的高强钢产品,以达到轻量化、安全高效、节能环保的行业发展需求。目前对于960mpa级高强钢的生产,普遍采用调质(离线淬火 高温回火)的热处理方式,配合钢中高含量的mn、cr、mo、ni、nb、v等合金元素,以达到高强度的目标,这种方式生产成本高,势必造成矿产资源和能源的消耗。如何做到既能节约生产成本、又能获得性能优异的钢板,已成为目前工程机械用高级别高强度结构钢生产的重要难题。
3.中国专利申请cn201410810301.0公开一种屈服强度900~1000mpa级调质高强钢的生产方法,其不足之处在于同时添加了cr、mo、ni、v、nb等合金元素,合金成本较高;且采用了离线淬火 400~550℃回火的热处理方法,增加了热处理成本和能源消耗。
4.中国专利申请cn201010291575.5公开一种屈服强度1000mpa级高强韧钢板的生产方法,其不足之处在于同时添加了cr、mo、ni、v、nb等合金元素,合金成本较高,且c含量(0.05~0.08%)过低,会造成炼钢脱碳时间长,生产效率低,mn含量(1.0~2.0%)偏高,易造成铸坯mn元素的偏析,从而导致铸坯低倍质量下降;另外该技术方案采用了400~600℃回火,回火温度较高,不利于节约能源,生产成本势必会增加。
5.现有技术对于屈服强度960mpa级高强钢板的生产,存在合金成本高、生产工艺流程长、热处理成本高等不足之处,无法满足现阶段钢铁行业对于低成本、节能环保、高效制造的生产需求。
技术实现要素:
6.针对屈服强度960mpa级高强钢的现有生产工艺存在的合金成本高、生产工艺流程长、热处理成本高问题,本发明提供一种屈服强度960mpa级高强钢板及其制造方法,以实现超低成本为目标,通过纯净化冶炼、连铸、轧制、冷却和热处理等工序,生产出的钢板屈服强度rp
0.2
:980~1060mpa、抗拉强度rm:1010~1090mpa、断后伸长率a:11~17%、-40℃冲击吸收功kv2:60~180j,具有生产成本低、工艺流程短、质量稳定、易焊接、易于工业化大批量生产的特点。
7.第一方面,本发明提供一种屈服强度960mpa级高强钢板的制造方法,包括如下步骤:
8.(1)冶炼:按重量百分比计,熔炼化学成分为c:0.14%~0.18%、si:0.10%~
0.40%、mn:0.80%~1.20%、p≤0.010%、s≤0.003%、ni:0.30%~0.60%、cr:0.10%~0.40%、nb:0.010%~0.050%、ti:0.008%~0.025%、als:0.020%~0.050%、b:0.0010%~0.0025%、o≤0.0030%、n≤0.0040%、h≤0.0002%,其余为铁及不可避免的杂质,碳当量(cev)=c mn/6 (ni cu)/15 (cr mo v)/5≤0.50%;
9.(2)连铸:铸坯厚度为150~300mm;
10.(3)加热:加热后出炉温度控制在1220~1260℃;
11.(4)轧制:粗轧开轧温度1140~1180℃,粗轧阶段全程高温轧制(1100~1180℃),同时结合大压下量实现钢板的心部组织渗透变形,至少有2~3道次的轧制压下率≥20%,中间坯厚度为成品厚度的2.5倍以上;精轧开轧温度为960~1000℃,精轧终轧温度为880~920℃;
12.(5)dq水冷:开冷温度≥850℃,终冷温度≤180℃;
13.(6)回火:回火加热温度为150~300℃,保温时间为40~90min,得到成品。
14.进一步的,所述步骤(2)控制中间包过热度在10~20℃,全程保护浇注,对铸坯堆垛缓冷。
15.进一步的,所述步骤(2)的堆垛缓冷采用热坯下铺上盖方式,四周用热坯包围,避免吹风,冷却时间为48h以上。
16.进一步的,所述步骤(3)的加热时间为3~5h。
17.进一步的,所述步骤(4)粗轧前进行高压水除鳞,除鳞水压力≥23mpa。
18.进一步的,所述步骤(5)控制冷却速度为18~30℃/s。
19.第二方面,本发明提供一种采用上述制造方法生产的屈服强度960mpa级高强钢板。
20.进一步的,所述屈服强度960mpa级高强钢板的厚度为10~30mm。
21.本发明的有益效果在于:
22.(1)优化合金成分设计,无需添加mo、v、cu等贵重金属元素,并严格控制cr、ni、nb、ti等合金元素的含量,实现超低成本合金成分设计;(2)无需离线淬火,采用在线淬火(dq水冷) 低温回火工艺,大大缩短了工艺流程和降低了热处理成本,减少了能源消耗;(3)实现了较低碳当量(cev≤0.50%)成分设计,钢板焊接性能好。
23.本发明提供的屈服强度960mpa级高强钢板屈服强度rp
0.2
:980~1060mpa、抗拉强度rm:1010~1090mpa、断后伸长率a:11~17%、-40℃冲击吸收功kv2:60~180j,性能富余量合适,质量稳定。
附图说明
24.为了更清楚地说明本发明实施例或现有技术中的技术方案,下面将对实施例或现有技术描述中所需要使用的附图作简单地介绍,显而易见地,对于本领域普通技术人员而言,在不付出创造性劳动的前提下,还可以根据这些附图获得其他的附图。
25.图1是本发明实施例1生产的屈服强度960mpa级高强钢板的典型金相组织图片。
26.图2是本发明实施例2生产的屈服强度960mpa级高强钢板的典型金相组织图片。
具体实施方式
27.为了使本技术领域的人员更好地理解本发明中的技术方案,下面将结合本发明实施例中的附图,对本发明实施例中的技术方案进行清楚、完整地描述,显然,所描述的实施例仅仅是本发明一部分实施例,而不是全部的实施例。基于本发明中的实施例,本领域普通技术人员在没有做出创造性劳动前提下所获得的所有其他实施例,都应当属于本发明保护的范围。
28.实施例1
29.厚度为10mm的屈服强度960mpa级高强钢板,采用如下制造方法制得:
30.(1)冶炼:按照熔炼化学成分c:0.15%、si:0.26%、mn:0.96%、p:0.007%、s:0.001%、ni:0.45%、cr:0.24%、nb:0.034%、ti:0.016%、als:0.035%、b:0.0013%、o:0.0021%、n:0.0029%、h:0.00014%,其余为铁及不可避免的杂质,cev=0.39%冶炼,严格控制s、p、o、n、h等有害元素及夹杂物;
31.(2)连铸:中间包过热度控制在10~20℃,全程保护浇注;铸坯厚度为150mm,对铸坯堆垛缓冷52h,采用热坯下铺上盖,四周用热坯包围,避免吹风;
32.(3)加热:连铸坯进行再加热,加热时间为3.3h,加热后出炉温度为1251℃;
33.(4)轧制:加热后的连铸坯进行高压水除鳞,除鳞水压力≥23mpa;粗轧开轧温度为1172℃,其中后2道次的轧制压下率≥20%,中间坯厚度为40mm;精轧开轧温度为994℃,精轧终轧温度892℃;
34.(5)dq水冷:开冷温度为853℃,终冷温度为160℃,冷却速度控制在18~30℃/s;
35.(6)回火:回火加热温度为280℃,保温时间为40min,得到成品。
36.对该钢板的力学性能进行测试,结果如下表1所示。
37.表1实施例1钢板的力学性能
[0038][0039]
实施例2
[0040]
厚度为30mm的屈服强度960mpa级高强钢板,采用如下制造方法制得:
[0041]
(1)冶炼:按照熔炼化学成分c:0.17%、si:0.35%、mn:1.15%、p:0.006%、s:0.001%、ni:0.56%、cr:0.39%、nb:0.044%、ti:0.018%、als:0.040%、b:0.0018%、o:0.0018%、n:0.0026%、h:0.00012%,其余为铁及不可避免的杂质,cev=0.48%冶炼,严格控制s、p、o、n、h等有害元素及夹杂物;
[0042]
(2)连铸:中间包过热度控制在10~20℃,全程保护浇注;铸坯厚度为300mm,对铸坯堆垛缓冷60h,采用热坯下铺上盖,四周用热坯包围,避免吹风;
[0043]
(3)加热:连铸坯进行再加热,加热时间为4.9h,加热后出炉温度为1238℃;
[0044]
(4)轧制:加热后的连铸坯进行高压水除鳞,除鳞水压力≥23mpa;粗轧开轧温度为1154℃,其中后3道次的轧制压下率≥20%,中间坯厚度为85mm;精轧开轧温度为968℃,精轧终轧温度914℃;
[0045]
(5)dq水冷:开冷温度为887℃,终冷温度为162℃,冷却速度控制在18~30℃/s;
[0046]
(6)回火:回火加热温度为230℃,保温时间为80min,得到成品。
[0047]
对该钢板的力学性能进行测试,结果如下表2所示。
[0048]
表2实施例2钢板的力学性能
[0049][0050]
尽管通过参考附图并结合优选实施例的方式对本发明进行了详细描述,但本发明并不限于此。在不脱离本发明的精神和实质的前提下,本领域普通技术人员可以对本发明的实施例进行各种等效的修改或替换,而这些修改或替换都应在本发明的涵盖范围内/任何熟悉本技术领域的技术人员在本发明揭露的技术范围内,可轻易想到变化或替换,都应涵盖在本发明的保护范围之内。
再多了解一些
本文用于企业家、创业者技术爱好者查询,结果仅供参考。