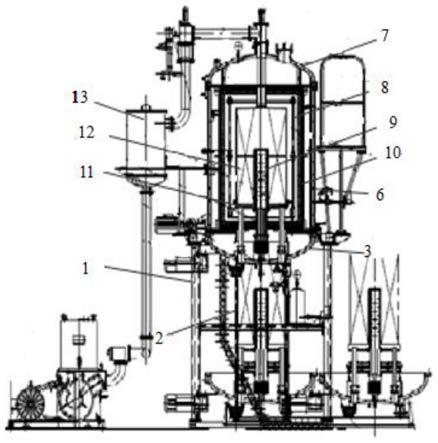
1.本发明涉及沉积炉设备技术领域,特别涉及一种分体式结构的化学气相沉积炉。
背景技术:
2.近些年来,随着航空、航天及光伏产业的发展,各种复杂服役环境对材料性能的要求越来越苛刻,c/c复合材料作为一种新型复合材料,具有高模量、高强度、低密度及耐高温等特点,在航天、航空、机械、电子、化工、冶金和核能等领域中应用前景广阔,是典型的战略性新兴材料,关系到国家安全和经济发展,具有不可替代性。经过几十年的研究和发展,我国c/c复合材料技术体系逐步形成,c/c复合材料产业正进入高速发展时期。但目前,我国c/c复合材料产业在装备成熟度、自动化、可靠性等方面与其它成熟行业和国际先进水平相比还存在较大差距:虽然设备的原理设计和总体结构基本可满足工艺要求,但各种设备的可靠性差、精细程度不高。由于c/c复合材料的制备是利用气相或液相的基体前驱体热解形成的基体c填充碳纤维预制体孔隙的过程,因此该填充过程的快慢直接决定了材料制备的周期、成本及性能,而化学气相沉积炉作为该环节的关键设备,对整个生产工艺及成本的影响是多方面的。
3.首先,设备的使用温度决定了沉积工艺的不同,通常,同一碳源气在更高的反应温度下,具有更快的裂解速度,热解碳的沉积也更快。其次,设备沉积区的温度均匀性决定了材料密度的均匀性,在恒温区内外径及上下端面温度差异越大,则反应速度差异越大,最终导致同一批次产品的密度出现差异。最后,设备的操作性和维护难度决定了设备的实际使用率,由于化学气相沉积炉为间断式作业,装出炉的时间及维修保养的时间在设备的整个生命周期占到了10-20%,而化学气相沉积炉的折旧费占到生产成本的20%,提升设备的操作性,降低维修保养的难度可以大大提升设备的使用率,进而降低生产成本。
4.现有的化学气相沉积炉主要有两种,一种为传统的金属内胆的双室沉积炉,采用金属材料(一般为耐热钢)制作内胆,加工精度高,密封性能优异,可以有效隔绝内室碳源气向外室发热体、保温层的扩散沉积。这有利于保护发热体、电极和保温层。但是,金属材料的内胆决定了该结构的化学气相沉积设备使用温度不能超过1000℃,否则会因为高温下金属内胆的变形而影响设备的使用寿命。另一种则是在传统双室炉的基础上,以碳/碳或石墨筒替代金属内胆的双室沉积炉,相比于金属内胆的沉积炉,其使用温度更高(理论上可以超过2000℃),但是缺点也很明显,石墨筒限于原料,很难做整体大筒,而拼装的石墨筒和碳/碳筒的气密性又很差,特别是密度较低时,根本不足以隔绝内室的碳源气向外室的发热体、保温层扩散沉积,这不仅会导致保温层密度增加,隔热性能降低,进而增大设备功耗,严重时甚至会导致短路,烧毁发热体和电极。因此,必须定期拆除内室后对外室进行除碳维护,该过程通常需要将炉盖吊起后再将内筒取出才能进行,对大尺寸沉积炉而言一般需要4-5名熟练工人进行操作,拆装总计耗时2-3天,严重影响设备使用率。此外,上述两种炉型均存在沉积区温度分布不均的问题,特别是装料后,炉内料柱内/外径及进/排气口位置差异尤其明显,而这一差异随着沉积炉设计尺寸的变大也被放大,进而导致同批次产品密度差异较
大。
技术实现要素:
5.本发明要解决的技术问题是提供一种性能优异、操作简单、经济实用、并可大幅度提升设备使用效率的分体式结构的化学气相沉积炉。
6.为了解决上述技术问题,本发明的技术方案为:
7.一种分体式结构的化学气相沉积炉,包括机架和升降机构,所述升降机构上连接有炉底,所述炉底上固定连接有中圈法兰,所述中圈法兰上通过螺栓与炉身连接,所述炉身顶部设置有炉盖,所述中圈法兰上固定连接有内外筒,所述内外分隔筒将所述炉身内分隔为内发热空间和外发热空间,所述内发热空间设置有内发热体,所述外发热空间设置有外发热体,所述炉底上设置有料台,料柱放置于所述料台上,且置于所述内发热体与所述外发热体之间。
8.优选地,所述升级机构为丝杆升降机。
9.优选地,所述内外分隔筒为碳/碳复合材料薄壁筒。
10.优选地,所述内发热体为碳/碳发热体,或等静压石墨发热体,或电极石墨发热体。
11.优选地,所述外发热体为等静压石墨发热体。
12.优选地,还包括尾气处理装置,所述尾气处理装置与炉盖连接,并连通至所述炉身内。
13.优选地,所述尾气处理装置包括依次连接的一级过滤器、二级过滤器以及三级过滤器。
14.优选地,所述一级过滤器为活性炭与金属过滤网构成。
15.优选地,所述二级过滤器冷凝过滤器。
16.优选地,所述三级过滤器为布袋除尘器。
17.与现有技术相比,本发明的有益效果为:
18.1、本发明为内外双室结构,内外之间用内外分隔筒进行分隔,装出料通过炉底上设有的料台在升降机构的带动下实现升降,由于采用碳/碳复合材料作为内外分隔筒,其实际使用温度可以达到1800℃。
19.2、由于采用了内外双室双发热体设计,本发明的工作区温度均匀性较好,当炉内料柱直径达到2.5m时,相比单外发热体加热的沉积炉,料柱内外径温差可由60-150℃降至10-30℃。
20.3、本发明采用了嵌套式的分体结构设计,相比于内外分隔筒固定于炉身的整体式设计,分体结构操作简单,无需吊起炉盖和分隔筒,只需2名熟练工人1天即可完成全部维护保养工作,经统计,人工成本可降低50%,设备空置率可降低10-15%。
附图说明
21.图1为本发明的结构示意图;
22.图2为本发明的局部结构示意图。
具体实施方式
23.下面结合附图对本发明的具体实施方式作进一步说明。在此需要说明的是,对于这些实施方式的说明用于帮助理解本发明,但并不构成对本发明的限定。此外,下面所描述的本发明各个实施方式中所涉及的技术特征只要彼此之间未构成冲突就可以相互组合。
24.参照图1-2,本发明的一种分体式结构的化学气相沉积炉,包括机架1和升降机构2,所述升级机构2为丝杆升降机,所述升降机构2上连接有炉底3,炉底3设置在所述丝杆升降机的丝杆上,所述炉底3上固定连接有中圈法兰4,所述中圈法兰4上通过螺栓5与炉身6连接,所述炉身6顶部设置有炉盖7,所述中圈法兰4上固定连接有内外筒8,所述内外分隔筒8将所述炉身6内分隔为内发热空间和外发热空间,所述内发热空间设置有内发热体9,所述外发热空间设置有外发热体10,所述炉底3上设置有料台11,料柱12放置于所述料台11上,且置于所述内发热体9与所述外发热体10之间。
25.在本发明中,所述内外分隔筒8为碳/碳复合材料薄壁筒,由于采用碳/碳复合材料作为分隔筒,其实际使用温度可以达到1800℃。
26.所述内发热体9为碳/碳发热体,或等静压石墨发热体,或电极石墨发热体。所述外发热体10为等静压石墨发热体。本发明为内外室双发热体同时加热,外发热体10采用等静压石墨发热体,从炉壁侧面引入热电偶进行监控,内发热体9为碳/碳发热体,从炉底中央引入热电偶进行监控,内外室发热体各自采用独立的plc进行控制。由于采用了内外双室双发热体设计,该沉积炉的工作区温度均匀性较好,当炉内的料柱12直径达到2.5m时,相比单外发热体加热的沉积炉,料柱内外径温差可由60-150℃降至10-30℃。
27.本发明为底部进气,顶部抽气的方式,碳源气及载气通过质量流量计控制流量,进入混气罐充分混合后,通过底部进气管进入炉身6内,同时在底部进气管上安装有智能电磁阀,通过炉身6内压力的监控来调节阀门的开合,一旦炉内压力超过预设压力上限,则自动关闭。
28.还包括尾气处理装置13,所述尾气处理装置13与炉盖7连接,并连通至所述炉身6内。所述尾气处理装置13包括依次连接的一级过滤器、二级过滤器以及三级过滤器。所述一级过滤器为活性炭与金属过滤网构成。所述二级过滤器冷凝过滤器。所述三级过滤器为布袋除尘器。尾气处理主要分为三段,尾气出炉到一级过滤器主要是通过活性炭及金属滤网对尾气中的较大固体颗粒进行筛除,一级过滤器到二级过滤器主要通过冷凝过滤装置(冷凝过滤器)对尾气中的焦油与炭黑混合物在冷凝后进行过滤,三级过滤器主要是通过布袋收尘的方式(布袋除尘器)对尾气中残余的微小固体颗粒进行回收,经过三级过滤后尾气可直接排放。
29.具体的,本发明的一种分体式结构的化学气相沉积炉,一方面采用内外双室加热,大大提高了沉积区的温度均匀性。另一方面采用半固定式分体结构设计,实现了内筒的快捷拆装,大大缩短了设备的维护保养工时,提高了沉积炉的使用率。
30.以上结合附图对本发明的实施方式作了详细说明,但本发明不限于所描述的实施方式。对于本领域的技术人员而言,在不脱离本发明原理和精神的情况下,对这些实施方式进行多种变化、修改、替换和变型,仍落入本发明的保护范围内。
再多了解一些
本文用于企业家、创业者技术爱好者查询,结果仅供参考。