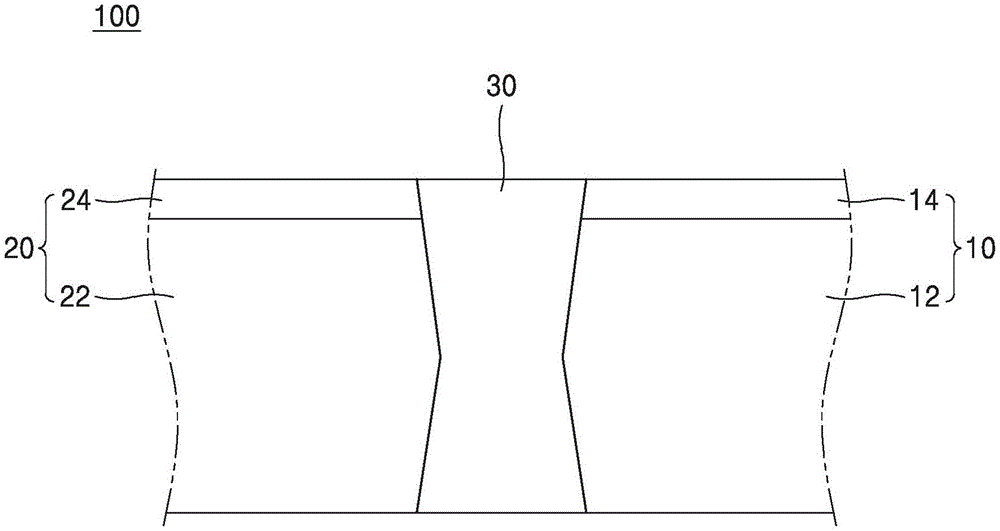
本发明涉及一种铝系镀覆坯料、其制备方法以及铝系镀覆坯料制备装置。
背景技术
具有各种强度的部件用于车辆。例如,需要在撞车或翻车中吸收能量的部件需要相对较弱的强度,而需要保持形状以确保乘客生存空间的部件需要较强的强度。
这是因为,当碰撞时需要吸收能量的部分的强度过高时,冲击能量无法被适当地吸收并原样传递到其他部分,导致向乘客和车辆的其他部件传递过大冲击的问题。
人们不断要求车辆的轻量化和低成本化,因此一个部件需要局部具有不同的强度。
部件的某些部分需要高强度以保护乘客,而某些部分需要相对较低的强度以吸收冲击能量。
这种部件的典型例子为乘用车的B柱。所述B柱的下部需要相对较低的抗拉强度,而上部需要较高的抗拉强度。需要强度差异的原因在于,在车辆发生碰撞时,同时需要一个必须以高强度保持形状的部分(翻车时需要支撑车顶的上部)和一个必须在被压碎的同时吸收冲击的部分(与其他车辆发生侧面碰撞可能性较高的下部)。
另外,为了确保稳定的空间以防止乘客受伤,B柱上部必须保持形状,因此需要高强度。如果不保证B柱上部强度,车辆倾覆时车顶会掉下来,对乘员的安全构成极大威胁。但B柱下部需要在变形的同时吸收冲击能量,因此需要相对较低的强度。这是因为,如果B柱下部也具有高强度,当发生侧面碰撞时,冲击能量不会被吸收,而是将冲击传递到其他结构材料上。
虽然具体要求的强度会根据车辆的类型或形状而有所不同,但B柱上部需要约1500MPa的抗拉强度,而B柱下部需要约500MPa至1000MPa的抗拉强度。
在现有技术中使用了用低强度材料形成部件后将单独的增强材料附接到需要高强度的部分的方法,但当某一部件根据分段需要不同强度时,也使用了一种方法,即,上部使用淬透性高的材料(或厚材料),而下部使用强度低、淬透性低的材料(或薄材料),然后用激光将两种材料接合在一起制成坯料,并对其进行热冲压工艺以生产最终产品。
另一方面,拼焊板(TWB)为通过将材料和厚度不同的两种以上的钢板材料接合来制备的部件。作为这种用于拼焊板的钢板材料,在表面使用铝-硅(Al-Si)镀层。另一方面,当使用这种镀覆钢板材料制备拼焊板时,在对所述镀覆钢板进行激光接合的同时,注入含有碳(C)和锰(Mn)的填充焊丝,即使钢板表面的铝(Al)组分混入熔融金属内部,也可以在850℃至1000℃的热冲压成型过程中确保全马氏体组织。
然而,当用激光接合镀覆钢板材料时,由于镀层的组分渗入接合部(接头部)的熔池内部,因此接合部具有与母材不同的物理性能。当镀层为铝-硅(Al-Si)系或锌(Zn)系时,在激光接合过程中镀层组分混入接合部中,导致机械性能下降。
据此,虽然可以通过填充焊丝的组分来解决或最大限度地减少接合部的强度下降现象,但根据材料(材料的镀覆附着量多)和接合条件(接合速度快),由于所混入的镀层组分(Al)无法在母材中均匀稀释而导致偏析等问题,从而仅通过填充焊丝组分的作用可能不够充分。
在韩国专利第10-1637084号(公告日:2016年7月6日,发明名称:一种填充焊丝以及使用其的定制焊接坯料制备方法)中公开了与本发明相关的背景技术。
技术实现要素:
技术问题
根据本发明的一实施例,提供一种铝系镀覆坯料,其可以最小化坯料接头部的硬度和物理性能的下降。
根据本发明的一实施例,提供一种铝系镀覆坯料,其可以防止坯料接头部发生偏析等缺陷。
根据本发明的一实施例,提供一种铝系镀覆坯料,其可以最小化在热冲压工艺后坯料接头部的物理性能下降。
根据本发明的一实施例,提供一种所述铝系镀覆坯料的制备方法。
根据本发明的一实施例,提供一种所述铝系镀覆坯料的制备装置。
技术方案
本发明的一方面涉及一种铝系镀覆坯料。在一具体实施例中,所述铝系镀覆坯料包括两个以上的铝系镀覆钢板相互连接的接头部,所述铝系镀覆钢板包括:基础钢板,其包括如下重量百分比的组分:碳(C):0.01重量%至0.5重量%;硅(Si):0.01重量%至1.0重量%;锰(Mn):0.5重量%至3.0重量%;磷(P):大于0重量%且小于等于0.05重量%;硫(S):大于0重量%且小于等于0.01重量%;铝(Al):大于0重量%且小于等于0.1重量%;氮(N):大于0重量%且小于等于0.001重量%;余量的铁(Fe)和其他不可避免的杂质;以及镀层,其以20g/m2至100g/m2的附着量形成于所述基础钢板的至少一面,并且包括铝(Al),所述接头部包括0.2重量%至2.0重量%的铝(Al),由所述两个以上的铝系镀覆钢板的在Ac3中最高Ac3温度以上不形成铁素体的组分体系组成,当将所述铝系镀覆坯料加热至Ac3以上进行压制成型,并以10℃/s至500℃/s的冷却速度冷却至300℃以下进行热冲压成型时,所述接头部的平均硬度大于等于所述基础钢板的平均硬度。
在一具体实施例中,所述基础钢板可以进一步包括铌(Nb)、钛(Ti)、铬(Cr)、钼(Mo)和硼(B)中的至少一个组分。
在一具体实施例中,所述镀层可以包括:表面层,其形成于所述基础钢板的表面,并包括80重量%以上的铝(Al);以及合金化层,其形成于所述表面层与所述基础钢板之间,包括铝-铁(Al-Fe)和铝-铁-硅(Al-Fe-Si)金属间化合物,并包括20重量%至70重量%的铁(Fe)。
在一具体实施例中,在所述热冲压成型之后,所述接头部可以具有包括90面积%以上的马氏体的显微组织。
根据本发明的另一发明,提供一种所述铝系镀覆坯料的制备方法。在一具体实施例中,所述铝系镀覆坯料的制备方法包括:钢板对齐步骤,其在两个以上的铝系镀覆钢板中,将一个镀覆钢板的边缘和另一镀覆钢板的边缘设置为彼此面对;以及钢板接合步骤,其向所述铝系镀覆钢板彼此面对的部分提供填充焊丝,并由激光头照射激光束以熔化所述铝系镀覆钢板彼此面对的部分和填充焊丝,从而形成接头部。当进行所述钢板接合时,通过照射激光束以基于所述接头部的形成方向制成预定角度的图案来进行接合,所述激光束的频率为100Hz至1500Hz,功率为1kW至20kW,所述接头部的形成速度为15mm/sec至170mm/sec,所述铝系镀覆钢板包括:基础钢板,其包括如下重量百分比的组分:碳(C):0.01重量%至0.5重量%;硅(Si):0.01重量%至1.0重量%;锰(Mn):0.5重量%至3.0重量%;磷(P):大于0重量%且小于等于0.05重量%;硫(S):大于0重量%且小于等于0.01重量%;铝(Al):大于0重量%且小于等于0.1重量%;氮(N):大于0重量%且小于等于0.001重量%;余量的铁(Fe)和其他不可避免的杂质;以及镀层,其以20g/m2至100g/m2的附着量形成于所述基础钢板的至少一面,并且包括铝(Al)。
在一具体实施例中,当将所述铝系镀覆坯料加热至Ac3以上进行压制成型,并以10℃/s至500℃/s的冷却速度冷却至300℃以下进行热冲压成型时,所述接头部的平均硬度可以大于等于所述基础钢板的平均硬度。
在一具体实施例中,所述填充焊丝可以包括奥氏体稳定化元素。
在一具体实施例中,在所述激光束照射时可以通过使所述镀覆钢板和激光头中的至少一个进行运动来制成所述图案。
在一具体实施例中,所述接头部的形成速度为15mm/sec至120mm/sec,所述激光束的频率、激光束半径和所述接头部的形成速度可以满足下式1的关系:
【式1】
在所述式1中,α为0.7,f为所述激光束的频率(Hz),r为从铝系镀覆钢板的表面测量的所述激光束的半径(mm),v为所述接头部的形成速度(mm/sec)。
根据本发明的另一发明,还提供一种所述铝系镀覆坯料的制备装置。在一具体实施例中,包括两个以上的铝系镀覆钢板相互连接的接头部的铝系镀覆坯料的制备装置包括:激光振荡部,其产生激光光源;钢板装载部,其设有两个以上的铝系镀覆钢板,并将一个镀覆钢板的边缘和另一镀覆钢板的边缘设置为彼此面对;焊丝供应部,其提供用于形成所述镀覆钢板的接头部的填充焊丝;以及激光头,其使用从所述激光振荡部提供的激光光源,将激光束照射到所述铝系镀覆钢板彼此面对的部分和所述提供的填充焊丝。当进行所述钢板接合时,通过照射激光束以基于所述接头部的形成方向制成预定角度的图案来进行接合,所述激光束的频率为100Hz至1500Hz,功率为1kW至20kW,所述接头部的形成速度为15mm/sec至170mm/sec。
在一具体实施例中,在所述激光束照射时可以通过使所述镀覆钢板和激光头中的至少一个进行运动来制成所述图案。
有益效果
本发明的铝系镀覆坯料通过将强度和厚度中的至少一个不同的两个以上的铝系镀覆钢板接合来制备,其可以最小化坯料接头部的硬度和物理性能的下降,可以防止发生坯料接头部的偏析等缺陷,并且可以最小化由于所述偏析在热冲压工艺中相变为Al-Fe金属间化合物而导致的接头部断裂现象。
附图说明
图1为根据本发明一具体实施例的铝系镀覆坯料的示意图。
图2的(a)为根据本发明一具体实施例的铝系镀覆坯料制备方法的示意图,图2的(b)为根据本发明另一具体实施例的铝系镀覆坯料制备方法的示意图。
图3为在通过照射激光束来接合铝系镀覆钢板的过程中镀层组分在基础钢板组分中没有被充分稀释的区域的示意图。
图4为根据本发明一具体实施例的铝系坯料的制备装置的示意图。
图5的(a)为通过现有方法制备的铝系坯料的剖视图,图5的(b)为显示实施例1的铝系坯料截面的光学显微照片。
图6的(a)为对实施例7的铝系坯料进行热冲压成型后各部分的硬度变化曲线图,图6的(b)为对比较例5的铝系坯料进行热冲压成型后各部分的硬度变化曲线图。
图7的(a)为实施例34的铝系坯料的剖视图,图7的(b)为显示比较例28的铝系坯料横截面的光学显微照片。
最佳模式
下面将更详细地描述本发明。此时,在本发明的描述中,当认为相关已知技术或配置的详细描述可能不必要地模糊本发明的本质时,将省略其详细描述。
并且后面描述的术语是考虑到本发明中的功能而定义的术语,其可以根据用户或操作者的意图或习惯而变化,因此应基于描述本发明的整个说明书的内容来进行定义。
铝系镀覆坯料
本发明的一方面涉及一种铝系镀覆坯料。图1为根据本发明一具体实施例的铝系镀覆坯料的示意图。参见所述图1,铝系镀覆坯料100包括两个以上的铝系镀覆钢板10、20相互连接的接头部30,所述铝系镀覆钢板包括:基础钢板12、22,其包括如下重量百分比的组分:碳(C):0.01重量%至0.5重量%;硅(Si):0.01重量%至1.0重量%;锰(Mn):0.5重量%至3.0重量%;磷(P):大于0重量%且小于等于0.05重量%;硫(S):大于0重量%且小于等于0.01重量%;铝(Al):大于0重量%且小于等于0.1重量%;氮(N):大于0重量%且小于等于0.001重量%;余量的铁(Fe)和其他不可避免的杂质;以及镀层14、24,其以20g/m2至100g/m2的附着量形成于基础钢板12、22的至少一面,并且包括铝(Al)。
在一具体实施例中,接头部30包括0.2重量%至2.0重量%的铝(Al),由所述两个以上的铝系镀覆钢板的在Ac3中铝系镀覆钢板的最高Ac3温度以上不形成铁素体的组分体系组成。优选地,其可以由在850℃以上不形成铁素体的组分体系组成。具体地,经过热冲压工艺后的接头部由可具有包括面积分率为90%以上的马氏体的显微组织的组分体系组成,所述热冲压工艺是在将所述铝系镀覆坯料加热至850℃至1000℃后进行压制成型并以10℃/s至500℃/s的平均冷却速度快速冷却的工艺。例如,其由可具有包括90%以上且100%以下的马氏体的显微组织的组分体系组成。
当将所述铝系镀覆坯料加热至Ac3以上并进行压制成型,以10℃/s至500℃/s的冷却速度冷却至300℃以下并进行热冲压成型时,所述接头部的平均硬度可以大于等于所述两个以上的基础钢板的每个平均硬度中最大的平均硬度,优选地,所述接头部的最小硬度大于等于所述基础钢板的平均硬度。
在本说明书中,所述铝系镀覆坯料的硬度值可以为根据KSB0811标准(金属材料的维克斯硬度测试方法)通过施加载荷300g的条件来测量的值。另外,所述KS标准为引用ISO6507国际标准的标准。
在一具体实施例中,所述接头部的平均硬度值是通过测量经过所述热冲压热处理的铝系镀覆坯料的接头部中相隔一定距离的五个点的硬度来计算平均值的。
在一具体实施例中,所述基础钢板的平均硬度值可以通过测量经过所述热冲压热处理的铝系镀覆坯料的基础钢板中以与测量所述接头部时相同的距离隔开的五个点的硬度来计算平均值的。
另外,在本说明书,术语“Ac3温度”为金属材料(例如钢)在升高(例如加热)所述金属材料的温度时从铁素体相完全转变为奥氏体相的最高温度(highest temperature)或临界温度(critical temperature)。
基础钢板
下面将对所述基础钢板的合金组分进行更详细的描述。
碳(C)
所述碳(C)为决定钢的强度和硬度的主要元素,添加碳的目的在于确保钢材在热冲压(或热压)工艺后的抗拉强度。另外,添加碳的目的还在于确保淬透性特性。在一具体实施例中,基于所述基础钢板的总重量,所述碳的含量为0.01重量%至0.5重量%。当所述碳含量低于0.01重量%时,难以达到本发明的机械强度,当其含量超过0.5重量%时,可能会导致钢材的韧性降低问题或钢的脆性控制问题。
硅(Si)
硅(Si)在钢板中用作铁素体稳定化元素。其可以起到通过使铁素体清洁来提高延展性并通过抑制低温区碳化物的形成来提高奥氏体中碳富集程度的作用。进一步地,其为热轧、冷轧、热冲压组织均质化(珠光体、锰的偏析带控制)和铁素体微细分散的关键元素。在一具体实施例中,基于所述基础钢板的总重量,所述硅的含量为0.01%重量至1.0重量%。当所述硅含量低于0.01重量%时,不能充分发挥上述功能,当其含量超过1.0重量%时,热轧和冷轧负荷增加,热轧红色氧化皮过多,并且接合性会降低。
锰(Mn)
添加所述锰(Mn)的目的在于增加热处理时的淬透性和强度。在一具体实施例中,基于所述基础钢板的总重量,所述锰的含量为0.5重量%至3.0重量%。当所述锰的含量低于0.5重量%时,热冲压后的材料因淬透性不足而不足(硬质相分率不足)的可能性很大,当其含量超过3.0重量%时,锰偏析或珠光体带会导致延展性和韧性下降,从而弯曲性能变差并可能会出现不均匀的显微组织。
磷(P)
所述磷(P)为一种容易偏析并降低钢的韧性的元素。在一具体实施例中,基于所述基础钢板的总重量,所述磷(P)的含量大于0重量%且小于等于0.05重量%。当包括在所述范围内时,可以防止韧性下降。当所述磷的含量超过0.05重量%时,工艺中引起裂纹并形成磷化铁化合物,从而可能降低韧性。
硫(S)
所述硫(S)为降低加工性和物理性能的元素。在一具体实施例中,基于所述基础钢板的总重量,所述硫的含量大于0重量%且小于等于0.01重量%。当所述硫的含量超过0.01重量%时,热压加工性降低,并且由于大夹杂物的形成,可能出现裂纹等表面缺陷。
铝(Al)
所述铝(Al)作为脱氧剂从钢中去除氧气。在一具体实施例中,基于所述基础钢板的总重量,所述铝的含量大于0重量%且小于等于0.1重量%。当铝的含量超过0.1重量%时,在炼钢过程中喷嘴堵塞,并且在铸造过程中由于氧化铝等而产生热脆性,从而可能会导致出现裂纹或延展性降低。
氮(N)
当大量添加所述氮(N)时,固溶氮量增加,从而可能降低钢板的冲击特性和延伸率并大大降低接头部的韧性。在一具体实施例中,基于所述基础钢板的总重量,所述氮的含量大于0重量%且小于等于0.001重量%。当所述氮的含量超过0.001重量%时,钢板的冲击特性和延伸率降低,并且接头部的可能可以降低。
在一具体实施例中,所述基础钢板可以进一步包括铌(Nb)、钛(Ti)、铬(Cr)、钼(Mo)和硼(B)中的至少一个组分。
铌(Nb)
添加铌(Nb)的目的在于通过减小马氏体(Martensite)板条束尺寸(Packet size)来增加强度和韧性。在一具体实施例中,基于所述基础钢板的总重量,所述铌的含量可以为0.005重量%至0.1重量%。当其含量在所述范围内时,在热轧和冷轧工艺中钢材的晶粒细化效果优异,防止炼钢/连铸过程中钢坯的裂纹和产品的脆性断裂,并可以最大限度地减少炼钢加工中形成粗大析出物。
钛(Ti)
添加所述钛(Ti)的目的在于通过热冲压热处理后形成析出物来增强淬透性,提高材料的品质。另外,通过在高温下形成Ti(C,N)等的析出相,有效帮助奥氏体晶粒细化。在本发明中,试图通过形成TiN来确保B淬透性效果并设定添加量的上限和下限。在一具体实施例中,基于所述基础钢板的总重量,所述钛的含量可以为0.005重量%至0.1重量%。当其含量在所述范围内时,可以防止连铸缺陷和析出物的粗大化,容易确保钢材的物理性能,并防止钢材表面的裂纹等缺陷。
铬(Cr)
添加所述铬(Cr)的目的在于提高所述铝系镀覆钢板的淬透性和强度。在一具体实施例中,基于所述基础钢板的总重量,所述铬的含量可以为0.01重量%至0.5重量%。当其含量在所述范围内时,可以提高所述铝系镀覆钢板的淬透性和强度,并防止生产成本的增加和钢材韧性的下降。
钼(Mo)
所述钼(Mo)抑制热轧和热冲压过程中析出物的粗大化并提高淬透性,其可以有助于提高强度。基于所述基础钢板的总重量,所述钼(Mo)的含量可以为0.001重量%至0.008重量%。当其含量在所述范围内时,抑制热轧和热冲压过程中析出物的粗大化和提高淬透性的效果可以优异。
硼(B)
添加所述硼(B)的目的在于通过确保马氏体组织来确保所述钢材的淬透性和强度,并且随着奥氏体晶粒生长温度的升高,其具有晶粒细化效果。在一具体实施例中,基于所述基础钢板的总重量,所述硼的含量可以为0.001重量%至0.008重量%。当其含量在所述范围内时,可以防止在硬质相晶界处发生脆性并确保高韧性和弯曲性。
在一具体实施例中,所述铝系镀覆钢板的制备方法可以包括如下步骤:对钢坯进行再加热,所述钢坯包括如下重量百分比的组分:碳(C):0.01重量%至0.5重量%;硅(Si):0.01重量%至1.0重量%;锰(Mn):0.5重量%至3.0重量%;磷(P):大于0重量%且小于等于0.05重量%;硫(S):大于0重量%且小于等于0.01重量%;铝(Al):大于0重量%且小于等于0.1重量%;氮(N):大于0重量%且小于等于0.001重量%;余量的铁(Fe)和其他不可避免的杂质;对所述再加热的钢坯进行精轧;将所述热轧的钢板卷取;对所述卷取的钢板进行冷轧;对所述冷轧的板材进行退火处理;以及在所述退火处理的板材表面形成镀层。
镀层
所述镀层以每单面20g/m2至100g/m2的附着量形成于所述基础钢板的至少一面,并且包括铝(Al)。在一具体实施例中,所述镀层的形成方法可以包括:将所述基础钢板浸入含有熔融铝和铝合金中至少一个的600℃至800℃的镀浴中,然后以1℃/s至50℃/s的平均冷却速度冷却。
在一具体实施例中,当将所述基础钢板浸入镀浴后,将空气或气体喷洒在所述基础钢板的表面上并擦拭热浸镀层,并可以通过控制喷洒压力来以调节镀覆附着量。
所述镀覆附着量可以在20g/m2至150g/m2的范围内形成于所述基础钢板的至少一面。优选在20g/m2至100g/m2的范围内形成于所述基础钢板的至少一面。当所述镀覆附着量小于20g/m2时,耐蚀性降低,当其超过100g/m2时,所述将铝系镀覆钢板接合时混入接头部的铝(Al)量增加,从而热冲压后接头部的强度可能会降低。
在一具体实施例中,所述镀层可以包括:表面层,其形成于所述基础钢板的表面,并包括80重量%以上的铝(Al);以及合金化层,其形成于所述表面层与所述基础钢板之间,包括铝-铁(Al-Fe)和铝-铁-硅(Al-Fe-Si)金属间化合物,并包括20重量%至70重量%的铁(Fe)。
在一具体实施例中,所述表面层可以包括80重量%至100重量%的铝,并且其平均厚度可以为10μm至40μm。当所述平均厚度小于10μm时,铝系镀覆坯料的耐蚀性降低,当其超过40μm时,接合时混入接头部的铝(Al)量增加,从而热冲压后接头部的机械物理性能下降。例如,平均厚度可以为10μm至30μm。
在一具体实施例中,所述合金化层可以包括20重量%至70重量%的铁(Fe)。由于所述合金化层在所述条件下具有较高的熔点,因此可以防止发生液体金属脆化(Liquid Metal Embrittlement)现象,所述液体金属脆化是指在热冲压加热炉中所述表面层被熔化以渗入所述基础钢板的组织中的现象。例如,所述合金化层可以包括20重量%至70重量%的铁(Fe)。
接头部
可以将所述铝系镀覆钢板彼此面对对齐,然后照射激光使其熔化而形成所述接头部,并且所述接头部由所述两个以上的铝系镀覆钢板的在Ac3中铝系镀覆钢板的最高Ac3温度以上不形成铁素体的组分体系组成,可以包括比上述基础钢板更多的奥氏体稳定化元素。所述奥氏体稳定化元素可以包括碳(C)和锰(Mn)中的至少一个。
所述接头部包括0.2重量%至2.0重量%的铝(Al)。所述铝的含量可以为熔融基础钢板的铝(Al)和从镀层混入的铝(Al)的总和。当所述接头部的铝(Al)含量低于0.2重量%时,在铝系镀覆钢板的接合过程中必须去除镀层,导致工艺成本增加,当其含量超过2.0重量%时,热冲压后接头部的马氏体分率降低,导致机械性能下降。更优选地,所述接头部可以包括0.2重量%至1.0重量%的铝。另一方面,当所述接头部包括超过1.0重量%的铝时,存在在接头部表面形成大量氧化膜的风险。
在一具体实施例中,可以通过将铝系镀覆坯料加热至Ac3以上的温度后进行压制成型并以10℃/s至500℃/s的平均冷却速度冷却至300℃以下的温度来制备热冲压件,在所述铝系镀覆坯料中,所述两个以上的铝系镀覆钢板和所述镀覆钢板相互连接,并且包括接头部。
所述热冲压件中对应于所述铝系镀覆钢板和所述接头部的部分具有比所述坯料的铝系镀覆钢板和接头部更高的抗拉强度。尤其,按面积分率计,所述坯料的接头部具有包括90%以上的马氏体的显微组织。例如,按面积分率计,所述坯料的接头部具有包括90%以上至100%以下的马氏体的显微组织。
本发明的铝系镀覆钢板的平均硬度可以彼此不同。在一具体实施例中,在形成接头部的两个铝系镀覆钢板中,所述接头部的平均硬度值可以大于铝系镀覆钢板的最大平均硬度值,优选地,接头部的最小硬度值可以大于所述最大的平均硬度值。在本发明中,可以将强度和厚度中至少一个不同的两个以上的铝系镀覆钢板接合。当强度不同时,平均硬度值可以彼此不同。
当将所述铝系镀覆坯料加热至Ac3以上进行压制成型,并以10℃/s至500℃/s的冷却速度冷却至300℃以下进行热冲压成型时,所述接头部的平均硬度大于所述两个基础钢板的每个平均硬度。
铝系镀覆坯料的制备方法
根据本发明的另一发明,提供一种所述铝系镀覆坯料的制备方法。在一具体实施例中,所述铝系镀覆坯料的制备方法包括:(S10)钢板对齐步骤和(S20)钢板接合步骤。
更具体地,所述铝系镀覆坯料的制备方法包括:(S10)钢板对齐步骤,其在两个以上的铝系镀覆钢板中,将一个镀覆钢板的边缘和另一镀覆钢板的边缘设置为彼此面对;以及(S20)钢板接合步骤,其向所述铝系镀覆钢板彼此面对的部分提供填充焊丝,并由激光头照射激光束以熔化所述铝系镀覆钢板彼此面对的部分和填充焊丝,从而形成接头部。
下面将针对每个步骤详细描述所述铝系镀覆坯料的制备方法。
(S10)钢板对齐步骤
所述步骤为在两个以上的铝系镀覆钢板中将一个镀覆钢板的边缘和另一镀覆钢板的边缘设置为彼此面对的步骤。
在所述两个以上的铝系镀覆钢板中,强度和厚度中的至少一个可以不同。当强度不同时,平均硬度值可以彼此不同。
所述铝系镀覆钢板包括:基础钢板,其包括如下重量百分比的组分:碳(C):0.01重量%至0.5重量%;硅(Si):0.01重量%至1.0重量%;锰(Mn):0.5重量%至3.0重量%;磷(P):大于0重量%且小于等于0.05重量%;硫(S):大于0重量且小于等于0.01重量%;铝(Al):大于0重量%且小于等于0.1重量%;氮(N):大于0重量%且小于等于0.001重量%;余量的铁(Fe)和其他不可避免的杂质;以及镀覆层,其以20g/m2至100g/m2的附着量形成于所述基础钢板的至少一面,并且包括铝(Al)。可以使用与上述相同的铝系镀覆钢板,因此将省略对其的详细描述。
(S20)钢板接合步骤
所述步骤为向所述铝系镀覆钢板彼此面对的部分提供填充焊丝,并由激光头照射激光束以熔化所述铝系镀覆钢板彼此面对的部分和填充焊丝,从而形成接头部的步骤。所述激光束熔化所述填充焊丝、铝系镀覆钢板的镀层和基础钢板以形成接头部。
填充焊丝
在一具体实施例中,所述填充焊丝可以包括奥氏体稳定化元素。例如所述奥氏体稳定化元素可以包括碳(C)和锰(Mn)中的至少一个。
所述填充焊丝熔入所述接头部,可以调整所述接头部的组分体系。
即使在所述基础钢板表面形成的镀层的铝(Al)混入接头部熔池中,由于添加到填充焊丝中的奥氏体稳定化元素的含量高,因此接头部的显微组织在热冲压后具有全马氏体组织。即,即使在不去除镀层的情况下镀层的组分混入焊接部,也可以防止硬度/强度的降低,因此焊接部的物理性能与母材部没有区别,从而可以防止焊接部的断裂现象。
另一方面,即使通过所述填充焊丝稀释镀层组分,根据接合条件,也可能无法将填充焊丝组分和镀层组分均匀地分布到基础钢板组分中。为了防止这种情况,当进行所述镀覆钢板的接合时,通过照射激光束以基于所述接头部的形成方向制成预定角度的图案来进行接合。
在一具体实施例中,在所述激光束照射时可以通过使所述镀覆钢板和激光头中的至少一个进行运动来制成所述图案。
例如,所述激光束以与形成所述接头部的方向成预定角度的方式进行图案运动,并且可以熔化所述填充焊丝、所述铝系镀覆钢板的镀层和基础钢板以形成所述接头部。
另外,可以通过在所述激光束进行图案运动的同时使镀覆钢板和激光头中至少一个进行相对运动而形成所述接头部。在本说明书中,所述“相对运动”是指所述镀覆钢板和激光头中的至少一个进行运动。优选地,在所述镀覆钢板处于静止状态下,所述激光头可以进行运动以形成接头部。
图2的(a)为根据本发明一具体实施例的铝系镀覆坯料制备方法的示意图,图2的(b)为根据本发明另一具体实施例的铝系镀覆坯料制备方法的示意图。
更具体地,作为所述相对运动的一例,图2的(a)示意性地示出了铝系镀覆钢板10、20进行图案运动以形成接头部30的过程。参见所述图2的(a),激光头300处于固定状态,向所述铝系镀覆钢板10、20彼此面对的部分提供填充焊丝200,并且可以照射激光束310。此时,铝系镀覆钢板10、20在与形成接头部30的方向(X)相反的方向上平行(水平)移动,同时,可以通过在以预定角度进行图案运动的同时照射激光束310来形成接头部30。
作为所述相对运动的另一例,图2的(b)示意性地示出了所述激光束进行图案运动以形成接头部的过程。参见所述图2的(b),铝系镀覆钢板10、20处于固定状态,向铝系镀覆钢板10、20彼此面对的部分提供填充焊丝200,并且激光头300可以进行运动以照射激光束310。此时,激光头300在与形成接头部30的方向(X)相同的方向上平行(水平)移动,同时,可以通过在以预定角度进行图案运动的同时照射激光束310来形成接头部30。
在一具体实施例中,所述激光束可以在与所述激光头的运动方向不同的方向上进行运动。优选地,其可以在与所述激光头的运动方向形成预定角度的同时进行运动。更优选地,其可以垂直于所述激光头的运动方向进行图案运动。
在一具体实施例中,当所述激光头进行运动时,激光束可以相对于所述激光头的运动方向进行45°以上且小于90°的图案运动。
在另一具体实施例中,当所述铝系镀覆钢板进行移动时,所述激光束可以相对于所述接头部的形成方向进行45°以上且小于90°的图案运动。
结果,当所述激光束朝向铝系镀覆钢板表面照射时,通过进行与所述接头部的形成方向(X)平行(水平)的相对运动的所述镀覆钢板和激光头中的至少一个,所述激光束可以具有与在所述铝系镀覆钢板的表面上所述接头部的形成方向(X)形成预定角度的运动图案。
因此,与以与接头部形成方向相同的方向照射激光束的情况相比,由于所述激光束在所述镀覆钢板表面上移动的激光束移动长度变长,因此不仅可向所述镀覆钢板传递能量的面积变宽,而且根据所述激光束移动路径和所述激光束半径,能量被传输的区域也可能会重叠,从而可以将所述镀层的组分和填充焊丝的组分充分稀释于所述基础钢板的组分以形成接头部。
在一具体实施例中,所述激光束可以具有100Hz至1500Hz的频率和1kW到20kW的功率。在一具体实施例中,所述激光束的功率可以指激光振荡部的输出值,所述激光束的频率可以是指所述激光束的图案运动的频率。
在一具体实施例中,当制备所述铝系镀覆坯料时,接头部的形成速度应为1m/min以上,激光频率应为1500Hz以下,激光束功率应为20kW以下,从而可以确保最低限度的生产率和商业可行性。所述激光频率和激光束功率越高越好,但为了实现超过1500Hz的频率和超过20kW的功率,需要高性能的设备,因此存在设备大型化、设备价格高的问题。另外,为了确保最低限度的生产率,需要将所述铝系镀覆钢板的接合速度,即接头部的形成速度维持在1m/min以上。所述接头部的形成速度是指所述激光头进行与所述接头部的形成方向平行(水平)的相对运动时单位时间内的位移。
在一具体实施例中,所述接头部的形成速度可以为1m/min至10m/min。当所述接头部的形成速度超过10m/min时,即使以100Hz至1500Hz的频率、1kW至20kW的功率、0.1mm至1.0mm的光束半径照射激光束,所述激光束移动路径的间隔增加,从而当所述铝系镀覆钢板的镀层和基础钢板被所述激光束熔化时,可能存在所述镀层的组分没有充分稀释于所述基础钢板组分的部分。在一具体实施例中,所述接头部的形成速度为15m/sec至170m/sec。优选地,可以为1m/min至7m/min。优选地,所述接头部的形成速度可以为15mm/sec至120mm/sec。
在一具体实施例中,所述激光束可以在半径0.1mm至1.0mm条件下照射。当所述激光束以超过1.0mm的半径照射到所述镀覆钢板的表面时,所述填充焊丝和所述镀覆钢板与照射所述激光束的激光头之间的距离需要很近,当所述填充焊丝随着所述接头部的形成而混入所述铝系镀覆钢板中且长度逐渐缩短而需要更换时,提供所述填充焊丝的空间或所述填充焊丝完全消耗时将其更换的空间可能不足。
图3示意性地示出了在通过照射具有小于0.1mm的激光束半径的激光束来接合铝系镀覆钢板的过程中镀层组分在基础钢板组分中没有充分稀释的区域。参见所述图3,当所述激光束半径小于0.1mm时,即使以100Hz至1500Hz的频率和1kW至20kW的功率条件照射激光束,由于激光束半径小,因此当所述铝系镀覆钢板10、20的镀层和基础钢板被所述激光束熔化时,可能存在所述镀层的组分在所述基础钢板的组分中没有充分稀释的区域(S)。
当所述激光束频率小于100Hz时,所述激光束的移动路径的间隔变大,即使满足激光束功率1kW至20kW、激光束半径0.1mm至1.0mm、接头部形成速度1m/min至7m/min的条件,当所述铝系镀覆钢板的镀层和基础钢板被所述激光束熔化时,可能存在所述镀层的组分在所述基础钢板的组分中没有充分稀释的部分。
当所述激光束功率小于1kW时,即使满足激光束频率100Hz至1500Hz、激光束半径0.1mm至1.0mm、接头部形成速度1m/min至7m/min的条件,到达所述镀覆钢板表面的能量不足,即所述镀覆钢板表面中的能量密度不足,当所述铝系镀覆钢板的镀层和基础钢板被所述激光束熔化时,可能存在所述镀层的组分在所述基础钢板的组分中没有充分稀释的部分。
在一具体实施例中,当照射所述激光束时,可以照射彼此间隔开的第一激光束和第二激光束。例如,所述第一激光束熔化填充焊丝、镀层和基础钢板,用第二激光束保持所述熔融的状态,均匀搅拌熔融区域以防止在接头部中发生偏析,从而可以具有优异的品质和机械物理性能。另一方面,当使用第一激光束和第二激光束时,所述第一激光束和第二激光束的功率总和可以为1kW到20kW。
另外,当所述铝系镀覆钢板在上述激光束功率、半径、频率和所述接头部形成速度范围内接合后进行加热到高温并快速冷却的热处理时,所述接头部的平均硬度可以大于等于所述铝系镀覆钢板的平均硬度,优选地,所述接头部的最小硬度可以大于等于所述铝系镀覆钢板的平均硬度。当所述接头部的平均硬度小于所述铝系镀覆钢板的平均硬度时,如果对所述热处理后的坯料施加拉伸力,则所述接头部可能会发生断裂。在一具体实施例中,当将所述铝系镀覆坯料加热至Ac3以上进行压制成型,并以10℃/s至500℃/s的冷却速度冷却至300℃以下进行热冲压成型时,所述接头部的平均硬度大于等于所述基础钢板的平均硬度。
在一具体实施例中,所述接头部的形成速度为15mm/sec至120mm/sec,此时,所述激光束的频率、激光束半径和所述接头部的形成速度可以满足下式1的关系:
【式1】
在所述式1中,α为0.7,f为所述激光束的频率(Hz),r为从铝系镀覆钢板的表面测量的所述激光束的半径(mm),v为所述接头部的形成速度(mm/sec)。
即使控制所述式1的激光束的频率、功率、半径和所述接头部形成速度,为了确保接头部有足够的抗拉强度,应该降低铝(Al)偏析的面积分率。为此,除了所述激光束的频率、功率、半径和所述接头部形成速度之外,还需要考虑许多变量,例如,所述激光束从激光头照射并传输到钢板时发生的能量损失、镀层的热反射率、钢板的导热率、基础钢板的厚度和镀层的厚度等。
另外,控制所述激光束的半径时的难点在于,不仅要考虑所述铝系镀覆钢板表面中的能量密度,还要考虑根据所述激光束的频率和所述接头部形成速度来确定的所述激光束在所述镀覆钢板表面中的移动路径,以将能量均匀地传递到接头部。
据此,本发明人通过过度重复实验,通过使用考虑到上述各种情况的校正因子(α),推导出仅利用激光束的频率、半径和接头部形成速度来确保接头部的足够抗拉强度的条件。
当满足根据所述式1的条件时,铝(Al)偏析分率可降低至5%以下。然而,此时所述接头部的形成速度优选可以为1m/min至7m/min,更优选可以为15mm/sec至120mm/sec。当所述接头部形成速度快时,存在将能量均匀地传递到所述接头部的时间不足的问题。例如,在接头部形成速度为120mm/s至170mm/s的条件下,即使满足所述式1,接头部的Al偏析也可以过度产生。
另一方面,即使所述接头部的铝(Al)偏析面积分率满足5%以下的条件,当在所述接头部和基础钢板的界面处发生铝(Al)偏析时,接头部,具体是接头部和钢板的界面处发生断裂的可能性很大。
在一具体实施例中,当所述激光束的图案角度为45°以上且小于90°时,可以防止在所述接头部和基础钢板的界面处发生铝(Al)偏析。所述图案角度是指所述接头部形成时所述接头部形成方向(X)与所述激光束在所述镀覆钢板表面上的移动路径(Y)之间的夹角。
铝系镀覆坯料的制备装置
根据本发明的另一发明,还提供一种所述铝系镀覆坯料的制备装置。图4为根据本发明一具体实施例的铝系坯料的制备装置的示意图。参见图4,包括两个以上的铝系镀覆钢板相互连接的接头部的铝系镀覆坯料的制备装置1000包括:激光振荡部500,其产生激光光源;钢板装载部400,其设有两个以上的铝系镀覆钢板,并将一个镀覆钢板的边缘和另一镀覆钢板的边缘设置为彼此面对;焊丝供应部210,其供应用于形成所述镀覆钢板的接头部的填充焊丝200;以及激光头300,其使用从所述激光振荡部500提供的激光光源,将激光束照射到所述铝系镀覆钢板彼此面对的部分和所述提供的填充焊丝。
在一具体实施例中,激光头300紧固在机械臂320上,可以向与所述接头部形成方向相反的方向移动。
在一具体实施例中,可以通过使用所述钢板装载部400在与所述接头部形成方向相同的方向上移动铝系镀覆钢板。
当进行所述钢板接合时,通过照射激光束以基于所述接头部的形成方向制成预定角度的图案来进行接合,所述激光束的频率为100Hz至1500Hz,功率为1kW至20kW。所述接头部的形成速度可以为1m/min至10m/min,优选可以为15mm/sec至170mm/sec。
可以使用与上述相同的铝系镀覆钢板。
在一具体实施例中,可以通过使所述钢板装载部的镀覆钢板和激光束中至少一个进行图案运动来制成所述图案。
具体实施方式
下面将通过本发明的优选实施例更详细地描述本发明的配置和作用。然而,提供以下实施例仅用于帮助理解本发明,本发明的范围不限于以下实施例。
实施例和比较例
实施例1
准备两个以上的强度和厚度均不同的铝系镀覆钢板,其包括:基础钢板,其包括如下重量百分比的组分:碳(C):0.01重量%至0.5重量%;硅(Si):0.01重量%至1.0重量%;锰(Mn):0.5重量%至3.0重量%;磷(P):大于0重量%且小于等于0.05重量%;硫(S):大于0重量%且小于等于0.01重量%;铝(Al):大于0重量%且小于等于0.1重量%;氮(N):大于0重量%且小于等于0.001重量%;余量的铁(Fe)和其他不可避免的杂质;以及镀层,其以20g/m2至100g/m2的附着量形成于所述基础钢板的至少一面,并且包括铝(Al)。所述铝系镀覆钢板的镀层包括:表面层,其分别形成于所述基础钢板的表面,并包括80重量%以上的铝(Al);以及合金化层,其形成于所述表面层与所述基础钢板之间,包括铝-铁(Al-Fe)和铝-铁-硅(Al-Fe-Si)金属间化合物,并包括20重量%至70重量%的铁(Fe)。
另外,如图4所示,在铝系镀覆坯料制备装置的钢板装载部中,将所述两个以上的铝系镀覆钢板中一个镀覆钢板的边缘和另一镀覆钢板的边缘设置为彼此面对。然后,将填充焊丝从焊丝供应部提供到所述铝系镀覆钢板彼此面对的部分,并且照射激光束,通过熔化所述铝系镀覆钢板彼此面对的部分和填充焊丝来形成接头部以制备铝系镀覆坯料。
当进行所述钢板接合时,通过照射激光束以基于所述接头部的形成方向制成预定角度的图案来进行接合。具体地,激光头以与接头部形成方向相同的方向平行(水平)移动,激光束相对于所述接头部形成方向以60°进行图案运动以照射。另外,所述激光束以100Hz的频率、1kW的光束功率和0.1mm的光束半径照射,并且接头部形成速度为1m/min。
实施例2至实施例16和比较例1至比较例12
除了通过使用下表1的激光束功率、光束半径、频率和接头部形成速度的条件来接合铝系镀覆钢板之外,以与所述实施例1相同的方法制备了铝系镀覆坯料。
实验例(1)硬度测试:分别制备所述实施例1至实施例16和比较例1至比较例12的三个铝系镀覆坯料试样,然后将每个试样加热到奥氏体单相区温度以上(Ac3以上),并以10℃/s至500℃/s的冷却速度冷却至300℃以下,然后测量所述铝系镀覆坯料的接头部和所述铝系镀覆坯料基础钢板部分的平均硬度值。
所述铝系镀覆坯料的硬度值为根据KSB0811标准(金属材料的维克斯硬度测试方法)通过施加载荷300g的条件来测量的值。另外,所述KS标准为引用ISO6507国际标准的标准。
所述接头部的平均硬度值是通过测量所述铝系镀覆坯料的接头部中相隔一定距离的五个点的硬度来计算平均值的,所述基础钢板的平均硬度值可以通过测量所述铝系镀覆坯料的基础钢板中以与测量所述接头部时相同的距离隔开的五个点的硬度来计算平均值。
当所述接头部的最小硬度大于等于所述基础钢板的平均硬度时,判定为合格(Pass),当其小于平均硬度时,判定为不合格(Fail),其结果如下表1所示。
【表1】
以下,在本发明中,“能量密度”假设为“激光振荡器的光束功率P(kW)除以钢板表面的激光束面积(π·r2)所得的值(但r为激光束的半径)”。
参见上表1的结果,对满足本发明的激光束照射和接头部形成速度的实施例1至实施例16而言,可以看出所述接头部的最小硬度大于等于所述基础钢板的平均硬度。
另一方面,对比较例1、比较例2、比较例7和比较例8而言,虽然能量密度足够,但即使在最小的接头部形成速度下,激光束的半径也很小,因此当所述铝系镀覆钢板的镀层和基础钢板被所述激光束熔化时,存在所述镀层的组分在所述基础钢板的组分中没有充分稀释的部分,从而所述接头部的最小硬度形成为小于所述基础钢板的平均硬度。
对比较例3、比较例4、比较例9和比较例10而言,即使将激光束半径值最大化(1.0mm)并将接头部形成速度最小化(1m/min),但由于频率较低,所述激光束移动路径的间隔增加,因此当所述铝系镀覆钢板的镀层和基础钢板被所述激光束熔化时,存在所述镀层的组分在所述基础钢板的组分中没有充分稀释的部分,从而所述接头部的最小硬度形成为小于所述基础钢板的平均硬度。
此外,对比较例5、比较例6、比较例11和比较例12而言,即使能量密度足够,将光束半径最大化,但由于速度太高,所述激光束移动路径的间隔增加,因此当所述铝系镀覆钢板的镀层和基础钢板被所述激光束熔化时,存在所述镀层的组分在所述基础钢板的组分中没有充分稀释的部分,从而所述接头部的最小硬度形成为小于所述基础钢板的平均硬度。
实施例17至实施例68和比较例13至比较例52
应用根据下表2至表5的激光束功率、光束半径、频率和接头部形成速度和根据下式1的条件对铝系镀覆钢板进行接合,激光头以与接头部形成方向相同的方向平行(水平)移动,激光束相对于所述接头部形成方向以45°进行图案运动以照射,除此之外,以与所述实施例1相同的方法制备了铝系镀覆坯料。
【式1】
在所述式1中,α为0.7,f为所述激光束的频率(Hz),r为从铝系镀覆钢板的表面测量的所述激光束的半径(mm),v为所述接头部的形成速度(mm/sec)。
实验例(2)接头部的铝(Al)偏析分率(%)和拉伸测试:分别制备所述实施例17至实施例68和比较例13至比较例52的三个坯料试样,然后将每个试样加热到奥氏体单相区温度以上(Ac3以上),并以10℃/s至500℃/s的冷却速度冷却至300℃以下。然后,对所述各试样的接头部的铝偏析面积分率进行了拉伸测试,其结果如下表2至表5所示。具体地,通过测量三个试样中铝(Al)偏析面积分率的平均值来显示所述接头部的铝偏析的面积分率,在所述拉伸测试结果中,对试样施加拉伸力后,将三个试样的所述接头部均未发生断裂的情况记为合格(Pass),将接头部中至少发生一次断裂的情况记为不合格(Fail)。
【表2】
【表3】
【表4】
【表5】
参见上表2至表5的结果,对本发明的实施例17至实施例68而言,满足式1的条件,接头部的铝偏析面积分率为5%以下,拉伸测试结果为接头部无断裂(合格)。然而,对不在本发明条件范围的比较例13至比较例52而言,当不满足本发明的式1的条件时,接头部的铝偏析面积分率超过5%,在拉伸测试过程中接头部发生断裂。另外,即使满足式1,当接头部形成速度超过7m/min时,由于接头部形成速度较快,因此激光束没有充分搅拌到基础钢板的内部,导致铝偏析过度发生,在拉伸测试时接头部发生断裂。
实施例69至实施例98和比较例53至比较例72
应用根据下表6至表7的激光束功率、接头部形成速度、光束半径和频率的条件对铝系镀覆钢板进行接合,激光头以与接头部形成方向相同的方向平行(水平)移动,激光束相对于所述接头部形成方向以下表6至表7条件的图案角度照射,除此之外,以与所述实施例1相同的方法制备了铝系镀覆坯料。此时,所述图案角度是指所述接头部形成时所述接头部形成方向(X)与所述激光束在所述镀覆钢板表面上的移动路径(Y)之间的夹角。
实验例(3)确认接头部铝(Al)偏析分率(%)、接头部界面的铝偏析和接头部是否断裂:分别制备所述实施例69至实施例98和比较例53至比较例72的三个坯料试样,然后将每个试样加热到奥氏体单相区温度以上(Ac3以上),并以10℃/s至500℃/s的冷却速度冷却至300℃以下。然后,所述每个试样的接头部的铝偏析面积分率、接头部界面是否出现铝偏析和拉伸测试结果见下表6和表7。具体地,通过测量三个试样中铝(Al)偏析面积分率的平均值来显示所述接头部的铝偏析的面积分率,在所述拉伸测试结果中,对试样施加拉伸力后,将三个试样的所述接头部均未发生断裂的情况记为x,将接头部中至少发生一次断裂的情况记为○。
【表6】
【表7】
另一方面,即使所述接头部的铝偏析面积分率满足5%以下的条件,当在所述接头部和基础钢板的界面处发生铝(Al)偏析时,接头部,具体是接头部和钢板的界面处发生断裂的可能性很大。参见上表6和表7的结果,对图案角度为45°以上且小于90°的实施例而言,可以看出,接头部的铝偏析以5%以下的面积分率形成,可以防止接头部与基础钢板的界面处发生铝(Al)偏析,并在拉伸测试过程中防止接头部的断裂。另一方面,对图案角度为小于45°的比较例53至比较例72而言,可以看出,接头部界面处发生铝偏析,并且接头部发生断裂。
下面图5的(a)为通过现有方法制备的铝系坯料的剖视图,其用激光束结合,但没有对激光束应用预定的图案角度,图5的(b)为显示实施例1的铝系坯料截面的光学显微照片。参见所述图5,可以看出,当采用不对激光束应用预定图案角度的现有方法时,由于镀层的组分在基础钢板的组分中没有充分稀释,因此接头部铝偏析的面积分率增加,但对所述实施例1而言,镀层的组分充分稀释于基础钢板的组分,从而可以最大限度地减少接头部铝偏析的发生。
图6的(a)为对实施例7的铝系坯料进行热冲压成型后各部分的硬度变化曲线图,图6的(b)为比较例5的铝系坯料各部分的硬度变化曲线图。参见所述图6,可以看出,对实施例7而言,热冲压后所述接头部的最小硬度大于等于所述基础钢板的平均硬度,但对不在本发明条件范围的比较例5而言,热冲压后所述接头部的最小硬度小于所述基础钢板的平均硬度。
图7的(a)为实施例34的铝系坯料的剖视图,图7的(b)为显示比较例28的铝系坯料截面的光学显微照片。参见所述图7,可以看出,实施例34的铝系坯料使接头部的铝偏析最小化,但对不在本发明的式1条件范围的比较例28而言,与所述实施例34相比,接头部处发生的铝偏析增加。
本领域普通技术人员可以很容易地对本发明进行简单的修改或变更,所有这些修改或变更均应包括在本发明的范围内。
本文用于企业家、创业者技术爱好者查询,结果仅供参考。