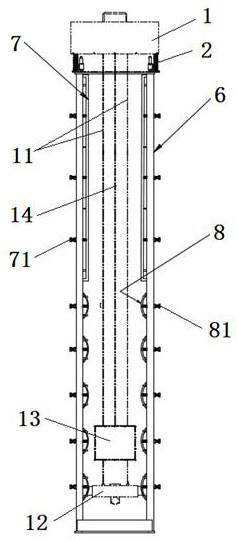
1.本发明涉及连铸自动化检测装备技术领域,尤其涉及一种用于连铸结晶器对中仪的离线标定方法。
背景技术:
2.板坯连铸机的对弧精度是指铸机固定侧设备位置与铸机设计弧度(包络线)的偏离值,对弧精度是铸机的一个重要的精度指标,对铸坯质量,特别是铸坯内部和表面裂纹类缺陷的控制有着至关重要的作用,同时对设备的使用寿命也有一定的影响。
3.铸机结晶器是连铸机的心脏,结晶器内外弧的对弧精度、内外弧铜板的锥度值、安装的左右、前后偏转角是控制铸坯角横裂、纵裂等表面质量缺陷、减少结晶器铜板异常磨损、防止连铸漏钢事故的一组重要参数。
4.如图1所示,通常对中仪的测量箱体1通过调整支架架设于结晶器3入口,结晶器3出口依次设有对称布置的足辊4及若干导向辊5,伸缩底座12通过钢丝绳11上下升降,数据采集装置13通过钢丝绳14上下升降;对中仪测量时通过驱动电机驱动钢丝绳11、14将数据采集装置13和伸缩底座12经结晶器3入口放至底部的相邻导向辊5之间,此时伸缩底座12张开抵靠至相邻导向辊5,数据采集装置13经钢丝绳14牵引由下部导向辊5缓慢向上移动并同时采集各导向辊5、足辊4以及结晶器3的相关数据,从而得到连铸机和结晶器的相关对弧数据。
5.但是由于生产现场的结晶器周边环境复杂、空间窄小,且结晶器本身的对中随时间和生产状态会逐步劣化,且传统的对中方式本身存在较多问题,因此对中仪采集的数据无法进行对比校验。且对中仪在投入使用前或者更换主要零部件后,为了提高测量的精确度,能够更精确的指导结晶器对中调整,也要对该对中仪进行标定。
6.鉴于目前没有合适、简便并全面地反映对中仪采集数据精度值的测量设备,导致在研究和控制铸坯表面质量缺陷上存在不确定因素,因此严重影响铸坯质量的控制,以及设备的使用寿命。
技术实现要素:
7.本发明所要解决的技术问题是提供一种用于连铸结晶器对中仪的离线标定方法,本方法模拟结晶器正常及各种异常量可测的状态,实现对中仪的离线标定,使对中仪所测的数据更具参考价值,用于研究和控制铸坯表面质量缺陷,以提高铸坯质量以及设备的使用寿命。
8.为解决上述技术问题,本发明用于连铸结晶器对中仪的离线标定方法包括如下步骤:步骤一、制作标定框架、模拟结晶器和模拟辊组,并且模拟结晶器和模拟辊组在标定框架内由上向下依次设置;步骤二、模拟结晶器的锥度为可调节形式,单边的模拟结晶器铜板设有上中下三组调
节螺栓,当模拟结晶器调节到需要的锥度后,采用固定螺钉将模拟结晶器铜板固定在标定框架上;步骤三、模拟辊组在模拟结晶器下方间隔布置,并且相邻模拟辊开度可调,当采用调节螺栓将相邻模拟辊调节到需要开口度后,采用固定螺钉将模拟辊固定于标定框架上;步骤四、在标定框架顶部架设对中仪,将模拟结晶器的锥度和模拟辊组各相邻模拟辊的开度调节至连铸生产工艺的理论值,启动对中仪分别采集模拟结晶器锥度采集数据和模拟辊组各相邻模拟辊开度采集数据;步骤五、模拟结晶器锥度理论值与采集数据的偏差,以及模拟辊组各相邻模拟辊开度理论值与采集数据的偏差作为对中仪的标定值。
9.进一步,所述模拟结晶器锥度通过模拟结晶器入口调节螺栓和出口调节螺栓进行调整,并且通过入口宽度和出口宽度表征锥度数据。
10.进一步,所述模拟辊组包括间隔布置于所述模拟结晶器出口下方的五对相邻模拟辊。由于本发明用于连铸结晶器对中仪的离线标定方法采用了上述技术方案,即本方法制作标定框架、模拟结晶器和模拟辊组,并且模拟结晶器和模拟辊组在标定框架内由上向下依次设置;且模拟结晶器的锥度为可调节形式,模拟辊组中相邻模拟辊开度可调;在标定框架顶部架设对中仪,将模拟结晶器的锥度和模拟辊组各相邻模拟辊的开度调节至连铸生产工艺的理论值,启动对中仪分别采集模拟结晶器锥度采集数据和模拟辊组各相邻模拟辊开度采集数据;理论值与采集数据的偏差作为对中仪的标定值。本方法模拟结晶器正常及各种异常量可测的状态,实现对中仪的离线标定,使对中仪所测的数据更具参考价值,用于研究和控制铸坯表面质量缺陷,以提高铸坯质量以及设备的使用寿命。
附图说明
11.下面结合附图和实施方式对本发明作进一步的详细说明:图1为生产现场连铸结晶器对中仪数据采集示意图;图2为本发明用于连铸结晶器对中仪的离线标定方法示意图;图3为本方法中结晶器锥度调节示意图;图4为本方法中模拟辊开度调节示意图。
具体实施方式
12.实施例如图2至图4所示,本发明用于连铸结晶器对中仪的离线标定方法包括如下步骤:步骤一、制作标定框架6、模拟结晶器7和模拟辊组,并且模拟结晶器7和模拟辊组在标定框架6内由上向下依次设置;步骤二、模拟结晶器7的锥度为可调节形式,单边的模拟结晶器铜板设有上中下三组调节螺栓71,当模拟结晶器7调节到需要的锥度后,采用固定螺栓72将模拟结晶器7固定在标定框架6上;步骤三、模拟辊组在模拟结晶器6下方间隔布置,并且相邻模拟辊8开度可调,当采用调节螺栓81将相邻模拟辊8调节到需要开口度后,采用固定螺钉82将模拟辊8固定于标定框架
6上;步骤四、在标定框架6顶部架设对中仪,将模拟结晶器7的锥度和模拟辊组各相邻模拟辊8的开度调节至连铸生产工艺的理论值,启动对中仪分别采集模拟结晶器7锥度采集数据和模拟辊组各相邻模拟辊8开度采集数据;对中仪的测量箱体1通过调整支架架设于标定框架6顶部,测量箱体1底部的钢丝绳11位于标定框架6内,对中仪通过钢丝绳11、伸缩底座12、数据采集装置13采集模拟结晶器7的锥度数据以及各相邻模拟辊8的开度数据;步骤五、模拟结晶器7锥度理论值与采集数据的偏差,以及模拟辊组各相邻模拟辊8开度理论值与采集数据的偏差作为对中仪的标定值。
13.优选的,所述模拟结晶器7锥度通过模拟结晶器入口调节螺栓和出口调节螺栓进行调整,并且通过入口宽度和出口宽度表征锥度数据。
14.优选的,所述模拟辊组包括间隔布置于所述模拟结晶器7出口下方的五对相邻模拟辊8。
15.本方法适用于不同锥度结晶器和不同开度导向辊的连铸机用对中仪的离线校验标定,按照标定流程,将对中仪固定在标定框架的上口,打开驱动伸缩底座的行走驱动电机,使伸缩底座和数据采集装置同步匀速下降,当伸缩底座下降到末端模拟辊位置的时候,驱动电机停止,伸缩底座打开并抵靠至模拟辊。逐步收紧钢丝绳,使钢丝绳提升数据采集装置,数据采集装置在上升过程中处于采集状态。
16.不同连铸机结晶器的锥度是不同的,为了使本方法具有通用性,模拟结晶器的锥度设计成可调节形式,单边的模拟结晶器有上中下三组调节螺栓,当调节到需要的锥度后,采用固定螺栓将模拟结晶器固定在标定框架上。
17.通过调节螺栓可以将模拟结晶器以及相邻模拟辊调节成模拟现场的实际状况。具体如下表所示。 结晶器入口宽度结晶器出口宽度1#辊间距2#辊间距3#辊间距4#辊间距5#辊间距理论值233227.7229.5229.5229.5229.6229.6模拟值237223.7227.5229.5231.5229.6229.6偏差值 4-4-20 200
18.对中仪在模拟结晶器和各辊辊间距保持在理论值状态下行走一遍,测得一组模拟数据,即采集数据,则理论数据与模拟数据的偏差作为对中仪的标定值,对中仪在实际测量过程中所采集的数据与偏差值比对,就可以用来验证对中仪的测量值是否精确。
19.本方法用于检测结晶器对中仪的准确度(精度)是否符合标准,使得整个测量过程更趋向于稳定,提高连铸结晶器对中自动检测的精确度,使测量数据更具参考价值,对中仪给出的结晶器锥度、足辊和导向辊的对弧精度更趋向于实际数据,从而能够更精确的指导结晶器的对中调整。通过提高结晶器的对中精度控制,则能有效减少铸坯表面质量问题,解决铸坯角横裂缺陷、纵裂缺陷等情况,提高产品质量及设备的使用寿命。
再多了解一些
本文用于企业家、创业者技术爱好者查询,结果仅供参考。