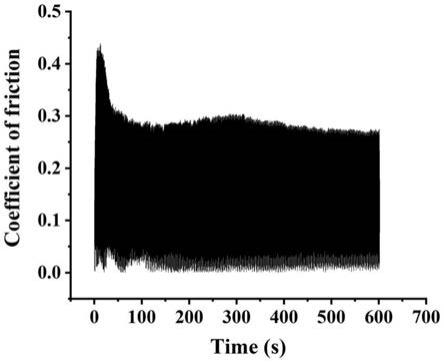
一种niti基自润滑复合材料及制备方法
技术领域
1.本发明属于复合材料领域,涉及一种niti基自润滑复合材料及制备方法
背景技术:
2.金属间化合物基自润滑复合材料是将固体润滑剂添加到金属间化合物基体中而形成的同时具有金属间化合物特性和固体润滑性能的复合材料;其中,基体化合物的性质一定程度赋予材料的强度、耐高温、耐腐蚀抗氧化等性能。富镍镍钛金属间化合物(ni
60
ti
40
)具有低密度、低模量、耐高温、耐腐蚀等优异的性质,其密度仅为6.7g/cm3,弹性模量只有95gpa,并且耐腐蚀性能与陶瓷相当。被认为是下一种划时代的轴承合金材料,这种轴承合金有望在航空航天等军事领域取得推广应用。作为轴承材料,摩擦磨损性能严重影响镍钛金属间化合物轴承的寿命。而干滑动下,ni
60
ti
40
的摩擦学性能较差,li等[x.li,x.chen,c.zhang,j.luo,preparation of self
‑
lubricating niti alloy and its self
‑
adaptive behavior,tribol.int.,130(2019)43
‑
51.]通过等离子烧结制备多孔niti材料,并将润滑油存储于niti孔隙中,所得材料具有很好的室温自润滑性能,然而油在高温下的燃烧分解这种niti自润滑材料只能在300℃以下的温度使用。在一些高温轴承部件(大于300℃),这种自润滑材料将润滑失效。这极大限制了ni
60
ti
40
轴承的使用范围和服役寿命。因此仍需要开发能在300℃提供有效润滑的新兴固体润滑材料。
技术实现要素:
[0003]
要解决的技术问题
[0004]
为了避免现有技术的不足之处,本发明提出一种niti基自润滑复合材料及制备方法,克服现有的镍钛基高温摩擦学性能的不足。本发明提供了一种高温、高真空、强腐蚀性条件下具有良好的摩擦学特性以及机械性能的高温自润滑轴承材料。
[0005]
技术方案
[0006]
一种niti基自润滑复合材料,其特征在于组分构成的质量百分比:50
‑
90%的镍钛金属间化合物、5
‑
25%的碱金属氟化物、5
‑
20%软金属和5
‑
30%硬质相;
[0007]
所述镍钛金属间化合物的质量比ni︰ti为60︰40;粒度100
‑
500目的粉末。
[0008]
所述碱金属氟化物为氟化钙、氟化钡、氟化锶中的一种或几种;采用粒度300
‑
500目的粉末。
[0009]
所述碱金属氟化物优选氟化钙与氟化钡的共晶,氟化钙与氟化钡的共晶为300目。
[0010]
所述软金属为银、铜、金、铅、铟等中的一种或几种;采用粒度100
‑
500目的粉末。
[0011]
所述硬质相为碳化铬、氧化铬、碳化钛、氧化铝等中的一种或几种;采用粒度200
‑
60目的粉末。
[0012]
一种制备所述niti基自润滑复合材料的方法,其特征在于步骤如下:
[0013]
步骤1:将镍钛金属间化合物、碱金属氟化物、软金属和硬质相,采用干混或湿混后得到混合物;
[0014]
步骤2:将混合物采用粉末冶金的方法进行烧结,烧结后自然冷却至室温,得到镍钛金属间化合物基自润滑复合材料;采用放电等离子烧结得处理参数为:真空度为10
‑3‑
10
‑1pa;升温速率为50
‑
150℃/min,优选90
‑
100℃/min;烧结温度为900
‑
1250℃,优选1050
‑
1150℃;施加压力为30
‑
40mpa;保温时间为5
‑
15min。
[0015]
所述干混采用机械球磨,所用的罐和球均为硬质wc,球料质量比为3:1
‑
10:1,转速为100
‑
150转/分钟,球磨时间3
‑
20小时。
[0016]
所述粉末冶金方法包括但不限于高温热压烧结、等静压烧结或放电等离子烧结;参数按照所采用方法的要求设置。
[0017]
一种所述niti基自润滑复合材料的应用,其特征在于:将复合材料经过机械加工得目标尺寸的抗磨部件,尤其是轴承部件。
[0018]
有益效果
[0019]
本发明提出的一种niti基自润滑复合材料及制备方法,材料的组份为:50
‑
85%的镍钛金属间化合物、5
‑
25%的碱金属氟化物、5
‑
20%软金属和5
‑
30%硬质相。制备过程物质按比例混合均匀,通过粉末冶金的方式将混合物制备成自润滑复合材料。该材料通过机加工方式得到抗磨性能优异的轴承部件。本发明的镍钛基高温自润滑材料具备机械强度高、摩擦系数低、耐磨性好、密度低、性能稳定、重现性好、比强度低、耐腐蚀性好和抗蠕变性能好等优点。该材料在氟化物气体介质中具有良好的耐蚀性。
[0020]
有益效果具体为:
[0021]
(1)本发明提供了一种性能优异的具有广泛应用前景的镍钛基自润滑复合材料。
[0022]
(2)本发明的镍钛基轴承材料具有优异的高温自润滑性能,在使用中不需要额外添加润滑剂,即可在对磨副间取得较低的摩擦系数,磨损率。可以省去润滑剂供给装置的设计,进而减轻重量。维护简单,这对于航空航天器件特别有益。
[0023]
(3)本发明材料的摩擦系数较低并且稳定,磨损率较低,制备工艺简单,材料的综合性能可以通过配方和工艺的调整进行控制。
[0024]
(4)本发明中的镍钛基体密度低、模量低。软金属相的加入主要提供在中温下的润滑,这主要是因为软金属较低的剪切强度,在摩擦界面形成涂抹的润滑层,进而降低摩擦系数和磨损,氟化物的加入主要是提供材料在较高温度的润滑,这主要是因为氟化物在较高温度下发生软化,而易于剪切,从而降低摩擦系数和磨损;硬质相的加入可以提高材料的硬度同时提高材料的抗磨能力。
[0025]
(5)本发明中制备的自润滑材料可以提高轴承部件的使用寿命,运行效率,同时降低能耗。
[0026]
(6)本发明中材料的制备工艺简单,通过配方和工艺的调整,可以调控材料性能。
附图说明
[0027]
图1:实施例1中镍钛金属间化合物在400℃下的摩擦系数;
[0028]
实施例1组成为70%ni
60
ti
40
‑
8%ag
‑
8%baf2/caf2‑
14%cr3c2的niti基自润滑复合材料在400℃下的摩擦系数随时间变化的摩擦系数曲线,在前50秒,摩擦系数从0.21降低至0.15左右而后保持总体稳定,摩擦系数在300秒左右虽有短暂升高,但整体稳定在较低的水平。相对于相同摩擦条件下,金属材料非润滑下材料的摩擦系数在0.5-1左右区间,所得摩
擦系数至少降低50%,这可以显著降低能耗。
[0029]
图2:实施例2中镍钛金属间化合物在600℃的摩擦系数
[0030]
实施例2组成为70%ni
60
ti
40
‑
8%ag
‑
8%baf2/caf2‑
14%cr3c2的niti基自润滑复合材料在600℃下的摩擦系数随时间变化的摩擦系数曲线,在前60秒,摩擦系数从0.17降低至0.13左右,而后摩擦系数虽有波动,但整体保持稳定。相对于相同摩擦条件下,金属材料非润滑下材料的摩擦系数在0.5
‑
1左右区间,所得摩擦系数至少降低50%,这可以显著降低能耗。
[0031]
图3:实施例3中镍钛金属间化合物在800℃的摩擦系数
[0032]
实施例3组成为70%ni
60
ti
40
‑
8%ag
‑
8%baf2/caf2‑
14%cr3c2的niti基自润滑复合材料在800℃下的摩擦系数随时间变化的摩擦系数曲线,在前50秒,摩擦系数从0.18降低至0.13左右,而后摩擦系数缓慢升高并稳定在0.16左右。相对于相同摩擦条件下,金属材料非润滑下材料的摩擦系数在0.5
‑
1左右区间,所得摩擦系数至少降低50%,这可以显著降低能耗。
具体实施方式
[0033]
现结合实施例、附图对本发明作进一步描述:
[0034]
本发明实施例提供了粉末冶金方法制备镍钛金属间化合物基自润滑复合材料,其特征在于所述材料按照质量百分比计由以下组分构成:
[0035]
50
‑
85%的镍钛金属间化合物,粉末,粒度100
‑
500目
[0036]5‑
25%的碱金属氟化物,粉末,粒度300
‑
500目
[0037]5‑
20%软金属,粉末,粒度100
‑
500目
[0038]5‑
30%硬质相,粉末,粒度200
‑
600目
[0039]
所述镍钛金属间化合物可根据现有技术中已知的方法制备,或购自市售产品。
[0040]
所述碱金属氟化物为氟化钙、氟化钡、氟化锶中的一种或几种,优选氟化钙与氟化钡的共晶。所述氟化钙与氟化钡的共晶可根据现有技术中已知的方法制备,或购自市售产品。例如,采用市售的产品,氟化钙与氟化钡的共晶为300目。
[0041]
所述软金属为银、铜、金、铅、铟等中的一种或几种,购自市售产品。
[0042]
所述硬质相为碳化铬、氧化铬、碳化钛、氧化铝等中的一种或几种,碳化铬购自市售产品。
[0043]
将上述物质按比例混合均匀,混合方式可以干混和湿混。例如干混,通过机械球磨的方式制备。机械球磨所用的罐和球均为硬质wc,球料质量比为3:1
‑
10:1,转速为100
‑
150转/分钟,球磨时间3
‑
20小时。
[0044]
将混合均匀的物料通过粉末冶金的方式制备自润滑复合材料。所述粉末冶金方法包括高温热压烧结、等静压烧结、放电等离子烧结等。例如放电等离子烧结,烧结处理参数为:真空度为10
‑3‑
10
‑1pa;升温速率为50
‑
150℃/min,优选90
‑
100℃/min;烧结温度为900
‑
1250℃,优选1050
‑
1150℃;施加压力为30
‑
40mpa;保温时间为5
‑
15min。
[0045]
采用具体实施例对本发明的材料进行详细说明:
[0046]
本发明材料的检测方法如下:
[0047]
摩擦磨损性能采用而后用umt
‑
tribolab(bruker,germany)高温摩擦磨损试验机
进行评价,对偶球为si3n4陶瓷,载荷为3
‑
15n,温度rt
‑
800℃,滑动线速度为0.1
‑
0.4m/s,摩擦半径为5mm,运行时间为10min。
[0048]
实施例1
[0049]
按照质量百分比,分别称取70%镍钛金属间化合物粉末(粒径为100μm;质量百分比为:60%ni,40%ti),8%银(粒度为80μm),8%氟化钙与氟化钡的共晶(粒度为100μm),14%碳化铬(粒度为20μm)通过机械球磨获得混合粉末,然后将混合粉末置于放电等离子烧结炉中进行烧结,采用的烧结参数为:真空度为5
×
10
‑2pa,升温速率为100℃/min,烧结温度为1150℃,施加压力为35mpa,保温时间为5min。烧结完成后随炉冷却至室温,得到镍钛金属间化合物基自润滑复合材料。
[0050]
摩擦实验中,对偶球为si3n4陶瓷,载荷为10n,温度400℃,滑动线速度为0.1m/s,摩擦半径为5mm,运行时间为10min
[0051]
所述自润滑复合材料的摩擦系数较小,为0.15,且数据稳定,其磨损率为3.75
×
10
‑6mm3n
‑1m
‑1,测定在载荷10n、滑动线速度0.1m/s下进行。
[0052]
图片1实施例1中镍钛金属间化合物在400℃下的摩擦系数。
[0053]
实施例2
[0054]
按照质量百分比,分别称取70%镍钛金属间化合物粉末(粒径为100μm;质量百分比为:60%ni,40%ti),8%银(粒度为80μm),8%氟化钙与氟化钡的共晶(粒度为100μm),14%碳化铬(粒度为20μm)通过机械球磨获得混合粉末,然后将混合粉末置于放电等离子烧结炉中进行烧结,采用的烧结参数为:真空度为5
×
10
‑2pa,升温速率为100℃/min,烧结温度为1150℃,施加压力为35mpa,保温时间为5min。烧结完成后随炉冷却至室温,得到镍钛金属间化合物基自润滑复合材料。
[0055]
摩擦实验中,对偶球为si3n4陶瓷,载荷为10n,温度600℃,滑动线速度为0.1m/s,摩擦半径为5mm,运行时间为10min
[0056]
所述自润滑复合材料的摩擦系数较小,为0.17,且数据稳定,其磨损率为1.12
×
10
‑6mm3n
‑1m
‑1,测定在载荷10n、滑动线速度0.1m/s下进行。
[0057]
图片2实施例2中镍钛金属间化合物在600℃的摩擦系数。
[0058]
实施例3
[0059]
按照质量百分比,分别称取70%镍钛金属间化合物粉末(粒径为100μm;质量百分比为:60%ni,40%ti),8%银(粒度为80μm),8%氟化钙与氟化钡的共晶(粒度为100μm),14%碳化铬(粒度为20μm)通过机械球磨获得混合粉末,然后将混合粉末置于放电等离子烧结炉中进行烧结,采用的烧结参数为:真空度为5
×
10
‑2pa,升温速率为100℃/min,烧结温度为1150℃,施加压力为35mpa,保温时间为5min。烧结完成后随炉冷却至室温,得到镍钛金属间化合物基自润滑复合材料。
[0060]
摩擦实验中,对偶球为si3n4陶瓷,载荷为10n,温度800℃,滑动线速度为0.1m/s,摩擦半径为5mm,运行时间为10min
[0061]
所述自润滑复合材料的摩擦系数较小,为0.16,且数据稳定,其磨损率为2.33
×
10
‑6mm3n
‑1m
‑1,测定在载荷10n、滑动线速度0.1m/s下进行。
[0062]
图片3实施例3中镍钛金属间化合物在800℃的摩擦系数。
再多了解一些
本文用于企业家、创业者技术爱好者查询,结果仅供参考。