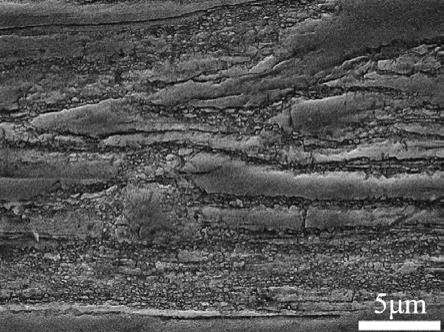
1.本发明涉及一种微合金化镁合金的制备方法。
背景技术:
2.镁合金具有低密度、高比强度和比刚度的优异性能,在现代金属轻量化的应用上具有明显优势,但较差的塑性与变形能力限制了镁合金的广泛应用。在此背景下,探索制备新的合金成分以期得到综合力学性能优良的镁合金是当下科研工作者的主要研究方向。研究表明,通过添加合适的合金元素并结合合理的热变形工艺可有效改善镁合金的强度和塑性。zn元素可以提高合金的强度、塑性及抗蠕变性能;zr元素可细化晶粒,减少热裂倾向,提高镁合金的力学性能和耐腐蚀性,其含量在0.5wt.%~0.8wt.%时晶粒细化效果最好。然而,加入大量的合金元素会在材料内部形成不利于后续热变形加工的第二相,对塑性产生不良影响;而加入微量的合金元素又无法达到理想的强化效果,难以实现强度的提高。有研究表明添加稀土元素可以改善镁合金的力学性能,但稀土元素价格较高,使得其在商业生产中无法作为镁合金的主要合金化元素。稀土元素的添加可显著提高镁合金的耐热性,细化晶粒,减少显微疏松和热裂倾向,改善铸造性能。塑性变形过程中非基底位错滑移会导致合金强度下降,而均匀分布的稀土合金相会抑制塑性变形过程中非基底位错滑移的产生从而提高强度,常用的稀土元素有gd、y、nd等,其中nd的延性参数高于gd和y。
技术实现要素:
3.本发明是要解决现有的镁合金材料成本过高、材料强度和塑性难以良好匹配的技术问题,而提供一种微合金化超高强度镁合金的制备方法。
4.本发明的微合金化超高强度镁合金的制备方法是按以下步骤进行的:一、制备微合金化镁合金:将纯镁块放置在带筋坩埚中,带筋坩埚的顶部盖上盖体,将带筋坩埚放置在电阻加热炉中,在保护气氛下将带筋坩埚中的纯镁块加热至720℃~740℃,待纯镁完全熔化后,将预热好的纯zn粒和预热好的mg
‑
30nd中间合金一起加入到纯mg熔体中,然后将混合熔体升温至760℃~780℃,将预热好的mg
‑
30zr中间合金加入到熔体中,将斜叶搅拌桨伸入熔体中并固定,在760℃~780℃进行多场应力协同均质搅拌3min~5min来促进合金元素均匀分散;取出斜叶搅拌桨,熔体在760℃~780℃静置20min~25min,扒去熔体表面的废渣,将预热好的精炼剂用锌箔包裹并用斜叶搅拌桨将其送入熔体中,斜叶搅拌桨伸入液面下,固定斜叶搅拌桨,在760℃~780℃进行多场应力协同均质搅拌熔体30s~40s进行精炼;然后在760℃~780℃的温度下静置保温30min~35min,扒去熔体表面废渣;将金属熔体浇铸到预热温度为250℃~260℃且提前充入保护气氛的铸铁模具中,持续通保护气氛直至合金自然冷却至室温,将其从铸铁模具中取出,得到铸态mg
‑
zn
‑
nd
‑
zr合金,采用电火花线切割机将铸态镁合金切割成块体;所述的保护气氛为co2与sf6的混合气体,二者的体积比为co2:sf6=40:(5~6);所述的斜叶搅拌桨设置有四个桨叶且相邻的两个桨叶之间呈90
°
夹角,每个桨叶
均与水平面呈45
°
夹角,每个桨叶的最外侧底角为圆弧结构,圆弧结构可对金属熔体产生向下的螺旋剪切压力,促进元素均匀分布,提高坯料的质量;所述的带筋坩埚的内壁竖直设置4个挡板,相邻的两个挡板之间呈90
°
夹角,每个挡板的底部均固定在带筋坩埚的底面上,每个挡板的顶部设置在带筋坩埚的中上部,每个挡板的侧边设置倒角,在搅拌时通过挡板的阻碍缓冲作用增大液层剪切力,加剧元素分散;所述的斜叶搅拌桨的桨叶的最外侧与带筋坩埚的挡板的最外侧的最小间距为1cm~2cm;所述的盖体是由两个半圆板组成,每个半圆板上各设置一个通气孔,盖体中间设置一个圆孔用以穿过斜叶搅拌桨;所述的多场应力协同均质搅拌为:将斜叶搅拌桨以50rpm~100rpm的搅拌速度搅拌使得熔体表面无明显涡流产生,以此来克服搅拌引起的夹杂和卷气等缺陷,同时坩埚内嵌竖直挡板可辅助对熔体进行搅拌和剪切,避免了斜挡板带来的熔体滞留死区问题,有利于熔体的混合分散;所述的铸态mg
‑
zn
‑
nd
‑
zr合金中zn的质量分数为3wt.%~3.5wt.%,nd的质量分数为0.3wt.%~0.9wt.%,zr的质量分数为0.5wt.%~0.6wt.%,余量为mg;二、进行分级形变热处理:首先将步骤一得到的铸态mg
‑
zn
‑
nd
‑
zr合金块体用三层锌箔包裹,然后放在箱式电阻炉中进行均匀化热处理,水冷淬火;然后对块体采用台式砂轮机打磨去除表面氧化物,最后采用四柱立式压力试验机进行梯度变径两级连续挤压,空冷至室温,得到具有超高强度的微合金化mg
‑
zn
‑
nd
‑
zr合金;所述的均匀化热处理方法如下:首先在430℃~450℃保温6h~6.5h使低熔点第二相完全融入基体中,增强固溶强化效果,随后升温至490℃~500℃保温8h,保证镁合金中的合金、稀土元素均匀分布,降低成分偏析;所述的梯度变径多级连续挤压的工艺如下:挤压温度为180℃~200℃,挤压速率为0.1mm/s~0.5mm/s;采用两级变径连续挤压,先进行小变形量挤压,挤压比是16:9;再进行大变形量挤压,挤压比是9:1;小变形量挤压可以积累一定的变形储能有利于后续的大变形挤压,经过两级连续挤压后,合金发生明显动态再结晶,析出相逐渐呈颗粒状均匀分布在晶界处,基体晶粒得到显著细化。
5.本发明制备的微合金化超高强度mg
‑
zn
‑
nd
‑
zr合金材料是通过微量的zn、nd和zr元素在镁基体中产生的强化机制来提高镁合金的力学性能;主要为zn元素可以提高合金的强度、塑性及抗蠕变性能;zr元素可细化晶粒,减少热裂倾向,提高力学性能和耐腐蚀性,其含量在0.5wt.%~0.8wt.%时晶粒细化效果最好;nd元素可显著提高镁合金的耐热性,细化晶粒,减少显微疏松和热裂倾向,改善铸造性能;步骤一中用斜叶搅拌桨在熔体液面下协同带筋坩埚的挡板进行多场应力协同均质搅拌有利于促进zn、nd和zr元素的快速扩散,提高镁合金材料的组织均匀性;250℃~260℃的浇铸温度有利于提高过冷度,有效细化晶粒;步骤二的分级均匀化热处理有利于增强固溶强化效果,促进元素均匀分布,减少成分偏析;梯度变径两级连续挤压在逐步减小坯料尺寸的同时进行两级连续挤压,可明显细化坯料内部晶粒、析出相的尺寸,同时在变形过程中变形组织沿挤压方向的均匀分布可进一步提高其塑性,便于在低温下挤压,降低能耗。
6.本发明中采用nd元素作为镁合金的合金化元素之一,在传统mg
‑
zn二元合金中添
加少量的稀土元素nd和合金元素zr,经过两级形变热处理后,在实现微合金化的同时达到良好的强韧化效果,确保合金具有高强度的同时仍具备可接受的塑性,而且微合金化也可以最大限度的减少因合金化而产生的夹杂等缺陷,降低成本,提高生产效率。
7.与现有技术相比,本发明具有以下优点和有益效果:(1)本发明提出了一种微合金化超高强度镁合金的制备方法,加入稀土元素nd有利于净化镁合金熔体,改善镁合金铸造性能,同时可以明显细化晶粒,调控微观组织;控制nd含量在0.3wt.%~0.9wt.%的原因是该成分范围内的原子比具有较好的细化晶粒和弱化织构效果,同时添加少量稀土元素降低了生产原料成本;由于zn元素在镁中具有较高的固溶度,添加zn可以显著提高镁合金的强度,并在后续挤压过程中产生一定的析出相弥散强化;本发明添加3wt.%~3.5wt.%zn的原因是在提高强度的前提下不损失过多塑性;zr元素的添加有利于细化晶粒,减少热裂倾向;添加0.5wt.%~0.6wt.%zr的原因是通过它的异质形核作用来细化镁合金组织,提高合金组织的稳定性和均匀性。本发明添加的zn、nd和zr元素通过内部反应会生成三元共晶相以及mgzn2相,之后的梯度变径两级连续挤压过程中也会动态析出大量细小的mgzn2相,通过细晶强化作用有效提高了镁合金的力学性能,同时zn和zr元素对于稀土元素弱化织构的效果具有放大作用;(2)本发明以mg
‑
nd和mg
‑
zr中间合金的形式在金属熔体中加入nd和zr元素,确保了合金成分的准确调控,操作简单易于进行,缩短工艺周期,大幅提高该合金的成型效率;(3)本发明采用的带筋坩埚为在坩埚内壁均匀设置四个竖直挡板,在搅拌时通过挡板的阻碍缓冲作用增大液层剪切力,加剧元素分散;(4)本发明采用的斜叶搅拌桨为45
°
四斜叶搅拌桨,叶片与水平方向呈45
°
倾斜,结合叶片外侧底部的圆角可对金属熔体产生向下的螺旋剪切压力,促进元素均匀分布,提高坯料的质量;(5)本发明采用与带筋坩埚相匹配的斜叶搅拌桨在液面下进行多场应力协同均质搅拌高温合金液的方法极大地促进元素在镁合金基体中的均匀分布,一定程度上消除了合金、稀土元素在金属基体中偏析的缺陷,解决了夹杂和卷气氧化等问题;(6)本发明步骤二中先进行分级均匀化热处理:其工艺为430℃
×
6h 490℃
×
8h,其中430℃
×
6h保证材料中低熔点第二相完全融入基体中,增强固溶强化效果,随后490℃
×
8h保证镁合金中的合金、稀土元素均匀分布,降低成分偏析;然后进行梯度变径两级连续挤压,通过自研发的多梯度平锥形挤压模孔,在逐步减小坯料尺寸的同时进行两级连续挤压变形,可明显细化坯料内部晶粒和析出相的尺寸,同时在变形过程中变形组织沿挤压方向的均匀分布可进一步提高性能;(7)本发明由于加入微量的nd和zr元素使得合金的热变形抗力减小,热变形温度可由300℃以上降低至200℃以下,有效限制晶粒长大的同时进一步节约成本、降低能耗;(8)本发明制备的超高强度微合金化镁合金的力学性能得到极大程度提高的主要原因是:1、晶粒显著细化所导致的细晶强化;2、由大量的细小弥散分布析出相所导致的orowan强化;本发明制备的超高强度微合金化镁合金的屈服强度为411mpa~475mpa,抗拉强度为467mpa~507mpa,延伸率为2.6%~3.6%。
附图说明
8.图1为试验一的步骤一中熔炼合金的装置示意图;图2为试验一的45
°
四斜叶搅拌桨4的示意图;图3为试验一的45
°
四斜叶搅拌桨4和带筋坩埚3组合在一起的俯视图;图4为试验一的步骤二中梯度变径两级连续挤压装置示意图;图5为图4的多梯度平锥形挤压模孔的放大图;图6是试验一制备的mg
‑
zn
‑
nd
‑
zr合金的om显微组织图;图7是试验二制备的mg
‑
zn
‑
nd
‑
zr合金的om显微组织图;图8是试验三制备的mg
‑
zn
‑
nd
‑
zr合金的om显微组织图;图9是试验一制备的mg
‑
zn
‑
nd
‑
zr合金的sem显微组织图;图10是试验二制备的mg
‑
zn
‑
nd
‑
zr合金的sem显微组织图;图11是试验三制备的mg
‑
zn
‑
nd
‑
zr合金的sem显微组织图;图12为工程应力
‑
工程应变曲线图。
具体实施方式
9.具体实施方式一:本实施方式为一种微合金化超高强度镁合金的制备方法,具体是按以下步骤进行的:一、制备微合金化镁合金:将纯镁块放置在带筋坩埚中,在带筋坩埚的顶部盖上盖体,将带筋坩埚放置在电阻加热炉中,在保护气氛下将带筋坩埚中的纯镁块加热至720℃~740℃,待纯镁完全熔化后,将预热好的纯zn粒和预热好的mg
‑
30nd中间合金一起加入到纯mg熔体中,然后将混合熔体升温至760℃~780℃,将预热好的mg
‑
30zr中间合金加入到熔体中,将斜叶搅拌桨伸入熔体中并固定,在760℃~780℃进行多场应力协同均质搅拌3min~5min;取出斜叶搅拌桨,熔体在760℃~780℃静置20min~25min,扒去熔体表面的废渣,将预热好的精炼剂用锌箔包裹并用斜叶搅拌桨将其送入熔体中,斜叶搅拌桨伸入液面下,固定斜叶搅拌桨,在760℃~780℃进行多场应力协同均质搅拌熔体30s~40s进行精炼;然后在760℃~780℃的温度下静置保温30min~35min,扒去熔体表面废渣;将金属熔体浇铸到预热温度为250℃~260℃且提前充入保护气氛的铸铁模具中,持续通保护气氛直至合金自然冷却至室温,将其从铸铁模具中取出,得到铸态mg
‑
zn
‑
nd
‑
zr合金,采用电火花线切割机将铸态镁合金切割成块体;所述的保护气氛为co2与sf6的混合气体,二者的体积比为co2:sf6=40:(5~6);所述的斜叶搅拌桨设置有四个桨叶且相邻的两个桨叶之间呈90
°
夹角,每个桨叶均与水平面呈45
°
夹角,每个桨叶的最外侧底角为圆弧结构;所述的带筋坩埚的内壁竖直设置4个挡板,相邻的两个挡板之间呈90
°
夹角,每个挡板的底部均固定在带筋坩埚的底面上,每个挡板的顶部设置在带筋坩埚的中上部,每个挡板的侧边设置倒角;所述的斜叶搅拌桨的桨叶的最外侧与带筋坩埚的挡板的最外侧的最小间距为1cm~2cm;所述的盖体是由两个半圆板组成,每个半圆板上各设置一个通气孔,盖体中间设置一个圆孔用以穿过斜叶搅拌桨;
两处所述的多场应力协同均质搅拌工艺均为:将斜叶搅拌桨以50rpm~100rpm的搅拌速度搅拌;所述的铸态mg
‑
zn
‑
nd
‑
zr合金中zn的质量分数为3wt.%~3.5wt.%,nd的质量分数为0.3wt.%~0.9wt.%,zr的质量分数为0.5wt.%~0.6wt.%,余量为mg;二、进行分级形变热处理:首先将步骤一得到的铸态mg
‑
zn
‑
nd
‑
zr合金块体用三层锌箔包裹,然后放在箱式电阻炉中进行均匀化热处理,水冷淬火;然后对块体采用台式砂轮机打磨去除表面氧化物,最后采用四柱立式压力试验机进行梯度变径两级连续挤压,空冷至室温,得到具有超高强度的微合金化mg
‑
zn
‑
nd
‑
zr合金;所述的均匀化热处理方法如下:首先在430℃~450℃保温6h~6.5h,随后升温至490℃~500℃保温8h;所述的梯度变径多级连续挤压的工艺如下:挤压温度为180℃~200℃,挤压速率为0.1mm/s~0.5mm/s;采用两级变径连续挤压,先进行小变形量挤压,挤压比是16:9;再进行大变形量挤压,挤压比是9:1。
10.具体实施方式二:本实施方式与具体实施方式一不同的是:步骤一中所述的铸态mg
‑
zn
‑
nd
‑
zr合金中zn的质量分数为3wt.%,nd的质量分数为0.3wt.%,zr的质量分数为0.5wt.%,余量为mg。其他与具体实施方式一相同。
11.具体实施方式三:本实施方式与具体实施方式一或二不同的是:步骤一中所述的精炼剂为caf2和mgcl2的混合物,其中caf2的质量分数为5wt.%。其他与具体实施方式一或二相同。
12.具体实施方式四:本实施方式与具体实施方式一至三之一不同的是:步骤一中纯zn粒的预热温度、mg
‑
30nd中间合金的预热温度和mg
‑
30zr中间合金的预热温度均为150℃~250℃。其他与具体实施方式一至三之一相同。
13.具体实施方式五:本实施方式与具体实施方式四不同的是:步骤二中所述的均匀化热处理方法如下:首先在430℃保温6h,随后升温至490℃保温8h。其他与具体实施方式四相同。
14.用以下试验对本发明进行验证:试验一:本试验为一种微合金化超高强度镁合金的制备方法,具体是按以下步骤进行的:一、制备微合金化镁合金:将纯镁块放置在带筋坩埚中,带筋坩埚的顶部盖上盖体,将带筋坩埚放置在电阻加热炉中,在保护气氛下将带筋坩埚中的纯镁块加热至720℃,待纯镁完全熔化后,将预热好的纯zn粒和预热好的mg
‑
30nd中间合金一起加入到纯mg熔体中,然后将混合熔体升温至760℃,将预热好的mg
‑
30zr中间合金加入到熔体中,将斜叶搅拌桨伸入熔体中距坩埚底部3cm并固定,在760℃进行多场应力协同均质搅拌3min来促进合金元素均匀分散(具体为将斜叶搅拌桨以100rpm的搅拌速度顺时针搅拌使得熔体表面无明显涡流产生,以此来克服搅拌引起的夹杂和卷气等缺陷,同时坩埚内嵌竖直挡板可辅助对熔体进行搅拌和剪切,避免了斜挡板带来的熔体滞留死区问题,有利于熔体的混合分散);取出斜叶搅拌桨,熔体在760℃静置20min,扒去熔体表面的废渣,将预热好的精炼剂用锌箔包裹并用斜叶搅拌桨将其送入熔体中,斜叶搅拌桨伸入液面下距坩埚底部3cm,固定斜叶搅拌桨,在760℃进行多场应力协同均质搅拌熔体30s进行精炼(具体为将斜叶搅拌桨以50rpm的
搅拌速度顺时针搅拌);然后在780℃的温度下静置保温30min,扒去熔体表面废渣;将金属熔体浇铸到预热温度为250℃且提前充入保护气氛的铸铁模具中,持续通保护气氛直至合金自然冷却至室温,将其从铸铁模具中取出,得到铸态mg
‑
zn
‑
nd
‑
zr合金,采用电火花线切割机将铸态镁合金切割成块体;所述的精炼剂为caf2和mgcl2的混合物,其中caf2的质量分数为5wt.%,其质量分数为镁合金总质量的1.5wt.%;所述的保护气氛为co2与sf6的混合气体,二者的体积比为co2:sf6=20:3;所述的保护气氛为co2与sf6的混合气体,二者的体积比为co2:sf6=20:3;所述的斜叶搅拌桨设置有四个桨叶且相邻的两个桨叶之间呈90
°
夹角,每个桨叶均与水平面呈45
°
夹角,每个桨叶的最外侧底角为圆弧结构,圆弧结构可对金属熔体产生向下的螺旋剪切压力,促进元素均匀分布,提高坯料的质量;所述的带筋坩埚的内壁竖直设置4个挡板,相邻的两个挡板之间呈90
°
夹角,每个挡板的底部均固定在带筋坩埚的底面上,每个挡板的顶部设置在带筋坩埚的中上部,每个挡板的侧边设置倒角,在搅拌时通过挡板的阻碍缓冲作用增大液层剪切力,加剧元素分散;所述的斜叶搅拌桨的桨叶的最外侧与带筋坩埚的挡板的最外侧的最小间距为1cm;所述的盖体是由两个半圆板组成,每个半圆板上各设置一个通气孔,盖体中间设置一个圆孔用以穿过斜叶搅拌桨;所述的铸态mg
‑
zn
‑
nd
‑
zr合金中zn的质量分数为3wt.%,nd的质量分数为0.3wt.%,zr的质量分数为0.5wt.%,余量为mg;所述的铸铁模具的内腔为空心圆柱体,尺寸为60mm
×
60mm
×
180mm;所述的铸态mg
‑
zn
‑
nd
‑
zr合金块的机械加工尺寸为30mm
×
30mm
×
60mm;二、进行分级形变热处理:首先将步骤一得到的铸态mg
‑
zn
‑
nd
‑
zr合金块体用三层锌箔包裹,然后放在箱式电阻炉中进行均匀化热处理,水冷淬火;然后对块体采用台式砂轮机打磨去除表面氧化物,最后采用四柱立式压力试验机进行梯度变径两级连续挤压,空冷至室温,得到具有超高强度的微合金化mg
‑
zn
‑
nd
‑
zr合金;所述的均匀化热处理方法如下:首先在430℃保温6h使低熔点第二相完全融入基体中,增强固溶强化效果,随后升温至490℃保温8h,保证镁合金中的合金、稀土元素均匀分布,降低成分偏析;所述的梯度变径多级连续挤压的工艺如下:挤压温度为180℃,挤压速率为0.5mm/s;采用两级变径连续挤压,先进行小变形量挤压,挤压比是16:9;再进行大变形量挤压,挤压比是9:1;小变形量挤压可以积累一定的变形储能有利于后续的大变形挤压,经过两级连续挤压后,合金发生明显动态再结晶,析出相逐渐呈颗粒状均匀分布在晶界处,基体晶粒得到显著细化。
15.试验一的步骤一中熔炼合金的装置如图1
‑
图3所示,具体是由电阻丝加热源1、电阻加热炉2、带筋坩埚3、45
°
四斜叶搅拌桨4和盖体5组成;所述的盖体5中心设置通孔5
‑
1用来穿过45
°
四斜叶搅拌桨4,盖体5是由两个半圆组合而成,两个半圆上各有一个通气孔5
‑
2;所述的带筋坩埚3的内壁竖直设置4个挡板3
‑
1,相邻的两个挡板3
‑
1之间呈90
°
夹
角,每个挡板3
‑
1的底部均固定在带筋坩埚3的底面上,每个挡板3
‑
1的顶部设置在带筋坩埚3的中上部,每个挡板3
‑
1的侧边设置倒角,在搅拌时通过挡板3
‑
1的阻碍缓冲作用增大液层剪切力,加剧元素分散;所述的斜叶搅拌桨4设置有四个桨叶4
‑
1且相邻的两个桨叶4
‑
1之间呈90
°
夹角,每个桨叶4
‑
1均与水平面呈45
°
夹角,每个桨叶4
‑
1的最外侧底角为圆弧结构,圆弧结构可对金属熔体产生向下的螺旋剪切压力,促进元素均匀分布,提高坯料的质量;所述的斜叶搅拌桨4的桨叶4
‑
1的最外侧与带筋坩埚3的挡板3
‑
1的最外侧的最小间距为1cm;电阻丝加热源1是内嵌在加热炉炉体2的内壁中。
16.试验一的步骤二的梯度变径两级连续挤压装置图见图4和图5,具体是由挤压筒体5、挤压垫块6、挤压坯料9和多梯度平锥形挤压模孔组成;所述的多梯度平锥形挤压模孔是由上部8和下部7组成;挤压垫块6、挤压坯料9和多梯度平锥形挤压模孔按照从上至下的顺序设置在挤压筒体5的内腔中;挤压筒体5的内腔为圆柱体,其直径为40mm,高度为150mm;挤压垫块6为圆柱体,直径为40mm,高度为10mm;多梯度锥形挤压模孔的外壁为圆柱体且外径为40mm,总体高度为40mm,其内腔为上大下小的锥形结构,上部8的上端内径为40mm,下端内径为30mm;下部7的上端内径为30mm,下端内径为10mm;多梯度平锥形挤压模孔与挤压筒体5的内腔同轴设置、滑动连接、紧密贴合。
17.试验二:本试验与试验一不同的是:步骤一中所述的mg
‑
zn
‑
nd
‑
zr合金块体中zn的质量分数为3wt.%,nd的质量分数为0.6wt.%,zr的质量分数为0.5wt.%,余量为mg。其他与试验一相同。
18.试验三:本试验与试验一不同的是:步骤一中所述的mg
‑
zn
‑
nd
‑
zr合金块体中zn的质量分数为3wt.%,nd的质量分数为0.9wt.%,zr的质量分数为0.5wt.%,余量为mg。其他与试验一相同。
19.图6是试验一制备的mg
‑
zn
‑
nd
‑
zr合金的om显微组织图;图7是试验二制备的mg
‑
zn
‑
nd
‑
zr合金的om显微组织图;图8是试验三制备的mg
‑
zn
‑
nd
‑
zr合金的om显微组织图;图9是试验一制备的mg
‑
zn
‑
nd
‑
zr合金的sem显微组织图;图10是试验二制备的mg
‑
zn
‑
nd
‑
zr合金的sem显微组织图;图11是试验三制备的mg
‑
zn
‑
nd
‑
zr合金的sem显微组织图。如图所示,经梯度变径多级连续挤压后材料发生显著动态再结晶,变形组织呈条带状沿挤压方向分布,伴随着动态再结晶的发生,晶粒尺寸明显细化;第二相均匀分布在晶界周围,可以有效钉扎晶界,进一步细化晶粒,能有效提高材料的强度与塑性。同时发现随着nd含量的增加,再结晶程度先增大后减小,再结晶晶粒尺寸变化不大,在0.6wt.%nd时再结晶程度最高,析出相数量明显增加,基本分布于再结晶区域。
20.在室温下对三种mg
‑
zn
‑
nd
‑
zr合金进行力学性能测试,得到工程应力
‑
工程应变曲线如图12所示,曲线1为试验一制备的mg
‑
3zn
‑
0.3nd
‑
0.5zr(wt.%)合金,曲线3为试验二制备的mg
‑
3zn
‑
0.6nd
‑
0.5zr(wt.%)合金,曲线2为试验三制备的mg
‑
3zn
‑
0.9nd
‑
0.5zr(wt.%)合金。由图中可知,试验一制备的mg
‑
3zn
‑
0.3nd
‑
0.5zr(wt.%)合金的屈服强度为411mpa,抗拉强度为467mpa,延伸率为4.1%;试验二制备的mg
‑
3zn
‑
0.6nd
‑
0.5zr(wt.%)合金的屈服强度为475mpa,抗拉强度为507mpa,延伸率为3.6%;试验三制备的mg
‑
3zn
‑
0.9nd
‑
0.5zr(wt.%)合金的屈服强度为422mpa,抗拉强度为472mpa,延伸率为2.6%。
再多了解一些
本文用于企业家、创业者技术爱好者查询,结果仅供参考。