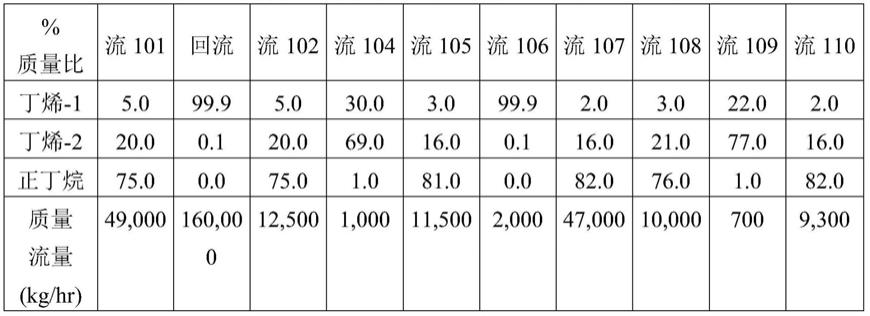
烯烃
‑
链烷烃膜分离方法
技术领域
1.化学工程涉及烯烃
‑
链烷烃膜分离方法。
背景技术:
2.在具有相似碳原子数的烯烃
‑
链烷烃原料流中,烯烃分离方法通常通过蒸馏来操作,这是采用非常高的回流比的传统方法,因为要分离的物质具有接近的相对挥发性,导致上述分离方法需要非常高的能量。因此,为了提高对烯烃产物的分离效率并减少能量消耗,已经开始研究在蒸馏方法中使用膜。但是,膜单元的级数和膜单元的设置位置影响到产物的分离效率和节能效率。将膜单元设置在与蒸馏塔的原料流、顶部流、底部流或循环流相连的一个或两个位置,使生产能力和分离效率低下,并且获得的节能效率也不是很好。
3.到目前为止,有一些关于具有接近沸点的碳氢化合物的分离方法的报导。例如,us专利文件no.2006/0281960a1披露了具有接近沸点的碳氢化合物的分离方法和膜的设置,以便从具有4
‑
16个碳原子的碳氢化合物原料中分离出至少一种正链烷烃。所述分离方法是通过将原料进料到至少一个蒸馏塔和至少一个膜单元中而获得。所述膜对至少一种正链烷烃具有特异性。然后,至少一种被分离的物质被进料回分离方法中,其中膜单元与蒸馏塔的进料、顶部、底部或侧抽位置相连,其中一个蒸馏塔可以在多个位置设置有多个膜单元。
4.us专利文件no.2006/0047176a1披露了通过复分解反应生产丁烯,包含将含有具有4个碳原子的链烷烃和烯烃的原料进料至分级分离方法中,以便将物质分成2个流。第一个流含有1
‑
丁烯,并且第二个流含有2
‑
丁烯。然后,通过异构化反应,第二个流的一部分2
‑
丁烯转化为1
‑
丁烯。第二个流的至少一部分异构化残余物再循环到之前的分级分离方法中。至少一种具有4个碳原子的原料和第二个流进料通过促进运输膜以进一步去除丁烷。
5.us专利文献no.2018/0029958a1披露了包含异丁烯、1
‑
丁烯、2
‑
丁烯、正丁烷和异丁烷的具有4个碳原子的原料的分离方法。所述分离方法通过使用有机腈、半渗透膜及其组合的萃取蒸馏来操作。分离出的烯烃进料回生产过程,通过异构化反应将至少一部分2
‑
丁烯转化为1
‑
丁烯产物,以获得至少80重量%的1
‑
丁烯产物。
6.基于上述原因,本发明旨在开发单级或多级串联的膜装置,其与蒸馏塔的进料和侧抽相连,以提高烯烃产物的生产能力和分离效率。此外,本发明还旨在减少烯烃
‑
链烷烃分离方法中的能量消耗。
技术实现要素:
7.本发明涉及一种为了提高烯烃产物的生产能力和分离效率,包括降低烯烃
‑
链烷烃分离方法的能量消耗,在含有具有2
‑
4个碳原子的碳氢化合物的原料流中,通过与蒸馏塔的进料和侧抽相连的单级或多级串联设置的促进输送膜的烯烃
‑
链烷烃分离方法。
8.在一方面,所述烯烃
‑
链烷烃分离方法包括以下步骤:
9.a.将含有具有2
‑
4个碳原子的碳氢化合物的原料流进料至蒸馏塔和膜单元中,其特征在于,所述膜单元包含在蒸馏塔的进料处与蒸馏塔相连的至少1级膜单元和与蒸馏塔
的侧抽相连的至少1级膜单元,其中所述膜单元包含对烯烃具有特异性的膜;和
10.b.分离一部分从膜单元通过的原料流,其中,至少一个流是主要包含烯烃的产物流并且至少一个流主要包含链烷烃。
附图说明
11.图1显示本发明1的烯烃
‑
链烷烃分离方法,设置有与蒸馏塔的进料和侧抽相连的1级膜单元。
12.图2显示本发明2的烯烃
‑
链烷烃分离方法,设置有与蒸馏塔的进料和侧抽相连的2级膜单元。
13.图3显示本发明3的烯烃
‑
链烷烃分离方法,设置有与蒸馏塔的进料和侧抽相连的3级膜单元。
14.图4显示本发明4的烯烃
‑
链烷烃分离方法,设置有与蒸馏塔的进料和侧抽相连的4级膜单元。
15.图5显示根据现有技术的烯烃
‑
链烷烃分离方法,未设置有膜单元。
16.图6显示根据现有技术的烯烃
‑
链烷烃分离方法,设置有与蒸馏塔的进料相连的1级膜单元。
17.图7显示根据现有技术的烯烃
‑
链烷烃分离方法,设置有与蒸馏塔的侧抽相连的1级膜单元。
具体实施方式
18.定义
19.除非另有说明,这里使用的技术术语或科学术语具有本领域技术人员的定义。
20.这里提到的任何工具、设备、方法或化学物质是指本领域技术人员常用的工具、设备、方法或化学物质,除非另有说明它们是本发明中特有的工具、设备、方法或化学物质。
21.在权利要求书或说明书中使用“包含”的单数名词或单数代词表示“一个”,也包括“一个或多个”、“至少一个”和“一个或一个以上”。
22.本技术中公开的所有组合物和/或方法以及权利要求,尽管在权利要求中没有具体说明,旨在涵盖与本发明明显不同的任何行动、性能、修改或调整的实施方案,并根据本领域普通技术人员获得与本实施方案相同的效用和结果。因此,可替代的或类似于本实施方案的客体,包括本领域技术人员清楚地理解的任何小的修改或调整,应被解释为仍在所附权利要求书中出现的发明精神、范围和概念中。
23.在本技术中,术语“约”是指在此出现或显示的任何数字,可因设备、方法或使用所述设备或方法的个人的任何错误而变化或偏离,包括根据例如湿度和温度等不可控参数改变反应条件而发生的变化或差异。
24.在下文中,示出本发明的实施方案而没有任何目的来限制本发明的任何范围。
25.本发明涉及含有具有2
‑
4个碳原子的碳氢化合物的原料流中的烯烃
‑
链烷烃分离方法,包括以下步骤:
26.a.将含有具有2
‑
4个碳原子的碳氢化合物的原料流送入蒸馏塔和膜单元,其特征在于,所述膜单元包括在蒸馏塔的进料处与蒸馏塔相连的至少1级膜单元和与蒸馏塔的侧
抽相连的至少1级膜单元,其中所述膜单元包括对烯烃具有特异性的膜;和
27.b.分离一部分从膜单元通过的原料流,其中至少一个流是主要包含烯烃的产物流并且至少一个流主要包含链烷烃。
28.在一个实施方案中,所述膜单元包含在蒸馏塔的进料处与蒸馏塔相连的至少1级膜单元,以及在蒸馏塔侧抽处与蒸馏塔相连的至少1级膜单元。
29.优选地,所述膜单元包含在蒸馏塔的进料处与蒸馏塔相连的至少2级串联的膜单元,以及在蒸馏塔的侧抽处与蒸馏塔相连的至少2级串联的膜单元。
30.最优选在蒸馏塔的进料处与蒸馏塔相连的2
‑
5级串联的膜单元,以及在蒸馏塔的侧抽处与蒸馏塔相连的2
‑
5级串联的膜单元。
31.在一个实施方案中,所述膜单元包含对烯烃具有特异性的促进运输膜。
32.在一个实施方案中,所述膜单元包含多糖材料,该多糖材料被选自银、铜或其组合的金属固定。优选由选自银的金属固定。
33.在一个实施方案中,所述烯烃
‑
链烷烃分离方法的原料流选自具有2
‑
4个碳原子的碳氢化合物,优选具有4个碳原子的碳氢化合物。
34.在一个实施方案中,所述原料流包含5
‑
95重量%的烯烃碳氢化合物和5
‑
95重量%的链烷烃碳氢化合物。优选包含20
‑
30重量%的烯烃碳氢化合物和70
‑
80重量%的链烷烃碳氢化合物。
35.在一个实施方案中,所述原料流含有选自丁烯
‑
1、丁烯
‑
2或其混合物的烯烃,并且链烷烃为正丁烷。
36.在一个实施方案中,所述碳氢化合物原料流进料至在蒸馏塔进料处与蒸馏塔相连的1级膜单元中,并在碳氢化合物原料流进料通过膜单元后,被分离成渗透物流和渗余物流,其在不同位置进料回蒸馏塔,并且其中,在蒸馏塔的侧抽处,原料流被抽出以进料至在蒸馏塔侧抽处与蒸馏塔相连的1级膜单元中,并且在原料流进料通过膜单元后,被分离成渗透物流和渗余物流,其在不同位置进料回蒸馏塔。
37.优选地,所述碳氢化合物原料流进料至串联的2级或更多级膜单元中,这些膜单元在蒸馏塔的进料处与蒸馏塔相连,并且当碳氢化合物原料流进料通过膜单元时,被分离成渗透物流和渗余物流,其中,渗透物流进料回蒸馏塔或与通过前级膜单元的前渗透物流合并以返回蒸馏塔,而渗余物流进料至串联的下级膜单元中,并且其中,在蒸馏塔的侧抽处,原料流进料至2级或更多级的串联的膜单元中,膜单元在蒸馏塔的侧抽处与蒸馏塔相连,当原料流进料通过膜单元时,被分离成渗透物流和渗余物流,其中,渗透物流进料回蒸馏塔或与通过前级膜单元的前渗透物流合并以返回蒸馏塔,而渗余物流进料至串联的下级膜单元中。
38.最优选地,所述碳氢化合物原料流进料至2
‑
5级串联的膜单元中,膜单元在蒸馏塔的进料处与蒸馏塔相连,当碳氢化合物原料流进料通过膜单元时,被分离成渗透物流和渗余物流,其中,渗透物流进料回蒸馏塔或与通过前级膜单元的前渗透物流合并以返回蒸馏塔,而渗余物流进料至串联的下级膜单元中,并且其中,在蒸馏塔的侧抽处,原料流进料至2
‑
5级串联的膜单元中,膜单元在蒸馏塔的侧抽处与蒸馏塔相连,当原料流进料通过膜单元时,被分离成渗透物流和渗余物流,其中,渗透物流进料回蒸馏塔或与通过前级膜单元的前渗透物流合并以返回蒸馏塔,而渗余物流进料至串联的下级膜单元中。
39.在一个实施方案中,所述通过膜的渗透物流在通过蒸馏塔的内部流的成分与通过膜的渗透物流的成分接近的位置处或具有相等或更少的烯烃浓度的位置处进料至蒸馏塔中,而渗余物流在通过蒸馏塔的内部流的成分与渗余物流的成分接近的位置处或具有相等或更少的链烷烃浓度的位置处进料至蒸馏塔中。
40.在一个实施方案中,原料流与蒸馏塔的回流比为3
‑
200。
41.在一个实施方案中,进料至任意级膜单元中的渗余物流与进料至前级的膜单元中的渗余物流的重量比为50%或更多。
42.在另一个实施方案中,所述烯烃
‑
链烷烃分离方法在30
‑
70℃的温度和1
‑
6.5巴的压力下,在具有80
‑
200理论级数的蒸馏塔中运行。优选在30
‑
60℃的温度和1
‑
5巴的压力下,在具有120
‑
180理论级数的蒸馏塔中运行。最优选在30
‑
50℃的温度和2
‑
5巴的压力下,在具有160
‑
170理论级数的蒸馏塔中运行。
43.在另一个实施方案中,与未设置有膜单元的现有技术的分离方法相比,所述烯烃
‑
链烷烃分离方法的能量消耗减少30
‑
50%。
44.在另一个实施方案中,与未设置有膜单元的现有技术的分离方法相比,所述烯烃
‑
链烷烃分离方法生产能力增加至少30%。
45.为了比较本发明的设置有膜单元模式的烯烃
‑
链烷烃分离方法与根据现有技术未设置有膜单元的烯烃
‑
链烷烃分离方法的效率,在图1、图2、图3和图4中,本发明的烯烃
‑
链烷烃分离方法具有至少有1个膜单元与蒸馏塔的进料处和侧抽相连,以及在图5、图6和图7中,根据现有技术的烯烃
‑
链烷烃分离方法,其未设置有膜单元或在蒸馏塔的进料处或侧抽处具有与蒸馏塔相连的1级膜单元,通过使用aspen plus模拟软件进行并测试。详情如下。
46.烯烃
‑
链烷烃分离方法可以通过将含有具有4个碳原子的碳氢化合物的原料流进料通过膜单元来完成,膜单元包含与蒸馏塔的进料和侧抽相连的促进输送膜。蒸馏塔级数为160
‑
170。温度为30
‑
50℃。压力为2
‑
5巴。
47.所述原料流含有20
‑
30重量%的烯烃化合物,其包含丁烯
‑
1和丁烯
‑
2,以及含量为70
‑
80重量%的链烷烃,所述链烷烃为正丁烷。
48.本发明的烯烃
‑
链烷烃分离方法
49.烯烃
‑
链烷烃分离方法1
50.烯烃
‑
烷烃分离方法1如图1所示。它通过将碳氢化合物的原料流(101)分离成2个流来完成,这2个流是进料至膜单元(102)的原料流和进料至蒸馏塔(103)的原料流。至膜单元(102)的原料流进料通过膜单元(12),膜单元(12)包含在蒸馏塔(11)的进料处与蒸馏塔(11)相连的1级膜单元。当至膜单元(102)的原料流进料通过膜单元(12)时,它被分离成主要包含烯烃的渗透物流(104)和主要包含链烷烃的渗余物流(105)。渗透物流(104)进料至蒸馏塔(11)中,其进料位置是通过所述蒸馏塔(11)的内部流的成分与渗透物流(104)的成分接近的位置,或具有相等或更少的烯烃浓度的位置。渗余物流(105)进料至蒸馏塔(11)中,其进料位置是通过所述蒸馏塔(11)的内部流的成分与渗余物流(105)的成分接近的位置,或具有相等或更少的链烷烃浓度的位置。
51.在蒸馏塔(11)的侧抽处,原料流(108)进料至膜单元(13)中,膜单元(13)包含在蒸馏塔的侧抽处与蒸馏塔相连的1级膜单元。当它进料至膜单元(13)中时,它被分离成主要包含烯烃的渗透物流(109)和主要包含链烷烃的渗余物流(110)。渗透物流(109)进料至蒸馏
塔(11)中,其进料位置是通过所述蒸馏塔(11)的内部流的成分与渗透物流(109)的成分接近的位置,或具有相等或更少的烯烃浓度的位置。渗余物流(110)进料至蒸馏塔(11)中,其进料位置是通过所述蒸馏塔(11)的内部流的成分与渗余物流(110)的成分接近的位置,或具有相等或更少的链烷烃浓度的位置。得到的烯烃产物(106)在蒸馏塔(11)的顶部被送出,而链烷烃碳氢化合物(107)在蒸馏塔(11)的底部被送出。
52.烯烃
‑
链烷烃分离方法2
53.烯烃
‑
链烷烃分离方法2如图2所示。它通过将碳氢化合物的原料流(201)分离成2个流来完成,这2个流是进料至膜单元(202)中的原料流和进料至蒸馏塔(203)中的原料流。至膜单元(202)的原料流进料通过膜单元,膜单元包含2级膜单元:在蒸馏塔(21)的进料处与蒸馏塔(21)相接的膜单元(22)和(23)。当至膜单元(202)的原料流进料通过膜单元(22)时,它被分离成主要包含烯烃的渗透物流(204)和主要包含链烷烃的渗余物流(205)。渗透物流(204)进料至蒸馏塔(21)中,其进料位置是通过所述蒸馏塔(21)的内部流的成分与渗透物流(204)的成分接近的位置,或具有相等或更少的烯烃浓度的位置。渗余物流(205)进料至膜单元(23)中,并被分离成主要包含烯烃的渗透物流(206)和主要包含链烷烃的渗余物流(207)。渗透物流(206)与渗透物流(204)合并为流(208),并在通过所述蒸馏塔(21)的内部流的成分与渗透物流(206)的成分接近的位置处或具有相等或更少的烯烃浓度的位置处进料回蒸馏塔(21)。渗余物流(207)进料至蒸馏塔(21)中,其进料位置是通过所述蒸馏塔(21)的内部流的成分与渗余物流(207)的成分接近的位置,或具有相等或更少的链烷烃浓度的位置。
54.在蒸馏塔(21)的侧抽处,原料流(211)进料至在蒸馏塔的侧抽处与蒸馏塔(21)相连的包含膜单元(24)和(25)的2级膜单元。当原料流(210)进料通过膜单元(24)时,它被分离成主要包含烯烃的渗透物流(212)和主要包含链烷烃的渗余物流(213)。渗透物流(212)进料至蒸馏塔(21)中,其进料位置是通过所述蒸馏塔(21)的内部流的成分与渗透物流(212)的成分接近的位置,或具有相等或更少的烯烃浓度的位置。渗余物流(213)进料至膜单元(25)中,并被分离成主要包含烯烃的渗透物流(214)和主要包含链烷烃的渗余物流(215)。渗透物流(214)与渗透物流(212)合并为流(216),并在通过所述蒸馏塔(21)的内部流的成分与渗透物流(214)的成分接近的位置处或具有相等或更少的烯烃浓度的位置处进料回蒸馏塔(21)。渗余物流(215)进料至蒸馏塔(21)中,其进料位置是通过所述蒸馏塔(21)的内部流的成分与渗余物流(215)的成分接近的位置,或具有相等或更少的链烷烃浓度的位置。得到的烯烃产物(209)在蒸馏塔(21)的顶部被送出,而链烷烃碳氢化合物(210)在蒸馏塔(21)的底部被送出。
55.烯烃
‑
链烷烃分离方法3
56.烯烃
‑
链烷烃的分离方法3如图3所示。它有在蒸馏塔的进料处与蒸馏塔相连的3级膜单元,和在蒸馏塔的侧抽处与蒸馏塔相连的3级膜单元。
57.烯烃
‑
链烷烃分离方法4
58.烯烃
‑
烷烃分离方法4如图4所示。它有在蒸馏塔的进料处与蒸馏塔相连的4级膜单元,和在蒸馏塔的侧抽处与蒸馏塔相连的4级膜单元。
59.根据现有技术的烯烃
‑
链烷烃分离方法
60.烯烃
‑
链烷烃分离方法5
61.烯烃
‑
烷烃分离方法5如图5所示。它是根据现有技术的未设置有膜单元的烯烃
‑
烷烃分离方法。
62.烯烃
‑
链烷烃分离方法6
63.烯烃
‑
烷烃分离方法6如图6所示。它有在蒸馏塔的进料处与蒸馏塔相连的1级膜单元。
64.烯烃
‑
链烷烃分离方法7
65.烯烃
‑
烷烃分离方法7如图7所示。它有在蒸馏塔的侧抽处与蒸馏塔相连的1级膜单元。
66.表1:从烯烃
‑
链烷烃分离方法1模型得到的质量平衡
[0067][0068]
表2:从烯烃
‑
链烷烃分离方法2模型得到的质量平衡
[0069][0070]
表3:从烯烃
‑
链烷烃分离方法3模型得到的质量平衡
[0071][0072]
表4:从烯烃
‑
链烷烃分离方法4模型得到的质量平衡
[0073][0074]
表5:从烯烃
‑
链烷烃分离方法5模型得到的质量平衡
[0075]
%质量比流501回流流502流503丁烯
‑
15.099.999.92.0丁烯
‑
220.00.10.116.0正丁烷75.00.00.082.0质量流量(kg/hr)49,000236,0002,00047,000
[0076]
表6:从烯烃
‑
链烷烃分离方法6模型得到的质量平衡
[0077]
%质量比流601回流流602流604流605流606流607丁烯
‑
15.099.95.030.03.099.92.0丁烯
‑
220.00.120.069.016.00.116.0正丁烷75.00.075.01.081.00.082.0质量流量(kg/hr)49,000200,00012,5001,00011,5002,00047,000
[0078]
表7:从烯烃
‑
链烷烃分离方法7模型得到的质量平衡
[0079]
%质量比流701回流流702流703流704流705流706丁烯
‑
15.099.999.92.03.022.02.0丁烯
‑
220.00.10.116.021.077.016.0正丁烷75.00.00.082.076.01.082.0质量流量(kg/hr)49,000171,0002,00047,00010,0007009,300
[0080]
原料流、产物流的物质组成和质量流量见表1至表7。
[0081]
表8:与未设置有膜单元的烯烃
‑
链烷烃分离方法相比,从本发明的烯烃
‑
链烷烃分离方法的模型和从根据现有技术在蒸馏塔的进料处或侧抽处设置有单个膜单元的烯烃
‑
链烷烃分离方法的模型得到的测试结果
[0082][0083]
本发明的烯烃
‑
链烷烃分离方法和根据现有技术在蒸馏塔进料处或侧抽处设置有单个膜单元的烯烃
‑
链烷烃分离方法,与根据现有技术未设置有膜单元的烯烃
‑
链烷烃分离方法相比,其分离效率和节能效率如表8所示。
[0084]
比较来自本发明的烯烃
‑
链烷烃分离方法模型与来自未设置有膜单元的烯烃
‑
链烷烃分离方法模型的结果,发现相比于根据现有技术的在蒸馏塔的进料处或侧抽处未设置有膜单元或设置有单个膜单元的烯烃
‑
链烷烃分离方法,本发明的烯烃
‑
链烷烃分离方法可以更好地提高烯烃分离效率。本发明的设置有膜单元的烯烃
‑
链烷烃分离方法可以提高进料回蒸馏塔中的烯烃回收率,其与设置的膜单元级数相关,这与降低烯烃
‑
链烷烃分离方法的能量消耗有关。
[0085]
从上述结果可以看出,本发明的烯烃
‑
链烷烃分离方法具有高效率,并且可以提高生产能力和烯烃回收率。这也减少本发明的目标中所指的能量消耗。
[0086]
本发明的最佳方式
[0087]
本发明的最佳方式如本发明的具体描述所提供。
再多了解一些
本文用于企业家、创业者技术爱好者查询,结果仅供参考。